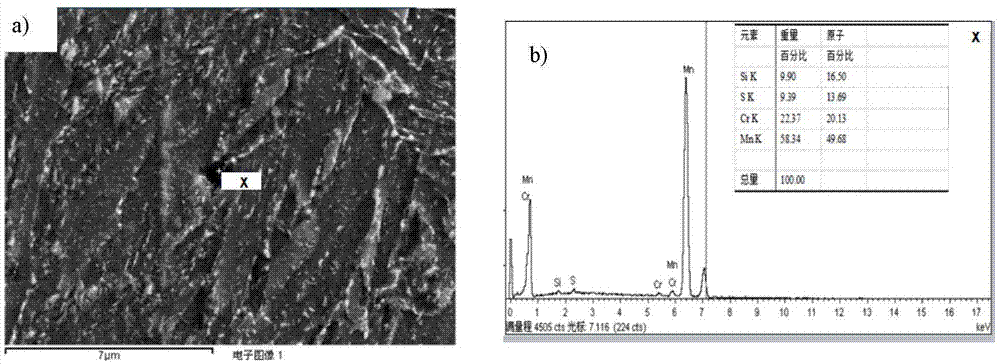
本发明涉及抗硫化氢应力腐蚀的125ksi级无缝油套管用钢及其制备工艺。
背景技术:
自上个世纪50年代初,在加拿大的阿尔伯达平切尔湾油田发生油井管硫化氢应力腐蚀开裂事故以来,世界各地的油气田陆续发生了硫化氢应力腐蚀开裂事故,引起了世界各地石油行业、钢铁行业的重视。研究发现,世界油气田中约有1/3含有硫化氢气体。普通套管应用于含硫油气田中,会在所受应力远远小于其屈服强度时突然发生断裂,轻者发生套管柱或是整口井报废,重者造成井喷,使硫化氢随着油气一同外溢,导致整台钻机及周围生态遭到巨大破坏。随着能源资源需求量的不断增加,研究开发高性能抗硫化氢应力腐蚀油套管(以下简称抗硫油井管)已引起世界各国的高度关注。自上个世纪60年代开始,日本和美国的油套管生产企业,例如:日本住友公司、jfe、v&m,率先开展了抗硫油套管的研究开发工作,陆续研发成功80ksi级、95ksi和110ksi级抗硫油套管并投入应用。国内宝钢、首钢、天津钢管厂、南钢、鞍钢等企业自上世纪90年代开始也陆续研发出c90、80ss、bgm65等多个级别的抗硫油套管并相继投入生产,目前t95及c110ksi级别的抗硫油套管正处于研制和小批量试生产阶段。近年,随着腐蚀性低的浅井不断枯竭,腐蚀性高的高压深井开发数量在不断增加,例如北美洲的南得克萨斯、密西西比气藏含硫化氢体积分数分别高达98%和78%;中国华北的赵兰庄油气藏、四川的部分气藏含硫化氢体积分数分别高达92%和17%。此外,随着钻井深度不断增加,耐硫油套管所承受的分压越来越高,再考虑到井内温度等恶劣环境因素,使得研究开发125ksi级别、甚至更高级别抗硫油套管用钢已成为一种必然趋势。钢材的强度和其抗硫化氢应力腐蚀性能成对立关系,即强度越高,其抗硫化氢应力腐蚀性能越弱,所以,开发高强度抗硫化氢应力腐蚀钢已成为世界级的技术难点。随着科研工作的不断深入,世界各地的研究学者们相继发现,淬火后的回火马氏体是理想的抗硫化氢应力腐蚀组织。另一普遍认同的观点是细化晶粒,无论是从增加强度还是增加抗硫化氢应力开裂能力方面都是有益无害的。还有一个被大家所共同接受的观点是,钢中第二相的形态及分布状态严重影响着钢材的抗硫化氢应力腐蚀性能,其中长条状的mns夹杂常常是导致硫化氢应力腐蚀开裂的裂纹源起点;此外,还有在晶界/亚晶界处析出巨大的碳化物m23c6也有可能成为裂纹源起点之说。技术实现要素:为解决现有技术的问题,本发明提供一种125ksi抗硫化氢应力腐蚀高强油套管用钢及其制备工艺,在满足抗硫化氢应力腐蚀的基础上提高油套管的强度,使之达到125ksi-140ksi之间,并降低油井管的制造成本。本发明提供一种125ksi抗硫化氢应力腐蚀高强油套管用钢,其化学成分按质量百分比为:c:0.08-0.27%,si:0.1-0.5%,mn:0.15-1.8%,cr:0.3-1.0%,mo:0.4-1.0%,v:0.05-0.4%,ti:0.01-0.1%,cu:0.1-0.7%,ni:0.2-3.0%,b:0.0001-0.002%,p:0-0.015%,s:0-0.010%,o:0-0.06%,n:0-0.05%,h:0-0.05%,其余由fe及不可避免的杂质组成。根据上文技术方案,优选的情况下,所述油套管用钢还包括化学成分按质量百分比为:al:0-0.005%,nb:0-0.2%,ca:0-0.008%,ce:0-0.03%,zr:0.0005-0.01%,rem:0.003%-0.05%,mg:0.0005-0.02%中的一种或几种。