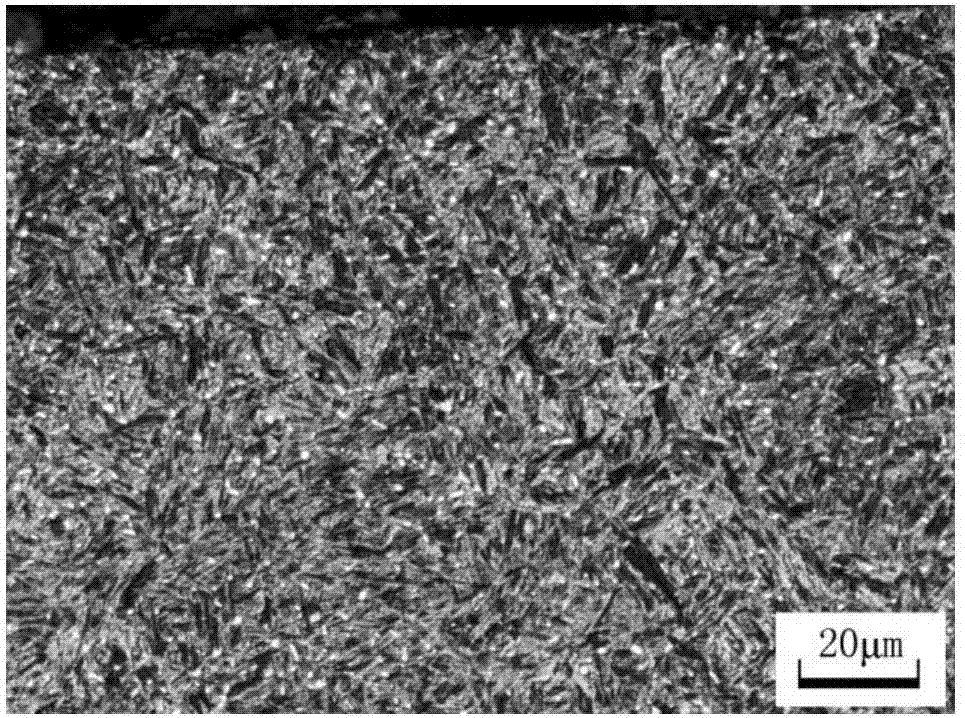
本发明涉及工程机械用钢
技术领域:
,特别涉及一种低淬透性耐磨带钢及其制造方法。
背景技术:
:低淬透性薄带耐磨钢特别适用于制造耐磨钢管和耐磨薄片构件,如矿山机械、水泥生产等所需的大量管状、带状耐磨零部件或构件。低淬透性薄带耐磨钢,具有良好的塑韧性,易于加工成型。一般采用该钢制作的零部件,采用电阻焊接后,可直接进行整体淬火或者高频感应淬火,获得外表面具有1mm~2mm高硬度耐磨层的构件,且构件心部具有较高的塑韧性。普通的耐磨钢虽然表面具有较高硬度,但由于添加了较多的cr、mo、ni等用于增加淬透性的元素,导致其心部具有同样的高强高硬组织,进而使其在受到折弯、剪切力时容易发生开裂、崩裂,并且成形性较差。而低淬透性耐磨带钢,可根据需要加工成各种形状,然后采用整体淬火或者感应淬火的方法,制得具有良好塑韧性心部的构件,具有成本低,易于批量生产,使用灵活方便的特点。公告号为cn103725976b的中国发明专利公布了一种高耐磨双金属复合耐磨板,该发明在低碳钢板或低碳合金钢板上焊接耐磨合金层,按质量百分数计,该耐磨合金层中各成分含量如下:c:0.35~0.55%、si:2~2.4%、mn:2.7~3.2%、cr:11~12.5%、mo:2.5~2.9%、v:0.7~1.8%、w:2.2~3.6%、b:0.7~1.1%,其余为fe。该发明采用堆焊方法,将上述耐磨合金层堆焊在低碳钢表面,堆焊合金的硬度为hrc55~hrc58,所制构件心部为低碳钢板,具有较好的塑韧性,而表面为高碳高合金钢板,具有较高的耐磨性。但其耐磨性完全是依靠耐磨合金本身的耐磨属性,合金含量很高,使得所制构件成本较高,并且所采用的堆焊方法具有施工速度慢的特点,其只能在较为简单的构件上使用。公告号为cn102134682b的中国发明专利公布了一种耐磨钢板,该发明提供一种耐磨钢板,其化学成分(重量%)为:c:0.31~0.40%、si:0.10~0.80%、mn:0.20~1.50%、p:≤0.050%、s:≤0.030%、cr:0~1.50%、mo:0~0.80%、al:0.02~0.20%、b:0.0005~0.0040%、ti:0~0.10%、ca:0~0.030%、0.10%≤cr+mo≤1.80%、0.05%≤al+ti≤0.18%,余量为fe和不可避免的杂质。该耐磨钢板的制造方法,包括冶炼、精炼、铸造、轧制、淬火和回火等步骤。通过以上成分及工艺得到的550hb级耐磨钢板硬度高≥550hb,可焊接和弯曲,微观组织为马氏体或马氏体和残余奥氏体。实现高强度、高硬度和较佳韧性的匹配,并具有可焊接性。该发明通过轧制、热处理进行组织调控,获得了高强度、高硬度和高韧性的匹配,但其添加的合金元素依然较多,且经过轧制淬火、回火步骤后钢板本身具有高强度,导致其成形性、延展性差,不适宜于进一步折弯成型、加工成复杂构件。技术实现要素:本发明的目的就是要解决现有耐磨钢淬透性高、使用过程中易发生开裂、制备工艺复杂和成本较高的问题,提供一种低淬透性耐磨带钢及其制造方法。为实现上述目的,本发明所设计的低淬透性耐磨带钢,按重量百分数计,其化学组成为:c:0.405~0.685%、si:0.10~0.20%、mn≤0.12%、p≤0.015%、s≤0.005%、ti:0.012~0.028%、nb:0.025~0.075%、als:0.015~0.038%、n:0.005~0.015%,余量为fe和不可避免杂质。