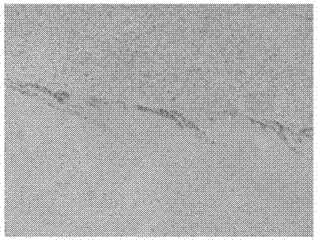
本发明属于金属焊接
技术领域:
,具体为一种塞钉式钛合金板材搅拌摩擦点焊方法。
背景技术:
目前,搅拌摩擦点焊(fssw)技术在铝、镁等轻合金材料方面的焊接研究和应用比较多。但是,由于传统的搅拌摩擦焊技术的焊具都是一体式搅拌头,搅拌头上都带有一定长度的搅拌针,所以在焊缝末端都会留下一个与搅拌针尺寸形状类似的“匙孔”。匙孔的存在降低了焊缝的相对有效宽度,并减小了搭接剪切强度和抗拉强度,降低了焊接质量和构件的安全性。基于此,人们提出了许多新的无匙孔或消除匙孔的搅拌摩擦焊接方法:如德国gkss在1999年提出了一种新的焊接方法——回填式搅拌摩擦点焊技术,该方法采用分离的搅拌针、搅拌套和压紧套,通过精确控制搅拌针、搅拌套和压紧套的相对运动,在点焊工具回撤的同时填充材料,焊点中心没有匙孔;如对于板材零件焊缝的起始点和收尾处的匙孔,则采用引出法消除匙孔——即在搅拌摩擦焊的起焊和收焊的位置设置起焊板和引出板,起焊板和引出板并列平行放置在被焊零件的起始端和末端,焊接起焊点从起焊板上开始,终点在引出板上,将匙孔引出到被焊零件以外,然后从零件上切除起焊板和引出板,达到被焊零件无匙孔的效果。但是这种方法对搅拌摩擦点焊却无法消除匙孔;对于环形焊缝,美国nasa开发出伸缩式搅拌头焊接法——即搅拌头在焊接过程中,搅拌针与轴肩同时旋转,搅拌针与轴肩是分离的,到达焊缝末端,搅拌针受到轴向的提升作用,搅拌针逐渐缩短,焊缝的深度也逐渐变浅,当搅拌针与轴肩端面平齐时,焊缝上就不存在搅拌针留下的收焊匙孔,从而消除收焊“匙孔”。同样该方法也不能有效消除搅拌摩擦点焊的匙孔。近年来还开发了诸如熔焊填补法、摩擦塞焊法、填充式搅拌摩擦塞补焊、铆接法等消除焊后匙孔的方法,这些技术在一定程度上都成功的解决了铝、镁合金fsw焊接的匙孔问题。如申请号为cn200910308559.x的专利采用了一种填充式搅拌摩擦塞补焊方法对匙孔进行填补,首先将存在的匙孔通过钻孔方式铣成锥孔,塞棒夹持部位做成圆柱体,将其前端加工成与锥孔匹配的形状,在适当的压力作用下高速旋转,塞棒边旋转边下降,塞棒端部与孔底及侧壁摩擦,使塞棒材料塑化,塑化材料的逐层堆积,填满匙孔,此时塞棒停转,并施以一定的压力,完成整个塞焊过程。申请号为cn201010136834.7的专利采用了一种先用传统的一体式搅拌摩擦焊具进行点焊,然后用组合式焊具进行二次焊接以塞补焊接匙孔的方法,分两步焊接实现了无匙孔点焊。但是这种方法一方面焊接过程复杂,更换补焊材料困难,不便于批量化生产;其次该焊具缺乏气氛保护装置,无法对钛合金材料实施焊接。因为钛合金材料在500℃以上极易与空气中的氧、氮、氢气体发生反应而是性能下降,因此钛合金材料必须在一定的气氛保护状态才能实施焊接。以上方法在一定程度上,都能有效解决铝、镁合金等轻金属的搅拌摩擦焊的“匙孔”问题,但这些方法对熔点较高、塑性流动性较差的钛、钛合金等材料的搅拌摩擦焊接,尤其是搅拌摩擦点焊焊接中的匙孔,则难以实现“匙孔”的有效去除。因此,目前fsw技术在钛合金材料搅拌焊接方面的应用研究还不够成熟,尤其是搅拌摩擦点焊(fssw)和摩擦塞点焊技术在钛合金板材搭接焊接上的应用研究还比较少。