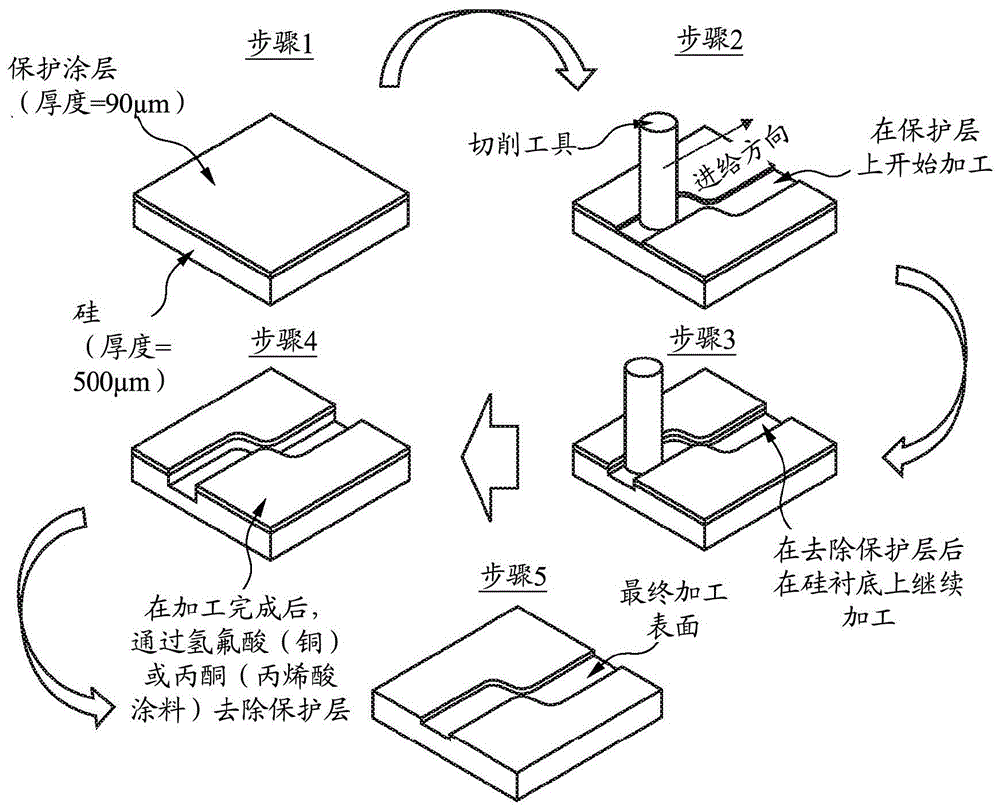
背景硅是一种坚硬易碎的材料,其广泛应用于半导体和微机电系统(mems)工业领域中。在硅中形成通道(特别是在微尺度上)可能具有挑战性,因为需要良好的加工质量和高精度的形状因子。目前,诸如深反应离子蚀刻(deepreactiveionetching,drie)和湿法蚀刻的减材技术通常用于mems/半导体工业中。这些技术可以经由光刻法通过图案化蚀刻停止部(etchstops)来实现图案化减材。这些技术本身很适合大规模制造。然而,这些技术在很大程度上局限于平面结构,且不适合加工较复杂的结构。该技术需要针对特定的材料进行调整,且如果需要创建微结构,而不是简单地蚀刻直线,则工艺就变得复杂了。使用皮秒和飞秒激光的基于激光的技术已经被证明实现了对硅微加工的良好精整。然而,处理时间非常慢。硅也可以通过磨削、研磨和抛光来机械制造。这是一种打磨方法,且通常用于对完整的硅基装置晶片进行薄化和对切成块的硅晶片进行整平。当需要高质量加工时,这是不合适的。机械微铣削是一种潜在的无掩模的替代方法,该方法可以获得新型的非平面三维结构。微铣削在延性材料的微加工中显示出巨大的潜力。然而,在脆性材料的微铣削中,产生过量的表面损伤和表面下损伤,例如边缘碎裂,仍然是一个挑战。当加工深度达到几百微米时,这个问题变得特别成问题。用于led中的氮化镓是另一种脆性材料,其需要高质量的微加工方法。所加工的轮廓的表面和边缘质量对光电性能有很大影响。choong等人(proc.imechepartb:jengineeringmanufacture,p1-9,2016)已经证明,选择晶体的结晶取向和所使用的切削工具的性质可以减少表面边缘碎裂。然而,这种减少不足以为许多应用提供合适质量的产品。仍然存在对加工脆性材料的方法的需要。本公开内容的概要根据本发明的第一个方面,提供了在脆性材料中切削通道(channel)的方法;该方法包括:提供复合材料,其中在脆性材料的表面上布置一层延性材料;和穿过延性材料层切削通道,去除布置在要切削的脆性材料部分上的延性材料部分,并切割到脆性材料中,以提供加工的复合物。发明人已经发现,将延性材料涂层施加到脆性材料的表面显著减少了在微铣削和其他切削技术中形成的表面边缘碎裂的量。不希望受理论的束缚,据信,延性材料充当能量缓冲物,并且减小了切削工具和脆性材料之间接触期间所产生的转移到脆性材料中的冲击能量的量。该方法可以是例如通过微铣削、微磨削、微车削、微钻削或飞切(flycutting)的铣削、磨削、车削、钻削或飞切的方法。在这种情况下,通道可以通过铣削、磨削、车削、钻削或飞切(例如通过微铣削、微磨削、微车削、微钻削或飞切)来切削到延性材料层中并穿过延性材料层。优选地,该方法是铣削的方法,并且将通道铣削到延性材料层中并穿过延性材料层。优选地,延性材料层与脆性材料的表面直接接触。当延性材料与脆性材料的表面直接接触时,边缘碎裂的减少最为显著。在使用中间层或粘合剂层将延性材料附接到脆性材料的某些情况下,只有当切削(例如铣削)具有小于某一深度(对于硅,该深度约为100μm)的通道时,才观察到可接受的边缘碎裂量。