进一步地,所述的低淬透性耐磨带钢,按重量百分数计,其化学组成为:c:0.480~0.600%、si:0.15~0.18%、mn≤0.10%、p≤0.010%、s≤0.003%、ti:0.012~0.023%、nb:0.025~0.065%、als:0.020~0.030%、n:0.007~0.010%,余量为fe和不可避免的杂质。进一步地,所述的低淬透性耐磨带钢,按重量百分数计,其化学组成为:c:0.600%、si:0.15%、mn:0.008%、p:0.008%、s:0.003%、ti:0.012%、nb:0.040%、als:0.030%、n:0.010%,余量为fe和不可避免的杂质。本发明各元素的作用及组成依据如下:c:c是提高硬度、强度和耐磨性的主要元素,钢中的c在0.405~0.685%范围可保证淬火后表面硬度,当钢中碳含量大于0.685%,淬透性深度会增加,导致薄钢板淬透性超过要求的值;当钢中碳含量小于0.405时,表面淬火硬度不够。本发明中c含量控制在0.405~0.685%,优选的c含量为0.48~0.60%。si:si是炼钢脱氧的必要元素,以固溶强化形式提高钢的强度,且能提高c在钢中的活度,从而加大钢带表面脱碳倾向,si含量太低脱氧效果不佳,si含量太高会增加淬透性和降低韧性。本发明中si含量控制在0.10~0.20%,优选的si含量为0.15~0.18%mn:mn是提高钢板淬透性的重要元素,mn含量高会造成较严重的中心偏析和降低韧性。本发明中mn含量控制在mn≤0.12%,优选的mn含量为mn≤0.10%。al:al是重要的细化晶粒元素,al可通过与n形成aln,细化奥氏体晶粒度,形成本质细晶粒钢,aln属于高温稳定型析出物,然而al对于增加钢的淬透性没有明显效果,且al含量过高,容易与o形成颗粒较大的尖角不规则形状的al2o3,使母材韧性恶化。本发明中al含量控制在0.015~0.038%,优选的al含量为0.020~0.030%。nb:nb具有细化晶粒的作用,且对提高钢的淬透性效果不明显。钢中添加nb与c和n形成nbx(cn)y的析出物,在700℃到900℃轧制,奥氏体再结晶与合金碳氮化物析出相竞争,nbx(cn)y等相优先在奥氏体内的位错上析出,析出能显著钉轧晶界,奥氏体再结晶滞后,从而使加工硬化奥氏体易于转变为铁素体。钢中nb含量添加超过0.075%以后,容易形成大颗粒的nbx(cn)y析出物,不能起到显著细化晶粒作用,而且还具有降低钢的韧性的作用。本发明中nb含量控制在0.025~0.075%,优选的nb含量为0.025~0.065%。ti:ti可显著细化晶粒,能够与n形成tin,同时不会显著提高淬透性。钢中的tin化合物具有较高的热稳定性,在1400℃左右仍不会发生明显的溶解,可以有效钉轧奥氏体晶界,防止加热过程中奥氏体的长大。但tin夹杂物容易在连铸过程中产生大颗粒立方体夹杂,这类形状夹杂物对韧性具有显著的影响,因此,ti含量不宜过高。本发明中ti含量控制在0.012~0.028%,优选的ti含量为0.012~0.023%。n:n作为与钢中ti和al形成高温稳定细小的化合物的关键因素,必须保证其在钢中的含量,但n添加太多,会造成形成的al和ti的氮化物尺寸过大,不利于韧性的提高。本发明中n含量控制在0.005~0.015%,优选的n含量为0.007~0.010%,s:s是钢中有害元素,常以mn的硫化物形态存在,其对钢韧性的不利影响较大,且本发明钢由于淬透性的限制,尽可能不添加mn,若在此情况下,钢中有较多s,会导致形成fes等,连铸形成热裂纹,因此,应尽可能降低s含量。