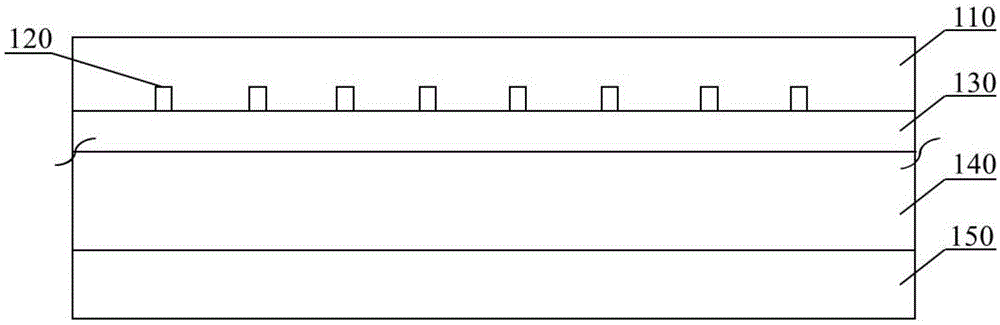
本发明涉及光波导芯片生产制造领域,尤其是涉及一种半导体硅基光波导器件及其制备方法。
背景技术:
:目前平面光波导分路器在国内外市场非常火爆,根据2016年4月5日市场及技术咨询公司electronicast报告,2015年全球平面光波导分路器市场总额达到6.96亿美元,同比增长达到14%。中国目前已经成为平面光波导分路器市场的主导者,占市场总额的35%以上。2012年之前,国内的光分路器器件全都是从韩国和日本进口,国内仅能做封装,大部分利润都被韩、日、欧美拿走。经过多年的潜心研究与开发,2015年之后,国内分路器芯片制造得到快速发展。常规波导器件使用石英基底片,表面光学器件折射率需依据衬底片折射率而设计和调整,对衬底片质量依赖性较大,并且需要专门的石英加工设备进行生产制造。有鉴于此,特提出本发明。技术实现要素:本发明的第一目的在于提供一种半导体硅基光波导器件的制备方法,解决了常规波导器件使用石英基底片,对衬底片质量依赖性较大且需订制专门的石英加工设备进行制造的技术问题。本发明的第一目的在于提供一种半导体硅基光波导器件的制备方法,包括以下步骤:(a)单面抛光硅片非抛光面淀积底包层;(b)在单面抛光硅片抛光面依次层叠淀积下包层、芯层以及掩膜层;(c)刻蚀芯层后形成波导通道并去除掩膜层;(d)在刻蚀后的芯层上淀积上包层,即得到半导体硅基光波导器件;优选地,所述掩膜层为金属掩膜层。进一步的,所述芯层为掺杂锗烷的二氧化硅,其中所述锗烷与二氧化硅的质量比为1-3:100,优选为1.8:100;优选地,芯层的厚度为5.5-6.5μm。进一步的,所述底包层为掺杂硼烷与磷烷的二氧化硅,其中所述硼烷与二氧化硅的质量比为1-3:100,所述磷烷与二氧化硅的质量比为1-3:100;优选地,所述硼烷与二氧化硅的质量比为1.7:100,所述磷烷与二氧化硅的质量比为1.9:100。进一步的,所述下包层为掺杂硼烷与磷烷的二氧化硅,其中所述硼烷与二氧化硅的质量比为1-3:100,所述磷烷与二氧化硅的质量比为1-3:100;优选地,所述硼烷与二氧化硅的质量比为1.7:100,所述磷烷与二氧化硅的质量比为1.9:100。进一步的,所述上包层为掺杂硼烷与磷烷的二氧化硅,其中所述硼烷与二氧化硅的质量比为1-3:100,所述磷烷与二氧化硅的质量比为1-3:100;优选地,所述硼烷与二氧化硅的质量比为1.7:100,所述磷烷与二氧化硅的质量比为1.9:100。进一步的,所述底包层的厚度为10-20μm,优选为18μm;和/或,下包层的厚度为10-20μm,优选为12μm;和/或,上包层的厚度为10-20μm,优选为18μm。进一步的,所述底包层、下包层、芯层和上包层的淀积方法均为等离子体增强化学气相沉积法。进一步的,所述底包层、下包层、芯层和上包层的淀积温度均为350-450℃,优选为400℃;优选地,所述底包层、下包层、芯层和上包层的淀积压力均为2-3torr,优选为2.2torr。进一步的,通过蒸镀和/或溅射淀积金属掩膜层;优选地,所述金属掩膜层为金属,金属选自铝、铬或钛中的至少一种,优选为铝。本发明的第二目的在于提供一种半导体硅基光波导器件,根据本发明提供的半导体硅基光波导器件的制备方法制备得到。与现有技术相比,本发明的有益效果为:本发明提供的半导体硅基光波导器件的制备方法采用半导体硅为衬底材料,与硅半导体制造设备兼容性好,并且不受衬底片折射率的影响,使得光波导器件的设计与制造更加灵活,同时该制备方法良品率和集成度高,为后续voa、awg等器件开发提供了工艺基础,应用前景广泛。本发明提供的半导体硅基光波导器件洁净度高,折射率稳定,厚度一致性好,应用前景广阔。