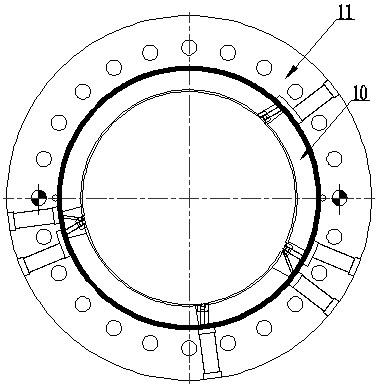
一种k形隔板腔的加工方法
技术领域
1.本发明涉及航天精密加工技术领域,特别涉及一种k形隔板腔的加工方法。
背景技术:2.k形隔板腔是航天超燃动力地面试验装置中的一个部件,其主要作用是在隔板腔组件中形成一个需要承压5mpa的冷却通道,用于冷却经过k形区域的高温燃气,其主要由本体、环肋、多个隔板和连接在隔板之间的转接头组成;其中,多个隔板与转接头钎焊形成k形隔板组件,本体和环肋钎焊后形成本体组件,k形隔板组件与本体组件钎焊后形成k形隔板腔。
3.采用现有技术加工k形隔板腔时存在以下问题:1)本体组件的尺寸较大,k形隔板组件为不规则的异形,二者装配时装配间隙很难保证要求;2)钎焊本体组件与k形隔板组件时,由于k形隔板组件与本体组件质量、重量、尺寸差异较大,钎焊过程中容易导致热量分布不均,造成k形隔板组件变形。
技术实现要素:4.本发明提供了一种k形隔板腔的加工方法,解决采用现有技术加工k形隔板腔的过程中,k形隔板组件与本体组件不易装配,以及装配后钎焊二者时k形隔板组件容易变形的问题。
5.本发明是通过以下方案来实现的:一种k形隔板腔的加工方法,包括以下步骤:a1.加工多个尺寸不同的一字形隔板和多个三向转接头,在转接头的接口处涂注膏状钎料并将其与隔板装配;用隔板工装将多个转接头与多个隔板固定,真空钎焊,得到k形隔板组件;a2.粗车环状本体,在其环面粗钻多个基准孔,环周镗铣多个进水孔,在本体上加工与进水孔连通的扇形水槽、流道方孔和流量孔;线切多个环肋,在其外端面车加工多个冷却槽道,使相邻冷却槽道之间形成筋条;在筋条上预置粘带钎料,将环肋装配在本体的内端面使环肋的接口与流道方孔对应,冷却槽道与流量孔对应;用本体工装将环肋与本体固定,真空钎焊,得到本体组件;a3.将本体组件切分为本体内环和本体外环;在本体内环和环肋的上、下端面分别精车出沉台面,并根据沉台面精铣出补偿块;粗车中间开设方槽的加强块,在其外端面及方槽两侧加工钎料槽;在补偿块的底面预置粘带钎料,加强块的钎料槽中涂注膏状钎料,将k形隔板组件、加强块和补偿块装配在本体内环上;用腔体工装固定k形隔板组件、加强块、补偿块和本体内环,真空钎焊,得到k形隔板分腔;a4.将本体外环氩弧焊在k形隔板分腔的外周,精加工,得到k形隔板腔。
6.进一步地,所述本体采用不锈钢材质;所述隔板、转接头、环肋、补偿块、加强块均采用高强铜合金材质;所述膏状钎料和粘带钎料均采用镍基含金材质。
7.进一步地,固定时,在所述隔板工装与k形隔板组件、所述本体工装与本体组件、所述腔体工装与k形隔板分腔的接触面分别涂刷厚度为0.1
‑
0.2mm的阻钎剂;所述膏状钎料涂注的直径均为0.5
‑
1mm;所述粘带钎料的预置的厚度均为0.05
‑
0.1mm。
8.进一步地,所述隔板工装包括设置在底板上并根据所述隔板的尺寸加工的多个l形卡板;所述卡板的竖板设在隔板的两侧,卡板的横板和底板上开设有相对应的固定孔,通过在固定孔中设置紧固件将卡板固定在隔板的两侧,夹紧隔板;所述底板与转接头对应的区域开设防止多余钎料将k形隔板组件与腔体工装粘连的圆孔。
9.进一步地,所述真空钎焊隔板和转接头的流程如下:冷态真空度2
‑5×
10
‑2pa,工作真空度3
‑
5pa;以120
‑
150℃/h的速率加热至400
‑
500℃,保持0.3
‑
0.5h;以150
‑
180℃/h的速率加热至900
‑
950℃,分压3
