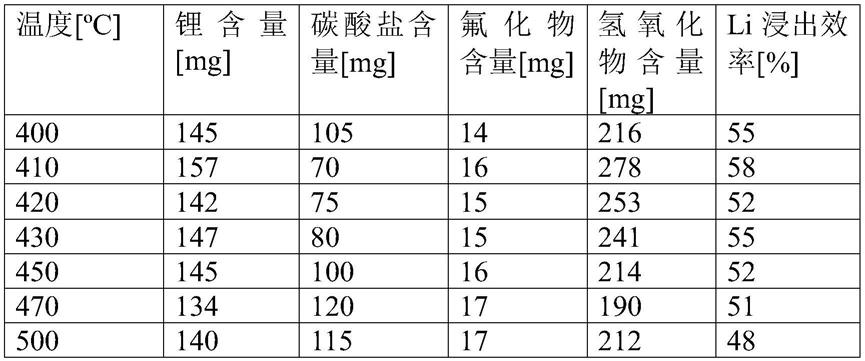
用于使废锂离子电池单元再循环的方法
[0001]
本发明涉及用于从含镍的废锂离子电池中回收过渡金属的方法,所述方法包括以下步骤:
[0002]
(a)在h2存在下,将含锂的过渡金属氧化物材料加热至在200至900℃的范围内的温度,所述材料包含典型的杂质,诸如氟化合物(例如无机氟化物)和/或磷化合物,
[0003]
(b)用水性介质处理在步骤(a)中获得的产物,
[0004]
(c)用于从步骤(b)的固体残留物中去除ni的固-固分离,
[0005]
(d)从在步骤(b)中获得的溶液中回收作为氢氧化物或盐的li,以及任选地进一步
[0006]
(e)从在步骤(c)中获得的固体ni-浓缩物中提取ni以及如果适用的话co。
[0007]
储存电能是日益增长的兴趣的主题。有效的电能储存将允许电能在有利时产生,并在需要的时间和需要的地点使用。二次电化学电池单元由于其可再充电性而非常适合于此目的。二次锂电池对于储能具有具体的兴趣,因为它们提供了归因于锂的小原子量和大电离能的高能量密度,并且它们已广泛用作许多便携式电子器件(诸如移动电话、膝上型计算机、微型相机等)的电源,但也用于电动车辆的电源。尤其对原料诸如钴和镍的日益增长的需求将在未来时间引起挑战。
[0008]
锂离子电池的寿命不是无限的。因此,预期将出现日益增长的数目的废锂离子电池。由于废锂离子电池包含重要的过渡金属诸如但不限于钴和镍以及另外锂,因此,废锂离子电池可能会成为用于新一代锂离子电池的原料的有价值的来源。出于这个原因,以从使用过的锂离子电池中使过渡金属以及任选地甚至锂再循环为目标,已经进行了增加的研究工作。
[0009]
不满足规格和要求的锂离子电池或锂离子电池的部分(所谓的不合格材料和生产废物)也可能是原料的来源。
[0010]
原料回收经过两个主要过程。一个主要过程基于对相应的电池废料进行熔炼,紧接着对从熔炼过程中获得的金属合金(锍)进行湿法冶金加工。另一个主要过程是对电池废料材料进行直接湿法冶金加工。原理已经公开于wo 2017/091562和电源杂志(j.power sources),2014,262,255ff。这样的湿法冶金过程将单独地或已经以用于制造新的阴极活性材料的所需的化学计量供应作为水性溶液或呈沉淀形式,例如作为氢氧化物的过渡金属。在后一种情况下,可以通过添加单一金属组分将金属盐溶液的组成调节至所需的化学计量。
[0011]
在wo 2017/091562中,描述了过渡金属的共沉淀。在wo 2014/180743中,描述了其中使用氨或胺的共沉淀方法。
[0012]
开始于用模型物质如licoo2的转化实验,jp 2012-229481公开了一种用于从废锂离子电池中回收金属的方法,该方法包括初步浸渍步骤,紧接着高温氧化、还原焙烧、用过滤的水性处理以及从滤液中回收碳酸锂以及从残留物中回收过渡金属。
[0013]
用于回收这样的有价值的材料的已知方法通常面临以下问题:废电池,即其中包含大多数这些材料的电池单元必须被拆卸以机械分离成分如电极和电解质,或者包含高水平的杂质如氟和/或磷化合物,必须要去除这些杂质以允许用于新电池单元(电池级材料)
生产的纯度回收所需的材料。因此,本发明的目的是提供一种允许容易地回收镍以及如果存在的话钴和锰的方法。本发明的另一个目的是提供一种用于回收电池废料中所包含的另外有价值的元素,即锂和作为石墨的碳的方法。本发明的另外的目的是提供一种减少昂贵和/或能耗步骤的数目的经济方法。本发明的具体目的是提供一种允许有效地回收镍,任选地钴和锰以及锂的方法。本发明的另外的目的是提供一种用于以高纯度回收所述过渡金属和锂,尤其具有低含量的铜和贵金属如ag、au和铂族金属的方法。
[0014]
因此,已经发现如在开始时定义的方法,在下文中也称为本发明的方法或本发明的再循环方法。本发明的方法包括以下更详细定义的步骤,在下文中也称为步骤(a)、步骤(b)、步骤(c)等:
[0015]
(a)在h2存在下,将含锂的过渡金属氧化物材料加热至在200至900℃的范围内的温度,所述材料源于锂离子电池并且包含作为杂质的氟化合物和/或磷化合物,
[0016]
(b)用水性介质处理在步骤(a)中获得的产物,
[0017]
(c)用于从步骤(b)的固体残留物中去除ni和如果适用的话co的固-固分离,
[0018]
(d)从在步骤(b)中获得的溶液中回收作为氢氧化物或盐的li,以及
[0019]
(e)从在步骤(c)中获得的固体ni-浓缩物中提取ni以及如果适用的话co。
[0020]
因此,本发明的典型方法包括以下步骤:
[0021]
(a)在h2存在下,将含锂的过渡金属氧化物材料加热至在200至900℃的范围内的温度,
[0022]
(b)用水性介质处理在步骤(a)中获得的产物,
[0023]
(c)用于从步骤(b)的固体残留物中去除ni的固-固分离,
[0024]
(d)从在步骤(b)中获得的溶液中回收作为氢氧化物或盐的li,
[0025]
(e)从在步骤(c)中获得的固体ni-浓缩物中提取ni以及如果适用的话co;
[0026]
其中在步骤(a)中加热的含锂的过渡金属氧化物材料源于锂离子电池,并且包含相对于所述含锂的过渡金属氧化物材料的重量在按重量计0.5至8、典型地1至8以及尤其2至8%的范围内的氟和/或按重量计在0.2%至2%的范围内的磷。
[0027]
然而,也可以按照以下顺序(步骤(a)、步骤(c)、以及然后步骤(b))进行步骤(a)至(c)。在本发明的优选实施方式中,按照上述字母顺序进行步骤(a)至(c),紧接着是步骤(d)和(e)。
[0028]
步骤(a)包括将含锂的过渡金属氧化物材料加热至在200-900℃、优选地300至600℃、更优选地350至500℃的范围内的温度。由于强加热,尤其在氧化条件下(但也在还原性气氛下,程度稍轻),倾向于增加形成不溶物质(诸如limno2),则优选的是通常不将含锂的过渡金属氧化物材料暴露于500℃或更高的温度(例如,高于450℃的温度)。所以,优选的是在含锂的过渡金属氧化物材料的制备期间以及还在步骤(a)中将温度保持低于500℃或甚至低于450℃,并且优选地在该步骤中将材料保持在范围350至450℃、尤其380至440℃的温度。
[0029]
