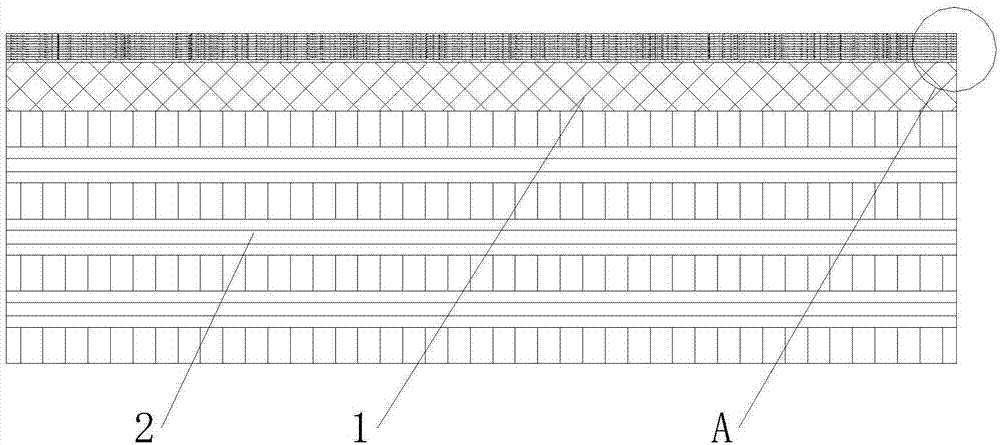
本发明涉及一种地热实木复合地板及加工工艺,特别是一种防开裂地热实木复合地板及加工工艺。
背景技术:
:随着人们消费水平和经济能力的提升,由基板和面板胶合而成的地采暖用实木复合地板由于其具有结构强度高、尺寸稳定性好的特点,越来越广泛的被人们所使用。但由于地暖地板在使用中会受到外界环境和地暖的持续高温影响,导致地板面板的含水率下降并引起收缩,从而造成面板的开裂现象,降低了地板的工作稳定性和使用寿命。并且当地板面层出现开裂问题后,还会造成表面的防水和耐磨漆层受到其干缩应力的影响,引起自身的开裂问题;使漆层不仅无法对面板的开裂起到有效的保护和防范作用,还会随开裂进一步降低对面板的防水和耐磨性能,使面板更加容易受到外界环境的影响加剧裂纹,进一步缩短了地板的使用寿命。因此,现有的地热实木复合地板存在面板和漆层容易开裂,使用寿命短的问题。技术实现要素:本发明的目的在于,提供一种防开裂地热实木复合地板及加工工艺。它具有面板和漆层不易开裂,使用寿命长的特点。本发明的技术方案:一种防开裂地热实木复合地板,包括孪叶苏木材质的面板,面板为径向板,面板底部依次设有由多块芯板依次胶合而成的基板,面板顶部由内到外依次设有水性附着剂层、第一底漆层、第二底漆层、第三底漆层、第四底漆层、第五底漆层、第六底漆层、第一面漆层、第七底漆层、第二面漆层和第三面漆层。前述的一种防开裂地热实木复合地板中,所述面板的含水率为7~10%,面板的厚度为0.6mm,所述基板为桉杂木板,基板的厚度为12~18mm,基板的含水率为10~12%。前述的一种防开裂地热实木复合地板中,所述水性附着剂层为hzs-902水性附着剂层,水性附着剂层的涂布量为25~30g/m2;所述第一底漆层为m-8001木质附着底漆层,第一底漆层的涂布量为20~25g/m2;第二底漆层、第三底漆层和第六底漆层为gm-606a晶莹底漆层,gm-606a晶莹底漆层的涂布量为25~30g/m2;第四底漆层为n-6001玻纤耐磨底漆层,第四底漆层的涂布量为30~35g/m2;第五底漆层为ym-505c软质底漆层,第五底漆层的涂布量为25~30g/m2;第七底漆层为gm-606b质透砂光底漆层,第七底漆层的涂布量为15~20g/m2;第一面漆层为c-7006超薄面漆层,第一面漆层的涂布量为70~80g/m2;第二面漆层为hzs-601b晶刚面漆层,第二面漆层的涂布量为8~10g/m2;第三面漆层为m-808原木哑光面漆层,第三面漆层的涂布量为6~8g/m2。前述的一种防开裂地热实木复合地板的加工工艺,包括以下步骤:①先将多层基板通过热压形成胶合板,再对胶合板的表面进行砂光,得a胶合板;②将面板和a胶合板通过热压形成复合板,得b复合板;③对b复合板的面板表面涂覆水性附着剂,然后经红外线干燥,得c复合板;④对c复合板的表面依次涂覆第一底漆、第二底漆和第三底漆,每次底漆涂覆后通过uv固化,得d复合板;⑤对d复合板的表面进行砂光后依次涂覆第四底漆、第五底漆和第六底漆,每次底漆涂覆后通过uv固化,得e复合板;⑥对e复合板的表面进行砂光后依次涂覆第一面漆和第七底漆,每次底漆或面漆涂覆后通过uv固化,得f复合板;⑦对f复合板的表面进行砂光后依次涂覆第二面漆和第三面漆,每次面漆涂覆后通过uv固化,得成品地板。前述的一种防开裂地热实木复合地板的加工工艺中,所述步骤①和步骤②中的热压温度为100~120℃,热压时间为4~8分钟,热压压力为1~1.2mpa,涂胶量为240~280g/m2。