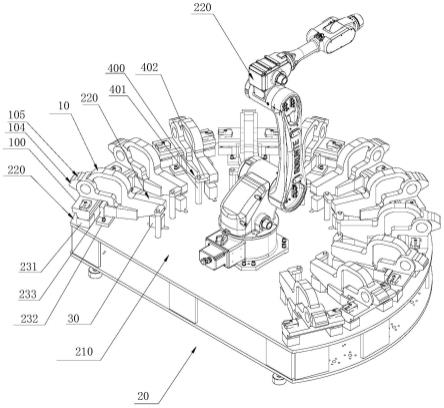
1.本发明属于机加工技术领域,尤其涉及一种车辆减速器制动钳加工方法。
背景技术:2.制动钳应用于铁路驼峰货运编组站场,是铁路驼峰车辆减速器的一个重要部件,两个制动钳由主轴与底座连接成制动钳组,用螺栓固定安装在制动轨上,常用的安装状态是,一根制动轨上均匀分布安装有七个制动钳组,制动钳支撑着制动轨完成车辆减速器制动,当货运车辆被制动时,动力组件通过制动钳组带动制动轨对货运车辆车轮两侧面进行钳夹式制动减速,达到预期速度后解除制动状态,车轮两侧的制动轨脱离车轮;整体制动过程,制动钳承受到较大的交变冲击力。
3.当前,我国铁路货运向重载化、快速化方向发展,货运车辆载重由原来的25吨轴重提高到27吨轴重,车辆编组密度,相比之前也有不同程度的提高。
4.目前,国内大型铁路驼峰编组场每天编组量接近2万辆,每辆被编组的车辆由25千米/小时的速度减速到5千米/小时的安全连挂速度,能量转变主要依靠制动钳传递,因此,对驼峰车辆减速器中制动钳产品的安全性和可靠性提出更高的要求。
5.我国现有铁路驼峰车辆减速器上使用的制动钳产品一般是zg270-500型铸钢件,随着铁路编组站场重载、编组量的增大,车辆减速器中的制动钳逐渐暴露出以下缺点:采用铸造工艺制成的制动钳产品存在夹渣、气孔等内部铸造缺陷,造成材质不均匀,抗拉强度低、延展性能差、材料性能偏脆、遇到较大外力时易断裂,直接影响制动钳的可靠性。实际货运车辆制动过程中,制动轨受到车轮0-280kn的交变外力,由于铸钢制动钳产品延展性较差,无法在短时间内把该作用力传导给其他的制动钳,致使受力较大的制动钳的钳臂断裂,给铁路编组工作带来安全隐患,严重时会导致货车脱线,造成安全事故。
6.根据调查,铁路配套企业,通过优化设计,消除锻造制动钳现存的质量缺陷,提高锻造制动钳产品使用的安全性和可靠性,设计一种通过堆焊耐磨合金来提高耐磨强度,例如现有技术“公开号为cn204775282u、发明名称为一种车辆减速器制动钳”,“公开号为cn213831699u,发明名称为一种高性能制动钳”,但是上述在实际生产时一般采用普通交直流电焊机人工进行堆焊,堆焊质量不稳定,易产生堆焊夹层,对操作人员技术水平要求高。焊材为d212焊条,焊材容易受潮,焊前必须进行烘干处理,造成制动钳焊接工序时间长、返工次数多,不利于大批量集中生产任务的按时、保质完成。现有焊条堆焊过程中会产生极大的有害气体,不但对大气环境有影响,而且对操作者的身体有更大的直接伤害。
7.人工普通交直流电焊机进行堆焊存在工作环境恶略、劳动强度高、工作效率低,而且合格率低的缺陷;为此,本发明涉及一种车辆减速器制动钳补强焊接方法。
技术实现要素:8.针对现有技术存在的问题,本发明提供了一种车辆减速器制动钳加工方法。本发明是这样实现的,一种车辆减速器制动钳加工方法,包括如下步骤:
9.s1、利用加工设备加工水平基准面和竖直基准面以及制动钳支撑面:所述制动钳为铸件本体,首先选择制动钳安装翼板的下表面作为水平基准面;选择靠近水平基准面侧所述制动轨安装槽的竖直面作为竖直基准面;制动钳支撑面为补强焊接面,将制动钳支撑面铣削加工有小于与成品尺寸3mm的堆焊深度;
10.s2、装夹制动钳:在焊接工装上依水平基准面和竖直基准面为安装基准固定装夹制动钳,使制动钳支撑面水平朝上;
11.s3、增加辅助支撑:在制动钳支撑面相对侧焊接工装上安装有辅助支撑组件,用于支撑制动钳防止制动钳发生倾斜;
12.s4、在制动钳支撑面上堆焊硬度为hrc35-50的硬质合金:
13.s4.1、采用焊接机器人进行二氧化碳气体保护焊焊接,焊丝选用铬钼合金钢气体保护药芯焊丝;焊接电流为180-260a;
14.s4.2、焊接起始点的确定,依制动钳支撑面的一端为焊接起点,制动钳支撑面的另一端部为焊接终点;