附图说明为了更清楚地说明本发明具体实施方式或现有技术中的技术方案,下面将对具体实施方式或现有技术描述中所需要使用的附图作简单地介绍,显而易见地,下面描述中的附图是本发明的一些实施方式,对于本领域普通技术人员来讲,在不付出创造性劳动的前提下,还可以根据这些附图获得其他的附图。图1为本发明实施例1提供的半导体硅基光波导器件的结构示意图。图标:110-上包层;120-波导通道;130-下包层;140-单面抛光硅片;150-底包层。具体实施方式下面将结合实施例对本发明的实施方案进行详细描述,但是本领域技术人员将会理解,下列实施例仅用于说明本发明,而不应视为限制本发明的范围。实施例中未注明具体条件者,按照常规条件或制造商建议的条件进行。根据本发明的第一个方面,本发明提供了一种半导体硅基光波导器件的制备方法,包括以下步骤:(a)单面抛光硅片非抛光面淀积底包层;(b)在单面抛光硅片抛光面依次层叠淀积下包层、芯层以及掩膜层;(c)刻蚀芯层后形成波导通道并去除掩膜层;(d)在刻蚀后的芯层上淀积上包层,即得到半导体硅基光波导器件;优选地,所述掩膜层为金属掩膜层。本发明提供的半导体硅基光波导器件的制备方法采用半导体硅为衬底材料,与硅半导体制造设备兼容性好,并且不受衬底片折射率的影响,使得光波导器件的设计与制造更加灵活,同时该制备方法良品率和集成度高,为后续voa、awg等器件开发提供了工艺基础,应用前景广泛。在本发明的一种优选实施方式中,芯层为掺杂锗烷的二氧化硅,其中所述锗烷与二氧化硅的质量比为1-3:100。在本发明中,锗烷与二氧化硅的典型但非限制性的质量比为1:100、1.2:100、1.4:100、1.6:100、1.8:100、2:100、2.2:100、2.4:100、2.6:100、2.8:100或3:100。通过对锗烷与二氧化硅的质量比进行控制,可以制备得到性能更加优异的半导体硅基光波导器件。锗烷与二氧化硅的质量比在1-3:100范围内,半导体硅基光波导器件的性能较好。在本发明的进一步优选实施方式中,锗烷与二氧化硅的质量比为1.8:100。通过对锗烷与二氧化硅的质量比的更进一步调整和优化,使得到的半导体硅基光波导器件的性能更好。锗烷是通式为genh2n+2的一系列锗与氢的化合物的总称。主要用于制造电子器件,如集成电路、光电器件。通过在光波导器件的二氧化硅层中掺杂锗烷,可以提高光波导器件的折射率,降低波导传输损耗,从而提高了光波导器件的性能。在本发明中,采用的锗烷为体积分数为5%的甲锗烷(geh4,氮气作为保护气),或者本领域技术人员熟知的与上述作用类似的其他锗烷。通过在芯层掺杂甲锗烷,可以提高芯层的折射率,从而提高光波导器件的性能。在本发明的一种优选实施方式中,芯层的厚度为5.5-6.5μm。在本发明中,芯层的典型但非限制性的厚度为5.5、6或6.5μm。芯层的厚度与波导的规格相一致,即设计6μm×6μm的波导通道就需要厚度为6μm的芯层,从而保证光波导器件的性能最佳。在本发明的一种优选实施方式中,底包层为掺杂硼烷与磷烷的二氧化硅,其中所述硼烷与二氧化硅的质量比为1-3:100,所述磷烷与二氧化硅的质量比为1-3:100。在本发明中,底包层中硼烷与二氧化硅的典型但非限制性的质量比为1:100、1.1:100、1.2:100、1.3:100、1.4:100、1.5:100、1.6:100、1.7:100、1.8:100、1.9:100、2:100、2.1:100、2.2:100、2.3:100、2.4:100、2.5:100、2.6:100、2.7:100、2.8:100、2.9:100或3:100;底包层中磷烷与二氧化硅的典型但非限制性的质量比为1:100、1.1:100、1.2:100、1.3:100、1.4:100、1.5:100、1.6:100、1.7:100、1.8:100、1.9:100、2:100、2.1:100、2.2:100、2.3:100、2.4:100、2.5:100、2.6:100、2.7:100、2.8:100、2.9:100或3:100。