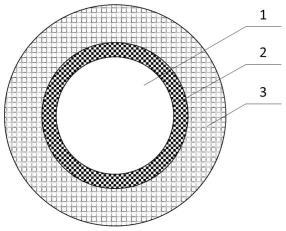
1.本发明涉及光学传输光缆领域,具体为一种耐高温碳密封涂覆光纤及其制作方法。
背景技术:2.光纤传感技术在石油天然气勘探具有重要应用。由于石油气田井下环境属于高温、高压且氢富含量较高的严苛环境,通常要将探测传输用的光纤进行钢管铠装成缆来实现光缆抗高压问题,同时还需要能耐高温的且抗氢损的光纤才能满足上述环境下的长期使用需求。
3.目前国内耐高温光纤主要有150℃耐温等级、300℃耐温等级和600℃以上耐温等级,其中:(1)150℃耐温等级的光纤是采用可紫外固化的耐高温丙烯酸改性树脂作为光纤涂覆层,该类光纤货架产品包括150℃碳密封涂覆光纤和150℃非涂碳的普通光纤;该光纤涂覆层的涂覆固化可以通过光纤拉丝在线涂覆紫外光固化工艺实现,能适应不同的拉丝速度,但耐高温等级较低,主流产品的典型长期工作温度在150℃左右的范围内;(2)300℃耐温等级的光纤目前主要采用聚酰亚胺作为涂覆层,可实现300℃左右温度区间长期工作和350℃~400℃短期工作,由于普通聚酰亚胺涂料只能通过加热固化,且因黏度低、粘接性弱等料性本身的特点,无法实现紫外快速固化,且需两层或多层涂覆达到可实用的目标涂覆层厚度;(3)600℃以上耐温等级的光纤一般是采用金属材料作为涂覆层,但需要特殊的金属液溅射或化学电镀法实现金属涂覆,工艺复杂,制作成本高。
4.井下环境一般都在300℃以上,如前所述的现有技术中的300℃耐温等级的光纤只对高温环境具有较好的适应性,无法解决井下高压、高湿度、高盐度引起的光纤传输损耗增加、涂覆层易被腐蚀、使用寿命下降的问题,尚不满足石油气田井下高压富氢环境对光纤抗氢损的需求。
5.因此,有必要对现有的耐高温光纤进行创新,来满足石油气田井下高温、高压且氢富含量较高的严苛环境。
技术实现要素:6.本发明所要解决的技术问题是针对现有技术的不足,提供一种耐高温碳密封涂覆光纤及其制作方法适用于石油气田井下高温、高压且氢富含量较高的严苛环境。
7.为达到以上目的,本发明采取的技术方案是:
8.一种耐高温碳密封涂覆光纤,其特征在于:光纤结构由从内而外依次包括光纤本体1、非晶态碳密封层2、硅代聚酰亚胺涂覆层3;所述非晶态碳密封层2其厚度为20nm~50nm。
9.进一步的,所述光纤本体1为弯曲不敏感波导结构。
10.进一步的,所述硅代聚酰亚胺涂覆层3直径为90μm~155μm。
11.一种耐高温碳密封涂覆光纤的制作方法,其特征在于:包括了如下步骤:
12.步骤1:将用于拉制光纤本体1的预制棒送进拉丝机的拉丝炉中,利用拉丝炉将预制棒加热至2000℃以上,通过高温熔融牵引成纤,拉制成为弯曲不敏感波导结构的光纤;
13.步骤2:将上述步骤1形成的光纤本体1穿过原位高温气相碳层沉积装置,沉积装置内事先通入含有不少于1种的含碳元素化合物气溶胶,通过原位高温裂解析碳沉积法,将上述含碳元素化合物气溶胶发生高温裂解反应,在光纤本体1表面沉积非晶态碳密封层2,通过调节沉积装置内的含碳元素化合物气体浓度以及光纤本体1在沉积装置中的停留时间,可以实现在光纤本体1表面制备厚度为20nm~50nm不同厚度的非晶态碳密封层(2);
14.步骤3:将上述步骤2形成的具有非晶态碳密封层2的光纤采用低速拉丝在线浸润热固化涂覆工艺在光纤表面浸润包裹液态的硅代聚酰亚胺耐高温复合材料;