即用al:0-0.005%,nb:0-0.2%,ca:0-0.008%,ce:0-0.03%,zr:0.0005-0.01%,rem:0.003%-0.05%,mg:0.0005-0.02%,组成的一种或是多种代替所述的fe的一部分。本发明125ksi抗硫化氢应力腐蚀高强油套管用钢按照上述设定的化学组成冶炼、经过热轧及热处理过程,其最终的力学性能满足:屈服强度:862-1034mpa,抗拉强度≧930mpa,0℃冲击功≧100j。该钢种在加载强度为85%×862mpa下,并浸泡在nace-a溶液中720h内不出现断裂,满足国际标准的抗硫化氢应力腐蚀nace-a试验要求。本发明还涉及保护一种由125ksi抗硫化氢应力腐蚀高强油套管用钢制得的油套管。本发明还提供一种125ksi抗硫化氢应力腐蚀高强油套管用钢的制备工艺,步骤如下:(1)按照上述设定的化学组成利用氧化物冶金工艺及真空中频炉冶炼技术在真空感应炉或真空中频炉中进行冶炼成钢锭,将钢锭锻造成方坯;(2)将步骤(1)获得的方坯加热后热轧成钢板,而后冷却至马氏体相变完成的温度mf以下或室温;所述冷却的方式为空冷、水冷或tmcp冷却;(3)将步骤(2)热轧冷却后的钢板进行热处理,所述热处理的工艺包括淬火和回火;具体为:将步骤(2)热轧冷却后的钢板进行淬火,冷却至马氏体相变完成的温度mf以下或室温,将淬火冷却后的钢板进行回火再冷却至室温,最终制成125ksi抗硫化氢应力腐蚀高强油套管用钢(抗硫化氢腐蚀耐油管道用钢、低碳低合金抗腐蚀耐硫套管用钢);其中所述淬火温度控制在830-950℃,保温时间30-90min;所述回火温度500-790℃,保温时间30-150min;所述淬火后的冷却方式为水淬、油淬或喷淋水冷却;所述回火后的冷却方式为缓冷或空冷。根据上文技术方案,优选的情况下,步骤(1)中所述方坯的边长为80-120mm。根据上文技术方案,优选的情况下,步骤(2)中所述方坯加热到1150-1250℃下保温1.5-5h。根据上文技术方案,优选的情况下,步骤(2)中热轧钢板的厚度为13-16mm。根据上文技术方案,优选的情况下,步骤(3)中所述热处理还包括正火,所述部分热轧冷却后的钢板在进行淬火和高温回火前还需先进行正火再冷却至室温,所述正火温度根据钢的具体成分控制在ac3以上30-50℃之内,即860-950℃之间,正火保温时间根据热轧钢板的厚度控制在10-40min之内。本发明的低碳低合金抗腐蚀耐硫套管用钢的组织为回火马氏体组织,部分钢材中包含少量下贝氏体组织。另外,本发明采用氧化物冶金和提高回火温度相结合的方法,降低位错密度并通过生成纳米尺寸的微细第二相质点来钉扎位错。本发明的有益效果:本发明的抗硫化氢应力腐蚀高强油套管用钢具有862mpa(125ksi)以上的屈服强度,抗硫化氢应力腐蚀性能满足国际标准nace-a实验。本发明根据nace和api标准中对高强度抗硫油套管化学成分的规定及建议,结合各元素在钢种的作用,设定抗硫化氢应力腐蚀高强油套管用钢的化学成分如下:碳(c):质量百分比0.08-0.27%碳(c)是决定钢板性能的基本元素,含碳量不同,钢板的强度、硬度、韧性和塑性也不同,即:增加含碳量能显著提高钢板强度,但同时降低钢的韧性和塑性,显著恶化钢板的抗腐蚀性能。综合高强度和抗硫化氢应力腐蚀性能考虑后,将高强耐硫油套管用钢的c含量设计在0.08-0.27%之间。硅(si):质量百分比0.1-0.5%硅(si)在炼钢过程中起至关重要的作用,具有还原和脱氧的作用。