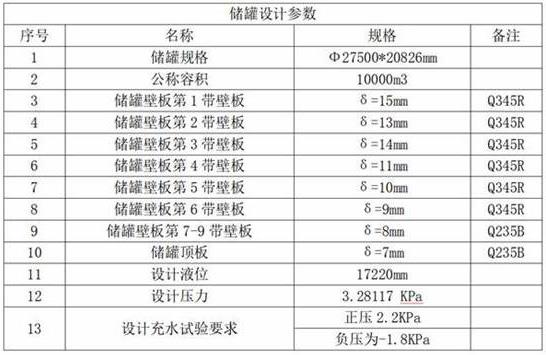
1.本发明涉及石油化工行业中储罐施工技术,具体而言,是一种用于存储原油、化工等产品钢制储罐的罐体凹陷修复施工方法。
背景技术:2.在煤制油、煤制气及其衍生化学品等新型煤化工项目中,大型金属储罐罐区承载着转运、存储等功能,是化工项目中不可或缺的装置区。钢制常压拱顶储罐是石化行业应用十分广泛的一种存储设备,在生产过程中操作不当或者极端天气引起气温骤变,导致灌顶、罐壁局部产生凹陷,对常压储罐的安全生产带来严重的威胁。罐体产生凹陷后,如何快速、安全、有效并最大可能的节约成本恢复其正常生产状态又成为一个不可避免的问题。
技术实现要素:3.本发明的目的是提供一种钢制储罐凹陷矫正的修复方法,从而实现大型钢制拱顶储罐凹陷修复的问题,提高工程施工质量及施工效率。
4.为解决以上技术问题,本发明采用的技术方案是:一种钢制储罐凹陷矫正的修复方法,包括以下步骤:步骤一,钢制储罐凹陷原因分析和储罐矫正压力计算;步骤二,安全泄压装置、压强监测装置安装;安全泄压装置用于在矫正过程中调节储罐内压力,压强监测装置用于对钢制储罐内压强进行监测;步骤三,利用储罐内外压强差进行初步矫正;凹陷金属储罐全部封闭完毕,利用内外压强差的不同和热胀冷缩的原理,储罐内部压力大于外部压力,作用在凹陷的区域使其逐步恢复原状,完成钢制储罐的初步修复;步骤四,金属钢制储罐的机械修复;搭设储罐外围脚手架直至顶层并预制机械矫正工装,机械矫正工装包括工字钢和由门形架和机械螺旋千斤顶组成的矫正组件;在初步修复未完全修复区域的储罐壁上竖向焊接所述工字钢,门形架的两端分别与工字钢两侧的凹陷部分储罐壁焊接;机械螺旋千斤顶置于门形架内部且机械螺旋千斤顶的活塞杆前端与工字钢焊接固定;通过机械螺旋千斤顶对未完全修复区域逐一进行外拉修复;步骤五,金属钢制储罐变形区域的焊缝无损检测;步骤六,金属钢制储罐盛水试验。
5.进一步地,步骤一中,根据现场环境、天气、昼夜温差和设计图纸计算最终矫正压强,矫正压强在金属储罐抗破坏压力以下。
6.进一步地,步骤二中,所述安全泄压装置包括泄压阀;在钢制储罐罐顶紧急通风口处接碳钢管,碳钢管连接至泄压阀。
7.进一步地,步骤二中,所述的压强监测组装包括一个带有压力刻度的u型玻璃管;钢制储罐罐顶氮气口处接碳钢管,u型玻璃管的一端通过胶管连接至碳钢管。
8.进一步地,步骤三中,金属储罐封闭完成后,根据压强监测装置的观测情况,控制
安全泄压装置,罐体初步修复后稳压一段时间,再逐步缓慢降压,防止已修复的凹陷区域二次凹陷。
9.进一步地,步骤四中,在未完全修复区域的储罐带板外壁中间处焊接槽钢作为加固圈。
10.本发明提供了一种大型钢制储罐利用内外不均衡压强差结合机械矫正的修复工艺。首先利用储罐内外压强差使得大部分凹陷区域恢复,然后利用机械修复将凹陷部位进一步恢复接近原始状态,施工材料容易获得、操作步骤简单,有助于提高工程施工质量及施工效率。
11.本方法特别适用于气温变化大、金属储罐凹陷严重等复杂条件下的矫正修复工作。
附图说明
12.图1是本发明安全泄压装置的结构示意图;图2是本发明压强监测装置的结构示意图;图3是u形玻璃管的结构示意图;图4是机械矫正工装在金属储罐壁上的位置示意图;图5是机械矫正工装的结构示意图。
13.图中,1-罐顶连接法兰,2-安全阀,3-闸阀,4-碳钢管,5-u形玻璃管,6-胶皮管,7-工字钢,8-门形架,9-机械螺旋千斤顶,10-矫正组件,11-支架。
具体实施方式
14.本发明是提供一种典型实施方式的钢制储罐凹陷矫正修复方法,其特征在于,包括以下步骤:步骤一,钢制储罐凹陷原因分析和储罐矫正压力计算。
