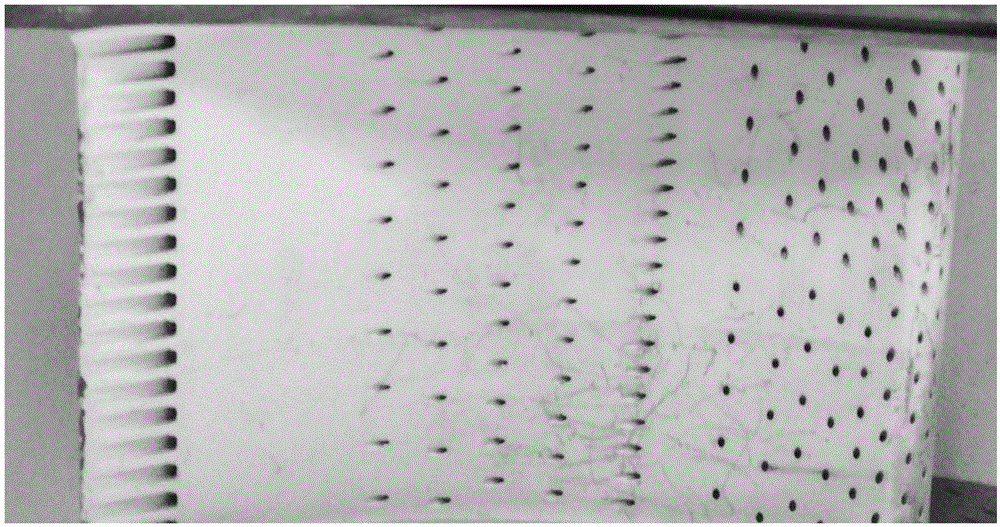
本发明属于发动机涡轮叶片热障涂层的陶瓷层修理领域,具体涉及一种去除热障涂层中陶瓷层的加压碱煮方法。
背景技术:
:目前,由于电子束物理气相沉积(简称eb-pvd)技术具有涂层化学成分易于精确控制、可得到柱状晶组织、涂层与基体结合强度高等优点,已经广泛应用于多种涡轮叶片高温防护涂层的制备加工,显著提高了涡轮叶片的抗高温氧化和抗腐蚀性能、隔热性能,延长了发动机工作寿命。但是,带有热障涂层的叶片在加工过程中或长时间使用后,因种种原因导致陶瓷层局部剥落现象。这就需要将叶片表面原有的陶瓷层去除,同时保证金属底层不会减薄,这样才能进行后续的陶瓷层再涂覆,形成完整的热障涂层。然而,由于eb-pvd技术制备的陶瓷层结合力强、硬度高,采用传统的机械吹砂方法去除陶瓷层时,往往会出现去除陶瓷层的同时,金属底层减薄严重的问题。因此,有必要研究一种陶瓷层去除技术,保证陶瓷层去除后,既对金属底层无任何损伤,又对基体材料本身无任何性能衰减作用;同时,再次沉积陶瓷层后,热障涂层质量满足性能要求。加压碱煮工艺是一种将碱性溶液放置到高压反应釜中,在一定的脉冲压力和温度条件下处理一定时间,碱性溶液与陶瓷类物质进行接触反应。目前,尚未应用于去除eb-pvd技术制备的热障涂层。技术实现要素:本发明的目的在于克服上述现有技术的缺点,提供一种去除热障涂层中陶瓷层的加压碱煮方法;该方法通过加压碱煮工艺,将热障涂层的陶瓷层去除干净,同时保证金属层的完整,并且对基体材料本身又无任何性能衰减作用;再次沉积陶瓷层,完成热障涂层的修复工艺。为达到上述目的,本发明采用以下技术方案予以实现:一种去除热障涂层中陶瓷层的加压碱煮方法,包括以下步骤:步骤1,将表面有陶瓷层的零件放置于高温高压反应釜中,反应釜中承载有碱液;步骤2,加热反应釜中的碱液,同时开启磁力搅拌;步骤3,反应釜中的碱液温度为(100~350)±5℃时,停止磁力搅拌,同时对高温高压反应釜进行脉冲加压;步骤4,脉冲加压停止后,进行磁力搅拌;步骤5,交替进行脉冲加压和磁力搅拌,共20-60min;步骤6,从反应釜中取出零件,热水冲洗零件,烘干零件后得到去除热障涂层中陶瓷层的零件。本发明的进一步改进在于:优选的,碱液为碱性物质和去离子水的混合液;其中碱性物质与去离子水的质量比例为1:(1~8)。优选的,碱性物质为naoh和koh的混合物,其中naoh和koh的质量比为1:(1~5)。优选的,磁力搅拌的转速为500~2000rpm。优选的,脉冲加压的压力为10~100mpa。优选的,步骤3中,脉冲加压时间为30~90s;步骤4中,磁力搅拌时间为30~90s。优选的,步骤5中,每次脉冲加压时间为30~90s,每次磁力搅拌时间为30~90s。优选的,步骤5中,整个脉冲加压和磁力搅拌过程中,加热反应釜,使得反应釜中碱液的温度维持在(100~350)±5℃之间。优选的,步骤6中,从反应釜取出零件前,通过磁力搅拌使反应釜内碱液的温度降至<50℃,同时释放反应釜内的压力至大气压。优选的,步骤6中,热水温度为80~100℃,热水冲洗时间≥1h。与现有技术相比,本发明具有以下有益效果:本发明公开了一种去除热障涂层中陶瓷层的加压碱煮方法;该方法利用碱液去除热障涂层中的陶瓷层;去除陶瓷层时,陶瓷层、金属层界面的α-al2o3层与碱溶液发生高温高压化学反应,陶瓷层产生剥离,对金属底层无损伤,金属底层无需补涂涂层,工序简单,便于陶瓷层的再涂覆;该方法方便、快捷,设备结构简单,易于操作;与传统机械吹砂方法相比,本发明的工艺参数控制准确,产品质量一致性高;通过实践发现,通过本方法处理过的零件,陶瓷层得到干净、有效的剥离,而金属层没有受到损伤,金属底层在陶瓷层去除前后,其厚度没有发生改变。