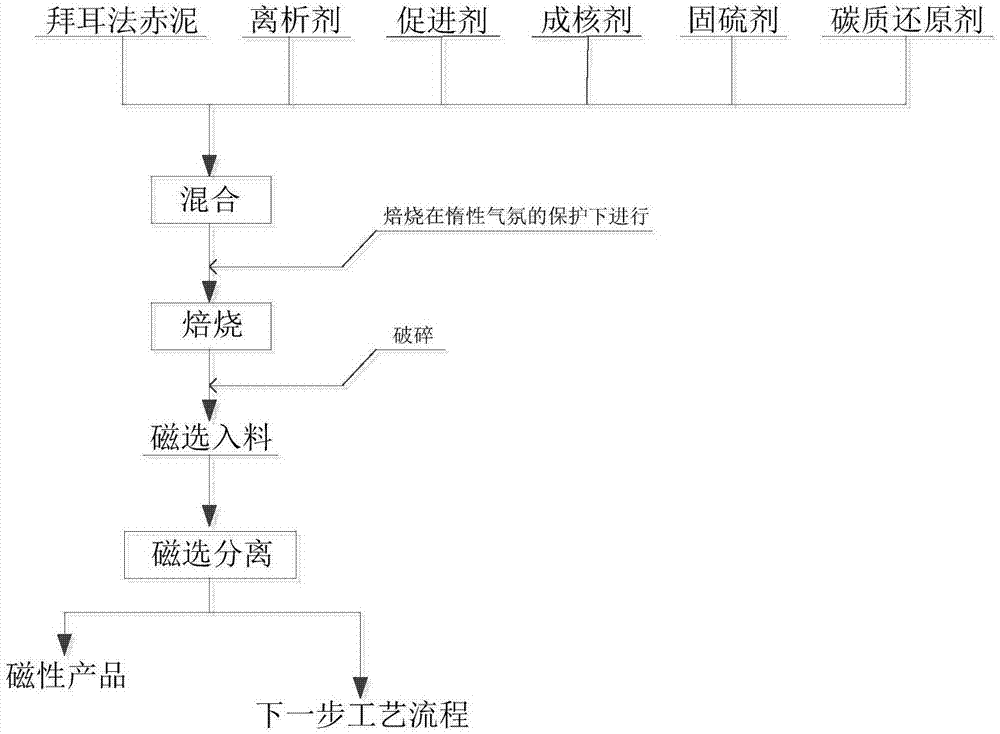
本发明涉及工业废料再利用及环保领域,具体涉及一种拜耳法赤泥还原焙烧提铁的方法。
背景技术:
赤泥是氧化铝生产过程中排放的强碱性固体废弃物,其因氧化铁含量较高(一般介于10%-30%之间),呈与赤色泥土相似的红色,故称赤泥。我国是世界最大的氧化铝生产和消费国,氧化铝产量约占世界35%-40%。目前氧化铝生产方法主要有拜耳法、烧结法和联合法三种,拜耳法工艺,每生产1t氧化铝排放赤泥1-1.5t。烧结法及联合法工艺,每生产1t氧化铝排放赤泥1.5-2.5t赤泥。截止2015年,全球赤泥堆存量超过35亿吨,并以每年1.2亿吨的速度增加。目前,我国每年赤泥排放量达到6000万吨,赤泥总堆存量超过6亿吨。其中氧化铝生产90%都采用拜耳法,铁矿石的分选主要采用磁选设备进行分离,但是,拜耳法赤泥中的铁多为弱磁性氧化铁fe2o3,即使采用磁场强度较高的磁选机进行回收,仍然不能达到理想效果。加上近年来钢铁价格不断下降,因此,在当前经济和技术条件下拜耳法赤泥提铁难以实现工业化。赤泥碱性强、盐分含量高,其生态化处置及资源化利用一直受强碱性制约而难以有效进行,外排赤泥以堆存为主,堆存过程中存在多种环境风险。赤泥高碱性、高盐分、有机物含量低、植物营养物质匮乏等化学特性抑制了植物在堆场的生长,对堆场植被重建极为不利。赤泥颗粒细小、na含量高,堆场表层返碱时有发生,形成的碱性粉尘污染空气(干法堆存的赤泥),危害周边植物及堆场工作人员的安全。赤泥颗粒容重大、导水率低,赤泥坝上容易发生水涝。赤泥中al、as、v等在强碱环境下迁移能力较大,na+和al3+浓度高,赤泥附液生物毒性强,一旦发生渗透对人体和植物的危害较大。到目前为止国内外一直还没有找到一种有效的赤泥利用途径。目前赤泥的主要处理方式是筑坝堆存,直接填海或者中和后填海。我国山东、河南、贵州、山西、广西等氧化铝厂,多处于内陆地区,采用平地高台、河谷拦坝、凹地充填等方法堆存赤泥。拜耳法赤泥中含的铁往往会导致其他有用组分不能得以综合利用,因此把拜耳法赤泥中的铁提前收回,有利于其他组分的回收。目前国内外针对赤泥综合回收利用进行了大量研究,主体工艺主要集中在还原焙烧—碱浸和直接酸浸等。但回收拜耳法赤泥中的铁主要采用化学浸出法,这不仅消耗大量的酸、碱等化学试剂,而且,化学试剂易腐蚀损坏设备,对设备质量要求较高。由于赤泥成分复杂,存在包裹性、碱性、等问题,赤泥的无害化综合利用成为世界性难题。目前的处理方法均存在利用率不足或成本高、工艺复杂的缺点。因此,开发赤泥的可行性综合回收利用新技术,具有重大的意义。赤泥中的铁由于晶粒特别细小,大部分都会被其他矿物包裹,尤其是被云母所包裹,若直接进行还原焙烧,则会存在两个比较明显的问题:首先是铁被赤泥中造岩矿物或其他矿物所包裹,难以进行解离和还原;接着就是由于赤泥中的铁由于晶粒过小,即使在焙烧中被还原成低价态的磁性氧化物,在磁选过程中也不能被磁选机分离出来。技术实现要素:针对现有技术中赤泥难处理、利用率低,工艺复杂、易造成二次污染等的现状提出一种工艺简单、环境友好、高效的拜耳法赤泥还原焙烧提铁的方法。