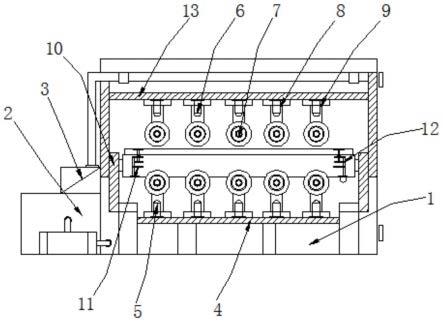
1.本发明涉及拉伸工艺技术领域,具体为一种复合铝板预拉伸工艺。
背景技术:2.复合铝板解决了由于闪光焊工艺复杂,需要大型设备,因而造成产品成本高,使用范围窄的问题,针对复合铝板的加工现有技术存在诸多问题。
3.比如申请号为:202010176861.0的发明记载了,本发明公开了一种提高超细晶铝板拉伸塑性的方法,其包括如下步骤:s1,退火处理,对轧制态铝板进行退火处理,得到退火态铝板;s2,挤压,对退火态铝板进行单道次挤压,压下量为80~90%,得到挤压态铝板;s3,堆叠,将退火态铝板和挤压态铝板堆叠为三明治结构的叠合板,中间层为退火态铝板,上、下面层为挤压态铝板;s4,冷轧,对叠合板进行轧制,轧制压下量为50~77%。通过该工艺制备的铝板具有高的强度同时保持合理的拉伸塑性。
4.类似于上述申请的铝板生产工艺目前还存在以下不足:
5.生产过程中会产生大量的废料,工艺步骤过于复杂,在实际拉伸的过程中铝板产生的应力不能及时去除,导致铝板的性能下降。
6.于是,有鉴于此,针对现有的结构及缺失予以研究改良,提出一种复合铝板预拉伸工艺,以期达到更具有更加实用价值性的目的。
技术实现要素:7.本发明的目的在于提供一种复合铝板预拉伸工艺,以解决上述背景技术中提出的现有的山地运输机在使用过程中不便根据环境所需配合山地轨道或者山地索道进行移动,使用不够灵活,存在使用局限性,且在较为平坦的位置不便使用者把运输机与其他动力组件分离进行独立手动推进,以及不便对运输机内部放置的物品进行下料处理的问题。
8.为实现上述目的,本发明提供如下技术方案:一种复合铝板预拉伸工艺,包括以下步骤,
9.步骤一:材料准备,选用10-12cm厚的复合铝板,将复合铝板送入到自动滚刷式的清洗机中对其表面进行清洗,然后使用烘干机对复合铝板的表面进行烘干,烘干后对复合铝板的表面均匀的涂抹一层润滑剂后备用;
10.步骤二:第一道拉伸,将经过步骤一中处理后的复合铝板移动到拉伸机的模具工位处进行第一道拉伸,第一道拉伸模具的厚度为8-10cm,复合铝板经过第一道拉伸后的形成厚度为8-10cm的半成品a;
11.步骤三:第二道拉伸,将步骤二中半成品a在拉伸机的进行第二道拉伸,第二道拉伸模具的厚度为6-8cm,半成品a经过第二道拉伸后的形成厚度为6-8cm的半成品b;
12.步骤四:第一次退火处理,将步骤三中得到的半成品b在真空退火炉中进行退火处理,去除半成品b表面的氧化膜,降低材料的应力,均匀材料成分,为后续加工做准备,半成品b退火完成后在其表面均匀的涂抹一层润滑剂后得到半成品c;
13.步骤五:第三道拉伸,将步骤四中半成品c移动到拉伸机的模具工位处进行第三道拉伸,第三道拉伸模具的厚度为4-6cm,半成品c经过第三道拉伸后形成厚度为4-6cm的半成品d;
14.步骤六:第二次退火处理,将步骤五中得到的半成品d在真空退火炉中进行退火处理,去除半成品d表面的氧化膜,半成品d退火完成后在其表面均匀的涂抹一层润滑剂后得到半成品e;
15.步骤七:第四道拉伸,将步骤六中得到的半成品e移动到拉伸机的模具工位处进行第四道拉伸,第四道拉伸模具的厚度为1-2cm,半成品e经过第四道拉伸后形成厚度为1-2cm的半成品f;
16.步骤八:打磨以及清洗处理,利用移动式的打磨机对半成品f的边缘部分进行打磨,然后将半成品f通过超声波清洗机中进行清洗,随后经过风干机进行风干得到成品。
17.进一步的,所述步骤二中第一道拉伸时间为7-10秒,拉伸机的拉伸压力为0.4-0.6mpa。
