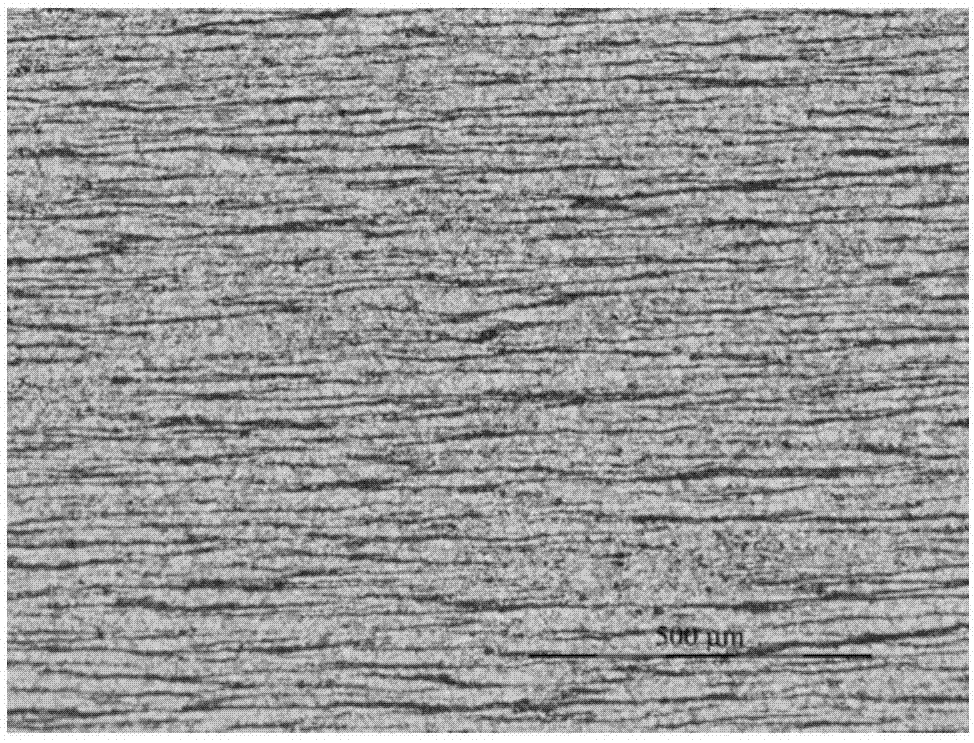
本发明涉及低合金控轧控冷钢,具体涉及一种再冷拔ERW焊管用钢及其热轧板卷和制备方法。
背景技术:
:冷拔液压和汽车油缸制造行业对无缝管的强度、韧性、焊接性等不断提出更高的要求,而随着冶金技术的进步、焊接技术和微合金化钢的发展,处于降低成本的需要使生产具有高强度、高韧性、良好的焊接性的再冷拔直缝焊管成为必须。技术实现要素:本发明的目的在于提供一种具有优良综合性能的强度级别在355MPa以上的再冷拔ERW焊管用钢,在TMCP工艺制度下,通过合理的成分设计,控制轧制和控制冷却得到铁素体+细珠光体+少量贝氏体为主的复相组织,钢的碳硅锰含量控制在合理的范围,在具有较好的焊接性、力学性能和高的表面质量的同时具有经济性,减少制造成本。经过分条后制作的ERW焊管采用正火处理后,焊缝区得到铁素体+珠光体组织,且组织均匀分布,主要用于再冷拔液压和汽车油缸精密焊管制造。一种再冷拔ERW焊管用钢,按照重量百分比含有碳0.15~0.30%;硅:≤0.40%;锰:0.60~1.60%;磷:≤0.020%;硫:≤0.020%;铌:0.0010~0.050%;钒:0.0010~0.050%;钛:0.0010~0.030%;铝:0.015~0.040%;镍:0.0025~0.40%;铬0.0020~0.50%;铜:0.0025~0.40%;钙:0.0010~0.0050%;氮:≤0.006%;氧:≤0.004%;氢:≤0.00025;铁和微量杂质:余量。进一步地,含有残余钼元素。一种再冷拔ERW焊管用钢的制备方法,包括如下步骤:(1)按照上述组分和配比备料;(2)转炉冶炼;(3)钢包吹氩;(4)LF炉精炼;(5)连铸;(6)再加热;(7)粗轧;(8)热机械控轧;(9)冷却。进一步地,步骤(2)采用300吨转炉冶炼。进一步地,步骤(7)采用7机架2250连轧机组生产线进行热机械控轧。进一步地,步骤(8)中采用如下步骤:(8-1)1180~1240℃加热;(8-2)1150~1180℃初轧开轧;(8-3)1000℃~950℃精轧开轧;(8-4)900℃~840℃精轧终轧;(8-5)650℃~600℃终止冷却并卷取。进一步地,步骤(9)采用再冷拔直缝焊管用钢高强度冷却工艺或层流冷却,优选水幕前段层流冷却,水冷15℃~35℃/S。。进一步地,热轧厚度规格10mm。进一步地,步骤(1)中铁水预处理,S≤0.005%:前扒渣和后扒渣,后扒渣亮面大于85%;步骤(2)中,P≤0.013,进行出钢挡渣操作,下渣量≤4kg/t,终点炉温1620~1635;步骤(4)中,LF脱硫,S≤0.010%:白渣操作,保证钢包顶渣充分还原;喂钙线,钙含量要求10~35ppm,保证喂钙线前后总弱搅时间不小于12min;步骤(5)中,中包目标温度控制在液相线温度以上10~30℃。一种再冷拔ERW焊管用钢热轧板卷,采用上述制备方法后,卷曲得到。与目前现有技术相比,本发明用于再冷拔液压和汽车油缸精密焊管,提高低温冲击性能、力学性能和经济性。相对于目前主要应用于油缸的冷拔无缝管在初始成本和降低机床加工成本上有明显优势。