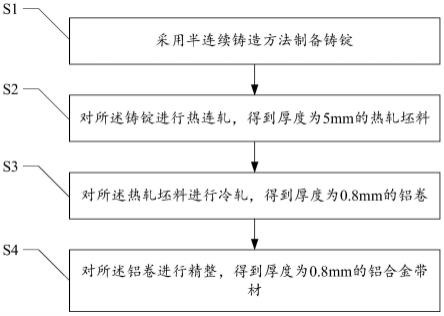
铝合金带材的制备方法及铝合金带材
【技术领域】
1.本发明涉及铝加工技术领域,尤其是涉及一种铝合金带材的制备方法及铝合金带材。
背景技术:2.在能源和环保的压力下,新能源汽车无疑将成为未来汽车的发展方向,新能源汽车的需求和发展,将带动新能源时代各类汽车电池、车身轻量化和汽车零部件产业的发展。
3.在汽车轻量化的材料中,铝合金材料的综合性价比高于钢、镁、塑料和复合材料,无论在应用技术、操作安全和回收利用方面都具有比较大优势。但部分汽车用料对于铝合金表面的光泽度具有一定的要求。
4.提升铝合金表面的光泽度的传统方法是通过机械抛光、化学抛光或电化学抛光等打磨工艺进行改善,采用这些方式改善铝合金表面的光泽度,不仅需要单独的设备,还需要人工辅助操作,导致了其生产成本高、效率低且工艺繁琐的问题。
技术实现要素:5.本发明的目的在于提供一种铝合金带材的制备方法,以解决现有铝合金改善表面光泽度的方法,导致其生产成本高、效率低且工艺繁琐的问题。
6.第一方面,本发明提供了一种铝合金带材的制备方法,其包括以下步骤:
7.步骤s1、采用半连续铸造方法制备铸锭;
8.步骤s2、对所述铸锭进行热连轧,得到厚度为5mm的热轧坯料;其中,所述热连轧的轧制过程中使轧辊的粘铝层厚度为11~15μm;
9.步骤s3、对所述热轧坯料进行冷轧,得到厚度为0.8mm的铝卷;其中,所述冷轧的轧制道次依次包括第一轧制道次、第二轧制道次、第三轧制道次、第四轧制道次以及第五轧制道次;
10.所述第一轧制道次:将厚度为5mm的所述热轧坯料轧制成厚度为3.2mm的铝卷一道热轧坯料,轧制速度为100~200m/min,轧辊的粗糙度为ra=0.4
±
0.02μm、rz=3.2
±
0.2μm、rpc=180~200,轧辊的轧制道次大于5道;
11.所述第二轧制道次:将厚度为3.2mm的所述一道热轧坯料轧制成厚度为2.1mm的二道热轧坯料,轧制速度为300~400m/min,轧辊的粗糙度为ra=0.32
±
0.02μm、rz=2.56
±
0.2μm、rpc=160~180,轧辊的轧制道次大于5道;
12.所述第三轧制道次:将厚度为2.1mm的所述二道热轧坯料轧制成厚度为1.42mm的三道热轧坯料,轧制速度为400~500m/min,轧辊的粗糙度为ra=0.28
±
0.01μm、rz=2.24
±
0.1μm、rpc=150~160,轧辊的轧制道次大于5道;
13.所述第四轧制道次:将厚度为1.42mm的所述三道热轧坯料轧制成厚度为0.95mm的四道热轧坯料,轧制速度为400~500m/min,轧辊的粗糙度为ra=0.28
±
0.01μm、rz=2.24
±
0.1μm、rpc=140~150,轧辊的轧制道次大于16道;
14.所述第五轧制道次:将厚度为0.95mm的所述四道热轧坯料轧制成厚度为0.8mm的所述铝卷,轧制速度为300~400m/min,轧辊的粗糙度为ra=0.28
±
0.01μm、rz=2.24
±
0.1μm、rpc=130~140,轧辊的轧制道次大于16道;
15.步骤s4,对所述铝卷进行精整,得到厚度为0.8mm的铝合金带材。
16.优选的,所述第一轧制道次、所述第二轧制道次、所述第三轧制道次、所述第四轧制道次以及所述第五轧制道次中,使用的轧辊分别经过3道或3道以上的轧制。
