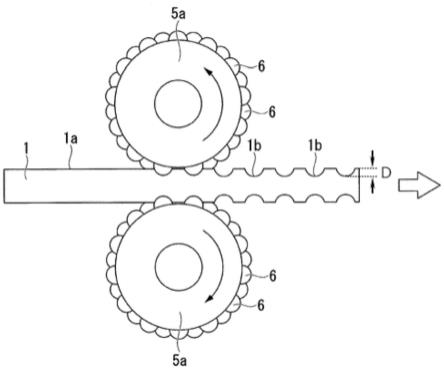
1.本发明涉及能够在热轧时减少表面瑕疵的产生的钛加工材的制造方法。
背景技术:2.通常的热轧用钛材的制造方法例如如下所述。首先,通过自耗电极式电弧熔炼法(var:vacuum arc remelting)、电子束熔炼法(ebr:electron beam remelting),使钛熔融并凝固,由此制造锭。接下来,通过开坯、锻造、轧制等热加工对锭进行初轧(breakdown),制成板坯、小钢坯(billet)等热轧用钛材。另外,近年来还开发出一种通过利用电子束熔炼法制造能够直接热轧的矩形锭来省略上述的初轧工序的技术。
3.但是,工业上使用的大型锭在凝固组织中存在达到数十mm的粗大的晶粒。若不经过初轧工序而直接对这样的锭进行热轧,则存在这样的情况:由于粗大的晶粒而产生不均匀的变形,发展成较大的表面瑕疵。另外,即使在经过初轧工序等的情况下,在初轧工序中的加工率较低或温度不合适的情况下,也会存在这样的情况:铸造组织残存、组织反而粗大等,从而在热轧时产生表面瑕疵。
4.若像这样产生表面瑕疵,则其后的去氧化皮工序中的成品率变得非常差,因此一直在谋求不易产生热轧表面瑕疵的热轧用钛材。
5.在专利文献1中,提出了这样的方法:在直接对钛材的锭进行热加工时,为了使表层附近的晶粒细粒化,在对表面层赋予应变之后,加热至再结晶温度以上,使自表面起的深度2mm以上的部分再结晶之后,进行热加工。
6.另外,在专利文献2和专利文献3中记载了一种热加工用钛材,通过使用顶端形状具有3mm~30mm的曲率半径的钢制工具或者半径为3mm~30mm的钢制球,使热加工用钛材的表面塑性变形,从而对表层部赋予应变。根据专利文献2和专利文献3,通过对这样的热加工用钛材进行热轧,能够使粗大的凝固组织的影响无害化,能够减轻表面瑕疵。
7.现有技术文献
8.专利文献
9.专利文献1:日本特开平1-156456号公报
10.专利文献2:国际公开第2010/090352号
11.专利文献3:日本特开2018-1249号公报
技术实现要素:12.发明要解决的问题
13.在专利文献1中,作为赋予应变的方法,可列举锻造、辊压、喷丸。然而,对于通常的喷丸,由于喷粒的直径小至0.5mm~1mm,因此所施加的应变量也较小。另外,在锻造、辊压的情况下,产生所谓的死区金属,应变量变少或向更靠内部的位置导入应变。因此,存在无法确保必要的再结晶层的厚度的情况、细粒化不充分的情况。
14.在专利文献2和专利文献3中,由于利用钢制工具进行打击或按压来赋予应变,因
此为了对表面整体稳定地赋予应变,有时需要长时间,从而效率不高。另外,在高强度材料的情况下,也存在这样的情况:冲击能量不会传递至内部,从而无法确保必要的细粒组织的厚度。因此,存在进一步改善的余地。
15.本发明是鉴于上述情况而完成的,其课题在于提供一种高效地制造能够减少在热轧时产生的表面瑕疵的钛加工材的方法。
16.用于解决问题的方案
17.用于解决上述课题的本发明的主旨如下。
18.一种钛加工材的制造方法,其是使钛坯料通过辊对的间隙的钛加工材的制造方法,其中,
19.所述辊对中的至少一个辊具有在将表面展开并进行俯视的情况下排列成交错状的多个突起,
20.所述钛加工材的制造方法具备通过将所述突起向所述钛坯料的表面压入从而在钛坯料的表面形成多个凹陷部的工序,
21.所述突起在其顶端具备球面状的按压面,在将所述按压面的高度设为h(mm)、将所述按压面的曲率半径设为r(mm)、将在所述钛坯料的通过方向上相邻的所述突起的中心间距离设为s(mm)、将所述突起的压入量设为d(mm)时,
22.所述r处于3~30的范围内,
23.所述d处于2~10的范围内且为h以下,
24.所述s处于2(r
2-(r-d)2)
1/2
~3(r
2-(r-d)2)
1/2
的范围内。
25.发明的效果
26.根据本发明,能够提供一种能够减少在热轧时产生的表面瑕疵的钛加工材的制造方法。
27.另外,根据本发明,即使是省略了锭的初轧工序的铸造状态的钛坯料,也能够稳定地使在热轧时产生的表面瑕疵轻微,能够高效地提供优异的热轧、冷轧产品。
附图说明
28.图1是表示本实施方式的钛加工材的形状的例子的立体图。
29.图2是本实施方式的钛加工材的剖面示意图。
30.图3的(a)、图3的(b)和图3的(c)是用于对本实施方式中的凹陷部的排列方式进行说明的图。
31.图4是本实施方式的钛加工材的剖面示意图。
32.图5是本实施方式的钛加工材的制造方法中使用的加工机的概略侧视图。
33.图6的(a)、图6的(b)和图6的(c)是用于对本实施方式中的突起6(6a、6b、6c)的排列方式进行说明的图。
34.图7的(a)、图7的(b)是用于对本实施方式中的突起6(6a、6d)的形状进行说明的辊径向上的剖面放大图。
具体实施方式
35.以下,使用附图对本发明的实施方式进行说明。
36.本发明人从减少由热轧引起的表面缺陷的观点出发,对使晶粒直径达到数十mm的锭的粗大的凝固组织、进而使初轧后仍残存的该凝固组织的影响无害化的方法和适应该方法的钛加工材,反复进行了深入研究,结果得到以下的见解,从而完成了本发明。
37.为了使粗大的凝固组织细粒化,或者为了消除残存有凝固组织的影响的部位,考虑这样的方法:在对钛坯料的表面赋予了预定的应变之后,通过热轧时的加热等预定的热处理,来进行再结晶。
38.在本发明中,使用具有预定的突起的辊对钛坯料进行轧制,将突起向钛坯料压入,由此,在钛坯料的表面形成多个凹陷部(凹凸),对坯料表层赋予应变。发现了通过该方法获得的钛加工材在表层具备加工组织,能够显著地抑制热轧时的表面缺陷。另外,在本发明中,通过将突起向钛坯料压入来使钛坯料物理性地塑性变形从而形成凹陷部,由此能够稳定地导入应变,而且能够向凹陷部的底部导入有效且充分的应变,通过之后的热轧时的加热在表层形成微细的再结晶,由此,能够抑制表面瑕疵的产生。