15.步骤4:对上述步骤3形成的包裹有液态的硅代聚酰亚胺耐高温复合材料的碳密封涂覆光纤采用分段热固化炉进行梯度加热,使得包裹在光纤表面的液态硅代聚酰亚胺耐高温复合材料转化成固态,形成硅代聚酰亚胺涂覆层3。
16.本发明对比现有技术有如下的有益效果:
17.采用本发明制备的耐高温碳密封涂覆光纤,其采用了厚度为20nm~50nm的非晶态碳密封层,从而具有更高的致密性和柔韧性,光纤动态疲劳系数至210以上,能有效提高光纤使用生命和可靠性,在高压富氢环境下具有显著的抗氢损效果,光纤的本体吸收损耗无明显增加;外部涂覆层采用硅代聚酰亚胺涂覆层,复合了硅烷键柔弹性和传统聚酰亚胺耐高温特性,可减少光纤微弯,通过单层涂覆既可兼顾光纤较低的衰减系数和较高的耐温等级。
附图说明
18.图1为本发明的光纤结构示意图;
19.图2为本发明的光纤本体边缘和非晶态碳密封层能谱仪元素分布测试图;
20.图3为本发明的光纤本体扫描电镜测试全貌图;
21.图4为本发明的非晶态碳密封层扫描电镜测试局部放大图。
22.附图标记说明:
23.1、光纤本体;2、非晶态碳密封层;3、硅代聚酰亚胺涂覆层。
具体实施方式
24.为了使本发明的目的技术方案以及优点更清楚地被理解,现结合附图及实施例对本发明做进一步详细说明。
25.由于碳密封涂覆光纤通过特殊的碳密封涂覆工艺在光纤表面形成致密的碳层,减缓光纤表面微裂纹生长,将光纤表面与环境密封隔离,阻止水分和氢对光纤机械强度和光学性能的影响,降低光纤在高湿度、高压环境下氢渗透而引起的传输损耗增加,提高光纤的耐疲劳性能和应力腐蚀敏感性参数,从而提高光纤的使用寿命和可靠性(如以下公式所示)。
[0026][0027]
式中:ts为光纤寿命(单位s),tp为筛选时间(单位s),m为光纤强度分布曲线weibull分布曲线的斜率,n为疲劳系数,np为筛选时断裂次数(次/km),l为光纤长度(km),f为允许断裂概率,σp为筛选后最小强度,σs为静态应力强度(使用应力)。
[0028]
故本发明的工作原理为:
[0029]
首先,通过原位高温裂解析碳沉积法在光纤本体1表面沉积厚度较厚的非晶态碳密封层2,形成的光纤结构见图1所示。在图1中,光纤结构从内到外依次为石英波导制备的光纤本体1、非晶态碳密封层2、硅代聚酰亚胺涂覆层3。如图2所示光纤本体边缘和非晶态碳密封层能谱仪元素分布测试图所示,从光纤本体向其边缘外侧扫描,作为光纤本体1主要材料石英的化学元素硅(si)氧(o)的信号强度降低,而碳(c)的信号强度增加,表明光纤本体1表面含有非晶态碳密封层2,其厚度达到20nm~50nm,如图3和图4所示。按gb/t 15972.33-2008《光纤试验方法规范第33部分:机械性能的测量方法和试验程序——应力腐蚀敏感性参数》进行测试,光纤的动态疲劳参数(即:动态n值)达到200以上。
[0030]
在上述技术方案基础上,所述光纤本体1直径为78μm~82μm时,硅代聚酰亚胺涂覆层3直径为90μm~110μm,所述光纤本体1直径为123μm~127μm时,硅代聚酰亚胺涂覆层3直径为135μm~155μm。
[0031]