技术实现要素:发明目的:为了克服现有技术中存在的不足,本发明目的是提供一种塞钉式钛合金板材搅拌摩擦点焊方法。技术方案:本发明所述的一种塞钉式钛合金板材搅拌摩擦点焊方法,包括以下步骤:a、加工点焊预置孔:将待点焊的钛合金板材搭接固定在焊机工作台上,对板材夹紧并定位,用扩孔钻对母材的施焊部位进行钻孔处理,加工一个凹锥形预置孔并用压缩空气吹扫以清理碎屑和油污,凹形锥孔的上开口直径为上层板材的厚度的1-3倍,下开口直径为上层板材的厚度的0.5-1倍,总深度为上层板材的厚度的1.9-3倍;b、焊接:依据焊件厚度,选择尺寸匹配的焊接锥形塞钉,锥形塞钉的轮廓尺寸略大于凹锥形预置孔的轮廓尺寸,材质选与母材相同牌号或硬度相近的同类型牌号钛合金材料,将锥形塞钉装入焊具的搅拌头,在纯度≥99.9%、进气流量为1.5-2.0l/min的氩气保护气氛下,启动搅拌头以600-1000r/min的转速和1-3mm/min的下压进给速度,将塞钉旋压压入被焊材料的预置孔中,将塞钉旋转扎入到预置孔中进行搅拌摩擦焊接3-10s,焊接完成瞬间即当搅拌头的下表面与母材上表面接触时(允许有0.1-0.5mm的下压量),搅拌头停止旋压进给,继续原位旋转搅拌3-10s后停止,并立即通过镍基耐高温合金材料制成的搅拌头对施焊区域进行载荷为20-30kn的静压顶锻10-20s,使得焊接区域的材料组织致密化,镍基耐高温合金材料的型号为gh4033、gh4037、gh4049或gh4080;c、移除焊具并清理:关闭保护气,卸载焊具,用砂轮打磨去除残余塞钉尾部和飞边,使焊点表面光滑美观,施焊完成。有益效果:本发明和现有技术相比,具有如下显著性特点:本发明焊接过程能耗低,无污染、无气孔、变形小;本发明的焊具结构简单,操作方便,可循环使用;本发明的塞钉结构合理,不但节省焊接材料,而且批量生产过程中塞钉更换方便,不需要更换焊具,焊接生产效率高;本发明焊后材料表面无匙孔、无剪薄或剪薄量极小,组织结构致密,机械性能优良,易于实现工业化生产;本发明有便捷的气氛保护装置,有效防护钛合金材料焊接过程有害气体的渗入;本发明的方法还可以用于钛及钛合金材料普通搅拌摩擦焊接后的匙孔填补、钛合金材料表面微区缺陷和其他焊缝缺陷的修复。附图说明图1是本发明的结构示意图。图2是本发明的组合式焊具的结构示意图。图3是本发明的塞钉和凹形预置孔的结构匹配示意图。图4是本发明的钛合金板点焊接头金相图。具体实施方式如图1-3,本实施例中所用的塞钉2一端被夹紧在搅拌头1内,另一端被旋压进钛合金板4的凹形预置孔7,氩气保护系统3的出气口对准施焊处。焊具为组合式焊具,包括套筒5、搅拌头1和锁紧螺母6,其中套筒5和锁紧螺母6的材质为碳素工具钢,优选为t10a,搅拌头1的材质为镍基耐高温合金,优选的牌号是gh4033、gh4037、gh4049或gh4080镍基高温合金,搅拌头1为可循环使用部件,搅拌头1轴肩表面损伤后,打磨修复可重复使用。塞钉2的结构主要分夹持端和锥体两部分,塞钉2按锥体结构又分为圆锥形塞钉2和阶梯型塞钉2两种,选用的依据主要取决于待焊母材的厚度,圆锥型塞钉2主要用于薄板(2-4mm),较厚材料(≥4mm)焊接通常选用阶梯型塞钉2。