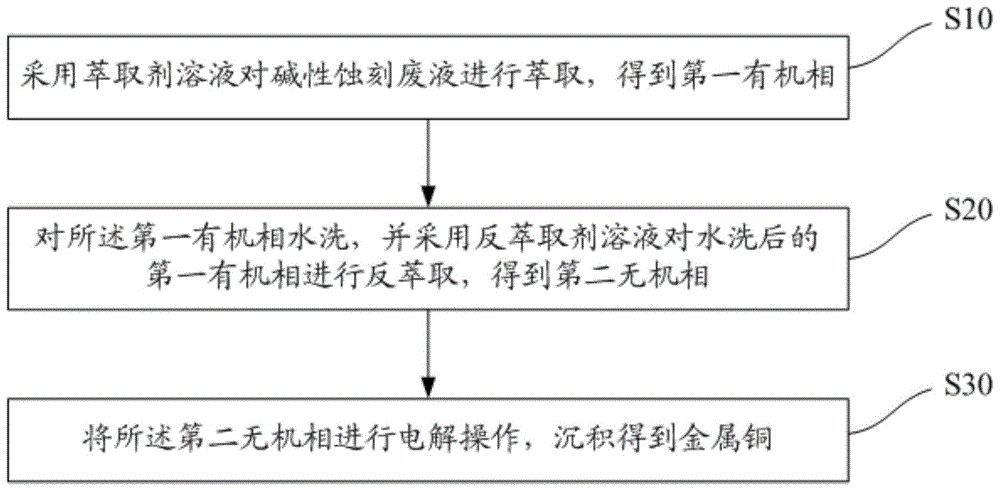
本发明涉及电路板碱性蚀刻废液处理
技术领域:
,特别涉及一种碱性蚀刻废液中铜的回收方法和回收系统。
背景技术:
:碱性蚀刻是印刷电路板制作过程中必不可少的关键工序,碱性蚀刻是指利用蚀刻液将工件上的线路防护层以外的裸露铜溶解蚀除,蚀刻过程中,当蚀刻液中铜离子的浓度达到饱和时蚀刻液失去蚀刻能力,便形成蚀刻废液,蚀刻废液含有大量的铜,因此很有必要从碱性蚀刻废液中回收金属铜。目前,碱性蚀刻废液中铜的回收方法一般采用直接电解方法,但是,由于铜表面往往容易附着有机物,则采用直接电解法电解沉积的铜纯度不高,品相较差。上述内容仅用于辅助理解本发明的技术方案,并不代表承认上述内容是现有技术。技术实现要素:本发明的主要目的是提供一种碱性蚀刻废液中铜的回收方法和回收系统,旨在提高电解沉积的铜品相。为实现上述目的,本发明提出的碱性蚀刻废液中铜的回收方法,包括以下步骤:采用萃取剂溶液对碱性蚀刻废液进行萃取,得到第一有机相;对所述第一有机相水洗,并采用反萃取剂溶液对水洗后的第一有机相进行反萃取,得到第二无机相;将所述第二无机相进行电解操作,沉积得到金属铜。在本发明的一实施例中,所述萃取剂溶液包括萃取剂和磺化煤油,所述萃取剂与所述磺化煤油的体积比范围值为1:5至7:20。在本发明的一实施例中,所述萃取剂选用酮肟系列铜萃取剂、铜萃取剂N901、铜萃取剂N902、铜萃取剂N910中的至少一种。在本发明的一实施例中,所述萃取剂溶液与所述碱性蚀刻废液的体积比范围值为1:1至2:1;和/或,所述反萃取剂溶液与所述第一有机相的体积比范围值为1:1至2:1;和/或,所述反萃取剂溶液为质量浓度为15%-25%的硫酸溶液。在本发明的一实施例中,所述萃取级数为多级;和/或,所述水洗级数为多级;和/或,所述反萃取级数为多级。在本发明的一实施例中,所述将所述第二无机相进行电解操作,沉积得到金属铜的步骤包括:将所述第二无机相通入电解槽中,以惰性金属为阳极,铜为阴极,在电流密度为200A/m2-400A/m2范围内进行电解,在阴极的表面沉积得到金属铜。在本发明的一实施例中,所述阳极选用镀层为铱的钛网板、镀层为钌的钛网板、铅板中的一种。在本发明的一实施例中,所述采用萃取剂溶液对碱性蚀刻废液进行萃取时,还得到第一无机相,所述采用萃取剂溶液对碱性蚀刻废液进行萃取,得到第一有机相步骤之后还包括:对所述第一无机相进行再生处理;和/或,所述采用反萃取剂溶液对水洗后的第一有机相进行反萃取时,还得到第二有机相,所述对所述第一有机相水洗,并采用反萃取剂溶液对水洗后的第一有机相进行反萃取,得到第二无机相步骤之后还包括:对所述第二有机相进行水洗,并循环至所述萃取剂溶液中,以作为萃取剂溶液使用;和/或,所述将所述第二无机相进行电解操作,沉积得到金属铜的步骤之后还包括:将电解回收铜后的电解液循环至反萃取剂溶液中,以作为反萃取剂溶液使用。本发明还提出了一种碱性蚀刻废液中铜的回收系统,应用于如前所述的碱性蚀刻废液中铜的回收方法,包括依次连通的碱性蚀刻废液收集桶、萃取槽、水洗槽、反萃取槽以及电解槽。