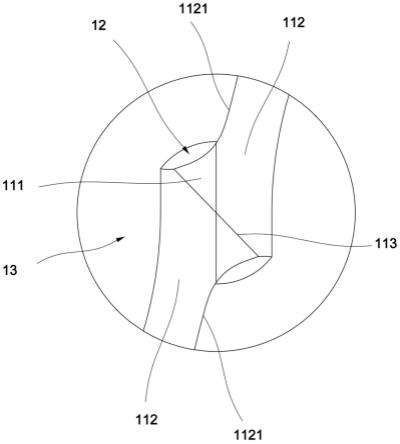
一种pcb钻针
技术领域
1.本发明涉及钻针技术领域,尤其涉及一种pcb钻针。
背景技术:2.pcb板,又称为印制电路板或印刷线路板,是重要的电子部件,是电子元器件的支撑体,也是电子元器件电气相互连接的载体。由于它是采用电子印刷术制作的,故被称为印刷电路板。
3.pcb板在电子产品中应用广泛,电子元器件安装到pcb板上之前,需要在pcb板上开孔,现有技术中的pcb钻针通常包括针体和针柄,针体设置在针柄的一端,针体远离针柄的一端设置有切削部,如图1所示,切削部包括第一后刀面100、第二后刀面200和横刃300,横刃300的两侧分别包括一个第一后刀面100和一个第二后刀面200;主切削刃110设置在第一后刀面100背离第二后刀面200的一侧边,主切削刃110的磨损速度快,主切削刃110的锋利程度不够,造成切削的速度较慢,并且不能保证针体具有足够的芯厚,针体的刚性差,容易断针。
4.因此,亟待需要一种pcb钻针来解决现有技术中的问题。
技术实现要素:5.本发明的目的在于提供一种pcb钻针,能够使主切削刃更加锋利,降低了主切削刃的磨损程度,提高了针体的刚性。
6.为达此目的,本发明采用以下技术方案:
7.一种pcb钻针,包括针体,所述针体的一端形成钻尖,所述钻尖包括横刃以及相对所述横刃的中心呈中心对称设置的两个尖部,每个所述尖部均包括呈夹角设置且相连的第一后刀面和第二后刀面;
8.每个所述尖部中,所述第二后刀面靠近所述第一后刀面的一侧设置有主切削刃,所述主切削刃由所述针体的外接圆向所述针体的轴心延伸且延伸至所述第一后刀面与所述第二后刀面交线的远离所述横刃的端点。
9.可选地,所述第一后刀面边缘到所述针体轴心的最小径向尺寸不小于所述第二后刀面边缘到所述针体轴心的最小径向尺寸。
10.可选地,所述针体上对应每个所述尖部均设置有绕所述针体的轴线螺旋延伸的第一排屑槽和第二排屑槽,所述第一排屑槽延伸至所述主切削刃和所述第一后刀面,所述第二排屑槽延伸至所述第二后刀面背离所述第一后刀面的一侧边缘,分别位于两个所述尖部且相邻的所述第一排屑槽和所述第二排屑槽的螺旋边界重合。
11.可选地,所述第一排屑槽的最大深度为所述针体外接圆直径的0.05-0.475倍。
12.可选地,所述第二排屑槽的最大深度为所述针体外接圆半径的0.15-0.475倍。
13.可选地,所述针体的最小径向宽度为芯厚,所述第一排屑槽的宽度为所述芯厚的0.5-1倍。
可以包括第一和第二特征直接接触,也可以包括第一和第二特征不是直接接触而是通过它们之间的另外的特征接触。而且,第一特征在第二特征“之上”、“上方”和“上面”包括第一特征在第二特征正上方和斜上方,或仅仅表示第一特征水平高度高于第二特征。第一特征在第二特征“之下”、“下方”和“下面”包括第一特征在第二特征正下方和斜下方,或仅仅表示第一特征水平高度小于第二特征。
31.在本实施例的描述中,术语“上”、“下”、“左”、“右”等方位或位置关系为基于附图所示的方位或位置关系,仅是为了便于描述和简化操作,而不是指示或暗示所指的装置或元件必须具有特定的方位、以特定的方位构造和操作,因此不能理解为对本发明的限制。此外,术语“第一”、“第二”仅仅用于在描述上加以区分,并没有特殊的含义。
32.实施例一
33.如图2所示,本实施例提供了一种pcb钻针,包括针体1,在针体1的一端形成钻尖11,钻尖11包括横刃113以及相对所述横刃113的中点呈中心对称设置的两个尖部,每个尖部均包括第一后刀面111和第二后刀面112,第一后刀面111和第二后刀面112相连且呈夹角设置,每个尖部中,第二后刀面112靠近第一后刀面111的一侧设置有主切削刃1121,主切削刃1121由针体1的外接圆向针体1的轴心延伸且延伸至第一后刀面111与所述第二后刀面112交线的远离横刃113的端点处。将主切削刃1121设置在第二后刀面112上,主切削刃1121由外接圆向针体1的轴心以及靠近第一后刀面111的一侧延伸,使主切削刃1121的径向前角减小,能够减小主切削刃1121的磨损速度,保证具有锋利的主切削刃1121,降低了切削的阻力,并且沿针体1的径向,主切削刃1121相比第一后刀面111更靠近外接圆,从而可以保证第一后刀面111沿第一后刀面111和第二后刀面112排列方向的尺寸,保证了有效的芯厚,能够增加钻针的刚性,使钻针不容易断裂,提高钻针的使用寿命。
