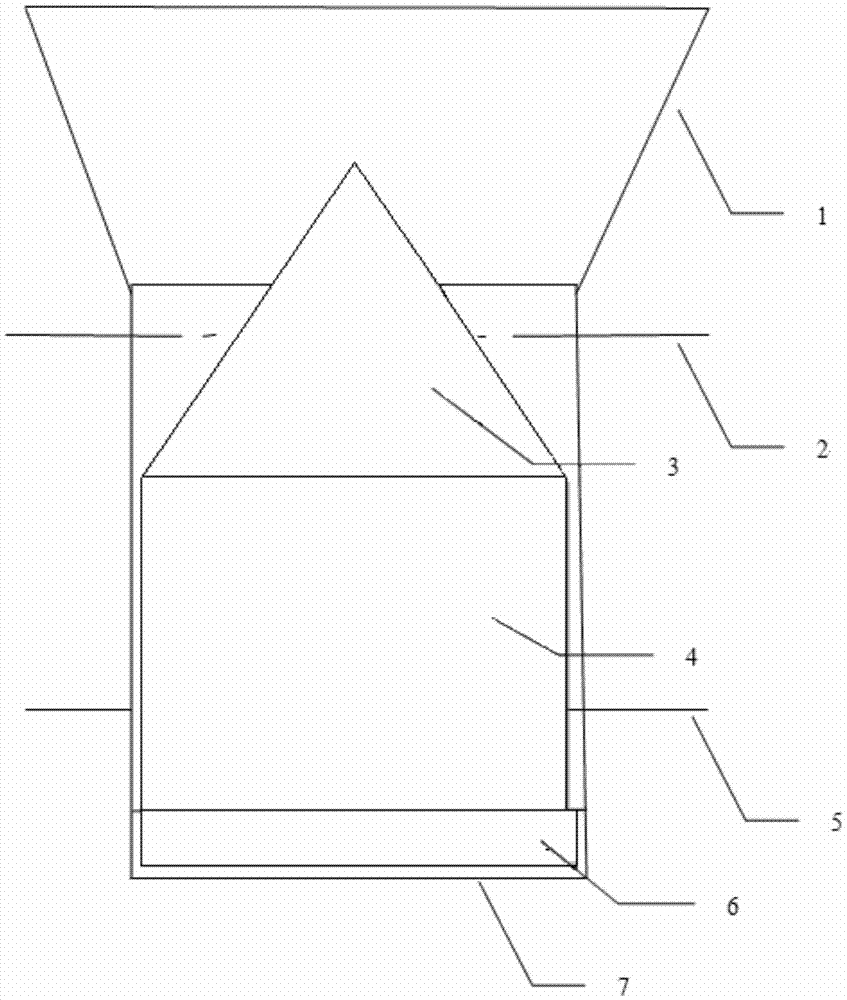
本发明涉及冶金领域的一种操作方法,是一种高炉空料线停炉操作方法,可以应用到所有炼铁高炉因某种原因需空料线到高炉风口中心线以下的停炉操作方法,具体是一种高炉空料线停炉不放残铁烧掉风口区死焦堆的方法。
背景技术:
:炼铁高炉生产到一定年限,就需要进行中修或大修,高炉停炉方法分为填充法和空料线法两种,空料线法即在停炉过程不向炉内装料,采用炉顶打水控制炉顶温度,当料面降至风口附近进行休风停炉,料线降至风口以上0.5m左右,部分风口暗红和挂渣,煤气中还没有o2出现,应及时出最后一次铁,铁后休风停炉,防止料线过低,出现o2气,形成爆炸性气体。高炉空料线停炉后期,当料线位于风氧过剩进程时,将鼓风量控制为高炉正常风量的40~50%,并且将炉顶打水上限量控制为能够确保炉顶煤气中h2的体积百分含量不大于15%的程度;当料线到达风氧过剩进程的结束点或炉顶煤气o2含量大幅上升时,即当料线深度达到风口中心线时,进行休风以完成高炉停炉操作;高炉空料线停炉后期,即在高炉渣铁出净时,炉顶通蒸汽,将炉顶煤气压力降到常压,热风风压降到0kpa,座料;然后继续向高炉送风出铁,直至渣铁出净后休风停炉,最后清出炉料,修补炉缸,这种停炉方法,依靠高炉炉料自重将炉缸里的渣铁通过铁口挤出,使停炉后渣铁液面降至铁口中心线以下500mm左右,适宜高炉修补铁口中心线下500mm以上区域的砖衬,高炉空料线停炉后期,打开铁口出铁,然后打开残铁口出渣铁能够使停炉后高炉内的料线降至风口水平面以下的概率高达90%以上。从以上技术分析,有以下问题,是目前本领域技术人员需要解决的:(1)高炉停炉是高炉大修、中修、小修前的停产操作,是高炉操作的一个组成部分,高炉降料面停炉是高炉长期休风检修前常见的一种工艺操作,一般要求把料面降到风口区域,以最大限度降低停炉后高炉清理的难度,减少高炉检修的工期和费用;由于担心如果出现最终料面位置过低,则大量风口吹空,极易形成爆炸性气体,影响停炉安全,所以在实际高炉空料线操作过程中,停炉休风后检查料面往往出现最终料面位置过高(远远高出风口中心线),则增大停炉后高炉清理的难度,增加高炉检修的工期和费用;(2)高炉空料线后期,当料线位于风氧过剩进程时,在料线深度达到风口中心线时,不采用依靠高炉炉料自重将炉缸里的渣铁通过铁口挤出的座料方法和打开残铁口出渣铁这两种方法,而把料线降到更低位置(风口中心线以下1.5米或更深的位置),以减少或取消停炉后人工扒炉;因此,研发一种能解决以上技术问题的方法成为本领域技术人员亟待解决的技术问题。技术实现要素:本发明所要解决的技术问题是,克服现有技术的缺点,提供一种高炉空料线停炉不放残铁烧掉风口区死焦堆的方法,该方法在高炉打水空料线过程中,将最终料面降得更深,风口区域炉缸死焦堆全部烧掉,最终全部料面降到风口中心线以下1.5米或更深,减少或取消停炉后人工扒炉,为检修、大修、凉炉缩短时间,减少或避免扒炉带来的人力、物力、财力消耗。