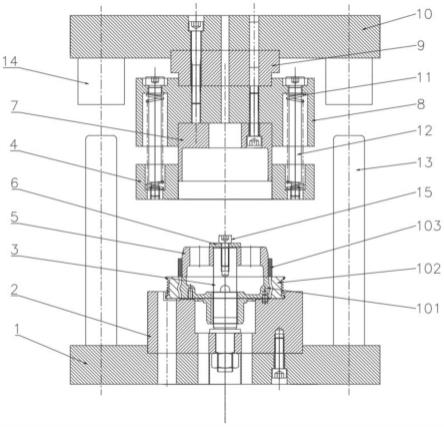
1.本发明涉及汽车发动机内橡胶减震轮总成的装配工装及工艺。
背景技术:2.目前,汽车发动机的传动皮带轮主要采用一组槽型进行传动,其中曲轴皮带轮为了达到降低震动和降低运行中的噪音,常采用橡胶减震轮作为汽车发动机的曲轴皮带轮,这样可以减少因发动机工作时产生的冲击振动,在普通的全铁皮带轮上,在中间环形切开成内外两个部分,在内轮毂、外带轮两部分之间的极小间隙里填充橡胶圈,也就是一橡胶层,这样发动机的动力首先传到内轮毂,再转到中间层减振橡胶圈,再从减振橡胶圈传到外带轮。这样,发动机的振动和响声就会因橡胶“层缓”后在铁质外带轮得到减小,从而降低噪音和缓解振动(冲击力)。现有的橡胶减震轮加工工艺多为注塑机将橡胶加热融化后注入内轮毂、外带轮之间,然后硫化降温后成型,这种加工工艺在橡胶降温后体积收缩,压脱力强度和扭转强度难以达到设计要求,且注塑机难以稳定控制,生产废品率高,产能节拍难以匹配需求。
技术实现要素:3.为了克服现有技术的上述不足,本发明的目的在于提供一种橡胶减震轮总成装配工装,解决注塑硫化工艺压脱力强度和扭转强度不足的问题,有效保证产品质量,压装效率高,且废品率低。
4.本发明的目的还在于提供一种橡胶减震轮总成装配工艺。
5.本发明的技术方案在于:一种橡胶减震轮总成装配工装,包括相对设置的上模板、下模板。
6.所述下模板上设有用于定位外带轮的下固定板;下固定板上装有用于与下固定板配合定位内轮毂的芯轴;用于将内轮毂压紧于下固定板且用于定位橡胶圈的定位器套装于芯轴;还包括一用于与装于芯轴上端的螺栓配合以快速装入/取下定位器的开口垫圈。
7.所述芯轴包括用于与下固定板连接的基准段、用于定位内轮毂和定位器的定位段。
8.所述定位器中心孔与芯轴定位段间隙配合;所述螺栓头部外径小于定位器中心孔内径;所述开口垫圈外径大于定位器中心孔内径;所述开口垫圈开口宽度小于螺栓头部外径、大于螺栓杆部外径。
9.所述下固定板上设有台阶定位槽,所述台阶定位槽包括三级台阶:用于定位外带轮的第一级台阶、用于定位内轮毂的第二级台阶、用于容置内轮毂小径段的第三级台阶。
10.所述第一级台阶与第二级台阶连接处设有用于保证橡胶圈压入后整圈平整避免尺寸超差的环状凸起。
11.所述台阶定位槽第三级台阶底部设有芯轴装配孔。
12.所述台阶定位槽第一级台阶与外带轮相对应处均布有多个l形排气槽,用于压装
过程中气体排出以免外带轮破裂;所述l形排气槽竖直部位于台阶定位槽第一级台阶内壁,水平部位于台阶定位槽第一级台阶底面。
13.所述定位器外圆周面由位于下部的定位面、位于中部的导向斜面、位于上部的导向弧面组成,导向弧面与导向斜面便于橡胶圈放入到定位器外,定位面用于定位橡胶圈;所述导向斜面与水平面夹角为78
°
~83
°
。
14.所述上模板上连接有上固定板;用于将置于定位器外的橡胶圈压入内轮毂与外带轮之间的压盘连接于上固定板下端。
15.用于与压盘同步下行将外带轮压紧于下固定板的上压板经限位导向柱与上固定块活动连接;所述上压板中心孔与压盘间隙配合。
16.所述上固定板上呈环形阵列设置有多个通孔一,所述各通孔一内设有凸缘。
17.所述上压板上与通孔一对应处设有通孔二;所述通孔二为台阶孔。
18.限位导向柱装于通孔一内,限位导向柱上端大头部与凸缘上端面相卡,限位导向柱下端与通孔二小台阶部相连。