15.1.钢制储罐凹陷原因分析钢制储罐结构、材料、环境、储存介质、操作方法、使用年限等原因均与储罐凹陷有一定的因果关系,需根据凹陷的严重程度结合具体情况进行分析论证。
16.具体而言,根据《石油化工立式圆筒形钢制焊接储罐设计规范》、《立式圆筒形钢制焊接储罐施工规范》,结合现场实际情况,确定储罐凹陷的具体原因。
17.2.储罐矫正压力计算金属钢制拱顶储罐凹陷修复初步矫正利用内外压强差进行自我修复,危险系数大,操作前需根据钢制储罐相应标准规范、设计文件、罐顶与罐壁连接处抗拉环受力分析、有效截面积等因素,通过结构屈服强度下限值最终确定矫正极限压力的大小。
18.步骤二,安全泄压装置、压强监测装置安装。
19.安全泄压装置用于在矫正过程中调节储罐内压力,压强监测装置用于对钢制储罐内压强进行监测。
20.金属钢制拱顶储罐凹陷修复初步矫正阶段,是利用内外压强差进行自我修复,可靠的安全泄压装置是进行控制压差、避免二次事故的决定性因素。根据罐体容积、高度、设计参数、修复时间段、现场环境等因素综合考虑安全泄压装置的泄压能力大小及防护装置。
21.如图1所示,所述安全泄压装置包括泄压阀;所述泄压阀由安全阀2和闸阀3组成,在钢制储罐罐顶紧急通风口处接碳钢管4,碳钢管4连接至泄压阀。
22.安装与安全泄压装置配套使用的压强监测装置,确保初步修复阶段压强可控。金属钢制储罐初步修复阶段核心就是利用储罐内外不均衡的压强差进行金属储罐本体的修复,而最重要的监测手段就是结合储罐的具体设计参数及现场情况制安可供储罐内部与外部监测压强差的相关装置,随着压强差的不断变化进行监测记录,与安全泄压装置进行配合使用,保证初步修复压力符合步骤二计算完成的矫正压力要求。
23.如图2所示,所述的压强监测组装包括一个带有压力刻度的u型玻璃管5(图3所示),u形玻璃管5内加水或其他液体;钢制储罐罐顶的氮气口处接碳钢管4,u型玻璃管5的一端通过胶管6连接至碳钢管4。
24.步骤三,利用储罐内外压强差进行初步矫正。
25.凹陷金属储罐全部封闭完毕,利用内外压强差的不同和热胀冷缩的原理,储罐内部压力大于外部压力,作用在凹陷的区域使其逐步恢复原状,完成钢制储罐的初步修复。
26.金属钢制储罐修复技术准备及现场准备完成后,根据储罐内部储存介质的特性及数量、现场天气状况选择具体修复的时间,确定后准备相应施工人员、安全警戒措施及应急救援措施。然后封闭金属储罐所有附属孔洞,利用压强监测装置间隔固定时间进行监测金属储罐内部压力,利用安全泄压装置控制金属储罐内部压力,确保其压力不超过步骤一确定的储罐矫正压力极限值。最终无论凹陷的金属储罐修复至何种状态,必须立即打开泄压装置确保内外压力的平衡,利用压强差修复结束。
27.步骤四,金属钢制储罐的机械修复。
28.搭设储罐外围脚手架直至顶层。金属钢制储罐利用压差修复后,依据实际情况开始机械修复过程。由于储罐内部装有介质以及罐内施工效率慢的因素,因此考虑外部进行机械修复,需要搭设脚手架。
29.预制机械矫正工装。根据初步修复后金属储罐的实际情况及脚手架预留作业空间情况、机械螺旋千斤顶数量,利用工字钢、钢板等材料制安足够数量的配套机械矫正工装。机械矫正工装包括工字钢7和由门形架8和机械螺旋千斤顶9组成的矫正组件10。
30.根据金属储罐初步修复程度划分区域,对罐壁部分进行加固,即在未完全修复区域的储罐带板外壁中间处横向焊接槽钢作为加固圈。然后结合已划分好的区域逐步进行机械矫正修复。