如:较好的成形(外径和内径的圆度);较好的表面质量(涂漆后较少缺陷并提高了抗疲劳寿命);较好的偏心率和壁厚公差(偏心率:冷拔焊管最大为3%,而冷拔无缝管通常为8%);更加安全(冷拔焊管必须100%通过整体管身涡流探伤+超声波探伤检测);良好的低温韧性;更低的剪切定尺成本;目前冷拔焊管(DOM管)占美国油缸市场份额的90%左右。钢的碳硅锰含量控制在适当的范围,进行适当的铌钛微合金化处理,得到的铁素体+贝氏体+珠光体组织均匀性较好,具有较佳的焊接性。具体来说:1)采用适当的C、Mn、Nb、V、Ti含量,为节约资源,秉持经济适用原则,不采用Mo和稀土元素加入,经济性好。进行钙处理,钙含量要求10~35ppm。2)采用铁素体+细珠光体+少量贝氏体组织。3)充分发挥热连轧机组突出的控制轧制和控制冷却能力来提高材料的强韧性能,轧制后冷却速率达到15~35℃/s。4)适用于ERW焊管生产,焊管进行正火处理,焊缝区晶粒细小,均匀弥散分布。附图说明图1为本发明金相组织图;图2为正火处理后焊缝金相组织图。具体实施方式下面根据附图对本发明进行详细描述,其为本发明多种实施方式中的一种优选实施例。再冷拔ERW焊管对焊接性能、力学性能、低温韧性有严格的要求,因此从成分设计、轧制和冶炼三个关键环节从严控制。第一,采用适当的碳、锰含量控制;第二,设计轧制、冷却工艺,综合微合金化、固溶强化和组织强化等方法,获得较为均匀的铁素体+细珠光体+少量贝氏体的复相组织,同时提高强度、塑性和韧性;第三,通过超纯净冶炼最大限度降低S和P的含量,减少硫化锰夹杂来提高韧性。再冷拔直缝焊管钢的化学成分为:碳0.15~0.30%;硅:≤0.40%;锰:0.60~1.60%;磷:≤0.020%;硫:≤0.020%;铌:0.0010~0.050%;钒:0.0010~0.050%;钛:0.0010~0.030%;铝:0.015~0.040%;镍:0.0025~0.40%;铬0.0020~0.50%;铜:0.0025~0.40%;钙:0.0010~0.0050%;氮:≤0.006%;氧:≤0.004%;氢:≤0.00025;铁和微量杂质:余量。特别地,要求不加入钼,钢中仅含有残余钼元素。根据马钢工业生产实践,钼的加入会增加产品的生产成本。钢区要求:1)铁水预处理,S≤0.005%:前扒渣和后扒渣,后扒渣亮面大于85%,2)转炉,P≤0.013。加强出钢挡渣操作,下渣量≤4kg/t;过程控制模型,终点炉温1620~1635。3)LF脱硫,S≤0.010%:白渣操作,保证钢包顶渣充分还原。喂钙线,钙含量要求10~35ppm,保证喂钙线前后总弱搅时间不小于12min。4)连铸中包目标温度控制在液相线温度以上10~30℃。再冷拔ERW焊管钢的控轧控冷工艺制度为:1.轧制道次分配:采用两机架可逆轧机粗轧、再进行7机架热连轧,最后进行轧制后层流冷却、卷取。在奥氏体再结晶区和未再结晶区多道次控制轧制,(1180~1240℃)加热-(1150~1180)℃初轧开轧-(1000℃~950℃)精轧开轧-(900℃~840℃)精轧终轧-(650℃~600℃)终止冷却并卷取。典型压下率(16mm):粗轧8道次:220,209,182,158,132,109,88,68,50mm精轧7道次:50,38.6,30.2,25.5,21.3,18.5,16.9,16mm典型压下率(2.8mm):粗轧6道次:220,204,165,130,96.8,67,43.7mm。