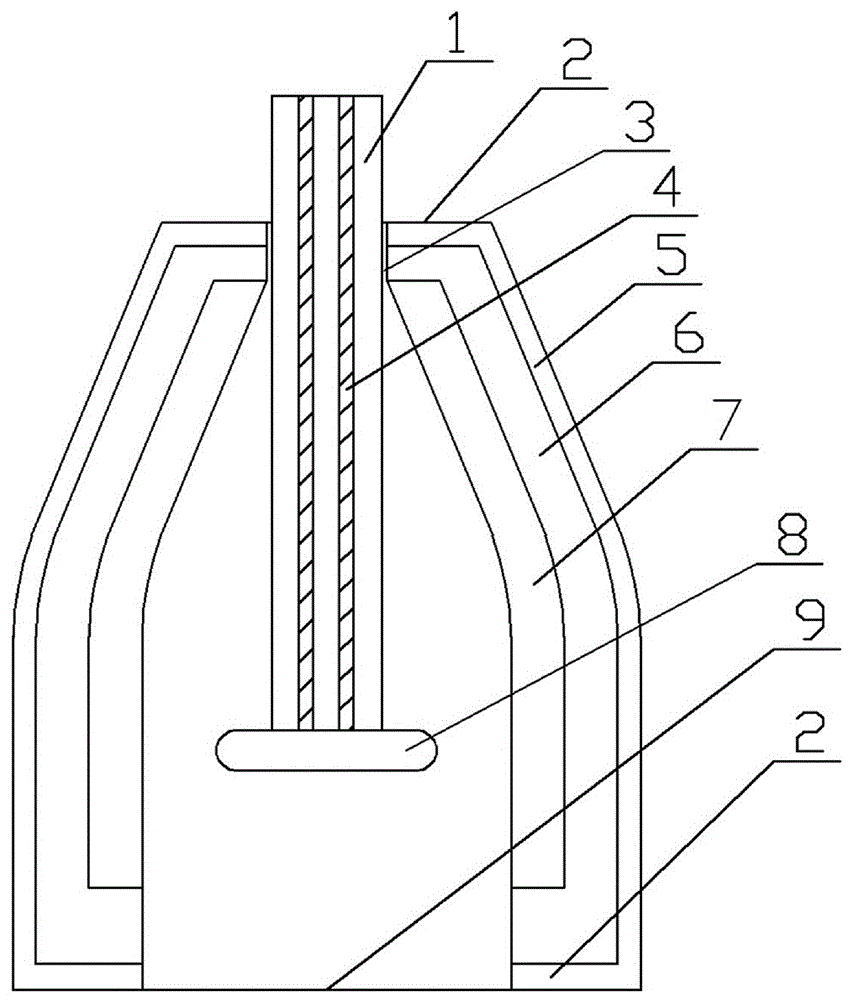
本发明属于机械铸造领域,涉及一种新型发热冒口,主要用于工程机械装载机车桥铸造。
背景技术:
:冒口是指为避免铸件出现缺陷而附加在铸件上方或侧面的补充部分。功能在铸型中,冒口的型腔是存贮液态金属的空腔,在铸件形成时补给金属,有防止缩孔、缩松、排气和集渣的作用,而冒口的主要作用是补缩。冒口的设计功能不同的冒口,其形式、大小和开设位置均不相同。排气作用是指浇注时型腔内的大量气体通过冒口顺利地排出型外;集渣作用是指由于冒口通常设在铸件顶部,熔渣上浮从而能够聚集击在冒口中,同时冒口还可以作为液态金属注满型腔的标志等作用。冒口要达到补缩的目的,必须满足以下条件。第一,冒口必须在有效的补缩距离之内;第二,冒口的模数必须大于铸件的模数,即冒口的凝固时间一定要比铸件的凝固时间长;第三,冒口内要有足够量的金属供给补缩铸件用;第四,冒口与铸件间的补缩通道,在凝固期间需要保持畅通。在车桥铸造工序中,钢水浇注入铸型后,由于冷却凝固,有液态转为固态,产生体积收缩。当体积收缩得不到金属液的补充时,在凝固后,铸件内模数较大的部位会产生缩松和缩孔。对于那些体积收缩较大的铸造合金,这种缺陷经常发生。缩孔和缩松会降低铸件的致密性,减少铸件的有效截面积,使力学性能大大降低,因此,必须设法控制,防止缺陷产生。使用冒口,是目前在铸造行业中控制凝固,补偿收缩的最有效,最普及的工艺措施。传统冒口本身不发热,造成冒口内钢水冷却太快,使得冒口的作用周期短,缩短了金属的凝固时间,造成冒口补缩效率低。目前,发热冒口一般有两种,一种是以铝粉、硅粉和氧化铁粉组成的发热剂,这种冒口虽然发热效果好,但是保温效果差,并且结构强度低,易破损;还有一种是通过介质加热,一般采用电加热,冒口内设置加热丝,并且对冒口进行重复利用以降低成本,但是冒口使用一次后,表面就会破损或粘留金属渣,即使重复使用,寿命依然较短。冒口内钢水的量不方便观测和控制,使用起来十分不方便。技术实现要素:本发明的目的是解决现有技术存在保温效果差以及使用不方便的技术问题,提供一种新型发热冒口,以克服现有技术的不足。一种新型发热冒口,包括两头设有开口的筒状冒口本体;所述冒口本体由内到外依次设有加热层、保温层和壳体层;所述冒口本体两端的开口分别为排气口和套接口;所述冒口本体的直径向排气口一侧逐渐收缩;所述保温层和壳体层的两端分别设有向排气口和套接口垂直延伸的弯折部。进一步的,所述冒口本体内设有浮块体;所述浮块体呈圆形并有一定厚度;所述浮块体上设有垂直连接的观测杆;所述观测杆的另一端为自由端,从冒口本体的排气口中垂直伸出;所述观测杆上设有条形凹槽气道。进一步的,所述浮块体和观测杆采用耐高温材料,其成分包括氧化钙、氧化镁、氧化硅、氧化铝和三氧化二铁;其中氧化钙含量为40%-60%,氧化镁含量为35%-55%,氧化钙和氧化镁的含量不低于95%。进一步的,所述壳体层采用从中间竖向断开的两半式,然后进行对接,在对接缝的两侧设有相对应的连接板,连接板上设有对应的螺栓孔,通过拧接螺栓进行固定。进一步的,所述加热层采用铝粉、硅粉、氧化铁粉和碳粉的混合物。