前述的一种防开裂地热实木复合地板的加工工艺中,所述步骤⑤和步骤⑥中砂光时所用的砂纸型号为240#,步骤⑦中砂光时所用的砂纸型号为320#。前述的一种防开裂地热实木复合地板的加工工艺中,所述步骤④的具体步骤为:将c复合板的表面涂覆第一底漆后放入双灯uv干燥机中双灯干燥,再涂覆第二底漆后放入双灯uv干燥机中半灯干燥,再涂覆第三底漆后放入双灯uv干燥机中一灯半干燥,得d复合板。前述的一种防开裂地热实木复合地板的加工工艺中,所述步骤⑤的具体步骤为:对d复合板的表面进行砂光后涂覆第四底漆,然后放入双灯uv干燥机中一灯干燥,再涂覆第五底漆后放入双灯uv干燥机中一灯干燥,再涂覆第六底漆后放入双灯uv干燥机中一灯干燥,得e复合板。前述的一种防开裂地热实木复合地板的加工工艺中,所述步骤⑥的具体步骤为:对e复合板的表面进行砂光后涂覆第一面漆,然后放入双灯uv干燥机中一灯干燥,再涂覆第七底漆后放入双灯uv干燥机中一灯半干燥,得f复合板。前述的一种防开裂地热实木复合地板的加工工艺中,所述步骤⑦的具体步骤为:对f复合板的表面进行砂光后涂覆第二面漆,然后放入双灯uv干燥机中一灯干燥,再涂覆第三面漆后放入四灯uv干燥机中四灯干燥,得成品地板。与现有技术相比,本发明通过将径向剖面的孪叶苏木板作为面板,孪叶苏木自身为散孔材质,密度较小,其单板的径向强度大于弦向强度,使面板在使用时的径向干缩系数较小、径向横纹抗拉强度大,从而有效减少面板和基板胶合后因无法自由收缩产生的干缩应力,减少裂纹的产生;通过面板厚度和含水率的设置,使面板在不同的外界环境中均能够有良好的工作稳定性,并且通过对面板厚度的降低可以使树脂和油漆进入木材自身的空隙中,从而降低面板的收缩空间,进一步防止开裂的问题;通过第二底漆层、第三底漆层、第六底漆层和第七底漆层的配合,可以使漆层整体具有良好的柔韧性和砂光性,从而使各漆层在依次涂覆时能够保持漆面的平整,提高漆层的粘附效果,而通过漆层的柔韧性能够有效缓冲或抵消面板微裂时产生的应力,避免裂纹的产生;第一底漆层和水性附着剂具有良好的附着性,使后续漆层在涂覆后能够和面板保持紧密结合,进一步提高了漆层对面板在开裂时起到的保护效果;通过第四底漆层、第五底漆层和第二面漆层的配合,可以提高漆层整体的硬度、耐刮擦性和耐磨性,从而保持漆层在使用时的完整性并防止外界对面板的刮擦;漆层的完整性提高后还可以进一步提高对地板的保护效果,从而避免地暖地板所在的高温低湿环境对地板含水率造成的影响,进一步降低地板的开裂。在加工过程中,本发明根据面板和基板的材质和尺寸优化了相应的工艺参数,使热压工艺在保证地板胶合强度的同时能够降低其热压温度和热压时间,从而使面板在热压过程中的含水率下降幅度降低,使面板在热压时能够保持合适的含水率范围,进一步防止开裂的问题;本发明还根据漆层的具体型号和涂布量设置了相应的干燥工艺,从而使各漆层之间能够保持紧密粘合并提高对地板的保护效果,进一步降低了面板开裂的可能性。所以,本发明具有面板和漆层不易开裂,使用寿命长的特点。附图说明图1是本发明的结构示意图;图2是图1的a向放大图。附图中的标记为:1-面板,2-基板,3-水性附着剂层,4-第一底漆层,5-第二底漆层,6-第三底漆层,7-第四底漆层,8-第五底漆层,9-第六底漆层,10-第一面漆层,11-第七底漆层,12-第二面漆层,13-第三面漆层。具体实施方式下面结合附图和实施例对本发明作进一步的说明,但并不作为对本发明限制的依据。实施例1。