此外,si还是确保钢板强度的有效元素之一,会对强度及韧性产生重要影响,因为si可以提高钢中固溶体的硬度和强度,增加钢的淬透性;且由于其热稳定性好,还增加钢淬火后的抗回火性,使钢能在较高温度下回火,从而改善钢的韧性和耐延迟断裂性能。但是si含量过高会使钢的导热性变差,钢锭、钢坯表面易出现开裂或裂纹缺陷。故si的含量设定在0.1-0.5%之间。锰(mn):质量百分比0.15-1.8%锰(mn)在钢中作为固溶强化元素而存在,可确保钢板强度并有利于韧性,高的mn/c比对提高屈服强度和冲击韧性是有益的;对于低合金高强钢采取降c增mn的措施,在提高强度的同时也能够获得良好的韧性。但由于锰是一种易偏析元素,促进有害元素p、s、sn、sb等向晶界偏析,形成偏析带,造成钢的组织和硬度不均匀;且偏析后位于晶界处的p、sn、sb等容易与h发生交互作用,从而使得晶界键合力大幅度下降,容易引起氢致沿晶断裂,对抗硫化氢性能不利,因此对于钢中的锰含量应进行限制。另外,mn具有降低钢的马氏体转变温度的作用,当偏析区mn、c含量达到一定比例时,极易在热轧后的冷却过程中产生对ssc极为敏感的马氏体、贝氏体组织。为保证钢板的高强度和良好韧性,限制氢致断裂,故mn的范围确定在0.15-1.8%之间。铬(cr):质量百分比0.3-1.0%铬(cr)能够通过提高钢的淬透性进而提高钢材的强度和硬度,而且,当钢材加入其他合金元素时该效果更为显著。cr是弱氧化元素,在冶炼过程中会具有一定的脱氧能力,利于调节氧含量。此外,cr可以降低ar3点,可进一步增加晶粒的细化效果。添加少量的cr显著增强了对co2气体腐蚀的抵抗力,因为cr在腐蚀产物膜中聚集,使其稳定性高于一般碳钢的腐蚀产物膜。另,cr元素含量增加会使得缓解平均腐蚀和局部腐蚀的积极作用减弱,但随着钢中含cr量的增加,出现最大腐蚀速率的温度上升。在高温条件下,cr元素存在增加局部腐蚀的倾向。适量减少钢材的含c量,抑制基体中形成cr元素析出生成cr的碳化物也能提高钢基体的抗ssc性能。钼(mo):质量百分比0.4-1.0%微量mo元素可以提高钢的淬透性及回火稳定性,从而提高钢的强度,改善钢的延展性和韧性;mo也可以降低ar3点,可进一步增加晶粒的细化效果。经高温回火后钢中呈高度弥散分布的碳化物mo2c能够固定钢中的可扩散氢,使得可扩散富集的氢含量大大降低,防止氢向脆弱的晶界聚集,这些碳化物是有益的强陷阱,可以有效地提高强度、细化晶粒、强化晶界;mo还可以阻碍p偏析;当mo与硫s发生反应时,一方面可以降低基体中的s含量,另一方面,形成弥散状的mos2,起到细化晶粒、提高材料的抗硫化氢应力腐蚀特性和局部腐蚀抗力。钒(v):质量百分比0.05-0.4%由于钒(v)的溶解温度较低,溶解度很大,只会产生中等程度的沉淀强化和比较弱的晶粒细化,阻止再结晶的效果较弱。钒仅在900℃以下对再结晶才有推迟作用,在奥氏体转变以后,钒几乎已完全溶解,所以钒几乎不在奥氏体中形成析出物。但在γ/a转变过程中或转变之后可大量析出产生析出强化,可大幅度提高钢材强度。v在钢中一般会以c、n化物或其复合化物析出,或形成高密度的位错结,对位错起到钉扎作用,可提高抗ssc性能。v与n结合生成的vn,尺寸细小,但体积分数很高,常会依附在其它类型夹杂物表面,对细化晶内组织、提高韧性产生有益作用。钛(ti):质量百分比0.01-0.1%钛(ti)是低合金高强度钢中常用的微合金元素之一。当钢中的ti含量大于0.01%时,只要在冶炼或连铸时通过合适的添加方法,都能够获得大量细小弥散分布的ti氧化物及氮化物。这些微细的ti氧化物及其复合夹杂物是抑制γ晶粒粗化和促进夹杂物诱导生成晶内铁素体的有效质点。