所述硅代聚酰亚胺涂覆层3是通过光纤拉丝在线单层薄壁涂覆法在非晶态碳密封层2表面涂覆,并使用分段热固化炉将其由液态固化为固态。所述硅代聚酰亚胺涂覆层3是一种玻璃化温度(tg)间于200℃~300℃,杨氏模量为2gpa的耐高温复合材料。所述硅代聚酰亚胺复合了硅烷键柔弹性和传统聚酰亚胺耐高温特性,当涂覆了所述硅代聚酰亚胺的光纤工作在300℃高温环境下时,此时因环境温度高于硅代聚酰亚胺的玻璃化温度(tg),其处于高弹态,相比普通聚酰亚胺材料更具柔韧性,减少光纤微弯,在通过单层涂覆即可兼顾光纤较低的衰减系数和较高的耐温等级。
[0032]
本发明中光纤的制作方法包括以下步骤:
[0033]
步骤1:在拉丝机所在塔架的合适位置事先安装分段热固化炉;
[0034]
步骤2:在拉丝机的裸纤测径仪下方且靠近分段热固化炉上方位置,安装事先设计加工好的用于一次涂覆杯和一次涂覆模具;
[0035]
步骤3:在拉丝机所在塔架的合适位置安装事先设计加工好的原位高温气相碳层沉积装置;
[0036]
步骤4:将用于拉制光纤本体的光纤预制棒夹装于拉丝机送棒装置;
[0037]
步骤5:将预制棒送进拉丝机的拉丝炉中,加热熔融并在重力作用下牵引成纤;
[0038]
步骤6:将上述步骤5形成的光纤本体1穿过步骤3所述的原位高温气相碳层沉积装置,通过原位高温裂解析碳沉积法在光纤本体1外面制备非晶态碳密封层2;
[0039]
步骤7:将上述步骤6形成的具有非晶态碳密封层2的光纤穿过步骤2所述的一次涂覆模具,并在一次涂覆杯中加入硅代聚酰亚胺耐高温复合材料液体,通过一定压力挤料,在光纤表面包裹液态的硅代聚酰亚胺耐高温复合材料;
[0040]
步骤8:用步骤1所述的分段热固化炉对上述步骤7形成的包裹有液态的硅代聚酰亚胺耐高温复合材料的碳密封涂覆光纤进行梯度加热,使得包裹在光纤表面的液态硅代聚酰亚胺耐高温复合材料转化成固态。
[0041]
实施例一:光纤本体1标称直径为80μm、涂覆层标称直径为105μm的耐高温碳密封涂覆光纤。
[0042]
该实施例中的光纤制备步骤如下:
[0043]
步骤1:在拉丝机所在塔架的合适位置事先安装6段式的分段热固化炉;
[0044]
步骤2:在拉丝机的裸纤测径仪下方且靠近分段热固化炉上方位置,安装事先设计加工好的用于一次涂覆杯和一次涂覆模具,模具孔径为208μm;
[0045]
步骤3:在拉丝机所在塔架的合适位置安装事先设计加工好的原位高温气相碳层沉积装置;
[0046]
步骤4:将用于拉制光纤本体1的细径弯曲不敏感光纤预制棒夹装于拉丝机送棒装置;
[0047]
步骤5:将预制棒送进拉丝机的拉丝炉中,在2150℃高温下加热熔融,并在重力作用下牵引成纤;
[0048]
步骤6:将上述步骤5形成的光纤本体1穿过步骤3所述的原位高温气相碳层沉积装置,通过原位高温裂解析碳沉积法在光纤本体1外面制备非晶态碳密封层2;通过调节沉积装置内的含碳元素化合物气体浓度为75%(v%)以及光纤本体1在沉积装置中的停留时间为6s,实现在光纤本体1表面制备非晶态碳密封层2;
[0049]
步骤7:将上述步骤6形成的具有非晶态碳密封层2的光纤穿过步骤2所述的一次涂覆模具,并在一次涂覆杯中加入硅代聚酰亚胺耐高温复合材料液体,通过0.03mpa压力挤料,采用低速拉丝在线浸润热固化涂覆工艺在光纤表面浸润包裹液态的硅代聚酰亚胺耐高温复合材料;
[0050]
步骤8:用步骤1所述的6段式分段热固化炉对上述步骤7形成的包裹有液态的硅代聚酰亚胺耐高温复合材料的碳密封涂覆光纤进行从150℃至450℃线性梯度加热,使得包裹在光纤表面的液态硅代聚酰亚胺耐高温复合材料转化成固态,形成硅代聚酰亚胺涂覆层3。