18.进一步的,所述步骤三中第二道拉伸时间为10-14秒,拉伸机的拉伸压力为0.3-0.5mpa。
19.进一步的,所述步骤四中退火的温度为400-450摄氏度,退火时间为15-25min。
20.进一步的,所述步骤五中第三道拉伸时间为5-7秒,拉伸机的拉伸压力为0.6-0.8mpa。
21.进一步的,所述步骤六中退火的温度为350-380摄氏度,退火时间为10-15min。
22.进一步的,所述步骤七中第四道拉伸时间为7-12秒,拉伸机的拉伸压力为0.5-0.8mpa。
23.进一步的,用于复合铝板预拉伸工艺的拉伸机包括机架,所述机架的一侧安装有电气箱,且电气箱的上方安装有控制箱,所述机架的内部下方安装有下支撑板,所述机架的内部一侧安装有第一拉伸机构,且第一拉伸机构的一侧安装有第二拉伸机构,所述第二拉伸机构远离第一拉伸机构的一侧安装有第三拉伸机构,且第三拉伸机构远离第二拉伸机构的一侧安装有第四拉伸机构,所述第四拉伸机构远离第三拉伸机构的一侧安装有第五拉伸机构,所述第一拉伸机构远离第二拉伸机构的一侧安装有第一夹持机构,所述第五拉伸机构远离第四拉伸机构的一侧安装有第二夹持机构,所述第二夹持机构远离第五拉伸机构的一侧和第一夹持机构远离第一拉伸机构的一侧均安装有支撑柱,所述机架的内部上方安装有上支撑板。
24.进一步的,所述第一拉伸机构、第二拉伸机构、第三拉伸机构、第四拉伸机构和第五拉伸机构结构相同,且第一拉伸机构包括:第一液压柱、第二液压柱、上拉伸辊、上转轴、第一电动机、第三液压柱、第四液压柱、下拉伸辊、下转轴和第二电动机,所述上支撑板的下方一侧安装有第一液压柱,且上支撑板的下方另一侧安装有第二液压柱,所述第二液压柱的下方安装有上拉伸辊,且上拉伸辊的两侧均安装有上转轴,所述上转轴的一侧安装有第一电动机,所述下支撑板的上方一侧安装有第三液压柱,且下支撑板的上方另一侧安装有第四液压柱,所述第四液压柱的上方安装有下拉伸辊,且下拉伸辊的两侧均安装有下转轴,所述下转轴的一侧安装有第二电动机。
25.进一步的,所述第一夹持机构和第二夹持机构结构相同,且第一夹持机构包括横
梁臂、上液压杆、下液压杆、铰链和夹板,所述横梁臂的上方安装有上液压杆,且横梁臂的下方安装有下液压杆,所述上液压杆和下液压杆的一端均安装有铰链,且上液压杆和下液压杆一侧均安装有夹板。
26.与现有技术相比,本发明的有益效果如下:
27.本发明通过两次退火以及多次拉伸的配合能够有效的去除铝板在实际拉伸过程中产生的应力,避免铝板性能的下降,在拉伸的过程中均匀材料的成分,方便后续的加工,而且此工艺加工过程简单,易于操作,方便流水化进行生产加工;
28.复合铝板放置在下拉伸辊和上拉伸辊之间,此时第一夹持机构和第二夹持机构对复合铝板进行夹持,具体为,上液压杆和下液压杆进行伸缩而夹板围绕铰链进行转动对复合铝板进行夹持,夹持固定好后,第一拉伸机构、第二拉伸机构、第三拉伸机构、第四拉伸机构和第五拉伸机构对复合铝板进行拉伸作业,首先第一电动机通过上转轴带动上拉伸辊进行转动,同时,第二电动机通过下转轴带动下拉伸辊进行转动使上拉伸辊和下拉伸辊相互配合对符合铝板进行拉伸作业。
附图说明
29.图1为本发明一种复合铝板预拉伸工艺的流程示意图;
30.图2为本发明一种复合铝板预拉伸工艺的拉伸机结构示意图;
31.图3为本发明拉伸机的第一拉伸机构侧视结构示意图;
32.图4为本发明拉伸机的第一拉伸机构正视结构示意图;
33.图5为本发明拉伸机的第一夹持机构的结构示意图;
