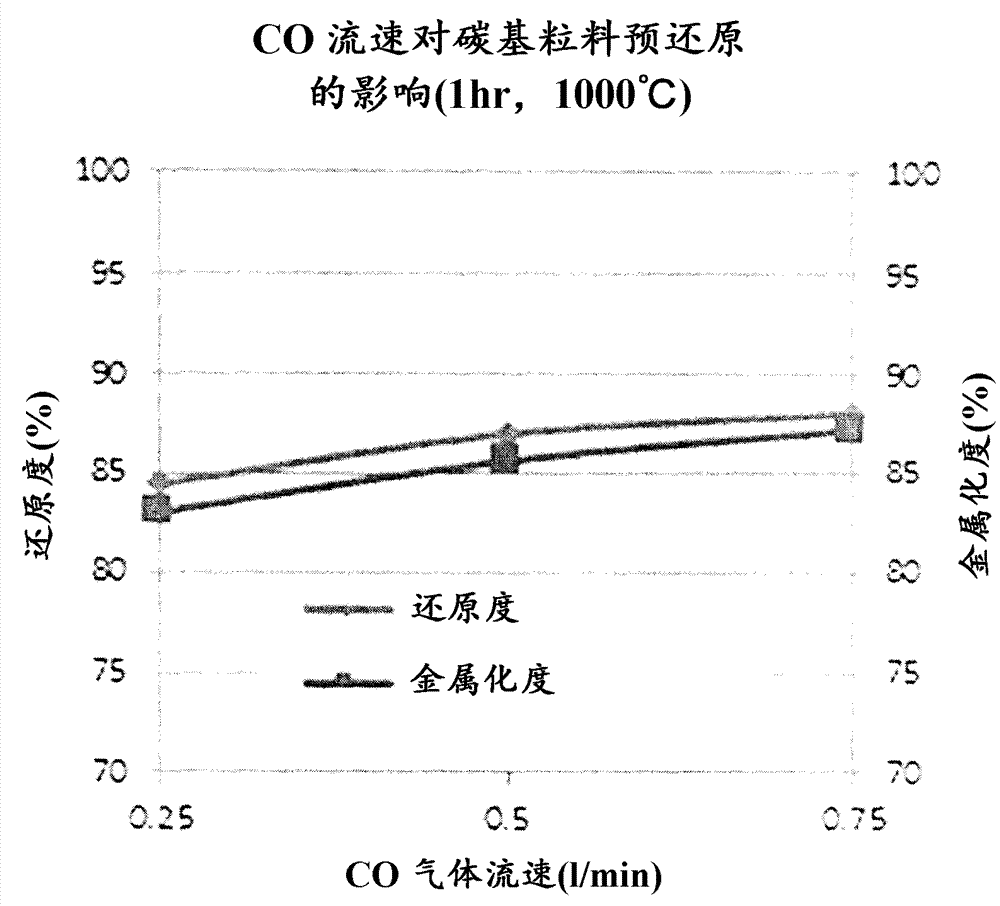
本发明涉及制备碳基钛铁矿粒料的固结方法、其固态还原和随后在电炉中熔炼。熔炼钛铁矿消耗相当大量电能。另外,由于发泡效应,可能阻碍炉的可操作性。到熔炼炉的进料一般由原钛铁矿和固体碳质还原剂组成。在具体过程中,原钛铁矿由经预还原钛铁矿粒料代替。用于后者制备过程的步骤是用膨润土制备钛铁矿粒料,并在过量固体碳质还原剂存在下在旋转炉中预还原粒料。因此,熔炼经预还原钛铁矿粒料在AC炉中进行。然而,以此方式产生的TiO2矿渣被作为无机粘合剂的膨润土污染。本发明的一个目的是提供基本目标在于使矿中所含铁氧化物金属化的预还原矿的替代方法。发明概述本发明提供一种制备用于熔炼的预还原钛铁矿的方法,其中矿中包含的金属氧化物,如铁、铬和锰氧化物,在固态反应中相对于氧化钛被选择性还原,方法包括预还原碳基矿粒料的步骤。粒料中除钛氧化物以外的金属氧化物可最大程度被预还原,即,基本完全,或者可部分被预还原。粒料可具有小于6mm尺寸,优选在2mm至5mm范围内。可从所需比例的矿、-106微米煤细粉和适合有机粘合剂的混合物制备粒料。可实际确定煤与金属氧化物含量之比。例如,可使用关于矿中的铁完全还原的化学计量比。有机粘合剂含量可在0至1%范围内。此含量可取决于所得粒料的物理性质,主要是生料态(greenstate)和经空气干燥或硬化态粒料的强度。粒料可经空气硬化至少4天。此阶段通常足以保证粒料足够强,以允许它们安全有效地处理到随后预还原反应器。粒料的机械强度优选高于600N。粒料也应具有在热反应器环境中可接受的性能,避免由于过度膨胀导致爆裂。可使用单一粘合剂或粘合剂的混合物。本发明不限于此方面。预还原粒料基于矿中所含铁氧化物的还原度来评估。铁氧化物应优选以与初始含量相差小于10%的量存在。然而,在正常和稳定操作期间,一致的预还原产率应为主要目的。可使粒料经过热还原过程,或经过混合固态还原过程。经空气干燥和硬化的粒料可在固定床反应器在最佳停留时间加热,最佳停留时间可在0.5至4小时范围。如果采用热预还原步骤,则可在1100至1200℃范围的温度加热粒料。如果采用混合固态预还原步骤,则可将粒料在控制还原气氛加热到在900至1000℃范围的温度。还原性气体可包含以下一个或多个:CO、合成气(CO+H2)、天然气和氢气。如果利用固定床反应器,则可在反应器中通过热装料(hotburden)过滤还原性气体。应选择还原性气体流速,以达到矿中铁氧化物足够的还原产率和可接受的反应器操作性能。本发明特别用于制备要在例如DC开式电弧炉中熔炼的预还原碳基钛铁矿微粒料。然而,可用本发明的原理预还原含钛磁铁矿、铬铁矿和锰铁矿粒料,分别用于随后产生氧化钛矿渣、铬和锰合金。已涉及在固定床反应器中加热经空气干燥粒料。这只是示例而非限制。可在预还原阶段用移动床和旋转炉代替固定床反应器。重要的是使粒料磨损最大限度地减小,并且应可能从其它物质分离预还原的细粉,例如,通过使用磁力或等效的技术。附图简述进一步关于附图通过实例描述本发明,其中:图1以流程图形式说明预还原碳基钛铁矿微粒料及其随后熔炼;图2为描绘在1000℃和0.5lCO/min,停留时间对预还原和金属化度的影响的图表;并且图3为描绘在1000℃和1h停留时间,CO流速对预还原和金属化度的影响的图表。优选实施方案描述以下参考预还原碳基钛铁矿微粒料描述本发明。虽然这是本发明原理的优选应用,但可使本文所述原理适应预还原含钛磁铁矿、铬铁矿和锰铁矿。将适合尺寸的原钛铁矿10送到混合机12。