[0051]
制作的光纤,经测试,光纤本体1直径为79.8μm,非晶态碳密封层2厚度为20.27nm,硅代聚酰亚胺涂覆层3直径为103.8μm,光纤的动态疲劳系数为216,光纤在常温下的衰减系数为0.306db/km@1550nm,光纤经过250小时300℃环境高温寿命老化后的衰减系数为0.309db/km@1550nm。该300℃碳密封涂覆φ79.8μm光纤经过144小时、1.2mpa连续载氢试验前后与同类型300℃非涂碳光纤的吸收损耗情况对比如表1所示。
[0052]
表1实施例一载氢前后吸收损耗情况对比
[0053][0054][0055]
实施例二:光纤本体1标称直径为125μm、涂覆层标称直径为145μm的耐高温碳密封涂覆光纤。
[0056]
该实施例中的光纤制备步骤如下:
[0057]
步骤1:在拉丝机所在塔架的合适位置事先安装6段式的分段热固化炉;
[0058]
步骤2:在拉丝机的裸纤测径仪下方且靠近分段热固化炉上方位置,安装事先设计加工好的用于一次涂覆杯和一次涂覆模具,模具孔径为220μm;
[0059]
步骤3:在拉丝机所在塔架的合适位置安装事先设计加工好的原位高温气相碳层沉积装置;
[0060]
步骤4:将用于拉制光纤本体1的细径弯曲不敏感光纤预制棒夹装于拉丝机送棒装置;
[0061]
步骤5:将预制棒送进拉丝机的拉丝炉中,在2160℃高温下加热熔融,并在重力作用下牵引成纤;
[0062]
步骤6:将上述步骤5形成的光纤本体1穿过步骤3所述的原位高温气相碳层沉积装置,通过原位高温裂解析碳沉积法在光纤本体1外面制备非晶态碳密封层2;通过调节沉积装置内的含碳元素化合物气体浓度为83%(v%)以及光纤本体1在沉积装置中的停留时间为9s,实现在光纤本体1表面制备非晶态碳密封层2;
[0063]
步骤7:将上述步骤6形成的具有非晶态碳密封层2的光纤穿过步骤2所述的一次涂覆模具,并在一次涂覆杯中加入硅代聚酰亚胺耐高温复合材料液体,通过0.04mpa压力挤料,采用低速拉丝在线浸润热固化涂覆工艺在光纤表面浸润包裹液态的硅代聚酰亚胺耐高温复合材料;
[0064]
步骤8:用步骤1所述的6段式分段热固化炉对上述步骤7形成的包裹有液态的硅代聚酰亚胺耐高温复合材料的碳密封涂覆光纤进行从150℃至450℃线性梯度加热,使得包裹在光纤表面的液态硅代聚酰亚胺耐高温复合材料转化成固态,形成硅代聚酰亚胺涂覆层3。
[0065]
制作的光纤,经测试,光纤本体1直径为125.1μm,非晶态碳密封层2厚度为29.62nm,硅代聚酰亚胺涂覆层3直径为145.3μm,光纤的动态疲劳系数为253,光纤在常温下的衰减系数为0.282db/km@1550nm,光纤经过250小时300℃环境高温寿命老化后的衰减系数为0.286db/km@1550nm。该300℃碳密封涂覆φ125.1μm光纤经过144小时、1.2mpa连续载氢试验前后与同类型300℃非涂碳光纤的吸收损耗情况对比如表2所示。
[0066]
表2实施例二载氢前后吸收损耗情况对比
[0067][0068]
以上所述实施例的实施方式仅用来说明本发明,而并非对本发明的限制,任何熟悉本技术领域的技术人员,在不脱离本发明揭露的技术范围内,可做出各种各样的变型、变化或替换,因此所有等同类似的技术方法都应涵盖在本发明的专利保护范围之内。