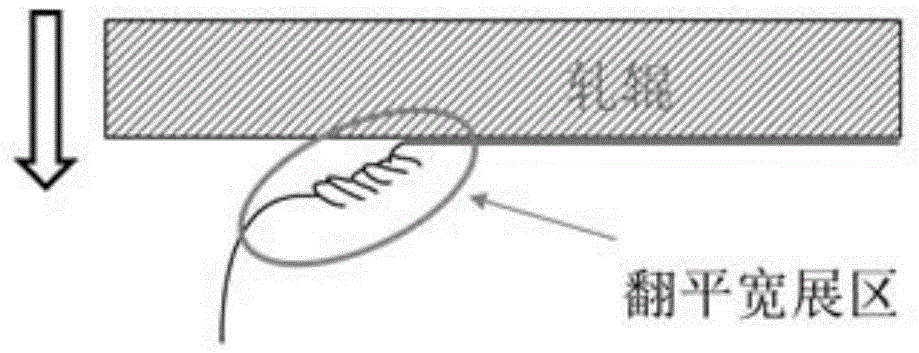
本发明属于热轧管线钢产品表面处理
技术领域:
,具体涉及一种减小热轧管线钢边部发纹缺陷宽度的制造方法。
背景技术:
:热轧管线钢板卷广泛用于石油、天然气输送,是国家能源动脉的基础工程,一般以热轧原卷交货,下游用户采用螺旋埋弧焊方式进行制管目前采用常规工艺生产的热轧管线钢边部发纹普遍较宽(10~25mm),会造成下游用户使用过程中加大切除量或无法去除,一方面增加客户使用难度,降低成材率,增加成本;另一方面可能因发纹缺陷造成产品质量问题而判废,甚至造成管道爆炸等重大安全事故。因此,减小发纹宽度对于提高产品成材率、产品质量,保障产品服役安全性具有重要意义。关于发纹的产生原因业界已基本达成共识,认为主要是轧制过程中带钢棱边由于二维传热导致该部位温度较低,塑性差,厚度方向的金属轧制过程中部分翻平至钢板表面所产生,示意图如图1所示。因此减小热轧带钢边部发纹宽度主要是从两个方面入手:1)减小铸坯到成品的总压缩比;2)改善带钢轧制过程边部温降大的特点,促进铸坯厚度方向的金属更多的流向轧制方向。经检索,本发明申请之前,申请公布号为cn107096795a中国专利公开了一种减小热轧带钢边部缺陷的制造方法。其仅通过改变优化粗轧负荷分配及减小立辊冷却水的方法,降低边部温降来减小边部缺陷,从其实施效果来看:边部缺陷改判量仅降低60%,而且并未具体量化缺陷减小的程度,难以达不到有效控制边部发纹缺陷的目的。另有,申请公布号为cn106734370a的中国专利公开了一种防止宽规格钢板边部产生折叠的方法,其针对宽厚板轧制中宽展比(成品宽度/铸坯宽度)≥1.5的钢板采取用液化气喷枪进行倒角方式进行清理,一方面该方法仅适用于宽板生产(热轧带钢宽展比≤1.0),另一方面采用人工清理,不仅效率低,人工成本高,而且工作环境恶劣。技术实现要素:本发明的目的在于,针对现有技术的不足,提供一种可将发纹宽度控制在小于5mm范围内的减小热轧管线钢边部发纹缺陷宽度的方法。本发明采用的技术方案为:一种减小热轧管线钢边部发纹缺陷宽度的制造方法,包括以下步骤:步骤一、采用边部形状为钝角状的连铸坯;步骤二、将连铸坯加热至目标加热温度;步骤三、连铸坯出炉除鳞;步骤四、对连铸坯进行定宽侧压;步骤五、连铸坯多道次粗轧,出粗轧后扣罩保温;步骤六、连铸坯精轧;步骤七、冷却连铸坯至目标冷却温度500~600℃。步骤八、将已制造完成的带钢卷成钢卷。按上述方案,在步骤一中,连铸坯边部的钝角角度为125~135°。按上述方案,在步骤三中,在连铸坯除鳞的同时对连铸坯两侧边部进行遮挡。按上述方案,采取弧形定宽机定宽,且弧形定宽机对连铸坯的单边侧压量小于20mm。按上述方案,在步骤五中,粗轧的总压缩比小于70%按上述方案,在步骤五中,采用7道次可逆轧制,其中第1,3,5,7道次轧制时开除鳞水,各道次的压下率分别为粗轧总压缩比的30%、25%、15%、10%、8%、8%、4%。按上述方案,在步骤六中,采用7机架精轧机精轧,其中前4机架的活套张力为4~8mpa。按上述方案,在步骤二中,目标加热温度为1210~1250℃。按上述方案,在步骤七中,目标冷却温度为500~600℃。本发明的有益效果为:1)可显著减小热轧管线钢的边部发纹的宽度,基本可消除边部发纹引起的产品质量问题,提高下游用户成材率及生产效率;2)全流程采用机械化控制,不额外增加人力成本,工作环境好,产品质量稳定;3)不改变现有的生产工艺及控制方法,适用大批量稳定化生产;附图说明图1为现有热轧带钢边部发纹产生机理示意图。图2为本发明中钝角连铸坯的结构示意图。图3为本发明中弧形定宽压力机的示意图。具体实施方式为了更好地理解本发明,下面结合附图和具体实施例对本发明作进一步地描述。