为了解决以上技术问题,本发明提供一种高炉空料线停炉不放残铁烧掉风口区死焦堆的方法,具体包括以下步骤:(1)停炉前安装高炉炉顶雾化打水系统,并正常使用停炉前安装炉顶雾化打水系统,对炉顶雾化打水系统的技术要求是:①喷枪数要达到至少8只;②喷枪喷出的水雾化水颗粒小于500μm;(2)停炉前一天,调整渣铁成分和铁水温度根据生产现状,减轻焦炭负荷,控制煤比小于100kg/t,加蛇纹石、石灰石、硅石、萤石调整渣铁成分;其中,控制铁水中:[si]:0.6%-0.8%,铁水温度pt=1510±10℃,炉渣:碱度r2=1.10±0.03、al2o3≤15.5%、mgo/al2o3=0.6±0.05;(3)加停炉料,停炉料为二段结构+盖面焦停炉料为二段结构+盖面焦,具体为:把软融带以下划分为第一段料,软融带以上划分为第二段料,第二段料焦炭负荷比第一段料减轻0.2-0.3,第二段料加完后加净焦作为盖面焦;炉料结构要求:块矿比例不超过10%,球团比例不超过20%,停用小块焦;加停炉料时加停煤焦,停炉过程中炉温控制:[si]:0.6-1.0%,pt≮1450℃,炉渣r:1.06±0.03,al2o3≤15.5%,mgo/al2o3=0.6±0.05,全焦负荷到达高炉工作容积中部时停止喷煤;(4)预休风具体为:①利用炉身以下的静压力孔、探瘤孔安装氮气管道通入氮气;②焊补和加固炉壳;③处理损坏的冷却设备;④加长探尺;(5)送风打水空料线操作1)停炉操作参数控制如下:炉顶温度≤450℃;严格控制煤气含h2量和o2量,要求h2最大不超过12%;o2<2%。最高风量为正常风量的90-100%;2)降料面过程控制各点温度在要求范围内,控制手段为调整风量和增减炉顶雾化水量;3)在停炉降料线过程中,保持较高炉顶压力操作,顶压保持比正常高20-40kpa;4)满足下列条件,增加风量烧掉风口区域死焦堆①料线已降到风口中心线以下;②有3个以上风口已吹空;③炉顶温度出现拐点向下;④炉喉温度出现拐点,大幅下降100℃以上;⑤单位时间内炉顶打水量已小于停炉过程最大打水量的60%;⑥炉顶压力平稳无10kpa以上的高压尖峰;⑦渣铁流动性好;5)风口全部吹空以后,继续加风烧1-2小时休风停炉。本发明进一步限定的技术方案是:进一步的,前述高炉空料线停炉不放残铁烧掉风口区死焦堆的方法中,步骤(1)中所述的喷枪单流体雾化防堵喷枪。技术效果,喷枪的喷口是裸露在高炉煤气中的,煤气的高温粉尘极易沾在喷枪口上,本发明的喷枪为防堵喷枪,有防堵机构,防止将喷枪堵塞。前述高炉空料线停炉不放残铁烧掉风口区死焦堆的方法中,控制步骤(1)打水系统工作稳定,每只喷枪单独实现远程人工手动控制,并显示工作参数。技术效果,这样能控制打水系统的稳定,方便操作。前述高炉空料线停炉不放残铁烧掉风口区死焦堆的方法中,步骤(2)中萤石加入量按矿批的0.6±0.1%加入。前述高炉空料线停炉不放残铁烧掉风口区死焦堆的方法中,步骤(3)中加净焦作为盖面焦时,净焦加入2批,分2次加入,每批净焦的重量等于第二段料焦批的重量。前述高炉空料线停炉不放残铁烧掉风口区死焦堆的方法中,步骤(5)停炉操作参数控制中控制煤气含h2<10%。