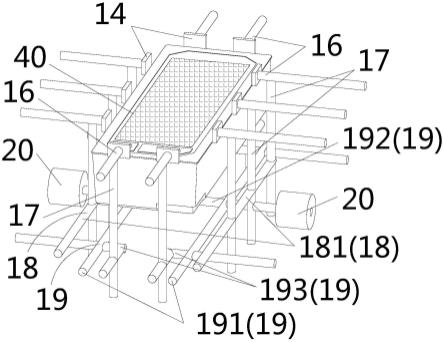
1.本实用新型涉及模具制造技术领域,尤其涉及一种复合双极板模具抽真空结构。
背景技术:2.燃料电池是一种继水力发电、热能发电以及原子能发电后的第四种发电技术,其发电效率高、清洁环保,是一种绿色新能源。双极板是质子交换膜燃料电池的关键部件,其质量在整个电池组中比重很大,约为80%,重要性不言而喻;复合双极板因其较高的使用寿命、优良的抗腐蚀性以及较低的制造成本而被人们所重视。
3.现有的复合双极板(阴极板或阳极板)在模压成型时,常存在以下问题:
4.(1)模压时未抽真空,排气无法排尽导致成型时双极板表面出现鼓包;
5.(2)模压模具设置有抽真空结构,但因真空密闭空间包含上下模具以及上模行程内的空间,空间较大,导致抽真空时间较长、抽真空难度较大、耗电较多,造成复合双极板成型周期较长,制造成本提高。
6.为了解决上述问题,本方案提出了一种复合双极板模具抽真空结构。
技术实现要素:7.本实用新型的发明目的在于解决现有的复合双极板在模压成型时,常存在模压时未抽真空,排气无法排尽导致成型时双极板表面出现鼓包,模压模具设置有抽真空结构,但因真空密闭空间较大,导致抽真空时间较长、抽真空难度较大、耗电较多,造成复合双极板成型周期较长,制造成本提高的问题。其具体解决方案如下:
8.一种复合双极板模具抽真空结构,包括上模和下模,所述上模中部嵌设有向下凸出的上模芯,所述下模中部设有下凹的模腔,模腔下部设有下模芯,模腔上部容纳上模芯的凸出部分,所述凸出部分的中段水平环绕四周设有密封机构,在密封机构以下的下模中设有排气机构,排气机构的一端与模腔腔体连通,排气机构的另一端分别与开关阀、真空泵连通,上模芯与下模芯的接触面处设有模压产品。
9.进一步地,所述密封机构包括设于上模芯的凸出部分的中段水平环绕四周的内凹密封槽、设于密封槽内的密封圈。
10.进一步地,所述密封圈为橡胶材料制成。
11.进一步地,所述排气机构包括环绕模腔腔体的内壁上内凹的多个内排气口、设于内排气口中的滤气片、与内排气口相连通的多个上排气管道、与多个上排气管道连通的多个垂直排气管道、分别与多个垂直排气管道连通的多个第一下排气管道和多个第二下排气管道、与第一下排气管道和多个第二下排气管道连通的两个外排气口,其中一个外排气口与所述开关阀连通,另一个外排气口与所述真空泵连通。
12.进一步地,所述内排气口为矩形,内排气口与所述滤气片匹配。
13.进一步地,所述滤气片所用材料为聚丙烯,滤气片目数为2~100,滤气片内部结构为多层,且不同层的孔隙不处于同一直线上。
14.进一步地,所述内排气口的数量为:沿模具的两长边方向各对称设有三个,沿模具的两短边方向各对称设有两个。
15.进一步地,所述第一下排气管道为两个同平面平行的两个直管。
16.进一步地,所述第二下排气管道包括两个同平面平行的两个直管、与两个直管的中部垂直的一个直管、一端分别与两个直管的两端连通的四个弯折管,四个弯折管的另一端分别与模具的两短边侧的所述垂直排气管道的下端连通。
17.进一步地,所述第一下排气管道与第二下排气管道处于不同的平面中。
18.综上所述,采用本实用新型的技术方案具有以下有益效果:
19.解决了现有的复合双极板在模压成型时,常存在模压时未抽真空,排气无法排尽导致成型时双极板表面出现鼓包,模压模具设置有抽真空结构,但因真空密闭空间较大,导致抽真空时间较长、抽真空难度较大、耗电较多,造成复合双极板成型周期较长,制造成本提高的问题。采用本方案具有以下优点:
20.(1)解决了现有的燃料电池的复合双极板成型鼓包问题。
21.(2)上模与下模形成封闭模腔,真空密闭空间小,抽真空快,缩短成型周期,提高生产效率,降低耗电成本。
22.(3)内排气口设置有滤气片,抽真空时,滤气片可防止成型粉末因抽真空产生的负压被吸进排气管道,造成排气管道堵塞。
23.本实用新型的结构设计合理且简单、防粉末堵塞、密封性好、效率高。
附图说明
24.为了更清楚地说明本实用新型实施例的技术方案,下面将对本实用新型实施例的描述中所需要使用的附图作简单地介绍。显而易见地,下面描述中的附图仅仅是本实用新型的一部分实施例,对于本领域普通技术人员来讲,在不付出创造性劳动性的前提下,还能够根据这些附图获得其他的附图。