17.优选的,所述第一轧制道次、所述第二轧制道次以及所述第三轧制道次中,使用的轧辊分别经过5道以上的轧制。
18.优选的,所述第四轧制道次和所述第五轧制道次中,使用的轧辊分别经过16道以上的轧制。
19.优选的,所述步骤s2中,所述热连轧的轧制过程中使轧辊的粘铝层厚度为13μm。
20.优选的,所述步骤s2中,所述热连轧进行前先对轧辊进行刷痕测试,并保证尼龙刷的刷痕宽度为28~30mm;所述热连轧包括采用单机架进行的热粗轧和采用三机架依次进行的热精轧,进行热精轧时其第三个机架的轧辊的温度大于80℃;所述热连轧的终轧温度为330~350℃。
21.优选的,所述步骤s3中,所述第一轧制道次、所述第二轧制道次以及所述第三轧制道次中使用的轧制油的参数为:轧制油的运动粘度小于或等于2.8厘斯,轧制油的酸值小于或等于0.20mgkoh/g,轧制油中添加剂的质量百分比为6.0~10.0%,轧制油的透光率大于或等于85%,轧制油的油盒试验小于或等于2c,轧制油的胶质小于或等于1000mg/100ml。
22.优选的,所述步骤s3中,所述第四轧制道次以及所述第五轧制道次中使用的轧制油的参数为:轧制油的运动粘度小于或等于2厘斯,轧制油中添加月桂酸以将其酸值控制在小于或等于0.20mgkoh/g,轧制油中添加剂的质量百分比为6.0~7.0%,轧制油的透光率大于或等于92%,轧制油的油盒试验小于或等于2b,轧制油的胶质小于或等于800mg/100ml。
23.优选的,所述步骤s4中,对所述铝卷进行精整的具体步骤包括:
24.对所述铝卷进行拉弯矫直;其中,拉弯矫直的速度小于或等于80mm/min,拉弯矫直后的所述铝卷每1000mm存在的波均小于3个,且波高小于或等于3mm,波长大于或等于500mm。
25.第二方面,本发明提供了一种铝合金带材,所述铝合金带材由上述铝合金带材的制备方法制成。
26.与现有技术相比,本发明中铝合金带材的制备方法通过限定热连轧的轧制过程中轧辊的粘铝层厚度,并限定冷轧的各轧制道次中轧辊的粗糙度,同时配合各步骤的工艺参数限定,可以使制备得到的铝合金带材的表面光泽度均匀且可控,后续无需进行打磨,以降低其生产成本,提高其生产效率,且使制备工艺更简单。
【附图说明】
27.为了更清楚地说明本发明实施例中的技术方案,下面将对实施例描述中所需要使用的附图作简单地介绍,显而易见地,下面描述中的附图仅仅是本发明的一些实施例,对于本领域普通技术人员来讲,在不付出创造性劳动的前提下,还可以根据这些附图获得其它的附图,其中:
28.图1为本发明实施例提供的一种铝合金带材的制备方法的步骤流程示意图;
29.图2为本发明实施例提供的一种铝合金带材的制备方法中冷轧使用的轧辊的轧制道次、轧辊的轮廓算术平均偏差以及铝卷的光泽度对比表图;
30.图3为本发明实施例提供的一种铝合金带材的制备方法中冷轧使用的轧辊的轧制道次、轧辊的轮廓最大高度以及铝卷的光泽度对比表图;
31.图4为本发明实施例提供的一种铝合金带材的制备方法中冷轧使用的轧辊的轧制道次、轧辊的粗糙度峰计数以及铝卷的光泽度对比表图。
【具体实施方式】