‑
5pa,保持2
‑
4h;以180
‑
210℃/h的速率加热至1010
‑
1035℃,3
‑
5pa,保持0.2
‑
0.5h;以150
‑
180℃/h控温冷却至700
‑
750℃,随炉冷却至400
‑
500℃向炉内填充高纯氩气使炉内压力达到6
‑8×
104pa后启动风扇冷却至100℃以下出炉。
10.进一步地,所述本体工装包括固定在底座上且依次设在环肋内部的多个衬板和顶板;所述衬板的内端面和顶板均设为正多边形,衬板的外端面设为与环肋匹配的弧形;所述顶板上均匀开设多个压紧孔,通过在压紧孔中固定压紧件使衬板压紧环肋,使环肋与本体紧贴。
11.进一步地,所述本体和环肋的真空钎焊流程如下:冷态真空度2
‑5×
10
‑2pa,工作真空度3
‑
5pa;以60
‑
90℃/h的速率加热至400
‑
500℃,保持0.3
‑
0.5h;以90
‑
120℃/h的速率加热至900
‑
950℃,保持4
‑
6h;以120
‑
150℃/h的速率加热至1010
‑
1035℃,保持0.2
‑
0.5h;加热结束后以90
‑
120℃/h控温冷却至700
‑
750℃,随炉冷却至400
‑
500℃向炉内填充高纯氩气使炉内压力达到6
‑8×
104pa后启动风扇冷却至100℃以下出炉。
12.进一步地,所述腔体工装包括连接在第一固定板和第二固定板之间的固定组件;所述第一固定板的内端面为适应于k形隔板腔外端面的弧面,外端面设为平面,第二固定板的内端面设为平面,外端面设为适应于k形隔板腔内端面的弧面;在第一固定板上部至底部之间开设有适应于隔板尺寸的竖槽,第一固定板和第二固定板上均设有用于贯穿固定组件的开孔,将固定组件贯穿、固定在第一固定板和第二固定板之间的开孔中,使补偿块与本体内环压紧。
13.进一步地,所述k形隔板组件和本体内环的真空钎焊流程如下:冷态真空度2
‑5×
10
‑2pa,工作真空度3
‑
5pa;以45
‑
60℃/h的速率加热至400
‑
500℃,保持0.3
‑
0.5h;以60
‑
90℃/h的速率加热至900
‑
950℃,分压3
‑
5pa,保持4
‑
5h;以90
‑
120℃/h的速率加热至1010
‑
1035℃,3
‑
5pa,保持0.2
‑
0.5h;加热结束后以90
‑
120℃/h控温冷却至700
‑
750℃,随炉冷却至400
‑
500℃向炉内填充高纯氩气使炉内压力达到6
‑8×
104pa后启动风扇冷却至100℃以下出炉。
14.进一步地,得到所述k形隔板组件、本体组件、k形隔板分体后,还对其进行压力测试;压力试验的条件相同,均为:在5mpa的纯净水压力下测试30min。
15.本发明具有以下优点:1).为了保证不规则k形隔板组件与本体组件的装配钎焊质量,首先,将本体组件分为本体内环、本体外环,本体内环先与异形的k形隔板组件装配并钎焊,得到隔板腔分体后,再与本体外环进行氩弧焊;通过上述方法不仅降低了k形隔板组件与本体组件的装配难度和装配工作量,也减小了本体组件与k形隔板组件的质量差,使钎焊过程中热量分布相对均匀,减小了钎焊时k形隔板组件的变形;2).调整了本体内环与k形隔板组件的钎焊结构,增加了加强块和补偿块,将本体组件与k形隔板组件的钎焊调整为k形隔板组件、加强块、补偿块与本体内环的钎焊,增加了钎焊面积,加强了钎缝强度。
附图说明
16.图1为k形隔板组件的示意图;图2为k形隔板组件的右视图;图3为隔板工装的俯视图;图4为隔板工装沿a
‑
