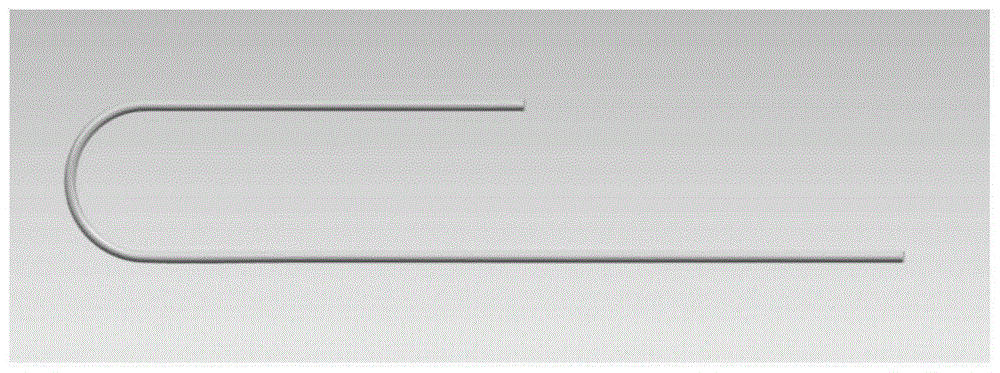
本发明属于金属纤维多孔材料
技术领域:
,更具体地,涉及一种用折弯结构铝合金丝制备的金属纤维多孔材料及其制备方法和应用。
背景技术:
:金属多孔材料是一种兼具结构和功能属性的新型工程材料,主要由金属基体和空气孔隙组成,它既有金属的特性,例如导电性、导热性、可塑性等,又由于孔隙的存在而具有功能特性,例如高比表面积、隔音、隔热、高的渗透性、能量吸收性等,同时,金属多孔材料具有比重小、高比强度等特点,所以其运用范围广泛,涉及航空航天、环保、石化、冶金、机械、建筑等行业。金属多孔材料这些年来飞速发展,很多国家的研究机构都把其作为重点发展的新型材料,提出了很多新的理论和工艺,应用领域不断开阔。金属纤维多孔材料由于制备工艺以及骨架材料的不同,使其具有丰富的结构和功能特性,具有三维网状多孔结构、高精度全连通的孔径、孔隙率高、比表面积大的结构特点,所以与其它多孔材料相比,具有许多优良性能。目前,主要针对于铜、镍、镍铬合金和不锈钢等材料制备成金属纤维多孔材料。6061铝合金由于其镁、硅合金特性多,具有加工性能极佳、优良的焊接特点及电镀性、良好的抗腐蚀性、韧性高及加工后不变形、材料致密无缺陷等优良特点,目前制备铝多孔材料主要采用粉末冶金法和气泡法,这种方式制备出来的铝多孔材料闭孔率高,而且强度较低,对于铝丝制备成铝纤维多孔材料的研究甚少。技术实现要素:为了解决上述现有技术存在的不足和缺点,本发明首要目的在于提供一种用折弯结构铝合金丝制备的金属纤维多孔材料,该金属纤维多孔材料具有所需孔隙率且质量轻、强度高、具有连通孔隙。本发明另一目的在于提供上述用折弯结构铝合金丝制备的金属纤维多孔材料的制备方法。该方法先将铝合金短丝放入特制模具均匀分布中使其聚集在一起,通过施加压力使铝合金短丝之间相互接触,并烧结使丝材之间实现冶金结合,制备获得具有连通孔隙的金属纤维多孔材料。本发明再一目的在于提供上述用折弯结构铝合金丝制备的金属纤维多孔材料的应用。本发明的目的通过下述技术方案来实现:一种用折弯结构铝合金丝制备的金属纤维多孔材料,所述金属纤维多孔材料是将折弯结构铝合金短丝置于特制模具中均匀分布,然后将该特制模具施加压力为0.1~1t后,真空状态下,在540~580℃烧结,降温至100~200℃后,随炉冷却制得;其中,所述特制模具包括压头、底座、外套筒、内衬管和限位垫,所述压头为t型结构,内衬管置于所述外套筒中,所述底座中央有凸部,所述内衬管的管径、底座的凸部和压头的凸杆的直径相同,所述外套筒的顶端设有环形凹槽,所述限位垫为环状,将所述限位垫放置在外套筒的环形凹槽中,所述压头的凸杆通过所述限位垫套于所述内衬管中,通过限位垫调节所得金属纤维多孔材料的高度。优选地,所述金属纤维多孔材料的孔隙率为40~85%。优选地,所述折弯结构铝合金短丝为6061铝合金、4043铝合金、5054铝合金或7075铝合金中的一种以上。更为优选地,所述折弯结构铝合金短丝的直径为0.1~1mm;所述折弯结构金属短丝的短边长度为5~10mm,所述折弯结构铝合金短丝的长边长度为10~15mm;所述折弯结构铝合金短丝的过渡圆弧直径为1~5mm。优选地,所述真空状态的真空度为10-2~10-3pa。优选地,所述烧结的升温速率为8~10℃/min,所述烧结的时间为2~3h。