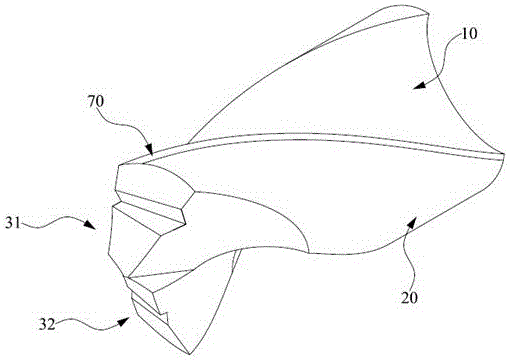
本发明属于钻头
技术领域:
,具体地说,涉及一种高效钻头。
背景技术:
:钻头是一种旋转而头端有切削能力的工具,一般以碳钢,或高速钢等材料经铣制或、轧制或磨制再经淬火,回火热处理后磨制而成,用于金属或其他材料上之钻孔加工,它的使用范围极广,可运用于钻床、车床、铣床、手电钻等工具机上使用。麻花钻是通过其相对固定轴线的旋转切削以钻削工件圆孔的工具。目前对工件进行钻孔加工时,由于麻花钻钻头的钻尖高速钻给,对于工件表面不可避免的会产生诸多毛刺,或造成孔壁粗糙的现象,严重影响孔壁的平整度,对于目前传统的钻头本身的革新尤为重要。技术实现要素:有鉴于此,本发明所要解决的技术问题是提供了一种高效钻头,通过设置独特的钻尖,配合分立两端的且不对称的第一割槽与第二割槽,避免以往钻孔容易造成孔壁粗糙的麻烦。为了解决上述技术问题,本发明公开了一种高效钻头,包括钻杆,钻杆具有两条相对的螺旋排屑槽,且螺旋排屑槽成型裸露出螺旋钻刃,螺旋钻刃在钻杆前端交汇成型出钻尖,钻尖具有分别由两条螺旋钻刃延伸的第一钻尖部与第二钻尖部;其中第一钻尖部具有磨削于其中一个螺旋钻刃前端的第一主切面,与相交的磨削于螺旋钻刃相对后端的第一副切面;第二钻尖部具有磨削于另一个螺旋钻刃前端的第二主切面,与相交的磨削于螺旋钻刃相对后端的第二副切面;其中第一主切面磨削第一割槽,第二主切面磨削第二割槽,第一割槽与第二割槽不关于钻尖中心对称。根据本发明一实施方式,其中上述第一主切面、第一副切面与第二主切面、第二副切面关于钻尖中心对称。根据本发明一实施方式,其中上述第一主切面与第一副切面夹角为钝角。根据本发明一实施方式,其中上述第一割槽截面成三角形,且开口角度在第一主切面上沿切削方向渐小,具有分别位于两端的最小开口角与最大开口角,最小开口角与最大开口角互补。根据本发明一实施方式,其中上述第二割槽截面成三角形,且开口角度在第二主切面上沿切削方向渐小,具有分别位于两端的最小开口角与最大开口角,最小开口角与最大开口角互补。根据本发明一实施方式,其中第一割槽或第二割槽分别将第一主切面或第二主切面分割梯形面或扇形面的截面,且梯形面或扇形面不关于钻尖中心对称。根据本发明一实施方式,最大开口角范围为94°~110°,最小开口角范围为70°~86°。根据本发明一实施方式,其中第一割槽或第二割槽径向宽度小于相邻的梯形面径向宽度。根据本发明一实施方式,其中螺旋钻刃沿切削方向一端具有刃口。与现有技术相比,本发明可以获得包括以下技术效果:通过设置独特的钻尖,配合分立两端的且不对称的第一割槽与第二割槽,避免以往钻孔容易造成孔壁粗糙的麻烦。当然,实施本发明的任一产品必不一定需要同时达到以上所述的所有技术效果。附图说明此处所说明的附图用来提供对本发明的进一步理解,构成本发明的一部分,本发明的示意性实施例及其说明用于解释本发明,并不构成对本发明的不当限定。在附图中:图1是本发明实施例的高效钻头立体图;图2是本发明实施例的高效钻头主视图。附图标记螺旋排屑槽10,螺旋钻刃20,第一钻尖部31,第二钻尖部32,第一主切面41,第一副切面42,第二主切面51,第二副切面52,第一割槽61,第二割槽62,刃口70。具体实施方式以下将配合附图及实施例来详细说明本发明的实施方式,藉此对本发明如何应用技术手段来解决技术问题并达成技术功效的实现过程能充分理解并据以实施。请一并参考图1与图2,图1是本发明实施例的高效钻头立体图;图2是本发明实施例的高效钻头主视图。如图所示,一种高效钻头,包括钻杆,钻杆具有两条相对的螺旋排屑槽10,且螺旋排屑槽10成型裸露出螺旋钻刃20,螺旋钻刃20在钻杆前端交汇成型出钻尖,钻尖具有分别由两条螺旋钻刃20延伸的第一钻尖部31与第二钻尖部32;其中第一钻尖部31具有磨削于其中一个螺旋钻刃20前端的第一主切面41,与相交的磨削于螺旋钻刃20相对后端的第一副切面42;第二钻尖部32具有磨削于另一个螺旋钻刃20前端的第二主切面51,与相交的磨削于螺旋钻刃20相对后端的第二副切面52;其中第一主切面41磨削第一割槽61,第二主切面42磨削第二割槽62,第一割槽61与第二割槽62不关于钻尖中心对称。