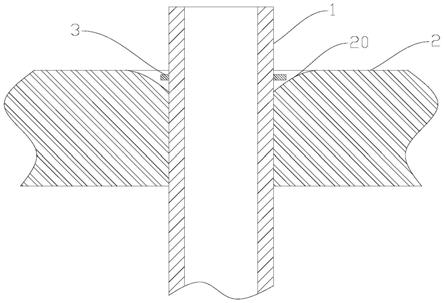
1.本发明涉及换热器制造技术领域,具体涉及一种换热器管板自动焊接工艺。
背景技术:2.在化工装备中,列管式换热器是一种重要的设备,而管板与换热管的焊接接头又是该设备中最重要又最容易失效的焊接接头,其质量直接影响着设备的使用寿命和装置的稳定。目前,换热器换热管与管板一般通过人工手工焊接,工艺流程过于简单,效率低,而且焊缝的致密性差,出现泄露的几率大;也有使用焊接机器人进行焊接,虽然提高了焊接效率,但是增加了企业的生产成本。
技术实现要素:3.为了克服现有技术的不足,本发明提供了一种焊接效率高,焊接后焊缝致密性高的换热器管板自动焊接工艺。
4.本发明采用如下技术方案实现:换热器管板自动焊接工艺,包括以下步骤:
5.s1、对管板及换热管进行打磨、清洗,除去表面锈层及油脂层;
6.s2、将打磨好的若干换热管插入到管板的孔洞内,且换热管凸出管板的外壁5
‑
10mm,在管板的外壁上开设凹槽,在换热管的外壁上焊接限位块,限位块位于凹槽内;
7.s3、使用管板焊机进行试焊,试焊完毕后、调整管板焊机参数进行最终焊接。
8.管板与限位块的材质相同,通过管板焊机对换热管与限位块的衔接处进行试焊。
9.所述管板焊机包括定位柱、转动轴和焊枪,所述转动轴插设在所述换热管内,至少三个所述定位柱顶触在所述管板的表面,所述焊枪围绕所述转动轴转动;
10.所述转动轴上设有胀紧套,所述胀紧套卡止在所述换热管内。
11.所述凹槽的槽底朝向换热管凸起。
12.所述定位柱包括柱体、尖锥部和设于柱体与尖锥部之间、用于驱动所述尖锥部转动的驱动部,所述驱动部包括壳体、电动机和轴承,所述壳体的一侧与所述柱体固定连接,所述壳体的另一侧设有穿孔,所述轴承适配地卡设在所述穿孔内,所述尖锥部穿设在所述轴承内,所述电动机固定设于壳体内,所述电动机用于驱动所述尖锥部转动。
13.所述柱体的外壁上还设有鹅颈管,所述鹅颈管内穿设有输气管,所述输气管朝向焊枪的头部输送氮气。
14.相比现有技术,本发明通过管板焊机焊接,自动化程度高,在保证低成本的同时,有效提高了焊接效率;进一步的,在焊接完成后,限位块埋设在焊缝内,提高了焊缝金属与换热管的连接强度,避免换热管震动引起焊缝松动、造成漏水,焊接的致密性高。
附图说明
15.图1是本发明结构示意图;
16.图2是管板焊机的结构示意图;
17.图3是定位柱的结构示意图;
18.图中:1、换热管;2、管板;20、凹槽;3、限位块;4、定位柱;41、柱体;42、尖锥部;43、壳体;44、电动机;45、轴承;5、转动轴;6、焊枪;7、胀紧套;8、鹅颈管。
具体实施方式
19.下面,结合附图以及具体实施方式,对本发明做进一步描述,需要说明的是,在不相冲突的前提下,以下描述的各实施例之间或各技术特征之间可以任意组合形成新的实施例。
20.如图1所示,换热器管板自动焊接工艺,包括以下步骤:
21.s1、对管板2及换热管1进行打磨、清洗,除去表面锈层及油脂层;确保了焊接面洁净,确保焊接的可靠性。
22.s2、将打磨好的若干换热管1插入到管板2的孔洞内,且换热管1凸出管板2的外壁5
‑
10mm,在管板2的外壁上开设凹槽20,凹槽20的槽底朝向换热管1凸起,在换热管1的外壁上焊接限位块3,限位块3位于凹槽20内;
23.s3、使用管板2焊机进行试焊,试焊完毕后、调整管板2焊机参数进行最终焊接。通过管板2焊机焊接,自动化程度高,在保证低成本的同时,有效提高了焊接效率;进一步的,在焊接完成后,限位块3埋设在焊缝内,提高了焊缝金属与换热管1的连接强度,避免换热管1震动引起焊缝松动、造成漏水。
24.管板2与限位块3的材质相同,通过管板2焊机对换热管1与限位块3的衔接处进行试焊。这样,通过在限位块3上进行试焊,便于焊接参数的调整,而且,在焊接参数偏差较大的情况下,试焊产生的焊缝无需清除,可以直接进行最终的调整参数后的焊接。