本发明中s含量控制在s≤0.005%,优选的s含量为s≤0.003%p:p固溶强化元素,钢中适量的p可促进铁素体的形成,并保持强度和塑形的良好平衡,但p含量过高,易引起铸坯中心偏析,对钢的冷弯成型性能和韧性造成不利影响。本发明中p含量控制在p≤0.015%,优选的p含量为p≤0.010%本发明还提供了一种低淬透性耐磨带钢的制造方法,包括铁水脱硫预处理、转炉冶炼、lf+rh炉精炼、板坯连铸、铸坯缓冷、板坯加热、热连轧、acc冷却和卷取工艺,所述的铸坯缓冷工艺,采用堆垛缓冷;所述的板坯加热工艺,加热温度为1170~1220℃,加热时间300~400min;所述的热连轧工艺,粗轧开轧温度≥1150℃,粗轧终轧温度为970~1100℃,末道次压下量≥35%,精轧开轧温度为880~920℃,压下量≥65%,精轧终轧温度为780~820℃;所述的acc冷却工艺,采取前端冷却,冷却速率≤10℃/s;所述的卷取工艺,卷取温度为700~720℃。进一步地,由于钢中未添加mo、ni、cu、cr等高含量的合金元素,不需要长时间的高温加热来保证合金元素固溶,而且较低的加热温度辅以钢中析出物tin的钉扎作用,可保证在加热阶段奥氏体晶粒得到充分的细化,因此,本发明所述的板坯加热工艺中优选的加热温度为1170~1210℃。进一步地,为了在奥氏体再结晶区,取得细化原奥氏体晶粒的效果,采用较大的压下量进行轧制,同时,为了保证后期精轧温度在一个合理的范围内,本发明优选的粗轧终轧温度控制在970~1000℃,末道次压下量≥35%。进一步地,在较低的奥氏体非再结晶温度进行高的压下量轧制,可充分扁平化奥氏体晶粒,从而在其中产生大量位错和nbx(cn)y的析出,进而保证在精轧终轧完成之后,奥氏体向铁素体转变过程中,大量的铁素体晶粒和珠光体具有充分的形核位置和高的形核率,从而有利于最大限度的细化组织,得到细晶组织,因此本发明优选的精轧开轧温度控制在880℃~910℃,压下量≥65%。本发明的主要原理是通过最大程度细化晶粒,来降低材料的淬透性,同时以廉价的c为主要增加硬度和耐磨性的元素,以nb、ti、al为显著的细化晶粒的元素,充分减少增加淬透性元素如si、mn等的含量,可在保证低淬透性的前提下,降低生产成本。本发明的优点在于:(1)本发明设计的低淬透性耐磨带钢,采用中高碳钢成分设计,未添加ni、mo、cu、cr等贵重合金和淬透性较高的合金,在降低生产成本的同时,也可保证其低淬透性,而且本发明添加了nb、ti等细化晶粒的元素,保证了本发明所设计带钢基体的韧性,同时由于晶粒的细化,进一步有利于降低其淬透性。(2)本发明通过严格控制板坯加热工艺中的加热温度、热连轧工艺中的粗轧终轧温度以及热连轧工艺中的精轧开轧和终轧温度,有利于本发明所设计钢中晶粒得到充分的细化,进而有利于降低其淬透性和提高其韧性。本发明所设计的低淬透性耐磨带钢的晶粒度可达到10~12级,淬硬层深度约1.5mm,其-20℃kv2冲击功≥95j。附图说明图1为本发明低淬透性耐磨带钢的热轧态金相组织显微结构示意图。图2为本发明低淬透性耐磨带钢的淬火态表层金相组织显微结构示意图。具体实施方式以下结合附图和具体实施例对本发明作进一步的详细描述。本发明优选实施例1~4对本发明所述低淬透性耐磨带钢及其制造方法进行进一步的详细描述,并采用对比例1~4对本发明所设计的低淬透性耐磨带钢的化学成分及主要制备工艺参数进行进一步的对比说明。表1为实施例1~4及对比例1~4的化学组成。