然而,在延性材料与脆性材料直接接触的情况下,即使在更大的通道深度(对于硅,大于约100μm)下,也观察到可接受的边缘碎裂量。提供复合材料的步骤可以包括将一层延性材料施加到脆性材料的表面以提供复合材料。提供复合材料的步骤可以包括将一层延性材料直接施加到脆性材料的表面以提供复合材料。该方法还可以包括从加工的复合物中去除延性材料以提供脆性材料的加工样品的步骤。可选择地,期望的产品可以是切削(例如铣削)的复合物。延性材料可以作为例如下面的脆性材料的保护层。延性层是诸如聚合物的隔离材料的情况尤其如此。通道可以是在平行于脆性材料的表面的平面中的直通道(即,在平面图中,当沿着垂直于脆性材料表面的平面的轴线观察时)。然而,通道可以在平行于脆性材料的表面的平面中包括至少一个曲线和/或角度。通道可以在平行于脆性材料表面的平面中包括多个曲线和/或角度。本发明在形成复杂形状方面最有用。许多现有的加工脆性材料的方法对形成复杂的形状而言是不够完善的。通道的横截面轮廓(即垂直于脆性材料表面的平面的横截面轮廓)可以是矩形的。然而,通道可以具有任何2维或2.5维的轮廓(在加工中,2.5维(2.5d)是指在没有悬垂元素的情况下包括从平面到第三维中的投影的表面。因此,2.5d表面可以表示为等高线图,只有一个深度或高度值垂直于平面的每个点。)。通道横截面的某些部分可能比其他部分更深。因此,通道可以具有弯曲的基部、倾斜的基部或者其可以具有台阶状的基部。切削通道可以是形成3d材料的第一步。通道可以沿其长度具有相同的深度,或者其可以沿其长度具有不同的深度。在通道具有不同深度的情况下,深度之间的过渡可能是平滑过渡,或者从一个深度到另一个深度的过渡可能涉及一个或多个台阶。脆性材料可以是单晶的,即它可以是单晶体的形式。脆性材料可以是多晶的。示例性脆性材料包括陶瓷和晶体元素(例如锗和硅)。示例性陶瓷包括玻璃和多孔陶瓷。脆性材料可选自:硅、锗、sige、氮化镓、硼硅酸盐玻璃、石英玻璃、钠钙玻璃、混凝土、陶瓷、石头、瓷砖、氧化铝(例如蓝宝石)、氧化锆、铌酸锂、碳化硅、碳化硼、氮化铝、氮化硅和碳化钨。特别优选的脆性材料包括:硅、锗、sige、蓝宝石和氮化镓。脆性材料可以是硅。脆性材料可以是氮化镓。脆性材料可以是蓝宝石。脆性材料可以是玻璃。示例性延性材料包括金属和金属合金及聚合物。示例性金属和金属合金包括有色金属或含有有色金属的合金。因此,示例性延性材料包括铝、铬、铜以及含有铝、铬或铜的合金。特别优选的延性材料包括铜及其合金。延性材料可以是铜。示例性聚合物包括热塑性聚合物和热固性聚合物两者。具体的示例包括丙烯酸树脂和环氧树脂。因此,延性材料可以是丙烯酸聚合物。延性材料可选自丙烯腈-丁二烯-苯乙烯(abs)和聚甲基丙烯酸甲酯(pmma)。延性材料可以是聚氯乙烯(pvc)。延性材料可以是环氧树脂。因此,延性材料可以是su-8。可以选择延性材料,使得延性材料和脆性材料之间的粘附功大于50mj/m2。延性材料和脆性材料之间的粘附功可大于70mj/m2。延性材料和脆性材料之间的粘附功可大于80mj/m2。当延性材料与脆性材料的表面紧密结合时,边缘碎裂的减少最为显著。