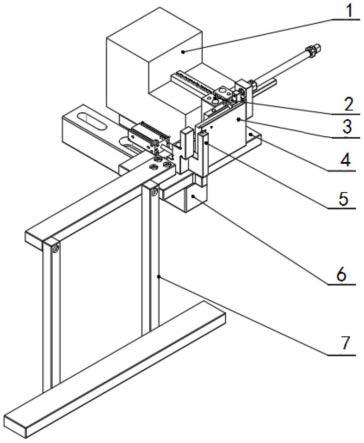
1.本实用新型涉及一种自动送钉系统,尤其是一种螺丝自动送钉系统,属于机加工辅助设备类。
背景技术:2.压铆螺钉是一种广泛用于薄板及钣金件加工中,用于连接母材及装配件的螺钉,按其不同使用场合,可定制多种规格。压铆螺钉定位后铆接在母材上,定位及送料是压铆工艺中最核心环节。
3.压铆机为通用机械,一般下模固定螺钉,上模向下运动施压,共同完成压铆动作。为防止零件与上下模干涉,压铆机上下模均设计成细轴类零件。这种设计虽适用于大部分零件的铆压,同时也限制了铆钉的送料——便于人工放钉,不便于自动化。
4.此外,铆压螺钉通常体积较小,不便于人工定位。对于需分辨方向的螺钉定位更为困难。传统的操作过程如下:先取一颗螺钉,后人工判别方向,再手动将螺钉下表面穿过定位销固定在下模座上。整个过程操作者要高度集中精力,手眼协调,受人的因素影响较大。
技术实现要素:5.本实用新型发明的目的:旨在设计一种自动送钉系统,能将螺钉准确定位在下模上,替代人工取放。
6.这种螺丝机的自动送钉系统,包括螺丝机1、传送轨道组件2、分料组件3、转接板4、二次搬运组件5、底座6和搁置加工件的产品定位架7,所述的螺丝机1、传送轨道组件2、分料组件3和二次搬运组件5分别经设置在底部的螺钉和销钉固定在转接板4上,其中:所述的传送轨道组件2紧挨着螺丝机1外侧设置,所述的传送轨道组件2外侧设置着分料组件3,所述的螺丝机1和轨道组件2的上表面上各设有一道螺丝输送槽1.1和定位轨道2.2,由互为衔接连通的螺丝输送槽1.1、定位轨道2.2组成螺丝机1的铆接螺钉10的外送通道;同时又通过设置在该外送通道尽头、与该外送通道相垂直设置的组成分料组件3中的滑槽轨道3.2构成相互贯通的t字形螺钉输送通道;所述的二次搬运组件5位于分料组件3左侧的转运板4的上表面并与架设在转运板4下底面上的底座固定连接;所述的产品定位架7为一矩形框架机构,其上部边框的右边伸出端通过连接螺钉与转运板4固定连接,使整块转运板4及其上部构件与产品定位架7形成悬臂状连接结构。
7.进一步地,所述的传送轨道组件2为一矩形块体,其上表面上设有一道与螺丝机1上设置的螺丝输送槽1.1连通的同规格定位轨道2.2,并在定位轨道面上设有一块经螺栓固定的有孔盖板2.1。
8.进一步地,所述的分料组件3由滑槽轨道3.2、压紧销3.3、分料滑槽3.4、轨道限位块3.5、压块3.7和移动气缸3.6组成,所述轨道限位块3.5设置在滑槽轨道3.2的左侧边、并通过下部的螺钉与滑槽轨道3.2固定连接,同时,所述的轨道限位块3.5的块体侧面各设有一呈上下分布的两个贯穿型通孔:位于上部的轨道限位块过孔3.51和下部的方孔3.52;所
述的移动气缸3.6的活塞杆伸出端固定在轨道限位块过孔3.51中,所述的分料滑槽3.4的左端槽体穿置在轨道限位块3.5的方孔3.52中,其右端槽体的上表面上设有一用于和活塞杆衔接的活塞杆固定孔3.41,分料滑槽3.4的上部设有配有压紧销3.3和弹簧3.8的压块3.7;所述的滑槽轨道3.2上部滑槽的内侧设有一用于与螺丝机1中螺丝输送槽1.1贯通的侧向开口3.9,并在同侧的螺丝输送槽1.1上另设有一可调节的侧挡板3.1。
9.进一步地,所述的二次搬运组件5由下模滑槽5.1、下模定位块5.2、薄型气缸5.3侧限位板5.4组成,所述的下模滑槽5.1经螺钉固定在转接板4上,所述的侧限位板5.4经螺钉固定在下模滑槽5.1上部对应的螺孔内,所述的下模滑槽5.1为两层台阶型块体,在其下部设有一向下开口的槽位5.11,所述的下模定位块5.2的滑动部分5.21穿过下模滑槽5.1下部的槽位5.11。