39.以下,参照附图对本实施方式的钛加工材的制造方法进行说明。此外,在以下的所有的附图中,为了易于观察附图,对各构成要素的厚度、尺寸的比率进行了调整。
40.首先,对通过本实施方式的钛加工材的制造方法制造的钛加工材(以下也称为“本实施方式的钛加工材”)进行说明。该钛材在表层具备加工组织,适合于之后供进行热轧的坯料。另外,优选的是,在该钛加工材中,凹陷部的底部的曲率半径r1为3mm~30mm,凹陷部排列成在俯视时呈交错状。
41.另外,对于本实施方式的钛加工材,优选的是,在将凹陷部的半径设为r1(mm)时,相邻的所述凹陷部的中心间距离p、以及排列有所述凹陷部的各列之间的距离q均处于(2
×
r1)mm至(3
×
r1)mm的范围内。
42.另外,优选的是,在本实施方式的钛加工材的制造方法中使用的钛坯料由工业用纯钛或者钛合金构成。
43.再者,对于在本实施方式的钛加工材的制造方法中使用的钛坯料,可例示出锭、板坯、大钢坯(bloom)或小钢坯。对于钛坯料的形状,剖面为圆形形状的钛坯料的直径为100mm~300mm,优选为90mm~250mm。
44.如后所述,本实施方式的钛加工材通过使用带突起的辊并将该辊向钛坯料压入而在钛坯料表面形成凹陷部从而赋予应变来制造。关于制造方法的详细情况将进行后述。
45.图1表示本实施方式的钛加工材的例子。本实施方式的钛加工材既可以如图1的(a)所示为板坯1,也可以如图1的(b)所示为大钢坯2,还可以如图1的(c)所示为与长度方向垂直的剖面是矩形的小钢坯(矩形小钢坯)3,亦可以如图1的(d)所示为与长度方向垂直的剖面是圆形的小钢坯(圆形小钢坯)4。另外,在图1的(a)的板坯1、图1的(b)的大钢坯2、图1的(c)的矩形小钢坯3和图1的(d)的圆形小钢坯4各自的表面1a、2a、3a、4a形成有多个凹陷部1b、2b、3b、4b。此外,虽未图示,但在钛加工材为图1的(a)~图1的(c)中的任意一个矩形剖面的情况下,还可以在长度方向上的侧面也形成有凹陷部。
46.图2表示沿着图1的(a)~图1的(d)中的a-a线的剖面示意图。此外,在图1的(a)~图1的(d)中沿着a-a线剖切的情况下,剖面结构在图1的(a)~图1的(d)中为相同的结构,因此为了便于说明,将该剖视图汇总表示于图2。
47.此外,在图1的(a)或图1的(b)所示的板坯1或大钢坯2中,厚度的1/2深度位置分别
为板坯厚度t或大钢坯厚度t的1/2t厚度的位置。另外,在图1的(c)所示的纵横比为1左右的矩形剖面的小钢坯3中,厚度的1/2深度位置为小钢坯剖面的重心位置,在图1的(d)所示的圆形剖面的小钢坯4中,厚度的1/2深度位置为小钢坯剖面的中心位置。
48.为了稳定地抑制可能由热轧产生的表面瑕疵,需要使钛加工材的结晶组织微细化。当然,使钛加工材整体的结晶组织微细化也能够抑制表面瑕疵,但为此需要对坯料整体赋予大量的应变。另外,存在根据需要而在热轧前沿宽度方向进行轧制的情况,但若对铸造状态的钛坯料进行的宽度方向上的压下量变大,则存在这样的情况:产生由粗大铸造组织引起的褶皱,在热轧后产生表面瑕疵。
49.这样,为了不仅稳定地抑制由铸造组织引起的表面瑕疵还稳定地抑制由增大宽度方向上的轧制时的褶皱引起的表面瑕疵,需要至少使表层在热轧时成为微细的再结晶组织。此处所说的表层是指,自凹陷部底部至深度3mm的深度位置之间的区域。另外,凹陷部底部是凹陷部的最深部。为了在进行热轧的加热时使表层成为微细的再结晶组织,需要自凹陷部底部至深度3mm的位置导入预定量的应变。根据各种调查的结果,本发明人明确了在自凹陷部底部起的深度3mm的区域,若等效应变为0.2以上,则在进行热轧的加热时产生再结晶,形成微细组织。这样获得的再结晶层的厚度为3mm以上,能够抑制热轧时的表面瑕疵。再结晶层的厚度为3mm以上便足够,上限没有特别限定,但为了增大该厚度,需要使用于导入应变的冲压载荷变大。因此,从冲压机的承受载荷的限制的观点出发,再结晶层的厚度的实质上限为25mm。
50.这样,本实施方式的钛加工材在表面形成有多个凹陷部,因此对坯料表层导入了充分的应变,在进行热轧时的加热时,能够形成微细且粒径一致的再结晶。
51.接下来,对形成于本实施方式的钛加工材的凹陷部的优选形态进行说明。
52.优选的是,如图1的(a)~图1的(d)所示,在本实施方式的钛加工材的表面形成有多个凹陷部1a~4a,这些凹陷部的曲率半径r1设为3mm~30mm。
53.将凹陷部的底部形状设为曲率半径r1为3mm~30mm的形状即设为球面状的理由是因为:在将具有上述曲率半径的突起向钛坯料1压入而形成凹陷部时,在凹陷部的底部附近不易形成死区金属部,向周围的金属流动成为各向同性(同心圆状)。即,是因为:通过将凹陷部的底部设为球面状,从而容易向凹陷部周边导入应变。另外,是因为:使用在顶端具有曲率半径r为3mm~30mm的球面状的按压面的突起即顶端为球头的突起来形成凹陷部,由此,凹陷部的形状不易成为在热轧时凹陷部的端部叠压而发展成表面瑕疵那样的陡峭的凹坑,后面将进行详述。由此,优选的是,凹陷部的底部形状设为曲率半径r1处于3mm~30mm的范围的形状(与顶端为球头状的突起对应的球面状)。
54.在凹陷部底部的球面状的曲率半径r1小于3mm的情况下,有可能成为向表面瑕疵发展的陡峭的凹坑、或者有可能无法在钛加工材表层的深度方向上充分地导入应变而导致组织被细粒化的表层厚度较浅,结果产生表面瑕疵。因此,优选的是,凹陷部底部的曲率半径r1设为3mm以上。