34.图中:1、机架;2、电气箱;3、控制箱;4、下支撑板;5、第一拉伸机构;501、第一液压柱;502、第二液压柱;503、上拉伸辊;504、上转轴;505、第一电动机;506、第三液压柱;507、第四液压柱;508、下拉伸辊;509、下转轴;5010、第二电动机;6、第二拉伸机构;7、第三拉伸机构;8、第四拉伸机构;9、第五拉伸机构;10、支撑柱;11、第一夹持机构;1101、横梁臂;1102、上液压杆;1103、下液压杆;1104、铰链;1105、夹板;12、第二夹持机构;13、上支撑板。
具体实施方式
35.下面将结合本发明实施例中的附图,对本发明实施例中的技术方案进行清楚、完整地描述,显然,所描述的实施例仅仅是本发明一部分实施例,而不是全部的实施例。
36.实施例一:
37.请参阅图1、图2和图3,具体为,用于复合铝板预拉伸工艺的拉伸机包括机架1,所述机架1的一侧安装有电气箱2,且电气箱2的上方安装有控制箱3,所述机架1的内部下方安装有下支撑板4,所述机架1的内部一侧安装有第一拉伸机构5,且第一拉伸机构5的一侧安装有第二拉伸机构6,所述第二拉伸机构6远离第一拉伸机构5的一侧安装有第三拉伸机构7,且第三拉伸机构7远离第二拉伸机构6的一侧安装有第四拉伸机构8,所述第四拉伸机构8远离第三拉伸机构7的一侧安装有第五拉伸机构9,所述第一拉伸机构5远离第二拉伸机构6的一侧安装有第一夹持机构11,所述第五拉伸机构9远离第四拉伸机构8的一侧安装有第二夹持机构12,所述第二夹持机构12远离第五拉伸机构9的一侧和第一夹持机构11远离第一拉伸机构5的一侧均安装有支撑柱10,所述机架1的内部上方安装有上支撑板13。
38.第一拉伸机构5、第二拉伸机构6、第三拉伸机构7、第四拉伸机构8和第五拉伸机构9结构相同,且第一拉伸机构5包括:第一液压柱501、第二液压柱502、上拉伸辊503、上转轴504、第一电动机505、第三液压柱506、第四液压柱507、下拉伸辊508、下转轴509和第二电动机5010,所述上支撑板13的下方一侧安装有第一液压柱501,且上支撑板13的下方另一侧安装有第二液压柱502,所述第二液压柱502的下方安装有上拉伸辊503,且上拉伸辊503的两侧均安装有上转轴504,所述上转轴504的一侧安装有第一电动机505,所述下支撑板4的上方一侧安装有第三液压柱506,且下支撑板4的上方另一侧安装有第四液压柱507,所述第四液压柱507的上方安装有下拉伸辊508,且下拉伸辊508的两侧均安装有下转轴509,所述下转轴509的一侧安装有第二电动机5010。
39.第一夹持机构11和第二夹持机构12结构相同,且第一夹持机构11包括横梁臂1101、上液压杆1102、下液压杆1103、铰链1104和夹板1105,所述横梁臂1101的上方安装有上液压杆1102,且横梁臂1101的下方安装有下液压杆1103,所述上液压杆1102和下液压杆1103的一端均安装有铰链1104,且上液压杆1102和下液压杆1103一侧均安装有夹板1105。
40.实施例二:
41.请参阅图1,本发明提供一种技术方案:一种复合铝板预拉伸工艺,包括以下步骤,
42.步骤一:材料准备,选用10cm厚的复合铝板,将复合铝板送入到自动滚刷式的清洗机中对其表面进行清洗,然后使用烘干机对复合铝板的表面进行烘干,烘干后对复合铝板的表面均匀的涂抹一层润滑剂后备用;
43.步骤二:第一道拉伸,将经过步骤一中处理后的复合铝板移动到拉伸机的模具工位处进行第一道拉伸,第一道拉伸模具的厚度为8cm,复合铝板经过第一道拉伸后的形成厚度为8cm的半成品a;