混合机也接收-106微米尺寸的煤细粉14和从单一粘合剂或从混合粘合剂组合物形成的有机粘合剂16。出于实际考虑确定输入煤与钛铁矿之比。例如,可使用达到钛铁矿中的铁完全还原的化学计量比。另外,最多1%的有机粘合剂或有机粘合剂混合物输入取决于所得粒料的物理性质,特别是粒料的生料强度和空气干燥强度。所得粒料也应具有在热反应器环境中可接受的性能(随后),避免由于过度膨胀导致爆裂。混合机12产生2mm至5mm尺寸的碳基钛铁矿微粒料。然后空气干燥这些粒料(步骤20)。然后,使经空气干燥硬化粒料经过热预还原步骤22,或经过混合固态预还原步骤24。在各情况下,将经空气干燥硬化的粒料在固定床反应器26加热最佳停留时间,一般0.5至4小时。如果利用热预还原过程,则在1100至1200℃范围的温度在反应器26中加热粒料。如果利用混合法,则将粒料在反应器26中在还原性气体30的控制气氛中加热到900至1000℃温度,还原性气体包含以下一个或多个:CO、合成气、天然气和氢气。还原性气体在反应器26中通过粒料热装料过滤。调节还原性气体流速,以达到足够预还原产率。也应调节流速优化反应器操作,主要是热效率和生产成本。关于所用预还原技术的重要过程参数包括:钛铁矿晶粒尺寸分布、粒料组成、粒料尺寸、操作温度、停留时间和还原性气体流速。在一致操作条件下进行,各方法能够产生一致预还原产率。尽管在比热还原方法更低的温度操作,但混合方法似乎比热方法提供更高预还原产率。从反应器26排出的完全或部分预还原钛铁矿粒料32可冷或热进料到常规钛铁矿熔炼过程34。不受以下解释限制,相信有机粘合剂提供在钛铁矿和煤细粉之间更紧密的接触。在高度还原性气氛中的小粒料尺寸特征帮助在气体还原剂(如CO和H2)扩散中传热和传质到反应部位。有机粘合剂16在过程温度烧尽,这是在粒料32所含钛铁矿晶粒中诱导局部还原和促进形成裂纹和孔的特征。因此,增加钛铁矿粒料的比表面积,并提高气体还原剂到反应部位的扩散速率。这又影响预还原产率。可顺利有效地操作还原过程,尽管可能在升高温度发生少量粒料熔结。热或冷进料到DC开式电弧炉34的完全或部分预还原的碳基钛铁矿粒料减少炉中电力消耗,有助于处理矿渣起泡,并改善炉34输出的TiO2矿渣36的等级。已通过试验确定,通过使用在1000℃温度经2小时停留时间进行的混合预还原过程,接近完全还原粒料中的氧化铁。随着温度、停留时间和还原性气体流速增加,预还原产率增加。使用在1100至1200℃温度的热预还原过程得到约85%预还原产率,这是受钛铁矿晶粒尺寸增加和煤细粉尺寸增加不利影响的值。在DC开式电弧炉中熔炼约4吨冷预还原钛铁矿粒料。这种炉的能耗在0.6至0.7kWh/kg预还原钛铁矿粒料范围,这是代表与常规钛铁矿熔炼过程相比节省30至40%电能的数字。熔炼过程稳定,没有可见起泡迹象。产物36包含约95%TiO2和约3%FeO。因此,在熔炼操作中使用常规钛铁矿原料,可得到较高级的TiO2矿渣(高于90%),没有起泡发生。使用本发明的方法,可用较低级钛铁矿作为原料产生至少85%TiO2含量的TiO2矿渣。已参考使用气体还原剂描述了本发明。然而,可利用固体还原剂代替还原性气体30,如无烟煤或煤。也可用移动床或用旋转炉结构代替反应器26(一般为固定床反应器),其条件为在粒料之间的磨损作用最大限度地减小。然而,应可例如用磁力技术从由反应器排出的其它物质分离经预还原粒料。可用过量的另外的含碳固体还原剂使矿渣中的残余铁减少到低于6%,而不诱导熔渣起泡。发明方法中试说明为了说明熔炼预还原钛铁矿粒料,使用200kWDC电弧炉设备。