25.图1为本实用新型一种复合双极板模具抽真空结构的沿模具长边方向的纵剖面结构图;
26.图2为本实用新型的上模芯结构图;
27.图3为本实用新型的排气机构结构图,此图中省去了下模。
28.附图标记说明:
29.10-上模,11-上模芯,12-密封槽,13-密封圈,14-内排气口,15-凸出部分,16-上排气管道,17-垂直排气管道,18-第一下排气管道,19-第二下排气管道,20-外排气口,30-下模,31-模腔,32-下模芯,40-模压产品,181-第一直管,191-第二直管,192-第三直管,193-弯折管。
具体实施方式
30.下面将结合本实用新型实施例中的附图,对本实用新型实施例中的技术方案进行清楚、完整地描述。显然,所描述的实施例仅仅是本实用新型一部分实施例,而不是全部的实施例。基于本实用新型中的实施例,本领域普通技术人员在没有作出创造性劳动前提下所获得的所有其他实施例,都属于本实用新型保护的范围。
31.如图1至3所示,一种复合双极板模具抽真空结构,包括上模10和下模30(整体呈矩形),上模10中部嵌设有向下凸出的上模芯11,下模30中部设有下凹的模腔31,模腔31下部设有下模芯32,模腔31上部容纳上模芯11的凸出部分15,凸出部分15的中段水平环绕四周设有密封机构,在密封机构以下的下模30中设有排气机构,排气机构的一端与模腔31腔体连通,排气机构的另一端分别与开关阀(图中未画出)、真空泵(图中未画出)连通,上模芯11与下模芯32的接触面处设有模压产品40。
32.具体地,密封机构包括设于上模芯11的凸出部分15的中段水平环绕四周的内凹密封槽12、设于密封槽12内的密封圈13,密封圈13为橡胶材料制成。
33.具体地,排气机构包括环绕模腔31腔体的内壁上内凹的多个内排气口14(本实施例中沿模具的两长边方向各对称设有三个内排气口14,沿模具的两短边方向各对称设有两个内排气口14)、设于内排气口14中的滤气片(图中未画出)、与内排气口14相连通的多个(本实施例中为十个)上排气管道16、与多个上排气管道16连通的多个(本实施例中为十个)垂直排气管道17、分别与多个垂直排气管道17连通的多个第一下排气管道18和多个第二下排气管道19、与第一下排气管道18和多个第二下排气管道19连通的两个外排气口20,其中一个外排气口20与开关阀连通,另一个外排气口20与真空泵连通。抽真空时,开关阀为关闭状态,开模时,则开关阀为打开状态。
34.具体地,内排气口14为矩形,内排气口14与滤气片匹配。
35.最优选地,滤气片所用材料为聚丙烯,滤气片目数为2~100,滤气片内部结构为多层,且不同层的孔隙不处于同一直线上。抽真空时,滤气片可防止成型粉末因抽真空产生的负压被吸进排气管道,造成排气管道堵塞。
36.具体地,第一下排气管道18为两个同平面平行的两个第一直管181。第二下排气管道19包括两个同平面平行的两个第二直管191、与两个第二直管191的中部垂直的一个第三直管192、一端分别与两个第二直管191的两端连通的四个(一端分别为两个)弯折管193,四个弯折管193的另一端分别与模具的两短边侧的垂直排气管道17的下端连通。
37.具体地,第一下排气管道18与第二下排气管道19处于不同的平面中。
38.综上所述,采用本实用新型的技术方案具有以下有益效果:
39.解决了现有的复合双极板在模压成型时,常存在模压时未抽真空,排气无法排尽导致成型时双极板表面出现鼓包,模压模具设置有抽真空结构,但因真空密闭空间较大,导致抽真空时间较长、抽真空难度较大、耗电较多,造成复合双极板成型周期较长,制造成本提高的问题。采用本方案具有以下优点:
40.(1)解决了现有的燃料电池的复合双极板成型鼓包问题。
41.(2)上模与下模形成封闭模腔,真空密闭空间小,抽真空快,缩短成型周期,提高生产效率,降低耗电成本。
42.(3)内排气口设置有滤气片,抽真空时,滤气片可防止成型粉末因抽真空产生的负压被吸进排气管道,造成排气管道堵塞。
43.本实用新型的结构设计合理且简单、防粉末堵塞、密封性好、效率高。
44.以上所述的实施方式,并不构成对该技术方案保护范围的限定。任何在上述实施方式的精神和原则之内所作的修改、等同替换和改进等,均应包含在该技术方案的保护范围之内。