55.另一方面,当凹陷部的曲率半径r1超过30mm时,存在这样的风险:死区金属部变大,无法对钛加工材表层赋予充分的应变,因此优选的是,凹陷部的曲率半径r1设为30mm以下。这样,通过将凹陷部的曲率半径r1设为30mm以下,能够使死区金属部变小,能够向钛加工材表层集中导入应变至充分的深度。
56.接下来,关于形成于本实施方式的钛加工材的凹陷部的优选的排列方式,例举使用板坯(图1的(a))来作为钛坯料的种类的情况,并结合附图进行说明。
57.图3的(a)~图3的(c)是用于对本实施方式中的凹陷部的排列方式进行说明的图,是对图1的(a)所示的钛加工材(板坯1)进行俯视时的凹陷部1b、1b
′
、1b
″
的示意图。此外,图3的(a)~图3的(c)中的附图标记x1~x3表示凹陷部的配置列。
58.另外,图4是用于对本实施方式中的凹陷部的形状进行说明的凹陷部剖视图,是沿着图3的(a)的b-b线的剖视图。
59.如图3的(a)所示,在俯视板坯1时,在1列上规则地配置有多个凹陷部1b的各突起列x1、x2、x3在板坯1的宽度方向或者长度方向上排列,且多个凹陷部1b相互在板坯1的宽度方向或者长度方向上交替地配置。即,凹陷部1b排列成在俯视时呈交错状。具有这样的排列方式的凹陷部1b利用具有该排列方式的带突起的辊形成,通过将该突起向板坯1的表面1a压入,能够高效地向板坯1的被轧制面导入均匀的应变。此外,突起列x1、x2、x3的配置方向可以是板坯1的宽度方向、长度方向中的任一方向,另外,也可以是与宽度方向(或者长度方向)具有一定的角度的方向。另外,为了便于说明,对突起列为3列的方式进行了说明,但关于该列数,可以根据板坯1的尺寸(直径、宽度等)、形成凹陷部时使用的带突起的辊、突起的尺寸等来适当决定。
60.另外,凹陷部既可以如图3的(a)和图4所示相互分离开一定的距离而配置,也可以如图3的(b)所示配置为在同列上相邻的凹陷部1b
′
彼此分离开的状态下在板坯宽度方向或者长度方向上排列的各列彼此相接触。另外,也可以如图3的(c)所示无间隙地配置成所有的凹陷部1b
″
相接触。
61.接下来,对在同列上排列的多个凹陷部中的相邻的凹陷部的中心间距离p、以及各列间的距离(凹陷部列间距离)q进行说明。如图3的(a)~图3的(c)、图4所示,中心间距离p是指,在对凹陷部1b、1b
′
、1b
″
进行俯视时,在同列上(例如列x1上、列x2上等)相邻的凹陷部的中心间的距离,另外,凹陷部列间距离q表示相邻的凹陷部列(例如列x1和列x2)的中心轴线间的距离。
62.在本实施方式中,优选的是,在将凹陷部的半径设为r1(mm)时,中心间距离p(mm)和凹陷部列间距离q(mm)均设为(2
×
r1)以上且(3
×
r1)以下。
63.在中心间距离p、凹陷部列间距离q比(2
×
r1)小的情况下,存在这样的担心:金属流动被抑制而导致向凹陷部周围导入的应变量变得不充分。另一方面,在中心间距离p、凹陷部列间距离q比(3
×
r1)大的情况下,相邻的凹陷部彼此的间隔过度增大,因此所导入的应变量变得不充分,其结果为有时无法充分地抑制热轧后的表面瑕疵。
64.以上,例举图1的(a)的板坯1,对本实施方式的凹陷部的优选形态进行了说明,在图1的(b)的大钢坯2、图1的(c)的矩形小钢坯3以及图1的(d)的圆形小钢坯4也形成有与上述相同形态的凹陷部。
65.本实施方式中的钛坯料是供进行热轧的钛铸坯,能够例示例如以下的(a)或(b)那样的锭、板坯、大钢坯、小钢坯等作为钛坯料。即,钛坯料不包括已经通过热轧或冷轧轧制成比预定的厚度小的钛板。因此,在长方体、立方体的钛坯料的情况下,以厚度例如为100mm以上的钛坯料为对象,在圆柱状的钛坯料的情况下,以直径例如为90mm以上的钛坯料为对象。钛坯料(b)由使钛熔融并进行铸造而得到的凝固组织构成,具有存在晶粒直径为10mm以上
的粗大粒的铸造状态的组织。
66.(a)一种钛坯料,该钛坯料通过如下这样获得:将通过自耗电极式电弧熔炼法(var:vacuum arc remelting)、电子束熔炼法(ebr:electron beam remelting)、等离子电弧熔炼法(pam:plasma arc melting)等使钛暂时熔融之后凝固而获得的锭进一步通过开坯、锻造、轧制等热加工进行初轧,成形为板坯、小钢坯等形状。
67.(b)一种钛坯料,该钛坯料通过如下这样获得:在通过电子束熔炼法或等离子电弧熔炼法使钛暂时熔融之后凝固时,形成能够直接热轧的大小的矩形锭,省略上述(a)的初轧工序。
68.在电子束熔炼法中,由于照射的电子束能够通过偏振光而集束,因此即使是铸模与熔融钛之间的狭窄的区域,也容易供给热,因此能够良好地控制铸件表面。另外,铸模的剖面形状的自由度较高。因此,优选的是,上述(b)那样的能够直接供进行热轧的尺寸的矩形或圆柱形的锭使用电子束熔炼炉来进行熔炼。另外,在等离子电弧熔炼法中,虽然加热原理与电子束熔炼法不同,但是能得到与电子束熔炼法相同的效果。
69.优选的是,钛坯料由工业用纯钛或者钛合金构成。
70.工业用纯钛包括jis h4600标准的1种~4种、以及与之对应的astm265b标准的grade1~4、din 17850标准的gradei(wl3.7025)、gradeii(wl3.7035)、gradeiii(wl3.7055)所规定的工业用纯钛。即,在本发明中作为对象的工业用纯钛由以质量%计c:0.1%以下、h:0.015%以下、o:0.4%以下、n:0.07%以下、fe:0.5%以下、剩余部分为ti构成。以下,关于各元素的含量的“%”意为“质量%”。
71.另一方面,对于低合金、α型钛合金,在必要的用途中适当使用合金即可。更优选的是,实质上合金成分为5%以下的低合金较佳。例如,能够例示添加了pd<0.15%、ru<0.10%、还添加了稀土类元素<0.02%的高耐腐蚀性合金、添加了合计不到5%的cu、al、si、sn、nb、fe的耐热合金等。
