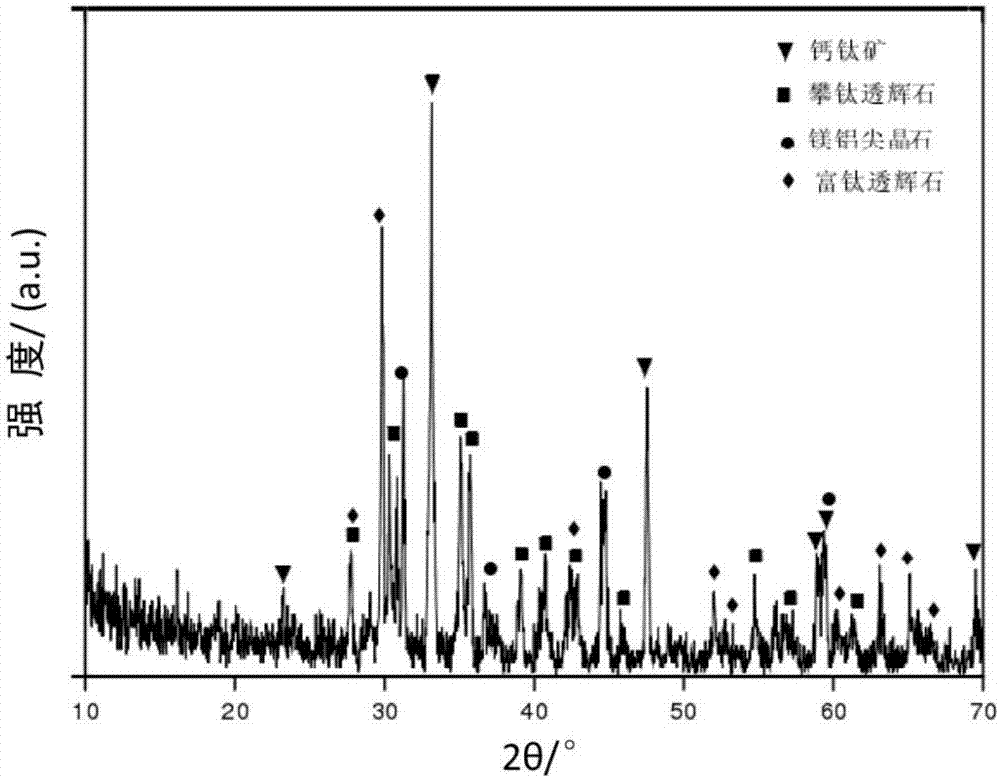
本发明涉及攀枝花钒钛磁铁矿高炉渣的回收利用
技术领域:
,尤其涉及到一种从攀枝花钒钛磁铁矿高炉渣中回收钒元素的方法。
背景技术:
:钒具有众多优异的物理性能和化学性能,用途十分广泛,有金属“维生素”之称。在钢中加入少量钒可使其弹性和强度都大增,抗磨损和抗爆裂性能极佳,既耐高温有抗奇寒。同时,钒的氧化物已成为化学工业中最佳催化剂之一。目前,提钒原料主要来自于钒矿、钢渣、石煤、废钒催化剂、石油和沥青废料等。钒钛磁铁矿是以铁、钒、钛元素为主,并伴有其他如镍、钴、铬等有价金属的多元共生铁矿。我国攀西地区蕴藏着极其丰富的钒钛磁铁矿,目前已工业化的生产方式主要提取了其中的铁和少量钒等,大量的含钒高炉渣长时间的堆积和废弃,使得大量的钒资源被浪费,不仅占用了大量土地,也带来了环境污染。按照每年约300万吨高炉渣的产生速度测算,其中每年约0.84万吨v2o5资源进入高炉渣中被废弃。因此,我们迫切需要开发一种从钒钛磁铁矿高炉渣中回收钒元素的方法。技术实现要素:本发明采用氧化焙烧-盐酸酸浸法,从攀枝花钒钛磁铁矿高炉渣中回收提取钒元素,得到了提取的最佳工艺条件,使钒的浸出率高达85.94%。本发明采用如下的技术方案:本发明的一种从攀枝花钒钛磁铁矿高炉渣中回收钒元素的方法的具体步骤如下:(1)将攀枝花钒钛磁铁矿高炉渣用粉碎机粉碎后用球磨机进行研磨,过筛得到200目的矿粉。(2)将(1)中的矿粉置于马弗炉中,在600℃下焙烧2h。(3)取5.0000g(2)中的矿粉,加入20ml9mol/l的盐酸溶液在90℃下浸出3h。(4)对(3)中的悬浊液进行过滤,得滤液。步骤(1)中过筛得到的矿粉粒度为200目。步骤(2)中焙烧温度为600℃。步骤(2)中焙烧时间为2h。步骤(3)中矿粉的质量为5.0000g。步骤(3)中盐酸浓度为9mol/l。步骤(3)中盐酸的体积为20ml。步骤(3)中浸出温度为90℃。步骤(3)中浸出时间为3h。本发明的积极效果如下:1)与常规焙烧方法相比,采用氧化焙烧法,不产生cl2、hcl和so2等有毒气体,对环境友好。2)与常规提钒方法相比,提钒效率更高,达85.94%。附图说明图1是实施例1从攀枝花钒钛磁铁矿高炉渣中回收钒元素的高炉渣的光学照片。图2是实施例1从攀枝花钒钛磁铁矿高炉渣中回收钒元素的高炉渣的x射线衍射图谱(xrd)。图3是实施例1从攀枝花钒钛磁铁矿高炉渣中回收钒元素的高炉渣的扫描电子显微镜照片(sem)。