在本发明的一实施例中,所述碱性蚀刻废液中铜的回收系统还包括蚀刻机缸和再生装置,所述蚀刻机缸连通所述碱性蚀刻废液收集桶,所述再生装置连通所述萃取槽和所述蚀刻机缸。本发明的技术方案,首先对碱性蚀刻废液进行萃取操作,使得其中的铜离子进入第一有机相,然后对第一有机相进行反萃取操作,使得铜离子进入第二无机相,最后对第二无机相进行电解操作便可沉积得到金属铜。由于电解操作之前采用萃取和反萃取操作,则能够有效去除铜表面易附着的有机物,使得最终电解沉积得到金属铜纯度较高,也即铜品相较好。附图说明为了更清楚地说明本发明实施例或现有技术中的技术方案,下面将对实施例或现有技术描述中所需要使用的附图作简单地介绍,显而易见地,下面描述中的附图仅仅是本发明的一些实施例,对于本领域普通技术人员来讲,在不付出创造性劳动的前提下,还可以根据这些附图示出的结构获得其他的附图。图1为本发明碱性蚀刻废液中铜的回收方法一实施例的步骤流程图;图2为本发明碱性蚀刻废液中铜的回收系统一实施例的流程示意图。附图标号说明:标号名称标号名称100回收系统60再生装置10碱性蚀刻废液收集桶61再生液储存桶20萃取槽62再生子液调配桶30水洗槽63再生子液储存桶40反萃取槽70蚀刻机缸50电解槽80水洗桶本发明目的的实现、功能特点及优点将结合实施例,参照附图做进一步说明。具体实施方式下面将对本发明实施例中的技术方案进行清楚、完整地描述,显然,所描述的实施例仅仅是本发明的一部分实施例,而不是全部的实施例。基于本发明中的实施例,本领域普通技术人员在没有作出创造性劳动前提下所获得的所有其他实施例,都属于本发明保护的范围。另外,各个实施例之间的技术方案可以相互结合,但是必须是以本领域普通技术人员能够实现为基础,当技术方案的结合出现相互矛盾或无法实现时应当认为这种技术方案的结合不存在,也不在本发明要求的保护范围之内。本发明提出一种碱性蚀刻废液中铜的回收方法。请参阅图1,在本发明的一实施例中,碱性蚀刻废液中铜的回收方法包括以下步骤:S10,采用萃取剂溶液对碱性蚀刻废液进行萃取,得到第一有机相;S20,对第一有机相水洗,并采用反萃取剂溶剂对水洗后的第一有机相进行反萃取,得到第二无机相;S30,将第二无机相进行电解操作,沉积得到金属铜。具体地,首先采用萃取剂溶剂对碱性蚀刻废液进行萃取操作,并搅拌30min-45min,静置待分层后,碱性蚀刻废液中的铜离子会与萃取剂中的有机基团结合并进入第一有机相。然后对得到的第一有机相进行水洗,以洗去第一有机相中残留的无机相或杂质;之后采用反萃取剂溶液对水洗后的第一有机相进行反萃取,并搅拌30min-45min,静置待分层后,铜离子进入第二无机相,这里反萃取剂溶液一般为无机酸溶液,能够与第一有机相中的铜离子结合成铜盐。最后对得到的第二无机相进行电解操作,便可沉积得到纯度较高的金属铜。因此,可以理解的,本发明的技术方案,首先对碱性蚀刻废液进行萃取操作,使得其中的铜离子进入第一有机相,然后对第一有机相进行反萃取操作,使得铜离子进入第二无机相,最后对第二无机相进行电解操作便可沉积得到金属铜。由于电解操作之前采用萃取和反萃取操作,则能够有效去除铜表面易附着的有机物,使得最终电解沉积得到金属铜纯度较高,也即铜品相较好。