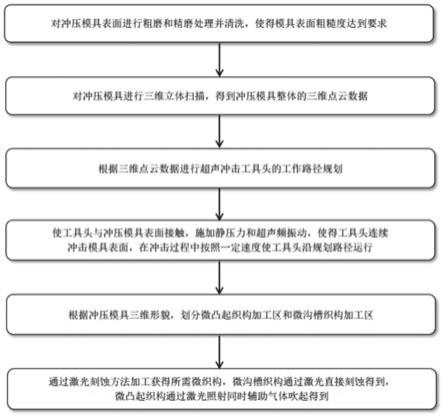
1.本发明涉及冲压模具表面处理技术领域,具体为一种超声冲击与微织构加工复合处理的冲压模具及方法。
背景技术:2.冲压模具是冲压工艺中通过压力压迫板料发生塑性变形的重要工具,冲压模具的表面处理技术决定着成形工件的质量。在冲压过程中,模具接触面积大,加之翻边过程中板料变形伴随巨大变形力,使得凹凸模具与板料之间容易发生剧烈摩擦,长时间摩擦易导致模具磨损,降低模具寿命。
3.目前的模具表面处理技术主要有渗碳、渗氮、镀铬、激光熔覆、td、pvd、cvd等,这些表面处理技术存在各种缺点:渗碳技术的废气燃烧影响环境,处理后的模具易出现表面晶间氧化等问题;渗氮技术易产生疏松多孔的表面化合物层,且脆性较大;镀铬技术的废液会污染环境,且不适用于高强板;激光熔覆技术其冷却过程中熔覆层内会产生残余应力,缺乏专用材料适配于所有模具;td覆层处理存在变形量,后期二次加热易导致成形件变形或开裂;pvd物理气相沉积技术的镀层耐热性普遍较差,成本较高;cvd化学气相沉积反应温度高,易导致模具变形,且沉积层界面易发生扩散。
4.针对冲压模具的摩擦磨损问题,中国专利“一种复合织构轧辊成形模具及其复合织构成形方法”,在轧辊冲压模具表面的不同区域设置微凸起织构和微凹坑织构,提高轧辊模具耐磨性能,改善材料流动。但其直接在光滑模具表面加工的微织构,并没有提高模具表面本身的耐磨性,微织构耐磨性较差,在实际工作中很容易快速被磨掉形貌,从而失去作用。
技术实现要素:5.为了解决现有技术中存在的技术问题,本发明旨在提供一种冲压模具表面超声冲击与微织构复合处理方法。本发明对冲压模具进行三维形貌分析,规划工具头运行路径,使工具头与模具表面接触,按规划路径运行,施加超声频震动使得工具头连续冲击模具表面,使模具表面纳米晶化。根据模具三维形貌划分微凸起织构加工区和微沟槽织构加工区,在超声冲击后的模具表面上通过激光加工获得微凸起织构和微沟槽织构。
6.本发明采用的技术方案如下:
7.第一方面,本发明提供了超声冲击与微织构加工复合处理冲压模具的方法,包括以下几个步骤:
8.步骤(1)对冲压模具的凸模和凹模进行粗磨和精磨处理;
9.步骤(2)对超声冲击工具头的工作路径进行规划;
10.步骤(3)将超声冲击工具头与冲压模具表面接触,对超声冲压工具头施加设定的静压力,同时对工具头施加超声频振动,使得工具头连续冲击模具表面,在冲击过程中按照设定速度使工具头沿规划路径运行;
11.步骤(4)将冲压模具的凸模工作表面分为接触区和非接触区;将冲压模具的凹模工作表面分为接触区和非接触区;再将凸模和凹模的接触区分为圆角区、立面区、其他区;
12.步骤(5)在凸模的圆角区和立面区加工微凸起织构,在凹模的圆角区和立面区加工微沟槽织构。
13.上述冲压模具表面超声冲击与微织构复合处理方法,通过该方法加工后的冲压模具表面硬度、耐磨性、耐腐蚀性提高,同时模具表面摩擦特性和材料流动得到主动优化,模具工作过程中的摩擦磨损大幅降低,模具寿命增长,模具冲压获得的成形件质量有所提高。
14.作为进一步的技术方案,凸模圆角区需要带动材料向下流动,为了增强此区域的材料流动,减少板材的减薄,需要在此区域加工微凸起织构。凸模立面区的材料需要在凸模带动下流入凹腔,为了促进材料流动,减少板材减薄,需要在此区域加工微凸起织构。