炉具有衬有单层三行菱镁矿-铬砖的1m外径喷水冷却钢壳,和衬有可夯实氧化镁的炉膛。耐火衬里得到0.656m熔炉内径(ID)。炉装配有氧化铝衬里锥形顶和在穹形底上螺栓固定的壳。用单个出渣口引出熔融矿渣和金属二者的流。炉装配有作为阴极操作的40mm直径的单个位于中心的石墨电极,而阳极包括埋入炉膛的钢销。进料系统包括用于通过炉进料管送入无烟煤和预还原钛铁矿粒料的各单独料斗。炉装配有排气系统,用于在释放进入大气前清除产生的过程气体。用专用有机粘合剂以所需用量制备包含到货原样钛铁矿、化学计量量无烟煤的碳基钛铁矿粒料。到货原样钛铁矿具有38µm至150µm尺寸范围的颗粒尺寸分布D100。将无烟煤研磨到D85通过106µm,以促进其混入钛铁矿粒料配方。粒料在包括985mm直径和170mm深度倾斜旋转盘的中试规模制粒装置中制备。测定粒料的机械强度,发现随所用粘合剂类型和用量变化,在环境条件对于生粒料在0.01-0.03MPa范围内,对于硬化粒料在0.81-1.50MPa范围内。使多批各250kg的硬化粒料在1100℃控制温度操作的电加热马弗炉中还原。在3小时灼烧期间,以10分钟间隔间歇吹入总共5kgCO通过反应器负荷。将粒料装入1700mmx900mm单盘,盘具有网筛负载区域,作为还原性气体的分布空间。化学分析在不同条件的原钛铁矿材料和预还原钛铁矿材料,具体地讲,用铁氧化态(Fe3+、Fe2+和Fe0)分析计算粒料的预还原和金属化产率。全部假定钛氧化物还原可忽略,并因此基于预还原之前和之后与每克铁结合的氧的物料衡算计算预还原产率。分别用公式[1]和[2]计算预还原和金属化产率。矿和无烟煤的化学分析分别汇总于表1和表2中。表1:原钛铁矿的主体化学组成(质量%)MgOAl2O3SiO2CaOTiO2V2O5Cr2O3MnOFeOFe2+Fe0Fe/Ti0.280.440.570.0546.60.250.091.0847.8713.50<0.051.33<0.05%:由于低于检测限(LOD),分析物浓度不能精确定量样品中的总Fe表示为%FeO表2:无烟煤的主体化学组成汇总(质量%)水分灰分挥发物固定碳总碳总硫3.574.746.1989.190.70.56总共产生约3.6吨预还原粒料。将粒料装入1m3袋中,由此收集五个复合物样品。5个复合物样品的化学分析在表3中给出。表3:预还原粒料的化学组成MgOAl2O3SiO2CaOTiO2V2O5Cr2O3MnO总FeFe0Fe2+CTi3+Fe/Ti比TP袋10.530.330.310.1044.40.360.071.0534.9225.559.377.236.551.32TP袋20.550.300.260.0744.50.360.081.0635.2325.449.797.726.761.32TP袋30.500.300.240.1543.50.330.071.0333.6021.9011.77.975.451.29TP袋40.480.320.390.1142.40.330.071.0534.4622.6611.88.014.781.35TP袋50.360.450.640.1841.90.330.071.0836.0124.2111.87.204.661.43平均0.480.340.370.1243.30.340.071.0534.8423.9510.897.635.641.32标准偏差0.070.060.160.041.170.020.0040.020.901.641.210.390.980.025个复合物样品的计算预还原和金属化度显示于表4中表4:钛铁矿粒料的预还原度和金属化度复合物样品编号预还原度,%金属化度,%179.773.2278.972.2373.665.2474.165.8575.167.2平均76.368.7标准偏差2.83.7表3和4显示由于均匀炉操作条件产生预还原到一致程度的粒料。