在使用中间层或粘合剂层将延性材料相当好地附接到脆性材料的某些情况下,仅当铣削具有小于一定深度(对于硅,该深度约为100μm)的通道时,才观察到可接受的边缘碎裂量。然而,在延性材料与脆性材料紧密结合的情况下,甚至在更大的通道深度(对于硅,大于约100μm)也观察到可接受的边缘碎裂量。下面提供了一种计算两个表面之间的粘附功的方法。脆性材料可以是单晶体的形式。通道可以沿着晶体的<100>方向铣削。在脆性材料是硅的情况下,这是特别优选的。硅可以是{100}表面硅晶片。已经观察到,沿着这个方向铣削可以减少表面边缘碎裂。可以使用水平轴铣床铣削通道,其中主轴平行于脆性材料的表面。在水平轴铣削过程中,相对于脆性材料,铣刀的主轴可以沿与旋转的铣刀的朝着脆性材料的切削刃相同的方向移动,这被称为逆铣(或常规铣削)。可选地,在水平轴铣削过程中,相对于脆性材料,铣刀的主轴可以沿与旋转的铣刀的朝着脆性材料的切削刃相反的方向移动,这被称为顺铣(或同向铣削)。相对于顺铣,逆铣可以减少表面边缘碎裂。不希望受理论的约束,据信,这是因为在一趟切削过程中由每个切削刃去除的材料量从一趟切削的开始时的非常小的值开始,并朝向每趟切削的结束增加,促进了材料去除过程中的塑性变形而不是脆性断裂。铣削步骤通常将使用铣削工具(即铣刀)来执行,该铣削工具具有在使用中围绕圆柱形表面的切削刃(例如,切削刃可以平行于主轴延伸,或者可以围绕主轴螺旋延伸)。铣刀可以是arbor铣刀或水平安装的端铣刀。铣刀可以是金刚石涂层铣刀(例如金刚石涂层碳化钨铣刀)、化学气相沉积(cvd)金刚石铣刀或单晶金刚石铣刀。铣刀可以是金刚石涂层铣刀。已经观察到,相对于替代工具,这样的工具且尤其是金刚石涂层铣刀减少了表面边缘碎裂。可选择地,工具可以涂有tialn。延性材料层可具有10μm至500μm的厚度。延性材料层可具有25μm至500μm的厚度。延性材料层可具有50μm至250μm的厚度。延性材料层可具有75μm至150μm的厚度。延性材料层可具有20μm至150μm的厚度。发明人已经表明,低至20μm的厚度提供了保护效果。脆性材料可以是50μm到100mm厚。脆性材料可以是100μm到1000μm厚。脆性材料可以是400μm到600μm厚。脆性材料可以是500μm厚。切削(例如铣削)到脆性材料中的通道可以是5μm到500μm深。毫无疑问,这是去除延性材料后最终产品中的通道的深度,且对应于脆性材料和延性材料之间的界面到复合物中通道底部的距离。切削(例如铣削)到脆性材料中的通道可以是10μm到150μm深。切削(例如铣削)到脆性材料中的通道可以是100μm到200μm深。大于100μm的深度可能要求脆性材料和延性材料直接接触和/或延性材料和脆性材料之间的粘附功大于80mj/m2,以便实现某些应用所期望的加工质量,例如,在脆性材料是硅的情况下。在通道在其横截面上或沿其长度具有可变深度的情况下,本段中提到的深度是通道最深部分的深度。当切削工具到达脆性材料和延性材料之间的界面时,通常观察到切削力的微小变化,并且这可以用于确定(在加工公差范围内)切削(例如铣削)到脆性材料中的通道的深度,即使在不知道延性材料层的深度或者延性材料层的深度在脆性材料的表面上有变化的情况下。