一种防开裂地热实木复合地板,构成如图1所示,包括孪叶苏木材质的面板1,面板1为径向板(径向板为木板在裁切时的长度方向指向树干中心),面板1底部依次设有由多块芯板依次胶合而成的基板2,面板1顶部由内到外依次设有水性附着剂层3、第一底漆层4、第二底漆层5、第三底漆层6、第四底漆层7、第五底漆层8、第六底漆层9、第一面漆层10、第七底漆层11、第二面漆层12和第三面漆层13。所述面板1的含水率为7~10%,面板1的厚度为0.6mm,所述基板2为桉杂木板,基板2的厚度为12~18mm,基板2的含水率为10~12%。所述水性附着剂层3为hzs-902水性附着剂层,水性附着剂层3的涂布量为25~30g/m2;所述第一底漆层4为m-8001木质附着底漆层,第一底漆层4的涂布量为20~25g/m2;第二底漆层5、第三底漆层6和第六底漆层9为gm-606a晶莹底漆层,gm-606a晶莹底漆层的涂布量为25~30g/m2;第四底漆层7为n-6001玻纤耐磨底漆层,第四底漆层7的涂布量为30~35g/m2;第五底漆层8为ym-505c软质底漆层,第五底漆层8的涂布量为25~30g/m2;第七底漆层11为gm-606b质透砂光底漆层,第七底漆层11的涂布量为15~20g/m2;第一面漆层10为c-7006超薄面漆层,第一面漆层10的涂布量为70~80g/m2;第二面漆层12为hzs-601b晶刚面漆层,第二面漆层12的涂布量为8~10g/m2;第三面漆层13为m-808原木哑光面漆层,第三面漆层13的涂布量为6~8g/m2;所述水性附着剂层、底漆层和面漆层的型号均为鹤山市创享科技有限公司在市面上的销售型号。所述一种防开裂地热实木复合地板的加工工艺,包括以下步骤:①先将多层基板通过热压形成胶合板,再对胶合板的表面进行砂光,得a胶合板;②将面板和a胶合板通过热压形成复合板,得b复合板;③对b复合板的面板表面涂覆水性附着剂,然后经12米红外线在80~120℃环境下干燥,得c复合板;④将c复合板的表面涂覆第一底漆后放入5kw的双灯uv干燥机中双灯干燥至8分干(干燥程度为80%),再涂覆第二底漆后放入双灯uv干燥机中半灯干燥至5~6分干,再涂覆第三底漆后放入双灯uv干燥机中一灯半干燥至8~9分干,得d复合板;⑤对d复合板的表面进行砂光后涂覆第四底漆,然后放入双灯uv干燥机中一灯干燥至7~8分干,再涂覆第五底漆后放入双灯uv干燥机中一灯干燥至6~7分干,再涂覆第六底漆后放入双灯uv干燥机中一灯干燥至至8~9分干,得e复合板;⑥对e复合板的表面进行砂光后涂覆第一面漆,然后放入双灯uv干燥机中一灯干燥至7~8分干,再涂覆第七底漆后放入双灯uv干燥机中一灯半干燥至8~9分干,得f复合板;⑦对f复合板的表面进行砂光后涂覆第二面漆,然后放入双灯uv干燥机中一灯干燥至6~7分干,再涂覆第三面漆后放入四灯uv干燥机中四灯干燥至完全干燥,得成品地板。所述步骤①和步骤②中的热压温度为100~120℃,热压时间为4~8分钟,热压压力为1~1.2mpa,涂胶量为240~280g/m2。所述步骤⑤和步骤⑥中砂光时所用的砂纸型号为240#,步骤⑦中砂光时所用的砂纸型号为320#。所述第一面漆层10在涂覆时通过淋涂机进行喷涂,其他底漆层和面漆层均用辊涂机进行辊涂。本发明的工作原理:本发明通过对面板的材质、厚度和纹理方向的优化,可以有效降低面板在作为地暖地板使用过程中的开裂现象;通过对地板在热压时工艺参数的设置,可以在保证面板和基板胶合强度的同时降低热压所需的时间和温度,从而减少面板在热压时造成的含水率消耗,使加工完成后的面板在作为地暖地板使用中能够拥有合适的含水率范围,进一步防止因含水率的降低造成面板干缩产生的开裂,提高面板的工作稳定性。