但当ti含量超过0.1%时,多余的钛形成的氧化物则很容易在冶炼或连铸过程中凝聚、粗化,如果不能上浮,就会残留在钢中成为微裂纹源,对钢的强度和韧性产生不利影响,所以ti的上限含量必须小于0.1%。铜(cu):质量百分比0.1-0.7%铜(cu)是奥氏体稳定化元素,其固溶强化作用能够提高钢板强度而不降低韧性,并增加钢板耐蚀性能。但若在冶炼或连铸过程中控制不当,则很容易产生铸坯裂纹。cu低于0.1%不能获得高的强化效果;若高于0.7%,则会由于ε-cu相的显著析出,损害钢板的韧性及热加工性能,容易产生热裂纹等缺陷。cu的添加虽然对抗硫性能的影响并不十分显著,但在一定程度上却能改变钢在硫化氢溶液中的电化学行为。另外,mo和cu形成的硫化物,可促进cu的氧化物单层膜在靠近金属基体处形成,提高钢材在硫化氢介质中的耐腐蚀性。镍(ni):质量百分比0.2-3.0%镍(ni)也会因固溶强化提高钢板强度和韧性,能够保证钢板强度及韧性。过低的ni则不能获得高强度,若过多则增加成本。故ni含量适宜范围为0.2~3.0%。硼(b):质量百分比0.0001-0.002%硼(b)能够提高淬透性使钢材强度增加。温度大于1300℃后,b在高温时的扩散快,易于在奥氏体晶界偏聚,冷却时先与n结合成bn,抑制晶界铁素体的长大,并在γ→α相变时,成为晶内铁素体的形核点。b在钢中还可以形成fe23(cb)6,有益于韧性的提高。但是,含b钢容易产生钢材强度合格率不稳定的现象,尤其是对需要热处理的钢材影响很大。因此控制b含量范围为0.0001-0.002%,若超过0.002%,则钢材的韧性劣化。磷(p):质量百分比0-0.015%磷(p)是作为杂质混入的不可避免的元素,会使钢板强度增加、韧性劣化。若超过0.015%则显著降低钢板延伸率及韧性,若过低会使精炼成本大幅增加,所以在冶炼成本能够承受的范围内应尽可能降低。硫(s):质量百分比0-0.010%硫(s)作为杂质元素进入钢中不可避免的元素,适当含量的s,则会形成高熔点的cus、cas等硫化物,部分mns则会依附在复合氧化物或氮化物周围呈球状分布。s含量过高则会生成粗大mns和cas系夹杂物,显著增加应力腐蚀断裂的敏感性,抗h2s腐蚀能力显著下降。因此,s含量应低于0.01%,且应在冶炼成本能够承受的范围内应尽可能降低s含量。氧(o):质量百分比0-0.06%氧(o)能够保证在钢中形成高熔点的ti、mg、ca、zr、rem等氧化物,各种合金元素对钢中的氧浓度影响不同,且冶炼及连铸过程中的操作工艺也会对钢中的氧含量和氧化物有重要影响。控制钢中的氧含量和氧化物是“氧化物冶金”技术的核心内容。一般地,若铸坯中氧含量大于60ppm时,则形成的氧化物粗大,会降低钢材的韧性及抗应力腐蚀断裂性能。因此,本发明控制氧含量在0.006%以下。氮(n):质量百分比0-0.005%氮(n)在工业钢中是不可能完全去除的元素,适量的n能在钢中与al和ti结合细化奥氏体晶粒,提高钢材的综合力学性能。在本发明确定的n含量小于0.005%范围内,钢中所形成的tin、bn、vn等粒子能够细化γ晶粒及晶内组织,有利于提高钢材韧性和抗h2s腐蚀性能。氢(h):质量百分比0-0.05%在炼钢过程和钢在存放或使用的过程中,会有h离子存在钢中,成为h脆的起源,对抗硫化氢应力腐蚀有决定性的影响,所以,钢中的h含量越少越好。铝(al):质量百分比0-0.005%在炼钢过程中喂入铝线,会与钢中的氧发生反应形成ai2o3,降低钢中的氧含量,另外也能起到一定的脱硫作用和晶粒细化作用。