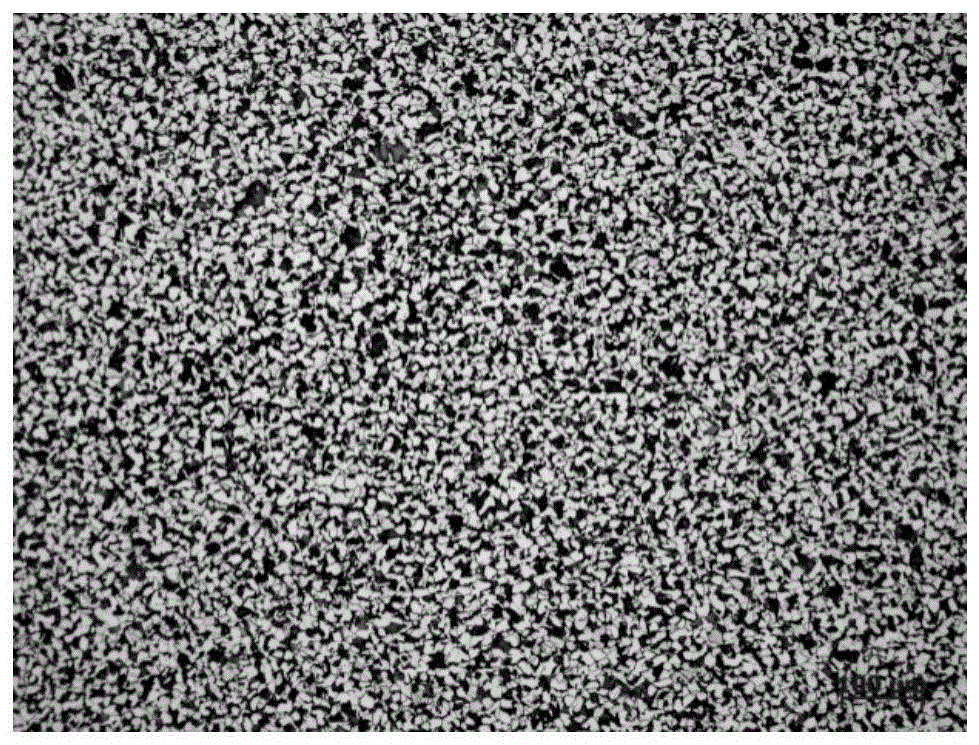
本发明涉及一种可直接冷锻加工的齿轴钢及其制造方法,即涉及一种冷锻加工前免热处理的齿轴钢轧材及其制造方法。
背景技术:
:变速箱在工业上的应用极为广泛,只要有动力变速传递,就会应用到变速箱。以乘用车为例,我国每年生产的乘用车变速箱超过2500万台。变速箱一端通过输入轴输入动力,通过不同模数的齿轮齿合后改变转速,通过输出轴输出动力。输入轴和输出轴都称为齿轴。目前齿轮行业中齿轴或齿轮的成型方式分为热锻、温锻及冷锻。冷锻因为其尺寸精度高、表面质量好,后续加工余量小等诸多优点,成为行业发展趋势。齿轴通常比齿轮锻造比小,所以更适合冷锻加工。众所周知,钢材在加热状态下,特别是奥氏体化后具有优良的塑形,即可锻性好。目前行业锻造成型仍采用热锻方式居多,虽然可锻性良好,但因为要加热而能耗高,且钢材经过加热后脱碳程度加剧,表面脱碳层变厚,影响了表面质量。热锻件的尺寸精度也会降低。相比较而言,热轧钢材直接进行冷锻加工的可塑性就相对较差,为了改善冷加工塑性,热轧钢材通常需要进行软化退火、等温退火、球化退火等热处理。退火热处理后再进行冷锻加工。材料每经一道热处理,就会增加加工周期、提高能耗,也增加生产成本。综上所述,无论是热轧材进行热锻还是先热处理(退火)再进行冷锻,成型加工前都有一道热处理,加工前的热处理会拉长加工周期、降低尺寸精度及增加生产成本。所以,开发一种能够不需要进行热处理(退火)可直接进行冷锻加工的热轧材,用于直接加工齿轴,不仅可以节省热处理工序,而且还能够消除因热处理导致的脱碳层变厚、加工精度变差。为了节省工序、降低能耗、减小脱碳层,开发可直接冷锻加工的钢材是值得期待的。技术实现要素:本发明的目的是提供一种高淬透性(组织均匀、硬度适中)、脱碳层浅(表面质量好)、带状组织级别低、尺寸精度高、具有较好冷锻性的齿轴钢。本发明的齿轴钢的热轧微观结构为铁素体+珠光体,且珠光体片层间距平均为0.14-0.15μm,屈服强度≥600mpa、抗拉强度≥880mpa、延伸率≥25%、面缩率≥50%,淬透性j9mm(淬透性测试中距端部9mm处的硬度)为35~40hrc,钢的延伸率和面缩率较高,塑性强,可直接冷锻加工。钢材强度和硬度区间刚好满足齿轴钢的加工要求。