上述实施例1~4及对比例1~4所述的低淬透性耐磨带钢的制造方法,主要包括铁水脱硫预处理、转炉冶炼、lf+rh炉精炼、板坯连铸、铸坯缓冷、板坯加热、热连轧、acc冷却和卷取工艺;所述的铸坯缓冷工艺,采用堆垛缓冷;所述的板坯加热工艺,加热温度为1170~1220℃,加热时间300~400min;所述的热连轧工艺,粗轧开轧温度≥1150℃,粗轧终轧温度为970~1100℃,末道次压下量≥35%,精轧开轧温度为880~920℃,压下量≥65%,精轧终轧温度为780~820℃;所述的acc冷却工艺,采取前端冷却,冷却速率≤10℃/s;所述的卷取工艺,卷取温度为700~720℃。表2为实施例1~4及对比例1~4的主要制备工艺参数。更具体地,按照表2所示的主要制备工艺参数生产实施例1~4及对比例1~4所述的低淬透性耐磨带钢。表1:化学组成(wt%)编号csimnpsnbtialsn实施例10.4050.200.050.0080.0040.0450.020.0150.005实施例20.6850.100.040.0150.0040.0250.0280.0380.015实施例30.5200.170.120.010.0050.0750.0180.0280.012实施例40.6000.150.080.0080.0030.0400.0120.0300.010对比例10.5800.150.060.0080.0050.0350.0280.0300.011对比例20.6501.000.050.0080.0050.0450.0220.0260.003对比例30.6000.130.070.0080.0050.1000.0280.0350.012对比例40.6300.150.250.0080.0040.0470.0250.0300.012表2:主要制备工艺参数参照gb/t225《钢的淬透性末端淬火试验方法》,从本发明所制低淬透性耐磨带钢的热轧态钢板上取直径为5mm,长度100mm圆柱体进行末端淬火试验,试验中采用洛氏硬度测量末端硬度,并距离端部5mm,每间隔0.5mm测量洛氏硬度hrc值;距离端部5mm~11mm,每隔2mm测量洛氏硬度hrc值,以洛氏硬度hrc值≥56为淬硬层深度。对于厚度>7mm的带钢,参照gb/t229《金属夏比缺口冲击试验方法》测定本发明所制低淬透性耐磨带钢的-20℃低温冲击韧性。表3为实施例1~4及对比例1~4的洛氏硬度hrc值及-20℃kv2冲击功。由表3可知,采用本发明方法制备的低淬透性耐磨带钢(实施例1~4)的淬硬层深度为1.5mm,淬透性较低,且所制钢-20℃kv2冲击功在95j~135j范围内,冲击韧性较高。对比例1因其加热温度过高,后续粗轧温度和精轧温度均偏高,压下率较小,导致其晶粒较粗,淬硬层深度达到3.5mm,显著高于实施例1~4,且其冲击韧性显著低于实施例1~4。对比例2因其si和n含量的提高,不利于晶粒细化,其淬硬层深度达到3.0mm,高于实施例1~4,且n含量的提高,使形成的tin析出物尺寸较大,严重影响其冲击韧性。对比例3中加入过多的nb元素,使其在精轧阶段形成的nbx(cn)y尺寸过大,不能起到钉扎位错和抑制再结晶的作用,导致其细化晶粒效果较差,冲击韧性较低,显著低于实施例1~4。对比例4中加入过多的mn元素,显著增加了淬透性,淬硬层深度达到4.0mm,显著高于实施例1~4,且其冲击韧性也不高。表3:hrc值及-20℃kv2冲击功图1和图2分别为采用本发明方法设计的低淬透性耐磨带钢热轧态金相组织显微结构示意图和淬火态表层金相组织显微结构示意图。由图1和图2可知,采用本发明方法设计的低淬透性耐磨带钢的组织特征形貌均匀,金相组织为铁素体和细密珠光体组织,无带状组织析出,晶粒尺寸较小,晶粒度按照gb/t6394《金属平均晶粒度测定方法》评测,达到10~12级,从而使得本发明所制带钢具有良好的塑形、韧性和低淬透性。当前第1页12