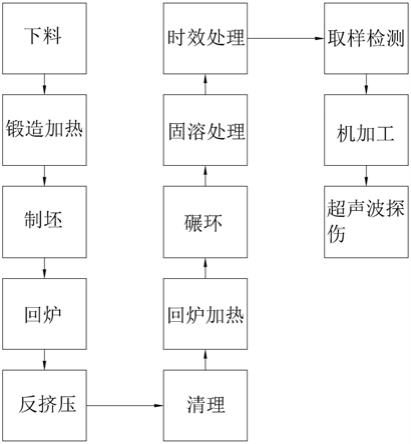
[0001]
本发明涉及铝合金锻造及热处理技术领域,特别涉及一种航天用高性能铝合金筒形锻件制造方法。
背景技术:[0002]
随着国内外航天工业、现代国防工业和交通运输业的飞速发展,航空航天用高性能筒形件铝合金已经引起了国内外航天领域的重视,铝合金整体高筒形环锻件由于工艺装备等制约,以前只能采用铸造工艺,但是铸造由于气孔、疏松、偏析等缺陷,导致产品报废率高和可靠性低等问题,目前,采用整体铝合金环件替代铸件,提高产品性能和可靠性是高筒铝合金构件制造的发展趋势。
[0003]
目前铝合金筒形锻件处理技术为:铸锭经过多向锻造后,进行冲孔,再进行芯轴拔长,再进行马架扩孔,再进行碾环,再进行热处理和粗加工。一方面由于芯轴拔长和马架扩孔的变形方式会对径向进行压缩变形,会导致径向力学性能偏低;同时这种变形方式对坯料的轴向没有约束,因此轴向流线不显著,导致轴向力学性能偏低;另一方面,由于生产过程中涉及到的热加工工序较多,而热加工属于热力耦合交替的过程,芯轴拔长和马架扩孔都是非连续热变形的过程,这种变形方式对坯料的轴向没有约束,因此轴向流线不显著,这种热力耦合反复交替的过程会导致锻件的质量把控较为困难,会增加锻件组织的不均匀性。
技术实现要素:[0004]
本发明的目的是提供一种航天用高性能铝合金筒形锻件制造方法,其优点在于通过对坯料进行多向锻造和反挤压处理,可以大幅度的提升轴向性能,提高锻件的组织均匀性。
[0005]
本发明的上述技术目的是通过以下技术方案得以实现的:
[0006]
一种航天用高性能铝合金筒形锻件制造方法,包括以下步骤:
[0007]
s1、下料:在铝合金铸锭上按尺寸规格下料得到坯料;
[0008]
s2、锻造加热:将坯料放置在加热炉内,升温至440℃~470℃,保温20h~25h;
[0009]
s3、制坯:沿坯料轴向镦拔两次后成形为圆饼件;
[0010]
s4、回炉:坯料回炉加热,升温至420~440℃,保温4~7h;
[0011]
s5、反挤压:将坯料冲孔,并使坯料轴向高度增加,然后坯料进行反挤压,之后将坯料空冷至室温;
[0012]
s6、清理:清理坯料的内孔和底片;
[0013]
s7、回炉加热:将s6中清理完成的坯料放置在加热炉内,升温至420℃~440℃,保温4h~8h;
[0014]
s8、碾环:将坯料碾环;
[0015]
s9、固溶处理:将坯料加热至500~530℃后进行保温,保温后,坯料出炉水冷,水温
40~65℃,入水时间20~40min;
[0016]
s10、时效处理:将坯料加热至140℃~175℃后进行保温,保温后,坯料出炉空冷至室温。
[0017]
进一步的,在步骤s3中,每次坯料单次镦拔的变形量≥65%。
[0018]
进一步的,在步骤s3中,坯料的成形尺寸至φ705
×
900mm。
[0019]
进一步的,在步骤s5中,将坯料的尺寸反挤压至φ705
×
φ360
×
1200mm。
[0020]
进一步的,在步骤s8中,坯料碾环尺寸至φ1040
×
φ860
×
1200mm。
[0021]
进一步的,在步骤s9中,保温时间范围是6~10h。
[0022]
进一步的,在步骤s10中,保温时间范围是5~12h。
[0023]
综上所述,本发明具有以下有益效果:
[0024]
1.通过反挤压将坯料的轴向流线变为为强制流线方向,可以大幅度的提升轴向性能,该变形方式没有对径向造成锻造压缩损伤,最大限度的提升径向性能,同时坯料在变形过程中,整体变形均匀一致,保证了组织均匀一致,保证坯料在各个方向最终的力学性能均匀一致。
[0025]
2.反挤压变形强制三向压缩变形,在反挤压过程中,坯料受到三向压应力的作用,可以对铝合金中的残余结晶相进行强制破碎,可以使第二相在后续热处理过程中,充分固溶和时效,大大提升产品的力学性能。