用于进行还原的气氛包含按体积计0.1%至100%的氢气。在一种实施方式中,其包含按体积计3%至50%的氢气,其余为非氧化性气体,优选地氮气、氩气、蒸汽、一氧化碳、二氧化碳或这些气体中的至少两种的混合物。优选的非氧化性气体是氮气和蒸汽以及氮气和蒸汽的混合物。在优选实施方式中,主要在氢气下,例如在包含按体积计(正常条件)35至
100%、优选地50至100%的氢气,其余如果存在的话是非氧化性气体的气氛下进行本方法的步骤(a)。
[0030]
在本发明的一种实施方式中,步骤(a)具有的持续时间在10分钟至30小时、优选地20min至8小时、更优选地30min至4小时的范围内。具有具体技术兴趣的是步骤(a)的持续时间持续20至90分钟,尤其30-60分钟。
[0031]
还原气氛中的氢气的浓度和反应时间相互依赖。通常,低浓度的氢气需要更长的还原时间,并且反之亦然。
[0032]
在本发明的优选方法中,因此通过在按体积计大于35%、尤其50-100%的h2存在下以及持续20至90分钟的时间段将含锂的过渡金属氧化物材料加热至在350至450℃的范围内的温度来进行步骤(a)。在本发明中,特别优选的方法使用以下进行步骤(a)以以尤其有效的方式回收li:400与420℃之间的温度持续最长达2.5小时(尤其约30至60分钟)以及35体积-%或更多的氢气;施加太高的温度可能导致较低的产率,较长的持续时间不会导致负面影响,但倾向于降低时空产率,而h2浓度≥35vol-%转化成短反应时间≤2.5h,以及因此是有利的;使用纯氢气可获得最佳的时空产率。
[0033]
在本发明的一种实施方式中,选择与步骤(a)的氢气浓度和持续时间相关的还原条件,使得至少一部分含锂的过渡金属氧化物材料包含通过施加磁场可以分离的顺磁性、铁磁性或亚铁磁性组分。优选的是由含锂的过渡金属材料的至少部分还原产生的铁磁性或亚铁磁性组分的形成。关于含锂的过渡金属材料中所包含的镍,还原度可以在1至100%之间的范围内变化,优选的是范围为80至100%。
[0034]
所述含锂的过渡金属氧化物材料是源于锂离子电池或锂离子电池的部分的材料。通常,所述含锂的过渡金属氧化物材料是在机械去除壳体、布线或电路之后获得的,从而通常主要由电池单元材料组成。出于安全原因,这样的锂离子电池完全放电,例如通过浸入干燥的导电浴,诸如金属碎片中,或以受控方式将电流例如经由逆变器输入到电网中。否则,可能发生短路,构成火灾和爆炸危险。这样的锂离子电池可以例如在锤式粉碎机中拆卸、穿孔、碾磨或者例如在工业粉碎机中撕碎。
[0035]
有利的是在开始步骤(a)之前至少部分地去除电解质,尤其包括有机溶剂或有机溶剂的混合物的电解质,例如通过干燥,例如在大气压或以下在50至250℃的范围内的温度下。如上所述,在使含锂的过渡金属氧化物材料经受本步骤(a)之前,含锂的过渡金属氧化物材料优选地不暴露于氧化性条件下的高温(尤其400℃或更高)。
[0036]
在本发明的一种实施方式中,所述含锂的过渡金属氧化物材料来自电池废料。在本发明的优选实施方式中,所述含锂的过渡金属氧化物材料来自机械处理的电池废料,例如来自在锤式粉碎机或工业粉碎机中处理的电池废料。这样的含锂的过渡金属氧化物材料可以具有的平均粒径(d50)在1μm至1cm的范围内。
[0037]
在本发明的一种实施方式中,在步骤(a)之前进行步骤(a1),所述步骤(a1)包括通过固-固分离方法去除例如碳或有机聚合物。这样的固-固分离方法的实例是电分选、筛分、磁分离或其他分类方法。固-固分离可以干式进行或在合适的分散介质,优选地水存在下进行。
[0038]
在本发明的一种实施方式中,在步骤(a)之前将机械处理的电池废料进行研磨。这样的研磨优选地在球磨机或搅拌式球磨机中进行。碾磨可以在湿式或干式条件,优选地干
式条件下进行。
[0039]
在本发明的一种实施方式中,使机械处理的电池废料经受溶剂处理,以溶解和分离用于将锂过渡金属氧化物结合到集电器膜上的聚合物粘合剂。合适的溶剂是以其纯形式或作为混合物的n-甲基吡咯烷酮、n,n-二甲基甲酰胺、n,n-二甲基乙酰胺和n-乙基吡咯烷酮、二甲基亚砜、六甲基磷酰胺、四甲基脲、磷酸三甲酯和磷酸三乙酯。
[0040]
上文描述的溶剂处理可以用一种或多种溶剂在连续步骤中进行或在使用能够溶解电解质组分和粘合剂聚合物的溶剂的一个步骤中进行。在范围为10℃至200℃的温度下施加溶剂。尤其聚合物的溶解可需要在范围为50至200℃,优选地100与150℃之间的升高的温度。除非施加高于1巴的压力,否则上限温度通常受溶剂沸点的限制。
[0041]
在一种实施方式中,在不存在湿度下,例如在干燥的气体如干燥的空气、干燥的氮气下,用非质子溶剂进行机械处理的电池废料的洗涤。
[0042]
在本发明的一种实施方式中,所述含锂的过渡金属氧化物材料不包含大量的杂质,诸如但不限于来自锂离子电池的部分的其他部分或材料。这样的含锂的过渡金属氧化物材料可以包括不合格材料。
[0043]
然而,所述含锂的过渡金属氧化物材料优选地包含在按重量计0.1至80%的范围内的除镍化合物(诸如镍/钴组分或镍/钴/锰或镍/钴/铝化合物)之外的化合物,以及如果适用的话,在极端情况下,有价值的材料是少数组分。这样的组分的实例是呈导电形式的碳,在下文中也称为导电碳,例如石墨、烟灰和石墨烯。杂质的另外的实例是铜及其化合物,铝及铝的化合物,例如氧化铝,铁及铁化合物,锌及锌化合物,硅及硅化合物,例如二氧化硅和具有零<y≤2的氧化硅sio
y
,锡、硅-锡合金,以及有机聚合物,诸如聚乙烯、聚丙烯和氟化聚合物,例如聚偏二氟乙烯、四氟乙烯聚合物等。另外的杂质包括氟化合物,例如无机氟化物,以及磷化合物,其可源于液体电解质,例如在广泛使用的lipf6中以及源于lipf6的水解的产物中。用作本发明方法的起始材料的电池废料可源于多个来源,以及因此在大多数实施方式中,所述含锂的过渡金属氧化物材料包含除镍/钴化合物或镍/钴/锰或镍/钴/铝组分以外的化合物,如果适用的话,这样的组分中的一种是相对于整个含锂的过渡金属氧化物材料在按重量计2至65%的范围内的呈导电形式的碳。
[0044]
在本发明的优选实施方式中,所述含锂的过渡金属氧化物材料包含在按重量计20ppm至3%的范围内的作为金属或呈其化合物中的一种或多种的形式的铜。
[0045]
在本发明的优选实施方式中,所述含锂的过渡金属氧化物材料包含在按重量计100ppm至15%的范围内的作为金属或呈其化合物中的一种或多种的形式的铝。
[0046]