31.如图4、5所示,在初步修复未完全修复区域的储罐壁上竖向焊接所述工字钢7,门形架8的两端分别与工字钢7两侧的管壁焊接;机械螺旋千斤顶9置于门形架8内部且机械螺旋千斤顶9的活塞杆前端与工字钢7焊接固定,与罐壁焊接时,需要注意焊接电流的大小,严禁对罐壁造成二次损坏。由机械螺旋千斤顶9对为完全修复区域逐一进行外拉修复。
32.通过合理划分修复区域,增加机械矫正套装数量,利用螺旋千斤顶9修复后,整个划分的单独修复区域要有计划、隔断的逐一进行拆除,防止造成二次事故。
33.步骤五,金属钢制储罐变形区域的焊缝无损检测。
34.整体矫正完成后,变形较大的壁板焊缝进行无损检测,尤其对t形焊缝检查焊缝质量是否符合要求。
35.步骤六,金属钢制储罐盛水试验。
36.修复完后的金属储罐无损检测试验完成后,再进行盛水试验,对储罐罐底、罐壁、灌顶根据设计要求进行正负压试验,检查修复后储罐有无泄漏、有无变形等情况发生。
37.下面以10000m3煤焦油储罐为例。在储罐充水试漏过程中(罐内充水至6m),因昼夜温差较大导致储罐壁板上半部分出现较大区域凹陷变形,内凹最大深度达600毫米左右,壁板变形面积达40%,同时导致盘梯扭曲。以此金属拱顶储罐修复为例做进一步说明。
38.本实施例主要说明初步利用压强差修复罐壁、最终机械矫正修复等方面的施工关键技术,其余步骤施工按相关设计、标准规范进行。
39.表1 储罐设计参数表2储罐变形情况测量方位最大变形量(第a代板-第b带板)变形面积/m
²
深度/mm30
°
7-85753160
°
7-857600120
°
7-848496150
°
7-884520210
°
6-880564240
°
8-872466270
°
6-880387315
°
7-848426一.煤焦油储罐凹陷原因分析1.在储罐充水试漏准备工作中,工作人员误将现有人孔和清扫孔及管口全部封闭,使储罐内部形成密封空间;2、遇到极端天气,夜间气温骤变,导致短时间温差达到18度,在储罐内部形成较大负压并超过设计值,导致储罐壁板内凹变形:(1)储罐清扫孔是在2022年4月15日下午15时许封闭完成,当日气温为3℃~20℃;
储罐发生内凹变形为4月16日凌晨,当日气温为2℃~16℃;(2)从储罐封闭到储罐内凹变形过程,储罐内温度变化差大约为18℃;4月15日下午3时许储罐封闭后内部温度达到峰值(20℃),至4月16日凌晨罐内温度逐渐降至最低值(2℃);因储罐壁板隔离和内部空气体积较大,其内温度变化滞后于罐外环境温度变化。
40.表3施工现场压强差分析二.煤焦油储罐矫正压力计算1、金属储罐罐顶与罐壁连接处抗拉环需要的截面面积按下式确定:ar=(pi-0. 00127dlr/d2)d2
×
103/8[б] tan(θ) = 2044. 21dlr
ꢀ‑
罐顶板及其附件重(n),dl = 0. 00127dlr/d2 = 0.60862 kpa[б]-材料许用应力(mpa),取设计温度下1/1. 6,材料标准屈服强度下限值,取140.63 mpa。
[0041]
经计算,满足罐顶与罐壁连接处所需有效截面积要求。
[0042]
2、当罐顶与罐壁连接处抗拉环的有效面积已确定时,微内压储罐的最大设计压力应按下式确定p=a relttanθ/200 d2 + 0. 00127dlr/d2 = 3. 28117 kpaa
ꢀ‑
罐顶与罐壁连接处抗压环的有效截面面积(mm2)dlr
ꢀ‑
罐顶板及其附件重(n),如上说明relt-设计温度下抗压环材料标准屈服强度下限值(mpa)3、罐顶与罐壁的连接结构产生屈曲破坏的压力应按下式确定:pf=1.6p—0.000746 dlr/d2 = 3.70613dlr
ꢀ‑