15.作为进一步的技术方案,凹模圆角区需要更好地让材料流入凹腔,此区域的摩擦系数需要尽可能的小,所以需要在此区域加工微沟槽织构。同理凹模立面区摩擦系数也应尽可能的小,所以需要在此区域加工微沟槽织构。
16.作为进一步的技术方案,微凸起织构具体形貌为高与底面直径比例为2:3的椭球冠状织构,在凹模的圆角区和立面区加工微沟槽织构,微沟槽织构具体形貌为横截面是正方形(深度与宽度比例为1:1)且与凹凸模的相对运动方向垂直的沟槽织构,且微沟槽织构与凹凸模的相对运动方向垂直。通过激光刻蚀方法加工获得所需微织构,微沟槽织构通过激光直接刻蚀得到,微凸起织构通过激光照射同时辅助气体吹起得到。
17.第二方面,本发明还提供了一种冲压模具,其通过前面所述的复合处理方法获得。
18.以上一个或多个技术方案存在以下有益效果:
19.(1)将超声纳米表面改性技术和微织构技术结合起来,可以综合两项技术的优点,与直接在模具上加工微织构相比,在纳米晶层上加工微织构会使织构硬度和耐磨性大幅提高,延长微织构存在时间,提高微织构减摩抗磨、改善材料流动的功效。
20.(2)冲压模具经超声冲击后的表面可以获得纳米晶体和残余压应力,模具表面硬度、耐磨性、耐腐蚀性大幅提升,提升冲压模具疲劳性能,同时表面形貌更加平整规则。
21.(3)冲压模具表面经激光加工后的微沟槽织构周围区域会出现显微硬度提高现象,提高冲压模具表面的整体硬度,增强模具耐磨性。
22.(4)冲压模具表面加工微凸起织构可以增大接触界面摩擦系数,可抑制材料流动,能略微减小板料最大减薄率。冲压模具表面加工微沟槽织构能储存润滑油和摩擦产生的磨粒,在工作过程中持续给油,减小接触界面的摩擦系数,可促进材料流动。在冲压模具特定的曲面区域加工适配于该区域的特定种类、特定形貌、特定分布、特定参数的微织构,可以对模具表面的摩擦特性分布和材料流动属性进行主动控制及优化,提高模具使用寿命,提高成形件质量,避免或减少板料减薄、褶皱、回弹、均匀性差等问题的出现。
23.(5)微凸起织构设置为高与底面直径比例为2:3的椭球冠状织构,微沟槽织构设置为横截面是正方形(深度与宽度比例为1:1)且与凹凸模的相对运动方向垂直的沟槽织构,是发挥织构功效的最佳形貌,能最大限度改善工件材料流动,降低模具表面摩擦磨损。
附图说明
24.图1为复合处理方法工艺流程图;
25.图2为超声冲击工作原理图;
26.图3为典型冲压模具表面区域划分图;
27.图4为微织构加工区域判定流程图;
28.图5为微沟槽织构加工示意图;
29.图6为微凸起织构加工示意图;
30.图7(a)为超声冲击路径规划中的凸模;图7(b)为超声冲击路径规划中的凸模路径规划示意图;图7(c)为超声冲击路径规划中的凹模;图7(d)为超声冲击路径规划中的凹模路径规划示意图;
31.图8(a)为微织构中的凸模加工区域划分示意图;图8(b)为微织构中的凹模加工区域划分示意图;
32.图9(a)为微凸起织构横截面示意图;图9(b)微沟槽织构横截面示意图;
33.图中:1为超硬工具头;2为纳米晶层;3为工件;4为竖直方向超声频振动;5为静压力;6为激光束;7为振镜;8为聚焦点;9为工作台;10为吹气管;11为凸模;12为凸模表面超声冲击路径;13为凹模;14为凹模表面超声冲击路径;15为凸模圆角区;16为凸模立面区;17为凹模圆角区;18为凹模立面区;19为微凸起织构横截面;20为微沟槽织构横截面。
