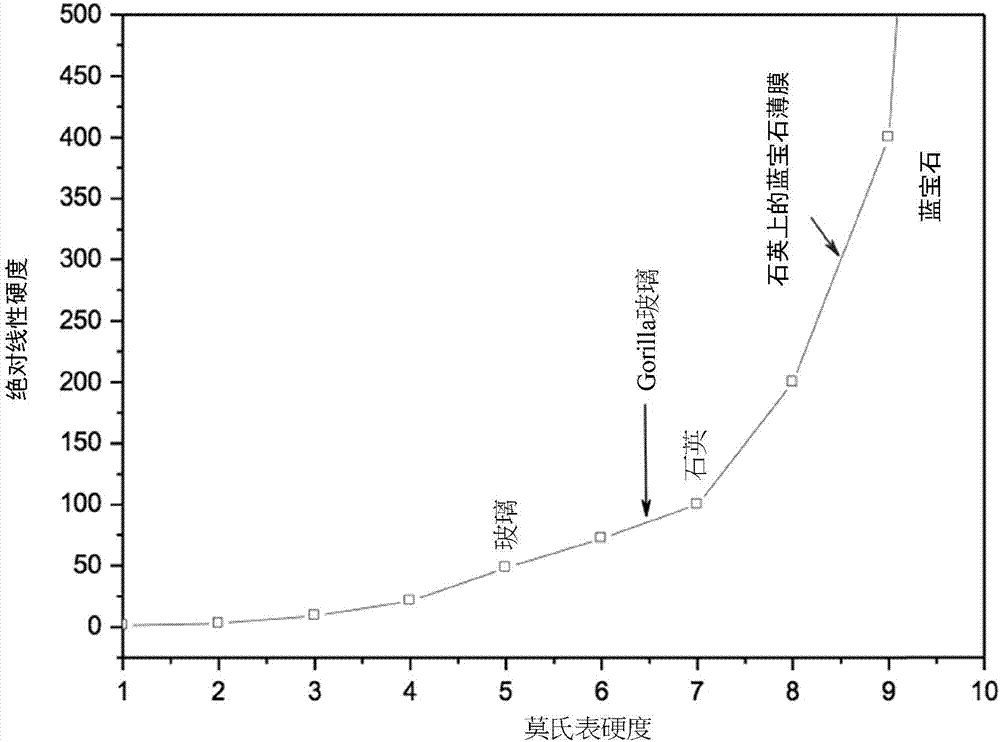
本发明涉及一种将较硬薄膜基板层转移至较软基板(尤其较软可挠基板)上的方法。详言的,本发明提供一种经由覆晶制程将蓝宝石薄膜层转移至较软可挠基板(例如pet、聚合物、塑料、纸及织物)上的方法。本发明涉及一种将较硬薄膜基板层转移至较软基板(尤其较软可挠基板)上的方法。详言的,本发明提供一种经由覆晶制程将蓝宝石薄膜层转移至较软可挠基板(例如pet、聚合物、塑料、纸及织物)上的方法。较硬薄膜蓝宝石基板层于较软基板上的组合与纯蓝宝石基板相比较佳。实际上,材料愈硬,其愈脆,因此,蓝宝石基板很难擦伤,但其容易碎裂且反过来亦常常如此,其中石英基板与蓝宝石基板相比较易于擦伤,但其脆性较小。因此,将较硬薄膜基板沉积于较软可挠基板上两全其美。较软可挠基板脆性较小,具有良好机械效能且通常成本较低。藉由使用较硬薄膜基板将实现防擦伤功能。
背景技术:
:蓝宝石目前积极考虑作为智能型手机及平板计算机的屏幕。其为钻石的后第二硬的材料,因此使用其作为屏幕将意味着智能型手机/平板计算机具有优异的耐擦伤及抗开裂性屏幕。蓝宝石屏幕已用于iphone5stouchid扫描仪及手机背面的相机镜头上。奢侈智能型手机制造商vertu亦研发蓝宝石屏幕。然而,由于蓝宝石为第二硬的材料,故其亦难以被切割及被抛光。外加大尺寸单晶蓝宝石的生长耗时,此导致制造时间长且制造成本高。蓝宝石屏幕的制造成本高及制造时间长限制apple公司将此类蓝宝石屏幕仅用于applewatch。目前流行的『钢化』屏幕材料使用来自corning的gorilla玻璃,其用于超过15亿装置。蓝宝石实际上比gorilla玻璃更难以擦伤且此经数个第三方研究院验证,诸如在阿尔弗雷德大学稻盛和夫工程学院的先进陶瓷技术中心(centerforadvancedceramictechnologyatalfreduniversity'skazuoinamorischoolofengineering)。在莫氏硬度表上,最新gorilla玻璃仅评分6.5mohs,低于矿物石英的莫氏值,使得gorilla玻璃易于被砂及金属擦伤。蓝宝石为行星上天然存在的钻石的后第二硬的材料,其在莫氏矿物硬度表上评分10。此测试比较一种物质擦伤另一种物质的能力,因此其抗碎裂性系为比耐擦伤性更好的指标。莫氏硬度测试经由较硬材料擦伤较软材料的能力来表征矿物的耐擦伤性。其比较一种物质擦伤另一种物质的能力,且因此为比抗碎裂性更好的耐擦伤性的指标。此展示于图1中。以下为来自『displayreview』对于蓝宝石屏幕的引语:「化学强化玻璃可为极好的,但蓝宝石在硬度、强度及韧性方面更好」hall解释道,加上「蓝宝石的破裂韧性度应比gorilla玻璃高约四倍,分别为约3mpa-m0.5对比0.7mpa-m0.5。」然而,此伴随一些相当大的缺点。蓝宝石较重,每立方公分3.98g(相比于gorilla玻璃的2.54g),折射光相对较多。除了较重的外,作为第二硬材料的蓝宝石亦为难以切割及抛光的材料。单晶蓝宝石生长为耗时的,尤其当直径尺寸较大(>6吋)时,此在技术上极具挑战性。因此,蓝宝石屏幕的制造成本高且制造时间长。本发明的目标为提供快速制造且成本低同时具有以下优势的蓝宝石屏幕材料的制造方式:●比任何硬化玻璃更硬;●比纯蓝宝石屏幕断裂的可能性更小;●重量比纯蓝宝石屏幕更轻;●透明度比纯蓝宝石屏幕更高。对于蓝宝石(al2o3)薄膜沉积的硬化,较软基板的软化/熔融温度应充分高于退火温度。大多数刚性基板,诸如石英、熔融硅石可符合此要求。然而,可挠基板,诸如聚对苯二甲酸乙二酯(pet)将无法符合该要求。pet的熔融温度为约250℃,远低于退火温度。pet为最广泛使用的可挠基板中的一者。将al2o3(蓝宝石)薄膜基板转移至较软可挠基板上的能力将使其应用自刚性基板(如玻璃及金属)显著拓宽至可挠基板(如pet、聚合物、塑料、纸及甚至织物)。可接着改良经转移基板的机械特性。因此,al2o3薄膜自刚性基板转移至可挠基板可避开此可挠基板的熔融温度常常较低的问题。技术实现要素:根据本发明的第一态样,提供一种将较硬薄膜基板层转移至较软可挠基板上的方法。详言的,本发明提供一种将蓝宝石薄膜层转移至较软可挠基板(例如pet、聚合物、塑料、纸及甚至织物)上的方法。此组合与纯蓝宝石基板相比较佳。根据本发明的第二态样,提供一种将蓝宝石(al2o3)涂覆于可挠基板上的方法,其包含:将至少一个第一薄膜沉积于至少一个第一基板上以形成至少一个经第一薄膜涂覆的基板的至少一个第一沉积过程;将至少一个第二薄膜沉积于至少一个经第一薄膜涂覆的基板上以形成至少一个经第二薄膜涂覆的基板的至少一个第二沉积过程;将至少一种催化剂沉积于至少一个经第二薄膜涂覆的基板上以形成至少一个经催化剂涂覆的基板的至少一个第三沉积过程;将至少一个蓝宝石(al2o3)薄膜沉积于至少一个经催化剂涂覆的基板上以形成至少一个经蓝宝石(al2o3)涂覆的基板的至少一个第四沉积过程;至少一个退火过程,其中所述至少一个经蓝宝石(al2o3)涂覆的基板在范围介于300℃至低于蓝宝石(al2o3)熔点的退火温度下退火有效持续时间以形成至少一个经硬化蓝宝石(al2o3)薄膜涂覆的基板;将至少一个可挠基板附接于至少一个蓝宝石(al2o3)薄膜上的至少一个经硬化蓝宝石(al2o3)薄膜涂覆的基板;至少一个机械分离过程,使至少一个硬化蓝宝石(al2o3)薄膜连同至少一个第二薄膜与至少一个经第一薄膜涂覆的基板分离以在所述至少一个可挠基板上形成至少一个经第二薄膜涂覆的硬化蓝宝石(al2o3)薄膜;以及至少一个蚀刻过程,自于所述至少一个可挠基板上的至少一个经第二薄膜涂覆的硬化蓝宝石(al2o3)薄膜移除至少一个第二薄膜以形成至少一个经蓝宝石(al2o3)薄膜涂覆的可挠基板。优选地,其中所述第一及/或所述可挠基板包含至少一种莫氏值低于所述沉积的至少一个蓝宝石(al2o3)薄膜的材料。在本发明第二态样的第一具体实例中,提供所述方法,其中所述至少一个第一及/或第二及/或第三及/或第四沉积过程包含电子束沉积及/或溅射沉积。在本发明第二态样的第二具体实例中,提供所述方法,其中所述至少一个经蓝宝石(al2o3)涂覆的基板及/或至少一个经硬化蓝宝石(al2o3)涂覆的基板及/或在所述至少一个可挠基板上的至少一个经第二薄膜涂覆的硬化蓝宝石(al2o3)薄膜及/或至少一个经蓝宝石(al2o3)薄膜涂覆的可挠基板包含至少一个蓝宝石(al2o3)薄膜。在本发明第二态样的第三具体实例中,提供所述方法,其中所述至少一个第一基板及/或所述至少一个可挠基板的厚度比所述至少一个蓝宝石(al2o3)薄膜的厚度大一或多个数量级。在本发明第二态样的第四具体实例中,提供所述方法,其中所述至少一个蓝宝石(al2o3)薄膜的厚度为所述至少一个第一基板及/或所述至少一个可挠基板的厚度的约1/1000。在本发明第二态样的第五具体实例中,提供所述方法,其中所述至少一个蓝宝石(al2o3)薄膜的厚度在150nm与600nm的间。在本发明第二态样的第六具体实例中,提供所述方法,其中所述有效持续时间不少于30分钟。在本发明第二态样的第八具体实例中,提供所述方法,其中所述有效持续时间不超过2小时。在本发明第二态样的第九具体实例中,提供所述方法,其中所述退火温度范围介于850℃至1300℃的间。