在本发明的优选实施方式中,所述含锂的过渡金属氧化物材料包含在按重量计100ppm至5%的范围内的作为金属或合金或呈其化合物中的一种或多种的形式的铁。
[0047]
在本发明的优选实施方式中,所述含锂的过渡金属氧化物材料包含在按重量计20ppm至2%的范围内的作为金属或合金或呈其化合物中的一种或多种的形式的锌。
[0048]
在本发明的优选实施方式中,所述含锂的过渡金属氧化物材料包含在按重量计20ppm至2%的范围内的作为金属或合金或呈其化合物中的一种或多种的形式的锆。
[0049]
在本发明的优选实施方式中,所述含锂的过渡金属氧化物材料包含在按重量计0.5至8、典型地1至8以及尤其2%至8%的范围内的氟,以有机氟化物(例如,结合在聚合物中的)以及无机氟化物(以其无机氟化物中的一种或多种)的总和计算。
[0050]
在本发明的优选实施方式中,所述含锂的过渡金属氧化物材料包含在按重量计0.2%至2%的范围内的磷。磷可以存在于一种或多种无机化合物中。
[0051]
上文给出的百分数中的每一个均是干燥的材料(即含锂的过渡金属氧化物材料)的按重量计。
[0052]
所述含锂的过渡金属氧化物材料包含镍和钴。含锂的过渡金属氧化物材料的实例可以基于锂化的镍钴锰氧化物(“ncm”)或锂化的镍钴铝氧化物(“nca”)或其混合物。
[0053]
层状镍-钴-锰氧化物的实例为通式li
1+x
(ni
a
co
b
mn
c
m
1d
)
1-x
o2的化合物,其中m1选自mg、ca、ba、al、ti、zr、zn、mo、v和fe,另外的变量定义如下:
[0054]
零≤x≤0.2
[0055]
0.1≤a≤0.8,
[0056]
零≤b≤0.99;通常零≤b≤0.5,优选地0.05<b≤0.5,
[0057]
零≤c≤0.6,
[0058]
零≤d≤0.1,并且a+b+c+d=1。
[0059]
在优选实施方式中,在根据通式(i)的化合物中
[0060]
li
(1+x)
[ni
a
co
b
mn
c
m
1d
]
(1-x)
o
2 (i)
[0061]
m1选自ca、mg、zr、al和ba,
[0062]
并且另外的变量如上文定义。
[0063]
锂化的镍-钴铝氧化物的实例为通式li[ni
h
co
i
al
j
]o
2+r
的化合物。r、h、i和j的典型值为:
[0064]
h在0.8至0.90的范围内,
[0065]
i在0.15至0.19的范围内,
[0066]
j在0.01至0.05的范围内,并且
[0067]
r在零至0.4的范围内。
[0068]
特别优选的是li
(1+x)
[ni
0.33
co
0.33
mn
0.33
]
(1-x)
o2、li
(1+x)
[ni
0.5
co
0.2
mn
0.3
]
(1-x)
o2、li
(1+x)
[ni
0.6
co
0.2
mn
0.2
]
(1-x)
o2、li
(1+x)
[ni
0.7
co
0.2
mn
0.1
]
(1-x)
o2、li
(1+x)
[ni
0.8
co
0.1
mn
0.1
]
(1-x)
o2(各个具有如上文定义的x)以及li[ni
0.85
co
0.13
al
0.02
]o2。
[0069]
所述含锂的过渡金属氧化物材料可以具有规则的形状,但是其通常具有不规则的形状。尽管,优选的是,例如在强制气流中,尽可能地从有机塑料和铝箔或铜箔中去除轻部分,诸如外壳零件。
[0070]
在一种实施方式中,在步骤(a)期间改变气氛的组成,例如,在进料中存在挥发性有机化合物的情况下,这可以进行,在惰性气氛下将挥发性有机化合物去除,然后将气氛切换为含氢气的气氛。
[0071]
在一种实施方式中,在用含氢气的气氛还原之前,在步骤(a)中使用范围在20至350℃之间的温度下的氧化性气氛。通过这种实施方式,可以烧掉一些杂质组分,即有机组分,或干燥材料(尤其使用如上文进一步所述的最高达250℃的温度。优选的氧化性气体是氧气或含氧气的气体,例如空气。进行本方法的步骤,优选地不使源于废锂离子电池单元的,含锂、过渡金属氧化物以及另外的氟和/或磷化合物的材料经受高于350℃的氧化。
[0072]
在一种实施方式中,在用含氢气的气氛还原之前,在步骤(a)中采用温度在20至900℃,尤其20至450℃之间的温度范围内的非氧化性且非还原性气氛。由此,可以去除挥发
性化合物。优选的气体是惰性气体,如氮气和氩气或二氧化碳。
[0073]
在本发明的一种实施方式中,在100与900℃之间的温度范围,诸如上文对于步骤(a)指定的温度范围内在蒸汽存在下进行步骤(a)。当在含氢气的气氛下还原之前去除挥发性有机化合物时,也可以添加蒸汽。
[0074]
在本发明的一种实施方式中,在石灰、石英或一种或多种硅酸盐或二氧化硅或其混合物,优选为石灰和二氧化硅存在下进行步骤(a)。石灰可以选自熟石灰和生石灰或煅石灰。在本发明的优选实施方式中,在相对于含锂的过渡金属氧化物材料按重量计2至40%的石灰或石英或硅酸盐或二氧化硅存在下进行步骤(a)。当使用这样的化合物时,在如上文所述的用含氢气的气氛还原之前,热处理可以是有利的。可以在上文提及的气氛的任一种,优选的是也可以包含蒸汽的惰性气体下进行这样的热处理。
[0075]
可以在允许引入氢气或不同气体的任何种类的烘箱中进行步骤(a)。这些烘箱可以分批或连续运行。优选的烘箱是回转窑和流化床反应器。这些反应器可以连续运行。可以在连续的烘箱或窑中或在窑的连续段中施加不同的气体组合物。在后一种情况下,以不可发生反应性气体的互混的方式引入气体。
[0076]
在已经进行步骤(a)之后,将热处理的所述含锂的过渡金属氧化物材料冷却例如至室温或稍微高于室温,例如25至90℃。
[0077]
在本发明的一种实施方式中,在步骤(b)之前进行步骤(b1),所述步骤(b1)包括通过干式固-固分离方法去除例如碳或有机聚合物。这样的干式固-固分离方法的实例是电分选、筛分、磁分离或其他分类方法。在此引入步骤(b1)作为额外步骤。如上文所提及的,干式固-固分离可以足以从在步骤(a)中获得的固体残留物中分离出含ni的固体材料。在这种情况下,将步骤(b)和(c)的顺序颠倒,将在水性处理之后获得的含ni的固体残留物直接浸出以提取ni以及如果适用的话其他过渡金属。
[0078]
本发明方法的步骤(b)包括用能够选择性溶解在步骤(a)中形成的li组分而不溶解热处理的材料中包含的过渡金属的水性介质处理所述热处理的含锂的过渡金属氧化物材料(步骤(a)中获得的材料或步骤(b1)的相应部分)。这种处理可以在环境温度或更高温度例如在20至150℃之间的范围内进行。当使用高于水的沸点的温度时,在升高的压力下进行处理。