具体实施方式
34.应该指出,以下详细说明都是例示性的,旨在对本发明提供进一步的说明。除非另有指明,本发明使用的所有技术和科学术语具有与本发明所属技术领域的普通技术人员通常理解的相同含义。
35.需要注意的是,这里所使用的术语仅是为了描述具体实施方式,而非意图限制根据本发明的示例性实施方式。如在这里所使用的,除非本发明另外明确指出,否则单数形式也意图包括复数形式,此外,还应当理解的是,当在本说明书中使用术语“包含”和/或“包括”时,其指明存在特征、步骤、操作、器件、组件和/或它们的组合;
36.本实施例提出了一种冲压模具表面超声冲击与微织构复合处理方法,其中,超声纳米表面改性技术是通过超硬冲击头对金属表面进行均匀超声冲击,使得工件表面材料晶粒破碎后形成纳米晶。超硬冲击头超声冲击后的材料表面可以获得纳米晶体和残余压应力,材料表面硬度大幅提升,表面形貌更加平整规则,提高了工件的耐磨性。但是,在冲压模具表面进行超声冲击,虽然可以获得表面纳米晶层,提高模具表面硬度和耐磨性,但无法改善成形件材料流动和应力分布,提高成形件质量。
37.因此,本技术将超声纳米表面改性技术和微织构技术结合起来,可以综合两项技术的优点,大幅提高冲压模具表面硬度和耐磨性,减小实际工作中冲压模具受到的摩擦力,改善金属板材成形质量,提高冲压模具使用寿命。
38.下面结合附图对本发明进行详细说明:
39.如图1所示,本实施例提供一种冲压模具表面超声冲击与微织构复合处理方法,对冲压模具进行三维形貌分析,规划工具头运行路径,使工具头与模具表面接触,按规划路径运行,施加超声频震动使得工具头连续冲击模具表面,使模具表面纳米晶化。根据模具三维形貌划分微凸起织构加工区和微沟槽织构加工区,在超声冲击后的模具表面上通过激光加工获得微凸起织构和微沟槽织构。具体的步骤如下:
40.(1)对冲压模具的凸模和凹模进行粗磨和精磨处理,使得冲压模具表面粗糙度达到:轮廓的算术平均偏差≤0.6μm,轮廓的最大高度≤3.2μm。并对精磨完成后的冲压模具进行清洗剂清洗。
41.(2)对冲压模具进行三维立体扫描,得到冲压模具整体的三维点云数据,根据三维点云数据进行超声冲击工具头的工作路径规划。
42.(3)将超声冲击工具头与冲压模具表面接触,通过空压机施加一定静压力,同时通过压电陶瓷换能器对工具头施加超声频振动,使得工具头连续冲击模具表面,在冲击过程中按照一定速度使工具头沿规划路径运行,具体参见图7(a)-图7(d);
43.(4)根据冲压模具三维形貌,划分微凸起织构加工区和微沟槽织构加工区。将凸模和凹模的工作表面分为接触区和非接触区,再将接触区分为圆角区、立面区、其他区,具体参见图8(a)中显示了凸模圆角区15和凸模立面区16;图8(b)显示了凹模圆角区17和凹模立面区18。
44.(5)在凸模的圆角区和立面区加工微凸起织构(参见图9(a)),微凸起织构具体形貌为高与底面直径比例为2:3的椭球冠状织构,在凹模的圆角区和立面区加工微沟槽织构,微沟槽织构具体形貌为横截面是正方形(深度与宽度比例为1:1)且与凹凸模的相对运动方向垂直的沟槽织构(参见图9(b)),且微沟槽织构与凹凸模的相对运动方向垂直。进一步的,本实施例中通过激光刻蚀方法加工获得所需微织构,微沟槽织构通过激光直接刻蚀得到(具体参见图5),微凸起织构通过激光照射同时辅助气体吹起得到(具体参见图6)。