10.根据以上技术方案提出的这种自动送钉系统,避免人工放螺钉,消除错放螺钉导致的不良现象的产生。实现了在压铆机上自动送钉,并可推广至相似产品装配螺钉工艺,进一步提高工厂自动化水平。具有以下特点:
11.1、自动送螺钉,降低人工作业强度,无需再仔细核对铆钉正反面,无需精确的将螺柱定位孔放置定位销上;
12.2、人工送钉时间3s,自动送钉时间1.5s,送钉时间为人工送钉时间的一半,提高了产能。
附图说明
13.图1为本实用新型的结构示意图;
14.图2为图1的爆炸图;
15.图3为传送轨道组件的结构示意图;
16.图4为分料组件的整体装配结构示意图;
17.图5为分料组件的爆炸分解示意图;
18.图6为分料组件的局部结构剖视图;
19.图7为二次搬运组件的整体结构示意图;
20.图8为二次搬运组件的爆炸图。
21.图中:
22.1-螺丝机;1.1-螺丝机输送槽;2-传送轨道组件;2.1-盖板;
23.2.2-定位轨道;3-分料组件;3.1-侧挡板;3.2-滑槽轨道;3.3-压紧销;
24.3.4-分料滑槽;3.41-活塞杆固定孔;3.5-轨道限位块;
25.3.51-轨道限位块过孔;3.52-方孔;3.6-移动气缸;3.7-压块;
26.3.8-弹簧;3.9-侧向开口;4-转运板;5-二次搬运组件;5.1-下模滑槽;
27.5.11-槽位;5.2-下模定位块5.21-下模定位块滑动部分;5.22-定位孔;
28.5.3-薄型气缸;5.4-侧限位板;6-底座;7-产品定位架;8-螺钉;
29.9-销钉;10-压铆螺钉。
具体实施方式
30.以下结合说明书附图进一步描述本实用新型,并给出本实用新型的实施例。本实
用新型提出的这种螺丝机的自动送钉系统,它是在螺丝机自动送料基础上配合铆钉机工作平台做的开发设计。其通用性强,可以根据螺钉的形状不同选用或定制不同螺丝机。
31.图1、图2给出了本实用新型的整体结构图和组成构件的解析爆炸图。
32.从图1、图2中可以看到:
33.这种螺丝机的自动送钉系统,包括螺丝机1、传送轨道组件2、分料组件3、转接板4、二次搬运组件5、底座6和搁置加工件的产品定位架7,所述的螺丝机1、传送轨道组件2、分料组件3和二次搬运组件5分别经设置在底部的螺钉和销钉固定在转接板4上,其中:所述的传送轨道组件2紧挨着螺丝机1外侧设置,所述的传送轨道组件2外侧设置着分料组件3,所述的螺丝机1和轨道组件2的上表面上各设有一道螺丝输送槽1.1和定位轨道2.2,由互为衔接连通的螺丝输送槽1.1、定位轨道2.2组成螺丝机1的铆接螺钉10的外送通道;同时又通过设置在该外送通道尽头、与该外送通道相垂直设置的组成分料组件3中的滑槽轨道3.2构成相互贯通的t字形螺钉输送通道;所述的二次搬运组件5位于分料组件3左侧的转运板4的上表面并与架设在转运板4下底面上的底座固定连接;所述的产品定位架7为一矩形框架机构,其上部边框的右边伸出端通过连接螺钉与转运板4固定连接,使整块转运板4及其上部构件与产品定位架7形成悬臂状连接结构。
34.图3给出的是本实用新型如图3所示的传送轨道组件2的具体结构示意图。这种传送轨道组件2为一矩形块体,其上表面上设有一道与螺丝机1上设置的螺丝输送槽1.1连通的同规格定位轨道2.2,并在定位轨道面上设有一块经螺栓固定的有孔盖板2.1。