a的剖面图;图5为本体组件的示意图;图6为本体组件沿纵轴线的剖面图;图7为环肋与本体贴合面的示意图;图8为本体工装的示意图;图9为本体工装沿横轴线的剖面图;图10为本体内环和本体外环的示意图;图11为k形隔板组件、本体内环与加强块的装配示意图;图12为腔体工装固定k形隔板组件和本体内环的示意图;图13为第二固定板的结构图;图14为本体内环与本体外环氩弧焊的示意图;图15为本体内环与本体外环氩弧焊时沿中轴线的剖面图;图16为k形隔板腔的示意图;图中:1
‑
隔板,2
‑
转接头,3
‑
隔板工装,31
‑
底板,32
‑
卡板,33
‑
紧固件,4
‑
本体,5
‑
环肋,6
‑
本体工装,61
‑
底座,62
‑
顶板,63
‑
衬板,64
‑
压紧件,7
‑
补偿块,8
‑
加强块,9
‑
腔体工装,91
‑
第一固定板,92
‑
第二固定板,93
‑
固定组件,10
‑
本体内环,11
‑
本体外环。
具体实施方式
17.下面结合具体实施方式对本发明进行详细的说明。
18.实施例1一种k形隔板腔的加工方法,包括以下步骤:a1.用高强铜合金材料线切五个尺寸不同的波纹板和空心板;在波纹板的两侧储能点焊一层非晶态钎料,并分别装配在五个空心板中,使二者的接触面贴紧,如果间隙过大
允许固定多层钎料,直至二者压合;将装配好的波纹板和空心板放入真空钎焊炉中,按照以下程序进行钎焊:冷态真空度2
‑5×
10
‑2pa,工作真空度3
‑
5pa;以240
‑
300℃/h的速率加热至400
‑
500℃,保持0.2
‑
0.4h;以300
‑
360℃/h的速率加热至900
‑
950℃,分压3
‑
5pa,保持1
‑
2h;以360
‑
420℃/h的速率加热至1020
‑
1035℃,分压3
‑
5pa,保持0.2
‑
0.5h;加热结束后随炉冷却至400
‑
500℃向炉内填充高纯氩气使炉内压力达到6
‑8×
104pa后启动风扇冷却至100℃以下出炉;钎焊完成后,得到内部有多个通槽的一字形隔板1;线切两个转接头2,使转接头2的两向在一条直线上,另一向与直线呈一定角度;在转接头2的接口内部铣加工钎料槽;用煤油、酒精清洗隔板1和转接头2;在转接头2一端线切出转接头盖;在转接头2的钎料槽涂注镍基含金膏状钎料,接口内端面粘贴0.05mm厚的镍基含金粘带钎料,将五个隔板1与两个转接口2装配成k形,并保证二者之间的角向偏差小于0.2mm;在转接头盖内壁粘贴一层0.1mm厚的镍基含金粘带钎料,并将其装配在转接头2上;在如图3、图4所示的隔板工装3与隔板1、转接头2的接触面分别涂刷厚度为0.1
‑
0.2mm的阻钎剂;用隔板工装3将装配好的隔板和转接头2固定;具体的,隔板工装3包括设置在底板31上并根据隔板1的尺寸加工的多个l形卡板32;卡板32的竖板设在隔板1的两侧,卡板32的横板和底板31上开设有相对应的固定孔,通过在固定孔中设置紧固件33将卡板32固定在隔板1的两侧,夹紧隔板1;底板31与转接头2对应的区域开设有防止多余钎料将隔板、转接头、腔体工装粘连的圆孔;将隔板工装3和装配好的隔板1、转接头2放入真空钎焊炉中,按照以下程序进行钎焊:冷态真空度2
‑5×
10
‑2pa,工作真空度3
‑
5pa;以120
‑
150℃/h的速率加热至400
‑
500℃,保持0.3
‑
0.5h;以150
‑
180℃/h的速率加热至900
‑
950℃,分压3
‑
5pa,保持2
‑
4h;以180
‑