铌(nb):质量百分比0-0.2%在钢中添加nb经高温回火后会形成高度弥散分布的碳化物nbc,nbc与氢的结合能较高,有利于固定钢中的扩散氢,防止氢向脆弱的晶界聚集,nb形成的这些碳化物是有益的氢陷阱,可以有效地提高强度、细化晶粒、强化晶界,微量的nb与碳反应形成弥散分布的强碳化物颗粒及高密度的位错结,对位错起到钉扎作用。这些都有利于提高钢材的抗ssc性能。钙(ca):质量百分比0-0.008%一般在工业化生产的精炼结束末期都会加入硅钙线、钙铁线或钙线,目的是使钢中的夹杂物球化,有利于探伤合格率的提高。ca能够使条状的mns系夹杂球化,有助于降低钢板的各向异性并提高z方向性能;同时ca所形成的cao或cas,与其它夹杂物复合而有利于韧性。但是,在钢液中的cas析出温度比cao低,二者对夹杂物形成铁素体的影响能力不同,所以,要通过工艺来调整cao和cas的尺寸和密度分布。钢中的ca含量若超过0.008%则会形成粗大夹杂物,降低韧性。铈(ce):质量百分比0-0.03%在炼钢过程中若是预计形成的al2o3过高进而影响钢材的抗硫化氢应力腐蚀性能时,则需要加入ce促进生成比al2o3偏碱性的ce2o3,同时ce2o3与al2o3相结合形成的xce2o3·yal2o3类化合物可以降低al2o3活度。锆(zr):质量百分比0.0005-0.01%锆(zr)能够通过氧化物冶金过程反应,在钢中形成高熔点的复合夹杂物,有效细化夹杂物质点,并使钢中mns球化,有利于提高韧性,显著提高钢材的抗硫化氢腐蚀性能。稀土元素(rem):质量百分比0.003-0.05%稀土元素(rem)稀土与钢液中的氧、硫等杂质的结合能大,可作为钢液的强脱氧剂和脱硫剂;此外,稀土与钢液中的氧、硫反应生成的氧化物、硫化物或氧硫化物可部分残留在钢液中,成为钢中的夹杂物,此类夹杂物的熔点高,可作为钢液凝固时的非匀质成核中心,起细化钢的凝固组织作用;又由于这些夹杂物在轧钢温度下不易变形,仍保持细小的球形或纺锤形,使钢中的夹杂物形态得到控制,从而避免或克服钢材在热压力加工时由于其他种类夹杂物(如mns)延伸变形所导致的钢材性能的各向异性,而使钢材的纵向、横向与厚度方向的性能趋于一致。另,钢中可能固溶微量稀土,特别是高碳钢和合金含量较高的某些钢板固溶稀土量较高(万分之几),可能产生某些合金化作用。这种合金化作用表现为稀土影响钢的相变过程,改变相变产物的组成与结构,从而使钢的耐腐蚀性能变好,以及提高钢的显微硬度。镁(mg):质量百分比0.0005-0.02%镁(mg)是强氧化元素,和氧有很强的结合力。mg和al在钢液中可以形成mgo·al2o3尖晶石,这是一种高熔点粒子,其它元素常以铝镁尖晶石作为核心,形成复合夹杂物,有利于提高韧性。但是,al2o3夹杂物常常作为点蚀的起止位置或裂纹的传播路径,降低抗硫化氢应力腐蚀性能。并且,在钢液的温度下,mg具有很高的蒸气压,在炼钢过程中mg非常活跃,因此收得率和成分命中率难以控制,很容易使钢板的力学性能变得不稳定。本发明的125ksi抗硫化氢应力腐蚀高强油套管用钢立足于合理的化学成分设计并利用氧化物冶金工艺技术控制钢中夹杂物的微细化、球状化和组成结构多样化(图1);采用的调质热处理工艺获得高强高韧的回火马氏体相变组织(图2);碳化物的控制原则是,减少晶界处形成巨大的m23c6碳化物,而使之在晶内或晶界处生成直径为纳米级的微小球状碳化物(图3),进而提高钢基体的抗硫化氢应力腐蚀性能。附图说明图1.本发明实施例7的抗硫化氢腐蚀耐油管道用钢的夹杂物组织;a)为125ksi抗硫化氢应力腐蚀高强钢的夹杂物形貌;b)为该形貌的能谱。图2.