72.更具体而言,作为低合金,例如存在高耐腐蚀性合金(astm grade 7、11、16、26、13、30、33或者与它们对应的jis品种、还少量地含有各种元素的合金)、ti-0.5cu、ti-1.0cu、ti-1.0cu-0.5nb、ti-1.0cu-1.0sn-0.3si-0.25nb、ti-0.5al-0.45si、ti-0.9al-0.35si等。另外,作为α型钛合金,例如存在ti-5al-2.5sn、ti-6al-2sn-4zr-2mo、ti-6al-2.75sn-4zr-0.4mo-0.45si等。
73.作为α+β型钛合金,例如存在ti-6al-4v、ti-6al-6v-2sn、ti-6al-7v、ti-3al-2.5v、ti-3al-5v、ti-5al-2sn-2zr-4mo-4cr、ti-6al-2sn-4zr-6mo、ti-1fe-0.35o、ti-1.5fe-0.5o、ti-5al-1fe、ti-5al-1fe-0.3si、ti-5al-2fe、ti-5al-2fe-0.3si、ti-5al-2fe-3mo、ti-4.5al-2fe-2v-3mo等。
74.再者,作为β型钛合金,例如存在ti-11.5mo-6zr-4.5sn、ti-8v-3al-6cr-4mo-4zr、ti-10v-2fe-3mo、ti-13v-11cr-3al、ti-15v-3al-3cr-3sn、ti-6.8mo-4.5fe-1.5al、ti-20v-4al-1sn、ti-22v-4al等。
75.对于本发明的钛合金,例如通过含有超过0%的选自o:0%~0.5%、n:0%~0.2%、c:0%~2.0%、al:0%~8.0%、sn:0%~10.0%、zr:0%~20.0%、mo:0%~25.0%、ta:0%~5.0%、v:0%~30.0%、nb:0%~40.0%、si:0%~2.0%、fe:0%~5.0%、cr:0%~10.0%、cu:0%~3.0%、co:0%~3.0%、ni:0%~2.0%、铂族元素:0%~
0.5%、稀土类元素:0%~0.5%、b:0%~5.0%和mn:0%~10.0%的1种以上的元素,能够对钛加工材的表面赋予目标功能。
76.作为上述以外的元素且能够在钛中含有的元素是作为金属材料的一般常识能够期待通过固溶强化、析出强化(存在不固溶的情况和形成析出物的情况)来提高强度等的元素。作为上述元素,能例示按原子序数为氢(1)至砹(85)的元素(其中,作为第18族元素的稀有气体元素除外),合计允许至5%左右。
77.上述以外的剩余部分为ti和杂质。作为杂质,能够在不阻碍目标特性的范围内含有,其他杂质主要有自原料、废料混入的杂质元素和在制造过程中混入的元素,作为例子,c、n、o、fe、h等为代表性的元素,此外存在mg、cl等自原料混入的元素、si、al、s等在制造过程中混入的元素等。若上述元素为2%左右以下,则可以认为是不阻碍本技术的目标特性的范围。
78.另外,本发明的钛合金例如也可以含有选自o:0.01%~0.5%、n:0.01%~0.2%、c:0.01%~2.0%、al:0.1%~8.0%、sn:0.1%~10.0%、zr:0.5%~20.0%、mo:0.1%~25.0%、ta:0.1%~5.0%、v:1.0%~30.0%、nb:0.1%~40.0%、si:0.1%~2.0%、fe:0.01%~5.0%、cr:0.1%~10.0%、cu:0.3%~3.0%、co:0.05%~3.0%、ni:0.05%~2.0%、铂族元素:0.01%~0.5%、稀土类元素:0.001%~0.5%、b:0.01%~5.0%和mn:0.1%~10.0%的1种以上的元素。
79.更为优选的是,本发明的钛合金含有选自o:0.02%~0.4%、n:0.01%~0.15%、c:0.01%~1.0%、al:0.2%~6.0%、sn:0.15%~5.0%、zr:0.5%~10.0%、mo:0.2%~20.0%、ta:0.1%~3.0%、v:2.0%~25.0%、nb:0.15%~5.0%、si:0.1%~1.0%、fe:0.05%~2.0%、cr:0.2%~5.0%、cu:0.3%~2.0%、co:0.05%~2.0%、ni:0.1%~1.0%、铂族元素:0.02%~0.4%、稀土类元素:0.001%~0.3%、b:0.1%~5.0%和mn:0.2%~8.0%的1种以上的元素,进一步优选的是,本发明的钛合金含有选自o:0.03%~0.3%、n:0.01%~0.1%、c:0.01%~0.5%、al:0.4%~5.0%、sn:0.2%~3.0%、zr:0.5%~5.0%、mo:0.5%~15.0%、ta:0.2%~2.0%、v:5.0%~20.0%、nb:0.2%~2.0%、si:0.15%~0.8%、fe:0.1%~1.0%、cr:0.2%~3.0%、cu:0.3%~1.5%、co:0.1%~1.0%、ni:0.1%~0.8%、铂族元素:0.03%~0.2%、稀土类元素:0.001%~0.1%、b:0.2%~3.0%和mn:0.2%~5.0%的1种以上的元素。
80.在此,作为铂族元素,具体而言能举出ru、rh、pd、os、ir和pt,能够含有上述元素中的1种以上的元素。在含有两种以上的铂族元素的情况下,上述铂族元素的含量意为铂族元素的总量。另外,作为稀土类元素(rem),具体而言能举出sc、y、la、ce、pr、nd、pm、sm、eu、gd、tb、dy、ho、er、tm、yb和lu,能够含有上述元素中的1种以上的元素。在含有两种以上的稀土类元素的情况下,例如可以使用混合稀土合金(mm)、钕镨合金那样的稀土类元素的混合物、化合物。另外,在含有两种以上的稀土类元素的情况下,上述稀土类元素的含量意为稀土类元素的总量。