优选地,所述内衬管的管径、底座的凸部与压头的凸杆的直径为20~50mm,所述凸杆长度为50~100mm,所述凸部高度为2~5mm。优选地,所述特制模具的材质为高强度石墨或不锈钢。所述的用折弯结构铝合金丝制备的金属纤维多孔材料的制备方法,包括如下步骤:s1.根据质量体积法计算并称取目标孔隙率的金属纤维多孔材料所对应的折弯结构铝合金短丝的质量;s2.将步骤s1的新型折弯结构铝合金短丝置于特制模具中均匀分布;将该特制模具置于,施加压力为0.1~1t后,高真空状态下,在540~580℃烧结,降温至100~200℃后,随炉冷却,制得金属纤维多孔材料。所述的用折弯结构铝合金丝制备的金属纤维多孔材料在制备轻质刚性减振材料领域中的应用。与现有技术相比,本发明具有以下有益效果:1.本发明将铝合金短丝放入特制模具均匀分布中使其聚集在一起,通过施加压力使铝合金短丝之间相互接触,并烧结使丝材之间实现冶金结合,制备获得具有连通孔隙的金属纤维多孔材料。该金属纤维多孔材料具有所需孔隙率且质量轻、强度高、具有连通孔隙。新型折弯结构铝合金短丝延续了纤维丝高力学强度特性,自然堆积状态下,相互勾结,具有较高连接强度,烧结之后纤维丝之间有多个冶金结合点,冶金结合更加可靠,弥补了铝合金短丝制备成金属纤维多孔材料方面的空白,为制备铝合金纤维多孔材料提供了方法。2.本发明采用特制模具通过可控制限位垫的高度实现对所得金属纤维多孔材料高度的控制,使其能够适应不同的使用要求。通常制造金属纤维多孔材料是将其放入液压机进行压制处理,而随后取出,所得的金属纤维多孔材料由于内部存在很大的内应力,脱离液压机后会产生弹性后效,使得实际孔隙率与所设定孔隙率有一定差距。而本发明优化改善了金属纤维多孔材料的烧结方法,采用特制模具在烧结炉进行液压操作,并且达到设定孔隙率后,特制模具在烧结过程中全程限位,减少了弹性后效的影响,所得金属多孔材料孔隙率与设定孔隙率误差小。本发明减少了材料在液压机上的操作步骤,工艺简单,步骤搭配合理,降低制备成本。3.本发明中由于铝合金短丝具备折弯结构,宏观上相互纠缠的折弯丝之间除了基本的接触连接外,更主要的是以交织连接和搭接为主,因此自然堆积状态下折弯丝比直短丝更容易形成堆垛状态。附图说明图1为本发明折弯结构铝合金丝单体结构的示意图。图2为实施例1-20中所使用的折弯结构铝合金丝单体结构的实物图。图3为本发明的特制模具结构剖面图及其实物图。图4为实施例1-3制得的金属纤维多孔材料的实物图。图5为实施例1制得的金属纤维多孔材料的sem照片。具体实施方式下面结合具体实施例进一步说明本发明的内容,但不应理解为对本发明的限制。若未特别指明,实施例中所用的技术手段为本领域技术人员所熟知的常规手段。除非特别说明,本发明采用的试剂、方法和设备为本
技术领域:
常规试剂、方法和设备。本发明实施例所使用折弯结构铝合金丝的化学成分如表1所示。表1新型折弯结构6061铝合金丝的化学组成成分cumnmgzncrtisifeal含量(%)0.15~0.40.150.8~1.20.250.04~0.350.150.4~0.80.7余量图1为本发明折弯结构铝合金丝单体结构的示意图。图2为实施例1-20中所使用的折弯结构6061铝合金丝单体结构的实物图。从图2中可知,该折弯结构铝合金短丝的直径为0.15mm,短边长度5mm,长边长度10mm,过渡圆弧直径2mm。实施例1本实施例选用的折弯结构6061铝合金短丝(直径为0.15mm,短边长度5mm,长边长度10mm,过渡圆弧直径2mm)制备金属纤维多孔材料,其具体操作步骤如下:(1)根据质量体积法,如公式(1)所示,计算孔隙率为60%所对应的新型折弯结构铝合金短丝质量,称取相应质量的折弯结构铝合金短丝13.8g;将其置于特制模具中均匀分布。p(%)=(1-m/ρv)×100式(1)其中,p表示目标孔隙率,m表示金属纤维多孔材料的质量,ρ表示铝合金的密度,v表示制备出金属纤维多孔材料的体积。其中,特制模具的结构如图3所示,所述特制模具包括压头1、底座2、外套筒3、内衬管4和限位垫5,所述压头1为t型结构,内衬管4置于所述外套筒3中,所述底座2中央有凸部,所述内衬管4的管径、底座2的凸部和压头1的凸杆的直径相同,所述外套筒3的顶端设有环形凹槽,所述限位垫5为环状,将所述限位垫5放置在外套筒3的环形凹槽中,所述压头1的凸杆通过所述限位垫5套于所述内衬管4中,可以通过限位垫5来调节所得金属纤维多孔材料的高度,当压头1向下移至与限位垫5接触时,压头1将被限制下移,通过可控制限位垫的高度实现对所得金属纤维多孔材料高度的控制,使其能够适应不同的使用要求。其中,所述内衬管的管径、底座的凸部与压头的凸杆的直径为20~50mm,所述凸杆长度为50~100mm,所述凸部高度为2~5mm,所述特制模具的材质为高强度石墨或不锈钢。(2)将上述装有铝合金短丝的特制模具置于真空热压烧结炉中,实行液压操作,施加压力值为0.5吨(t),使得特制模具压头1与限位垫5的上表面接触,预制金属纤维多孔材料的体积得到控制,使模具内金属纤维多孔材料的孔隙率控制在60%%,此时铝合金丝之间紧密接触、相互勾结,接触点显著增多;然后实行真空操作,使得炉内工作区真空度达到10-2pa以下,以8℃/min的速率升温至540℃烧结2h,然后随炉冷却,当温度降到200℃以下时取出样品,得到所需孔隙率为60%的金属纤维多孔材料。将本实施例所得金属纤维多孔材料依次进行超声波清洗、干燥处理。图4为实施例1制得的金属纤维多孔材料的sem照片。从图4中可知,金属纤维多孔材料为多孔结构,且可以观察到铝合金短丝之间产生了冶金结合点,冶金结合更加可靠。实施例2与实施例1制备方法相同,区别在于:步骤(1)中所述的折弯结构铝合金短丝的质量为10.4g,得到所需孔隙率为70%的金属纤维多孔材料。实施例3与实施例1制备方法相同,区别在于:步骤(1)中所述的折弯结构铝合金短丝的质量为6.9g,得到所需孔隙率为80%的金属纤维多孔材料。图5为实施例1-3制得的金属纤维多孔材料的实物图。其中,从左至右依次为制备的孔隙率为60%、70%、80%的金属纤维多孔材料。从图5中可知,孔隙率越低,制备出的金属纤维多孔材料越密集。实施例4与实施例1制备方法相同,区别在于:选用的新型折弯结构铝合金短丝的直径为0.15mm,短边长度10mm,长边长度15mm,过渡圆弧直径2mm,制得孔隙率为60%的金属纤维多孔材料。实施例5与实施例2制备方法相同,区别在于:选用的新型折弯结构铝合金短丝的直径为0.15mm,短边长度10mm,长边长度15mm,过渡圆弧直径2mm,制得孔隙率为70%的金属纤维多孔材料。