在80mm直径管式反应器中的实验室试验得到的结果显示此方法的很重要特征,在图2和3中呈现。在1000℃温度进行的试验显示,预还原和金属化度二者均与停留时间和CO流速相关。增加CO流速似乎正面影响产率,表明在此过程中CO扩散将起重要作用。进行部分还原钛铁矿粒料的连续熔炼(约70%预还原产率),以证明稳定炉操作和产生一致矿渣品质,具体地讲,矿渣TiO2等级高于85%。试验工作也有证明过程比能量需求的目的。矿渣结果显示于表5中。表5:来自稳定熔炼操作的矿渣分析,%质量出渣*TiO2Cr2O3MnOFeOV2O5SiO2CaOAl2O3MgOA84.741,341,372,060,301,310,341,966,58B87.840,601,182,590,211,160,282,493,65C83.150,311,682,730,291,200,382,767,50D88.860,450,684,890,170,490,311,452,70E88.190,450,994,370,160,430,351,533,53F91.270,311,471,580,150,280,321,473,15G94.280,081,321,250,100,210,170,981,61H93.320,091,211,480,100,160,141,102,40*由差值得到表6:来自稳定熔炼操作的生铁组成发展,%质量出渣FeTiVSiCrMnCPSA95.540.670.240.341.040.481.660.020.01B95.920.430.230.361.080.441.530.000.01C95.150.550.160.381.470.331.920.020.02D97.030.160.090.180.520.211.760.020.03E94.590.290.200.621.140.512.570.030.05F91.813.640.230.641.170.861.620.010.02G95.830.570.200.410.710.601.640.020.02H93.661.340.321.280.890.881.560.020.05达到低至1.3%矿渣FeO含量,没有可见矿渣起泡迹象。保持此条件较长时间,在此期间显示稳定炉操作,并产生一致FeO含量的矿渣。关于此具体试验工作的结果表明,熔炼部分还原钛铁矿和在矿渣中具有较低FeO含量的情况下操作炉在技术上是可能的。在115-140kW范围功率水平和在100-115V相应电压操作200kWDC开式电弧炉。检测在60-90kW范围的一致炉热损失。用光学高温计测定的平均出渣温度分散在1670和1780℃之间范围内。熔炼预还原碳基粒料的比能量需求(SER)测定在0.6-0.7kWh/kg预还原钛铁矿。可实现相对于常规熔炼方法所需的炉电力减少30-40%,假定可实现至少70%预还原产率。为了预测炉弧稳定性,对研究的不同条件测定弧电阻率。发现弧电阻率在0.0168-0.0240Ω.cm的范围内,此范围接近0.0175Ω.cm,这是在熔炼过程中利用富CO气氛(无起泡存在)的弧电阻率典型值。当前第1页1 2 3