本发明通过面板表面不同漆层的配合,可以有效克服常规耐磨漆面柔性较差的特点,增加了漆层整体的柔韧性,使漆层可以有效缓冲或抵消面板微裂时产生的应力和具有良好的完整性,从而保护面板在微裂时免受外界环境的持续影响,使面板的含水率能够长期稳定的保持在适宜的范围内,从而通过减少面板的干缩幅度来降低面板的开裂现象。实施例2。一种防开裂地热实木复合地板,包括孪叶苏木材质的面板1,面板1为径向板,面板1底部依次设有由11块芯板依次胶合而成的基板2,每块芯板的厚度相同,相邻芯板的纹理方向按横纹和纵纹相互交替设置,面板1顶部由内到外依次设有水性附着剂层3、第一底漆层4、第二底漆层5、第三底漆层6、第四底漆层7、第五底漆层8、第六底漆层9、第一面漆层10、第七底漆层11、第二面漆层12和第三面漆层13。所述面板1的含水率为7%,面板1的厚度为0.6mm,所述基板2为桉杂木板,基板2的厚度为12mm,基板2的含水率为10%。所述水性附着剂层3为hzs-902水性附着剂层(鹤山市创享科技有限公司),水性附着剂层3的涂布量为25g/m2;所述第一底漆层4为m-8001木质附着底漆层,第一底漆层4的涂布量为20g/m2;第二底漆层5、第三底漆层6和第六底漆层9为gm-606a晶莹底漆层,gm-606a晶莹底漆层的涂布量为25g/m2;第四底漆层7为n-6001玻纤耐磨底漆层,第四底漆层7的涂布量为30g/m2;第五底漆层8为ym-505c软质底漆层,第五底漆层8的涂布量为25g/m2;第七底漆层11为gm-606b质透砂光底漆层,第七底漆层11的涂布量为15g/m2;第一面漆层10为c-7006超薄面漆层,第一面漆层10的涂布量为70g/m2;第二面漆层12为hzs-601b晶刚面漆层,第二面漆层12的涂布量为8g/m2;第三面漆层13为m-808原木哑光面漆层,第三面漆层13的涂布量为6g/m2。所述一种防开裂地热实木复合地板的加工工艺,包括以下步骤:①先将多层基板通过热压形成胶合板,热压时所用的热压温度为110℃,热压时间为6分钟,热压压力为1.1mpa,相邻基板之间的胶粘剂涂胶量为260g/m2;热压完成后再对胶合板的表面进行砂光,得a胶合板;②将面板和a胶合板通过热压形成复合板,面板在热压前的含水率为9%,热压时所用的热压温度为110℃,热压时间为6分钟,热压压力为1.1mpa,面板和a胶合板之间的胶粘剂涂胶量为260g/m2,得b复合板;③对b复合板的面板表面涂覆水性附着剂,然后经12米红外线在80℃环境下干燥,得c复合板;④将c复合板的表面涂覆第一底漆后放入5kw的双灯uv干燥机中双灯干燥至8分干,再涂覆第二底漆后放入双灯uv干燥机中半灯干燥至5~6分干,再涂覆第三底漆后放入双灯uv干燥机中一灯半干燥至8~9分干,得d复合板;⑤对d复合板的表面进行砂光后涂覆第四底漆,砂光时所用的砂纸型号为240#,然后放入双灯uv干燥机中一灯干燥至7~8分干,再涂覆第五底漆后放入双灯uv干燥机中一灯干燥至6~7分干,再涂覆第六底漆后放入双灯uv干燥机中一灯干燥至8~9分干,得e复合板;⑥对e复合板的表面进行砂光后涂覆第一面漆,砂光时所用的砂纸型号为240#,然后放入双灯uv干燥机中一灯干燥至7~8分干,再涂覆第七底漆后放入双灯uv干燥机中一灯半干燥至8~9分干,得f复合板;⑦对f复合板的表面进行砂光后涂覆第二面漆,砂光时所用的砂纸型号为320#,然后放入双灯uv干燥机中一灯干燥至6~7分干,再涂覆第三面漆后放入四灯uv干燥机中四灯干燥至完全干燥,得成品地板。