35.这种传送轨道组件2紧挨着螺丝机1安置,其表面设置的定位轨道2.2实际上是螺丝机1上设置的一道螺丝输送槽1.1的延伸,用于输送铆接螺钉10。
36.图4、图5和图6给出的是本实用新型中二次搬运组件5的整体结构装配图和组成构件的爆炸分解图。
37.这种分料组件3由滑槽轨道3.2、压紧销3.3、分料滑槽3.4、轨道限位块3.5、压块3.7和移动气缸3.6组成,所述轨道限位块3.5设置在滑槽轨道3.2的左侧边、并通过下部的螺钉与滑槽轨道3.2固定连接,同时,所述的轨道限位块3.5的块体侧面各设有一呈上下分布的两个贯穿型通孔:位于上部的轨道限位块过孔3.51和下部的方孔3.52;所述的移动气缸3.6的活塞杆伸出端固定在轨道限位块过孔3.51中,所述的分料滑槽3.4的左端槽体穿置在轨道限位块3.5的方孔3.52中,其右端槽体的上表面上设有一用于和活塞杆衔接的固定孔3.41,分料滑槽3.4的上部设有配有压紧销3.3和弹簧3.8的压块3.7;所述的滑槽轨道3.2上部滑槽的内侧设有一用于与螺丝机1中螺丝输送槽1.1贯通的侧向开口3.9,并在同侧的螺丝输送槽1.1上另设有一可调节的侧挡板3.1,用于弥补长行程导致的误差。
38.在这种分料组件3中,利用设置的侧挡板3.1用螺丝从后方固定在滑槽轨道3.2上;压紧销3.3固定在分料滑槽3.4的销孔中,松配,其下方为在定位孔中的压铆螺钉,上方由弹簧3.8压紧,弹簧3.8固定在压块3.7的盲孔中;气缸3.6穿过轨道限位块过孔3.51及分料滑槽的上设置的活塞杆固定孔3.41与分料滑槽3.4连接,分料滑槽3.4主体穿过方孔3.52,能在3.52内来回滑动。
39.图7为二次搬运组件的整体结构示意图;图8为二次搬运组件的爆炸图。
40.这种二次搬运组件由下模滑槽5.1、下模定位块5.2、薄型气缸5.3侧限位板5.4组成,所述的下模滑槽5.1经螺钉固定在转接板4上,所述的侧限位板5.4经螺钉固定在下模滑
槽5.1上部对应的螺孔内,所述的下模滑槽5.1为两层台阶型块体,在其下部设有一向下开口的槽位5.11,所述的下模定位块5.2的滑动部分5.21穿过下模滑槽5.1下部的槽位5.11。
41.侧限位板5.4用螺钉固定在下模滑槽5.1上,下模滑槽5.1由螺钉固定在转接板4上;下模定位块5.2与薄型气缸5.3螺纹连接,下模定位块5.2的滑动部分5.21穿过下模滑槽5.1的槽位5.11。
42.二次搬运组件细节如图8所示,压铆螺钉到达下模定位块上方,在压紧销3.3和弹簧3.8的压力下落入下模定位块的定位孔5.22。薄型气缸5.3通气,下模定位块5.2在下模滑槽的约束下移动到压铆位。即完成送钉动作。此处设计采用与前段送钉类似结构,自制加工件替代传统的直线滑轨,整体空间布局更紧凑合理。
43.根据以上技术方案提出的这种螺丝机的自动送钉系统,其工作原理如下:压铆螺钉有螺丝机不断输送,随着挤压前方的螺钉,使前方的槽体内的螺钉不断地向前移动、穿过传送轨道2至滑槽轨道3.2;而后该压铆螺钉在分料组件3中的移动气缸3.6的推动及滑槽轨道的约束下移动到下模定位块5.2处。随后在压紧销3.3和弹簧3.8的作用下压铆螺丝10快速下落到下模定位孔5.22中;与此同时,随着薄型气缸5.3,下模定位块5.2在下模滑槽的约束下移动到压铆位,即完成整个送钉动作。
44.以上仅仅是本技术人依据本实用新型技术方案给出的基本实施例,任何本行业的普通技术人员参照本技术方案作出的不具备实质性创意的改进,均属于本实用新型保护的范畴。