81.接下来,对本实施方式的钛加工材的制造方法进行说明。
82.本实施方式的钛加工材的制造方法是使钛坯料通过辊对的间隙而在所述钛坯料的表面形成多个凹陷部的钛加工材的制造方法。在本实施方式的钛加工材的制造方法中,作为所述辊对中的至少一个辊,使用具有在将表面展开并进行俯视的情况下排列成交错状
的多个突起的辊。使用这样的在表面具备多个突起的辊,将该突起向钛坯料表面压入,由此,形成凹陷部,对坯料表层部赋予应变。通常,在试图通过锻造、大直径辊对锭等赋予应变的情况下,在与模具接触的部分不产生金属流动,而是产生所谓的被称为死区金属的部位。由于该死区金属部的应变量较小,因此若通过锻造、大直径辊赋予应变,则不是对表层部而是对更靠内部的部分导入应变,从而无法使表层部的组织细粒化。
83.因此,本发明人对通过防止死区金属的产生且高效地对钛坯料表层均匀地赋予应变从而使粗粒部不产生的方法进行了研究,发现了若利用下述的方法进行处理,则能够高效地对表层赋予应变。
84.以下,对本实施方式的钛加工材的制造方法进行详述。
85.本实施方式的钛加工材的制造方法在如下条件下进行:所述突起在其顶端具备球面状的按压面,在将所述按压面的高度设为h(mm)、所述按压面的曲率半径设为r(mm)、在所述钛坯料的通过方向上相邻的所述突起的中心间距离设为s(mm)、所述突起的压入量设为d(mm)时,所述r处于3~30的范围内,所述d处于2~10的范围内且为h以下,所述s处于2(r
2-(r-d)2)
1/2
~3(r
2-(r-d)2)
1/2
的范围内。
86.优选的是,在本实施方式的钛加工材的制造方法中,排列有突起的各列间的距离l处于2(r
2-(r-d)2)
1/2
~3(r
2-(r-d)2)
1/2
的范围内。
87.另外,优选的是,在本实施方式的钛加工材的制造方法中,形成凹陷部的工序在钛坯料的表层温度为0℃以上且500℃以下的温度下进行。
88.再者,优选的是,在本实施方式的钛加工材的制造方法中,形成凹陷部的工序之前的钛坯料通过使用电子束熔炼法或等离子电弧熔炼法而制造。
89.此外,优选的是,在本实施方式的钛加工材的制造方法中,钛坯料由工业用纯钛或者钛合金构成。
90.此外,优选的是,在本实施方式的钛加工材的制造方法中,钛坯料为板坯、大钢坯或小钢坯。
91.作为本实施方式的钛加工材的制造方法中使用的加工机,例举具备一对辊2的双辊式加工机来进行说明,图5表示该双辊式加工机的概略侧视图。此外,在以下的说明中,例举使用板坯(图1的(a))来作为加工对象即钛坯料的种类的情况进行说明。另外,图中的粗箭头为钛坯料(板坯)1的输送方向,细箭头表示辊2的旋转方向。
92.如图5所示,本实施方式是在一对辊5a之间输送钛坯料(板坯)1的同时进行加工的方法。具体而言,本实施方式是这样的方法:在排列有具有曲率半径r为3mm~30mm的顶端形状的多个突起6的一对辊5a之间输送钛坯料1,同时向该钛坯料1的表面1a压入突起6,使表面1a塑性变形预定量而在表面1a形成凹陷部1b,由此,对钛坯料1的表层赋予应变。此外,在钛坯料1中,至少在后期工序的热轧时成为被轧制面的面形成凹陷部1b而导入应变即可。即,凹陷部1b的形成面既可以仅为坯料的一部分的面,也可以是整个面。因此,在一对辊5a中的至少一个辊形成有前述那样的突起6即可。
93.根据该制造方法,能够容易且高效地制造能够显著地抑制热轧时的表面缺陷的钛加工材。
94.此外,在本实施方式中,当在表面具备突起6的辊5a之间进行输送而在钛坯料1的表面1a形成凹陷部1b时,输送次数(辊间的通过次数)既可以是1次,也可以设为两次以上。
即,也可以如反向轧制那样,在辊5a之间输送一次而在表面形成凹陷部,之后将第二次的输送方向设为与第一次的输送方向相反的方向,然后再次在辊5a之间输送并将突起6压靠于钛坯料。另外,这样的压入工序没有特别限定,可以在钛坯料不产生裂纹的范围内决定该次数。
95.另外,作为本实施方式的加工对象的钛坯料的形状可以是图1的(a)所示的板坯、图1的(b)所示的大钢坯,另外也可以是图1的(c)所示的相对于长度方向成直角的剖面为矩形的小钢坯3、图1的(d)所示的相对于长度方向成直角的剖面为圆形的小钢坯4。
96.在钛坯料为板坯、大钢坯的情况下,钛坯料中面积最大的面成为热轧时的被轧制面,因此至少在该面形成凹陷部即可。另外,在钛坯料为小钢坯的情况下,沿着其长度方向延伸的整个面可能成为被轧制面。因此,例如,在剖面为矩形的小钢坯的情况下,优选的是,在其整个面形成凹陷部,向钛坯料的整个表面导入应变。例如,在采用了图1的(d)所示的剖面为圆形的小钢坯4来作为钛坯料的情况下,优选的是,如曼内斯曼型轧制法那样使用设有多个预定的突起的筒型、锥型的辊来进行加工。具体而言,例如,优选的是,利用如下方法在小钢坯表面形成凹陷部而导入应变,该方法即:在圆形小钢坯4的外周配置筒型(或者锥型)的多个辊(例如3个辊),使圆形小钢坯4在被轧制并自转的同时在输送方向上行进。
97.这样,在本实施方式中,例举了图5所示的双辊式加工机,但在本发明的钛坯料的制造方法中,无论加工机的类型、辊数等如何,均能够采用上述那样的曼内斯曼型轧制法等,辊数也可以是3个以上。即使在这样的情况下,也是在至少1个辊形成有本实施方式的突起6即可。
98.如图5所示,在辊5a的表面设有多个突起6,该突起6具有曲率半径r为3mm~30mm的顶端形状。另外,上述多个突起6在将辊5a表面展开并进行俯视的情况下排列成交错状。