[0079]
在本发明的一种实施方式中,所使用的水性介质包含弱酸例如碳酸(其通过在大气压或更高压力下将二氧化碳溶解在水中而获得)、甲酸、乙酸或亚硫酸。这些酸以在水中为0.1至10w%的浓度,优选为1至10w%的浓度使用。当使用碳酸时,优选的是在10至150巴的二氧化碳压力下使用它。在具体的技术兴趣的实施方式中,步骤(b)的水性介质既不包含弱酸也不包含二氧化碳或碳酸。
[0080]
在本发明的一种实施方式中,步骤(b)中使用的水性介质是水,例如去离子水。在本发明的一种实施方式中,步骤(b)中使用的水性介质是甲酸水溶液。
[0081]
在本发明的一种实施方式中,首先将来自步骤(a)的固体残留物或步骤(b1)中获得的含锂的过渡金属材料部分用水处理,以及在固-液分离例如水处理后的过滤之后如上文描述的用稀释的弱酸二次处理。两种提取物可以分开保存,以分离溶解的不同li物质。
[0082]
在本发明的一种实施方式中,步骤(b)具有的持续时间在20分钟至10小时,优选地1至3小时的范围内。
[0083]
在一种实施方式中,步骤(b)进行至少两次,以达到氢氧化锂或锂盐的最佳回收。在每个处理之间进行固-液分离。所获得的锂盐溶液可以统一或单独处理以回收固体锂盐。在不同溶解度的不同锂盐的情况下,后者可以是有利的。在这种情况下,第一提取物将主要包含高度可溶的锂盐,而连续的提取物将包含较低浓度的难溶盐。
[0084]
在本发明的一种实施方式中,水性介质与在步骤(a)或(b1)中获得的材料的比率为在按重量计1:1至99:1,优选地2:1至9:1的范围内。
[0085]
在本发明的一种实施方式中,从步骤(a)或(b1)获得的材料在步骤(b)之前被研磨,以在这些材料例如通过残留的粘合剂聚合物以某种方式团聚的情况下彼此解聚不同的固体颗粒。这样的研磨优选地在球磨机或搅拌式球磨机中进行。研磨可以在干式或湿式条件下进行。优选地,研磨也在连续步骤(b)中使用的水性介质中进行。
[0086]
如果适用的话,在步骤(b)结束时可以释放压力。获得包含lioh、lihco3和/或li2co3或在步骤(b)中使用的酸的li盐的水性溶液。
[0087]
固体残留物包含在水性溶液中,形成悬浮液。在如上文描述的两个或更多个步骤中提取一种或多种li化合物的情况下,固体残留物将分别包含在第二或最后步骤的浆料中。
[0088]
在本发明的优选实施方式中,通过固-液分离步骤回收分散在li盐溶液中的从步骤(b)获得的固体残留物。这可以是过滤或离心,或是沉降和倾析的种类。为了回收这样的固体材料细颗粒,例如平均直径为50μm或更小,可以添加絮凝剂,例如聚丙烯酸酯。通过固-液分离获得的固体残留物分散在水中。
[0089]
然后根据步骤(c)处理分散在水性介质中,例如分散在如上文描述的li盐溶液或水中的固体残留物。通过进行步骤(c),镍和如果适用的话co被回收为含镍(以及如果适用的话钴)的固体。
[0090]
本发明的步骤(c)包括固-固分离步骤。在优选实施方式中,它是湿式固-固分离步骤。这种固-固分离步骤用于从含锂的过渡金属氧化物材料的金属或金属氧化物组分中分离出不溶性组分,如碳和聚合物或不溶性无机组分,例如金属颗粒或金属氧化物颗粒。在步骤(c)的固-固分离之后,获得了固体浓缩物部分,其包含大部分的ni和如果适用的话富集形式的co。可以通过机械、柱或气动或混合浮选进行这样的固-固分离步骤。在许多实施方式中,将捕收剂化合物添加到浆料中,其使目标组分疏水。用于碳和聚合物颗粒的典型捕收剂化合物是烃或脂肪醇,其以1g至50kg/t的热处理的来自步骤(a)的含锂的过渡金属氧化物材料的量引入。也可以相反地进行浮选,即通过具体的捕收剂物质,例如脂肪醇硫酸盐或酯基季铵盐,将最初的亲水性组分转化为强疏水性组分。优选的是使用烃捕收剂例如矿物油、煤油或柴油的直接浮选。为了提高浮选对碳和聚合物颗粒的选择性,可以添加抑制剂,这减少泡沫相中夹带的金属和金属氧化物组分的量。可以使用的试剂可以是用于控制在3至9的范围内的ph值的酸或碱。也可以是吸附在金属或金属氧化物表面上的离子组分,例如硅酸钠或双极性组分,如例如氨基酸。为了提高浮选效率,添加与疏水性目标颗粒例如聚合物颗粒、碳质颗粒例如石墨或煤形成团粒的载体颗粒可以是有利的。通过使用磁性载体颗粒,可以形成可以磁性分离的磁性团粒。在目标组分是顺磁性、亚铁磁性或铁磁性的情况下,也可以通过使用高强度磁性分离器(“whims”)、中强度磁性分离器(“mims”)或低强度磁性分离器(“lims”)的磁分离来分离这些组分。其他固-固分离技术利用了固体成分的密度
差,例如石墨与金属或金属氧化物之间的密度差。这些技术包括使用密度介于将要分离的固体组分的密度之间的流体的浮沉法。另一种此类技术是重介质分离。基于密度差的另外的分离技术是螺旋分选机和水力旋流器。
[0091]
同样,可以使用前文所述的固-固分离技术的至少两种的组合。
[0092]
在一种优选实施方式中,步骤(c)中的固-固分离是磁分离。
[0093]
在本发明的一种实施方式中,从步骤(b)获得的材料在步骤(c)之前被研磨,以在这些材料例如通过残留的粘合剂聚合物以某种方式团聚的情况下彼此释放不同的固体颗粒。这样的研磨优选地在球磨机或搅拌式球磨机中进行。
[0094]
在本发明的一种实施方式中,步骤(c)是使用水性介质,优选地水作为流体的湿式固-固分离。流体介质与在步骤(b)中获得的固体材料的比率在按重量计1:1至99:1,优选地2:1至9:1的范围内。
[0095]
从步骤(c)的湿式固-固分离,得到两种浆料,一种包含含目标过渡金属的固体材料,以及一种包含其他组分,如碳质材料和聚合物以及如果适用的话还一些无机化合物。通过合适的选择以及必要时固-固分离步骤的组合,获得至少60%的ni并将其浓缩成一种部分。优选地,至少80至99%的ni被分离。
[0096]
在本发明的一种实施方式中,进料到步骤(c)的浆料的液相包含溶解的锂。在这种情况下,使从步骤(c)中的固-固分离中获得的一种或另一种或两种浆料经受固-液分离,以回收锂溶液。然后在步骤(d)中进一步处理锂溶液。
[0097]
在步骤(d)中,对从前述任何一个步骤获得的包含锂的溶液进行处理,以回收作为呈固体材料形式的氢氧化物或盐的锂。