实施例1塞钉式钛合金搅拌摩擦点焊方法的实施工序为:(1)先将需要点焊的钛合金板4在焊机上固定定位,确保焊接过程中上下层母材间不发生胀形和移动,并移动焊机工作台位置以确定点焊施焊点位,用锥形钻头对母材施焊点位加工一个凹锥形预置孔7,并用压缩空气吹扫清理预置孔7使其表面无碎屑、无油污,以施焊区域上层板材的厚度为h,凹形锥孔的上开口直径取1h,深度通常取1.9h,通常为凹形盲孔;(2)以预置孔7内径和深度为基准,按体积充满原则和界面紧密贴合的原则制备和选择匹配型号的塞钉2,按照塞钉2锥形轮廓尺寸略大于凹形预置孔7尺寸、塞钉2顶尖先接触预置孔7底部的要求去设计塞钉2尺寸,从而保证焊接完成后,塞钉2能够完全填充满凹形预置孔7,且锥孔底部没有孔洞缺陷,而且在搅拌焊接的过程中,塞钉2锥面能与预置孔7内表面紧密贴合,以产生足够的摩擦热量,塞钉2为焊接耗材,焊接过程中,塞钉2与母材预置孔7周围的金属搅拌摩擦塑化后,最终被填充于预置孔7内,塞钉2的锥体部分长度要略大于凹形预置孔7深度,以保证焊后在锥孔底部没有孔洞,塞钉2的材质可以选与硬度相近的同类型牌号钛合金材料,也可选硬度相近的同类型牌号钛合金材料;(3)焊接前需将塞钉2预置入搅拌头1的夹持体内并夹紧,夹持的力度和深度以确保启动搅拌头1旋转过程中,塞钉2不脱落为准,焊接前还需开启氩气保护气阀门,通入保护氩气(纯度≥99.9%),进气流量为1.5l/min,确保焊接区域在氩气保护氛围下施焊,防止氧、氮、氢等气体在高温下融入焊缝组织;(4)启动焊具旋转,按工艺要求,在600转/分钟的旋转速度下,让焊具带着塞钉2旋转下压,下压进给速度为1mm/min,将塞钉2旋压进入母材预置孔7中,利用塞钉2外轮廓与凹型预置孔7内轮廓界面间摩擦的摩擦热,使得塞钉2和预置孔7的接触面产热并塑化,在轴向进给力的作用下,使塞钉2边搅拌摩擦边往预置孔7中旋压;(5)焊具搅拌头1夹持体的下表面(即轴肩)下压到与钛合金母材上表面接触时(允许下压量0.1-1.0mm),焊具停止轴向进给,原位旋转搅拌摩擦3s,让搅拌头1轴肩对钛合金材料进一步充分摩擦、搅拌,使塞钉2与预置孔7周围的材料进一步受热塑化、搅拌变形并充分融合,实现上下层母材与塞钉2界面的致密结合;(6)搅拌焊接完成后,焊具停止旋转,同时立即通过机床主轴对焊具施加20kn的轴向载荷,利用搅拌头1轴肩对施焊区域进行静压顶锻,使焊接区的塑化材料组织更加致密,静压顶锻时间约10s;(7)顶锻结束后,关闭保护气阀门,移除保护气罩和焊具,用砂轮打磨去除点焊区域的飞边和塞钉2的残留夹持柄,使点焊区域表面光滑美观。本发明的方法还可以用于钛及钛合金材料普通搅拌摩擦焊接后的匙孔填补、钛合金材料表面微区缺陷和其他焊缝缺陷的修复。实施例2塞钉式钛合金搅拌摩擦点焊方法的实施工序为:(1)先将需要点焊的钛合金板4在焊机上固定定位,确保焊接过程中上下层母材间不发生胀形和移动,并移动焊机工作台位置以确定点焊施焊点位,用锥形钻头对母材施焊点位加工一个凹锥形预置孔7,并用压缩空气吹扫清理预置孔7使其表面无碎屑、无油污,以施焊区域上层板材的厚度为h,凹形锥孔的上开口直径取3h,深度通常取3h,通常为凹形盲孔;(2)以预置孔7内径和深度为基准,按体积充满原则和界面紧密贴合的原则制备和