图4是在不同矿物粒度的条件下,矿物粒度与钒元素浸出率的关系图。图5是在不同的焙烧温度下,焙烧温度与钒元素浸出率的关系图。图6是在不同的焙烧时间下,焙烧时间与钒元素浸出率的关系图。图7是在不同的盐酸浓度下,盐酸浓度与钒元素浸出率的关系图。图8是在不同的固液比下,固液比与钒元素浸出率的关系图。图9是在不同的浸出温度下,浸出温度与钒元素浸出率的关系图。图10是在不同的浸出时间下,浸出时间与钒元素浸出率的关系图。图11是实施例1从攀枝花钒钛磁铁矿高炉渣中回收钒元素的高炉渣反应后的sem图。具体实施方式下面的实施例是对本发明的进一步详细描述。下述实施例中所使用的实验方法如无特殊说明,均为常规方法。下述实施例中所用的材料、试剂等,如无特殊说明,均可从商业途径得到。实施例1为实现上述目的,具体从攀枝花钒钛磁铁矿高炉渣中回收钒元素的方法步骤为:1)将攀枝花钒钛磁铁矿高炉渣用粉碎机粉碎后用球磨机进行研磨,过筛得到200目的矿粉。2)将(1)中的矿粉置于马弗炉中,在600℃下焙烧2h。3)取5.0000g(2)中的矿粉,加入20ml9mol/l的盐酸溶液在90℃下浸出3h。4)对(3)中的悬浊液进行过滤,得滤液。以下结合附图实施例对本发明作进一步详细描述:攀枝花钒钛磁铁矿高炉渣的的光学照片(图1)中显示其呈现出灰黑色的块状固体结构,表面覆盖黄色泡沫状固体,质地坚硬致密。在室温下测得的xrd图(图2)中可以看出其主要矿相为钙钛矿、攀钛透辉石、镁铝尖晶石和富钛透辉石,由于钒含量较低(1%左右),因此在xrd中衍射峰不明显。过筛后矿粉的扫描电子显微镜(sem)(图3)确定了炉渣具有致密的块状结构,几乎没有裂缝合孔隙,使得炉渣硬度高,这与肉眼观察到的外观一致。其x射线荧光光谱分析(xrf)结果见表1。表1攀枝花某厂自然冷却的含钛型高炉渣化学成分/(质量分数,%)成分caosio2tio2al2o3mgofe2o3v2o5mnocs其余含量26.9824.8216.8913.577.611.391.060.61.250.665.17我们采用球磨机研磨得到了不同粒度的矿粉,考察的粒度对浸出率的影响。实验结果显示(图4)炉渣越细,钒的浸出效率越高。矿物与酸接触的表面积随着炉渣粒度的减小而增大,捕获h+及能量的障碍越小,越有利于h+进入矿物晶格中,破坏晶格从而将钒释放出来。从理论上说,矿物粒度越小,越有利于钒的浸出,但在实际生产过程中,随着矿物粒度的减小,操作工艺也随之复杂化,所以选择200目。