本实施例根据市场需求限定了基板2和面板1的具体结构和相应尺寸,并根据该尺寸结构进一步优化了相应的工艺参数,使面板能够在保持自身结构稳定性的同时降低地板的整体厚度,从而提高了本实施例的适用范围。实施例3。一种防开裂地热实木复合地板,包括孪叶苏木材质的面板1,面板1为径向板,面板1底部依次设有由11块芯板依次胶合而成的基板2,每块芯板的厚度相同,相邻芯板的纹理方向按横纹和纵纹相互交替设置,面板1顶部由内到外依次设有水性附着剂层3、第一底漆层4、第二底漆层5、第三底漆层6、第四底漆层7、第五底漆层8、第六底漆层9、第一面漆层10、第七底漆层11、第二面漆层12和第三面漆层13。所述面板1的含水率为10%,面板1的厚度为0.6mm,所述基板2为桉杂木板,基板2的厚度为18mm,基板2的含水率为12%。所述水性附着剂层3为hzs-902水性附着剂层(鹤山市创享科技有限公司),水性附着剂层3的涂布量为30g/m2;所述第一底漆层4为m-8001木质附着底漆层,第一底漆层4的涂布量为25g/m2;第二底漆层5、第三底漆层6和第六底漆层9为gm-606a晶莹底漆层,gm-606a晶莹底漆层的涂布量为30g/m2;第四底漆层7为n-6001玻纤耐磨底漆层,第四底漆层7的涂布量为35g/m2;第五底漆层8为ym-505c软质底漆层,第五底漆层8的涂布量为30g/m2;第七底漆层11为gm-606b质透砂光底漆层,第七底漆层11的涂布量为20g/m2;第一面漆层10为c-7006超薄面漆层,第一面漆层10的涂布量为80g/m2;第二面漆层12为hzs-601b晶刚面漆层,第二面漆层12的涂布量为10g/m2;第三面漆层13为m-808原木哑光面漆层,第三面漆层13的涂布量为8g/m2。所述一种防开裂地热实木复合地板的加工工艺,包括以下步骤:①先将多层基板通过热压形成胶合板,热压时所用的热压温度为110℃,热压时间为6分钟,热压压力为1.1mpa,相邻基板之间的胶粘剂涂胶量为260g/m2;热压完成后再对胶合板的表面进行砂光,得a胶合板;②将面板和a胶合板通过热压形成复合板,面板在热压前的含水率为12%,热压时所用的热压温度为110℃,热压时间为6分钟,热压压力为1.1mpa,面板和a胶合板之间的胶粘剂涂胶量为260g/m2,得b复合板;③对b复合板的面板表面涂覆水性附着剂,然后经12米红外线在120℃环境下干燥,得c复合板;④将c复合板的表面涂覆第一底漆后放入双灯uv干燥机中双灯干燥至8分干,再涂覆第二底漆后放入双灯uv干燥机中半灯干燥至5~6分干,再涂覆第三底漆后放入双灯uv干燥机中一灯半干燥至8~9分干,得d复合板;⑤对d复合板的表面进行砂光后涂覆第四底漆,砂光时所用的砂纸型号为240#,然后放入双灯uv干燥机中一灯干燥至7~8分干,再涂覆第五底漆后放入双灯uv干燥机中一灯干燥至6~7分干,再涂覆第六底漆后放入双灯uv干燥机中一灯干燥至8~9分干,得e复合板;⑥对e复合板的表面进行砂光后涂覆第一面漆,砂光时所用的砂纸型号为240#,然后放入双灯uv干燥机中一灯干燥至7~8分干,再涂覆第七底漆后放入双灯uv干燥机中一灯半干燥至8~9分干,得f复合板;⑦对f复合板的表面进行砂光后涂覆第二面漆,砂光时所用的砂纸型号为320#,然后放入双灯uv干燥机中一灯干燥至6~7分干,再涂覆第三面漆后放入四灯uv干燥机中四灯干燥至完全干燥,得成品地板。本实施例根据市场需求限定了基板2和面板1的具体结构和相应尺寸,并根据该尺寸结构进一步优化了相应的工艺参数,使地板整体能够进一步提高自身的结构强度和防开裂效果。