32.下面将对本发明实施例中的技术方案进行清楚、完整地描述,显然,所描述的实施例仅是本发明的一部分实施例,而不是全部的实施例。基于本发明中的实施例,本领域普通技术人员在没有做出创造性劳动前提下所获得的所有其它实施例,都属于本发明保护的范围。
33.如图1所示,本发明实施例提供了一种铝合金带材的制备方法,该铝合金带材的制备方法包括以下步骤:
34.步骤s1、采用半连续铸造方法制备铸锭。
35.其中,采用半连续铸造方法制备铸锭之前包括步骤:将铝锭经过熔炼炉融化,并进行配料。即先将所述铝锭经过所述熔炼炉融化,然后进行配料,最后再采用半连续铸造方法制备铸锭。
36.该铝合金带材的配料根据实际需求,可以进行不同组分及质量百分比的配比,在此不一一进行举例说明。
37.步骤s2、对所述铸锭进行热连轧,得到厚度为5mm的热轧坯料。
38.其中,所述热连轧的轧制过程中使轧辊的粘铝层厚度为11~15μm。
39.对所述铸锭进行热连轧之前包括步骤:对所述铸锭进行铣削,将其冷隔粗晶层及偏析层铣削干净;其中,所述铸锭的上表面和下表面均铣削15mm。
40.所述热连轧采用“1+3”热连轧的方式进行轧制;即所述热连轧包括先采用单机架进行的热粗轧和后采用三机架依次进行的热精轧。
41.所述热连轧进行轧制前先对其轧辊进行刷痕测试,并保证尼龙刷的刷痕宽度为28~30mm;所述热连轧的终轧温度为330~350℃,即所述热精轧最后进行轧制时的温度为330~350℃;进行热连轧时其第三个机架的轧辊的温度大于80℃,这样设置可以得到表面纹路细腻且均一的热轧坯料。
42.优选的,所述热连轧的轧制过程中轧辊的粘铝层厚度为13μm;当然,根据实际需求,所述热连轧的轧制过程中轧辊的粘铝层厚度还可以为12μm或14μm等。
43.步骤s3、对所述热轧坯料进行冷轧,得到厚度为0.8mm的铝卷。
44.其中,所述冷轧的轧制道次依次包括第一轧制道次、第二轧制道次、第三轧制道次、第四轧制道次以及第五轧制道次。
45.所述第一轧制道次:将厚度为5mm的所述热轧坯料轧制成厚度为3.2mm的一道热轧坯料,轧制速度为100~200m/min,轧辊的粗糙度为ra(轮廓算术平均偏差)=0.4
±
0.02μm、rz(轮廓最大高度)=3.2
±
0.2μm、rpc(粗糙度峰计数)=180~200,轧辊的轧制道次大于5
道。
46.所述第二轧制道次:将厚度为3.2mm的所述一道热轧坯料轧制成厚度为2.1mm的二道热轧坯料,轧制速度为300~400m/min,轧辊的粗糙度为ra=0.32
±
0.02μm、rz=2.56
±
0.2μm、rpc=160~180,轧辊的轧制道次大于5道。
47.所述第三轧制道次:将厚度为2.1mm的所述二道热轧坯料轧制成厚度为1.42mm的三道热轧坯料,轧制速度为400~500m/min,轧辊的粗糙度为ra=0.28
±
0.01μm、rz=2.24
±
0.1μm、rpc=150~160,轧辊的轧制道次大于5道。
48.所述第四轧制道次:将厚度为1.42mm的所述三道热轧坯料轧制成厚度为0.95mm的四道热轧坯料,轧制速度为400~500m/min,轧辊的粗糙度为ra=0.28
±
0.01μm、rz=2.24
±
0.1μm、rpc=140~150,轧辊的轧制道次大于16道。
49.所述第四轧制道次轧制得到的厚度为0.95mm的所述四道热轧坯料经过清洗后进行完全再结晶退火,之后再进行所述第五轧制道次的轧制。完全再结晶退火后晶粒细小,形貌接近等轴晶。