进一步的,本发明限制了碱性物质和去离子水的比例,以及碱性物质中本身不同碱液之间的比例,其中naoh与koh之间的比例,以及碱性物质与去离子水之间的比例能够根据不同的脉冲压力、温度、保温时间、搅拌转速进行按比例配制。进一步的,限制了磁力搅拌的转速和脉冲的压力;因陶瓷层呈柱状晶形貌,存在由表面至金属层的纵向显微通道,然而通道尺寸为纳米级,较小的脉冲压力无法将碱溶液输送到陶瓷层与金属层的界面,无法与α-al2o3层发生有效接触,而过高的脉冲压力又会引起叶片型面结构的变化;因此将脉冲压力限制在10~100mpa,在有效将碱液输送到陶瓷层与金属层界面的同时,不会对叶片本身的形状造成影响。进一步的,磁力搅拌和脉冲加压交替进行,在磁力搅拌过程中,将磁力搅拌与脉冲压力配合开启、关闭,保证磁力搅拌与脉冲压力交替作用于反应溶液从而保证反应溶液与α-al2o3层的充分反应,达到陶瓷层的有效去除。进一步的,去除陶瓷层的整个过程中,始终保持温度维持在一定的温度范围内;过低的溶液温度将引起化学反应无法进行,过高的溶液温度对金属层存在一定的近表面腐蚀现象,只有将溶液温度控制在有效的范围内,才能保证碱液与α-al2o3层的充分反应。进一步的,从反应釜取出零件前,降低碱液温度与反应釜内的压力,保证操作安全。进一步的,通过热水进行冲洗零件;当零件取出时,表面附着有碱液,只有热水能够去除表面的碱液,且必须保证冲洗时间,使得冲洗干净。【附图说明】图1为实施例1陶瓷层去除前带涂层零件实物图;图2为实施例1陶瓷层去除后零件实物图;图3为陶瓷层去除前热障涂层显微组织形貌;图4为实施例1陶瓷层去除后金属层显微组织形貌;图5为实施例1陶瓷层再涂覆后热震考核零件实物图;图6为实施例2陶瓷层去除前带涂层零件实物图;图7为实施例2陶瓷层去除后零件实物图;图8为实施例2陶瓷层去除后金属层显微组织形貌;图9为实施例2陶瓷层再涂覆后热震考核零件实物图。【具体实施方式】下面结合具体步骤与附图对本发明做进一步详细描述,本发明公开了一种去除热障涂层中陶瓷层的加压碱煮方法;本发明通过控制加压碱煮工艺去除热障涂层中陶瓷层方法的工艺参数,以此实现陶瓷层的有效去除,金属底层的完整、无损伤。该方法具体过程包括以下步骤:1)按照预先设计的碱溶液比例进行配制;反应釜中的碱溶液采用naoh、koh和去离子水的混合液,其中碱性物质与去离子水的质量比例为1:1~1:8,碱性物质中naoh和koh的质量比为1:1~1:5,各类物质之间的比例根据不同的脉冲压力、温度、保温时间、搅拌转速进行按比例配制。2)将表面有陶瓷层的零件放置到高温高压反应釜中,关闭反应釜并保证反应釜的密封性;3)将反应釜中的碱溶液进行加热,控制加热温度,反应釜中的溶液温度控制范围为(100~350)±5℃,并设置磁力搅拌转速,转速为500~2000rpm,开启磁力搅拌,保证碱溶液温度的均匀性;反应过程只有将溶液温度控制在有效的范围内,保证碱液与α-al2o3层的充分反应,过低的溶液温度将引起化学反应无法进行,过高的溶液温度对金属层存在一定的近表面腐蚀现象。4)待温度升至工艺温度后,对反应釜进行脉冲加压,控制加压时间;应釜中的脉冲压力控制范围为10~100mpa,脉冲加压时,压力保持时间控制在30~90s。因陶瓷层呈柱状晶形貌,存在由表面至金属层的纵向显微通道,然而通道尺寸为纳米级,较小的脉冲压力无法将碱溶液输送到陶瓷层与金属层的界面,无法与α-al2o3层发生有效接触,而过高的脉冲压力又会引起叶片型面结构的变化。