在本发明第二态样的第十具体实例中,提供所述方法,其中所述退火温度范围介于1150℃至1300℃的间。在本发明第二态样的第十一具体实例中,提供所述方法,其中所述至少一种材料包含石英、熔融硅石、硅、玻璃、钢化玻璃、pet、聚合物、塑料、纸及/或织物,另外其中用于至少一个可挠基板的所述材料不可藉由至少一个蚀刻过程蚀刻。在本发明第二态样的第十二具体实例中,提供所述方法,其中所述至少一个可挠基板与所述至少一个硬化蓝宝石(al2o3)薄膜的间的所述附接比所述至少一个第一薄膜与所述第二薄膜的间的黏结强。在本发明第二态样的第十三具体实例中,提供所述方法,其中所述至少一个第一薄膜包含铬(cr)或在所述至少一个第一薄膜与所述至少一个第二薄膜的间形成较弱黏结的任何材料,另外其中用于第一薄膜的所述材料不可藉由至少一个蚀刻过程蚀刻。在本发明第二态样的第十四具体实例中,提供所述方法,其中所述至少一个第二薄膜包含银(ag)或在所述至少一个第一薄膜与所述至少一个第二薄膜的间形成较弱黏结的任何材料,另外其中用于第二薄膜的所述材料不可藉由至少一个蚀刻过程蚀刻。在本发明第二态样的第十五具体实例中,提供所述方法,其中所述至少一种催化剂包含选自由以下组成的群的金属:钛(ti)、铬(cr)、镍(ni)、硅(si)、银(ag)、金(au)、锗(ge)及熔点高于所述至少一个第一基板的金属。在本发明第二态样的第十六具体实例中,提供所述方法,其中所述至少一个经催化剂涂覆的基板包含至少一个催化剂膜;其中所述至少一个催化剂膜为不连续的;其中所述至少一个催化剂膜的厚度范围介于1nm至15nm的间;以及其中所述至少一个催化剂膜包含直径范围介于5nm至20nm的间的奈米点。熟习此项技术者应了解,本文所述的本发明除特定描述的彼等内容外允许进行变化及修改。本发明包括全部此类变化及修改。本发明亦包括本说明书中单独或共同提及或指示的所有步骤及特征,以及所述等步骤或特征中的任两者或两者以上的任何及所有组合。本发明的其他态样及优势将由随后说明书的综述而对熟习此项技术者显而易见。附图说明当结合附图时,本发明的以上及其他目标及特征将由以下本发明的描述而变得显而易见,其中:图1展示莫氏矿物硬度表;图2展示当与普通玻璃、gorilla玻璃、石英及纯蓝宝石相比时,「石英上的蓝宝石薄膜」的顶部表面硬度;图3展示石英、石英上的蓝宝石薄膜及纯蓝宝石的透光率;图4展示石英及在1300℃下退火2小时及未退火的石英上的190nm蓝宝石薄膜的透光率;图5展示在750℃、850℃及1200℃下退火2小时的石英上的400nm蓝宝石薄膜的xrd结果;图6展示与石英及蓝宝石基板相比,在1200℃下退火2小时及未退火的石英上的400nm蓝宝石薄膜的电子束透射光谱;图7展示与石英及蓝宝石基板相比,在1150℃下退火2小时及未退火的熔融硅石上的160nm蓝宝石薄膜的电子束透射光谱;图8a展示藉由溅射沉积及在850℃、1050℃及1200℃下退火2小时所制备的石英上的400nm蓝宝石薄膜的xrd结果;图8b展示藉由溅射沉积及在1150℃下退火2小时所制备的石英上的厚度为220nm、400nm及470nm的蓝宝石薄膜的xrd结果;图9展示与石英基板相比,藉由溅射沉积及在1100℃下退火2小时所制备的石英上的220nm、400nm及470nm蓝宝石薄膜的透射光谱;图10展示藉由溅射沉积及在750℃、850℃、1050℃及1150℃下退火2小时所制备的熔融硅石上的350nm蓝宝石薄膜的xrd结果;图11展示与熔融硅石基板相比,藉由溅射沉积及在1150℃下退火2小时所制备的熔融硅石上的180nm-600nm蓝宝石薄膜的透射光谱;图12展示熔融硅石及熔融硅石上250nm经退火蓝宝石薄膜的透射率,所述熔融硅石上250nm经退火蓝宝石薄膜有或无10nmti催化剂且在700℃及1150℃下退火2小时;图13(a)展示不同样品在不同退火条件下的x射线反射(xrr)量测结果。图13(b)展示不同样品在不同退火条件下的光学透射光谱;图14(a)至14(e)展示吸收体超颖材料制造中的ebl步骤,其中圆盘数组的间距为600nm,圆盘直径:365nm,金厚度:50nm且cr厚度:30nm;图14(f)展示二维金圆盘数组吸收体超颖材料的扫描电子显微镜(sem)图像;图15(a)至15(e)展示覆晶转移法的示意图,将面积为500μm乘500μm的三层吸收体超颖材料转移至pet可挠基板;图16(a)及16(b)展示透明pet基板上的可挠性nir吸收体超颖材料;每一分隔图案的面积尺寸为500μm乘500μm;图17展示石英基板上的吸收体超颖材料(金圆盘/ito/金/cr/石英)的相对反射光谱,nir光通常聚焦于装置且藉由15×接物镜收集反射信号,蓝线为实验结果且红线为使用rcwa方法的模拟反射光谱;图18(a)至18(d)展示:(a)在可挠性超颖材料(具有曲面)上量测的角度解析背反射光谱,光自pet侧入射且藉由nir侦测器收集背反射;(b)在可挠性吸收体超颖材料上量测的透射光谱,自pet侧收集自pmma侧入射的光;以及(c)及(d)为使用rcwa方法在可挠性吸收体超颖材料上模拟的反射及透射光谱;以及图19展示在不同弯曲条件下量测超颖材料装置的反射光谱的实验图示;可挠基板藉由调节a与b的间的距离而弯曲且入射角(自0度变化至45度)藉由pet基板的斜率及入射光方向来界定;图20展示用于al2o3薄膜转移的制造结构;图21展示al2o3薄膜自供体基板剥离;图22展示蚀刻牺牲ag层以完成al2o3薄膜转移至pet基板;图23展示备用于薄膜转移的al2o3总成的制造样品;图24展示al2o3自供体基板分离。具体实施方式本发明不受本文所述的特定具体实例中的任一者限制于范畴内。呈现以下具体实例仅用于例示。在不希望受理论束缚的情况下,本发明者已经由其试验发现实现将较硬薄膜基板层转移至较软可挠基板(例如pet、聚合物、塑料、纸及甚至织物)上的任务的实验及研究。此组合与纯蓝宝石基板相比较佳。实际上,材料愈硬,其愈脆,因此,蓝宝石基板很难擦伤,但其容易碎裂且反过来亦常常如此,其中石英基板与蓝宝石基板相比较易于擦伤,但其脆性较小。因此,将较硬薄膜基板沉积于较软可挠基板上两全其美。较软可挠基板脆性较小,具有良好机械效能且成本较低。藉由使用较硬薄膜基板将实现防擦伤功能。对于蓝宝石(al2o3)薄膜沉积的硬化,较软基板的软化/熔融温度应充分高于退火温度。大多数刚性基板,诸如石英、熔融硅石可符合此要求。然而,可挠基板,诸如聚对苯二甲酸乙二酯(pet)将无法符合所述要求。pet的熔融温度为约250℃,远低于退火温度。pet为最广泛使用的可挠基板中的一者。将al2o3(蓝宝石)薄膜基板转移至较软可挠基板上的能力将使其应用自刚性基板(如玻璃及金属)显著拓宽至可挠基板(如pet、聚合物、塑料、纸及甚至织物)。可接着改良经转移基板的机械特性。因此,al2o3薄膜自刚性基板转移至可挠基板可避开此可挠基板的熔融温度常常较低的问题。根据本发明的第一态样,提供一种将较硬薄膜基板层涂覆/沉积/转移至较软基板上的方法。详言的,本发明提供一种将蓝宝石薄膜层沉积于较软可挠基板(例如pet、聚合物、塑料、纸及织物)上的方法。此组合与纯蓝宝石基板相比较佳。