50.所述第五轧制道次:将厚度为0.95mm的所述四道热轧坯料轧制成厚度为0.8mm的所述铝卷,轧制速度为300~400m/min,轧辊的粗糙度为ra=0.28
±
0.01μm、rz=2.24
±
0.1μm、rpc=130~140,轧辊的轧制道次大于16道。
51.所述第一轧制道次、所述第二轧制道次以及所述第三轧制道次中使用的轧制油的参数为:轧制油的运动粘度小于或等于2.8厘斯,轧制油的酸值小于或等于0.20mgkoh/g,轧制油中添加剂的质量百分比为6.0~10.0%,轧制油的透光率大于或等于85%,轧制油的油盒试验小于或等于2c,轧制油的胶质小于或等于1000mg/100ml。
52.所述步骤s3中,所述第四轧制道次以及所述第五轧制道次中使用的轧制油的参数为:轧制油的运动粘度小于或等于2厘斯,轧制油中添加月桂酸以将其酸值控制在小于或等于0.20mgkoh/g,轧制油中添加剂的质量百分比为6.0~7.0%,轧制油的透光率大于或等于92%,轧制油的油盒试验小于或等于2b,轧制油的胶质小于或等于800mg/100ml。这样设置可以保证油品润滑足够的同时,增加油品的清洗能力,使铝卷表面的铝粉和铝灰去除得更彻底,使铝卷的表面纹路更清晰均匀,光泽度更好。
53.所述第四轧制道次以及所述第五轧制道次中使用的轧制油添加月桂酸的作用是为了增加油品的清洗能力,因为轧制油在前面三个轧制道次的使用时,其酸值会受到影响而改变。
54.所述第五轧制道次轧制得到的厚度为0.8mm的所述铝卷经过清洗后进行稳定化退火,之后再进行以下步骤s4。这样设置可以去除铝卷的残余应力。
55.本实施例中,所述第一轧制道次、所述第二轧制道次、所述第三轧制道次、所述第四轧制道次以及所述第五轧制道次中,使用的轧辊分别经过3道或3道以上的轧制。
56.其中,使用的轧辊分别经过3道或3道以上的轧制,也可以理解为轧辊低粗糙度轧制道次必须有3道或3道以上的轧制;即在进行所述第一轧制道次、所述第二轧制道次、所述第三轧制道次、所述第四轧制道次以及所述第五轧制道次之前,对应使用的新轧辊分别经过其它的材料进行过3道或3道以上的轧制,之后才进行对应的所述第一轧制道次、所述第二轧制道次、所述第三轧制道次、所述第四轧制道次以及所述第五轧制道次。
57.具体地,所述第一轧制道次、所述第二轧制道次以及所述第三轧制道次中,使用的
轧辊分别经过5道以上的轧制,即在进行所述第一轧制道次、所述第二轧制道次以及所述第三轧制道次之前,对应使用的新轧辊分别经过其它的材料进行过5道以上的轧制,之后才进行所述第一轧制道次、所述第二轧制道次以及所述第三轧制道次;因为轧辊的表面粗糙度ra、rz以及rpc在前5道时衰减的特别快,形成的铝卷的表面粗糙度波动大,而在5道后会出现缓慢衰减,使形成铝卷的表面粗糙度波动降低。
58.具体地,所述第四轧制道次以及所述第五轧制道次中,使用的轧辊分别经过16道以上的轧制,即在进行所述第四轧制道次以及所述第五轧制道次之前,对应使用的轧辊分别经过其它的材料进行过16道以上的轧制,之后才进行所述第四轧制道次以及所述第五轧制道次;因为轧辊的表面粗糙度ra、rz以及rpc衰减程度几乎平稳,此时铝卷的表面光泽度也趋近定值,从而达到光泽度可控的目的。