切削到脆性材料中的通道可以是从50μm到1000μm宽。这种规模的加工可以被描述为微加工。加工的复合物可以被描述为微加工的复合物,在这种情况下,延性材料被去除,这样做提供了对脆性材料的微加工样品。优选地,该方法是铣削脆性材料的方法。在这种情况下,用于铣削通道的铣削工具的主轴速度可以是10,000r/min至100,000r/min。主轴速度可以是25,000r/min至75,000r/min。这些实施方案尤其适用于脆性材料是硅的情况。用于铣削通道的铣削工具的切削速度(vc)可以是0.1mm/min至150mm/min。主轴速度可以为5mm/min至100mm/min。这些实施方案尤其适用于脆性材料是硅的情况。用于铣削通道的铣削工具的切削速度(vc)可以是0.1mm/min至150mm/min。主轴速度可以为5mm/min至100mm/min。这些实施方案尤其适用于脆性材料是硅的情况。铣削工具的每齿进给量(fz)可以为0.01μm/齿至0.3μm/齿。铣削工具的每齿进给量可以为0.05μm/齿至0.1μm/齿,特别是在工具(铣刀)是金刚石涂层端铣刀的情况下。铣削工具的每齿进给量可以为0.1μm/齿至0.2μm/齿,特别是在工具是cvd金刚石或单晶金刚石端铣刀的情况下。这些实施方案尤其适用于脆性材料是硅的情况。铣削设备可包括空气轴承主轴。铣削设备可包括三轴驱动级。铣削设备可包括力测量传感器。在延性材料是金属(例如铜)的情况下,可以将中间金属层施加到脆性材料,且随后通过电镀将延性金属施加到中间金属层。复合材料因此包括夹在延性金属层和脆性材料表面之间的中间金属层。该中间金属层可以是10nm至100nm厚。中间金属层可以是25nm至75nm厚。中间金属层可以是钛。可选地,延性金属(例如铜)层可以直接施加到脆性材料的表面。这可以通过例如溅射来实现。可选地,对于某些材料,这可以通过直接电镀来实现。在延性材料是金属(例如铜)的情况下,可以通过将铜层暴露于氢氟酸(例如暴露于硝酸和氢氟酸溶液的混合物)来去除铜。在存在中间金属层的情况下,这些条件通常也会溶解中间金属层。延性层可以是丙烯酸聚合物或共聚物。如果是这样,丙烯酸可以作为乳胶涂料施加到脆性材料的表面,例如通过将脆性材料浸入涂料中或通过喷涂脆性材料。延性层可以是环氧树脂,例如su-8。如果是这样,可以通过溅射或旋涂将环氧树脂施加到脆性材料的表面。在延性层是聚合物的情况下,可以使用合适的有机溶剂将其去除。一种特别用于丙烯酸聚合物的示例性有机溶剂是丙酮。可选择地,等离子蚀刻可用于去除聚合物层(例如环氧树脂层)。与纯化学蚀刻不同,等离子蚀刻提供了降低的热负荷。此外,切削的脆性材料的表面上不会有有机残留物。边缘碎裂的平均长度可小于50μm。边缘碎裂的平均长度可小于25μm。边缘碎裂的平均长度可小于15μm。边缘碎裂可以通过沿加工通道的竖直图像视图在碎裂表面上50个等距数据点上取平均长度测量值来定量表征。在本发明的第二方面,提供了通过本发明第一方面的方法获得或通过本发明第一方面的方法可获得的加工产品。