前述高炉空料线停炉不放残铁烧掉风口区死焦堆的方法中,步骤(5)中停炉操作参数控制时炉顶温度平均≤350℃。前述高炉空料线停炉不放残铁烧掉风口区死焦堆的方法中,步骤(5)中每次加风100-200m3/min。本发明的有益效果是:停炉降料线过程中,冶炼参数变化大,特别是高炉煤气利用率,往往造成停炉中后期炉温不足,渣铁流动性不好,造成炉内气流不稳,随料层减薄,易出管道气流,渣铁出不尽增大停炉后扒炉工作量,就起原因为打水降料面停炉过程,随料面降低,料层减薄,炉内软融带以上间接还原区逐步消失,软融带以上的金属料主要为直接还原,需要消耗大量热量,所以采用本发明停炉料的设计。采用本发明方法满足以上加风条件,每次加风100~200m3/min,直到加到全风作业或比正常全风冶炼条件下更高的风量,以加速烧掉风口区域炉缸死焦堆,空全部料面到风口中心线以下1.5米甚至更深。采用本发明的方法,在高炉空料线安全、快速休风停炉后,高炉内料面降到风口中心线以下1.5米或更深,风口区域死焦堆全部烧掉见附图1中编号3,停炉后不需人工扒风口区域死焦堆,缩短凉炉时间,不仅节约了人工扒炉费和工器具费等,而且至少为高炉小修、中修、大修节省了1天时间;以2150m3高炉为例,节省1天时间,就可以早日投产1天,相当于增产5000吨铁水,按增产每吨铁效益400元计算,产生效益:5000*400=200(万元)。附图说明图1为本发明实施例的结构示意图;图中:1-炉腹,2-风口中心线,3-风口区域死焦堆,4-风口区域下面死焦堆,5-铁口中心线,6-死铁层残铁,7-炉缸及死铁层内型。具体实施方式实施例1本实施例提供的一种高炉空料线停炉不放残铁烧掉风口区死焦堆的方法,具体包括以下步骤:(1)停炉前安装高炉炉顶雾化打水系统,并正常使用停炉前安装炉顶雾化打水系统,对炉顶雾化打水系统的技术要求是:①喷枪数要达到至少8只实现均匀打水;②喷枪喷出的水雾化效果要好,雾化水颗粒小于500μm;(2)停炉前一天,调整渣铁成分和铁水温度根据生产现状,减轻焦炭负荷,控制煤比小于100kg/t,加蛇纹石、石灰石、硅石、萤石调整渣铁成分,保证渣铁流动性好;其中,控制铁水中:[si]:0.6%-0.8%,铁水温度pt=1510±10℃,炉渣:碱度r2=1.10±0.03、al2o3≤15.5%、mgo/al2o3=0.6±0.05;(3)加停炉料,停炉料为二段结构+盖面焦停炉料为二段结构+盖面焦,具体为:把软融带以下划分为第一段料,软融带以上划分为第二段料,大幅减轻第二段料焦炭负荷防止停炉前炉温下降过多,炉内煤气不稳,渣铁流动性变差,渣铁出不尽问题,第二段料焦炭负荷比第一段料减轻0.2-0.3,第二段料加完后加净焦作为盖面焦;炉料结构要求:块矿比例不超过10%,球团比例不超过20%,停用小块焦;加停炉料时加停煤焦,适当缩小矿批,停炉过程中炉温控制:[si]:0.6-1.0%,pt≮1450℃,炉渣r:1.06±0.03,al2o3≤15.5%,mgo/al2o3=0.6±0.05,全焦负荷到达高炉工作容积中部时停止喷煤,降低富氧量,以维持风口前理论燃烧温度保持基本稳定;(4)预休风具体为:①利用炉身以下的静压力孔、探瘤孔安装氮气管道通入氮气,以降低炉顶温度和稀释煤气浓度;②焊补和加固炉壳;③处理损坏的冷却设备,不许向炉内漏水;④加长探尺;(5)送风打水空料线操作1)停炉操作参数控制如下:炉顶温度≤450℃;严格控制煤气含h2量和o2量,要求h2最大不超过12%;o2<2%。