根据本发明的第二态样,提供一种将蓝宝石(al2o3)涂覆于可挠基板上的方法,其包含:将至少一个第一薄膜沉积于至少一个第一基板上以形成至少一个经第一薄膜涂覆的基板的至少一个第一沉积过程;将至少一个第二薄膜沉积于至少一个经第一薄膜涂覆的基板上以形成至少一个经第二薄膜涂覆的基板的至少一个第二沉积过程;将至少一种催化剂沉积于至少一个经第二薄膜涂覆的基板上以形成至少一个经催化剂涂覆的基板的至少一个第三沉积过程;将至少一个蓝宝石(al2o3)薄膜沉积于至少一个经催化剂涂覆的基板上以形成至少一个经蓝宝石(al2o3)涂覆的基板的至少一个第四沉积过程;至少一个退火过程,其中所述至少一个经蓝宝石(al2o3)涂覆的基板在范围介于300℃至低于蓝宝石(al2o3)熔点的退火温度下退火有效持续时间以形成至少一个经硬化蓝宝石(al2o3)薄膜涂覆的基板;将至少一个可挠基板附接于至少一个蓝宝石(al2o3)薄膜上的至少一个经硬化蓝宝石(al2o3)薄膜涂覆的基板;至少一个机械分离过程,使至少一个硬化蓝宝石(al2o3)薄膜连同至少一个第二薄膜与至少一个经第一薄膜涂覆的基板分离以在所述至少一个可挠基板上形成至少一个经第二薄膜涂覆的硬化蓝宝石(al2o3)薄膜;以及至少一个蚀刻过程,自于所述至少一个可挠基板上的至少一个经第二薄膜涂覆的硬化蓝宝石(al2o3)薄膜移除至少一个第二薄膜以形成至少一个经蓝宝石(al2o3)薄膜涂覆的可挠基板。优选地,其中所述第一及/或所述可挠基板包含至少一种莫氏值低于所述沉积的至少一个蓝宝石(al2o3)薄膜的材料。在本发明第二态样的第一具体实例中,提供所述方法,其中所述至少一个第一及/或第二及/或第三及/或第四沉积过程包含电子束沉积及/或溅射沉积。在本发明第二态样的第二具体实例中,提供所述方法,其中所述至少一个经蓝宝石(al2o3)涂覆的基板及/或至少一个经硬化蓝宝石(al2o3)涂覆的基板及/或在所述至少一个可挠基板上的至少一个经第二薄膜涂覆的硬化蓝宝石(al2o3)薄膜及/或至少一个经蓝宝石(al2o3)薄膜涂覆的可挠基板包含至少一个蓝宝石(al2o3)薄膜。在本发明第二态样的第三具体实例中,提供所述方法,其中所述至少一个第一基板及/或所述至少一个可挠基板的厚度比所述至少一个蓝宝石(al2o3)薄膜的厚度大一或多个数量级。在本发明第二态样的第四具体实例中,提供所述方法,其中所述至少一个蓝宝石(al2o3)薄膜的厚度为所述至少一个第一基板及/或所述至少一个可挠基板的厚度的约1/1000。在本发明第二态样的第五具体实例中,提供所述方法,其中所述至少一个蓝宝石(al2o3)薄膜的厚度在150nm与600nm的间。在本发明第二态样的第六具体实例中,提供所述方法,其中所述有效持续时间不少于30分钟。在本发明第二态样的第八具体实例中,提供所述方法,其中所述有效持续时间不超过2小时。在本发明第二态样的第九具体实例中,提供所述方法,其中所述退火温度范围介于850℃至1300℃的间。在本发明第二态样的第十具体实例中,提供所述方法,其中所述退火温度范围介于1150℃至1300℃的间。在本发明第二态样的第十一具体实例中,提供所述方法,其中所述至少一种材料包含石英、熔融硅石、硅、玻璃、钢化玻璃、pet、聚合物、塑料、纸及/或织物,另外其中用于至少一个可挠基板的所述材料不可藉由至少一个蚀刻过程蚀刻。在本发明第二态样的第十二具体实例中,提供所述方法,其中所述至少一个可挠基板与所述至少一个硬化蓝宝石(al2o3)薄膜的间的所述附接比所述至少一个第一薄膜与所述第二薄膜的间的黏结强。在本发明第二态样的第十三具体实例中,提供所述方法,其中所述至少一个第一薄膜包含铬(cr)或在所述至少一个第一薄膜与所述至少一个第二薄膜的间形成较弱黏结的任何材料,另外其中用于第一薄膜的所述材料不可藉由至少一个蚀刻过程蚀刻。在本发明第二态样的第十四具体实例中,提供所述方法,其中所述至少一个第二薄膜包含银(ag)或在所述至少一个第一薄膜与所述至少一个第二薄膜的间形成较弱黏结的任何材料,另外其中用于第二薄膜的所述材料不可藉由至少一个蚀刻过程蚀刻。在本发明第二态样的第十五具体实例中,提供所述方法,其中所述至少一种催化剂包含选自由以下组成的群的金属:钛(ti)、铬(cr)、镍(ni)、硅(si)、银(ag)、金(au)、锗(ge)及熔点高于所述至少一个第一基板的金属。在本发明第二态样的第十六具体实例中,提供所述方法,其中所述至少一个经催化剂涂覆的基板包含至少一个催化剂膜;其中所述至少一个催化剂膜为不连续的;其中所述至少一个催化剂膜的厚度范围介于1nm至15nm的间;以及其中所述至少一个催化剂膜包含直径范围介于5nm与20nm的间的奈米点。定义:出于明晰及完整性的目的,以下术语的定义用于本发明:词语「蓝宝石(sapphire)」当在本文中使用时系指亦称为矿物刚玉宝石品种、氧化铝(α-al2o3)或矾土的材料或基板,包括在所述材料或基板中具有不同杂质的彼等材料或基板。纯刚玉(氧化铝)为无色的,或具有~0.01%钛的刚玉。由不同化学杂质或微量元素的存在引起的各种蓝宝石颜色为:.蓝色蓝宝石通常因痕量铁及钛(仅0.01%)而有颜色。.铁及铬的组合产生黄色或橙色蓝宝石。.铬单独产生粉红色或红色(红宝石);至少1%铬产生深红色红宝石。.铁单独产生淡黄色或绿色。.紫色蓝宝石因钒而有颜色。词语「较硬(harder)」当在本文中使用时系指材料在与另一种材料相比时的相对硬度量度。出于明晰的目的,当第一材料或基板定义为与第二材料或基板相比较硬时,第一材料或基板的莫氏值将高于第二材料或基板的莫氏值。词语「较软(softer)」当在本文中使用时系指材料在与另一种材料相比时的相对硬度量度。出于明晰的目的,当第一材料或基板定义为与第二材料或基板相比较软时,第一材料或基板的莫氏值将低于第二材料或基板的莫氏值。词语「可挠(flexible)」当在本文中使用时系指基板能够使用力进行物理操纵而在所述基板不断裂的情况下改变其物理形状的机械特性。词语「屏幕(screen)」当在本文中用作名词时系指设备的覆盖玻璃/覆盖屏幕/覆盖窗/显示屏幕/显示窗/覆盖表面/覆盖板。出于明晰的目的,虽然在许多情形中,给定设备上的屏幕具有显示设备界面及保护设备表面的双重功能,其中对于此类情形,良好的透光性为所述屏幕的所需特征;但此并非必须的。在仅需要提供表面保护功能的其他情形中,屏幕的透光性并非必须的。在本发明的一个具体实例中,提供一种研发透明屏幕的方法,所述屏幕与gorilla玻璃相比较硬且较佳且与纯蓝宝石屏幕相当,但具有以下优势:.比任何硬化玻璃更硬;.比纯蓝宝石屏幕断裂的可能性更小;.重量比纯蓝宝石屏幕更轻;.透明度比纯蓝宝石屏幕更高。在本发明的一个具体实例中,提供一种将蓝宝石薄膜沉积于石英基板上的方法。藉由沉积后处理(诸如热退火),本发明的一个具体实例已实现高达8-8.5mohs的顶部表面硬度,接近于9mohs的蓝宝石单晶硬度。本发明的一个具体实例在本文中称为「石英上的蓝宝石薄膜」。图2展示当与普通玻璃、gorilla玻璃、石英及纯蓝宝石相比时,「石英上的蓝宝石薄膜」的顶部表面硬度。石英基板自身为与玻璃相比具有较高莫氏值的单晶sio2。此外,其熔点为1610℃,可耐受高退火温度。此外,基板可切割成所需尺寸,本发明的一个具体实例可接着在上面沉积蓝宝石薄膜。