硼烷又称硼氢化合物,是硼与氢组成的化合物的总称。通过在光波导器件的二氧化硅层中掺杂硼烷,可以降低光波导器件的折射率,从而可以通过控制光波导器件的折射率来控制光波导器件的性能。在本发明中,采用的硼烷为体积分数为5%的甲硼烷(bh3,氮气作为保护气),或者本领域技术人员熟知的与上述作用类似的其他硼烷。通过在二氧化硅中掺杂甲硼烷,可以降低二氧化硅层的折射率,从而控制光波导器件的性能。磷烷是具有五配位磷的有机化合物,稳定的磷烷多为氟原子的衍生物或环状磷酸酯。磷烷是半导体器件制造中的重要n型掺杂源,同时磷烷还用于多晶硅化学气相沉淀、离子注入工艺、mocvd工艺、磷硅玻璃(psg)钝化膜制备等工艺中。通过在光波导器件的二氧化硅层中掺杂磷烷,可以提高光波导器件的折射率,从而可以通过控制光波导器件的折射率来控制光波导器件的性能。在本发明中,采用的磷烷为体积分数为5%的磷化氢(ph3,氮气作为保护气),或者本领域技术人员熟知的与上述作用类似的其他磷烷。通过在二氧化硅中掺杂磷化氢,可以提高二氧化硅层的折射率,从而控制光波导器件的性能。通过对底包层中硼烷与二氧化硅的质量比和磷烷与二氧化硅的质量比进行控制,可以制备得到性能更加优异的半导体硅基光波导器件。底包层中硼烷与二氧化硅的质量比在1-3:100范围内以及磷烷与二氧化硅的质量比在1-3:100范围内,光波导器件的性能较好。在本发明的进一步优选实施方式中,底包层中硼烷与二氧化硅的质量比为1.7:100,磷烷与二氧化硅的质量比为1.9:100。通过对底包层中硼烷与二氧化硅的质量比和磷烷与二氧化硅的质量比的更进一步调整和优化,使得到的半导体硅基光波导器件的性能更好。在本发明的一种优选实施方式中,下包层为掺杂硼烷与磷烷的二氧化硅,其中所述硼烷与二氧化硅的质量比为1-3:100,所述磷烷与二氧化硅的质量比为1-3:100。在本发明中,下包层中硼烷与二氧化硅的典型但非限制性的质量比为1:100、1.1:100、1.2:100、1.3:100、1.4:100、1.5:100、1.6:100、1.7:100、1.8:100、1.9:100、2:100、2.1:100、2.2:100、2.3:100、2.4:100、2.5:100、2.6:100、2.7:100、2.8:100、2.9:100或3:100;下包层中磷烷与二氧化硅的典型但非限制性的质量比为1:100、1.1:100、1.2:100、1.3:100、1.4:100、1.5:100、1.6:100、1.7:100、1.8:100、1.9:100、2:100、2.1:100、2.2:100、2.3:100、2.4:100、2.5:100、2.6:100、2.7:100、2.8:100、2.9:100或3:100。通过对下包层中硼烷与二氧化硅的质量比和磷烷与二氧化硅的质量比进行控制,可以制备得到性能更加优异的半导体硅基光波导器件。下包层中硼烷与二氧化硅的质量比在1-3:100范围内以及磷烷与二氧化硅的质量比在1-3:100范围内,光波导器件的性能较好。在本发明的进一步优选实施方式中,下包层中硼烷与二氧化硅的质量比为1.7:100,磷烷与二氧化硅的质量比为1.9:100。通过对下包层中硼烷与二氧化硅的质量比和磷烷与二氧化硅的质量比的更进一步调整和优化,使得到的半导体硅基光波导器件的性能更好。在本发明的一种优选实施方式中,上包层为掺杂硼烷与磷烷的二氧化硅,其中所述硼烷与二氧化硅的质量比为1-3:100,所述磷烷与二氧化硅的质量比为1-3:100。