25.如图2所示,所述管板2焊机包括定位柱4、转动轴5和焊枪6,所述转动轴5插设在所述换热管1内,至少三个所述定位柱4顶触在所述管板2的表面,所述焊枪6围绕所述转动轴5转动;
26.所述转动轴5上设有胀紧套7,所述胀紧套7卡止在所述换热管1内。转动轴5插入到换热管1内、定位柱4顶触管板2,胀紧套7张紧,可靠实现对焊枪6的定位,再通过电动机44驱动焊枪6转动,即可实现对管板2及换热管1的自动焊接,焊接效率高。
27.所述凹槽20的槽底朝向换热管1凸起。这样,便于熔融后的焊接金属在凹槽20内流动、并充满凹槽20,提高焊接后的连接强度。
28.如图3所示,所述定位柱4包括柱体41、尖锥部42和设于柱体41与尖锥部42之间、用于驱动所述尖锥部42转动的驱动部,所述驱动部包括壳体43、电动机44和轴承45,所述壳体43的一侧与所述柱体41固定连接,所述壳体43的另一侧设有穿孔,所述轴承45适配地卡设在所述穿孔内,所述尖锥部42穿设在所述轴承45内,所述电动机44固定设于壳体43内,所述电动机44用于驱动所述尖锥部42转动。电动机44驱动尖锥部42转动后,尖锥部42会在管板2的表面钻设小孔,然后电动机44停止,这样,小孔可以起到对定位柱4的限位作用,防止了在焊接的过程中定位柱4发生小范围的串动,提高了焊接精度。
29.所述柱体41的外壁上还设有鹅颈管8,所述鹅颈管8内穿设有输气管,所述输气管朝向焊枪6的头部输送氮气。鹅颈管8可以随意弯曲、并保持当前的状态,这样,确保了在不同的施工环境下,鹅颈管8内的输气管都能指向焊枪6的头部,确保能在焊接处形成稳定的
氮气氛围。
30.上述实施方式仅为本发明的优选实施方式,不能以此来限定本发明保护的范围,本领域的技术人员在本发明的基础上所做的任何非实质性的变化及替换均属于本发明所要求保护的范围。
技术特征:1.换热器管板自动焊接工艺,其特征在于:包括以下步骤:s1、对管板及换热管进行打磨、清洗,除去表面锈层及油脂层;s2、将打磨好的若干换热管插入到管板的孔洞内,且换热管凸出管板的外壁5
‑
10mm,在管板的外壁上开设凹槽,在换热管的外壁上焊接限位块,限位块位于凹槽内;s3、使用管板焊机进行试焊,试焊完毕后、调整管板焊机参数进行最终焊接。2.根据权利要求1所述的换热器管板自动焊接工艺,其特征在于:管板与限位块的材质相同,通过管板焊机对换热管与限位块的衔接处进行试焊。3.根据权利要求1所述的换热器管板自动焊接工艺,其特征在于:所述管板焊机包括定位柱、转动轴和焊枪,所述转动轴插设在所述换热管内,至少三个所述定位柱顶触在所述管板的表面,所述焊枪围绕所述转动轴转动;所述转动轴上设有胀紧套,所述胀紧套卡止在所述换热管内。4.根据权利要求1所述的换热器管板自动焊接工艺,其特征在于:所述凹槽的槽底朝向换热管凸起。5.根据权利要求1所述的换热器管板自动焊接工艺,其特征在于:所述定位柱包括柱体、尖锥部和设于柱体与尖锥部之间、用于驱动所述尖锥部转动的驱动部,所述驱动部包括壳体、电动机和轴承,所述壳体的一侧与所述柱体固定连接,所述壳体的另一侧设有穿孔,所述轴承适配地卡设在所述穿孔内,所述尖锥部穿设在所述轴承内,所述电动机固定设于壳体内,所述电动机用于驱动所述尖锥部转动。6.根据权利要求5所述的换热器管板自动焊接工艺,其特征在于:所述柱体的外壁上还设有鹅颈管,所述鹅颈管内穿设有输气管,所述输气管朝向焊枪的头部输送氮气。
技术总结本发明提供了一种换热器管板自动焊接工艺。涉及换热器制造技术领域。焊接效率高,焊接后焊缝致密性高。包括以下步骤:S1、对管板及换热管进行打磨、清洗,除去表面锈层及油脂层;S2、将打磨好的若干换热管插入到管板的孔洞内,且换热管凸出管板的外壁5
技术研发人员:蒋德超 孙松召 孙志伟 黄敏姝 檀帅乐 谈娇娇
受保护的技术使用者:江苏鼎嘉机械设备科技有限公司
技术研发日:2021.05.06
技术公布日:2021/9/10