[0098]
在本发明的一种实施方式中,通过蒸发溶液中包含的水来回收li盐或lioh。有利的是,通过添加化学计量的量的lioh或li2co3或通过添加氨来中和残留的酸。
[0099]
在本发明的一种实施方式中,通过添加碳酸钠或碳酸铵,或通过优选地在压力下通过溶解二氧化碳而形成的碳酸作为碳酸li的通过沉淀从li盐溶液中回收li。
[0100]
在本发明的优选实施方式中,li被回收为lioh。
[0101]
可以通过溶解和重结晶进一步纯化获得的固体li盐和/或lioh,如本领域中已知的。
[0102]
使从步骤(c)获得的固体ni-浓缩物经受步骤(e),允许提取ni-浓缩物中所含的ni和如果适用的话co以及如果适用的话其他有价值的金属,诸如锂。为了提取,可以应用熔炉或酸或碳酸铵。
[0103]
在本发明的一种实施方式中,这样的步骤(e)可以是通过将步骤(c)中获得的固体ni-浓缩物原样熔炼或作为共进料在专用于来自采矿生产的ni-浓缩物的熔炉中火法冶金的。
[0104]
在步骤(e)的过程中,过渡金属材料用浸出剂处理,该浸出剂优选地为选自以下的酸:硫酸、盐酸、硝酸、甲磺酸、草酸和柠檬酸或前述的至少两种的组合,例如硝酸和盐酸的组合。在另一种优选形式中,浸出剂是
[0105]
--
无机酸,诸如硫酸、盐酸、硝酸,
[0106]
--
有机酸,诸如甲磺酸、草酸、柠檬酸、天冬氨酸、苹果酸、抗坏血酸或甘氨酸,
[0107]
--
碱,诸如氨,胺、氨、碳酸铵的水性溶液或者氨与二氧化碳的混合物,或
[0108]
--
螯合剂,诸如edta或二甲基乙二肟。
[0109]
在一种形式中,浸出剂包括酸水溶液,诸如无机或有机酸水溶液。在另一种形式中,浸出剂包括碱,优选地氨或胺。在另一种形式中,浸出剂包括络合物形成剂,优选地螯合剂。在另一种形式中,浸出剂包括无机酸、有机酸、碱或螯合剂。
[0110]
浸出剂的浓度可以在宽范围内,例如按重量计0.1至98%,以及优选地在10与80%之间的范围内变化。酸水溶液的优选实例是硫酸水溶液,例如浓度为在按重量计10至98%的范围内。优选地,酸水溶液具有的ph值在-1至2的范围内。调节酸的量以维持过量的酸(相对于过渡金属)。优选地,在步骤(e)结束时,所得溶液的ph值在-0.5至2.5的范围内。作为浸出剂的碱的优选实例是nh3与金属(ni,co)的摩尔比率为1:1至6:1,优选地2:1至4:1的氨水,优选地也在碳酸根或硫酸根离子存在下。合适的螯合剂如edta或二甲基乙二肟通常以1:1至3:1的摩尔比率施加。
[0111]
可以在氧化剂存在下进行浸出。优选的氧化剂是作为纯气体或呈与惰性气体例如氮气的混合物或作为空气的氧气。其他氧化剂是氧化性酸,例如硝酸。
[0112]
在本发明的一种实施方式中,这样的步骤(e)可以通过将在步骤(c)中获得的固体ni-浓缩物溶解在选自以下的酸中来进行:硫酸、盐酸、硝酸、甲磺酸、草酸和柠檬酸。
[0113]
在本发明的一种实施方式中,这样的步骤(e)可以通过用碳酸铵或碳酸氢铵的水性溶液处理在步骤(c)中获得的固体ni-浓缩物来进行。这样的水性溶液可以包含额外的氨。
[0114]
在本发明的一种实施方式中,在步骤(e)中用选自以下的酸处理从步骤(c)获得的ni-浓缩物:硫酸、盐酸、硝酸、甲磺酸、草酸和柠檬酸或前述的至少两种的组合,例如硝酸和盐酸的组合。在酸水溶液的情况下,酸的浓度可以在宽范围内,例如按重量计0.1至99%,优选地在10与96%之间的范围内变化。调节酸的量以维持过量的酸。优选地,在步骤(e)结束时,所得溶液的ph值在-0.5至2的范围内。
[0115]
酸水溶液的优选实例是硫酸水溶液,例如浓度为在按重量计10至98%的范围内。
[0116]
按照步骤(e)的处理可以在20至200℃,尤其20至130℃的范围内的温度下进行。如果需要高于100℃的温度,则在高于1巴的压力下进行步骤(e)。否则,常压是优选的。在本发明的上下文中,常压意指1atm或1013毫巴。“正常条件”意指常压和20℃。
[0117]
在本发明的一种实施方式中,在被保护免受强酸的容器,例如富钼和铜的钢合金、基于镍的合金、双相不锈钢或衬玻璃或搪瓷或钛涂覆的钢中进行步骤(e)。另外的实例是得自耐酸聚合物,例如聚乙烯,诸如hdpe和uhmpe、氟化聚乙烯、全氟烷氧基烷烃(“pfa”)、聚四氟乙烯(“ptfe”)、pvdf和fep的聚合物衬里和聚合物容器。fep代表氟化的乙烯丙烯聚合物(四氟乙烯和六氟丙烯的共聚物)。
[0118]
可以将步骤(e)中获得的浆料搅拌、搅动或经受研磨处理,例如在球磨机或搅拌式球磨机中。这样的研磨处理通常导致水或酸更好地进入微粒过渡金属材料。
[0119]
在本发明的一种实施方式中,步骤(e)具有的持续时间在10分钟至10小时,优选地1至3小时的范围内。例如,步骤(e)中的反应混合物以至少0.1w/l的功率搅拌或通过泵送循环以实现良好的混合并避免不溶组分的沉降。通过使用挡板可以进一步改善剪切。所有这些剪切装置都需要施加足够的耐腐蚀性,并且可以由与对于容器本身所描述的类似的材料和涂层产生。
[0120]
步骤(e)可以在空气气氛下或在用n2稀释的空气下进行。尽管,优选的是在惰性气氛例如氮气或稀有气体诸如ar下进行步骤(e)。
[0121]
根据步骤(e)的处理导致源于阴极活性材料的金属化合物的溶解,例如包括除碳和有机聚合物以外的杂质的所述ncm或nca的溶解。在大多数实施方式中,在进行步骤(e)之后获得浆料。残留的锂和过渡金属,诸如但不限于镍、钴、铜和如果适用的话锰,在浸出时通常呈溶解的形式,例如呈其盐的形式。
[0122]
在本发明的一种实施方式中,在还原剂存在下进行步骤(e)。还原剂的实例是有机还原剂,诸如甲醇、乙醇、糖、抗坏血酸、脲、含有淀粉或纤维素的生物基材料,以及无机还原剂,诸如肼及其盐诸如硫酸盐和过氧化氢。用于步骤(e)的优选的还原剂是不留下基于除镍、钴或锰以外的金属的杂质的那些还原剂。步骤(e)中还原剂的优选实例是甲醇和过氧化氢。借助于还原剂,例如可以将co
3+
还原为co
2+
或将mn(+iv)或mn
3+
还原为mn
2+
。
[0123]
在本发明的优选实施方式中,相对于co以及如果适用的话mn的量,使用过量的还原剂。在存在mn的情况下,这种过量是有利的。
[0124]
在本发明的优选实施方式中,相对于co
3+
的量,使用过量的还原剂。
[0125]