在本发明的一实施例中,萃取剂溶液包括萃取剂和磺化煤油,萃取剂和磺化煤油的体积比范围值为1:5-7:20。这里磺化煤油又称260号溶剂油,具有较好的溶解性,作为萃取剂的溶剂,能够较好地溶解萃取剂。在配制萃取剂溶液时要合理调配各组分的配比,以使得萃取剂溶液对铜的选择性和萃取效率较佳。比如采用萃取剂和磺化煤油的体积比值为1:5、或1:4、或3:10、或7:20。在本发明的一实施例中,萃取剂选用酮肟系列铜萃取剂、铜萃取剂N901、铜萃取剂N902、铜萃取剂N910中的至少一种。其中,酮肟系列铜萃取剂为高效铜萃取剂,对铜具有较高的选择性,能够使得碱性蚀刻废液中的铜尽可能完全与有机基团结合并进入第一有机相中,进而有利于提升铜回收率。这里酮肟系列铜萃取剂可选用高位阻β-二酮类萃取剂,可以直接从市场上购买得到。铜萃取剂N901、铜萃取剂N902及铜萃取剂N910均为高效铜萃取剂,能够萃取更多的铜,使得铜萃取率较高。在使用时,萃取剂可选用其中的一种或多种混合物。在本发明的一实施例中,萃取剂溶液与碱性蚀刻废液的体积比范围值为1:1至2:1;为了保证碱性蚀刻废液中铜离子能够尽可能完全萃取出来,则萃取剂溶液的用量要适宜,一般不能少于碱性蚀刻废液的用量。例如萃取剂溶液与碱性蚀刻废液的体积比为1:1、或1.5:1、或2:1。在本发明的一实施例中,反萃取剂溶液与第一有机相的体积比范围值为1:1至2:1。同样地,为了使得第一有机相中的铜离子能够尽可能完全反萃取出来,则反萃取剂溶液的用量也要适宜,一般不能少于第一有机相的用量,比如反萃取剂溶液与第一有机相的体积比为1:1、或1.5:1、或2:1。在本发明的一实施例中,反萃取剂为质量浓度为15%-25%的硫酸溶液。这里反萃取剂溶液选用硫酸溶液,使用时要选择合适浓度的硫酸溶液,以使得铜反萃取效果较佳。比如硫酸溶液采用质量分数为15%、或20%、或25%。当然地,这里反萃取剂溶液也可选用其他的酸溶液,比如稀盐酸溶液。在本发明的一实施例中,萃取级数为多级。采用多级萃取操作,能够使得碱性蚀刻废液中的铜离子尽可能完全萃取,以降低碱性蚀刻废液中的铜离子含量,并且提升铜萃取率,从而有利于铜回收率的提升。这里萃取级数可选用二级萃取、三级萃取或四级萃取,这样既能提升铜萃取率,又能节省萃取操作成本。在本发明的一实施例中,水洗级数为多级,采用多级水洗操作,能够更有效地去除第一有机相中残留的无机相和杂质,以提升后续铜反萃取率。这里水洗级数选用二级水洗或三级水洗,这样既能有效去除有机相中残留的无机相和杂质,又能节省水洗操作成本。在本发明的一实施例中,反萃取级数为多级。采用多级反萃取,能够使得第一有机相中的铜离子尽可能完全反萃取,提升铜反萃取率,进而有利于铜回收率的提升。需要说明的,本发明碱性蚀刻废液中铜的回收方法中,萃取级数、水洗级数及反萃取级数均为多级,这样会使得铜回收率较高,且电解沉积的铜纯度较高,品相较好。在本发明的一实施例中,步骤S30,将第二无机相进行电解操作,沉积得到金属铜包括:将第二无机相通入电解槽中,以惰性金属为阳极,铜为阴极,在电流密度为200A/m2-400A/m2范围内进行电解,在阴极的表面沉积得到金属铜。