本发明实施例7的抗硫化氢腐蚀耐油管道用钢的微观金相组织;图3.本发明实施例7的抗硫化氢腐蚀耐油管道用钢的碳化物析出形态;a)为低倍下碳化物析出的形貌与分布状态;b)为高倍下该试验钢板析出物的形态;c)为该析出物的能谱。图4.本发明实施例7的抗硫化氢腐蚀耐油管道用钢的马氏体板条束群和位错形态。具体实施方式下述非限定性实施例可以使本领域的普通技术人员更全面地理解本发明,但不以任何方式限制本发明。下述实施例中涉及的抗硫化氢应力腐蚀敏感性评估方法,如下:抗硫化氢应力腐蚀敏感性的评估用恒定负载拉伸试验验证,参照室内实验评价标准nacetm0177-2005(实验方法a),将试样侵泡在饱和h2s水溶液中,测试其在单轴负载拉伸应力条件下,负载应力为实际屈服强度85%时的抗开裂性能。实验温度为24±3℃,溶液介质为nacetm0177-2005标准a溶液:采用饱和h2s水溶液,由溶解在蒸馏水中5.0%的氯化钠和0.5%的冰醋酸组成(冰醋酸的体积分数占99.5%).实验时间为720h(30d),试样经720h仍不发生断裂,则判定耐硫套管用钢的抗硫化氢应力腐蚀(ssc)性能合格。实施例1表1为本发明的抗硫化氢应力腐蚀油套管用钢的化学成分,表2为本发明的抗硫化氢应力腐蚀油套管用钢的热处理方法(对热轧后的钢板进行热处理,部分参数见表2)。按照表1设定的化学组成利用氧化物冶金工艺在真空感应炉中进行冶炼,而后铸造形成钢锭,并冷却至室温。再将钢锭加热至1050℃进行锻造,冷却至室温成为80×80mm的方坯。而后方坯在炉中以加热温度1150℃保温2h后进行热轧,最终轧成厚度为13mm的钢板,空冷至室温。将热轧冷却后的钢板以900℃正火,保温10min,空冷至室温后,再以820℃淬火,保温30min,喷淋水冷至马氏体相变完成温度mf以下,最后以540℃回火,保温30min,把钢板放在石棉网中缓冷至室温,最终得到125ksi抗硫化氢腐蚀钢板,其力学性能及抗硫化氢实验结果如表3所示。实施例2表1为本发明的抗硫化氢应力腐蚀油套管用钢的化学成分,表2为本发明的抗硫化氢应力腐蚀油套管用钢的热处理方法(对热轧后的钢板进行热处理,部分参数见表2)。按照表1设定的化学组成成分利用氧化物冶金工艺在真空感应炉中进行冶炼,而后铸造形成钢锭,并冷却至室温。再将钢锭加热至1100℃进行锻造,冷却至室温成为80×80mm方坯。而后在炉中以加热温度1200℃保温2h后进行热轧,最终轧成厚度为15mm的钢板,空冷至室温。将热轧冷却后的钢板以910℃正火,保温15min,空冷至室温后,再以830℃淬火,保温30min,油淬至马氏体相变完成温度mf以下,最后以570℃回火,保温40min,把钢板放在石棉网中缓冷至室温,最终得到125ksi抗硫化氢腐蚀钢板,其力学性能及抗硫化氢实验结果如表3所示。实施例3表1为本发明的抗硫化氢应力腐蚀油套管用钢的化学成分,表2为本发明的抗硫化氢应力腐蚀油套管用钢的热处理方法(对热轧后的钢板进行热处理,部分参数见表2)。按照表1设定的化学组成成分利用氧化物冶金工艺在真空感应炉中进行冶炼,而后铸造形成钢锭,并冷却至室温。再将钢锭加热至1100℃进行锻造,冷却至室温成为100×100方坯。而后在炉中以加热温度1200℃保温2h后进行热轧,最终轧成厚度为15mm的钢板,空冷至室温。将热轧冷却后的钢板以920℃正火,保温20min,空冷至室温后,再以850℃淬火,保温30min,油淬至马氏体相变完成温度mf以下,最后以600℃回火,保温30min,空冷至室温,最终得到125ksi抗硫化氢腐蚀钢板,其力学性能及抗硫化氢实验结果如表3所示。