44.步骤三:第二道拉伸,将步骤二中半成品a在拉伸机的进行第二道拉伸,第二道拉伸模具的厚度为6cm,半成品a经过第二道拉伸后的形成厚度为6cm的半成品b;
45.步骤四:第一次退火处理,将步骤三中得到的半成品b在真空退火炉中进行退火处理,去除半成品b表面的氧化膜,降低材料的应力,均匀材料成分,为后续加工做准备,半成品b退火完成后在其表面均匀的涂抹一层润滑剂后得到半成品c;
46.步骤五:第三道拉伸,将步骤四中半成品c移动到拉伸机的模具工位处进行第三道拉伸,第三道拉伸模具的厚度为4cm,半成品c经过第三道拉伸后形成厚度为4cm的半成品d;
47.步骤六:第二次退火处理,将步骤五中得到的半成品d在真空退火炉中进行退火处理,去除半成品d表面的氧化膜,半成品d退火完成后在其表面均匀的涂抹一层润滑剂后得到半成品e;
48.步骤七:第四道拉伸,将步骤六中得到的半成品e移动到拉伸机的模具工位处进行第四道拉伸,第四道拉伸模具的厚度为1cm,半成品e经过第四道拉伸后形成厚度为1cm的半成品f;
49.步骤八:打磨以及清洗处理,利用移动式的打磨机对半成品f的边缘部分进行打磨,然后将半成品f通过超声波清洗机中进行清洗,随后经过风干机进行风干得到成品。
50.步骤二中第一道拉伸时间为7秒,拉伸机的拉伸压力为0.4mpa。
51.步骤三中第二道拉伸时间为10秒,拉伸机的拉伸压力为0.3mpa。
52.步骤四中退火的温度为400摄氏度,退火时间为15min。
53.步骤五中第三道拉伸时间为5秒,拉伸机的拉伸压力为0.6mpa。
54.步骤六中退火的温度为350摄氏度,退火时间为10min。
55.步骤七中第四道拉伸时间为7秒,拉伸机的拉伸压力为0.5mpa。
56.实施例三:
57.请参阅图1,本发明提供一种技术方案:一种复合铝板预拉伸工艺,包括以下步骤,
58.步骤一:材料准备,选用11cm厚的复合铝板,将复合铝板送入到自动滚刷式的清洗机中对其表面进行清洗,然后使用烘干机对复合铝板的表面进行烘干,烘干后对复合铝板的表面均匀的涂抹一层润滑剂后备用;
59.步骤二:第一道拉伸,将经过步骤一中处理后的复合铝板移动到拉伸机的模具工位处进行第一道拉伸,第一道拉伸模具的厚度为9cm,复合铝板经过第一道拉伸后的形成厚度为9cm的半成品a;
60.步骤三:第二道拉伸,将步骤二中半成品a在拉伸机的进行第二道拉伸,第二道拉伸模具的厚度为7cm,半成品a经过第二道拉伸后的形成厚度为7cm的半成品b;
61.步骤四:第一次退火处理,将步骤三中得到的半成品b在真空退火炉中进行退火处理,去除半成品b表面的氧化膜,降低材料的应力,均匀材料成分,为后续加工做准备,半成品b退火完成后在其表面均匀的涂抹一层润滑剂后得到半成品c;
62.步骤五:第三道拉伸,将步骤四中半成品c移动到拉伸机的模具工位处进行第三道拉伸,第三道拉伸模具的厚度为5cm,半成品c经过第三道拉伸后形成厚度为5cm的半成品d;
63.步骤六:第二次退火处理,将步骤五中得到的半成品d在真空退火炉中进行退火处理,去除半成品d表面的氧化膜,半成品d退火完成后在其表面均匀的涂抹一层润滑剂后得到半成品e;
64.步骤七:第四道拉伸,将步骤六中得到的半成品e移动到拉伸机的模具工位处进行第四道拉伸,第四道拉伸模具的厚度为1.5cm,半成品e经过第四道拉伸后形成厚度为1.5cm的半成品f;
65.步骤八:打磨以及清洗处理,利用移动式的打磨机对半成品f的边缘部分进行打磨,然后将半成品f通过超声波清洗机中进行清洗,随后经过风干机进行风干得到成品。
66.步骤二中第一道拉伸时间为8秒,拉伸机的拉伸压力为0.5mpa。