本发明将通过以下编号的段落被进一步描述。1.一种在脆性材料中铣削微尺度通道的方法,所述方法包括:提供复合材料,其中在脆性材料的表面上布置一层延性材料;和穿过所述一层延性材料铣削通道并铣削到所述脆性材料中,以提供微加工的复合物。2.根据段落1所述的方法,其中所述一层延性材料与所述脆性材料的所述表面直接接触。3.根据段落1或段落2所述的方法,其中提供所述复合物的方法步骤包括将一层延性材料施加到脆性材料的表面以提供所述复合材料。4.根据段落1至3中任一项所述的方法,其中所述方法还包括从所述微加工的复合物中去除所述延性材料以提供所述脆性材料的微加工样品的步骤。5.根据段落1至4中任一项所述的方法,其中所述通道在平行于所述脆性材料的所述表面的平面中包括至少一个曲线和/或角度。6.根据段落1至5中任一项所述的方法,其中所述通道在平行于所述脆性材料的所述表面的平面中包括多个曲线和/或角度。7.根据段落1至6中任一项所述的方法,其中所述延性材料选自铝、铬、铜及其合金。8.根据段落1至6中任一项所述的方法,其中所述延性材料是丙烯酸聚合物。9.根据段落1至6中任一项所述的方法,其中所述延性材料是环氧树脂。10.根据段落1至9中任一项所述的方法,其中所述脆性材料为50μm至100mm厚。11.根据段落1至10中任一项所述的方法,其中铣削到所述脆性材料中的所述通道为5μm至500μm深。12.根据段落11所述的方法,其中铣削到所述脆性材料中的所述通道为100μm到200μm深。13.根据段落1至12中任一项所述的方法,其中铣削到所述脆性材料中的所述通道为50μm到1000μm宽。14.根据段落1至13中任一项所述的方法,其中所述一层延性材料为25μm至500μm厚。15.根据段落1至14中任一项所述的方法,其中所述脆性材料选自硅、锗、蓝宝石和氮化镓。16.根据段落15所述的方法,其中所述脆性材料是单晶硅。17.根据段落15所述的方法,其中所述通道沿着晶体的<100>方向被铣削。18.一种微加工产品,其根据段落1至17中任一项所述的方法获得或根据段落1至17中任一项所述的方法是可获得的。附图简述参考附图,在下文中进一步描述本发明的实施方案,在附图中:图1示出了本发明的示例性方法的示意图。图2示出了可用于实施本发明的方法的示例性微铣削系统。图3示出了使用i)钛粘合剂层上的铜延性材料;ii)没有延性材料;和iii)丙烯酸涂料延展层的硅的微铣削的加工轮廓的带注解的扫描电子显微镜(sem)图像。图4示出了使用各种延性材料和切削工具获得的加工样品的表面形貌。图5示出了使用具有不同涂层厚度的pmma延性层获得的加工硅样品的表面形貌。图6示出了在不同加工取向和总加工深度下,使用pmma延性层获得的加工硅样品的表面形貌。详细描述本说明书中提到的脆性材料是指具有高达10mpa√m的断裂韧性(kic)的材料,断裂韧性即材料抗裂纹扩展的能力。某些特别感兴趣的材料具有高达5mpa√m或甚至高达3mpa√m的断裂韧性(kic)。本说明书中提到的延性材料是指具有在50mm内为5%或更大的伸长率的材料(即,当样品受到应变时,50mm样品的长度可以容许增加的百分比)。