精轧7道次:43.7,26,15.3,9.1,6.0,4.3,,3.4,2.8mm。2.冷却方式:水幕前段层流冷却,水冷15℃~35℃/S。TMCP工艺制度的依据是:热机械轧制(TMCP)是以再结晶、相变等冶金工艺为基础,在规定的变形和温度条件下完成固溶强化、沉淀强化、位错强化和晶粒细化等硬化处理,从而使轧制状态钢板性能达到最佳化。为获得强度和韧性的合理匹配,充分发挥七机架热连轧机组的轧制和冷却能力,采用控制轧制和加速冷却的方式生产,它通过高温奥氏体区形变再结晶、低温奥氏体未再结晶区的变形以及轧后的加速冷却来获得最佳效果。在组织上,采用铁素体+细珠光体+少量贝氏体。通过控制TMCP工艺及其他有利于贝氏体组织形成的因素,沿奥氏体晶界或奥氏体晶内先期产生少量贝氏体,分割奥氏体晶粒为若干小空间,在随后的相变中,由于转变速度很快,分割后的空间限制了贝氏体的长大,从而得到进一步细化的组织。由另外,铁素体+细珠光体+少量贝氏体组织更接近平衡组织而转变更加充分,冲击韧性的稳定性更好。金相组织见图1和图2。母材组织主要为铁素体(70%)+珠光体(20%)+贝氏体(10%),且分布均匀。焊缝组织主要为铁素体(75%)+珠光体(25%)。根据本发明用钢的化学成分范围,经300吨转炉冶炼,经过钢包吹氩、LF炉精炼、连铸,再加热后,进入两机架R1和R2粗轧,再经7机架2250连轧机组生产线进行热机械控轧,轧后采用再冷拔直缝焊管用钢高强度冷却工艺,热轧厚度规格10mm。化学成分见表1,TMCP工艺制度见表2,机械性能见表3,显微组织见图1。表1.实施例再冷拔ERW焊管用钢的化学成分(%)序号CSiMnPSNbTiAlsCa10.180.031.410.0110.00240.0090.0170.00180.001920.190.011.380.0080.00300.0110.0150.00170.002230.190.021.390.0090.00330.0110.0180.00180.002040.180.031.420.0100.00340.0090.0170.00190.0024表2.再冷拔ERW焊管用钢TMCP工艺制度表3再冷拔ERW焊管用钢力学性能检验结果(纵向)序号Rel,(N/mm2)Rm,(N/mm2)A,%141257930242857231.5344556229.5444858032表4再冷拔直缝焊管用钢纵向冲击性能检验结果(KV2/J)通过实验可以确定:1)本发明的再冷拔直缝焊管钢具有良好低温冲击韧性。2)本发明的再冷拔直缝焊管钢组织均匀,主要为铁素体+珠光体+少量贝氏体,性能优良。3)本发明的再冷拔直缝焊管钢的综合性能:ReH:385~420MPa,Rm:540~590MPa,-20℃夏比冲击功165J。4)合格率达到100%以上。5)ERW焊接后经正火处理焊缝去组织为铁素体+珠光体,分布均匀上面结合附图对本发明进行了示例性描述,显然本发明具体实现并不受上述方式的限制,只要采用了本发明的方法构思和技术方案进行的各种改进,或未经改进直接应用于其它场合的,均在本发明的保护范围之内。当前第1页1 2 3