19.所述上压板下端面与限位导向柱上端面之间的间距等于压盘下端压装面与上模板下端面之间的间距。
20.所述限位导向柱上套装有弹簧;所述弹簧上端与上固定块相抵,下端与上压板相抵;上压板与上固定板、压盘同步下行至与外带轮接触后,上固定板继续带动压盘克服弹簧弹力下行以将橡胶圈压入内轮毂与外带轮之间。
21.所述下固定板上设有用于让位内轮毂上定位销的让位孔。
22.所述l形排气槽宽度为5
±
0.2mm,深度为0.5
±
0.1mm;所述l形排气槽有三个。
23.所述芯轴基准段与定位段之间设有用于与下固定板相抵的凸缘;所述基准段与定位段同轴度为0.02mm;所述芯轴定位段与定位器中心孔的配合间隙为0.05mm。
24.所述下模板、上模板上设有相互配合在模具合模时起导向作用的导柱、导套。
25.所述通孔二小台阶部为用于与限位导向柱下端连接的螺纹孔。
26.所述弹簧上端与通孔一内凸缘下端面相抵,弹簧下端与通孔二内台阶面相抵。
27.所述上固定板与上模板之间设有上垫板;所述上模板下端面设有用于与上垫板上端配合的凹槽,所述上固定板上端面设有与上垫板下端配合的凹槽。
28.所述上固定板下端面设有用于装配压盘的凹槽。
29.所述压盘外圆周壁与内圆周壁同轴度为0.05mm,外圆周壁、内圆周壁与压装面交汇处为便于橡胶圈压入到内轮毂和外带轮之间空隙的尖角;所述压盘与上压板中心孔的配合间隙为0.05mm。
30.本发明还提供一种使用上述橡胶减震轮总成装配工装进行装配的橡胶减震轮总成装配工艺,包括如下步骤:1)将上模板、下模板连接于油压机;将橡胶圈放入加温箱内;2)将内轮毂套装在芯轴上,并下移至下固定板第二级台阶上;3)将定位器套装在芯轴上后,装入开口垫圈并锁紧螺栓使定位器压紧内轮毂;4)将外带轮放置在下固定板第一级台阶上;5)将橡胶圈从加温箱内取出,表面沾(压装)润滑油后,经定位器导向弧面与导向斜面套装于定位器外置于定位器定位面处;
6)油压机驱动上模板带动上固定板、上压板、压盘同步下行;当上压板下端接触到外带轮后,橡胶圈被限制在上压板和定位器之间;上模板带动上固定板、压盘克服弹簧弹力压缩弹簧继续下行将橡胶圈压入内轮毂与外带轮之间的空隙内,限位导向柱上端面与上模板下端面接触后,保持压力6~10秒;7)油压机驱动上模板带动上固定板、压盘上行至限位导向柱上端大头部与凸缘上端面接触后,上压板与上固定板、压盘、上模板同步上行回位,压装完成;8)拧松螺栓取下开口垫圈,取下定位器,取出产品。
31.本发明使用加工完成的橡胶圈、内轮毂和外带轮,使用油压机,在总成装配工装上,通过芯轴和定位器将内轮毂固定,下固定板将外带轮定位;将橡胶圈放入定位器的外面,放置容易且不易损坏橡胶圈;然后通过油压机工作带动上固定板、上压板、压盘同步下行至上压板与外带轮接触后,上固定板继续带动压盘克服弹簧弹力下行将橡胶圈慢慢压入到内轮毂和外带轮之间的空隙内,将内轮毂、外带轮和橡胶圈组合成一个整体,完成橡胶减震轮的装配,在压装完成后,上模复位上行,成品固定在下模,取下开口垫圈,即可取出定位器和成品。本发明既解决注塑硫化工艺压脱力强度和扭转强度不足的问题,提供了合格的橡胶减震轮,有效保证产品质量,生产效率高,同时废品率低,易于成本控制。
附图说明
32.图1为本发明装配工装的结构示意图。图2为下固定板的结构示意图。
33.图3为图2的a-a剖视图。