在本发明的一种实施方式中,提取介质,例如酸溶液和如果适用的话还原剂,与在步骤(c)中获得的ni-浓缩物的比率为在按重量计1:1至99:1,优选地2:1至9:1的范围内。
[0126]
在其中步骤(e)中已经使用所谓的氧化性酸的实施方式中,优选的是添加还原剂以去除未使用的氧化剂。氧化性酸的实例是硝酸以及硝酸与盐酸的组合。在本发明的上下文中,盐酸、硫酸和甲磺酸是非氧化性酸的优选的实例。
[0127]
根据所使用的酸的浓度,在步骤(e)中获得的浸出物可以具有的过渡金属浓度在按重量计1至20%,优选地按重量计3至15%的范围内。
[0128]
在一种实施方式中,在惰性气体如氮气或氩气下进行步骤(e)。
[0129]
在本发明的一种实施方式中,从步骤(c)获得的ni浓缩物在步骤(e)之前被研磨,以在这些ni浓缩物例如通过残留的粘合剂聚合物以某种方式团聚的情况下彼此释放不同的固体颗粒。这样的研磨优选地在球磨机或搅拌式球磨机中进行。
[0130]
根据步骤(e)中使用的酸水溶液的浓度和量,在步骤(e)中获得的液相可以具有的过渡金属浓度在按重量计1至25%,优选地按重量计6至15%的范围内。过渡金属浓度取决于所使用的酸的相应盐的溶解度。优选地,进行步骤(e)使得主要金属诸如ni以及任选地co和mn的过渡金属浓度略低于最不可溶的盐的溶解度极限,以确保溶液中的高金属浓度。
[0131]
可以在步骤(e)之后进行的任选的步骤是去除不溶解的固体,例如碳质材料和由电池外壳产生的聚合物。所述步骤可以通过添加或不添加絮凝剂的过滤离心或沉降和倾析来进行。所获得的固体残留物可以用水洗涤并且可以被进一步处理以便例如通过如上文描述的固-固分离方法分离碳质和聚合物组分。
[0132]
在本发明的一种实施方式中,步骤(e)和不溶解的固体的去除以连续操作模式顺序进行。
[0133]
在连续的步骤(e1)中溶解了步骤(e)中的ni-浓缩物,可以将上述浆料或溶液的ph值调节至2.5至8,优选地5.5至7.5以及甚至更优选地6至7。ph值可以通过常规手段,例如通过电位滴定法确定,并且是指在20℃下连续液相的ph值。通过用水稀释或通过添加碱或通过其组合来进行ph值的调节。合适的碱的实例是氨和碱金属氢氧化物,例如lioh、naoh或
koh,呈固体形式,例如作为粒料,或优选地作为水性溶液。前述的至少两种的组合也是可行的,例如氨和苛性钠水溶液的组合。
[0134]
优选地,任选的步骤(e2)包括去除在任选的步骤(e1)中形成的al、cu、fe、zr、zn、zn、前述的至少两种的组合的碳酸盐、氧化物、磷酸盐、氢氧化物或羟基氧化物的沉淀物。所述沉淀物可以在调节ph值期间形成。磷酸盐可以是化学计量的或碱性的磷酸盐。不希望受到任何理论的束缚,在通过在步骤(a)期间形成的六氟磷酸盐或其分解产物的水解而形成磷酸盐之际,可以生成磷酸盐。可以通过过滤或借助于离心机或通过沉降去除所述沉淀物。优选的过滤器是带式过滤机、板框压滤机、吸滤器和错流过滤器。可以添加助滤剂和/或絮凝剂以改善固-液分离。
[0135]
在本发明的优选实施方式中,步骤(e2)包括任选的步骤(e3)。步骤(e3)包括用金属镍、金属钴或金属锰或前述的至少两种的任何组合处理在步骤(e1)或步骤(e2)之后获得的溶液。
[0136]
在任选的步骤(e3)中,将在步骤(e2)之后获得的溶液与金属镍、钴或锰或前述的至少两种的组合例如在柱中接触。在这样的实施方式中,有利的是提供填充有呈块或颗粒形式的金属镍、金属钴或金属锰或前述的至少两种的组合的柱,例如作为固定床,并允许溶液流以流过这样的柱。
[0137]
在本发明的一种实施方式中,在常压下进行步骤(e3)。
[0138]
在本发明的一种实施方式中,步骤(e3)具有的持续时间在30分钟至5小时的范围内。如果在柱中进行步骤(e1),则持续时间对应于平均停留时间。
[0139]
在本发明的一种实施方式中,在ph值范围为1至6,优选地ph 2至5下进行步骤(e3)。步骤(e1)中的ph值越低,则在氢气形成下溶解的选自ni、co和mn的金属的量越高。
[0140]
步骤(e3)对于去除铜痕量特别有用。通过进行步骤(e3),没有将需要额外的纯化步骤的新杂质引入到过渡金属的溶液中。即使所述金属镍、钴或锰包含痕量铜,它们也不会溶解。
[0141]
任选的步骤(f)包括过渡金属作为混合的氢氧化物或混合的碳酸盐,优选地作为混合的氢氧化物的沉淀。
[0142]
在本发明的优选实施方式中,通过添加氨或有机胺诸如二甲胺或二乙胺,优选地氨和至少一种无机碱诸如氢氧化锂、氢氧化钠、氢氧化钾、碳酸钠、碳酸氢钠、碳酸钾或碳酸氢钾或前述的至少两种的组合来进行步骤(f)。优选的是添加氨和氢氧化钠。
[0143]
在本发明的一种实施方式中,在10至85℃的范围内的温度下进行步骤(f),优选的是20至50℃。在本发明的一种实施方式中,有机胺或氨的浓度是在0.05至1mol/l,优选地0.1至0.7mol/l的范围内。在该上下文中,术语“氨浓度”包括氨和铵的浓度。给予特别优选的是ni
2+
和co
2+
在母液中的溶解度各自不大于1000ppm,更优选地各自不大于500ppm的氨量。
[0144]
在本发明的一种实施方式中,在本发明方法的步骤(f)期间混合是受影响的,例如用搅拌器、转子定子混合器或球磨机。优选给出的是将至少1w/l,优选地至少3w/l以及更优选地至少5w/l的搅拌器输出引入到反应混合物中。在本发明的一种实施方式中,可以将不大于25w/l的搅拌器输出引入到反应混合物中。
[0145]
可以在一种或多种还原剂存在或不存在下进行本发明方法的任选步骤(f)。合适
的还原剂的实例是肼、伯醇,诸如但不限于甲醇或乙醇,此外抗坏血酸、葡萄糖和碱金属亚硫酸盐。优选的是在步骤(f)中不使用任何还原剂。在其中过渡金属氧化物材料中存在大量锰,例如,相对于相应的阴极活性材料的过渡金属部分,至少3mol-%的情况下,还原剂或惰性气氛的使用或两者结合使用是优选的。
[0146]
可以在惰性气体如氮气或氩气或二氧化碳的气氛下进行本发明方法的步骤(f)。
[0147]
在本发明的一种实施方式中,在9至13.5的范围内的ph值下进行步骤(f),在氢氧化物的情况下,优选的是ph值为11至12.5,以及在碳酸盐的情况下,ph值在7.5至8.5的范围内。ph值是指在23℃下测定的母液中的ph值。
[0148]
可以在分批反应器中,或优选地连续地,例如在连续搅拌釜式反应器中,或在两个或更多个级联,例如两个或三个连续搅拌釜式反应器中进行步骤(f)。