99.将突起6的顶端的按压面设为曲率半径r为3mm~30mm的球面状即设为球头的理由是因为:在将突起6向钛坯料1压入而形成凹陷部1b时,在凹陷部1b的底部附近不易形成死区金属部,向周围的金属流动成为各向同性(同心圆状)。即,是因为:通过将突起6的顶端设为球头,从而容易向压入后形成的凹陷部1b的周边导入应变。此外,是因为:通过将压入的突起6的顶端形状设为球头,从而凹陷部1b的形状不易成为在热轧时凹陷部1b的端部叠压而发展成表面瑕疵那样的陡峭的凹坑。例如,在将突起的顶端形状设为矩形、四棱锥、三棱锥的情况下,突起必然存在平面部和角形状的角部。在利用这样的突起形成凹陷部的情况下,有时会在平面部形成死区金属部。另外,存在这样的担心:因凹陷部部中的角形状的角部,金属流动被约束,向坯料深度方向导入应变受到阻碍。因此,设于辊5a的突起6的顶端的按压面采用曲率半径r为3mm~30mm的范围的球面状(球头)。
100.在突起6顶端的球面状的按压面(球头)的曲率半径r小于3mm的情况下,当突起6的压入量d较大(例如2mm以上)时,会形成发展成表面瑕疵的陡峭的凹坑,另一方面,若减小压入量d(例如小于2mm)以不产生陡峭的凹坑,则无法向坯料表层的深度方向充分地导入应变,组织被细粒化的表层厚度较浅而产生表面瑕疵。因此,曲率半径r设为3mm以上。
101.另一方面,在曲率半径r超过30mm的情况下,死区金属部变大,无法对坯料表层赋予充分的应变,因此曲率半径r设为30mm以下。这样,通过将曲率半径r设为30mm以下,能够使死区金属部变小,能够向坯料表层集中导入应变至充分的深度。此外,若曲率半径r较小,则容易受到突起6的磨损的影响,因此曲率半径r的下限优选为5mm。另外,若曲率半径r较
大,则对辊5a的负荷载荷增大,因此曲率半径r的上限优选为15mm。
102.在本实施方式中,使用具备突起6的辊5a,该突起6具有上述那样的形状,通过向钛坯料1压入该突起6从而形成凹陷部1b而导入应变,但此时的压入量d设为2mm~10mm且为突起的按压面高度h(mm)以下。
103.为了充分地抑制热轧后的表面瑕疵,预先使热轧前的钛加工材的自表面起的深度3mm以上的表层细粒化是有效的。在本实施方式中,为了使钛坯料的自表面起的深度3mm以上的表层细粒化,需要施加距坯料表面的深度为2mm以上的压入量的变形。即,通过突起6的压入而形成的凹陷部1b的凹部的深度设为2mm以上。另一方面,若压入量d超过突起6的按压面高度h,则除了可能形成发展成表面瑕疵那样的陡峭的凹坑之外,还会使得金属流动没有了去处。因此,突起6的压入量d设为处于2mm~10mm的范围且为突起的按压面高度h以下。
104.为了向坯料表层导入充分的应变,使热轧后的表层组织细粒化,以2mm以上的压入量d对突起6进行压入,但为了获得该压入量d,优选的是,突起6的高度h超过目标压入量d。若突起3的高度h过低,则存在无法确保充分的压入量d的担心。从上述观点出发,突起6的高度h也可以设为超过突起6的按压面高度h的高度(参照后述的图7的(b))。另外,设于突起6d的顶端的球面状的按压面可以是具有按压面高度h=曲率半径r的关系的形状即半球面状,不过也可以是具有按压面高度h<曲率半径r的关系的形状。此外,球面状是指构成球面的一部分的形状,例如,如图7的(a)、图7的(b)所例示,也可以是半球面状。
105.接下来,对突起6在辊5a上的排列方式进行说明。
106.图6的(a)~图6的(c)是用于对本实施方式中的突起6(6a、6b、6c)的排列方式进行说明的图,是将辊5a的表面展开并进行俯视时的突起6a、6b、6c的示意图。此外,图6的(a)~图6的(c)中的附图标记y1~y3分别表示突起列。
107.另外,图7的(a)、图7的(b)是用于对本实施方式中的突起6(6a、6d)的形状进行说明的辊径向上的剖面放大图,特别是,图7的(a)是沿着图6的(a)的c-c线的剖视图。
108.如图6的(a)~图6的(c)所示,在将辊5a的表面展开并进行俯视时,在1列上规则地配置有多个突起6(6a、6b、6c)的各突起列y1、y2、y3沿着辊5a的宽度方向或者周向排列,且多个突起6(6a、6b、6c)相互沿着辊5a的宽度方向或者周向交替地配置。即,突起6排列成在俯视时呈交错状。通过将以这样的排列方式设置的突起6向坯料1的表面1a压入而形成凹陷部1b,能够高效地向坯料1的被轧制面导入均匀的应变。此外,突起列y1、y2、y3的配置方向可以是辊5a的周向、宽度方向中的任一方向,另外,也可以是与周向(或者宽度方向)具有一定的角度的方向。另外,为了便于说明,对突起列为3列的方式进行了说明,但关于该列数,也可以根据所使用的辊的尺寸(直径、宽度等)、突起6的尺寸等来适当决定。
109.另外,突起6既可以如图6的(a)和图7的(a)所示相互分离开一定的距离而配置,也可以如图6的(b)所示配置为在使相邻的突起6b彼此分离开的状态下,使在辊周向或者宽度方向上排列的各列彼此相接触。另外,也可以如图6的(c)所示无间隙地配置成所有的突起6c相接触。
110.此外,图7的(b)也与图7的(a)同样是突起彼此不接触而分离地配置的例子,但如上述那样,针对突起6d的形状,也可以是超过突起6d的曲率半径r的高度h。在该情况下,突起高度h中具有超过曲率半径r的部分,即具有与辊表面垂直的部分(圆柱部)p。
111.接下来,对在同一列上排列的多个突起6中的相邻的突起6的中心间距离s和各列
间的距离(突起列间距离)l进行说明。如图6的(a)~图6的(c)、图7的(a)、图7的(b)所示,中心间距离s是指,在对突起6进行俯视时,在同一列上(例如在列y1上或列y2上等)相邻的突起6的中心间的距离,另外,突起列间距离l表示相邻的突起列(例如y1和y2)的中心轴线间的距离。另外,突起列间距离l是沿着辊的旋转方向的距离。
112.在本实施方式中,以该中心间距离s为2(r
2-(r-d)2)
1/2
~3(r
2-(r-d)2)
1/2
的范围内(r:曲率半径,d:压入量)的方式排列突起6。即,在将突起6俯视时的半径设为r的情况下,优选的是,中心间距离s处于2r以上且3r以下的范围内。