某些特别感兴趣的材料在50mm内具有10%或更大或者甚至25%或更大的伸长率。当材料被描述为金属元素(例如铜)的合金时,其旨在意味着该合金包括该金属元素。这可能意味着按重量计合金包含超过50%的指定金属元素。可用于执行本发明的方法的示例性铣削机器包括:nanowaremts5r、minitechmini-mill/gx、kernevo和kugler3/5x。贯穿本说明书的描述和权利要求,词语“包括”和“包含”及其变化形式意指“包括但不限于”,并且其不旨在(并且不)排除其他成分、添加物、部件、整数或步骤。贯穿本说明书的描述和权利要求,单数涵盖复数,除非上下文另外要求。特别地,在使用不定冠词的情况下,应当理解本说明书预期多个以及单个,除非上下文另外要求。结合本发明的特定方面、实施方案或示例所描述的特征、整数、特性、化合物、化学成分或组应当理解为可适用于本文描述的任何其他方面、实施方案或示例,除非与该方面、实施方案或示例不相容。在本说明书中公开的所有特征(包括任何附随的权利要求、摘要和附图)和/或这样公开的任何方法或过程的所有步骤可以以任何组合来组合,除此类特征和/或步骤中的至少某些相互排斥的组合外。本发明并不被任何前述实施方案的细节限制。本发明扩展至在本说明书中公开的特征的任何新颖特征或任何新颖组合(包括任何附随的权利要求、摘要和附图),或这样公开的任何方法或过程的步骤的任何新颖的步骤或任何新颖的组合。请读者注意,与本说明书同时提交或在此之前提交的与本申请有关的、并且与本说明书一起向公众开放供查阅的所有论文和文献以及所有此类论文和文献的内容通过引用并入本文。示例1:减少边缘碎裂的初步研究实验方法边缘碎裂减少策略的概述减少边缘碎裂的产生在硅微铣削中很重要。碎裂的存在可能导致功能性失效,因为边缘碎裂是由表面微点蚀和开裂形成的。发明人已经将延性材料沉积到硅的顶表面上,以减少加工过程中的边缘开裂。这可能有助于创造一种能量缓冲物,该能量缓冲物吸收接触期间切削工具和工件表面之间的冲击能量。预计其他脆性材料也会观察到类似的结果。选择延性材料,诸如铜和丙烯酸基涂料。这两种材料可以容易地涂到硅上。图1示出了示例性边缘碎裂减少方法的示意图,示出了本发明方法中的各种处理阶段。在加工之前,将厚度约为90μm的铜或丙烯酸基涂料层分别电镀或作为乳胶涂料手工涂覆到(001)表面硅晶片的表面上(步骤1)。对于硅工件上的铜,使用大约50nm厚的薄钛片(未示出)将铜粘附到硅表面上,以防止任何分层。在完成相应的表面延性层涂覆工艺后,在每个工件的表面上进行槽铣削以形成通道(步骤2)。加工在延性层上开始,并继续进入硅衬底中(步骤3)。铣削过程期间不断监控切削力。当切削工具的深度到达延性层和硅之间的界面时,注意到切削力发生了微小的变化。有了这种现象,就确定了硅衬底表面的位置,且这标志着用于确定要铣削到硅中的通道的深度的起点。最后,使用硝酸或氢氟酸溶液去除电镀铜层和钛粘合剂层,同时在加工后使用丙酮去除丙烯酸基涂料(步骤4和5)。加工系统的设置上述实验是在图2所示的纳米波mts5r微铣削系统上进行的。其包括进给精度为0.1μm的三轴运动平台、空气轴承主轴、工件夹具和kistler测力计。