进一步的,所述保温层采用珍珠岩、石棉、硅土、耐火纤维和高岭土的混合物;按重量分,其比例为:珍珠岩30%-50%、石棉5%-10%、硅土20%-40%、耐火纤维5%-10%和高岭土5%-10%。进一步的,所述壳体层采用金属壳体。其制备步骤为:1).制作壳体层,采用卷板机和液压冲机制作壳体层的侧面板,然后将裁切好的弯折部焊接在侧面板上,焊接连接板、把手;2).制作加热层,制作加热层内外侧对应的模具,将加热层的混合物填充在模具中,压实,将外侧模具取出;3).制作保温层,制作保温层外侧对应的模具,将外侧模具套接在步骤2的加热层上,将保温层的混合物填充在步骤2的加热层外侧和外侧模具之间,压实;取出保温层外侧模具和加热层内侧模具;4).套接壳体层,将壳体层从保温层的两侧卡入、对接,然后将螺栓拧接在连接板上固定;由于壳体层采用焊接,尺寸会有小部分误差,若壳体层与保温层之间留有间隙,可以填充石棉,或在保温层外面缠绕石棉,再将壳体层卡入、对接;5).制作浮块体和观测杆;将添加有镁土和硅土的耐火粘土通过模具制备成型,然后煅烧得到成品,成品中的氧化钙极易与空气中水分反应,所以密封保存。将浮块体和观测杆通过套接口放置于冒口本体内,观测杆从排气口中伸出,将冒口本体套接在铸件模具上,浇注满后,金属液流入冒口内部,将浮块体顶起,观测杆上升,以此来确定金属液的实时量。发热保温冒口通过发热层反应产生热量、保温层减缓热量损失的双效结合,提高冒口内金属液温度,延长冒口内金属液的凝固时间,实现冒口对铸件的补缩,并有效提高补缩能力。附图说明图1是本发明剖视结构示意图;图2是本发明立体结构示意图。1.观测杆2.弯折部3.排气口4.气道5.壳体层6.保温层7.加热层8.浮块体9.套接口10.对接缝11.连接板。具体实施方式为了使本
技术领域:
的人员更好地理解本申请中的技术方案,下面将结合本申请具体实施例,对本发明进行更加清楚、完整地描述,显然,所描述的实施例仅仅是本申请一部分实施例,而不是全部的实施例。基于本申请中的实施例,本领域普通技术人员在没有作出创造性劳动前提下所获得的所有其他实施例,都应当属于本发明保护的范围。实施例1一种新型发热冒口,包括两头设有开口的筒状冒口本体;所述冒口本体由内到外依次设有加热层7、保温层6和壳体层5;所述冒口本体两端的开口分别为排气口3和套接口9;所述冒口本体的直径向排气口一侧逐渐收缩;所述保温层和壳体层的两端分别设有向排气口和套接口垂直延伸的弯折部2。所述冒口本体内设有浮块体8;所述浮块体呈圆形并有一定厚度;所述浮块体上设有垂直连接的观测杆1;所述观测杆的另一端为自由端,从冒口本体的排气口3中垂直伸出;所述观测杆上设有条形凹槽气道4。所述浮块体和观测杆采用耐高温材料,其成分包括氧化钙、氧化镁、氧化硅、氧化铝和三氧化二铁;其中氧化钙含量为40%-60%,氧化镁含量为35%-55%,氧化钙和氧化镁的含量不低于95%。所述壳体层采用从中间竖向断开的两半式,然后进行对接,在对接缝的两侧设有相对应的连接板,连接板上设有对应的螺栓孔,通过拧接螺栓进行固定。所述加热层采用铝粉、硅粉、氧化铁粉和碳粉的混合物。