附图说明
[0026]
图1是航天用高性能铝合金筒形锻件制造方法的步骤示意图;
[0027]
图2是反挤压工序前坯料的结构示意图;
[0028]
图3是反挤压工序后坯料的结构示意图;
[0029]
图4是试样1的金相显微图;
[0030]
图5是试样2的金相显微图。
[0031]
图中1、上模具;2、下模具。
具体实施方式
[0032]
以下结合附图对本发明作进一步详细说明。
[0033]
实施例:一种航天用高性能铝合金筒形锻件制造方法,如图1所示,包括以下步骤:
[0034]
s1、下料:在铝合金铸锭上按尺寸规格下料得到坯料,坯料的尺寸为φ600
×
1240mm。
[0035]
s2、锻造加热:工作人员将坯料放置在加热炉内进行加热,将坯料升温至440℃~470℃,之后对坯料进行保温,保温时间范围是20h~25h。
[0036]
s3、制坯:沿坯料轴向以宽砧强力压下锻造法进行两次镦拔,坯料成形为圆饼件,在镦拔的过程中,坯料单次镦拔的变形量≥65%,坯料成形的尺寸为φ705
×
900mm。
[0037]
s4、回炉:将坯料回炉加热至420℃~440℃,当达到指定温度之后,坯料保温4h~7h。
[0038]
s5、反挤压:准备专用模具,专用模具包括上模具1和下模具2,上模具1安装在冲压机的冲头上,如图2所示,下模具2安装在冲压机的砧座上,将坯料放入到下模具2中,之后如
图3所示,上模具1下压在坯料上冲孔,并使坯料的高度增加,完成坯料的反挤压,坯料的成形尺寸至φ705
×
φ360
×
1200mm。
[0039]
坯料通过反挤压将坯料的轴向流线变为为强制流线方向,可以大幅度的提升轴向性能,该变形方式没有对径向造成锻造压缩损伤,最大限度的提升径向性能,同时坯料在变形过程中,整体变形均匀一致,保证了组织均匀一致,保证坯料在各个方向最终的力学性能均匀一致。
[0040]
s6、清理:清理坯料内孔和底片,坯料尺寸至:φ705
×
φ380
×
1200mm。
[0041]
s7、回炉加热:将s6中清理完成的坯料放置在加热炉内,升温至420℃~440℃,之后保温4h~8h。加热使坯料的塑性增加,方便之后的加工变形。
[0042]
s8、碾环:将坯料碾环,坯料尺寸至φ1040
×
φ860
×
1200mm,此时坯料为高筒形。
[0043]
s9、固溶处理:将坯料加热至500~530℃后进行保温,保温的时间范围是6~10h,保温后,坯料出炉水冷,水温40~65℃,入水时间20~40min。
[0044]
s10、时效处理:将坯料加热至140℃~175℃后进行保温,保温时间范围是5~12h,保温后,坯料出炉空冷至室温。
[0045]
s11、取样检测:对坯料沿轴向取样100mm高,对环件三个方向做性能。进行检测。
[0046]
s12、机加工:将坯料机加工尺寸至φ1020
×
φ880
×
1050mm。
[0047]
s13、超声波探伤:对坯料进行超声波探伤。
[0048]
铝合金检测:铝合金锻件检测结果见表1。
[0049]
项目试样1试样2标准抗拉强度(mpa)486511≥450mpa屈服强度(mpa)433455≥380mpa延伸率(%)886~14%超声波探伤a级a级gjb1580a-2004
[0050]
表1。
[0051]
金相检测:试样1的微观金相图见图4,试样2的微观金相图见图5。
[0052]
结论:合金组织没有断裂缺陷,晶粒组织细小且密集。
[0053]
本具体实施例仅仅是对本发明的解释,其并不是对本发明的限制,本领域技术人员在阅读完本说明书后可以根据需要对本实施例做出没有创造性贡献的修改,但只要在本发明的权利要求范围内都受到专利法的保护。