为了实现上述目的,本发明采用如下技术方案:将拜耳赤泥与离析剂、促进剂、成核剂、固硫剂、还原剂混合获得混合生料,将混合生料还原焙烧获得还原产物,还原产物经磁选获得铁精矿;所述离析剂为含氯化合物,其添加量为赤泥质量的3-10wt%;所述促进剂为含钠化合物,其添加量为赤泥质量的5-15wt%;所述成核剂为含铁化合物,其添加量为赤泥质量的3-8wt%;所述固硫剂为含钙化合物,其添加量为赤泥质量的5-12wt%;所述还原剂为固体碳,其添加量为赤泥质量的5-15wt%;所述含铁化合物为熔点≤1171℃的还原性含铁化合物。在本发明的技术方案中,在还原焙烧的过程中添加了离析剂、促进剂、成核剂、固硫剂、还原剂;所添加的离析剂(含氯化合物)进行氯化离析,破坏拜耳赤泥的包裹体结构,使包裹在里面的铁分离出来进行还原焙烧在还原剂表面还原为金属铁颗粒。为了减少氯化物对设备和环境的危害程度以及加快铁的离析速度,加入促进剂(含钠化合物),在高温下钠盐易融解形成液相,强化还原过程中的传质,另外,钠离子在熔融状态下穿透能力较强,更有利于铁的分离。同时加入成核剂,所述成核剂同时具有较低的熔点,也具有还原性,能够在其表面直接发生还原反应,就地使新生态的铁优先聚集在周围,并促进铁晶核形成与长大;起到成核剂的作用,另外再加入含钙化合物作为固硫剂,既可以对焙烧过程中产生含硫气体起到固硫作用,又可以形成硅酸钙等热力学更稳定的物质,促进包裹体铁的分离,方便铁的还原与富集。优选的方案,所述含氯化合物的添加量为赤泥质量的3-6wt%。优选的方案,所述含氯化合物选自氯化钠、氯化钙、氯化镁中的至少一种。在本发明中,当所加入的离析剂为氯化钠时,其同时作为离析剂和促进剂,若额外再加入促进剂,其添加量需减去所加入氯化钠的质量。以防加入的促进剂的量过大。发明人发现,所加入促进剂的量过大,会使得在成核剂的作用下使聚集在一起的铁重新分散。影响反应效果。优选的方案,所述的含钠化合物选自碳酸钠、氢氧化钠、硅酸钠中的至少一种。优选的方案,所述含铁化合物的添加量为3-5wt%。优选的方案,所述的含铁化合物为fes2。发明人发现,成核剂的加入可以促进铁晶核形成与长大,大幅降低磁选分离的难度。磁选效率随着含铁化合物的量的增大而增大,当含铁化合物的添加加达到3%时,铁的回收率即可大于3%,当含铁化合物的添加量≥5wt%时,铁的回收率不再出现波动,故优选为3-5wt%。优选的方案,所述含钙化合物的添加量为赤泥质量的6-10wt%。作为更进一步的优选,所述含钙化合物的添加量为赤泥质量的7-10wt%。优选的方案,所述含钙化合物选自碳酸钙、氧化钙、氢氧化钙中的至少一种。在本发明中,氯化钙同时作为离析剂和固硫剂,若额外再加入固硫剂,其添加量需减去所加入氯化钙的质量。以防加入的固硫剂的量过大。优选的方案,所述固体碳的添加量为赤泥质量的8-15wt%。作为进一步的优选,所述固体碳的添加量为赤泥质量的11-15wt%。优选的方案,所述固体碳选自活性炭、烟煤、无烟煤、焦炭中的至少一种。作为进一步的优选,所述固体碳选自活性炭、烟煤中的至少一种在本发明的技术方案中,对赤泥的粒径没有过多的限制,无需进行磨矿直接与离析剂、促进剂、成核剂、固硫剂、还原剂混合即可。优选的方案,所述还原焙烧在惰性气氛的保护下进行。