45.其中,超声冲击工作原理如图2所示,其中超硬工具头1对工件3施加静压力5和竖直方向超声频振动4,然后会在工件3的表面形成一层纳米晶层2;超声纳米表面改性技术是通过超硬冲击头对金属表面进行均匀超声冲击,使得工件表面材料晶粒破碎后形成纳米晶。超硬冲击头超声冲击后的材料表面可以获得纳米晶体和残余压应力,材料表面硬度大幅提升,表面形貌更加平整规则,提高了工件的耐磨性。但是,在冲压模具表面进行超声冲击,虽然可以获得表面纳米晶层,提高模具表面硬度和耐磨性,但无法改善成形件材料流动和应力分布,提高成形件质量。
46.凸模圆角区需要带动材料向下流动,为了增强此区域的材料流动,减少板材的减薄,需要在此区域加工微凸起织构。凸模立面区的材料需要在凸模带动下流入凹腔,为了促进材料流动,减少板材减薄,需要在此区域加工微凸起织构。凹模圆角区需要更好地让材料流入凹腔,此区域的摩擦系数需要尽可能的小,所以需要在此区域加工微沟槽织构。同理凹模立面区摩擦系数也应尽可能的小,所以需要在此区域加工微沟槽织构。
47.因此,微织构是通过激光刻蚀等方法在工件表面加工特定形状微纳结构,可以改善摩擦副间的摩擦学性能,并已在刀具减摩、机械密封、轴承润滑等领域有所应用,在模具表面处理领域具有广泛应用前景。微凸起织构具有钉扎犁耕效应,能增大接触界面摩擦系数,板料发生塑性变形时变形抗力、流动阻力大,可抑制材料流动,能略微减小板料最大减薄率。微沟槽/微凹坑织构能储存润滑油和摩擦产生的磨粒,在工作过程中持续给油,减小接触界面的摩擦系数,板料发生塑性变形时变形抗力、流动阻力小,可促进材料流动。在冲压模具的复杂曲面表面进行微沟槽和微凸起织构的加工,在特定的曲面区域加工适配于该区域的特定种类、特定形貌、特定分布、特定参数的微织构,可以对模具表面的摩擦特性分布和材料流动属性进行主动控制及优化,提高模具使用寿命,提高成形件质量,避免或减少
板料减薄、褶皱、回弹、均匀性差等问题的出现。但是在冲压模具表面直接加工微织构,无法提高模具本身的耐磨性,加工出的微织构由于形貌尺寸小,很容易在实际冲压时被快速磨掉织构形貌,失去作用。
48.本实施例中将超声纳米表面改性技术和微织构技术结合起来,可以综合两项技术的优点,与直接在模具上加工微织构相比,在纳米晶层上加工微织构会使织构硬度和耐磨性大幅提高,延长微织构存在时间,提高微织构减摩抗磨、改善材料流动的功效。
49.本实施例中的冲压模具经超声冲击后的表面可以获得纳米晶体和残余压应力,模具表面硬度、耐磨性、耐腐蚀性大幅提升,提升冲压模具疲劳性能,同时表面形貌更加平整规则。
50.本实施例中的冲压模具表面经激光加工后的微沟槽织构周围区域会出现显微硬度提高现象,提高冲压模具表面的整体硬度,增强模具耐磨性。
51.本实施例中的冲压模具表面加工微凸起织构可以增大接触界面摩擦系数,可抑制材料流动,能略微减小板料最大减薄率。冲压模具表面加工微沟槽织构能储存润滑油和摩擦产生的磨粒,在工作过程中持续给油,减小接触界面的摩擦系数,可促进材料流动。在冲压模具特定的曲面区域加工适配于该区域的特定种类、特定形貌、特定分布、特定参数的微织构,可以对模具表面的摩擦特性分布和材料流动属性进行主动控制及优化,提高模具使用寿命,提高成形件质量,避免或减少板料减薄、褶皱、回弹、均匀性差等问题的出现。