经沉积蓝宝石薄膜的厚度恰好为石英基板的1/1000。合成石英晶体的成本相对较低(在本发明揭示于本文中时,其仅为us$10/kg以下)。因此,在本发明的一个具体实例中,制造成本及制造时间相比于纯蓝宝石基板的制造显著减少。本发明的一个具体实例的特征及益处比硬化玻璃更高的硬度在本发明的一个具体实例中,所研发的石英上的蓝宝石薄膜顶部表面硬度的最大值为8.5mohs。智能型手机屏幕中所用的最新gorilla玻璃的硬度值仅评分约6.5mohs,且天然石英基板的硬度值为7mohs。因此,本发明相比于最新技术具有显著提高的顶部表面硬度。石英上的蓝宝石薄膜的硬度值为8.5mohs,其非常接近于纯蓝宝石的硬度值9mohs,且石英上的蓝宝石薄膜具有制造成本较低的优点且需要较少制造时间。比蓝宝石碎片化更少、更轻实际上,材料愈硬,其愈脆,因此,蓝宝石基板很难擦伤,但其容易碎裂且反过来亦常常如此。石英具有相对低的弹性模数,使其远比蓝宝石更加耐冲击。此外,在本发明的一个具体实例中,经沉积蓝宝石薄膜与石英基板相比极薄,其中所述经沉积蓝宝石薄膜的厚度仅为石英基板的1/1000。因此,石英上的蓝宝石薄膜的整体重量几乎与石英基板相同,其仅为相同厚度纯蓝宝石基板重量的66.6%(或2/3)。此是因为石英的密度仅为2.65g/cm3,而蓝宝石的密度为3.98g/cm3且gorilla玻璃的密度为2.54g/cm3。换言的,石英基板仅比gorilla玻璃重4.3%,但纯蓝宝石基板大致为gorilla玻璃及石英的1.5倍重。表1展示石英、gorilla玻璃及纯蓝宝石的密度的比较。表1:gorilla玻璃、石英及纯蓝宝石的密度的比较及其百分比差异。材料密度差异gorilla玻璃2.54g/cm3100%石英2.65g/cm3104.3%纯蓝宝石3.98g/cm3156.7%由apple公司提交的新近公开的专利,亦即美国专利申请案第13/783,262号亦指出,其已设计一种使蓝宝石与玻璃层融合在一起产生蓝宝石迭层玻璃的方式以组合蓝宝石的耐用性与玻璃的重量及可挠性优势。然而,抛光较大面积(>6吋)及薄(<0.3mm)的蓝宝石基板极具挑战性。因此,在石英上使用蓝宝石薄膜为具有较轻重量、较高顶部表面硬度、较少碎片化基板的屏幕的最佳组合。比纯蓝宝石更高的透明度由于蓝宝石晶体、石英晶体及gorilla玻璃的折射率分别为1.76、1.54及1.5,故归因于菲涅尔反射损失(fresnel'sreflectionloss),其整体透光率为85%、91%及92%。此意味着在透光率与耐用性的间存在少量取舍。蓝宝石透射较少光,其可导致装置较暗或装置电池组寿命较短。当透射较多光时,则节省更多能量且装置电池组寿命将更长。图3展示石英、石英上的蓝宝石薄膜及纯蓝宝石的透光率。大多数晶体(包括蓝宝石及石英)均具有双折射问题。藉由比较其对正常射线及异常射线的折射率(n0及ne),差异δn的量值藉由双折射来定量。此外,本发明的一个具体实例的δn值亦较小,使得施用较薄基板厚度(~1mm)的双折射问题并不严重。举例而言,纯蓝宝石用作appleiphone5s的相机覆盖镜头,其未报导任何模糊影像。表2展示石英及蓝宝石对正常射线及异常射线的折射率(n0及ne)、其双折射差异δn。表2:石英及蓝宝石对正常射线及异常射线的折射率(n0及ne)、其差异δn比纯蓝宝石制造时间更短且制造成本更低近来,合成蓝宝石及石英单晶均为生长及市售的。由于蓝宝石的熔点高于石英,故蓝宝石的生长更加困难且成本较高。更重要的是,蓝宝石的生长时间比石英长得多。生长用于大于6吋产品的蓝宝石亦具有挑战性且仅有限数目的公司可实现。因此,其限制生产量,使得蓝宝石基板的生产成本高于石英。表3展示石英及蓝宝石的化学式、熔点及莫氏硬度值。表3:石英及蓝宝石的化学式、熔点及莫氏硬度值。材料化学式熔点莫氏硬度石英sio21610℃7蓝宝石al2o32040℃9纯蓝宝石使用中的另一难题为蓝宝石晶体的硬度值为9mohs,极其难以切割及抛光。迄今为止,抛光较大面积(>6吋)及薄(<0.3mm)的蓝宝石基板极具挑战性。尽管较大数目的蓝宝石晶体生长炉目前在操作中,但成功率不太高且此防止蓝宝石基板的价格降低太多。corning已声称蓝宝石屏幕的成本可高达gorilla玻璃的10倍。相比的下,石英的硬度值为7mohs且其易于切割及抛光。此外,合成石英晶体的成本相对便宜(在本发明时成本仅为us$10/kg以下)。因此,石英上的蓝宝石薄膜的额外成本为将蓝宝石薄膜沉积于石英基板上及石英上的蓝宝石薄膜的后处理。在本发明的一个具体实例中,当全部条件优化时,大批量生产方法可为快速的且成本低。在本发明的一个具体实例中,提供一种将较硬蓝宝石薄膜沉积于石英基板上的方法。薄膜厚度在150nm-1000nm范围内。藉由沉积后处理(诸如在500℃-1300℃下热退火),本发明的此具体实例已实现8-8.5mohs的硬度,其非常接近于9mohs的蓝宝石单晶硬度。在本发明的另一个具体实例中,提供厚度为150nm-500nm且实现8-8.5mohs的硬度值且亦具有低散射损失的良好光学效能的蓝宝石薄膜。退火温度为1150至1300℃,其非常接近于9mohs的蓝宝石单晶硬度。图4展示石英及在1300℃下退火2小时及未退火的石英上的190nm蓝宝石薄膜的透光率。因此,在硬度方面,石英上的蓝宝石薄膜与纯蓝宝石屏幕相当,且由于石英的密度仅为2.65g/cm3而蓝宝石的密度为3.98g/cm3,故其重量几乎与玻璃/石英基板相同,为纯蓝宝石基板重量的约66.6%。由于吾人可将基板切割成所需尺寸,接着沉积蓝宝石薄膜,故制造成本及时间与纯蓝宝石基板相比显著减少。实际上,藉由电子束沉积的蓝宝石薄膜的硬度值并不太高。在本发明的一个具体实例中,硬度值经量测低于7mohs。然而,在进行热退火过程后,薄膜硬度显著提高。本发明的一个具体实例已发现,蓝宝石薄膜在1300℃下退火2小时的时候软化。膜厚度收缩约10%且膜硬度提高至8-8.5mohs。由于石英基板为熔点为1610℃的单晶sio2,故其可耐受高退火温度。因此,石英基板上的经退火蓝宝石薄膜的硬度可达到8.5mohs。图4展示石英及在1300℃下退火2小时及未退火的石英上的190nm蓝宝石薄膜的透射率。此外,在本发明的其他具体实例中,蓝宝石薄膜的退火过程在其他基板上进行。举例而言,熔融硅石基板上的1000℃退火蓝宝石薄膜及玻璃基板上的500℃退火蓝宝石薄膜,量测其硬度。电子束及溅射沉积为将蓝宝石薄膜沉积于石英及其他相关基板上的两种最流行的方法。在本发明的具体实例中,使用此两种常见沉积法。藉由电子束沉积的蓝宝石薄膜关于藉由电子束沉积将蓝宝石薄膜沉积于给定基板上的概述点给定如下:.蓝宝石薄膜的沉积使用电子束蒸发,因为氧化铝具有在2040℃下的极高熔点。小尺寸纯氧化铝中的白色颗粒或无色晶体用作电子束蒸发源。高熔点的氧化铝亦使得退火温度可达至蓝宝石熔点以下(例如在大气压下的2040℃)。.基板垂直卡在远离蒸发源450mm的样品支架上。当发生沉积时,样品支架在1-2rpm下旋转。.蒸发室的基础真空低于5×10-6托且当发生沉积时,真空保持在1×10-5托以下。.沉积于基板上的膜的厚度为约150nm至1000nm。沉积速率为约在沉积期间基板无需外部冷却或加热。膜厚度藉由椭圆偏振测量法及/或扫描电子显微镜(sem)量测。.