开始回风不要太大,待炉料下降后,风量与风压对应,再逐渐回风,最高风量为正常风量的90%-100%;风量水平应控制不易产生管道行程的煤气速度,以炉顶煤气压力平稳不出现高压尖峰(10kpa)为宜;2)降料面过程控制各点温度在要求范围内,控制手段为调整风量和增减炉顶雾化水量;3)在停炉降料线过程中,保持较高炉顶压力操作,顶压保持比正常高20-40kpa,即使发生崩料、管道行程、爆震等情况,需减顶压时,维持较高顶压,降低煤气流速;4)满足下列条件,增加风量烧掉风口区域死焦堆①料线已降到风口中心线以下;②有3个以上风口已吹空;③炉顶温度容易控制,炉顶温度出现拐点向下;④炉喉温度出现拐点,大幅下降100℃以上;⑤单位时间内炉顶打水量(每小时炉顶打水量)已小于停炉过程最大打水量的60%;⑥炉顶压力平稳无10kpa以上的高压尖峰;⑦渣铁流动性好;5)风口全部吹空以后,继续加风烧1-2小时休风停炉。在本实施例中,步骤(1)中所述的喷枪单流体雾化防堵喷枪;控制步骤(1)打水系统工作稳定,每只所述喷枪单独实现远程人工手动控制,并显示工作参数,这样能控制打水系统的稳定,方便操作,工作参数包括水的压力、水的流量、导出管煤气温度、煤气冷却后平均温度、喷枪开启数量、阀门的状态及相关参数的历史记录、故障报警等;步骤(5)中停炉操作参数控制时炉顶温度平均≤350℃。在本实施例中,步骤(2)中萤石加入量按矿批的0.6±0.1%加入;步骤(3)中加净焦作为盖面焦时,净焦加入2批,分2次加入,每批净焦的重量等于第二段料焦批的重量;步骤(5)停炉操作参数控制中控制煤气含h2<10%;步骤(5)中每次加风100-200m3/min。满足以上加风条件,每次加风100~200m3/min,直到加到全风作业或比正常全风冶炼条件下更高的风量,以加速烧掉风口区域炉缸死焦堆,空全部料面到风口中心线以下1.5米甚至更深。实施例2本实施例提供一种具体的高炉空料线停炉不放残铁烧掉风口区死焦堆的方法的实施方案,采用2150m3的高炉进行试验,高炉的上端为炉腹1,高炉上设有风口中心线2及铁口中心线5,高炉内由上之下设置有风口区域死焦堆3、风口区域下面死焦堆4、死铁层残铁6及炉缸及死铁层内型7,结构如图1所示;(1)停炉前安装高炉炉顶雾化打水系统,并正常使用(当炉顶温度高时)7月12-14日高炉计划定修48小时,利用此机会,对原炉顶降温洒水系统改造为炉顶喷雾打水降温系统,割除原有炉顶4根打水管,并在同一标高新开4个新孔,采购安装8只单流体自动伸缩雾化防堵喷枪及水管管道、控制系统等,炉顶喷雾打水降温系统与原高炉炉顶洒水总管连接,高炉原炉顶洒