罐顶板及其附件重量(n)包边角钢重1538. 34kg4、储罐变形充压矫形压力确定:pj = 3. 2 kpa,小于设计值3.28117 kpa。
[0043]
三.制备并安装安全泄压装置利用储罐罐顶dn200紧急通风口,dn200碳钢管及配套阀门接至地面,制安一套可供储罐紧急泄压的安全装置,地面操作处制安防护棚。
[0044]
四、压强监测装置制安利用储罐罐顶dn25氮气口,dn25碳钢管及配套阀门接至离罐基础1.5m处,通过变径及1/4寸透明软胶管及u型玻璃管5组合成可供监测的u型压强监测装置,将u型玻璃管竖
直固定在底部罐壁处,通过u型玻璃管5与之对应的刻度值进行储罐内部压强监测。
[0045]
五、金属储罐利用罐内外压强差进行初步矫正对煤焦油储罐罐顶包边角钢、安全泄压装置、压强监测装置、防护装置进行最终检查,确认无问题后开始初步矫正。确保泄压装置为打开状态,罐壁所有dn250物料入口、dn150物料出口、罐壁人孔、dn25凝结水出口、dn50蒸汽入口等确保封闭,灌顶dn500透光孔(保持常开,升压时再关闭)、dn200雷达液位计口、dn300呼吸阀口等确保用盲板、垫片封堵完成,并用肥皂水检测无泄漏。
[0046]
煤焦油储罐于5月15日准备升压恢复罐壁凹陷,上午6:30所有人员已经就位,辅助吊车、装载机均已就位,7:00开始封闭顶部人孔法兰,于7:30开始关闭罐底排气泄压阀,罐体在气温变化下开始逐步增压,通过泄压阀严格控制压增情况,于7:40罐体出现响动逐渐开始恢复,直至9:00左右罐体恢复至90%左右,剩余时间均在稳压过程中,具体记录如下表:(六)脚手架搭设钢制储罐初步修复结束后,结合储罐保温脚手架专项施工方案开始搭设储罐外围脚手架直至顶层,对需要机械修复的部位,结合现场实际,适当改变此处脚手架结构,留取足够的空间进行机械矫正修复作业。
[0047]
(七)机械矫正工装制安准备槽钢[12 132m,工字钢工20 96m,20mm厚钢板9m2,10mm厚钢板5m2。预制带加强筋的工字钢7、门型架8、加强板的机械矫正工装。制安过程中结合储罐外脚手架与储罐间隙进行作业,确认所有焊缝满焊,焊接厚度符合强度要求。
[0048]
(八)金属储罐机械矫正修复煤焦油储罐外侧脚手架由架子队搭设完成经三方验收合格,罐壁矫正前对罐体壁板可能存在的应力区域进行标注;与壁板相焊接的材料及焊材应与壁板匹配;然后在储罐6、7、8带板外壁中间处增加12#槽钢加固圈各1道,凹陷需要矫正的部分暂时避开;其后储罐壁板矫正对其局部变形利用20t螺旋千斤顶、20号工字钢、20mm厚钢板预制好的矫正工装、吊车配合物料机具吊装,采用外拉方式进行逐步机械矫正。罐壁矫形完成后加固圈与壁板间断焊(槽钢焊100毫米空200毫米,上下交叉错开),以达到罐壁加强作用;并对变形量较大的焊缝进行矫正后的检查。矫正工装与罐壁焊接时注意焊接电流,防止烧穿罐壁。
[0049]
(九)煤焦油储罐变形焊缝无损检测煤焦油储罐变形较大的壁板焊缝进行ut无损检测,尤其对t形焊缝检查进行检测,经过探伤公司射线检测合格。
[0050]
(十)煤焦油储罐盛水试验煤焦油储罐机械矫正完成后,对储罐进行盛水试验,试验结果正常,符合验收标准。
[0051]
1、储罐底板在充满水(设计液位17.22米)后,48小时内无泄漏;2、储罐壁板在充满水(设计液位17.22米)后,48小时内无泄漏、无异常变形;3、储罐顶板在储罐充水至16.22m后,首先进行2.2kpa正压试验,罐顶无异常变形,所有焊缝经发泡剂检查无泄漏;然后进行罐顶稳定性试验,试验压力为-1.8kpa,储罐无异常变形。