实施例6与实施例3制备方法相同,区别在于:选用的新型折弯结构铝合金短丝的直径为0.15mm,短边长度10mm,长边长度15mm,过渡圆弧直径2mm,制得孔隙率为80%的金属纤维多孔材料。实施例7与实施例1制备方法相同,区别在于:选用的新型折弯结构铝合金短丝的直径为0.2mm,短边长度5mm,长边长度10mm,过渡圆弧直径2mm,制得孔隙率为60%的金属纤维多孔材料。实施例8与实施例2制备方法相同,区别在于:选用的新型折弯结构铝合金短丝的直径为0.2mm,短边长度5mm,长边长度10mm,过渡圆弧直径2mm,制得孔隙率为70%金属纤维多孔材料。实施例9与实施例3制备方法相同,区别在于:选用的新型折弯结构铝合金短丝的直径为0.2mm,短边长度5mm,长边长度10mm,过渡圆弧直径2mm,制得孔隙率为80%金属纤维多孔材料。实施例10与实施例1制备方法相同,区别在于:步骤2中所述烧结温度为560℃,制得孔隙率为60%的金属纤维多孔材料。实施例11与实施例2制备方法相同,区别在于:步骤2中所述烧结温度为560℃,制得孔隙率为70%的金属纤维多孔材料。实施例12与实施例3制备方法相同,区别在于:步骤2中所述烧结温度为560℃,制得孔隙率为80%的金属纤维多孔材料。实施例13与实施例1制备方法相同,区别在于:步骤2中所述烧结温度为580℃,制得孔隙率为60%的金属纤维多孔材料。实施例14与实施例2制备方法相同,区别在于:步骤2中所述烧结温度为580℃,制得孔隙率为70%的金属纤维多孔材料。实施例15与实施例3制备方法相同,区别在于:步骤2中所述烧结温度为580℃,制得孔隙率为80%的金属纤维多孔材料。实施例16与实施例1制备方法相同,区别在于:步骤2中所述烧结保温时间为3h,制得孔隙率为60%的金属纤维多孔材料。实施例17与实施例2制备方法相同,区别在于:步骤2中所述烧结保温时间为3h,制得孔隙率为70%的金属纤维多孔材料。实施例18与实施例3制备方法相同,区别在于:步骤2中所述烧结保温时间为3h,制得孔隙率为80%的金属纤维多孔材料。实施例19与实施例1制备方法相同,区别在于:步骤(1)中选用的新型折弯结构铝合金短丝的直径为0.1mm,短边长度10mm,长边长度15mm,过渡圆弧直径1mm,所述的折弯结构铝合金短丝的质量为20.7g,得到所需孔隙率为40%的金属纤维多孔材料。实施例20与实施例1制备方法相同,区别在于:步骤(1)中选用的新型折弯结构铝合金短丝的直径为1mm,短边长度10mm,长边长度15mm,过渡圆弧直径5mm,所述的折弯结构铝合金短丝的质量为5.2g,得到所需孔隙率为85%的金属纤维多孔材料。本发明实施例所制得的金属纤维多孔材料均具有所需孔隙率且质量轻、强度高、具有连通孔隙。上述实施例中的铝合金也用4043铝合金、5054铝合金或7075铝合金替换。新型折弯结构铝合金短丝延续了纤维丝高力学强度特性,自然堆积状态下,相互勾结,具有较高连接强度,烧结之后纤维丝之间有多个冶金结合点,冶金结合更加可靠。上述实施例为本发明较佳的实施方式,但本发明的实施方式并不受上述实施例的限制,其他的任何未背离本发明的精神实质与原理下所作的改变、修饰、替代、组合和简化,均应为等效的置换方式,都包含在本发明的保护范围之内。当前第1页12