在本发明中,上包层中硼烷与二氧化硅的典型但非限制性的质量比为1:100、1.1:100、1.2:100、1.3:100、1.4:100、1.5:100、1.6:100、1.7:100、1.8:100、1.9:100、2:100、2.1:100、2.2:100、2.3:100、2.4:100、2.5:100、2.6:100、2.7:100、2.8:100、2.9:100或3:100;上包层中磷烷与二氧化硅的典型但非限制性的质量比为1:100、1.1:100、1.2:100、1.3:100、1.4:100、1.5:100、1.6:100、1.7:100、1.8:100、1.9:100、2:100、2.1:100、2.2:100、2.3:100、2.4:100、2.5:100、2.6:100、2.7:100、2.8:100、2.9:100或3:100。通过对上包层中硼烷与二氧化硅的质量比和磷烷与二氧化硅的质量比进行控制,可以制备得到性能更加优异的半导体硅基光波导器件。上包层中硼烷与二氧化硅的质量比在1-3:100范围内以及磷烷与二氧化硅的质量比在1-3:100范围内,光波导器件的性能较好。在本发明的进一步优选实施方式中,上包层中硼烷与二氧化硅的质量比为1.7:100,磷烷与二氧化硅的质量比为1.9:100。通过对上包层中硼烷与二氧化硅的质量比和磷烷与二氧化硅的质量比的更进一步调整和优化,使得到的半导体硅基光波导器件的性能更好。在本发明的一种优选实施方式中,底包层的厚度为10-20μm。在本发明中,底包层的典型但非限制性的厚度为10、11、12、13、14、15、16、17、18、19或20μm。底包层具有平衡应力的作用,通过对底包层的厚度进行控制,可以制备得到平衡应力更加优异的半导体硅基光波导器件。底包层的厚度在10-20μm范围内,光波导器件的性能较好。在本发明的进一步优选实施方式中,底包层的厚度为18μm。通过对底包层的厚度的更进一步调整和优化,使得到的半导体硅基光波导器件的性能更好。在本发明的一种优选实施方式中,下包层的厚度为10-20μm。在本发明中,下包层的典型但非限制性的厚度为10、11、12、13、14、15、16、17、18、19或20μm。下包层为光波导器件的组成部分,通过对下包层的厚度进行控制,可以制备得到性更加优异的半导体硅基光波导器件。下包层的厚度在10-20μm范围内,光波导器件的性能较好。在本发明的进一步优选实施方式中,下包层的厚度为12μm。通过对下包层的厚度的更进一步调整和优化,使得到的半导体硅基光波导器件的性能更好。在本发明的一种优选实施方式中,上包层的厚度为10-20μm。在本发明中,上包层的典型但非限制性的厚度为10、11、12、13、14、15、16、17、18、19或20μm。上包层为光波导器件的组成部分,通过对上包层的厚度进行控制,可以制备得到性更加优异的半导体硅基光波导器件。上包层的厚度在10-20μm范围内,光波导器件的性能较好。在本发明的进一步优选实施方式中,上包层的厚度为18μm。通过对上包层的厚度的更进一步调整和优化,使得到的半导体硅基光波导器件的性能更好。在本发明的一种优选实施方式中,所述底包层、下包层、芯层和上包层的淀积方法均为等离子体增强化学气相沉积法。等离子体增强化学气相沉积是借助微波或射频等使含有薄膜组成原子的气体电离,在局部形成等离子体,而等离子体化学活性很强,很容易发生反应,在基片上沉积出所期望的薄膜。为了使化学反应能在较低的温度下进行,利用了等离子体的活性来促进反应,因而这种cvd称为等离子体增强化学气相沉积(pecvd)。pecvd具有基本反应温度低,沉积速率快,成膜质量好,针孔较少,不易龟裂的优点,因此广泛应用于光波导器件的制备。在本发明的一种优选实施方式中,底包层、下包层、芯层和上包层的淀积温度均为350-450℃。在本发明中,淀积的典型但非限制性的温度为350、360、370、380、390、400、410、420、430、440或450℃。通过对淀积温度进行控制,可以制备得到性能更加优异的半导体硅基光波导器件。