113.在中心间距离s比2(r
2-(r-d)2)
1/2
小的情况(比2r小的情况)下,存在无法充分地确保突起6的压入量d而导致应变量不充分的担心。再者,在中心间距离s比2(r
2-(r-d)2)
1/2
小的情况(比2r小的情况)下,存在这样的担心:当将突起6压入时,周围的凹陷部成为对金属流动的阻碍,供金属流动的空间受到限制,从而无法赋予充分的应变。另一方面,在中心间距离s比3(r
2-(r-d)2)
1/2
大的情况(比3r大的情况)下,由于相邻的突起6彼此的间隔过度增大,因此由突起6压入而被导入的应变量变得不充分,其结果为有时无法充分地抑制热轧后的表面瑕疵。
114.此外,即使在中心间距离s为2r以上的情况也就是即使在相邻的突起6之间存在一定程度的间隙的情况下,被突起6压入的部分也伴随着向周围的金属流动,因此除了在所形成的凹陷部1b的表层部周边能够充分地导入应变之外,在该间隙部分也能够充分地导入应变。
115.再者,在本实施方式中,优选的是,突起列间的距离l设在2(r
2-(r-d)2)
1/2
~3(r
2-(r-d)2)
1/2
的范围内。即,在将突起6俯视时的半径设为r的情况下,优选的是,突起列间的距离l处于2r以上且3r以下的范围内。
116.在突起列间的距离l比2(r
2-(r-d)2)
1/2
小的情况(比2r小的情况)下,能够赋予一定的应变,但还存在该应变量不充分的情况,除此之外还担心辊的加工负荷、载荷的增大。因此,优选的是,突起列间的距离l设为2(r
2-(r-d)2)
1/2
以上。另一方面,在突起列间的距离l比3(r
2-(r-d)2)
1/2
大的情况(比3r大的情况)下,由于相邻的突起列彼此的间隔过度增大,因此由突起6压入而被导入的应变量变得不充分,其结果为有时无法充分地抑制热轧后的表面瑕疵。因此,优选的是,突起列间的距离l设为3(r
2-(r-d)2)
1/2
以下。
117.在本实施方式中,使用具备以上说明的突起6的辊5a,能够确保上述的压入量d地进行在坯料1形成凹陷部1b的加工。
118.对于使用了这样的辊5a的加工,若能够确保上述压入量d,则进行一次即可,但考虑到加工机的能力、规格,也可以进行多次,能够确保合计的压入量d处于上述范围内即可。
119.此外,在本实施方式中,作为对坯料1进行加工的方法,与像锻造那样进行压下的方式相比,通过采用图5所示的轧制方式,金属流动变得更容易,具有不易形成上述的死区金属的效果。
120.另外,若使用将坯料1的整个宽度覆盖的辊5a,则能够高效地导入应变。另外,在本实施方式中,由于突起6仅对所接触的部分进行压入,因此与利用不存在突起的平坦的辊、模具对钛坯料的整个宽度进行压入相比,即使是较小的载荷也能够导入所需的应变。
121.当使用带突起6的辊5a在钛坯料表面形成多个凹陷部时,既可以不对钛坯料进行加热而在常温下进行,也可以在将钛坯料加热到最高500℃以下之后进行。
122.在本实施方式中,在常温~温轧温度下,对钛加工材的成为被轧制面的表面赋予应变。为了减少在热轧时产生的表面瑕疵,需要形成达到一定程度的深度的再结晶组织。特别是在高硬度的钛坯料的情况下,应变难以进入至钛坯料的内部,为了将应变赋予至表层的较深的位置,需要以较大的载荷赋予凹凸形成的加工。然而,新发现了这样的情况:通过赋予应变会使得表层附近的延展性降低,从而在表面产生裂纹。因此,为了稳定地将应变赋予至较深的位置并且使表层的延展性提高,将温度提高一定程度而使钛坯料自身的强度降低也是有效的。另一方面,对于强度没有那么高的钛坯料,使应变集中于表层能够使表层的组织变得微细,因此在室温下赋予应变较佳。
123.另一方面,若在超过500℃的高温下进行凹陷部形成的加工,则存在这样的情况:通过加工而赋予的应变立即消失,从而在之后的加热时无法进行再结晶。另外,在超过500℃时,有时会在钛坯料的表面形成氧化固化层,存在这样的担心:该氧化固化层在加工时被压入而产生表面缺陷,在之后的热轧时发展成表面瑕疵。若为500℃以下,则不会发生上述那样的问题,因此优选的是,以500℃以下为上限。
124.另外,钛坯料的强度和延展性变高的温度区根据合金种类不同而有所不同,因此并非在更高的温度下进行加工即可。例如,在工业用纯钛等的情况下,在室温附近,作为钛的变形机理的重要变形机理之一的孪晶变形活跃地活动,但在400℃~500℃左右的温度下,不发生该孪晶变形,因此与室温相比延展性降低,反而容易产生裂纹。另一方面,在含有大量的al的合金类的情况下,即使在室温附近,该孪晶变形也几乎不发生,因此通过加热至500℃以下,能够确保延展性。另外,β型钛合金具有这样的特征:若在300℃~500℃下长时间加热,则会由于时效硬化而强度提高,且延展性降低。另外,若使钛坯料成为高温,极端地减弱材料强度,则存在这样的担心:在塑性变形时表面的凹陷部形状的起伏(深度)变得过大,因该起伏而产生表面瑕疵。因此,根据钛坯料的品种、种类,来选择在轧制后表面不产生裂纹且能获得适当的再结晶组织、表面状态的温度范围即可。
125.如以上已说明的那样,在本实施方式的制造方法中,在排列有多个突起的一对辊之间输送钛坯料的同时,向该钛坯料的表面压入突起,由此,使该钛坯料塑性变形预定量而在表面形成凹陷部。其结果是能够高效且稳定地向坯料表层导入应变。并且,通过之后的热轧时的加热,在表层形成微细的再结晶,由此,能够抑制表面瑕疵的产生。
126.另外,通过由本实施方式的制造方法获得的钛加工材,能显著地抑制热轧后的表面缺陷。通过将本发明应用于矩形、圆柱形的锭,从而即使不经过开坯轧制等初轧工序,在对板、带状卷材或棒材进行热轧时,也能够起到能够将表面缺陷抑制至不存在问题的程度的效果。