主轴上装有直径为0.5mm的具有单出屑槽的单晶金刚石端铣刀。主轴沿着运动平台的z轴(垂直于脆性材料的表面)安装。此外,运动平台沿x轴或y轴(平行于脆性材料表面)的移动驱动工件夹具和用于在加工过程中测量切削力的测力计。实验程序获得良好加工质量的条件包括选择主要加工参数,即通道深度、进给速度和主轴速度、工具旋转方向(即逆铣或顺铣,其中铣刀的主轴分别沿与接触脆性材料的切削刃相同或相反的方向移动)。优选在{100}表面硅晶片上沿<100>方向加工。这是因为<100>方向与其他取向相比具有更高的断裂韧性。表1示出了针对下面描述的比较示例的最佳范围以及还有所采用的加工参数。为了证明本发明的方法即使在次优条件下也可有效减少边缘碎裂,下面描述的比较示例没有使用最佳范围。表1:硅微铣削研究的加工条件对具有延性层的两个工件进行加工,以获得几个不同深度的通道,深度范围在30μm至150μm之间。为了比较,还对未涂覆的硅工件进行了类似的加工。上面提到的通道深度是指从加工通道的基部到硅表面的距离。对于涂覆的工件,加工在铜或聚合物表面上开始,并继续进入硅衬底中。铣削过程期间不断监控切削力。当切削工具的深度到达延性材料和硅之间的界面层时,注意到切削力发生了微小的变化。因此,硅衬底表面的位置被确定,并且这标志着用于确定要铣削到硅中的通道的深度的起点。加工后,将各个工件从接地金属背衬拆下,利用丙酮并通过暴露于超声波水浴来清洗。例如,使用硝酸和氢氟酸溶液从涂覆铜的工件去除沉积的铜和钛粘合剂片。丙酮清洗掉从涂有涂料的工件去除丙烯酸涂料。最后,使用台式日立tm3030sem系统对最终加工表面上产生的边缘碎裂的规模进行定量和定性表征。结果与讨论图3示出了三个硅工件上的最终加工表面的sem图像:i)在加工过程中已经在钛粘合剂层上涂覆有铜延性材料的工件;ii)在加工过程中没有涂覆延性材料的工件;和iii)在加工过程中已经涂覆有丙烯酸涂料(pmma)延性层的工件。可以测量的边缘碎裂量是平均长度。该测量在每个加工轮廓的扫描电子显微镜(sem)图像上进行的。在每个加工轮廓的逆铣侧上进行测量。通过沿加工通道的竖直图像视图在碎裂表面上50个等距数据点上取平均长度测量值来定量表征边缘碎裂。结果在表2中提供。表2:针对铣削涂覆有铜/粘合剂的硅和涂覆有丙烯酸的硅的边缘碎裂的平均长度因此,对于丙烯酸涂料和铜/钛粘合剂系统两者,在50μm的通道深度下观察到没有边缘碎裂。相比之下,对于30μm和50μm深的通道而言,没有延性层的硅在加工过程中表现出大量的边缘碎裂。此外,对于100μm深的通道,用丙烯酸基涂料层加工过的硅工件产生的边缘碎裂明显小于用铜涂层和钛粘合剂层加工过的工件。示例2–减少边缘碎裂的进一步研究在进一步的可加工性研究中,将涂覆铜的硅样品(如示例1中那样将铜电镀到硅上)与涂覆pmma和su-8的硅样品一起加工,并与未涂覆的硅样品进行比较。在这项研究中,pmma和su-8都旋涂到硅上。分别用单晶金刚石(scd)和涂覆tialn的工具进行加工。图4描绘了不同牺牲材料和切削工具的能力的比较。