作为进一步的优选,所述惰性气氛选自氮气和/或氩气。优选的方案,所述还原焙烧的温度为1000℃-1250℃。发明人发现,温度过低还原的铁聚集颗粒较小,过高则会使被烧物质容易玻璃化。作为进一步的优选,所述还原焙烧的温度为1200℃-1250℃。优选的方案,所述还原焙烧的时间为0.5-1h。发明人发现,焙烧时间不足会导致铁颗粒来不及聚集,过长则又会使还原的铁氧化。优选的方案,所述还原产物在惰性气氛的保护下冷却至室温后,磨细至还原产物中的粒径小于0.074mm的颗粒的质量占还原产物总质量的80%及以上,然后对磨细后的还原产物进行磁选分离,得到磁性产品和非磁性残渣。优选的方案,所述磁选分离的磁场强度为1000-2000gs。作为进一步的优选,所述磁选分离的磁场强度为1600-2000gs。本发明的有益效果:采用上述技术方案的拜耳赤泥还原焙烧过程中添加添加剂的方法,以少量氯化物为基质作离析剂,通过添加促进剂含钠化合物、成核剂铁化合物、固硫剂钙类化合物、碳质还原剂等等构成添加剂,能显著改善并提高赤泥中铁的还原程度与增大凝聚态还原铁颗粒粒径,能显著促进铁的金属化,提高铁的回收率与品位。本发明与现有技术相比具有以下优点:1、本发明在还原焙烧的过程中添加离析剂(氯化物)进行氯化离析,破坏包裹体结构,使包裹在里面的铁分离出来进行还原焙烧。2、本发明为了减少氯化物对设备和环境的危害程度以及加快铁的离析速度,在离析剂中加入促进剂(含钠化合物),在高温下钠盐易融解形成液相,强化还原过程中的传质,另外,钠离子在熔融状态下穿透能力较强,更有利于铁的分离。3、本发明过程中在离析剂中加入成核剂(fes2),fes2具有较低的熔点,也具有还原性,能够在其表面直接发生还原反应,就地使新生态的铁优先聚集在周围,起到成核剂的作用,有利于铁颗粒的形成与长大。4、本发明所添加的钙类化合物,既可以对焙烧过程中产生含硫气体起到固硫作用,又可以形成硅酸钙等热力学更稳定的物质,促进包裹体铁的分离,方便铁的还原与富集。5、本发明对环境友好,铁的回收率可高达90%以上,品位可达60%以上。附图说明图1是本发明的工艺流程图。具体实施方式本发明由下列实施例进一步说明,但不受这些实施例的限制。实施例1拜耳法赤泥取自河南某地,拜耳法原料为一水硬铝石和三水软铝石,全铁含量23.17%。按照上表的比例与拜耳法赤泥混匀;将混合生料置于高温炉中在1000℃下焙烧30min;继续再惰性气体下冷却至室温后磨细至80%≤0.074mm;精磨细后的烧结熟料于磁选分离得到磁性产品和非磁性残渣,其中磁选磁场强度为1000gs;磁性产品可直接作为铁精矿产品,非磁性产品可以作为下一步工艺处理的原料。采用本方法获得的各技术指标如下:磁性铁精矿铁品位为60.6%,铁回收率为90.3%。实施例2拜耳法赤泥取自贵州某地,拜耳法原料以一水硬铝石为主,全铁含量20.79%。组分名称具体化合物用量,%(相对于赤泥的质量)离析剂氯化钙4促进剂碳酸钠8成核剂fes24固硫剂氢氧化钙6还原剂烟煤12按照上表的比例与拜耳法赤泥混匀;将混合生料置于高温炉中在1100℃下焙烧40min;继续再惰性气体下冷却至室温后磨细至80%≤0.074mm;精磨细后的烧结熟料于磁选分离得到磁性产品和非磁性残渣,其中磁选磁场强度为1200gs;磁性产品可直接作为铁精矿产品,非磁性产品可以作为下一步工艺处理的原料。