210℃/h的速率加热至1010
‑
1035℃,分压3
‑
5pa,保持0.2
‑
0.5h;加热结束后,以150
‑
180℃/h控温冷却至700
‑
750℃,随炉冷却至400
‑
500℃向炉内填充高纯氩气使炉内压力达到6
‑8×
104pa后启动风扇冷却至100℃以下出炉;钎焊完成后,得到如图1、图2所示的k形隔板组件;目视检验钎缝的完整性,对k形隔板腔的腔道压力测试,具体的,试验介质为纯净水,在压力为5mpa的条件下,测试30min,保证钎缝不泄露;a2.用不锈钢材质粗车环状本体4,在其环面粗钻多个基准孔,环周镗铣多个进水孔,根据进水孔位置在本体内周线切割出多个扇形槽和多个楔形竖槽,并在槽口出形成止口;用不锈钢材质加工与扇形槽匹配的多个上盖板和多个下盖板,在各上盖板和下盖板的内端面加工有与多个楔形镶块匹配的接口;用不锈钢材质加工出与楔形竖槽匹配的多个楔形镶块,并在各楔形镶块的内端面加工出台阶槽和32个角度为15
°
、直径为3mm的流量孔,内部加工出7个流道方孔,两面分别加工出至少3个钎料槽;在止口和钎料槽处预置镍基膏状钎料,将多个上盖板、多个下盖板分别装配在多个扇形槽处,使每组上盖板与下盖板之间形
成扇形水槽;将多个楔形镶块分别装配在多个楔形竖槽处,使进水孔、扇形水槽、流道方孔与流量孔相连通;将装配后的本体、上盖板、下盖板和楔形镶块放入真空钎焊炉的有效区进行真空钎焊;用高强铜合金材质加工出多个尺寸不同的环肋5,并在四个环肋5的外表面车加工16条3mm宽的冷却槽道,使相邻冷却槽道之间形成3mm宽的筋条;用煤油、酒精清洗本体4和环肋5,在各筋条部位粘贴一层0.1mm厚的镍基含金钎料,如图7所示,将四个环肋5装配在本体4内周,使环肋5的接口与镶块的流道方孔对应,冷却槽道与流量孔对应;在如图8、图9所示的本体工装6与本体4、环肋5的接触面分别涂刷厚度为0.1
‑
0.2mm阻钎剂;用本体工装6将环肋5与本体4固定,具体的,本体工装6包括固定在底座61上且依次设在环肋内部的多个衬板63和顶板62;衬板63的内端面和顶板62均设为正多边形,衬板63的外端面设为与环肋5匹配的弧形;顶板62上均匀开设多个压紧孔,通过在压紧孔中固定压紧件64使衬板63压紧环肋5,使环肋5与本体4紧贴;将本体工装6、环肋5与本体4一并放置在真空钎焊炉中,按照以下参数进行钎焊:冷态真空度2
‑5×
10
‑2pa,工作真空度3
‑
5pa;以60
‑
90℃/h的速率加热至400
‑
500℃,保持0.3
‑
0.5h;以90
‑
120℃/h的速率加热至900
‑
950℃,保持4
‑
6h;以120
‑
150℃/h的速率加热至1010
‑
1035℃,保持0.2
‑
0.5h;加热结束后,以90
‑
120℃/h控温冷却至700
‑
750℃,随炉冷却至400
‑
500℃向炉内填充高纯氩气使炉内压力达到6
‑8×
104pa后启动风扇冷却至100℃以下出炉;钎焊完成后得到如图5、图6所示本体组件;钎焊结束后,目视检验钎缝的完整性,对本体组件腔道压力测试;具体的,试验介质为纯净水,在压力为5mpa的条件下,测试30min,确保钎缝不泄露;a3.如图10所示,将本体组件线切为本体内环10和本体外环11;在本体内环10和环肋的上、下端面分别精车出沉台面,并根据沉台面用高强铜合金材质精铣出下表面与沉台面匹配,上表面为平面的补偿块7;并用高强铜合金材质粗车内端面为平面,外端面与环肋匹配的加强块8,在其中间开设方槽,并在方槽两侧及加强块8外端面线切出钎料槽;用煤油、酒精清洗补偿块7、加强块8,如图11所示,在加强块8的钎料槽中预置膏状钎料后装配在本体内环10的内端面,将k形隔板组件外端的隔板1穿过加强块8的方槽和环肋5接口后装配在镶块的台阶槽中;在补偿块7的底面粘贴一层0.1mm的镍基含金粘带钎料后装配在沉台面中;在如图12、13所示的腔体工装9与k形隔板组件、加强块8、补偿块7和本体内环接触面分别涂刷厚度为0.1