52.本实施例中:微凸起织构设置为高与底面直径比例为2:3的椭球冠状织构,微沟槽织构设置为横截面是正方形(深度与宽度比例为1:1)且与凹凸模的相对运动方向垂直的沟槽织构,是发挥织构功效的最佳形貌,能最大限度改善工件材料流动,降低模具表面摩擦磨损。
53.下面以一种倒梯形冲压模具为例,进行进一步的说明:
54.(1)对倒梯形冲压模具的六个加工表面进行粗磨和精磨处理,使得倒梯形冲压模具表面粗糙度达到:轮廓的算术平均偏差≤0.6μm,轮廓的最大高度≤3.2μm。并对精磨完成后的倒梯形冲压模具进行清洗。
55.(2)通过激光三维扫描仪(或其他适于大面积复杂曲面扫描的设备)以三角形测距法(或其他合适方法)对倒梯形冲压模具发射出激光光点或线性激光,以多个侦测器测量冲压模具表面到激光三维扫描仪的距离,扫描重复3-6次,获取倒梯形冲压模具整体的三维点云数据。
56.根据倒梯形冲压模具三维点云数据,通过三维制图软件在模具表面进行超声冲击工具头工作路径规划,规划工具头直径为10mm,路径间距为0.1-0.3mm。其凸模和凹模路径规划如图7(b)和7(d)所示。
57.(3)使超声冲击工具头与冲压模具表面接触,通过空压机施加一定静压力,同时通过压电陶瓷换能器对工具头施加超声频振动,使得工具头连续冲击模具表面,在冲击过程中按照一定速度使工具头沿规划路径运行。具体加工参数为:静压力:20-100n;振幅:10μm;单位面积冲击次数:8000-50000mm2/次;工具头移动速度:1000-3000mm/min。
58.(4)根据冲压模具三维形貌,将凸模和凹模的工作表面分为接触区和非接触区,再将接触区分为圆角区、立面区、其他区。划分微凸起织构加工区和微沟槽织构加工区,凸模圆角区和凸模立面区为微凸起织构加工区,凹模圆角区和凹模立面区为微沟槽织构加工
区。倒梯形冲压模具的微织构加工区域划分如图8所示。
59.微凸起织构设置为高与底面直径比例为2:3的椭球冠状织构,具体参数为:高度50-200μm,底面直径75-300μm,间距200-500μm;微沟槽织构设置为横截面是正方形(深度与宽度比例为1:1)且与凹凸模的相对运动方向垂直的沟槽织构,具体参数为:深度与宽度均为50-200μm,间距为200-500μm。微织构形貌横截面如图9所示。
60.通过皮秒激光器进行激光刻蚀获得所需微织构,微沟槽织构通过激光直接刻蚀得到,微凸起织构通过激光照射同时辅助气体吹起得到。具体加工参数为:波长:1064nm;功率:5-50w;脉冲重复频率:1-200khz;扫描速度:50-200mm/s;开关光延时:100μs;脉宽:5-15ps;加工重复次数:2-10次;电流:5-30a;环境温度:10-35℃;辅助气体种类:n2和o2;气体压力:0.5-5mpa;吹气角度:30-90
°
。
61.以上所述仅为本发明的优选实施例而已,并不用于限制本发明,对于本领域的技术人员来说,本发明可以有各种更改和变化。凡在本发明的精神和原则之内,所作的任何修改、等同替换、改进等,均应包含在本发明的保护范围之内。