34.进一步地,分别位于两个尖部的第一后刀面111和第二后刀面112的相交处形成尖角结构,有利于进一步保证有效芯厚,从而增加钻针的刚性。此处需要说明的是,有效芯厚为针体1的最小径向宽度。
35.可选地,第一后刀面111边缘到针体1轴心的最小径向尺寸不小于第二后刀面112边缘到针体1轴心的最小径向尺寸,以使针体1具有以第二后刀面112边缘到针体1轴心的最小径向尺寸为半径的内接圆,芯厚不小于该内接圆的直径,能够进一步保证该pcb钻针的芯厚,提高针体1的刚性,减少断针的情况的发生,提高pcb钻针的使用寿命。
36.优选地,如图3所示,针体1上对应每个尖部均设置有绕针体1的轴线螺旋延伸的第一排屑槽12和第二排屑槽13,第一排屑槽12延伸至主切削刃1121和第一后刀面111,第二排屑槽13延伸至第二后刀面112背离所述第一后刀面111的一侧边缘,分别位于两个尖部且相邻的第一排屑槽12和第二排屑槽13的螺旋边界重合。在该pcb钻针切削的过程中,切屑优先从第一排屑槽12排出,当第一排屑槽12积满切屑时,切屑逐渐向第二排屑槽13移动,切削在过渡位置会受到剪切力的作用,从而将长条状的切屑挤断排出,防止长条状切屑缠绕在钻针上造成断针,提高了该pcb钻针的排屑能力,将切削及时排出钻孔,减少切屑与孔壁的摩擦,降低孔壁的粗糙度,提高加工质量。
37.在实际的加工过程中,第一排屑槽12的宽度可以由外接圆延伸至对侧尖部的第二后刀面112上;第二排屑槽13的宽度还可以延伸至对侧尖部的第一后刀面111上。
38.可选地,如图3所示,第一排屑槽12的最大深度为针体11外接圆直径的0.05-0.475
倍,例如为0.1倍、0.2倍、0.3倍或0.45倍。本实施例中的第一排屑槽12的最大深度优选为针体11外接圆直径的0.3倍,保证第一排屑槽12的容屑能力和排屑功能的同时,保证针体1的芯厚,提高针体1的强度。
39.可选地,如图3所示,第二排屑槽13的最大深度为针体1外接圆半径的0.15-0.475倍,例如为0.2倍、0.3倍或0.45倍。本实施中的第二排屑槽13的最大深度优选为针体1外接圆半径的0.3倍,进一步提升针体1的容屑能力和排屑能力,同时能够保证切屑在第一后刀面111和第二后刀面112的交界处能够受到剪切力而被铰断,变成短条装切削而排出,减小切屑对孔壁的磨损,提高孔壁的加工质量,防止长条状切屑缠绕在钻针上引起断针。
40.可选地,第一排屑槽12的宽度为芯厚的0.5-1倍,例如0.55倍、0.6倍、0.7倍、0.8倍或0.9倍。芯厚为两个第一排屑槽12之间的最短距离。本实施例中优选第一排屑槽12的宽度为芯厚的0.55倍,保证针体1的芯厚的厚度,提高针体1的强度,从而进一步提高针体11整体容屑空间和第一排屑槽12的排屑能力。
41.优选地,同一尖部对应的第一排屑槽12和第二排屑槽13间隔设置形成刃瓣。本实施例中,通过设置第一排屑槽12和第二排屑槽13的宽度,使得第一排屑槽12和第二排屑槽13之间的距离更短,不需要设置边刀结构,节省了加工的工序,提高了对pcb钻针的加工效率,还能够在pcb钻针钻孔的过程中减少针体1与钻孔孔壁的接触面积,减少针体1与孔壁摩擦产生的热量,降低高温对孔壁的灼蚀,提高加工的质量。
42.可选地,第一排屑槽12和第二排屑槽13的螺旋角度相同,第一排屑槽12和第二排屑槽13的螺旋角度均为30
°‑
55
°
。例如可以为40
°
、45
°
或50
°
。具体地,在本实施例中第一排屑槽12的螺旋角沿针体1向针柄的方向逐渐增大,例如靠近钻尖11的第一排屑槽12螺旋角定义为前螺旋角,前螺旋角的角度为40
°
,靠近针柄部分的第一排屑槽12的螺旋角定义为后螺旋角,后螺旋角的角度为50
°
,通过第一排屑槽12和第二排屑槽13螺旋角的逐渐增大,能够更加有利于断屑和切屑的排出,降低孔壁的粗糙度,进一步提高孔壁的加工质量。在其他实施例中,第一排屑槽12和第二排屑槽13的螺旋角度可以均为45