实施例4表1为本发明的抗硫化氢应力腐蚀油套管用钢的化学成分,表2为本发明的抗硫化氢应力腐蚀油套管用钢的热处理方法(对热轧后的钢板进行热处理,部分参数见表2)。按照表1设定的化学组成成分利用氧化物冶金工艺在真空感应炉中进行冶炼,而后铸造形成钢锭,并冷却至室温。再将钢锭加热至1150℃进行锻造,冷却至室温成为80×80mm方坯。而后在炉中以加热温度1200℃保温2h后进行热轧,最终轧成厚度为16mm的钢板,空冷至室温。将热轧冷却后的钢板以930℃正火,保温25min,空冷至室温后,再以900℃淬火,保温30min,喷淋水冷至马氏体相变完成温度mf以下,最后以630℃回火,保温50min,空冷至室温,最终得到125ksi抗硫化氢腐蚀钢板,其力学性能及抗硫化氢实验结果如表3所示。实施例5表1为本发明的抗硫化氢应力腐蚀油套管用钢的化学成分,表2为本发明的抗硫化氢应力腐蚀油套管用钢的热处理方法(对热轧后的钢板进行热处理,部分参数见表2)。按照表1设定的化学组成成分利用氧化物冶金工艺在真空感应炉中进行冶炼,而后用铸锭法形成钢锭,待钢锭冷却至室温得到圆锭。再将钢锭加热至1050℃进行锻造,冷却至室温成为120×120mm方坯。而后在炉中以加热温度1250℃保温2h后进行热轧,最终轧成厚度为15mm的钢板,空冷至室温。再将热轧冷却后的钢板以850℃淬火,保温40min,喷淋水冷至马氏体相变完成温度mf以下,最后以750℃回火,保温70min,把钢板放在石棉网中缓冷至室温,最终得到125ksi抗硫化氢腐蚀钢板,其力学性能及抗硫化氢实验结果如表3所示。实施例6表1为本发明的抗硫化氢应力腐蚀油套管用钢的化学成分,表2为本发明的抗硫化氢应力腐蚀油套管用钢的热处理方法(对热轧后的钢板进行热处理,部分参数见表2)。按照表1设定的化学组成成分利用氧化物冶金工艺在真空感应炉中进行冶炼,而后铸造形成钢锭,并冷却至室温。再将钢锭加热至1100℃进行锻造,冷却至室温成为80×80mm方坯。而后在炉中以加热温度1250℃保温2h后进行热轧,最终轧成厚度为14mm的钢板,空冷至室温。再将热轧冷却后的钢板以920℃淬火,保温30min,喷淋水冷至马氏体相变完成温度mf以下,最后以720℃回火,保温60min,空冷至室温,最终得到125ksi抗硫化氢腐蚀钢板,其力学性能及抗硫化氢实验结果如表3所示。实施例7表1为本发明的抗硫化氢应力腐蚀油套管用钢的化学成分,表2为本发明的抗硫化氢应力腐蚀油套管用钢的热处理方法(对热轧后的钢板进行热处理,部分参数见表2)。按照表1设定的化学组成成分利用氧化物冶金工艺在真空感应炉中进行冶炼,而后铸造形成钢锭,并冷却至室温。再将钢锭加热至1150℃进行锻造,冷却至室温成为80×80mm方坯。而后在炉中以加热温度1200℃保温2h后进行热轧,最终轧成厚度为16mm的钢板,空冷至室温。再将热轧冷却后的钢板以880℃淬火,保温30min,油淬至马氏体相变完成温度mf以下,最后以760℃回火,保温30min,把钢板放在石棉网中缓冷至室温,最终得到125ksi抗硫化氢腐蚀钢板,其力学性能及抗硫化氢实验结果如表3所示。从图2中可以清楚的看出本发明钢为回火马氏体结构,此外还可以看出晶粒内部和晶界上均匀的分布着夹杂物。通过对钢板组织进行epma检测,钢板中的夹杂物直径长度多小于2μm,且呈球状,仅有个别长度不过3μm的多边形夹杂。图1为epma下本发明钢板中较为常见且典型的夹杂物,此夹杂物直径小于1μm,呈球状,结合图1b)中的能谱可知,图1a)中的夹杂物为mns,此种小型圆形mns一改以往长条状结构,大大降低了点蚀发生的概率,进而提高了材料的抗硫化氢应力断裂性能。