较高温度膜沉积可能自室温至1000℃。关于将蓝宝石薄膜电子束沉积于另一种基板上的过程的较详细描述给定如下:1)蓝宝石薄膜的沉积使用电子束蒸发,因为氧化铝具有在2040℃下的高熔点。氧化铝颗粒用作电子束蒸发源。高熔点的氧化铝亦使得退火温度可达至蓝宝石熔点以下(例如在大气压下的2040℃)。2)经涂覆的基板垂直卡在远离蒸发源450mm的样品支架上。当发生沉积时,样品支架在2rpm下旋转。3)沉积于基板上的膜的厚度为约190nm至1000nm。沉积速率为约在沉积期间基板无需外部冷却或加热。膜厚度藉由椭圆偏振测量法量测。4)在蓝宝石薄膜沉积于基板上后,其藉由500℃至1300℃的熔炉退火。温度升高速度为5℃/min且降低速度为1℃/min。时间介于30分钟至2小时,同时保持在特定热退火温度下。5)沉积基板包括石英、熔融硅石及(钢化)玻璃。其熔点分别为1610℃、1140℃及550℃。上面涂覆的蓝宝石薄膜的退火温度分别为1300℃、1000℃及500℃。6)石英及在1300℃下退火2小时及未退火的石英上的190nm蓝宝石薄膜的透射率展示于图4中。在400nm-700nm完整可见区中的透光率百分比大于86.7%且在550nm下为最大91.5%,而对于纯蓝宝石基板,透光率百分比仅为85-86%。透射愈多光表明自显示面板的背光源节省愈多能量,因此使得装置电池组寿命愈长。本发明的一个具体实例的退火过程在蓝宝石薄膜沉积于基板上后,其在500℃至1300℃的熔炉中退火。温度升高速率为5℃/min且降低速率为1℃/min。退火时间为30分钟至2小时,同时维持在特定热退火温度下。在上述范围内使用不同温度的多步骤退火亦用于增强硬度且亦减少薄膜的微裂。表4展示藉由电子束沉积制备在不同退火温度下的表面硬度及xrd特征峰。所述表亦展示膜中存在的各种蓝宝石结晶相;最常见相为α、θ及δ。表4:藉由电子束沉积制备在不同退火温度下的表面硬度及xrd特征峰。表4展示蓝宝石薄膜的表面硬度随在500℃至1300℃范围内变化的退火温度而变化。实际上,未退火的电子束沉积的蓝宝石薄膜的初始硬度值为约5.5mohs。然而,在进行热退火过程后,膜硬度显著提高。对于在500℃-850℃、850℃-1150℃及1150℃-1300℃范围内的退火温度,石英上的蓝宝石薄膜的硬度值分别为硬度表中的6-7mohs、7-8mohs及8-8.5mohs。图5展示在750℃、850℃及1200℃下退火2小时的石英上的400nm蓝宝石薄膜的xrd结果。当退火温度大于850℃时,膜开始部分结晶。新xrd峰的出现对应于氧化铝θ及δ结构相的混合。当在1300℃以上退火时,膜将开始出现一些可显著散射可见光的较大微晶;此将减小透射强度。此外,随着此较大微晶积聚愈来愈多,膜将开裂且一些微尺寸块将自基板分离。在本发明的一个具体实例中,发现石英基板上的蓝宝石薄膜可在1150℃至1300℃下在半小时至两小时内退火。膜厚度将收缩约10%且膜硬度提高至8-8.5mohs。由于石英基板为熔点为1610℃的单晶sio2,故其可耐受如此高的退火温度。在此退火温度下,石英基板上的经退火蓝宝石薄膜的硬度已达到8.5mohs。在1200℃下退火2小时及未退火的石英上的400nm蓝宝石薄膜的透光率展示于图6中,同时与石英及蓝宝石基板相比。石英上的蓝宝石薄膜在400-700nm可见区内的透光率大于88%且在550nm下达到最大92%。干涉图案归因于材料折射率及膜厚度的差异。整体平均透光率为约90%,而纯蓝宝石基板仅为85-86%。此外,在某些波长下,石英上的蓝宝石薄膜的光透射光谱与石英基板一致,表明光学效能极好且散射损失低。干涉图案最大强度与最小强度的间的差异仅为约4%。对于实际应用,透射愈多光表明自显示面板的背光源节省愈多能量,因此使得装置电池组寿命愈长。石英上的蓝宝石薄膜的厚度已测试厚度在150-1000nm范围内的石英上的蓝宝石薄膜。在本发明的一个具体实例中,当退火温度为1150℃至1300℃时,仅提供厚度为150nm-500nm的具有良好光学效能及低散射损失的蓝宝石薄膜。然而,当厚度大于600nm时,膜将开裂,引起显著散射,降低透射强度。对于沉积于石英上的厚度为150nm-500nm的蓝宝石薄膜,在1150℃至1300℃下退火后,全部量测硬度可达到莫氏硬度表中的8-8.5,其表明甚至更薄的涂覆膜亦可充当防擦伤层。其他可能用于防擦伤涂覆的基板除石英基板的外,本发明的其他具体实例亦已研究蓝宝石薄膜在诸如熔融硅石及硅的不同基板上的沉积。具有较高退火或熔融温度、可在30分钟至2小时内耐受850℃退火温度的其他回火玻璃或透明陶瓷基板亦可能用作基板,以增强其表面硬度达到莫氏硬度表中的7-8。举例而言,schottnextrema透明陶瓷具有在925℃下的短加热温度;corninggorilla玻璃的软化温度达至850℃。由于熔融硅石的退火温度为约1160℃,故其为开始研究其作为基板的适合性的良好候选物。然而,熔融硅石上的蓝宝石薄膜与石英上的蓝宝石薄膜相比展示自850℃至1150℃退火的不同行为,尽管其在相同沉积条件下沉积。蓝宝石膜在熔融硅石上的黏着性不如在石英上的良好(或归因于膨胀系数的显著差异),在熔融硅石基板上出现膜的局部分层及微尺寸开裂。然而,使用更薄的膜,可引起光散射的此等问题得到极大改良。图7展示在1150℃下退火2小时的熔融硅石上的160nm蓝宝石薄膜的透射率。熔融硅石上的蓝宝石薄膜在400nm-700nm完整可见区中的透射率大于88.5%且在470nm下达到最大91.5%。整体平均透光率百分比为约90%,而纯蓝宝石基板仅为85%-86%。此外,经量测的表面硬度亦保持在莫氏硬度表中的8以上。熔融温度在约1410℃下的硅为作为基板的不透明基板。在相同沉积条件下,硅上的蓝宝石膜展示与石英基板相比类似的莫氏硬度特征,其亦划分成两组温度范围。然而,硅并非透明基板,因此其无法用作透明覆盖玻璃或窗应用。因此,蓝宝石膜可作为保护层仅提供防擦伤目的,以保护硅表面免于擦伤(硅的莫氏硬度表硬度为7)。此类保护层可潜在消除厚玻璃囊封。此将提高光吸收,因此增加集光效率。其他可耐受高温处理的基于无机半导体的太阳能电池亦可在上面具有类似蓝宝石薄膜沉积。根据如本文所述的本发明的具体实例,据设想,熟习此项技术者可非常充分地应用本发明以将蓝宝石薄膜沉积于其他基板上,使得蓝宝石薄膜将充当其下方基板的防擦伤保护层,其限制条件为此等基板可耐受本发明的退火温度适用的持续时间。藉由溅射沉积的经退火蓝宝石薄膜藉由溅射沉积的蓝宝石薄膜关于藉由溅射沉积将蓝宝石薄膜沉积于给定基板上的步骤给定如下:1)蓝宝石薄膜的沉积可使用铝或氧化铝目标藉由溅射沉积来进行。2)将基板附接于远离目标约95mm的样品支架上。当发生沉积时,使样品支架旋转以实现厚度均一性,例示性速率为10rpm。3)蒸发室的基础真空低于3×10-6毫巴且涂覆压力为约3×10-3毫巴。4)沉积于基板上的膜的厚度为约150nm至600nm。5)较高温度膜沉积可能自室温至500℃。本发明的另一个具体实例的退火过程在蓝宝石薄膜沉积于基板上后,其藉由500℃至1300℃的熔炉退火。温度升高速率为5℃/min且降低速率为1℃/min。时间介于30分钟至2小时,同时维持在特定热退火温度下。