127.为了减小变形阻力,对本实施方式的钛加工材进行热轧时的加热温度优选设在800℃~950℃的范围。再者,为了抑制在板坯加热时产生的氧化皮,加热温度优选比β相变点小。在此,β相变点是指钛坯料随着加热而成为β相单相的下限温度。
128.这样,根据本实施方式制造而成的钛加工材起到如下效果:不但适合供进行热轧,而且通过热轧所制造的热轧材料的表面缺陷被显著地抑制,之后,即使实施冷轧也能够制造健全的产品。
129.另外,根据本实施方式,即使是省略了锭的初轧工序的铸造状态的钛坯料,也能够使在热轧时产生的表面瑕疵轻微,能够提供优异的热轧、冷轧产品。
130.另外,若将本实施方式应用于经过了初轧工序的钛坯料,则在热轧时产生的表面缺陷极为轻微。其结果是,能够使热轧后的板、棒材的去氧化皮工序、最终产品的成品率进一步提升。
131.实施例
132.以下,通过实施例更详细地说明本发明。
133.<实施例1>
134.首先,通过电子束熔炼法(ebr)或者等离子电弧熔炼法(pam)对具有表1(工业用纯钛)和表2(钛合金)所示的成分组成的钛坯料进行铸造,制成了具有铸造状态的粗大的凝固组织的大致矩形的锭。此外,关于表1的坯料符号m9,是对该锭进行了锻造而得到的。此外,表2的钛坯料的合金成分的“mm”是混合稀土合金(含有稀土类元素的合金)。
135.接下来,自符号m9以外的锭切出厚度约120mm、宽度约250mm、长度约450mm的钛坯料并进行了机械加工。关于符号m9,自所述锻造后的坯料切出厚度约120mm、宽度约250mm、长度约450mm的钛坯料并进行了机械加工。此外,切出的各坯料以如下方式切出:切出的位置关系相对于锭一致,且距锭的表面的深度位置大致相同。
136.对于所切出的坯料(m1~m18)中的成为后述的热轧时的被轧制面的面(单面),通过使用了具有被设成表3a、表4a和表5a所示的形状和排列的突起的辊的双辊式加工机(参照图5),在坯料表面形成凹陷部,制成了钛加工材。在此时的压入量(d)、加工温度等加工条件如表3a、表4a和表5a那样进行了各种变化的条件下进行。此外,突起在图6的(a)~图6的(c)所示的俯视图中排列成交错状。另外,利用直径300mm的辊(无突起)对坯料a2进行了加工。
137.接下来,将钛加工材在低于β相变点的温度下加热了约两小时后,利用连续热轧带钢轧机热轧至厚度约6mm。对该热轧板实施喷丸,进而使该热轧板通过由硝酸-氢氟酸构成的连续酸洗作业线来实施酸洗从而进行了去氧化皮。之后,通过目视观察对产生的表面瑕疵进行标记,对表面瑕疵的产生状况进行了评价。在此,β相变点是指钛坯料随着加热而成为β相单相的下限温度。
138.具体而言,在通过连续酸洗作业线后的热轧板中,除轧制方向上的前后端的不稳定部以外,以200mm间隔来划分长度,将检测到表面瑕疵的部分的区间数除以整体的区间数(40个区间)得到的比例设为表面瑕疵发生率。根据表面瑕疵发生率,将0%评价为
“◎”
,将超过0%且为5%以下且约1mm的微小的表面瑕疵评价为
“○”
,将超过5%或约10mm以上的较大的表面瑕疵评价为
“×”
。此外,
“◎”
和
“○”
为合格,
“×”
为不合格。
139.在表3b中将工业用纯钛的实施例和比较例并列示出,在表4b中将钛合金的实施例和比较例并列示出。辊的加工温度均为室温。
140.另外,表5b表示在进行辊加工时将坯料的温度加热至100℃~400℃并实施了基于辊进行的凹凸形成加工的例子。
141.由表3a~表5b可知,若在本发明的范围内利用排列有突起的辊对坯料进行轧制而形成凹陷部,则表面瑕疵发生率低至5%以下,在更为优选的条件范围内能够降低至0%。
142.另一方面,可知,在保持坯料而不进行加工的情况、辊表面不存在突起的情况、突起的曲率半径(r)、压入量(d)、突起中心间的距离(s)脱离本发明范围的情况的例子即比较例中,表面瑕疵发生率均较高。
143.特别是,在突起中心间的距离(s)脱离2(r
2-(r-d)2)
1/2
~3(r
2-(r-d)2)
1/2
的范围(2r1至3r1的范围)的a14、a15中,与未加工的a1、利用无突起的辊进行轧制的a2相比,虽然表面瑕疵发生率降低至20%左右,但是达不到5%以下。
144.另外可知,如由作为实施例的c1~c20可知那样,在加工温度为100℃~400℃的情况下,也能得到与在室温下得到的效果相同的效果。
145.作为实施例的a10和a17是利用排列有预定的突起的辊实施了两次压下的实施例,能得到本发明的效果。
146.作为比较例的a33是对m9的对锭进行锻造而得到的坯料进行热轧的情况,表面瑕疵发生率高达48%。相对于此,在作为实施例的a41中,通过利用排列有预定的突起的辊对该坯料进行轧制,从而能得到表面瑕疵发生率降低至0%的效果。
147.[表1]
[0148]
表1
[0149][0150]
ebr;电子束熔炼法
[0151]
pam;等离子电弧熔炼法
[0152]
[表2]
[0153]
表2
[0154][0155]
ebr;电子束熔炼法
[0156]
pam;等离子电弧熔炼法
[0157]
[表3a]
[0158]
表3a
[0159][0160]
[表3b]
[0161]
表3b
[0162][0163]
[表4a]
[0164]
表4a
[0165][0166]
[表4b]
[0167]
表4b
[0168][0169]
[表5a]
[0170]
表5a
[0171][0172]
[表5b]
[0173]
表5b
[0174][0175]
附图标记说明
[0176]
1、2、3、4、钛坯料(板坯、大钢坯、小钢坯);1a、2a、3a、4a、表面;1b、2b、3b、4b、凹陷
部;1b1、2b1、3b1、4b1、凹陷部的底部;5a、辊;6、6a、6b、6c、6d、突起。