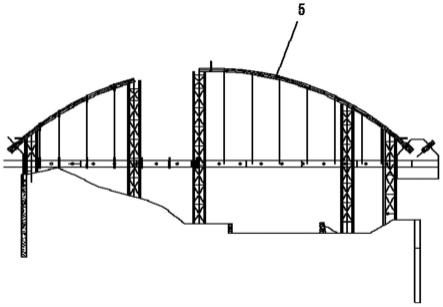
1.本发明涉及桥梁施工领域,尤其涉及一种钢管拱吊装方法。
背景技术:2.目前,倒虹吸悬架段拱肋采用钢管制作,全桥共分为12个钢管拱单元,每跨为6个拱架吊装单元(含拱脚2个),吊装节段接口处搭设钢管临时支架,配合汽车吊进行吊装,钢拱架采用从两端向中部实施逐段延伸吊装,最后在桥跨中合龙成拱方式进行,吊装工程量以及吊装难度都非常大,同时定位点精度要求也非常高,因此,合理设计的钢管拱吊装方法具有重要的意义。
技术实现要素:3.为了解决上述技术问题,本发明提供了一种钢管拱吊装方法,包括步骤:s1、设备准备。s2、吊装规划及吊前准备,具体为:(1)在钢管拱肋以单台汽车吊进行起重吊装;(2)第五段的吊装采用双台起重量差别较大的吊车进行起吊。s3、试吊。s4、钢管拱肋单元吊装,具体为:(1)对拱肋的拼接面进行标定,确定出拱肋接缝处的上下左右具体位置以保证拼接焊缝段的快速对中;(2)对于单端的固定,采用全站以进行跟踪测量,全站仪架设在单个拱肋的中心线处,控制拱肋的单端固定精度,同时通过前期预留在支架顶部的放射片、拱肋中线标识线对拱肋的平面位置进行复核,确保拱肋初步对中的误差控制在20mm以内,再通过千斤顶进行精调,确定位置后,直接将拱肋下部垫块与支架固定;(3)单跨主拱肋采取从两端向跨中对称安装,拱肋接口采用外坡口,在安装段到位后利用马板固定,实现接口对位;(4)吊装时,将吊索与钢管拱肋及吊钩通过卡环连接好,并在钢管拱肋两端系上缆风绳进行拱肋高空姿态调整;(5)在全站仪的监测下,利用已拼接段的记号和吊车的起吊实现拱肋平面位置确定,利用千斤顶进行标高精调,确保符合要求后,将定位工装与弦管焊接,用定位马板连接拱肋接口并紧固;(6)每节拱肋吊装段架设安装完成后,当架设与此相连的另一吊装段时,需要提前对已经完成的拱架节段的标高及轴线进行复测,当发生拱架吊装段轴线偏位或者标高沉降时,需要及时调整,通过使用千斤顶进行微调,直至达到安装精度要求,待调整到位并固定拱架段后,再架设与之关联的另一吊装拱肋段。s5、合龙段拱肋单元吊装。s6、拱肋接口焊接。s7、测量控制。
4.进一步地,步骤s2的(2)中,采用100t+25t汽车吊进行双机抬吊,在吊装过程中100t汽车吊的主臂高度为33米、对应的最大吊装半径为9米,25t汽车吊的主臂高度为32米、对应的最大吊装半径为9米。
5.进一步地,步骤s4的(2)中,在支架上设置反射片,通过免棱镜技术将反射片固定在支架上,以提前确定拱肋的轴线,在管肋吊装过程中,通过免棱镜放样确定管肋的水平位置和高程,施工中,将拱肋的中线标记、测量点位和支架点位3个测量点进行相互复核。
6.进一步地,步骤s2中,吊装前在吊装平台上把拱轴线画出,在平台上设置半弧形的拱架钢板底托,用全站仪对其位置定位和测量标高,以控制底托位置的坐标高程,每段拱架
的安装步骤为起吊、移位、就位、定位马板;逐段进行吊装,逐段焊接直至合龙段安装,分段环形焊缝的焊接,两侧吊装段在焊接时保持同步。