水总管为高炉风口高压水系统的分支,能提供1.3mpa水压及每小时160吨打水量,所以不需额外增加增压泵就能满足新喷枪对压力的需求;(2)停炉前一天,减轻焦炭负荷,调整渣相结构(调整渣铁成分和铁水温度)8月30日0:00按计划减轻焦炭负荷及加蛇纹石、石灰石、硅石、萤石调整渣相,焦炭负荷及燃料比由3.107、600kg/t调整为2.944、658kg/t,铁水温度由1495温度提高到1507-1518℃;铁水含硅由0.4%提高到0.7%-0.8%,炉渣ai2o3由16.86%降到14.87%,mgo由8.73%提高到9.32%,mgo/ai2o3由0.52提高到0.62,炉渣r2由1.25降到1.10,渣铁流动性良好;(3)加停炉料,停炉料为二段结构+盖面焦按计划30日22:00加停炉料,第一段16批,焦炭负荷调为o/c=2.446,焦比=672kg/t;第二段14批,o/c=2.239,焦比=733kg/t,合计o/c=2.345,焦比=700.1kg/t,并调整炉渣成分,最后集中加入2罐盖面焦共40.2吨。停炉料下达炉缸后铁水温度最高上升到1523℃,后期逐步下降到1463℃;铁水含硅最高上升到0.93%,中后期逐步下降到0.69%;炉渣ai2o3控制在≤15.5%,停炉休风前上升16.17%,估计与停炉末期烧炉缸死焦堆有关,炉渣mgo控制在8.5-10%,mgo/ai2o3为0.62,炉渣r2控制在1.0-1.1,直到停炉休风前,渣铁流动性良好,干渣沟被冲刷出一条深沟;(4)预休风31日6:18预休风,焊补和加固炉壳;处理损坏的冷却设备,不许向炉内漏水;加长探尺等,拆除炉身标高23.815静压力计,使炉壳周围4个静压力孔直接与氮气管道相连,送风前全开静压力氮气管道阀门吹入氮气到炉身下;0#和2#热风炉热风阀阀柄停炉前几天发现漏水,做闭水处理,向阀柄进出水管通氮气,不仅冷却热风阀柄,同时氮气随鼓风进入高炉,起到稀释煤气浓度的效果;(5)送风打水空料线操作第一阶段:空料料到风口中心线以下,随料层减薄,风量总体呈下降趋势14:06复风,15:06风量3573nm3/min,顶压161kpa,达到降料线方案的预定要求。20:46料线已超过18.83米,进入炉腰下部,此时顶温平均342℃,最高点达到409℃,炉内减风200nm3/min控制顶温,21:14煤气在线分析h2含量达到10.16%,减风300m3/min,21:20减风500m3/min,目的是减小打水量控制h2含量小于10%,减风同时少降顶压(与正常操作比少降20kpa),以控制煤气流速,防止管道气流发生;22:51煤气在线分析h2含量下降到9.54%,进入控制范围,料线已降到21.2米,已过炉腹中部(21.05米),22:58减风400m3/min为切煤气做准备,23:07减风300m3/min,23:17风量减至1323m3/min,此时料线已下降到21.5米,到达炉腹中下部,达到预定切煤气料面点,23:22开炉顶放散,23:27关重力除尘器煤气切断阀切煤气,23:30加风300m3/min,23:51加风200m3/min,9月1日0:26加风100m3/min,1:42、1:54、2:15因炉顶温度超出控制范围,分别减风200、200、100m3/min。