15.s4.3、启动焊接机器人由焊接起点向焊接终点进行堆焊,堆焊采用分层堆焊,在堆焊第一层后去渣堆焊第n层,n≥2,堆焊完成后保证堆焊层的厚度为4-5mm;所述堆焊层与制动钳支撑面基体内侧制动钳上的圆弧倾斜过度25-35
°
;
16.s5、精加工制动钳支持面:焊接完成后将制动钳固定在铣床上对制动钳支撑面按照图纸加工要求进行精加工,保证加工面的光洁度不大于25;堆焊层的厚度为2.5-3.5mm;
17.s6、检验:
18.s6.1、焊接黑皮检测:采用目测的方法进行观察堆焊层加工后表面是否存在焊接黑皮:根据技术要求堆焊层加工后表面允许带单个直径不大于3mm、相邻间距不小于30mm的黑皮不超6块,若超出,需全部去除堆焊层,重新进行堆焊;
19.s6.2、表面光洁度检测:采用表面光洁度对精加工制动钳支持面进行检测,要求表面光洁度高于25;
20.s6.3、硬度检测:在硬度检测时采用多点均布求平均值的方法进行检测;确定制动钳支撑面的检测区域;沿制动钳支撑面的长度方向检测区域距离制动钳支撑面两端20mm;沿制动钳支撑面的宽度方向检测区域距离制动钳两侧面5mm;在上述检测区域布置不少于8个测量点,所述测量点分为两列,两列的测量点成交错设置;对上述测量点逐一进行硬度检测,然后求出平均值得出堆焊层的硬度,该硬度应当大于hrc35-50,否侧视为不合格,需要全部去除堆焊层,重新进行堆焊。
21.在制动钳支撑面上堆焊硬度为hrc35-50的硬质合金后采用与s4同样的焊接参数在事先加工好的制动钳钳鼻的斜面上进行堆焊;堆焊后与制动钳支持面同时精加工和检验。
22.优选的,所述焊接工装,包括工作台和焊接机器人;所述工作台的上等间距安装有制动钳定位工装;所述制动钳定位工装包括水平定位块和竖直定位构件;所述水平定位块的上表面与制动钳安装翼板水平基准面贴合,制动钳安装翼板的两端通过紧固螺栓与水平定位块固定连接;竖直定位构件包括水平基座,所述水平基座上设有竖直定位块,所述竖直定位块的右侧面与制动钳的竖直基准面贴合。
23.还包括定位基准尺,所述定位基准尺包括定位杆,所述定位杆的上部安装有旋转
定位尺。
24.本发明的优点:采用上述技术方案,提高产品的合格率、改善工作环境,提高生产效率等优点。
附图说明
25.图1是本发明不带钳鼻的制动钳结构示意图;
26.图2是本发明带有钳鼻的制动钳结构示意图;
27.图3是本发明焊接工装结构示意图。
28.图中、10、制动钳;100、制动钳安装翼板;101、水平基准面;102、竖直基准面;103、制动钳支撑面;104、钳鼻;105、钳鼻斜面;20、焊接工装;210、圆形工作台;220、焊接机器人;230、制动钳定位工装;231、水平定位块;232、水平基座;233、竖直定位块;30、辅助支撑;40、定位基准尺;401、定位杆;402、旋转定位尺。
具体实施方式
29.为了使本发明的目的、技术方案及优点更加清楚明白,以下结合实施例,对本发明进行进一步详细说明。应当理解,此处所描述的具体实施例仅仅用以解释本发明,并不用于限定本发明。
30.实施例1,一种车辆减速器制动钳加工方法,包括如下步骤
31.s1、利用加工设备加工水平基准面101和竖直基准面102以及制动钳支撑面103:所述制动钳10为铸件本体,首先选择制动钳安装翼板100的下表面作为水平基准面101;选择靠近水平基准面侧所述制动轨安装槽的竖直面作为竖直基准面102;制动钳支撑面为补强焊接面,将制动钳支撑面铣削加工有小于与成品尺寸3mm的堆焊深度;采用上述水平基准面和竖直基准面保证制动钳支撑面的加工精度,同时利于装夹,可以实现一次装夹完成堆焊;
32.s2、装夹制动钳:在焊接工装20上依水平基准面和竖直基准面为安装基准固定装夹制动钳,使制动钳支撑面水平朝上;采用专用的焊接工作,大大提高工作效率,同时保证焊接精度,在实际使用时,焊接工作台上布置多个焊接工装,这样可以保证焊接机器人连续不间断的工作,提高生产效率;
33.s3、增加辅助支撑30:在制动钳支撑面相对侧焊接工装上安装有辅助支撑组件,用于支撑制动钳防止制动钳发生倾斜,保证焊接精度;