7.进一步地,步骤s3中,试吊前,检查各指挥信号系统是否正常;正式试吊,先进行空负荷试验,检查设备是否正常运转,正常后进行吊臂性能动负荷试验,在每次吊装前均应进行试吊,试吊块先吊离地面10~15cm后制动,作升降及旋转各一次,动作过程中检查吊机各工作机构的传动情况,再使吊物离开地面10~15cm后制动,静止10分钟,测量重物下滑量。
8.进一步地,步骤s4的(4)中,当吊车将第一段拱肋吊起到离地面约10~15cm高度,检查吊装工况,确认满足各项要求,再继续提升到安装高度,通过缆风绳配合吊车调整拱肋的空中姿态,使拱肋拼接端与已安装段对位,高端上弦管轻靠落放在临时支撑钢管柱平台上的定位工装上,再使吊钩缓缓下落,通过全站仪精测后,吊钩起升,调整定位工装位移及标高。
9.进一步地,步骤s5中,安装前,需要在实际温度时间段测量合龙段长度,经过多次测量并核对数据无误后方可进行拱肋的合龙,在与确定合龙段长度时温度较为一致的时间段内完成合龙段拱肋的切割,吊装工作。
10.进一步地,步骤s5具体的为:拱肋及吊钩通过卡环连接,并在拱肋两端分别系上缆风绳,吊车将钢拱架吊起到离地面约10~15cm时,检查吊装工况,确认满足各项要求,再继续提升到安装高度,通过缆风绳配合吊车调整拱段的空中姿态,使拱段两端基本对位后,合龙段正对安装位置时,吊车慢慢下放合龙段缓缓就位,同时控制拱架两端高程,当下降至比设计高程高出1~3cm时停止下降,通过吊钩和拱肋缺口端部的标识来调整拱肋的水平位置,使吊钩均匀下放实现拱肋接头合龙,通过千斤顶精调合龙段标高,符合要求后采用马板固定。
11.进一步地,步骤s4中,拱肋焊接根据按照顺序从低向高组织焊接,利用拼装时焊缝位置的码板作为定位板;焊接前将焊缝坡口提前打磨光洁;同时清除坡口两侧50~80mm范围内氧化皮、透迹、油污等;检查合格后进行焊接,焊缝采用手工二保焊焊接;拱肋焊缝要求双数焊工对称焊接,同时对焊接层间温度控制,确保焊缝质量满足要求,焊接完成后进行无损检测。
12.进一步地,步骤s7中,拱肋吊装前按桥梁中心线、拱轴线控制点进行放样安装支架,并进行拱轴线贯通测量,确保吊装过程中拱轴线不出现偏差,每段拱肋安装就位后,用全站仪检测拱肋轴线和标高。
13.本发明的上述技术方案具有如下优点:
14.(1)采用双台起重量差别较大的吊车进行起吊,既实现了工程的顺利吊装,又为双台起重量差别较大的汽车吊吊装总结了一定的经验,避免了双台起吊因受力不均而产生的吊车倾覆问题;
15.(2)对拱肋的拼接面进行标定,确定出拱肋接缝处的上下左右具体位置,这样保证拼接焊缝段的快速对中,保证了快速、高效的组织安装;
16.(3)对于单端的固定,采用全站以进行跟踪测量,全站仪直接架设在单个拱肋的中心线处,精确控制拱肋的单端固定精度,同时通过前期预留在支架顶部的放射片、拱肋中线标识线对拱肋的平面位置进行复核,确保拱肋初步对中的误差控制在20mm以内,再通过千斤顶进行精调,确定位置后,直接将拱肋下部垫块与支架固定,不但能提高放样的精度,也
避免了因人员在高空架立棱镜而产生的人为误差,同时也能很快的拱肋的轴线进行固定。
附图说明
17.图1为拱脚第一段和第二段吊装示意图;
18.图2为拱肋第三段和第四段吊装示意图;
19.图3为拱肋第五段吊装示意图;
20.图4为拱肋第六段合拢吊装示意图;