这里第二无机相作为电解液,由泵和管道通入至电解槽中,以铜片或铜箔为阴极,惰性金属为阳极,并保持电流密度为200A/m2-400A/m2范围内,如此便可进行高效率的电解操作,在阴极铜片或铜箔的表面沉积得到金属铜。在本发明的一实施例中,阳极选用镀层为铱的钛网板、镀层为钌的钛网板、铅板中的一种。钛网板的表面采用铱或钌镀层,能够提高电解操作的效率,并且能够延长阳极的使用寿命。当然也可选用铅板,电解效率也较高。在使用时可选用其中的任一种。进一步地,采用萃取剂溶液对碱性蚀刻废液进行萃取时,还得到第一无机相,步骤S10之后还包括:对第一无机相进行再生处理。由于第一无机相含有与蚀刻液相同的成分,则可以对第一无机相进行再生处理,以得到再生子液并循环用于蚀刻工序。这里对第一无机相进行再生处理,以提升资源利用率,节约资源成本,避免资源浪费。并且,对第一无机相进行再生处理得到的再生子液品质能够与市场上直接购买的蚀刻液相媲美,且蚀刻速率与市场上的无铜蚀刻液相当,从而实现了资源循环利用最大化。进一步地,采用反萃取剂溶液对水洗后的第一有机相进行反萃取时,还得到第二有机相,步骤S20之后还包括:对第二有机相进行水洗,并循环至萃取剂溶液中,以作为萃取剂溶液使用。由于第二有机相的成分与萃取剂溶液的成分相同,可以将其循环至萃取剂溶液中作为萃取剂溶液继续使用,如此,可提升资源利用率,节约资源成本,从而实现资源循环利用最大化。进一步地,步骤S30:将第二无机相进行电解操作,沉积得到金属铜的之后还包括:将电解回收铜后的电解液循环至反萃取剂溶液中,以作为反萃取剂溶液使用。由于电解回收铜后电解液成分与反萃取剂溶液成分相同,可以循环至反萃取剂溶液中作为反萃取剂溶液继续使用,以提升资源利用率,节约资源成本,实现资源循环利用最大化。需要说明的是,水洗水经过一定周期后,经由收集泵抽至氨氮处理机,利用折点氯气法进行处理,达到氨氮排放标准后排放至污水站进行综合处理。请参阅图2,本发明还提出了一种碱性蚀刻废液中铜的回收系统100,应用于如前所述的碱性蚀刻废液中铜的回收方法,包括依次连通的碱性蚀刻废液收集桶10、萃取槽20、水洗槽30、反萃取槽40以及电解槽50。碱性蚀刻废液收集10用于收集蚀刻工序产生的碱性蚀刻废液,萃取槽20用于碱性蚀刻废液的萃取操作,即将碱性蚀刻废液收集桶10中的碱性蚀刻废液抽至萃取槽20中,并加入萃取剂溶液,搅拌,进行萃取操作,静置分层后将第一有机相抽至水洗槽30中进行水洗操作,之后将水洗后的第一有机相抽至反萃取槽40中,并加入反萃取剂溶液,搅拌,静置后分层,并将第二无机相抽至电解槽50中进行电解操作,便可沉积得到金属铜。需要的说明的时,这里萃取槽20采用多个依次连通的萃取槽20,即采用多级萃取操作;同样地,水洗槽30也采用多个依次连通的水洗槽,即多级水洗操作;反萃取槽40也采用多个依次连通的反萃取槽40,即多级反萃取操作。可以理解的,最前面的萃取槽20连通于碱性蚀刻废液收集桶10,最后面的萃取槽20连通最前面的水洗槽30,最后面的水洗槽30连通于最前面的反萃取槽40,最后面的反萃取槽40连通电解槽50,这样,电解操作之前采用多级萃取、多级水洗及多级反萃取操作,则最终电解操作沉积得到的金属铜纯度较高,品相较好。