34.s4、在制动钳支撑面上堆焊硬度为hrc35-50的硬质合金:
35.s4.1、采用焊接机器人进行二氧化碳气体保护焊焊接,焊丝选用规格为yd172或yd212铬钼合金钢气体保护药芯焊丝,直径为1.2mm、1.6mm和2.0mm三种;对应堆焊电流为1.2mm焊丝采用180-220a,1.6mm焊丝采用200-240a;2.0mm焊丝采用220-260a;
36.s4.2、焊接起始点的确定,制动钳支撑面的一端为焊接起点,制动钳支撑面的另一端部为焊接终点,本实施例中依制动钳支撑面的内端为焊接起点a,制动钳支撑面的外端部为焊接终点b;
37.s4.3、启动焊接机器人由焊接起点向焊接终点进行堆焊,堆焊采用分层堆焊,在堆焊第一层后去渣堆焊第n层,n≥2,堆焊完成后保证堆焊层的厚度为4-5mm;所述堆焊层与制动钳支撑面基体内侧制动钳上的圆弧倾斜过度25-35
°
;保证堆焊耐磨硬质合金层的焊接强
度,同时防止与制动轨安装时发生干涉;
38.s5、精加工制动钳支持面:焊接完成后将制动钳固定在铣床上对制动钳支撑面按照图纸加工要求进行精加工,保证加工面的光洁度不大于25;堆焊层的厚度为2.5-3.5mm;
39.s6、检验:
40.s6.1、焊接黑皮检测:采用目测的方法进行观察堆焊层加工后表面是否存在焊接黑皮:根据技术要求堆焊层加工后表面允许带单个直径不大于3mm、相邻间距不小于30mm的黑皮不超6块,若超出,需全部去除堆焊层,重新进行堆焊;
41.s6.2、表面光洁度检测:采用表面光洁度对精加工制动钳支持面进行检测,要求表面光洁度高于25;
42.s6.3、硬度检测:在硬度检测时采用多点均布求平均值的方法进行检测;确定制动钳支撑面的检测区域;沿制动钳支撑面的长度方向检测区域距离制动钳支撑面两端20mm;沿制动钳支撑面的宽度方向检测区域距离制动钳两侧面5mm;在上述检测区域布置不少于8个测量点,所述测量点分为两列,两列的测量点成交错设置;对上述测量点逐一进行硬度检测,然后求出平均值得出堆焊层的硬度,该硬度应当大于hrc35-50,否侧视为不合格,需要全部去除堆焊层,重新进行堆焊。
43.实施例2,根据实际制动钳的种类,一种不带钳鼻(请参阅图1),一种带有钳鼻(请参阅图2),当加工带有钳鼻的制动钳时,在钳鼻斜面上堆焊硬质合金,在上述实施例1的基础上,在制动钳支撑面上堆焊硬度为hrc35-50的硬质合金后采用与s4同样的焊接参数在事先加工好的制动钳钳鼻的斜面上进行堆焊;堆焊后与制动钳支持面同时精加工和检验。
44.优选的,请参阅图3,所述焊接工装20,包括圆形工作台210,所述圆形工作台的中心位置安装有焊接机器人220,焊接机器人属于现有技术,其控制方式和工作原理在此不进行赘述;所述圆形工作台的外边缘沿圆周方向等间距安装有制动钳定位工装230;所述制动钳定位工装包括水平定位块231和竖直定位构件;所述水平定位块的上表面与制动钳安装翼板水平基准面贴合,制动钳安装翼板的两端通过紧固螺栓与水平定位块固定连接;竖直定位构件包括水平基座232,用于安装,所述水平基座上设有竖直定位块233,所述竖直定位块的右侧面与制动钳的竖直基准面贴合。工作台既可以采用圆形工作台也可以采用方形工作台,采用圆形工作台焊接机器人在多产品焊接时,焊接机器人做旋转运动,逐一进行焊接作业;采用方形工作台焊接机器人和被焊接工件相对直线运动,基于设备空间利用率,本实施例优选圆形工作台。
45.还包括定位基准尺40,所述定位基准尺包括定位杆401,所述定位杆的上部安装有旋转定位尺402。进一步保证制动钳的定位基准,利于焊接机器人坐标定位,定位找正后将选择定位尺移开,防止与制动钳焊接在一起。
46.本发明的优点:采用上述技术方案,提高产品的合格率、改善工作环境,提高生产效率等优点。
47.以上所述仅为本发明的较佳实施例而已,并不用以限制本发明,凡在本发明的精神和原则之内所作的任何修改、等同替换和改进等,均应包含在本发明的保护范围之内。