在不同温度下的多步骤退火亦用于增强硬度且亦减少薄膜的微裂。此展示于表5中。表5:藉由溅射沉积制备的石英上的蓝宝石膜在不同退火温度下的表面硬度及xrd特征峰。表5展示石英上的蓝宝石薄膜的表面硬度随着在500℃至1300℃范围内变化的退火温度而变化。实际上,藉由溅射沉积、未退火的蓝宝石薄膜的初始硬度值略微高于藉由电子束沉积;约6-6.5mohs。在进行热退火过程后,膜硬度的效能不同于藉由电子束沉积。当退火温度在500℃-850℃范围内时,膜硬度无显著变化。对于850℃-1150℃范围,涂覆于石英上的薄膜易于剥离。然而,在1150℃-1300℃范围中,膜形成硬膜,其表面硬度为150nm-300nm厚度的8-8.5mohs及300nm-500nm厚度的8.5-8.8mohs。图8a展示在850℃、1050℃及1200℃下退火2小时的石英上的400nm蓝宝石薄膜的xrd结果。出现xrd峰相当于氧化铝的θ、δ及α结构相的混合。不同于电子束蒸发,溅射沉积的xrd结果中出现氧化铝的α相使得表面硬度更加硬化,平均评分8.7mohs。而图8b展示在1150℃下退火2小时的石英上的厚度为220nm、400nm及470nm的蓝宝石薄膜的xrd结果。α相的出现始于约300nm且当蓝宝石薄膜的厚度增加至470nm时,原始混合的结构相几乎均转化成α相。表面硬度为在此类条件下最硬的。然而,进一步增加蓝宝石薄膜的厚度将使得膜分层。藉由溅射沉积制备的在1100℃下退火2小时的石英上的220nm、400nm及470nm蓝宝石薄膜的光透射光谱展示于图9中,同时与石英基板相比。对于石英上的经退火220nm蓝宝石薄膜,光学效能为极好的且几乎无散射损失。在400nm-700nm完整可见区中的透射率大于87%且在520nm下达到最大91.5%。整体平均透射率为约90.2%。干涉图案最大强度与最小强度的间的差异仅为约4.5%。然而,当蓝宝石薄膜的厚度大于300nm时,透光强度开始下降,尤其在uv范围中,表明瑞利散射(rayleighscattering)开始占主导。瑞利散射的强波长相依性适用于粒度低于1/10波长的散射粒子。此归因于结晶尺寸小于100nm的蓝宝石薄膜中α相的形成。因此,表面硬度变得更硬,但透射率变得更糟。对于石英上的经退火400nm及470nm蓝宝石薄膜,400nm-700nm完整可见区中的透光率百分比分别在81%-88%及78%-87%内。其整体平均透射率值分别为约85.7%及83.0%。然而,当蓝宝石薄膜的厚度大于500nm时,较大微晶积聚,使得微裂形成,膜将开裂且一些微尺寸块将与基板分离。藉由溅射沉积的熔融硅石上的蓝宝石薄膜除石英基板的外,低成本熔融硅石为经蓝宝石薄膜涂覆的基板的可能候选物,因为熔融硅石的退火温度为约1160℃。表6展示随着退火温度在750℃至1150℃范围内变化,熔融硅石上的蓝宝石薄膜的表面硬度。实际上,藉由溅射沉积且未退火的熔融硅石上的蓝宝石薄膜的初始硬度值略低于石英上的蓝宝石薄膜的初始硬度值;约5.5-6mohs。对于850℃-1150℃范围,全部150nm-600nm蓝宝石薄膜的硬度甚至更糟,低于5mohs。然而,在1150℃下,对于全部150nm-600nm蓝宝石薄膜,膜可再次形成硬膜,其表面硬度为8-8.5。表6:藉由溅射沉积制备的熔融硅石上的蓝宝石膜在不同退火温度下的表面硬度及xrd特征峰。图10展示藉由溅射沉积及在750℃、850℃、1050℃及1150℃下退火2小时所制备的熔融硅石上的350nm蓝宝石薄膜的xrd结果。xrd结果展示氧化铝的混合的θ及α结构相共存于熔融硅石基板上。因此,蓝宝石薄膜具有8-8.5mohs的硬表面,而熔融硅石基板仅评分5.3-6.5。与熔融硅石基板相比,藉由溅射沉积、在1150℃下退火2小时所制备的熔融硅石上的180nm-600nm蓝宝石薄膜的透射光谱展示于图11中。对于熔融硅石上的经退火180nm及250nm蓝宝石薄膜,光学效能极好且几乎无散射损失。蓝宝石薄膜在400-700nm完整可见区中的透射率分别在88.9%-93.1%及84.8%-92.8%内。其整体平均透射率值分别为约91.3%及90.7%。对于熔融硅石上的经退火340nm及600nm厚的蓝宝石薄膜,跨越400nm-700nm可见区的透射率分别在75%-86%及64%-80%内。其整体平均透射率分别为约81.7%及74.1%。因此,在1150℃下退火的厚度为150nm-300nm的熔融硅石上的蓝宝石薄膜具有良好的光学效能及约91%透射率,且亦具有>8mohs的强表面硬度。低温退火过程目前流行的『钢化』屏幕材料使用来自corning的gorilla玻璃,其用于超过15亿装置。在莫氏硬度表上,最新gorilla玻璃仅评分6.5-6.8,其低于矿物石英,使其仍容易被砂擦伤。因此,存在将较硬薄膜沉积于玻璃基板上的另一方向。然而,对于大多数常用覆盖玻璃,其所允许的最大退火温度仅在600℃-700℃范围内。在此温度范围内,先前经退火蓝宝石薄膜的硬度仅可达到6-7mohs,接近于玻璃基板自身的硬度。因此,研发一种新技术以使用700℃以下的温度而促使经退火蓝宝石薄膜的莫氏硬度超过7。在吾等本发明的另一个具体实例中,吾等可将一层或多层较高硬度蓝宝石薄膜沉积于所允许的最大退火温度低于850℃的较低硬度基板(例如gorilla玻璃、钢化玻璃、钠钙玻璃等)上。因此,可将较硬防擦伤薄膜涂覆于玻璃上。此为提高其表面硬度的最快捷且成本较低的方式。在吾等本发明的又一个具体实例中,藉由施用诸如ti及ag的金属的奈米层,吾等已展示多晶蓝宝石薄膜可在较低温度下生长。此催化性增强可在显著低于不使用奈米金属催化剂时的温度下诱发。增强来自一旦存在足以使得经沉积原子可聚集的动能而使得结晶能够建立,且此退火温度可始于300℃。低温退火始于300℃的本发明的具体实例呈现于表7中。表7:基板/ti催化剂/蓝宝石膜的结构在未退火(室温)、300℃、400℃及500℃退火温度下的具体实例。图13(a)展示按照表7中的具体实例,不同样品在不同退火条件下的x射线反射(xrr)量测结果,而13(b)展示按照表7中的具体实例,不同样品在不同退火条件下的光学透射光谱。在一个具体实例中,吾等研发一种将极薄『不连续』金属催化剂及较厚蓝宝石膜沉积于玻璃基板上的方法。藉由沉积后处理,诸如在600-700℃下热退火,吾等已实现7-7.5mohs的硬度,其高于大多数玻璃的硬度。藉由诸如电子束蒸发或溅射的沉积系统沉积的奈米金属催化剂的厚度应在1-15nm的间。此催化剂并非连续膜,如由sem所示。经沉积金属可具有(5-20nm)直径的奈米点(nd)形状。金属包含钛(ti)及银(ag)。较厚蓝宝石膜在100-1000nm范围内。实际上,藉由电子束或溅射沉积的蓝宝石薄膜的硬度值并不太高。吾等已量测硬度,其仅为约5.5-6mohs。然而,在热退火过程后,膜硬度显著提高。在无奈米金属催化剂的情况下,在退火温度600-850℃下的膜硬度为6-7mohs。在添加奈米金属催化剂后,在退火温度600-700℃下的膜硬度已提高至7-7.5mohs且在退火温度701-1300℃下实现8.5至9mohs的硬度。此极大提高玻璃基板上的表面硬度且详言的,其在低于玻璃软化温度的此退火温度下。此意味着玻璃将不会在退火期间变形。