[0149]
可以在空气下、在惰性气体气氛下,例如在稀有气体或氮气气氛下,或在还原性气氛下进行本发明方法的步骤(f)。还原性气体的实例是例如so2。优选给出的是在惰性气体气氛下,特别是在氮气下进行。
[0150]
出于进一步纯化的目的,可以将在步骤(f)中回收的固体溶解在酸,例如盐酸,或更优选地硫酸中。
[0151]
通过进行本发明的方法,可以从包含镍和钴以及如果适用的话的还有锰的阴极材料中回收过渡金属镍和钴以及如果适用的话的锰,其形式为它们可以非常容易地转化为阴极活性材料。特别地,本发明的方法允许回收包含仅可容忍的痕量杂质诸如铜、铁和锌,例如具有小于10ppm的铜(优选地甚至更少,例如1至5ppm)的过渡金属,诸如镍和钴,以及任选地锰。
[0152]
在本发明的一种实施方式中,将在步骤(c)中获得的固体ni-浓缩物用在水性溶液中浓度为0.2至30wt%,优选地按重量计1至20%的碳酸(氢)铵处理。可以将浆料加热到30至150℃的温度。在高于混合物的沸点的温度下,在压力下进行加热。在沸点以下,施加压力有利于在系统中维持足够的氨和二氧化碳。
[0153]
可以在惰性气氛下或在氧气存在下,例如在空气下进行用碳酸(氢)铵的处理。浸出或溶液还可以包含额外的氨和/或过氧化氢。
[0154]
通过碳酸(氢)铵处理,ni和如果适用的话co和cu将作为铵络合物溶解。浸出液中金属铵络合物的浓度可以在按金属计0.2至30wt%,优选地1-15wt%的范围内。使通过该处理获得的溶液经受固-液分离,得到主要包含ni和如果适用的话co和cu铵络合物的溶液以及分开的主要包含其他过渡金属如果适用的话即mn和fe的固体残留物。
[0155]
可以加热获得的溶液,并且可以通过用二氧化碳吹扫来去除氨。通过这第一碳酸ni以及经过较长的处理,有利地在升高的温度下,也将获得作为沉淀物的碳酸co。这允许两种金属分离。在本发明的一种实施方式中,ni和co碳酸盐不彼此分离。从母液中分离出沉淀的混合的ni/co碳酸盐并且可以将其通过硫酸或其他酸溶解,得到相应的ni和如果适用的话co盐的溶液。该溶液还可以包含少量的cu盐,如上所述,这些铜盐可以通过用金属ni、co或mn进行处理而去除。同样如上文描述的,可以通过在2.5至8之间的ph值下的氢氧化物或碳酸盐沉淀来去除可以低浓度包含的其他杂质如fe或al。
[0156]
可以从纯化的ni和如果适用的话co盐溶液中共沉淀出ni和co氢氧化物。
[0157]
在本发明的一种实施方式中,将溶液进一步处理以例如通过溶剂提取方法分别提
取ni和co盐。可以经由本领域已知的电化学方法从分离的ni和co盐中回收纯金属。
[0158]
通过工作实施例进一步说明本发明。
[0159]
通过使用icp-oes(电感耦合等离子体-发射光谱法)或icp-ms(电感耦合等离子体-质谱法)的元素分析确定金属杂质和磷。燃烧后,用热导检测器(cmd)测定总碳。用离子敏感电极(ise)检测燃烧后的总氟或h3po4蒸馏后的离子氟根的氟。用粉末x射线衍射法(pxrd)测定固体的相组成。
[0160]
nl:正常的升,在正常条件下(1atm,20℃)下的升。
[0161]
除非另有特别定义,否则百分数是指按重量计%。表述按重量计%和wt%可以互换使用。无论在何处提及,术语“室温”和“环境温度”表示在约18与25℃之间的温度。
[0162]
实施例1:
[0163]
步骤(a.1)在h2存在下的热处理
[0164]
将量为60g的包含以下的机械处理的电池废料:
[0165]
32.8g的以类似的摩尔量包含镍、钴和锰的废阴极活性材料,
[0166]
17.5g的呈石墨和烟灰和残留电解质形式的有机碳,以及
[0167]
9.7g的另外的杂质,包括al(0.6g)、cu(0.5g)、f(总共:2.2g)、fe(0.55g)、p(0.3g)、zn(0.04g)、zr(0.15g)、mg(2mg)、ca(6mg)
[0168]
置于管式炉中的石墨坩埚中,并将其在氩气流动(20nl/h)下在45分钟过程中加热至400℃。在氩气中10wt%氢气的流动(22nl/h)下,将温度保持恒定持续7.5小时直到停止氢气流动,以及在氩气流动下使炉冷却至环境温度。从坩埚中回收50.1g的热处理的材料,示出ni/co合金、石墨和lioh的xrd信号。
[0169]
步骤(b.1)在步骤(a.1)中获得的产物的水性处理
[0170]
将5.5g的在步骤(a.1)中获得的材料在53ml去离子水中制成浆料,并在环境温度下搅拌30min,并然后过滤。发现澄清的滤液包含133mg li
+
、212mg氢氧根阴离子、93mg碳酸根离子和13mg氟根离子。这对应于其中65%的锂作为lioh存在时的锂浸出效率为46%。
[0171]
步骤(c.1)用于从步骤(b.1)的固体残留物中去除ni的固-固分离
[0172]
将量为12g的从步骤(a.1)获得的氢气处理的材料在100ml去离子水中制成浆料,并在超声发生器(sonotrode)的辅助下用桨式搅拌器在800rpm下分散10分钟。将浆料引入到来自艺利磁铁欧洲有限公司(eriez magnetics europe ltd)的实验室规模的l系列4型高强度湿式磁选机中。将钢丝绒放在罐中的分离器的极之间。将进料浆料在5min内泵送到基质中,同时使基质保持1特斯拉磁化。用去离子水冲洗附着的固体,直到从出口获得澄清且无色的溶液,以充分回收非磁性部分。去除电场后,通过再次用去离子水冲洗从罐中去除磁性部分。将两种回收的浆料过滤并在烘箱中干燥,得到9.0g的磁性部分和1.25g的非磁性部分。非磁性部分包含86wt%的碳和小于0.2wt%的无机和有机氟。磁性部分中的ni、co和mn金属含量为52wt%。
[0173]
步骤(d.1):从在步骤(b.1)中获得的溶液中回收li盐
[0174]
在减压下,将在步骤(b)中获得的包含总量为79mg锂离子的31.5g的澄清滤液浓缩至干。用干燥的氮气再填充烧瓶,并将其转移到充满氩气的手套箱中。回收了215mg的固体材料,示出主要lioh以及痕量的li2co3的x射线衍射信号。
[0175]
步骤(e.1):从在步骤(c.1)中获得的固体ni-浓缩物中酸性提取ni和co
[0176]