选择匹配型号的塞钉2,按照塞钉2锥形轮廓尺寸略大于凹形预置孔7尺寸、塞钉2顶尖先接触预置孔7底部的要求去设计塞钉2尺寸,从而保证焊接完成后,塞钉2能够完全填充满凹形预置孔7,且锥孔底部没有孔洞缺陷,而且在搅拌焊接的过程中,塞钉2锥面能与预置孔7内表面紧密贴合,以产生足够的摩擦热量,塞钉2为焊接耗材,焊接过程中,塞钉2与母材预置孔7周围的金属搅拌摩擦塑化后,最终被填充于预置孔7内,塞钉2的锥体部分长度要略大于凹形预置孔7深度,以保证焊后在锥孔底部没有孔洞,塞钉2的材质可以选与硬度相近的同类型牌号钛合金材料,也可选硬度相近的同类型牌号钛合金材料;(3)焊接前需将塞钉2预置入搅拌头1的夹持体内并夹紧,夹持的力度和深度以确保启动搅拌头1旋转过程中,塞钉2不脱落为准,焊接前还需开启氩气保护气阀门,通入保护氩气(纯度≥99.9%),进气流量为2.0l/min,确保焊接区域在氩气保护氛围下施焊,防止氧、氮、氢等气体在高温下融入焊缝组织;(4)启动焊具旋转,按工艺要求,在600-1000转/分钟的旋转速度下,让焊具带着塞钉2旋转下压,下压进给速度为2mm/min,将塞钉2旋压进入母材预置孔7中,利用塞钉2外轮廓与凹型预置孔7内轮廓界面间摩擦的摩擦热,使得塞钉2和预置孔7的接触面产热并塑化,在轴向进给力的作用下,使塞钉2边搅拌摩擦边往预置孔7中旋压;(5)焊具搅拌头1夹持体的下表面(即轴肩)下压到与钛合金母材上表面接触时(允许下压量0.1-1.0mm),焊具停止轴向进给,原位旋转搅拌摩擦10s,让搅拌头1轴肩对钛合金材料进一步充分摩擦、搅拌,使塞钉2与预置孔7周围的材料进一步受热塑化、搅拌变形并充分融合,实现上下层母材与塞钉2界面的致密结合;(6)搅拌焊接完成后,焊具停止旋转,同时立即通过机床主轴对焊具施加30kn的轴向载荷,利用搅拌头1轴肩对施焊区域进行静压顶锻,使焊接区的塑化材料组织更加致密,静压顶锻时间约20s;(7)顶锻结束后,关闭保护气阀门,移除保护气罩和焊具,用砂轮打磨去除点焊区域的飞边和塞钉2的残留夹持柄,使点焊区域表面光滑美观。本发明的方法还可以用于钛及钛合金材料普通搅拌摩擦焊接后的匙孔填补、钛合金材料表面微区缺陷和其他焊缝缺陷的修复。实施例3塞钉式钛合金搅拌摩擦点焊方法的实施工序为:(1)先将需要点焊的钛合金板4在焊机上固定定位,确保焊接过程中上下层母材间不发生胀形和移动,并移动焊机工作台位置以确定点焊施焊点位,用锥形钻头对母材施焊点位加工一个凹锥形预置孔7,并用压缩空气吹扫清理预置孔7使其表面无碎屑、无油污,以施焊区域上层板材的厚度为h,凹形锥孔的上开口直径取1.5h,深度通常取2.5h,通常为凹形盲孔;(2)以预置孔7内径和深度为基准,按体积充满原则和界面紧密贴合的原则制备和选择匹配型号的塞钉2,按照塞钉2锥形轮廓尺寸略大于凹形预置孔7尺寸、塞钉2顶尖先接触预置孔7底部的要求去设计塞钉2尺寸,从而保证焊接完成后,塞钉2能够完全填充满凹形预置孔7,且锥孔底部没有孔洞缺陷,而且在搅拌焊接的过程中,塞钉2锥面能与预置孔7内表面紧密贴合,以产生足够的摩擦热量,塞钉2为焊接耗材,焊接过程中,塞钉2与母材预置孔7周围的金属搅拌摩擦塑化后,最终被填充于预置孔7内,塞钉2的锥体部分长度要略大