实施例4。一种防开裂地热实木复合地板,包括孪叶苏木材质的面板1,面板1为径向板,面板1底部依次设有由11块芯板依次胶合而成的基板2,每块芯板的厚度相同,相邻芯板的纹理方向按横纹和纵纹相互交替设置,面板1顶部由内到外依次设有水性附着剂层3、第一底漆层4、第二底漆层5、第三底漆层6、第四底漆层7、第五底漆层8、第六底漆层9、第一面漆层10、第七底漆层11、第二面漆层12和第三面漆层13。所述面板1的含水率为8%,面板1的厚度为0.6mm,所述基板2为桉杂木板,基板2的厚度为15mm,基板2的含水率为11%。所述水性附着剂层3为hzs-902水性附着剂层(鹤山市创享科技有限公司),水性附着剂层3的涂布量为25g/m2;所述第一底漆层4为m-8001木质附着底漆层,第一底漆层4的涂布量为20g/m2;第二底漆层5、第三底漆层6和第六底漆层9为gm-606a晶莹底漆层,第二底漆层5的涂布量为25g/m2,第三底漆层6的涂布量为30g/m2,第六底漆层9的涂布量为30g/m2;第四底漆层7为n-6001玻纤耐磨底漆层,第四底漆层7的涂布量为30g/m2;第五底漆层8为ym-505c软质底漆层,第五底漆层8的涂布量为25g/m2;第七底漆层11为gm-606b质透砂光底漆层,第七底漆层11的涂布量为15g/m2;第一面漆层10为c-7006超薄面漆层,第一面漆层10的涂布量为80g/m2;第二面漆层12为hzs-601b晶刚面漆层,第二面漆层12的涂布量为8g/m2;第三面漆层13为m-808原木哑光面漆层,第三面漆层13的涂布量为6g/m2。所述一种防开裂地热实木复合地板的加工工艺,包括以下步骤:①先将多层基板通过热压形成胶合板,热压时所用的热压温度为110℃,热压时间为6分钟,热压压力为1.1mpa,相邻基板之间的胶粘剂涂胶量为260g/m2;热压完成后再对胶合板的表面进行砂光,得a胶合板;②将面板和a胶合板通过热压形成复合板,面板在热压前的含水率为10%,热压时所用的热压温度为110℃,热压时间为6分钟,热压压力为1.1mpa,面板和a胶合板之间的胶粘剂涂胶量为260g/m2,得b复合板;③对b复合板的面板表面涂覆水性附着剂,然后经12米红外线在120℃环境下干燥,得c复合板;④将c复合板的表面涂覆第一底漆后放入双灯uv干燥机中双灯干燥至8分干,再涂覆第二底漆后放入双灯uv干燥机中半灯干燥至5~6分干,再涂覆第三底漆后放入双灯uv干燥机中一灯半干燥至8~9分干,得d复合板;⑤对d复合板的表面进行砂光后涂覆第四底漆,砂光时所用的砂纸型号为240#,然后放入双灯uv干燥机中一灯干燥至7~8分干,再涂覆第五底漆后放入双灯uv干燥机中一灯干燥至6~7分干,再涂覆第六底漆后放入双灯uv干燥机中一灯干燥至8~9分干,得e复合板;⑥对e复合板的表面进行砂光后涂覆第一面漆,砂光时所用的砂纸型号为240#,然后放入双灯uv干燥机中一灯干燥至7~8分干,再涂覆第七底漆后放入双灯uv干燥机中一灯半干燥至8~9分干,得f复合板;⑦对f复合板的表面进行砂光后涂覆第二面漆,砂光时所用的砂纸型号为320#,然后放入双灯uv干燥机中一灯干燥至6~7分干,再涂覆第三面漆后放入四灯uv干燥机中四灯干燥至完全干燥,得成品地板。本实施例对基板2和面板1的尺寸结构做了进一步限定,并根据该尺寸结构进一步优化了相应的工艺参数,使复合地板的整体尺寸与其对结构强度和防开裂效果的提升达到最佳。