在这种150μm的深的加工深度下,从图4中可以明显看出,当用scd和pmma或su-8一起作为牺牲层加工时,可以获得最小的边缘碎裂和表面缺陷。涂层厚度在20μm至80μm之间变化。图5示出了先前沉积有不同涂层厚度的涂覆有pmma的硅的加工后(post-machined)的微沟槽的表面形貌。同样明显的是,在表面边缘被牺牲层材料保护的情况下,随着涂层厚度的增加,产生的边缘碎裂的尺寸变化最小。先前的工作已经表明,硅在加工时的取向会影响边缘碎裂的量。图6示出了在不同加工取向下在不同的总加工深度下,加工后的硅微沟槽的表面形貌。事实上,在不同的加工取向和总加工深度下观察到最小的边缘碎裂变化和产生。此外,在由单晶金刚石(scd)工具和涂覆tialn的工具加工的沟槽下也观察到了类似的特性,尽管scd工具被证明比tialn工具好得多。此研究的结果在表3中定量化地总结。表3:对经scd工具和涂覆tialn的工具加工的各种工件所测量的边缘碎裂长度示例3-粘附功有无数种方法来测量涂层的粘附强度,或者在该上下文的特定情况下,测量延性牺牲材料和脆性衬底材料之间的粘附强度。在一种方法中,通过测量表面润湿性定量表征粘附强度。润湿性,通常定义为一种流体在其他不混溶流体存在下扩散或粘附到固体表面的趋势。这种测量可以通过称为接触角测量的过程进行。该过程涉及将液滴沉积到感兴趣的表面上,同时使用测角仪测量液滴沿该表面扩散时液滴的接触角。在这样的研究中通常使用至少两种具有已知表面张力的液体。在当前的研究中,选择去离子水(di-h2o)和100%甘油。在带有钛种子层的铜(copperwithtitaniumseedlayer)(cu/ti)、pmma、su-8和单晶硅衬底的表面上分别进行了测量。在获得关于每个测试表面的相关接触角后,分别表示分离两个表面所需功和粘附强度的粘附功和界面张力均可通过调和平均数模型计算,如下所示:调和平均数模型用于近似低能量相与界面能的极性和非极性部分的相互作用,且从而评估粘附功wls:其中:→层表面张力的非极性部分→层表面张力的极性部分→衬底表面张力的非极性部分→衬底表面张力的极性部分此外,在空气环境中将液体层与固体衬底分离所需的粘附功也可以通过dupre等式推导出来:wls=(1+cosθ)γl(2)其中:θ→测量的液体层和固体衬底之间的接触角γl→包括非极性部分和极性部分的总的层表面张力两种材料的接触角可以分别用去离子水(di-h2o)和甘油测量。取多个数据点,并确定这些数据点上的平均接触角。因此,在去离子水和甘油条件下,分别确定了铜-钛种子层、pmma、su-8和硅表面的平均接触角。然后,使用等式1和2计算空气环境中的粘附功和界面张力。表3、表4和表5分别示出了平均接触角、计算的每种材料的表面张力和计算的粘附功以及界面张力。表5提供了su-8、pmma和铜的计算的粘附功。这种现象证实了研究中所使用的su-8的机械性能优于pmma和铜两者。表4:测量的接触角的平均值表5:计算的每种材料的表面张力表6:计算的空气环境中的粘附功和界面张力。接触中的材料粘附功(mj/m2)界面张力(mj/m2)铜/钛在硅上73.37.1pmma在硅上77.56.2su-8在硅上84.96.1当前第1页12