于凹形预置孔7深度,以保证焊后在锥孔底部没有孔洞,塞钉2的材质可以选与硬度相近的同类型牌号钛合金材料,也可选硬度相近的同类型牌号钛合金材料;(3)焊接前需将塞钉2预置入搅拌头1的夹持体内并夹紧,夹持的力度和深度以确保启动搅拌头1旋转过程中,塞钉2不脱落为准,焊接前还需开启氩气保护气阀门,通入保护氩气(纯度≥99.9%),进气流量为1.7l/min,确保焊接区域在氩气保护氛围下施焊,防止氧、氮、氢等气体在高温下融入焊缝组织;(4)启动焊具旋转,按工艺要求,在800转/分钟的旋转速度下,让焊具带着塞钉2旋转下压,下压进给速度为1.5mm/min,将塞钉2旋压进入母材预置孔7中,利用塞钉2外轮廓与凹型预置孔7内轮廓界面间摩擦的摩擦热,使得塞钉2和预置孔7的接触面产热并塑化,在轴向进给力的作用下,使塞钉2边搅拌摩擦边往预置孔7中旋压;(5)焊具搅拌头1夹持体的下表面(即轴肩)下压到与钛合金母材上表面接触时(允许下压量0.1-1.0mm),焊具停止轴向进给,原位旋转搅拌摩擦7s,让搅拌头1轴肩对钛合金材料进一步充分摩擦、搅拌,使塞钉2与预置孔7周围的材料进一步受热塑化、搅拌变形并充分融合,实现上下层母材与塞钉2界面的致密结合;(6)搅拌焊接完成后,焊具停止旋转,同时立即通过机床主轴对焊具施加25kn的轴向载荷,利用搅拌头1轴肩对施焊区域进行静压顶锻,使焊接区的塑化材料组织更加致密,静压顶锻时间约15s;(7)顶锻结束后,关闭保护气阀门,移除保护气罩和焊具,用砂轮打磨去除点焊区域的飞边和塞钉2的残留夹持柄,使点焊区域表面光滑美观。本发明的方法还可以用于钛及钛合金材料普通搅拌摩擦焊接后的匙孔填补、钛合金材料表面微区缺陷和其他焊缝缺陷的修复。实施例4选用厚度为4mm厚(实测厚度为4.01mm)的陕西宝钛ta1板材进行施焊,将钛板剪成200mm*100mm的条形试样,选用标准阶梯型同材质的塞钉2进行搅拌摩擦点焊,塞钉2为与母材同材质的ta1钛合金,焊具搅拌头1选用平面轴肩搅拌头1,焊具搅拌头1和塞钉2的尺寸形状如表1所示,焊接工艺参数如表2所示,其中,d1为搅拌头1夹持体直径,d1为搅拌头1轴肩直径,l为搅拌头1轴肩锥体部分长度,d2为塞钉2锥体大端直径,d2为塞钉2锥体小端直径,l1为塞钉2锥体大端长度,l2为塞钉2锥体小端长度。表1搅拌头及塞钉形状和尺寸名词材质形状/mm锥度搅拌头gh4049d1=20,d1=16,l=75°塞钉ta1d2=6,d2=3,l1=5,l2=318°表2搅拌摩擦点焊工艺参数工艺主轴转速扎入下压速度下压量停留搅拌时间搅拌摩擦点焊700r/min1.5mm/min0.5mm10s为了评定钛合金点焊接头的性能,采用点焊接头剪切拉伸实验进行接头性能评测,以评价焊接效果。对点焊后的试样以焊点直径为中心,垂直于焊缝方向,截取40*200mm的长条形试样,然后按国标要求加工成标准拉伸试样,同时对点焊结构进行纵向刨切取样,进行金相检验分析,以检验组织的致密性。焊后的抗剪拉伸试样和试样金相如图4所示,从检验结果可见,点焊后材料表面成形性好,无明显宏观和微观缺陷,组织致密,钛合金板4与塞钉2间的界面结合良好,内部组织无孔洞缺陷,力学性能尚能达到同截面母材强度的90%。当前第1页12