‑
0.2mm阻钎剂;用腔体工装9固定k形隔板组件、加强块8、补偿块7和本体内环10固定,具体的,腔体工装9包括连接在第一固定板91和第二固定板92之间的固定组件93;第一固定板91的内端面为适应于k形隔板腔外端面的弧面,外端面设为平面,第二固定板92的内端面设为平面,外端面设为适应于k形隔板腔内端面的弧面;在第一固定板91上部至底部之间开设有适应于隔板1尺寸的竖槽,第一固定板91和第二固定板92上均设有用于贯穿固定组件93的开孔,将固定组件93贯穿、固定在第一固定板91和第二固定板92之间的开孔中,使补偿块7、加强块8与本体内环10压紧;
将腔体工装9、k形隔板组件、加强块8、补偿块7和本体内环10一并放置在真空钎焊炉中,按照以下参数进行钎焊:冷态真空度2
‑5×
10
‑2pa,工作真空度3
‑
5pa;以45
‑
60℃/h的速率加热至400
‑
500℃,保持0.3
‑
0.5h;以60
‑
90℃/h的速率加热至900
‑
950℃,分压3
‑
5pa,保持4
‑
5h;以90
‑
120℃/h的速率加热至1010
‑
1035℃,3
‑
5pa,保持0.2
‑
0.5h;加热结束后以90
‑
120℃/h控温冷却至700
‑
750℃,随炉冷却至400
‑
500℃向炉内填充高纯氩气使炉内压力达到6
‑8×
104pa后启动风扇冷却至100℃以下出炉;钎焊完成后得到k形隔板分腔;目视检验钎缝的完整性,对k形隔板分腔进行压力测试;具体的,试验介质为纯净水,在压力为5mpa的条件下,测试30min,保证钎缝不泄露;a4.如图14、15所示,将本体外环11氩弧焊在k形隔板分腔的外周,为了防止对钎缝的影响,在循环水的冷却下,进行氩弧焊操作;精加工k形隔板腔至设计尺寸,并去加强块8多余的部分;精加工完成后,得到如图16所示的k形隔板腔;将k形隔板腔置于真空钎焊炉中消除应力;对k形隔板腔腔道压力测试;具体的,试验介质为纯净水,在压力为5mpa的条件下,测试30min,确保钎缝不泄露。
19.通过上述方法实现了k形隔板腔的加工,在压力实验过程中,腔道均没有泄露,且k形隔板组件的形变在0.5mm以内,满足设计要求。
20.本发明的有益效果是:为了保证k形隔板组件与本体组件的装配钎焊质量,首先,将本体组件分为本体内环、本体外环,本体内环先与异形的k形隔板组件装配并钎焊,得到隔板腔分体后,再与本体外环进行氩弧焊;通过上述方法不仅降低了k形隔板组件与本体组件的装配难度和装配工作量,也减小了本体组件与k形隔板组件的质量差,使钎焊过程中热量分布相对均匀,减小了钎焊时k形隔板组件的变形;调整了本体内环与k形隔板组件的钎焊结构,增加了加强块和补偿块,将本体组件与k形隔板组件的钎焊调整为k形隔板组件、加强块、补偿块与本体内环的钎焊,增加了钎焊面积,加强了钎缝强度。
21.本发明的内容不限于实施例所列举,本领域普通技术人员通过阅读本发明说明书而对本发明技术方案采取的任何等效的变换,均为本发明的权利要求所涵盖。