淀积温度在350-450℃范围内,半导体硅基光波导器件的性能较好。在本发明的进一步优选实施方式中,淀积温度为400℃。通过对淀积温度的更进一步调整和优化,使得到的半导体硅基光波导器件的性能更好。在本发明的一种优选实施方式中,底包层、下包层、芯层和上包层的淀积压力均为2-3torr。在本发明中,淀积的典型但非限制性的压力为2、2.1、2.2、2.3、2.4、2.5、2.6、2.7、2.8、2.9或3torr。通过对淀积压力进行控制,可以制备得到性能更加优异的半导体硅基光波导器件。二氧化硅的淀积压力在350-450℃范围内,半导体硅基光波导器件的性能较好。在本发明的进一步优选实施方式中,淀积压力为2.2torr。通过对淀积压力的更进一步调整和优化,使得到的半导体硅基光波导器件的性能更好。在本发明的一种优选实施方式中,通过蒸镀和/或溅射淀积金属掩膜层。金属掩膜层的蒸镀和溅射属于物理气相沉积法,是指在真空条件下,利用各种物理方法,将镀料气化成原子、分子或使其离化为离子,直接沉积到基体表面上的方法。物理气相沉积技术具有膜/基结合力好、薄膜均匀致密、薄膜厚度可控性好、应用的靶材广泛、溅射范围宽、可沉积厚膜、可制取成分稳定的合金膜和重复性好等优点,因此在本发明中采用物理气相沉积法进行金属掩膜层的淀积。在本发明的一种优选实施方式中,金属掩膜层为金属,金属选自铝、铬或钛中的至少一种,或者本领域技术人员熟知的与上述作用类似的其他金属。在本发明的进一步优选实施方式中,金属掩膜层中的金属为铝。在本发明的一种优选实施方式中,淀积底包层后还包括硅片清洗的步骤,分别用带有兆声的sc-1溶液和稀氢氟酸溶液对硅片进行清洗。在本发明中,采取物理方式加化学方式对硅片进行清洗,sc-1溶液清洗为化学方式,sc-1溶液是能去除颗粒和有机物质的碱性溶液。由于sc-1溶液中的过氧化氢为强氧化剂,能氧化硅片表面和颗粒。颗粒上的氧化层能提供消散机制,分裂并溶解颗粒,破坏颗粒和硅片表面之间的附着力,而脱离硅表面。过氧化氢的氧化效应也在硅片表面形成一个保护层,阻止颗粒重新粘附在硅片表面;稀氢氟酸溶液清洗为化学方式,是将硅片放入到10%的氢氟酸溶液中浸泡2分钟,可以将硅片表面自然生成的氧化膜去除并抑制氧化膜再次形成,同时氢氟酸还可以将附着在氧化膜上的金属污染物溶解掉;超声清洗为物理方式,是利用超声波在液体中的空化作用、加速度作用及直进流作用对液体和污物进行直接、间接的作用,使污物层被分散、乳化、剥离而达到清洗目的。通过sc-1溶液清洗、稀氢氟酸溶液清洗和超声清洗的结合,可以达到更好的硅片清洗效果,进而得到性能更好的半导体硅基光波导器件。根据本发明的第二个方面,本发明提供了一种半导体硅基光波导器件,根据本发明提供的半导体硅基光波导器件的制备方法制备得到。本发明提供的半导体硅基光波导器件洁净度高,折射率稳定,厚度一致性好,应用前景广阔。为了进一步了解本发明,下面结合具体实施例和对比例对本发明效果做进一步详细的说明。本发明涉及的各原料均可通过商购获取。实施例1本实施例提供了一种半导体硅基光波导器件,其结构如图1所示,由下往上依次为底包层150、单面抛光硅片140、下包层130、波导通道120和上包层110。其制备方法包括以下步骤:(a)选用通用的单面抛光硅片140进行淀积前清洗,然后用pecvd设备对单面抛光硅片140非抛光面进行底包层150淀积,底包层150为掺杂硼磷的二氧化硅,其中甲硼烷与二氧化硅的质量比为1.7:100,磷化氢与二氧化硅的质量比为1.9:100,厚度为18μm。(b)使用带有兆声的稀氢氟酸溶液和sc-1溶液对单面抛光硅片140进行清洗,然后在单面抛光硅片140抛光面依次淀积下包层130、芯层以及铝掩膜层。下包层130为掺杂硼烷与磷烷的二氧化硅,下包层130中甲硼烷与二氧化硅的质量比为1.7:100,磷化氢与二氧化硅的质量比为1.9:100,厚度为12μm;芯层为掺杂锗烷的二氧化硅,芯层中甲锗烷与二氧化硅的质量比为1.8:100,厚度为6μm。