21.图中:1、第一段;2、第二段;3、第三段;4、第四段;5、第五段;6、第六段。
具体实施方式
22.下面结合附图和实施例,对本发明的具体实施方式作进一步详细描述。以下实施例用于说明本发明,但不用来限制本发明的范围。
23.本发明的描述中,需要理解的是,术语“中心”、“纵向”、“横向”、“上”、“下”、“前”、“后”、“左”、“右”、“竖直”、“水平”、“顶”、“底”“内”、“外”等指示的方位或位置关系为基于附图所示的方位或位置关系,仅是为了便于描述本发明和简化描述,而不是指示或暗示所指的装置或元件必须具有特定的方位、以特定的方位构造和操作,因此不能理解为对本发明的限制。此外,术语“第一”、“第二”仅用于描述目的,而不能理解为指示或暗示相对重要性。
24.在本发明的描述中,需要说明的是,除非另有明确的规定和限定,术语“安装”、“相连”、“连接”应做广义理解,例如,可以是固定连接,也可以是可拆卸连接,或一体地连接;可以是机械连接,也可以是电连接;可以是直接相连,也可以通过中间媒介间接相连,可以是两个元件内部的连通。对于本领域的普通技术人员而言,可以具体情况理解上述术语在本发明中的具体含义。
25.钢管拱吊装过程如图1~图4所示,包括第一步,拱脚第一段1和第二段2吊装;第二步,拱肋第三段3和第四段4吊装;第三步,拱肋第五段5吊装;第四步,拱肋第六段6合拢吊装。本发明提供了一种钢管拱吊装方法,包括步骤:
26.1、设备准备
27.吊装前应对汽车吊、钢丝绳、卡环等进行全面检查,在确定安全无误的情况下方可进行吊装。
28.2、吊装规划及吊前准备
29.在钢管拱肋主要以单台汽车吊进行起重吊装,第五段5的吊装具有单节重量大、吊装难度大、汽车吊吊装作业半径受限等特点,利用传统的单台起吊或双台吊车起吊(要求设备尽量同规格)无法实现或实现投入的成本将大幅度增加,采用双台起重量差别较大的吊车进行起吊,考虑到汽车吊停放在安装段落的右后侧,采用100t+25t汽车吊进行双机抬吊,在吊装过程中100t汽车吊主臂高度为33米对应最大吊装半径为9米,25t汽车吊主臂高度为32米对应最大吊装半径为9米。100t吊车主臂最大受力为22.5吨,25t吊车主臂最大受力为4.5吨,安全系数为0.8,(22.5+4.5)
×
0.8=21.6吨,大于24米长一节钢管拱重量20.5吨。实现了工程的顺利吊装,又为双台起重量差别较大的汽车吊吊装总结了一定的经验,避免了双台起吊因受力不均而产生的吊车倾覆问题。
30.吊装前,在吊装平台上把拱轴线清晰画出,在平台上设置半弧形的拱架钢板底托,
用全站仪对其位置定位和测量标高,以控制底托位置的坐标高程。每段拱架的安装步骤为:起吊
→
移位
→
就位
→
定位马板。逐段进行吊装,逐段焊接直至合龙段安装。分段环形焊缝的焊接,两侧吊装段在焊接时保持同步。
31.3、试吊
32.试吊前,由总指挥正式下令指挥人员及操作人员就位,检查各指挥信号系统是否正常;各人员汇报准备工作情况,并用信号及时通知总指挥;正式试吊,先进行空负荷试验,检查设备是否正常运转,正常后进行吊臂性能动负荷试验,在每次吊装前均应进行试吊,试吊块先吊离地面10~15cm后制动,作升降及旋转各一次,动作过程中检查吊机各工作机构的传动情况。再使吊物离开地面10~15cm后制动,静止10分钟,测量重物下滑量。