在本发明一实施方式中,钻杆设置两条相对的螺旋排屑槽10,借此成型出切削进给的螺旋钻刃20,螺旋钻刃20沿切削方向一端具有刃口70。相应的,在螺旋钻刃20的前端通过砂轮磨削,形成钻尖。钻尖包括分立两侧的第一钻尖部31与第二钻尖部32,形成对立,实现进给。其中,第一钻尖部31具有位于螺旋钻刃20前侧端部的第一主切面41,侧向相交有第一副切面42,优选的,第一主切面41与第一副切面42夹角为钝角,开合较大,形成切削方向。第二钻尖部32对应的具有第二主切面51与第二副切面52,优选的,第一主切面41、第一副切面42与第二主切面51、第二副切面52关于钻尖中心对称,保证钻孔时的直线进给,避免错位偏移,在主切削方向上保持稳定。此外,本发明在第一主切面41和第二主切面51上分别磨削不对称的第一割槽61和第二割槽62,形成切棱,加快钻进的效率,同时使得孔壁更为光滑平整,对于毛刺可以有效割除,排屑也加强,大大提高了钻孔成型效率,工艺性更好。具体而言,第一割槽61截面成三角形,且开口角度在第一主切面41上沿切削方向渐小,具有分别位于两端的最小开口角与最大开口角,最小开口角与最大开口角互补。在本实施方式中,三角截面更为锋利,同时位于第一主切面41上的两侧开口渐变处理,应对钻进的切削方向,利用夹角较小的前开口首先冲击,进给切削,然后后端夹角较大的后开口延伸过渡,不断扩大钻进的开口尺寸,辅助前端施力,在螺旋钻刃20的开孔下,继续不断打磨孔壁,提高光滑平整度,较之以往无割槽的麻花钻头,大大提高了孔壁成型后的工艺性,方便实用。而将两侧开口互补处理,实现180°的补偿,共同增殖,限制了渐变的区间,增强了首尾的稳定性。同理,第二割槽62截面成三角形,且开口角度在第二主切面51上沿切削方向渐小,具有分别位于两端的最小开口角与最大开口角,最小开口角与最大开口角互补。第一割槽61或第二割槽62分别将第一主切面41或第二主切面51分割梯形面或扇形面的截面,且梯形面或扇形面不关于钻尖中心对称。本发明的第一割槽61与第二割槽62位置不对称,旨在扩大孔壁加工时的面积,倘若将两个割槽对称处理,则钻进范围有限,孔壁打磨不够充分。优选的,本发明第一割槽61或第二割槽62最大开口角范围为94°~110°,最小开口角范围为70°~86°,渐变区间较小,过渡稳定,在钻进的时候对孔壁的加工更精准。优选的,第一割槽61或第二割槽62径向宽度小于相邻的梯形面径向宽度,保证足够的钻尖宽度,利于钻进。本发明对比其他同尺寸类型钻头在10mm的304不锈钢钢板钻孔,得到下表试验数据:无第一、第二割槽对称的第一、第二割槽截面为正方形的第一、第二割槽宽度保持不变的第一、第二割槽本发明所提供的第一、第二割槽孔壁市面均值(光滑度)市面均值+20%市面均值-20%市面均值+20%市面均值+60%毛刺市面均值市面均值-20%市面均值+20%市面均值-10%市面均值-80%排屑效率市面均值市面均值+20%市面均值-20%市面均值+10%市面均值+50%极限钻孔数量(继续则烧毁)4~8个5~10个4~6个4~7个17~39个由表可知,在钻尖两端磨削出不对称的第一割槽61、第二割槽62之后,能够使得孔壁更为光滑、平整,而且毛刺减少,排屑更为顺畅,钻孔数量明显提升,耐用度大大提高。如此一来,也能相对加快钻孔转速,提升效率,实用性加强。上述说明示出并描述了本发明的若干优选实施例,但如前所述,应当理解本发明并非局限于本文所披露的形式,不应看作是对其他实施例的排除,而可用于各种其他组合、修改和环境,并能够在本文所述发明构想范围内,通过上述教导或相关领域的技术或知识进行改动。而本领域人员所进行的改动和变化不脱离本发明的精神和范围,则都应在本发明所附权利要求的保护范围内。当前第1页12