实验例1:根据gb/t1923-2009《木材干缩性测定方法》对6份孪叶苏木单板进行干缩测试,其单板干缩系数的计算公式为k=y/m,其中y-%为试件在含水率9%至绝干时的干缩率,m-%为试件的干缩率;单板差异干缩率的计算公式为d=k弦/k径,其中k弦-%为试件弦向干缩系数,k径-%为试件径向干缩系数。结果如表1所示:表1木材干缩系数由表1数据可知,孪叶苏木单板的径向干缩系数小于弦向干缩系数,径向干缩系数范围在0.17~0.19%,弦向干缩系数范围0.35~0.4%。弦向与径向差异干缩率在2倍左右。因此,通过将剖面为径切面的孪叶苏木单板作为本发明的面板可以有效降低面板因含水率变化产生的干缩效果,从而降低了面板开裂的可能性。实验例2:使用万能力学试验机根据ly/t2879-2017《装饰微薄木》中的单板横向抗拉强度测试方法对12份孪叶苏木单板试件进行测试,设备力值范围为100n。12份试件中6份试件的单板方向为径向,6份试件的单板方向为弦向;12份试件的单板厚度均为0.6mm,含水率均为9%。结果如表2所示:表2单板横向抗拉强度由表2数据可知,单板径向抗拉强度明显大于弦向抗拉强度,其径向强度是弦向的1.8倍。因此,将径向板作为面板可以有效避免面板在干缩时,基板因相互胶合产生的干缩应力造成面板的开裂,从而进一步降低面板开裂的可能性。实验例3:分别将6组面板和基板样品通过热压压合形成胶合板,其中面板为0.6mm的孪叶苏木单板,含水率为10%;基板为桉杂材质的实木复合地板用胶合板。热压时的热压温度为110℃,热压时间为6分钟,热压压力为1.1mpa,面板和基板之间的胶粘剂涂胶量为260g/m2。然后通过针式含水率测试仪分别对压合前后的每组面板测试6个点的含水率,取平均值。测试结果如表3所示:表3热压过程表板含水率变化单位:%样品1样品2样品3样品4样品5样品6面板(原材料)10.210.510.29.89.810.2面板(成品)8.58.68.28.08.18.3由表3数据可知,热压前后面板的含水率变化明显,热压后的面板含水率降低2%。然后分别将6组压合后的样品作为地暖地板进行测试,测试过程中地暖循环水的温度为50℃,室内温度为23℃,湿度为50%,测试时间为10天。然后通过针式含水率测试仪分别对测试前后的每组面板测试6个点的含水率,取平均值。测试结果如表4所示:表4地热环境中表板含水率变化单位:%样品1样品2样品3样品4样品5样品6面板(成品)8.58.68.28.08.18.3面板(地热环境)6.56.87.06.26.56.8由表4数据可知,面板在地热环境中的含水率变化明显,其含水率下降2%。因此本发明根据面板在热压过程中的含水率变化和在地暖地板中的使用状态,优化了面板原料的含水率,使面板在使用过程中的含水率能够保持在6~7%,降低干缩开裂的可能性。实验例4:依据ly/t1700-2007《地采暖用木质地板》中的测试方法对本发明所述的防开裂地热实木复合地板进行耐热尺寸稳定性、耐湿尺寸稳定性、表面耐湿热性能、表面耐龟裂、表面耐冷热循环等理化项目测试。测试结果如表5所示:表5成品性能分析测试项目耐热尺寸稳定性%耐湿尺寸稳定性%甲醛释放量mg/l浸渍剥离结果0.200.120.5符合测试项目静曲强度mpa弹性模量mpa表面耐磨g/100r漆膜硬度h结果4246800.083由表5数据可知,通过对材料、漆层的设置和相应加工工艺的配合,可以使本发明所述的防开裂地热实木复合地板具有良好的尺寸稳定性、表面耐磨性和漆膜硬度。从而有效降低了本发明在使用过程中的开裂现象,提高了本发明的使用寿命。当前第1页12