67.步骤三中第二道拉伸时间为12秒,拉伸机的拉伸压力为0.4mpa。
68.步骤四中退火的温度为420摄氏度,退火时间为20min。
69.步骤五中第三道拉伸时间为6秒,拉伸机的拉伸压力为0.7mpa。
70.步骤六中退火的温度为36摄氏度,退火时间为12min。
71.步骤七中第四道拉伸时间为9秒,拉伸机的拉伸压力为0.6mpa。
72.综上,请参阅图1、图2、图3、图4和图5,该复合铝板预拉伸工艺,具体为,步骤一:材料准备,选用10-12cm厚的复合铝板,将复合铝板送入到自动滚刷式的清洗机中对其表面进行清洗,然后使用烘干机对复合铝板的表面进行烘干,烘干后对复合铝板的表面均匀的涂抹一层润滑剂后备用;
73.步骤二:第一道拉伸,将经过步骤一中处理后的复合铝板移动到拉伸机的模具工位处进行第一道拉伸,第一道拉伸模具的厚度为8-10cm,复合铝板经过第一道拉伸后的形成厚度为8-10cm的半成品a,第一道拉伸时间为7-10秒,拉伸机的拉伸压力为0.4-0.6mpa;
74.步骤三:第二道拉伸,将步骤二中半成品a在拉伸机的进行第二道拉伸,第二道拉伸模具的厚度为6-8cm,半成品a经过第二道拉伸后的形成厚度为6-8cm的半成品b,第二道拉伸时间为10-14秒,拉伸机的拉伸压力为0.3-0.5mpa;
75.步骤四:第一次退火处理,将步骤三中得到的半成品b在真空退火炉中进行退火处理,去除半成品b表面的氧化膜,降低材料的应力,均匀材料成分,为后续加工做准备,半成品b退火完成后在其表面均匀的涂抹一层润滑剂后得到半成品c,退火的温度为400-450摄氏度,退火时间为15-25min;
76.步骤五:第三道拉伸,将步骤四中半成品c移动到拉伸机的模具工位处进行第三道拉伸,第三道拉伸模具的厚度为4-6cm,半成品c经过第三道拉伸后形成厚度为4-6cm的半成品d,第三道拉伸时间为5-7秒,拉伸机的拉伸压力为0.6-0.8mpa;
77.步骤六:第二次退火处理,将步骤五中得到的半成品d在真空退火炉中进行退火处理,去除半成品d表面的氧化膜,半成品d退火完成后在其表面均匀的涂抹一层润滑剂后得到半成品e,退火的温度为350-380摄氏度,退火时间为10-15min;
78.步骤七:第四道拉伸,将步骤六中得到的半成品e移动到拉伸机的模具工位处进行第四道拉伸,第四道拉伸模具的厚度为1-2cm,半成品e经过第四道拉伸后形成厚度为1-2cm的半成品f,第四道拉伸时间为7-12秒,拉伸机的拉伸压力为0.5-0.8mpa;
79.步骤八:打磨以及清洗处理,利用移动式的打磨机对半成品f的边缘部分进行打磨,然后将半成品f通过超声波清洗机中进行清洗,随后经过风干机进行风干得到成品。
80.本发明的拉伸机的使用原理如下:将复合铝板放置在下拉伸辊508和上拉伸辊503之间,此时第一夹持机构11和第二夹持机构12对复合铝板进行夹持,具体为,上液压杆1102和下液压杆1103进行伸缩而夹板1105围绕铰链1104进行转动对复合铝板进行夹持,夹持固定好后,第一拉伸机构5、第二拉伸机构6、第三拉伸机构7、第四拉伸机构8和第五拉伸机构9对复合铝板进行拉伸作业,首先第一电动机505通过上转轴504带动上拉伸辊503进行转动,同时,第二电动机5010通过下转轴509带动下拉伸辊508进行转动使上拉伸辊503和下拉伸辊508相互配合对符合铝板进行拉伸作业。
81.以上所述,仅为本发明较佳的具体实施方式,但本发明的保护范围并不局限于此,任何熟悉本技术领域的技术人员在本发明揭露的技术范围内,根据本发明的技术方案及其发明构思加以等同替换或改变,都应涵盖在本发明的保护范围之内。