(c)铝掩膜层淀积后进行光刻,然后使用干法刻蚀铝掩膜层,去胶后使用干法刻蚀芯层,形成波导通道120,刻蚀芯层后湿法将铝掩膜全部去除。(d)用pecvd设备在刻蚀后的芯层上淀积上包层110,上包层110为掺杂硼烷与磷烷的二氧化硅,甲硼烷与二氧化硅的质量比为1.7:100,磷化氢与二氧化硅的质量比为1.9:100,厚度为1.8μm。通过该方法生产制造出了8波导通道(6μm×6μm横截面积)splitter光波导器件。其中,底包层150、下包层130、芯层和上包层110的淀积温度为400℃,淀积压力为2.2torr。实施例2本实施例提供了一种半导体硅基光波导器件,本实施例的制备方法与实施例1的不同之处在于,芯层的厚度为5.5μm,通过该方法生产制造出了8通道(5.5μm×5.5μm横截面积)splitter光波导器件。实施例3本实施例提供了一种半导体硅基光波导器件,本实施例的制备方法与实施例1的不同之处在于,芯层的厚度为6.5μm,通过该方法生产制造出了8通道(6.5μm×6.5μm横截面积)splitter光波导器件。实施例4本实施例提供了一种半导体硅基光波导器件,本实施例的制备方法与实施例1的不同之处在于,芯层中甲锗烷与二氧化硅的质量比为1:100。实施例5本实施例提供了一种半导体硅基光波导器件,本实施例的制备方法与实施例1的不同之处在于,芯层中甲锗烷与二氧化硅的质量比为3:100。实施例6本实施例提供了一种半导体硅基光波导器件,本实施例的制备方法与实施例1的不同之处在于,下包层中甲硼烷与二氧化硅的质量比为1:100,磷化氢与二氧化硅的质量比为3:100。实施例7本实施例提供了一种半导体硅基光波导器件,本实施例的制备方法与实施例1的不同之处在于,下包层中甲硼烷与二氧化硅的质量比为3:100,磷化氢与二氧化硅的质量比为1:100。实施例8本实施例提供了一种半导体硅基光波导器件,本实施例的制备方法与实施例1的不同之处在于,上包层中甲硼烷与二氧化硅的质量比为1:100,磷化氢与二氧化硅的质量比为3:100。实施例9本实施例提供了一种半导体硅基光波导器件,本实施例的制备方法与实施例1的不同之处在于,上包层中甲硼烷与二氧化硅的质量比为3:100,磷化氢与二氧化硅的质量比为1:100。对比例1本对比例提供了一种石英基光波导器件,本对比例的制备方法与实施例1的不同之处在于,衬底片为石英片,没有下包层淀积,直接在石英基底上淀积芯层,经过铝掩膜层淀积与铝掩膜层光刻、铝掩膜层刻蚀、芯层刻蚀、铝掩膜层去除后进行上包层淀积,实际芯层与上包层折射率不同于实施例。试验例1实验以实施例1-9和对比例1提供的光波导器件为研究对象,对比研究光波导器件的偏振相关损耗(pdl)和插损(il)这两种性能。实验数据和结果如下。表1不同光波导器件的性能数据偏振相关损耗(pdl)插损(il)实施例10.13实施例20.153.1实施例30.153.2实施例40.143.2实施例50.153.3实施例60.163.2实施例70.163.4实施例80.183.3实施例90.173.4对比例10.193.5分析数据可得结果,实施例1-9提供的半导体硅基光波导器件在偏振相关损耗和插损方面的性能均优于或持平于对比例1提供的光波导器件的性能,说明本发明提供的半导体硅基光波导器件的制备方法制备得到的光波导器件具有优良的性能,应用前景广泛。最后应说明的是:以上各实施例仅用以说明本发明的技术方案,而非对其限制;尽管参照前述各实施例对本发明进行了详细的说明,本领域的普通技术人员应当理解:其依然可以对前述各实施例所记载的技术方案进行修改,或者对其中部分或者全部技术特征进行等同替换;而这些修改或者替换,并不使相应技术方案的本质脱离本发明各实施例技术方案的范围。当前第1页12