59.本实施例中,所述冷轧的轧制过程中,所述第一轧制道次至所述第五轧制道次中,轧辊的表面粗糙度的三个参数逐步降低,可以使铝卷的表面粗糙度也逐渐降低,避免留下大的波峰波谷,造成表面光泽度不均匀。
60.本实施例中,所述第一轧制道次至所述第五轧制道次中,轧辊的轧制道次也可以设置为必须大于或等于3道次,这样铝卷经过低粗糙度的轧辊轧制后原始峰高才能被磨削去除,以叠加上新辊表面形貌,与原始波谷复合形成新的表面形态;若轧辊的轧制道次少,前面形貌未能全部磨削去除,会影响铝卷表面光泽度的均匀性。
61.本实施例中,所述冷轧使用的轧辊的轧制道次、轧辊的轮廓算术平均偏差(ra)以及铝卷的光泽度对比表如图2所示;所述冷轧使用的轧辊的轧制道次、轧辊的轮廓最大高度(rz)以及铝卷的光泽度对比表如图3所示;所述冷轧使用的轧辊的轧制道次、轧辊的粗糙度峰计数(rpc)以及铝卷的光泽度对比表如图4所示。
62.步骤s4,对所述铝卷进行精整,得到厚度为0.8mm的铝合金带材。
63.其中,对所述铝卷进行精整的具体步骤包括:
64.对所述铝卷进行拉弯矫直;其中,拉弯矫直的速度小于或等于80mm/min,所述铝卷的板形要求平整,拉弯矫直后的所述铝卷每1000mm存在的波均小于3个,且波高小于或等于3mm,波长大于或等于500mm。
65.对所述铝卷进行拉弯矫直时,还可以对所述铝卷进行清洗。
66.与现有技术相比,本实施例中铝合金带材的制备方法通过限定热连轧的轧制过程中轧辊的粘铝层厚度,并限定冷轧的各轧制道次中轧辊的粗糙度,同时配合各步骤的工艺参数限定,可以使制备得到的铝合金带材的表面光泽度均匀且可控,后续无需进行打磨,以降低其生产成本,提高其生产效率,且使制备工艺更简单,同时使制备得到的铝合金带材的综合机械性能优良,表面质量优良。
67.另外,所述铝合金带材的制备方法根据实际需求,还可以通过适应性更改步骤s2中热连轧的工艺参数、步骤s3中冷轧的工艺参数以及步骤s3中冷轧的各轧制道次中轧辊的粗糙度来制备得到厚度为0.15~1.2mm的铝合金带材或其它厚度的铝合金带材,并保证该铝合金带材的光泽度可控,生产成本低,生产效率高,且制备工艺简单,从而使制备得到的铝合金满足不同客户的需求。
68.经验证,采用上述铝合金带材制备方法制备铝合金带材,并保证热连轧的轧制过程中轧辊的粘铝层厚度为13μm,冷轧过程中第一轧制道次至第五轧制道次的控制,第一轧
制道次至第五轧制道次中轧辊的表面粗糙度逐步降低,轧辊的轧制道次大于或等于3道次等工艺,可以有效控制铝合金表面的光泽度,使光泽度垂直轧制的表面范围为10-300gu;经a公司验证5052h32厚度为0.4mm的铝合金的表面光泽度可以稳定保持在90-100gu,b公司验证1060h24厚度0.15mm的铝合金的表面光泽度可以稳定保持在160-180gu,且表面细腻均匀,质量优良。
69.本发明还提供了一种铝合金带材的实施例,该铝合金带材由上述实施例中铝合金带材的制备方法制成。
70.由于本实施例中的铝合金带材由上述实施例中铝合金带材的制备方法制成,因此其也达到了上述实施例中铝合金带材的制备方法所达到的技术效果,在此不作赘述。
71.以上所述仅为本发明的实施例,并非因此限制本发明的专利范围,凡是利用本发明说明书及附图内容所作的等效结构或等效流程变换,或直接或间接运用在其它相关的技术领域,均同理包括在本发明的专利保护范围内。