图3为钢材回火热处理的最后一段时间内,各种碳化物析出,其中包括:m3c型碳化物,尺寸适中并球状化,均匀分布在晶界中和晶内,如图3b)所示;另一种纳米级微细碳化物是由与碳化物生成能力较强的v和mo与c结合而形成的纳米尺寸的四方晶mc(m=v,mo)碳化物,如图3a)所示,该mc碳化物会引起析出强化。此外,在本发明用钢中粗大的m23c6(m=fe,cr,mo)夹杂物十分少,进而降低油套管用钢的硫化氢应力腐蚀敏感性。从图4中可以看出,本发明用钢的位错密度较低,且位错并不是按照一个方向发生的,而是经过缠结形成位错网,这种位错缠结有利于形成有效的h陷阱,进而增加抗硫化氢应力腐蚀性能。实施例8表1为本发明的抗硫化氢应力腐蚀油套管用钢的化学成分,表2为本发明的抗硫化氢应力腐蚀油套管用钢的热处理方法(对热轧后的钢板进行热处理,部分参数见表2)。按照表1设定的化学组成成分利用氧化物冶金工艺在真空感应炉中进行冶炼,而后铸造形成钢锭,并冷却至室温。再将钢锭加热至1100℃进行锻造,冷却至室温成为80×80mm方坯。而后在炉中以加热温度1250℃保温2h后进行热轧,最终轧成厚度为16mm钢板,空冷至室温。再将热轧冷却后的钢板以900℃淬火,保温90min,水淬至马氏体相变完成温度mf以下,最后以630℃回火,保温150min,空冷至室温,最终得到125ksi抗硫化氢腐蚀钢板,其力学性能及抗硫化氢实验结果如表3所示。本发明上述实施例1-8的钢均通过了nacetm0117a实验,成为合格的125ksi级别低碳低合金抗硫化氢应力腐蚀耐硫油套管用钢。本发明上述实施例2-8的钢的组织为回火马氏体组织,实施例1的钢的组织为回火马氏体组织,包含少量下贝氏体组织,含量低于15%。表1本发明的抗硫化氢应力腐蚀油套管用钢的成分(m%)编号csimncrmovticuninbbmgrem实施例10.100.50.50.90.50.10.060.6-----实施例20.150.40.70.80.50.30.020.4-----实施例30.200.10.50.30.50.20.060.6-----实施例40.250.40.30.80.70.30.040.6-----实施例50.120.10.50.80.50.30.060.6-0.1---实施例60.180.11.10.60.50.30.080.51.00.20.0015--实施例70.270.40.50.30.80.30.060.61.0--0.02-实施例80.100.41.80.81.00.40.100.61.00.20.0015-0.05表2本发明的抗硫化氢应力腐蚀油套管用钢的热处理方法表3本发明的抗硫化氢应力腐蚀油套管用钢的力学性能及抗硫化氢实验结果编号屈服强度/mpa抗拉强度/mpa冲击功/0℃/jnacetm0177-2005-a实验实施例1913965107720h实施例2896932164720h实施例3887946132720h实施例49241017105720h实施例59611043169720h实施例6895947182720h实施例79891145101720h实施例89821095116720h对于任何熟悉本领域的技术人员而言,在不脱离本发明技术方案范围情况下,都可利用上述揭示的技术内容对本发明技术方案作出许多可能的变动和修饰,或修改为等同变化的等效实施例。因此,凡是未脱离本发明技术方案的内容,依据本发明的技术实质对以上实施例所做的任何简单修改、等同变化及修饰,均应仍属于本发明技术方案保护的范围内。当前第1页12