34.图4为芯轴的结构示意图。
35.图5为定位器的结构示意图。
36.图6为图4的俯视图。
37.图7为开口垫圈的结构示意图。
38.图8为图7的俯视图。
39.图9为上固定板的结构示意图。
40.图10为图9的俯视图。
41.图11为上压板的结构示意图。
42.图12为图11的俯视图。
43.图13为压盘的结构示意图。
44.图14为本发明的工艺步骤示意图之一。
45.图15为本发明的工艺步骤示意图之二。
46.图16为本发明的工艺步骤示意图之三。
47.图17为本发明的工艺步骤示意图之四。
48.图18为本发明的工艺步骤示意图之五。
49.图19为本发明的工艺步骤示意图之六。
50.图中,下模板1;内轮毂101,外带轮102,橡胶圈103;下固定板2、台阶定位槽201、第一级台阶2011、第二级台阶2012、第三级台阶2013、环状凸起202、l形排气槽203、芯轴装配孔204、让位孔205;芯轴3、基准段104、定位段105、凸缘301;定位器5、定位面501、502、导向
斜面108、导向弧面107;开口垫圈6;螺栓15;上固定板8、通孔一112、凸缘113、凹槽114、尖角115;压盘7、外圆周壁109、内圆周壁110、压装面111;上压板4、中心孔401、通孔二106;限位导向柱12;弹簧11;上模板10;上垫板9;导柱13;导套14。
具体实施方式
51.图1中,本发明的橡胶减震轮总成装配工装,包括相对设置的上模板10、下模板1;下模板1、上模板10上设有相互配合在模具合模时起导向作用的导柱13、导套14。
52.下模板1上设有用于定位外带轮102的下固定板2;下固定板2上装有用于与下固定板2配合定位内轮毂101的芯轴3;用于将内轮毂101压紧于下固定板2且用于定位橡胶圈103的定位器5套装于芯轴3。还包括一用于与装于芯轴3上端的螺栓15配合以快速装入/取下定位器5的开口垫圈6,如图7、图8所示。
53.芯轴3包括用于与下固定板2连接的基准段104、用于定位内轮毂101和定位器5的定位段105;芯轴3基准段104与定位段105之间设有用于与下固定板2相抵的凸缘301;基准段104与定位段105同轴度为0.02mm,如图4所示。
54.定位器5中心孔502与芯轴3定位段105间隙配合;两者的配合间隙为0.05mm。螺栓15头部外径小于定位器5中心孔502内径;开口垫圈6外径大于定位器5中心孔502内径;开口垫圈6开口宽度小于螺栓15头部外径、大于螺栓15杆部外径。
55.下固定板2上设有台阶定位槽201,如图2、图3所示,台阶定位槽201包括三级台阶:用于定位外带轮102的第一级台阶2011、用于定位内轮毂101的第二级台阶2012、用于容置内轮毂101小径段的第三级台阶2013。第一级台阶2011与第二级台阶2012连接处设有用于保证橡胶圈103压入后整圈平整避免尺寸超差的环状凸起202。台阶定位槽第三级台阶2013底部设有芯轴装配孔204。台阶定位槽201第一级台阶2011与外带轮102相对应处均布有三个l形排气槽203,l形排气槽203宽度为5
±
0.2mm,深度为0.5
±
0.1mm用于压装过程中气体排出以免外带轮102破裂;l形排气槽竖直部位于台阶定位槽201第一级台阶2011内壁,水平部位于台阶定位槽201第一级台阶2011底面。下固定板2上设有用于让位内轮毂上定位销的让位孔205。