所述保温层采用珍珠岩、石棉、硅土、耐火纤维和高岭土的混合物;按重量分,其比例为:珍珠岩30%-50%、石棉5%-10%、硅土20%-40%、耐火纤维5%-10%和高岭土5%-10%。所述壳体层采用金属壳体。所述冒口本体的中间呈圆柱形,上部或上、下部设有锥形或弧形收缩。其制备步骤为:1).制作壳体层,采用卷板机和液压冲机制作壳体层的侧面板,然后将裁切好的弯折部焊接在侧面板上,焊接连接板、把手;2).制作加热层,制作加热层内外侧对应的模具,将加热层的混合物填充在模具中,压实,将外侧模具取出;3).制作保温层,制作保温层外侧对应的模具,将外侧模具套接在步骤2的加热层上,将保温层的混合物填充在步骤2的加热层外侧和外侧模具之间,压实;取出保温层外侧模具和加热层内侧模具;4).套接壳体层,将壳体层从保温层的两侧卡入、对接,然后将螺栓拧接在连接板上固定;由于壳体层采用焊接,尺寸会有小部分误差,若壳体层与保温层之间留有间隙,可以填充石棉,或在保温层外面缠绕石棉,再将壳体层卡入、对接;5).制作浮块体和观测杆;将添加有镁土和硅土的耐火粘土通过模具制备成型,然后煅烧得到成品,成品中的氧化钙极易与空气中水分反应,所以密封保存。所述壳体层为重复使用部件;所述保温层可以重复使用多次,直至成份出现结晶硬块再更换。实施例2所述保温层中的珍珠岩、石棉、硅土、耐火纤维和高岭土按重量分,其比例为:珍珠岩40%、石棉10%、硅土40%、耐火纤维5%%和高岭土5%%。所述珍珠岩选用尺寸为1-3mm的小颗粒珍珠岩,加入石棉、硅土、耐火纤维和高岭土后混合均匀。实施例3本品与砂型冒口、发热冒口进行温度对比试验,见表1:表1时间(分钟)0.513579实验组(实施例1)温度℃140015001450140013001200对照组1(砂型冒口)温度℃900140012001000800600对照组2(发热冒口)温度℃140014501350125011501000由表1可知,本申请的保温效果要明显超出砂型冒口和发热冒口,冒口补缩时间一般为5分钟左右,本申请在第5分钟时,冒口内温度为1400℃,里面金属为液体状体,可以完全达到补缩状态,而砂型冒口已经下降到1000℃,发热冒口已经下降到1250℃,都以出现结渣现象,影响补缩。实施例4在车桥铸造时,采用中间浇注,两侧补缩的方式,将浮块体和观测杆通过套接口放置于冒口本体内,观测杆从排气口中伸出,将冒口本体套接在铸件模具的两端,浇注满后,金属液流入冒口内部,将浮块体顶起,观测杆上升,以此来确定金属液的实时量。冒口本体内的金属液对铸件进行补缩,产生的气泡从观测杆的气道中排出,在补缩过程中,铝粉、硅粉、氧化铁粉和碳粉的混合物受热发生反应,反应过程中持续放热,保持金属液的温度;保温层有效防止温度散发。浮块体在金属液的上表面,也可以减少热量散发,从而不用添加覆盖剂。补缩完成后,将壳体层取下,然后将保温层、加热层和剩余金属渣切割取下,壳体层重复利用,保温层根据结晶情况选择是否再利用。发热保温冒口通过发热层反应产生热量、保温层减缓热量损失的双效结合,提高冒口内金属液温度,延长冒口内金属液的凝固时间,实现冒口对铸件的补缩,并有效提高补缩能力,有效的解决了现有技术存在保温效果差以及使用不方便的技术问题。当前第1页12