因此,金属催化剂的作用不仅增强蓝宝石薄膜与玻璃基板的间的黏着性,而且诱发蓝宝石薄膜的硬化。藉由电子束沉积制备的具有及不具有奈米金属催化剂的蓝宝石薄膜在不同退火范围内的表面硬度展示于表8中。表8:藉由电子束沉积制备的具有及不具有奈米金属催化剂的蓝宝石薄膜在不同退火范围内的表面硬度。关于藉由电子束沉积将蓝宝石薄膜沉积于玻璃基板上的概述点给定如下:1)蒸发室的基础真空低于5×10-6托且当发生沉积时,沉积真空保持在1×10-5托以下。2)将基板附接于距离蒸发源例如450mm的样品支架上。当发生沉积时,样品支架在1-2rpm下旋转。3)使用诸如电子束蒸发及溅射的沉积系统沉积具有较高熔点的奈米金属,诸如ti、cr、ni、si、ag、au、ge等。藉由qcm传感器监测,直接沉积于基板上的金属催化剂的厚度为约1-15nm。奈米金属催化剂的沉积速率为约在沉积期间基板无需外部冷却或加热。膜形态藉由sem俯视图及截面视图量测。4)使用电子束蒸发沉积蓝宝石薄膜,因为其具有在2040℃下的极高熔点。小尺寸纯氧化铝中的白色颗粒或无色晶体用作电子束蒸发源。高熔点的氧化铝亦使得退火温度可达至蓝宝石熔点以下(例如在大气压下的2040℃)。5)沉积于基板上的蓝宝石薄膜的厚度为约100nm至1000nm。沉积速率为约基板在沉积期间处于室温下且活性温度并非必需的。膜厚度可藉由椭圆偏振测量法或具有类似或更佳精确性的其他适当方法量测。6)在蓝宝石薄膜沉积于基板上后,其在500℃至1300℃的熔炉中退火。温度升高梯度应为逐渐的(例如5℃/min)且降低梯度亦应为逐渐的(例如1-5℃/min)。在指定热退火温度范围内的退火时间介于30分钟至10小时。在上述范围内使用不同温度的多步骤退火亦可用于增强硬度且亦减少薄膜的微裂。图12展示熔融硅石及熔融硅石上250nm经退火蓝宝石薄膜的透射率,所述熔融硅石上250nm经退火蓝宝石薄膜有或无10nmti催化剂且在700℃及1150℃下退火2小时。对于700℃退火结果,在400-700nm可见区中的平均透射率百分比大于89.5%且在462nm下达到最大93.5%,而熔融硅石基板的平均透射率为93.5%。薄膜转移过程在本发明的另一个具体实例中,提供一种可使用覆晶转移(fct)技术制造多层可挠性超颖材料的方法及制造设备。此类超颖材料包括转移至较软可挠基板上的薄膜较硬基板。此技术不同于诸如将奈米结构直接制造于可挠基板上的金属剥离过程或奈米印刷技术的其他类似技术。其为使用双侧光学黏着剂作为中间转移层的无溶液fct技术,且可将刚性基板上的三层超颖材料奈米结构首先转移至黏着剂上。本发明的另一个具体实例为使得超颖材料可自诸如玻璃、石英及金属的刚性基板转移至诸如塑料或聚合物膜的可挠基板上的制造方法及设备。因此,可独立于所用原始基板制造可挠性超颖材料。装置制造多层超颖材料的示意性制造过程展示于图14中。首先,使用习知ebl方法在经铬(cr)涂覆的石英上制造多层电浆子或超颖材料装置。30nm厚的cr层用作牺牲层。接着,分别使用热蒸发及rf溅射法将金/ito(50nm/50nm)薄膜沉积于cr表面上。接下来,将厚度为约300nm的zep520a(正电子束抗蚀剂)薄膜旋涂于ito/金/cr/石英基板的顶部且使用ebl方法在zep520a上获得二维孔数组。为获得金奈米结构(圆盘图案),将50nm厚的第二金薄膜涂覆于电子束图案化抗蚀剂上。最后,藉由移除抗蚀剂残余物形成二维金圆盘数组奈米结构。每一超颖材料图案的面积大小为500μm乘500μm,且圆盘数组的间距为600nm,圆盘直径为约365nm。覆晶转移(fct)技术可挠性吸收体超颖材料的转移过程展示于图15中,将双侧黏性光学透明黏着剂(50μm厚;例如由3m制造的市售产品)附接于pet基板(70μm厚)。因此,将三层超颖材料装置与光学黏着剂紧密接触地放置且包夹在刚性基板与光学黏着剂的间。注意,石英基板上的cr薄膜在rf溅射过程后暴露于空气数个小时,使得cr表面上存在薄的原生氧化物膜。因此,cr与金的间的表面黏着与金/ito/金圆盘/光学黏着剂边界相比弱得多。此使得三层超颖材料奈米结构可自经cr涂覆的石英基板剥离。一旦将超颖材料奈米结构转移至pet基板上,其具有足以弯曲成各种形状的可挠性。最后,超颖材料奈米结构藉由在装置的顶部上旋涂300nm厚的pmma层而囊封。在另一个具体实例中,本发明提供一种可藉由弯曲pet基板而变换成各种形状的新颖nir超颖材料装置。图16(a)展示由透明pet及pmma薄膜包夹的可挠性吸收体超颖材料。在可挠基板上制造数个面积大小为500μm乘500μm的吸收体超颖材料奈米结构。实际上,使用pet层的可挠特性,吸收体超颖材料装置可符合许多形状,例如圆柱形(图16(b))。圆柱形基板的最小半径为约3mm,在10次可重复弯曲测试后,在超颖材料装置上可观察到无明显缺陷。光学表征及仿真上文所论述的三层金属/介电质奈米结构为吸收体超颖材料装置。所述装置的设计使得入射光能量强烈集中于ito层中。nir三层超颖材料架构的吸收效应可解释为局部表面电浆子共振或磁共振。此处论述的吸收现象不同于抑制金属圆盘数组中中透射效应,其中入射光由于超薄金属奈米结构的异常共振而被强烈吸收。为表征金圆盘/ito/金吸收体超颖材料的光学特性,使用傅里叶变换红外光谱仪(fouriertransforminfraredspectrometer,ftir)量测吸收体超颖材料的反射光谱。藉由组合红外显微镜与ftir光谱仪,可量测微区奈米光子装置的透射及反射光谱。在图17中,使用100μm乘100μm的取样面积量测空气/超颖材料界面的反射光谱(实验线图)。在波长约1690nm的吸收峰处,反射效率为约14%,亦即吸收体超颖材料在此波长下起作用。在rcwa模拟(模拟线图)中,使用e.d.palik,handbookofopticalconstantsofsolids,academicpress,newyork,1985中的实际光学常数;其内容以全文引用的方式并入本文中。在共振波长下,实验及计算彼此完全相符。可挠性吸收体超颖材料的反射光谱展示于图18(a)(0°线图)中。与图17中的ftir结果相比,可挠性超颖材料的吸收下降已红移至约1.81μm。此红移主要归因于周围介质的折射率变化(光学黏着剂及pet的折射率为约1.44)。在图18(c)及图18(d)中,采用三维严格耦合波分析(rcwa)方法计算吸收体超颖材料上的反射及透射光谱,且使用金、ito、cr、sio2及pet材料经实验证实的参数。亦可在理论模拟中观察到在约1.81μm波长下的共振吸收。然而,在量测的反射光谱中存在约1.2μm的两个共振下降。在rcwa计算(图18(c))中,再现双重下降且归因于两个局部共振模式,因为其对入射角极其不敏感。对于角度依赖性计算,使用te偏振光(电场垂直于入射平面)以拟合实验结果。虽然入射角自0度变化至45度,但反射效率展示增加趋势,因为光在大角度入射下无法高效集中。然而,实验中的背反射效率(图18(a))明显降低。此是因为吾等当前实验设定(下一部分中所论述)仅允许吾等收集背反射信号(入射及收集方向彼此相同)且大入射角的收集效率极低。在图18(b)中,使用相同ftir设定量测可挠性超颖材料的透射光谱,主要差异为光自空气/pmma界面入射。在约1.85μm的波长下观察到fano型透射峰。