56.定位器5外圆周面由位于下部的定位面501、位于中部的导向斜面108、位于上部的导向弧面107组成,导向弧面107与导向斜面108便于橡胶圈103放入到定位器5外,定位面501用于定位橡胶圈103;导向斜面108与水平面夹角为81
°±
30
′
;如图5、图6所示。
57.上模板10上连接有上固定板8;上固定板8与上模板10之间设有上垫板9;上模板10下端面设有用于与上垫板9上端配合的凹槽,上固定板8上端面设有与上垫板9下端配合的凹槽。用于将置于定位器5外的橡胶圈103压入内轮毂101与外带轮102之间的压盘7连接于上固定板8下端;上固定板8下端面设有用于装配压盘7的凹槽114。上固定板8上呈环形阵列设置有多个通孔一112,各通孔一112内设有凸缘113,如图9、图10所示。
58.压盘7外圆周壁109与内圆周壁110同轴度为0.05mm,外圆周壁109、内圆周壁110与压装面111交汇处为便于橡胶圈103压入到内轮毂101和外带轮102之间空隙的尖角115,如图13所示。
59.用于与压盘7同步下行将外带轮102压紧于下固定板2的上压板4经限位导向柱12与上固定块8活动连接;上压板4中心孔401与压盘7间隙配合,两者的配合间隙为0.05mm。上
压板4上与通孔一112对应处设有通孔二106;通孔二106为台阶孔;如图11、图12所示。
60.限位导向柱12装于通孔一112内,限位导向柱12上端大头部与凸缘113上端面相卡,限位导向柱12下端与通孔二106小台阶部螺纹孔相连。上压板4下端面与限位导向柱12上端面之间的间距等于压盘7下端压装面111与上模板10下端面之间的间距。限位导向柱12上套装有弹簧11;弹簧11上端与上固定块8通孔一内凸缘113下端面相抵,下端与上压板4通孔二106内台阶面相抵;上压板4与上固定板8、压盘7同步下行至与外带轮102接触后,上固定板8继续带动压盘7克服弹簧11弹力下行以将橡胶圈103压入内轮毂101与外带轮102之间。
61.本发明的橡胶减震轮总成装配工艺,包括如下步骤:1)将上模板10、下模板1连接于油压机;将橡胶圈103放入加温箱内;2)将内轮毂101套装在芯轴3上,并下移至下固定板2第二级台阶2012上;3)将定位器5套装在芯轴3上(如图14所示)后,装入开口垫圈6并锁紧螺栓15使定位器5压紧内轮毂101(如图15所示);4)将外带轮102放置在下固定板2第一级台阶2011上(如图16所示);5)将橡胶圈103从加温箱内取出,表面沾压装润滑油后,经定位器5导向弧面107与导向斜面108套装于定位器5外置于定位器5定位面501处(如图17所示);6)油压机驱动上模板10带动上固定板8、上压板4、压盘7同步下行;当上压板4下端接触到外带轮102后,橡胶圈103被限制在上压板4和定位器5之间(如图18所示);上模板10带动上固定板8、压盘7克服弹簧11弹力继续下行将橡胶圈103压入内轮毂101与外带轮102之间的空隙内,限位导向柱12上端面与上模板10下端面接触后,此时上固定板8下端面与上压板4上端面接触,保持压力6秒(如图19所示);7)油压机驱动上模板10带动上固定板8、压盘7上行至限位导向柱12上端大头部与凸缘113上端面接触后,上压板4与上固定板8、压盘7、上模板10同步上行回位,压装完成;8)拧松螺栓15取下开口垫圈6,取下定位器5,取出产品。