°
,即第一排屑槽12和第二排屑槽13的螺旋角度沿针体1向针柄的方向是不变的,同样有利于断屑和切削的排出,降低孔壁粗糙度,从而提高从孔壁的加工质量。
43.可选地,第一排屑槽12的深度沿针体1向针柄的方向逐渐减小,第二排屑槽13的深度沿针体1向针柄的方向逐渐减小,可以理解的是,第一排屑槽12和第二排屑槽13的深度的逐渐减小,使得两个第一排屑槽12之间的距离沿针体11向针柄的方向逐渐增大,两个第二排屑槽13之间的距离沿针体1向针柄的方向逐渐增大,能够进一步地提高针体1的韧性和强度。
44.可选地,该pcb钻针的针体1和针柄均由硬质合金材料制成,硬质合金具有硬度高、耐磨、强度高和韧性好的优点,能够提高该pcb钻针的使用寿命。
45.可选地,钻尖11还包括钻尖角α,两个第二后刀面112的夹角为钻尖角α,钻尖角α的角度为105
°‑
170
°
,例如钻尖角α可以为110
°
、120
°
、130
°
、140
°
、150
°
或160
°
,本实施例中钻尖角α的角度为150
°
,能够保证针体11具有锋利的主切削刃1121。
46.可选地,针体1还包括基面,该基面为过第一后刀面111和第二后刀面112的交线做的与针体1端面呈第一预设夹角β的面,针体1的端面为过钻尖且垂直于针体1中心轴线的平面,该第一预设夹角β的度数为(180
°‑
α)/2,第一后刀面111与基面的夹角为第一后刀面角
γ,第二后刀面112与基面的夹角为第二后刀面角δ,第一后刀面角γ大于0
°
且小于δ,第一后刀面角的度数大于0
°
小于第二后刀面角的角度,能够保证第二后刀面112上的主切削刃1121更加锋利,同时还能降低第一后刀面111和第二后刀面112的磨损速度,进一步提高该pcb钻针的使用寿命。
47.表1
[0048][0049]
表2
[0050]
机床设备钻孔机转速160kr/min孔数2500hit进给量1.62m/min退刀速25.2m/min
[0051]
表3
[0052][0053]
如上表所示,表1为本实施例提供的pcb钻针的参数,表2为加工条件,将表1中的钻针安装到表2提供的钻孔机上,在表2的加工条件下在pcb板板厚为12mm的板材上钻孔,得到表3的实验数据,其中对照组为现有的pcb钻针的结构。
[0054]
在实际加工的过程中,cpk的数值越大,表示孔壁的加工质量越好,由表3的实验数据可知,实验组的三组数据可以明显看出本实施例提供的pcb钻针在加工后的cpk的数值明显大于对照组的pcb钻针的cpk的数值,由此可见本实施例提供的pcb钻针加工过程中稳定性强,通过实验组和对照组的实验结果看,本实施例提供的pcb钻针结构缠丝和塞孔现象有了明显的改善。因此足以说明,在针体1上并排设置两个螺旋延伸的第一排屑槽12和第二排屑槽13,第一排屑槽12和第二排屑槽13的螺旋边界重合,能够保证在该pcb钻针切削的过程中,切屑优先从第一排屑槽12排出,当第一排屑槽12积满切屑时,切屑逐渐向第二排屑槽13移动,切削在过渡位置会受到剪切力的作用,从而将长条状的切屑挤断排出,防止长条状切
屑缠绕在钻针上造成断针,降低孔壁的粗糙度,提高加工的质量,提高了该pcb钻针的排屑能力和钻针的使用寿命。
[0055]
实施例二
[0056]
如图4-图5所示,本实施例提供的pcb钻针,与实施例一不同的是本实施例中的pcb钻针的第一后刀面111与基面的夹角大于-60
°
且小于0
°
,主切削刃1121设置在第二后刀面112上,该pcb钻针,主切削刃1121的径向前角减小,能够减小主切削刃1121的磨损速度,保证具有锋利的主切削刃1121,降低了切削的阻力,并且两个尖部的相交处保留了第一后刀面111的尖端,保证了有效的芯厚,能够增加钻针的刚性,使钻针不容易断裂,提高钻针的使用寿命。
[0057]
显然,本发明的上述实施例仅仅是为了清楚说明本发明所作的举例,而并非是对本发明的实施方式的限定。对于所属领域的普通技术人员来说,能够进行各种明显的变化、重新调整和替代而不会脱离本发明的保护范围。这里无需也无法对所有的实施方式予以穷举。凡在本发明的精神和原则之内所作的任何修改、等同替换和改进等,均应包含在本发明权利要求的保护范围之内。