5)加压时,关闭磁力搅拌;加压停止时,开启磁力搅拌;磁力搅拌和脉冲加压的交互过程中脉冲压力和磁力搅拌转速不变,每次脉冲加压30~90s,磁力搅拌30~90s,整个过程中始终对反应釜进行加热,使得反应釜中溶液的温度为(100~350)±5℃。在磁力搅拌过程中,将磁力搅拌与脉冲压力配合开启、关闭,保证磁力搅拌与脉冲压力交替作用于反应溶液从而保证反应溶液与α-al2o3层的充分反应,达到陶瓷层的有效去除。6)重复步骤5),交替共持续20-60min;使得在加压、搅拌过程中,反应釜碱溶液温度控制在工艺温度范围内,保温时间达到工艺设定时间后,加压停止,开启磁力搅拌,关闭加热控制系统,开始降温,同时释放反应釜内压力;7)当反应釜内的温度降至50℃以下,反应釜内的压力为大气压时,打开反应釜,取出零件将陶瓷层去除干净的零件取出并放置到流动的热水中进行冲洗,热水温度为80~100℃,冲洗时间不少于1小时;8)冲洗结束后,将零件取出并使用真空烘箱烘干后装箱。实施例1:1)按照设计的碱溶液比例进行配制,naoh、koh和去离子水的质量分别为100g、100g、200g;2)将图1中的零件放置到高温高压反应釜中,关闭反应釜并保证反应釜的密封性;3)将反应釜中的碱溶液进行加热,控制加热温度为150±5℃,并设置磁力搅拌转速为1000rpm,开启磁力搅拌,保证碱溶液温度的均匀性;4)待温度升至工艺温度150±5℃后,停止磁力搅拌,对反应釜进行脉冲加压,脉冲压力设定为10~35mpa,控制加压时间为30s;5)加压停止后,开始磁力搅拌,磁力搅拌30s;磁力搅拌结束后,进行加压,加压时,关闭磁力搅拌;每次磁力搅拌时间30s,加压时间30s;6)重复步骤5),在加压、搅拌过程中,反应釜碱溶液温度控制在工艺温度150±5℃范围内,保温时间达到工艺设定时间20min后,加压停止,开启磁力搅拌,关闭加热控制系统,开始降温,同时释放反应釜内的压力;7)当反应釜内的温度降至50℃以下,压力与大气压相等时,打开反应釜,取出零件将陶瓷层去除干净的零件取出并放置到流动的热水中进行冲洗,热水温度为100℃;冲洗时间1小时后冲洗结束;8)冲洗结束后,将零件取出并使用真空烘箱烘干后装箱。图2为本实施方案陶瓷层去除后的零件实物图。从图2中可以看出,陶瓷层去除彻底,无任何陶瓷层残留。去除陶瓷层后,叶片表面呈均匀一致的颜色,未出现金属层剥落、起皮、鼓泡等缺陷。为验证陶瓷层去除后,金属底层减薄情况,对本实施方案后的叶片进行解剖检测涂层厚度(从零件的右侧切割一部分进行显微分析),如图4所示陶瓷层去除后金属层显微组织形貌,与图3所示陶瓷层去除前热障涂层显微组织形貌进行对比,未出现金属层开裂现象。同时,检测陶瓷层去除前后金属层厚度,结果如表1所示。从表1中可以看出,陶瓷层去除部位与存在陶瓷层部位的金属底层厚度未发生变化,金属底层保存完好。表1实施例1的陶瓷层去除前后各层厚度涂层类别去除面层前去除面层后底层厚度/μm3636面层厚度/μm2000同时,对陶瓷涂层去除后的叶片进行陶瓷层再涂覆,对再涂覆后的零件进行热震性能考核,考核条件是:1100℃保温5min,水冷1min,循环次数为100次。从图5陶瓷层再涂覆后热震考核零件实物图可以看出,涂层完整,涂层结合力和寿命较好。