采用本方法获得的各技术指标如下:磁性铁精矿铁品位为63.6%,铁回收率为90.1%。实施例3拜耳法赤泥取自山东某地,拜耳法原料以三水软铝石为主,全铁含量26.01%。组分名称具体化合物用量,%(相对于赤泥的质量)离析剂氯化镁3促进剂氢氧化钠5成核剂fes23固硫剂碳酸钙7还原剂烟煤11按照上表的比例与拜耳法赤泥混匀;将混合生料置于高温炉中在1200℃下焙烧50min;继续再惰性气体下冷却至室温后磨细至80%≤0.074mm;精磨细后的烧结熟料于磁选分离得到磁性产品和非磁性残渣,其中磁选磁场强度为1600gs;磁性产品可直接作为铁精矿产品,非磁性产品可以作为下一步工艺处理的原料。采用本方法获得的各技术指标如下:磁性铁精矿铁品位为61.6%,铁回收率为91.2%。实施例4拜耳法赤泥取自山东某地,拜耳法原料以三水软铝石为主,全铁含量26.01%。按照上表的比例与拜耳法赤泥混匀;将混合生料置于高温炉中在1200℃下焙烧50min;继续再惰性气体下冷却至室温后磨细至80%≤0.074mm;精磨细后的烧结熟料于磁选分离得到磁性产品和非磁性残渣,其中磁选磁场强度为1600gs;磁性产品可直接作为铁精矿产品,非磁性产品可以作为下一步工艺处理的原料。采用本方法获得的各技术指标如下:磁性铁精矿铁品位为62.1%,铁回收率为91.9%。实施例5拜耳法赤泥取自广西某地,拜耳法原料以一水硬铝石为主,全铁含量24.72%。组分名称具体化合物用量,%(相对于赤泥的质量)离析剂氯化钠5促进剂碳酸钠10成核剂fes24固硫剂碳酸钙9还原剂活性炭15按照上表的比例与拜耳法赤泥混匀;将混合生料置于高温炉中在1250℃下焙烧60min;继续再惰性气体下冷却至室温后磨细至80%≤0.074mm;精磨细后的烧结熟料于磁选分离得到磁性产品和非磁性残渣,其中磁选磁场强度为2000gs;磁性产品可直接作为铁精矿产品,非磁性产品可以作为下一步工艺处理的原料。采用本方法获得的各技术指标如下:磁性铁精矿铁品位为63.6%,铁回收率为93.2%。实施例6拜耳法赤泥取自山东某地,拜耳法原料以三水软铝石为主,全铁含量26.01%。组分名称具体化合物用量,%(相对于赤泥的质量)离析剂氯化镁6促进剂氢氧化钠5成核剂fes28固硫剂碳酸钙7还原剂烟煤11按照上表的比例与拜耳法赤泥混匀;将混合生料置于高温炉中在1200℃下焙烧50min;继续再惰性气体下冷却至室温后磨细至80%≤0.074mm;精磨细后的烧结熟料于磁选分离得到磁性产品和非磁性残渣,其中磁选磁场强度为1600gs;磁性产品可直接作为铁精矿产品,非磁性产品可以作为下一步工艺处理的原料。采用本方法获得的各技术指标如下:磁性铁精矿铁品位为62.3%,铁回收率为92.1%。对比例1拜耳法赤泥取自河南某地,拜耳法原料为一水硬铝石和三水软铝石,全铁含量23.17%。经检测,拜耳赤泥中无氯元素。按照上表的比例与拜耳法赤泥混匀;将混合生料置于高温炉中在1000℃下焙烧30min;继续再惰性气体下冷却至室温后磨细至80%≤0.074mm;精磨细后的烧结熟料于磁选分离得到磁性产品和非磁性残渣,其中磁选磁场强度为1000gs;磁性产品可直接作为铁精矿产品,非磁性产品可以作为下一步工艺处理的原料。