在搅拌的250ml分批反应器中,将3.0g的从步骤(c.1)获得的作为磁性部分的材料悬浮在50g的去离子水中,并加热至40℃。缓慢添加33.4g h2so4(96%h2so4)在20.0g去离子水中的混合物,紧接着添加3.62g h2so4(96%h2so4)、1.2g过氧化氢水溶液(30%h2o2)在3.47g去离子水中的混合物。观察到缓慢的气体逸出,只有少量泡沫形成。将所得浆料在60℃下搅拌3小时,并然后冷却至环境温度。用玻璃料过滤所得混合物,并用62.2g去离子水洗涤固体残留物。回收111.4g的红色澄清滤液,其包含535mg ni、535mg co、423mg mn,对应于各自ni、co和mn的浸出效率均大于95%。
[0177]
替代步骤(e.1):从在步骤(c.1)中获得的固体ni-浓缩物中氨提取ni和co
[0178]
在搅拌的250ml分批反应器中,将3.0g的从步骤(c.1)获得的作为磁性部分的材料悬浮在117g的25%的氨水性溶液和20g的碳酸铵以及9g的去离子水的混合物中,在搅拌下加热至60℃。在搅拌下在5h的时间段内添加40.1g的过氧化氢水溶液(30%h2o2)。反应随着气体逸出而放热。将所得浆料在60℃下搅拌3小时,并然后冷却至环境温度。用玻璃料过滤所得混合物,并用60.3g的去离子水洗涤固体残留物。回收204.7g的深色澄清合并滤液,其包含534mg ni、520mg co、2mg mn,分别对应于ni和co的浸出效率为95%和94%,而mn的浸出效率为仅0.5%。在其中mn可能干扰随后的分离步骤的情况下,这样的氨浸出方法可以是有利的。
[0179]
实施例2:步骤(a.1)在h2存在下的热处理
[0180]
将量为20g的包含以下的机械处理的电池废料:55wt.-%的以类似的摩尔量包含镍、钴和锰的废阴极活性材料,29wt.-%的呈石墨和烟灰和残留电解质形式的有机碳,以及16wt.-%的另外的杂质,包括al(1wt.-%)、cu(0.8wt.-%)、f(总共:3.7wt.-%)、fe(0.9wt.-%)、p(0.5wt.-%)、zn(0.07wt.-%)、zr(0.3wt.-%)、mg(<0.01wt.-%)、ca(0.01wt.-%)置于旋转炉中,并将其在氩气的流动(20nl/h)下在45分钟过程中分别加热至400、410、420、430、450、470、500℃。在各自温度下,在氢气的流动(100%,20nl/h)下,将温度保持恒定持续另外45min。之后,停止氢气的流动,并在氩气的流动下使炉冷却至环境温度。从烘箱中回收热处理的材料,示出ni/co合金、石墨和lioh的xrd信号。在每个加热实验之后确定加热的材料中的li的量。
[0181]
步骤(b.1)在步骤(a.1)中获得的产物的水性处理
[0182]
将5g的在步骤(a.1)中获得的材料在50ml去离子水中制成浆料,并在环境温度下搅拌30min,并然后过滤。发现澄清的滤液包含以下列出的浓度的锂、氢氧化物、碳酸盐和氟化物(表1)。
[0183]
表1:在h2下热处理期间的实验条件以及浸出滤液的分析。
[0184][0185]
与实施例1类似,进行步骤(c1)、(d1)和(e1)。
[0186]
实施例3:步骤(a.1)在h2存在下的热处理
[0187]
将量为20g的包含以下的机械处理的电池废料:55wt.-%的以类似的摩尔量包含镍、钴和锰的废阴极活性材料,29wt.-%的呈石墨和烟灰和残留电解质形式的有机碳,以及16wt.-%的另外的杂质,包括al(1wt.-%)、cu(0.8wt.-%)、f(总共:3.7wt.-%)、fe(0.9wt.-%)、p(0.5wt.-%)、zn(0.07wt.-%)、zr(0.3wt.-%)、mg(<0.01wt.-%)、ca(0.01wt.-%)置于旋转炉中,并将其在氩气的流动(20nl/h)下在45分钟过程中加热至400℃。如表2所示,在氢气的流动(100%,20nl/h)下,将温度保持恒定持续15、30、45、60、150或450min。之后,停止氢气的流动,并在氩气的流动下使炉冷却至环境温度。从烘箱中回收热处理的材料,示出ni/co合金、石墨和lioh的xrd信号。在每个加热实验之后确定加热的材料中的li的量。
[0188]
步骤(b.1)在步骤(a.1)中获得的产物的水性处理
[0189]
将5g的在步骤(a.1)中获得的材料在50ml去离子水中制成浆料,并在环境温度下搅拌30min,并然后过滤。发现澄清的滤液包含以下列出的浓度的锂、氢氧化物、碳酸盐和氟化物(表2)。
[0190]
表1:在h2气氛下加热持续时间以及浸出滤液的分析。
[0191][0192]
与实施例1类似,进行步骤(c1)、(d1)和(e1)。
[0193]
实施例4:
[0194]
步骤(a.3)热处理之前的溶剂处理
[0195]
将量为750g的包含以下的机械处理的电池废料:55wt.-%的以类似的摩尔量包含镍、钴和锰的废阴极活性材料,29wt.-%的呈石墨和烟灰和残留电解质形式的有机碳,以及16wt.-%的另外的杂质,包括al(1wt.-%)、cu(0.8wt.-%)、f(总共:3.7wt.-%)、fe(0.9wt.-%)、p(0.5wt.-%)、zn(0.07wt.-%)、zr(0.3wt.-%)、mg(<0.01wt.-%)、ca(0.01wt.-%)与2.5l水混合,在环境温度下搅拌60min,并然后过滤。
[0196]
步骤(a.1)在h2存在下的热处理
[0197]
将在步骤(a.3)中获得的量为20g的材料置于旋转炉中,并将其在氩气的流动(20nl/h)下在45分钟的过程中加热至400℃。在氢气/氩气混合物的流动(20nl/h)下,将温度保持恒定持续数小时;氢气浓度分别为3、5、7、10、14、25、35或100vol-%,如下表3所示。之后,停止氢气的流动,并在氩气的流动下使炉冷却至环境温度。从烘箱中回收热处理的材料,示出ni/co合金、石墨和lioh的xrd信号。在每个加热实验之后确定加热的材料中的li的量。
[0198]
步骤(b.1)在步骤(a.1)中获得的产物的水性处理
[0199]
将5g的在步骤(a.1)中获得的材料在50ml去离子水中制成浆料,并在环境温度下搅拌30min,并然后过滤。发现澄清的滤液包含以下列出的浓度的锂、氢氧化物、碳酸盐和氟化物(表3)。
[0200]
表3:加热期间的h2浓度和浸出滤液的分析。
[0201][0202]
与实施例1类似,进行步骤(c1)、(d1)和(e1)。