至此9月1日2:15料线已下降到23.59米已过风口中心线0.39米(风口中心线料线23.2米),见表1停炉前中期控制参数,按常规操作,这时要进行休风停炉,本发明就突破在这个地方,不休风停炉,反而增加风量继续烧死焦堆。表1停炉前中期控制参数第二阶段:满足加风条件烧掉风口区域死焦堆,风量总体呈上升趋势过去当降料面降到风口中心线以下0-500mm时,即休风停炉,本发明技术方案要求,料线降到此位置时,加风烧死焦堆;9月1日2:15料线已降到23.59米(风口中心线料线为23.2米),2:43分11#、14#、18#风口吹空,2:45满足加风条件开始加风,具体相关参数见表2、表3、表4,风量由2080m3/min加到2130m3/min,2:49分7#、9#、10#、12#、17#、21#、26#风口吹空,3:11分2#、19#、20#、25#风口吹空,3:15风量加到2480m3/min,到4:10风量已加到3400m3/min,4:19分3#、16#、22#、23#风口吹空,至此26个风口已全部吹空,见表4风口吹空时间;4:42风量加到3930m3/min,已恢复到正常生产时风量,到5:56风量加到4340m3/min,见表2停炉中后期控制参数;6:16分准确、安全、顺利休风停炉,休风下来观察测量料面已下降到风口中心线以下1.5米,不需人工扒炉操作,缩短凉炉时间。表2停炉中后期控制参数表3炉顶打水过程调整时间打水流量m3/h累计打水量m3平均顶温℃14:4530832615:00602328715:23857436016:15905332316:5010016532818:291206230319:001007030819:4214025234621:3010015531223:03609428500:37807731701:3513011545002:28805529603:096018826406:17关闭表4风口吹空时间风口号时间风口号时间1#/13#/2#03:1014#02:433#04:1915#/4#03:2216#03:405#03:5217#02:496#/18#02:437#02:4919#03:118#/20#03:119#02:4921#02:4910#02:4922#04:1311#02:4323#04:1312#02:4924#/13#/25#03:0014#02:4326#02:49本次降料线停炉炉顶压力平稳,全过程无爆震,实现了准确、安全、快速、经济成功停炉;以2150m3高炉为例,节省1天时间,就可以早日投产1天,相当于增产5000吨铁水,按增产每吨铁效益400元计算,产生效益:5000*400=200(万元)。除上述实施例外,本发明还可以有其他实施方式。凡采用等同替换或等效变换形成的技术方案,均落在本发明要求的保护范围。当前第1页12