采用本方法获得的各技术指标如下:磁性铁精矿铁品位为52.3%,铁回收率为84.1%。对比例2拜耳法赤泥取自贵州某地,拜耳法原料以一水硬铝石为主,全铁含量20.79%。组分名称具体化合物用量,%(相对于赤泥的质量)离析剂氯化钙4成核剂fes24固硫剂氢氧化钙6还原剂烟煤12按照上表的比例与拜耳法赤泥混匀;将混合生料置于高温炉中在1100℃下焙烧40min;继续再惰性气体下冷却至室温后磨细至80%≤0.074mm;精磨细后的烧结熟料于磁选分离得到磁性产品和非磁性残渣,其中磁选磁场强度为1200gs;磁性产品可直接作为铁精矿产品,非磁性产品可以作为下一步工艺处理的原料。采用本方法获得的各技术指标如下:磁性铁精矿铁品位为54.3%,铁回收率为84.7%。对比例3拜耳法赤泥取自贵州某地,拜耳法原料以一水硬铝石为主,全铁含量20.79%。组分名称具体化合物用量,%(相对于赤泥的质量)离析剂氯化钙4促进剂碳酸钠8固硫剂氢氧化钙6还原剂烟煤12按照上表的比例与拜耳法赤泥混匀;将混合生料置于高温炉中在1100℃下焙烧40min;继续再惰性气体下冷却至室温后磨细至80%≤0.074mm;精磨细后的烧结熟料于磁选分离得到磁性产品和非磁性残渣,其中磁选磁场强度为1200gs;磁性产品可直接作为铁精矿产品,非磁性产品可以作为下一步工艺处理的原料。该对比例的其他条件与实施例2相同,仅未加入成核剂,铁回收率在降低,发明人发现,该对比例中所形成的铁晶粒尺寸远小于实施例2中所获得的铁晶粒的尺寸。采用本方法获得的各技术指标如下:磁性铁精矿铁品位为56.9%,铁回收率为40.7%。对比例4拜耳法赤泥取自广西某地,拜耳法原料以一水硬铝石为主,全铁含量24.72%。按照上表的比例与拜耳法赤泥混匀;将混合生料置于高温炉中在1250℃下焙烧60min;继续再惰性气体下冷却至室温后磨细至80%≤0.074mm;精磨细后的烧结熟料于磁选分离得到磁性产品和非磁性残渣,其中磁选磁场强度为2000gs;磁性产品可直接作为铁精矿产品,非磁性产品可以作为下一步工艺处理的原料。从该实施例可以看出,促进剂过量,铁回收率降低,这是因为促进剂过量会使得聚集的铁晶粒重新分散。采用本方法获得的各技术指标如下:磁性铁精矿铁品位为48.3%,铁回收率为67.5%。对比例5拜耳法赤泥取自山东某地,拜耳法原料以三水软铝石为主,全铁含量26.01%。组分名称具体化合物用量,%(相对于赤泥的质量)离析剂氯化镁6促进剂氢氧化钠5成核剂fes22固硫剂碳酸钙7还原剂烟煤20按照上表的比例与拜耳法赤泥混匀;将混合生料置于高温炉中在1200℃下焙烧50min;继续再惰性气体下冷却至室温后磨细至80%≤0.074mm;精磨细后的烧结熟料于磁选分离得到磁性产品和非磁性残渣,其中磁选磁场强度为1600gs;磁性产品可直接作为铁精矿产品,非磁性产品可以作为下一步工艺处理的原料。发明人发现,还原剂过量,而成核剂不足时,过量的还原剂会阻碍晶粒的增长,另一方面,还原剂过量会消除某些磁性铁的磁性。采用本方法获得的各技术指标如下:磁性铁精矿铁品位为51.7%,铁回收率为79.9%。当前第1页12