在本发明的一实施例中,碱性蚀刻废液中铜的回收系统100还包括蚀刻机缸70和再生装置60,蚀刻机缸70连通碱性蚀刻废液收集桶10,再生装置60连通萃取槽20和蚀刻机缸70。如此的设置,萃取槽20中萃取后的第一无机相通入再生装置60中进行再生处理,经再生处理得到的再生子液可以循环至蚀刻机缸70中,作为蚀刻液继续使用。这里再生装置60包括依次连通的再生液储存桶60、再生子液调配桶61及再生子液储存桶63,再生液储存桶61连通于萃取槽20,再生子液储存桶63连通于蚀刻机缸70。如此,萃取槽20中萃取后的第一无机相首先进行再生液储存桶61中,然后分批量进入再生子液调配桶62中加入补加剂进行调配,以达到蚀刻液的标准,配置得到再生子液,之后进入再生子液储存桶63中储存,以便于蚀刻工序随时使用。需要说明的是,当萃取槽20设置有多个,再生液储存桶61连通于最后一个萃取槽20。同样的,反萃取槽40还连通有水洗桶80,使得反萃取槽40中反萃取后的第二有机相进入水洗桶80中,这里水洗桶80与前面的萃取槽20相连通,以使得水洗桶80中第二有机相循环至萃取槽20中,以作为萃取剂溶液循环利用。当萃取槽20设置有多个,水洗桶80连通于第一个萃取槽20。以下通过具体实施例对本发明碱性蚀刻废液中铜的回收方法和回收系统进行详细说明。实施例1本实施例中,碱性蚀刻废液中铜离子浓度为58g/L,氨氮值为18000ppm;首先,采用萃取剂溶液与碱性蚀刻废液的体积比为1:1,进行萃取操作,这里萃取剂溶液包括萃取剂和磺化煤油,且二者体积比值为20%,萃取剂选用高位阻β-二酮萃取剂,进行三级萃取操作,分层得到第一有机相和第一无机相,将第一无机相进行再生处理后并循环至蚀刻工序;将第一有机相进行二级水洗,水洗后采用质量浓度为20%的硫酸溶液作为反萃取剂溶液进行二级反萃取操作,得到第二有机相和第二无机相,这里反萃取剂溶液与第一有机相的体积比为1:1。将第二有机相水洗后循环至一级萃取中作为萃取剂溶液继续使用,将第二无机相通入电解槽中,以镀层为铱的钛网板为阳极,铜片为阴极,在电流密度为300A/m2下进行电解,在阴极铜片的表面沉积便可得到金属铜。实施例2本实施例中,碱性蚀刻废液中铜离子浓度为58g/L,氨氮值为18000ppm;首先,采用萃取剂溶液与碱性蚀刻废液的体积比为1.5:1,进行萃取操作,这里萃取剂溶液包括萃取剂和磺化煤油,且二者体积比值为25%,萃取剂选用铜萃取剂N901,进行三级萃取操作,分层得到第一有机相和第一无机相,将第一无机相进行再生处理后并循环至蚀刻工序;将第一有机相进行二级水洗,水洗后采用质量浓度为20%的硫酸溶液作为反萃取剂溶液进行二级反萃取操作,得到第二有机相和第二无机相,这里反萃取剂溶液与第一有机相的体积比为1.5:1。将第二有机相水洗后循环至一级萃取中作为萃取剂溶液继续使用,将第二无机相通入电解槽中,以镀层为钌的钛网板为阳极,铜片为阴极,在电流密度为300A/m2下进行电解,在阴极铜片的表面沉积便可得到金属铜。