在共振波长下,实验的透射效率高于理论模拟(图18(d))。此可归因于金平面膜及二维圆盘数组上的缺陷,其增强泄漏辐射效率且因此造成量测结果的较高透射效率。如图19中所示,弯曲pet基板使得吾等量测吸收体超颖材料在不同弯曲形状下的光学反应。弯曲pet基板的形状藉由调节基板末端(a与b)的间的距离来控制。吸收体装置上的经解析背反射的角度藉由改变弯曲条件来量测。根据图19,由在超颖材料装置位置处的弯曲斜率确定入射角根据图18(a),观察到当入射角自0度增加至45度时,背反射的强度变得较弱且吸收下降变得较浅。尽管如此,其仍展示可挠性吸收体超颖材料的共振吸收波长对光的入射角并不敏感。由超颖材料制成的装置可制成非常敏感的传感器。本发明提供一种在可挠基板上制造超颖材料装置的新颖技术。可挠性使得装置可弯曲及拉伸,改变装置结构。由于各装置的共振频率为装置结构的功能,故共振频率可藉由弯曲及拉伸基板而调谐。因此,本发明的另一个具体实例为一种超颖材料,其允许物理方式改变材料结构,导致其共振频率变化。无需改变材料组成。本发明超颖材料的一个具体实例为用作电磁波吸收体的可挠性电浆子或超颖材料奈米结构装置。在本发明的上述具体实例中,已报导在nir波长下工作的高度可挠性三层吸收体超颖材料装置。藉由使用fct方法,使用光学透明黏着剂(例如由3m制造的市售产品)将三层金圆盘/ito/金吸收体超颖材料自石英基板转移至透明pet基板。此外,三层吸收体超颖材料藉由pmma薄膜及光学黏着层囊封以形成可挠装置。ftir实验展示吸收体超颖材料对石英基板及高度可挠pet基板起良好作用。此外,在此可挠性超颖材料上观察到角度不敏感的吸收效应及fano型透射共振。此外,本发明中所述的无溶液fct技术亦可用于将其他可见光-nir金属/介电质多层超颖材料转移至可挠基板上。在可见光-nir范围内起作用的可挠性超颖材料将在三维空间的光操控中,尤其当超颖材料架构设计于曲面上时,展示更多优势。在本发明的另一个具体实例中,可采用本发明的fct技术以便将硬化薄膜转移至较软可挠基板上。关于将薄膜转移至可挠基板上的实验详情将al2o3薄膜自刚性基板转移至pet基板所采用的方法为经由使用弱黏着性金属夹层转移。此方法基于所参考的2012年12月23日申请的美国非临时专利申请案序号13/726,127及2012年12月23日申请的美国非临时专利申请案序号13/726,183,其两者皆主张2011年12月23日申请的美国临时专利申请案序号61/579,668的优先权。本发明的一个具体实例为使用透明聚酯胶带施加机械应力以使al2o3薄膜完全与牺牲金属层分开。接着,将al2o3薄膜转移至pet基板且牺牲金属层可藉由酸蚀刻去除。首先,将薄铬(cr)膜(亦即30-100nm厚)沉积于熔融硅石基板上,接着将薄银(ag)膜(亦即30-100nm厚)沉积于cr顶部上。接着,沉积另一金属层,诸如ti膜(3-10nm厚)且其用于退火过程。接着,将al2o3薄膜(例如100-500nm)沉积于金属层上。接着,按照如本文中稍早揭示的本发明的低温退火过程中的具体实例,在300℃-800℃温度范围中进行退火。将光学透射率高于95%的可挠性透明聚酯胶带附接于al2o3膜且机械剥离硬化al2o3薄膜。制造结构示意性图解于图20中。由于表面能量不同,故cr与ag的间的黏着性弱且因此可易于藉由施加应力克服。所施加的应力由纯张开应力模式及剪切应力模式组成。此两种模式确保ag与cr的间的澈底分离。在所施加的应力下,硬化al2o3薄膜将使其自身与牺牲ag层及可挠性透明聚酯胶带一起自刚性基板分离,如图21中所示。最后,牺牲ag层藉由将图21中所描绘的总成由诸如稀hno3(1:1)的酸浸没来蚀刻去除。由于胶带及al2o3薄膜为耐酸性的,故蚀刻剂溶液将仅较快蚀刻去除牺牲ag层。在ag薄膜完全蚀刻去除后,将al2o3完全转移至图22中所描绘的pet基板。结果图23展示制造用于转移al2o3薄膜的样品。在熔融硅石基板上,将cr以约5nm/min的溅射产率首先溅射于基板上,使其典型厚度为50nm。接着,藉由电子束蒸发将50nmag沉积于其顶部上。最后,藉由电子束蒸发将约200nm厚的al2o3沉积于总成。图24展示在使用透明胶带施加机械剥离后,al2o3膜自熔融硅石基板及cr剥离。al2o3连同ag膜及胶带一起自刚性基板完全且平滑地分离而无任何开裂及气泡。在酸中蚀刻去除牺牲ag层后,将al2o3成功转移至可挠pet基板。诸如对熟习此项技术者显而易见的修改及变化被认为属于本发明的范畴内。工业实用性本发明系关于一种将较硬薄膜基板层转移至较软基板(尤其可挠基板)上的方法。详言的,本发明提供一种经由覆晶制程将蓝宝石薄膜层转移至较软可挠基板(例如pet、聚合物、塑料、纸及甚至织物)上的方法。较硬薄膜蓝宝石基板层于较软基板上的组合与纯蓝宝石基板相比较佳。实际上,材料愈硬,其愈脆,因此,蓝宝石基板很难擦伤,但其容易碎裂且反过来亦常常如此,其中石英基板与蓝宝石基板相比较易于擦伤,但其脆性较小。因此,将较硬薄膜基板沉积于较软基板上两全其美。较软可挠基板脆性较小,具有良好机械效能且常常成本较低。藉由使用较硬薄膜基板将实现防擦伤功能。视需要,本文中论述的不同功能可以不同顺序及/或彼此并行地进行。此外,视需要,上述功能中的一或多者可视情况存在或可组合。在本说明书通篇,除非本文另有规定,否则词语「包含(comprise)」或诸如「包含(comprises)」或「包含(comprising)」的变形应理解为暗示包括所陈述整体或整体的群组,但不排除任何其他整体或整体的群组。在本发明中且尤其在申请专利范围及/或段落中亦应注意,诸如「包含(comprises)」、「包含(comprised)」、「包含(comprising)」及其类似物的术语可具有其归于美国专利法中的含义;例如其可意谓「包括(includes)」、「包括(included)」、「包括(including)」及其类似物;且诸如「基本上由组成(consistingessentiallyof)」及「基本上由组成(consistsessentiallyof)」的术语具有其归于美国专利法中的含义,例如其使得要素无需明确列举,但排除先前技术中所发现或影响本发明的基础或新颖特征的要素。此外,在本说明书及申请专利范围通篇,除非本文另有规定,否则词语「包括(include)」或诸如「包括(includes)」或「包括(including)」的变形应理解为暗示包括所陈述整体或整体的群组,但不排除任何其他整体或整体的群组。本文中所用的选择术语的其他定义可见于【实施方式】内且通篇应用。除非另外定义,否则本文中所用的全部其他技术术语具有与一般熟习本发明所属技术者通常理解相同的含义。虽然上述发明已相对于各个具体实例及实施例加以描述,但应理解,其他具体实例如以下申请专利范围及其等效物中所表述,属于本发明的范畴内。此外,以上特定实施例仅解释为说明性的,且不以任何方式限制本发明的其余部分。无需进一步详细描述,咸信熟习此项技术者可基于本文中的描述最大程度利用本发明。本文中所列举的全部公开案以全文引用的方式并入本文中。此文件中此部分或任何其他部分中任何参考文件的引用或标识不应解释为承认此类参考物可用作本申请案的先前技术。当前第1页12