通过设置不同的焙烧温度,考察了焙烧温度对钒浸出率的影响。实验结果显示(图5)随着焙烧温度的增加,钒的浸出率不断提高。当焙烧温度达到650℃时,矿粉开始部分烧结,对浸出率有所影响。当焙烧温度达到800℃时,矿粉完全烧结。且焙烧温度在大于600℃时钒的浸出率增加幅度开始减小,所以选择最佳焙烧温度为600℃。随后我们还考察了焙烧时间对钒浸出率的影响,实验结果见图6。我们发现焙烧时间短,低价钒不能充分氧化成五价钒氧化物。当钒基本氧化完全后,浸出率就不会有提升,而且会浪费能源。焙烧时间太短或者太长都不利于钒的浸出,所以适宜的焙烧时间为2h。而钒的浸出率随浸出剂(hcl)浓度的增大而升高(图7),由化学反应动力学分析,溶液中酸的浓度越高,反应越容易进行。这是由于h+浓度增大,进入矿物晶格的几率就越大,越有利于破坏矿物的结构,增加钒的浸出率。但随着盐酸浓度的增加浸出率逐渐趋于平稳。提升盐酸浓度并不经济,所以选择盐酸的浓度为9mol/l。同时,盐酸体积也会影响钒的浸出率(图8),当固液比小时,矿浆的粘度大,外扩散阻力大,氢离子不易与钒氧化物接触,不利于反应的进行。固液比过大,会增加浸出剂的用量,降低浸出液中钒的浓度,所以选择固液比为1:4(即20ml盐酸溶液)。通过设置不同的浸出温度,考察了浸出温度对钒浸出率的影响(图9)。结果显示,在常温下,钒的浸出率很低。随着温度的升高,分子热运动加剧,浸出剂的反应活性也得以加强,使浸出更易进行。同时,在升温条件下浸出液的粘度降低,20℃和90℃的浸出液粘度相差很大,溶液粘度的降低,有利于提高分子的扩散速度,从而提高钒的溶解速度。温度升高,氢离子也能更容易的进入矿物晶格,破坏矿石结构,提高钒的浸出率。但是温度也不能过高,温度过高容易使浸出液沸腾沾出造成浸出液浪费也易造成冒槽,腐蚀设备。所以适宜的浸出温度为90℃。而随着反应时间的增加,钒浸出率增高(图10),钒能被持续浸出。在2h时,浸出率为84.96%。在3h时,浸出率为85.94%。进一步延长浸出时间时浸出率浸出减缓,说明绝大部分的钒已经进入的液相,浸出率提升不大,所以选择浸出时间为3h。通过对比焙烧-酸浸前后矿粉的sem照片我们发现,在反应结束后(图11),其晶体结构遭到了破坏,出现了大量的狭缝和空隙,含钒离子更容易进入液相。尽管已经示出和描述了本发明的实施例,对于本领域的普通技术人员而言,可以理解在不脱离本发明的原理和精神的情况下可以对这些实施例进行多种变化、修改、替换和变型,本发明的范围由所附权利要求及其等同物限定。当前第1页12