33.4、钢管拱肋单元吊装
34.单元钢管拱肋吊装到位后,现在普遍应用的技术为采用汽车吊将吊装位置的平面误差控制到50mm以内后,下放到支座上,后采用千斤顶精调,揽风绳固定。为了保证能快速、高效的组织安装,在订购钢管拱肋的过程中,已对拱肋的拼接面进行标定,确定出拱肋接缝处的上下左右具体位置,这样保证的拼接焊缝段的快速对中;其次对于单端的固定,采用全站以进行跟踪测量,全站仪直接架设在单个拱肋的中心线处,精确控制拱肋的单端固定精度,同时通过前期预留在支架顶部的放射片、拱肋中线标识线对拱肋的平面位置进行复核,确保拱肋初步对中的误差控制在20mm以内,再通过千斤顶进行精调,确定位置后,直接将拱肋下部垫块与支架固定。
35.传统的测量方法基本上都是用全站仪进行观测放样点位,在高空中人工扶棱镜存在安全隐患,同时对于测点的精度有一定的影响,本项目在实施过程中,应用了全站仪的免棱镜测量技术,同时在支架上设置反射片,通过免棱镜技术将反射片固定在支架上,以提前确定拱肋的轴线。在管肋吊装过程中,通过免棱镜放样确定管肋的水平位置和高程,施工中,可以将拱肋的中线标记、测量点位和支架点位3个测量点进行相互复核,从而提高拱肋的水平精度。这样不但能提高放样的精度,也避免了因人员在高空架立棱镜而产生的人为误差,同时也能很快的拱肋的轴线进行固定。
36.单跨主拱肋采取从两端向跨中对称安装,拱肋接口采用外坡口,在安装段到位后利用马板固定,实现接口对位。
37.吊装时,将吊索与钢管拱肋及吊钩通过卡环连接好,并在钢管拱肋两端系上缆风绳进行拱肋高空姿态调整。当吊车将第一段1拱肋吊起到离地面约10~15cm高度,检查吊装工况,确认满足各项要求,再继续提升到安装高度。地面上作业人员通过缆风绳配合吊车调整拱肋的空中姿态,使拱肋拼接端与已安装段对位。高端上弦管轻靠落放在临时支撑钢管柱平台上的定位工装上,再使吊钩缓缓下落。通过全站仪精测后,吊钩起升,调整定位工装位移及标高。
38.在全站仪的监测下,利用已拼接段的记号和吊车的起吊实现拱肋平面位置确定。利用千斤顶进行标高精调,确保符合要求后,将定位工装与弦管焊接,用定位马板连接拱肋接口并紧固。
39.每节拱肋吊装段架设安装完成后,当架设与此相连的另一吊装段时,需要提前对已经完成的拱架节段的标高及轴线进行复测,当发生拱架吊装段轴线偏位或者标高沉降时,需要及时调整,通过使用千斤顶进行微调,直至达到安装精度要求。待调整到位并牢固
固定拱架段后,再架设与之关联的另一吊装拱肋段。
40.5、合龙段拱肋单元吊装
41.安装前,需要在实际温度时间段测量合龙段长度,经过多次测量并核对数据无误后方可进行拱肋的合龙。在与确定合龙段长度时温度较为一致的时间段内完成合龙段拱肋的切割,吊装工作。具体过程如下:
42.拱肋及吊钩通过卡环连接好,并在拱肋两端分别系上缆风绳。吊车将钢拱架吊起到离地面约10~15cm时,检查吊装工况,确认满足各项要求,再继续提升到安装高度。地面人员通过缆风绳配合吊车调整拱段的空中姿态,使拱段两端基本对位后,合龙段正对安装位置时,吊车慢慢下放合龙段缓缓就位,同时控制拱架两端高程,当下降至比设计高程(考虑到预拱高)高出1~3cm时停止下降。通过吊钩和拱肋缺口端部的标识来调整拱肋的水平位置,使吊钩均匀下放实现拱肋接头合龙,通过千斤顶精调合龙段标高,符合要求后采用马板固定。