实施例21)按照设计的碱溶液比例进行配制,naoh、koh和去离子水的质量分别为100g、500g、4800g;2)将图6中的零件放置到高温高压反应釜中,关闭反应釜并保证反应釜的密封性;3)将反应釜中的碱溶液进行加热,控制加热温度为350±5℃,并设置磁力搅拌转速为2000rpm,开启磁力搅拌,保证碱溶液温度的均匀性;4)待温度升至工艺温度350±5℃后,停止磁力搅拌,对反应釜进行脉冲加压,脉冲压力设定为75~100mpa,控制加压时间为60s;5)加压停止后,开始磁力搅拌,磁力搅拌90s;磁力搅拌结束后,进行加压,加压时,关闭磁力搅拌;每次磁力搅拌时间90s,加压时间60s;6)重复步骤5),在加压、搅拌过程中,反应釜碱溶液温度控制在工艺温度350±5℃范围内,保温时间达到工艺设定时间50min后,加压停止,开启磁力搅拌,关闭加热控制系统,开始降温,同时释放反应釜内的压力;7)当反应釜内的温度降至50℃以下,压力与大气压相等时,打开反应釜,取出零件将陶瓷层去除干净的零件取出并放置到流动的热水中进行冲洗,热水温度为80℃,冲洗时间2小时后冲洗结束;8)冲洗结束后,将零件取出并使用真空烘箱烘干后装箱。图7为本实施方案陶瓷层去除后零件实物图。从图中可以看出,陶瓷层去除彻底,无任何陶瓷层残留。去除陶瓷层后,叶片表面呈均匀一致的颜色,未出现金属层剥落、起皮、鼓泡等缺陷。为验证陶瓷层去除后,金属底层减薄情况,对本实施方案后的叶片进行解剖检测涂层厚度,如图8所示陶瓷层去除后金属层显微组织形貌,与图3所示陶瓷层去除前热障涂层显微组织形貌进行对比,未出现金属层开裂现象。同时,检测陶瓷层去除前后金属层厚度,结果如表2所示。从表2中可以看出,陶瓷层去除部位与存在陶瓷层部位的金属底层厚度未发生变化,金属底层保存完好。表2实施例2的陶瓷层去除前后各层厚度涂层类别去除面层前去除面层后底层厚度/μm3636面层厚度/μm2000同时,对陶瓷涂层去除后的叶片进行陶瓷层再涂覆,对再涂覆后的零件进行热震性能考核,考核条件是:1100℃保温5min,水冷1min,循环次数为100次。从图9陶瓷层再涂覆后热震考核零件实物图可以看出,涂层完整,涂层结合力和寿命较好。实施例31)按照设计的碱溶液比例进行配制,naoh、koh和去离子水的质量分别为100g、300g、1600g;2)将图1中的零件放置到高温高压反应釜中,关闭反应釜并保证反应釜的密封性;3)将反应釜中的碱溶液进行加热,控制加热温度为100±5℃,并设置磁力搅拌转速为500rpm,开启磁力搅拌,保证碱溶液温度的均匀性;4)待温度升至工艺温度100±5℃后,停止磁力搅拌,对反应釜进行脉冲加压,脉冲压力设定为36~74mpa,控制加压时间为90s;5)加压停止后,开始磁力搅拌,磁力搅拌50s;磁力搅拌结束后,进行加压,加压时,关闭磁力搅拌;每次磁力搅拌时间50s,加压时间90s;6)重复步骤5),在加压、搅拌过程中,反应釜碱溶液温度控制在工艺温度100±5℃范围内,保温时间达到工艺设定时间60min后,加压停止,开启磁力搅拌,关闭加热控制系统,开始降温,同时释放反应釜内的压力;7)当反应釜内的温度降至50℃以下,压力与大气压相等时,打开反应釜,取出零件将陶瓷层去除干净的零件取出并放置到流动的热水中进行冲洗,热水温度为90℃;冲洗时间2小时后冲洗结束;8)冲洗结束后,将零件取出并使用真空烘箱烘干后装箱。为验证陶瓷层去除后,金属底层减薄情况,对本实施方案后的叶片进行解剖检测涂层厚度,同时检测陶瓷层去除前后金属层厚度,结果如表3所示。从表3中可以看出,陶瓷层去除部位与存在陶瓷层部位的金属底层厚度未发生变化,金属底层保存完好。表3实施例3的陶瓷层去除前后各层厚度涂层类别去除面层前去除面层后底层厚度/μm3636面层厚度/μm2000以上所述仅为本发明的较佳实施例而已,并不用以限制本发明,凡在本发明的精神和原则之内,所作的任何修改、等同替换、改进等,均应包含在本发明的保护范围之内。当前第1页12