实施例3本实施例中,碱性蚀刻废液中铜离子浓度为58g/L,氨氮值为18000ppm;首先,采用萃取剂溶液与碱性蚀刻废液的体积比为2:1,进行萃取操作,这里萃取剂溶液包括萃取剂和磺化煤油,且二者体积比值为35%,萃取剂选用铜萃取剂N910,进行三级萃取操作,分层得到第一有机相和第一无机相,将第一无机相进行再生处理后并循环至蚀刻工序;将第一有机相进行二级水洗,水洗后采用质量浓度为25%的硫酸溶液作为反萃取剂溶液进行二级反萃取操作,得到第二有机相和第二无机相,这里反萃取剂溶液与第一有机相的体积比为2:1。将第二有机相水洗后循环至一级萃取中作为萃取剂溶液继续使用,将第二无机相通入电解槽中,以铅板为阳极,铜片为阴极,在电流密度为300A/m2下进行电解,在阴极铜片的表面沉积便可得到金属铜。对比例1本实施例中,碱性蚀刻废液中铜离子浓度为58g/L,氨氮值为18000ppm;直接将碱性蚀刻废液通入电解槽中,以石墨板为阳极,不锈钢板为阴极,在电流密度为300A/m2下进行电解,在阴极不锈钢板的表面沉积便可得到金属铜。对比例2本实施例中,碱性蚀刻废液中铜离子浓度为58g/L,氨氮值为18000ppm;首先,采用萃取剂溶液与碱性蚀刻废液的体积比为1:1,进行萃取操作,这里萃取剂溶液包括萃取剂和磺化煤油,且二者体积比值为20%,萃取剂选用羟肟系列萃取剂,进行三级萃取操作,分层得到第一有机相和第一无机相,将第一无机相进行再生处理后并循环至蚀刻工序;将第一有机相进行二级水洗,水洗后采用质量浓度为20%的硫酸溶液作为反萃取剂溶液进行二级反萃取操作,得到第二有机相和第二无机相,这里反萃取剂溶液与第一有机相的体积比为1:1。将第二有机相水洗后循环至一级萃取中作为萃取剂溶液继续使用,将第二无机相通入电解槽中,以镀层为铱的钛网板为阳极,铜片为阴极,在电流密度为300A/m2下进行电解,在阴极铜片的表面沉积便可得到金属铜。对各实施例和各对比例中性能参数如铜萃取率、反萃取效率、萃氨率及铜纯度进行计算,并将计算得到的数据记录表1中。由表1的性能参数数据可以看出,相较于对比例1(直接电解沉积铜)和对比例2(采用常规羟肟系列萃取剂进行三级萃取二级反萃取),本发明实施例1至实施例3中采用酮肟系列铜萃取剂、铜萃取剂N901、铜萃取剂N902、铜萃取剂N910中的至少一种,并进行三级萃取二级反萃取操作,其铜萃取效率和反萃取效率较高,则铜处理效率高,进而铜回收率较高。各实施例得到的萃氨率较低,则本发明使用的萃取剂寿命相比较长。并且,最终经电解沉积的金属铜纯度较高,品相较好。同时,由实施例1至实施例3进行比较发现,随着萃取剂浓度和用量的增加,铜萃取率提升;随着反萃取剂浓度和用量的增加,其反萃取效率提升;进而萃氨率下降,萃取剂的使用寿命延长,最终电解沉积得到的铜纯度升高。因此,本发明碱性蚀刻废液中铜的回收方法能够沉积得到纯度较高、品相较好的金属铜。表1各实施例和各对比例的性能参数以上所述仅为本发明的优选实施例,并非因此限制本发明的专利范围,凡是在本发明的发明构思下,利用本发明说明书内容所作的等效结构变换,或直接/间接运用在其他相关的
技术领域:
均包括在本发明的专利保护范围内。当前第1页1 2 3