一种减小热轧管线钢边部发纹缺陷宽度的制造方法,具体包括以下步骤:步骤一、采用弧形连铸坯将连铸坯边部形状由直角状改变成钝角状,钝角角度为125~135°,如图2所示;同时保证连铸坯的宽度超过带钢成品宽度50mm;步骤二、采用步进梁式加热炉将连铸坯加热至目标加热温度,该温度为1210~1250℃;步骤三、连铸坯出加热炉除鳞,除鳞的同时对连铸坯两侧边部进行遮挡;步骤四、采用弧形定宽压力机对连铸坯进行定宽侧压(特定的:此次h≥h),同时单边侧压量≤20mm,如图3所示;步骤五、连铸坯多道次粗轧:粗轧采用多道次可逆轧制;本实施例采用7道次轧制,其中第1,3,5,7道次轧制时开除鳞水,粗轧总压缩比≤70%;各道次的压下率分别为粗轧总压缩比的30%、25%、15%、10%、8%、8%、4%。出粗轧后立即用辊道保温罩进行扣罩保温;步骤六、连铸坯精轧:连铸坯切除舌头后进入多机架精轧机精轧,本实施例中采用7机架精轧机f1~f7,其中前4机架的活套张力f为4~8mpa;步骤七、冷却:精轧结束采用层流冷却系统进行将连铸坯冷却至目标温度,该温度为500~600℃。步骤八、采用卷取机将已制造完成的带钢卷成钢卷。本发明的工作原理为:1)将连铸坯的边部形状由传统的直角状改为钝角状,可明显减缓轧制过程中边部散热的速度,降低了因边部表面温度低、塑性差导致的变形不均匀形成较宽的翻平宽展,继而减小了发纹宽度;同时,采用钝角连铸坯降低了原始铸坯的边部厚度,降低了总压缩比,板厚方向的金属翻平至钢板上表面的程度将明显减轻;2)板坯出炉后由于棱边部位属于二维传热区冷速快,故除鳞过程中对边部进行遮挡,可有效降低边部温降速度,减小带钢边部发纹宽度;3)用弧形定宽机替换直角定宽机,主要是利用弧形模的倒角功能,将钝角连铸坯的棱边部位进一步压制成圆弧状,降低后续轧制过程的散热速度,提高了边部温度;同时,限定定宽侧压量≤20mm,若侧压量过大,则会造成边部金属隆起较高,造成板坯轧制前厚度增加,翻平宽展的程度将进一步加剧,导致带钢发纹宽度增大;4)出轧后保温辊道扣罩,缓解钢坯行走过程中的边部温降;5)粗轧采用多道次,有利于板厚方向的金属更多的流向轧制方向;将粗轧总压缩比控制在70%以下,避免粗轧阶段边部温降大,如总压缩比过大则板坯厚度方向的金属在轧制过程中更容易向宽度方向延伸,形成翻平宽展造成成品发纹宽度增加;同时将粗轧的压下分配向高温段调整,主要是因为温度高边部和心部的温差比较小,更容易促使金属向轧制方向流动。将粗轧中间坯的厚度设计在58-60mm是为了尽可能保留将更多厚度方向的金属留至精轧压缩。6)适当增加精轧机前几个机架的活套张力,利用带张力轧制时,厚度方向的金属受拉应力作用,沿轧向流动阻力减小,从而缩小翻平宽展的量。实施例1~10采用不同连铸坯,分别利用两种方法(利用传统制造方法制造及本发明所述制造方法)制造带钢,并对这两种带钢的质量。各实施例中连铸坯的参数如表1所示;各实施例中的主要工艺参数如表2所示。表1各实施例中的连铸坯及成品情况实施例连铸坯宽度/mm连铸坯厚度/mm连铸坯形状成品宽度/mm11250230钝角120021300230钝角125031400230钝角135041650230钝角160051600230钝角155061800230钝角175071350230钝角130081500230钝角145091600230钝角1550101400230钝角1350表2各实施例的主要工艺参数表3.各实施例的实施效果实施例实施前-发纹宽度/mm实施后—发纹宽度/mm115321633122413151006152718.53.58194918410205各实施例使用传统方法及本发明所述制造方法获得带钢其发纹宽度如表3所示。从表3中可得,利用本发明所述制造方法,热轧管线钢带钢边部发纹宽度大大减小,质量异议率由原来的9%降至0%(2017年武钢曾发生因管线钢边部发纹过宽导致的质量异议,该异议率为9.01%。2018年实施后未发生一起因该问题的质量问题)。本发明实采用的减小热轧带钢宽度的方法适用于所有热轧带钢,并不局限于实施例中所列举的产品。最后应说明的是,以上仅为本发明的优选实施例而已,并不用于限制本发明,尽管参照实施例对本发明进行了详细的说明,对于本领域的技术人员来说,其依然可以对前述各实施例所记载的技术方案进行修改,或者对其中部分技术特征进行等同替换,但是凡在本发明的精神和原则之内,所作的任何修改、等同替换、改进等,均应包含在本发明的保护范围之内。当前第1页12