43.6、拱肋接口焊接:拱肋焊接根据按照顺序从低向高组织焊接。直接利用拼装时焊缝位置的码板作为定位板;焊接前将焊缝坡口提前打磨光洁;同时清除坡口两侧50-80mm范围内氧化皮、透迹、油污等;检查合格后进行焊接,焊缝全部采用手工二保焊焊接;拱肋焊缝要求双数焊工对称焊接,同时加强焊接层间温度的控制,确保焊缝质量满足要求,焊接完成后及时进行无损检测。
44.7、测量控制
45.拱肋吊装前按桥梁中心线、拱轴线控制点进行放样安装支架,并进行拱轴线贯通测量,确保吊装过程中拱轴线不出现偏差。每段拱肋安装就位后,用全站仪检测拱肋轴线和标高。
46.(1)拱肋标记设施
47.拱肋安装时,为控制拱肋线型及标高的位置正确,在厂内拱肋制作阶段时,在拱肋每节段上弦管拱背节段口切线位置,特定的里程上标记(既可以控制轴线,又可以确定标高)进行测量控制,选取每段拱架的上下钢管的分段接口后0.5m的中点作为测量校准控制点。
48.(2)线形控制
49.拱肋线形通过调节各节拱肋的标高及拱轴线位置来保证,为确保拱肋按预期线形合龙,必须充分做好吊装过程中的线形控制。
50.(3)所用仪器
51.测距精度为
±
(2mm+2ppm)的测角标称精度为
±
2秒的全站仪、水准仪(s3级)、50m钢尺。
52.(4)控制网的测设:
53.测量人员完成平面控制网和高程控制网的测设。控制网内各测量控制点还要保证满足拱肋安装后,定期观测的要求;两个控制网之间要进行闭合差测设,以满足拱肋安装测量精度要求。
54.(5)拱脚安装定位测量:
55.拱肋在厂内制作时,应使用钢冲钉在拱脚上做好测量观测点位的标记,以便安装观测用。
56.拱脚安装时,将全站仪架设在相对应的控制点上,拱脚吊上支撑架后,对其进行初步测量,根据全站仪观测得出数据,通知安装人员对拱脚进行调整,拱脚安装重点要观测定位尺寸和倾斜度,一定要保证定位尺寸和倾斜度的精度达到设计要求。吊装时,测量人员架设全站仪观测每个单元件的观测点,依据测量数据指导安装人员进行调整。直至拱脚段的空间位置符合设计要求。
57.(6)拱肋的定期观测
58.在安装完后,测量人员还应进行多次的观测,对拱肋在不同的状况下的数据进行记录,并将数据提供给施工人员及设相关单位。
59.对焊接施工过程中实行过程监控,安装焊接完后进行复测,以保证焊接过程中拱架的位置没有超过设计要求,发现超差应立即通知施工人员及时进行处理,以保证拱架的线形要求;
60.考虑到随着拱肋的安装,过水管荷载持续增加,可能引起过水管带动支架下沉。所以,每安装一个节段,要对已安装的节段进行循环监测,并及时进行调整,以保证成拱的线形及拱脚处拱架受力良好;在拆卸临时支撑时,进行跟踪观测,观测拱架的沉降数据是否在规定范围以内。
61.以上所述仅是本发明的优选实施方式,应当指出,对于本技术领域的普通技术人员来说,在不脱离本发明技术原理的前提下,还可以做出若干改进和变型,这些改进和变型也应视为本发明的保护范围。