本发明的技术方案为:一种可直接冷锻加工的齿轴钢的制造方法,包括如下步骤(1)冶炼:钢水在lf炉外精炼时白渣保持时间≥25min,lf炉外精炼总时间不小于40min,lf炉外精炼后进行真空脱气,真空保持时间≥30min,lf炉外精炼及真空脱气时进行全程吹氩软搅拌氩气流量不宜过小或过大,过小搅拌效果不佳,多大导致钢水翻腾引起二次氧化产生夹杂物。夹杂物会导致热处理开裂,存在恶性质量事故的风险。冶炼结束后钢水组分质量百分含量为c:0.15~0.45%,si:≤0.35%,mn:0.60~1.40%,p:≤0.030%,s:≤0.030%,cr:0.60~1.40%%,余量为fe及不可避免的杂质元素。(2)浇注:将钢水浇注成钢坯(优选连铸方坯,在连铸时采用末端电磁搅拌、轻压下等工艺手段对铸坯内部质量进行控制),浇注时过热度控制在10~30℃,浇注全程氩气保护避免钢水氧化。(3)轧制:将钢坯再加热使完全奥氏体化,预热段温度控制在750~865℃,第一加热段温度在950~1070℃,第二加热段温度在1000~1200℃,均热段温度在1070~1200℃,总加热时间3小时以上,充分固化。出炉进行高压水除鳞,接着清理热坯表层,清理厚度0.5~4mm,去除坯料表面裂纹、凹坑、脱碳等表面缺陷,确保轧材表面质量,该工序为保证表面质量的关键操作。然后采用14架二辊轧机+5架三辊轧机进行轧制:4架二辊轧机粗轧—6架二辊轧机中轧—4架二辊轧机预精轧—5架三辊轧机精轧,单道次最大压下量控制在20~26mm,轧制过程中进行控冷,依次布置至少四个喷雾水箱进行控冷,中轧后分布1#水箱进行喷雾冷却,预精轧后分布2#及3#水箱进行喷雾冷却,精轧后分布4#水箱进行喷雾冷却,在轧制过程中对钢材进行强弱交替的冷却,其中1#水箱的冷却水相对开启度为40~65%进行强冷,2#、3#水箱的冷却水相对开启度为10~20%进行弱冷,通过1#、2#、3#水箱的冷却,使得坯料进精轧机组的来料温度在780~870℃,精轧终轧温度在770~850℃,使得精轧在单相区轧制,4#水箱的冷却水相对开启度相比2#、3#水箱提高至30~50%,让精轧结束后坯料温度快速达到上冷床的温度要求750~830℃,节省或缩短精轧后坯料上冷床的转移等待时间。另外,材料的终轧温度在770~850℃,此时晶相仍然没有达到转变温度,终轧完成后在上冷床之前通过4#水箱进行较强的轧后水冷,确保上冷床时钢材的温度快速调整到750~830℃,以降低奥氏体转变开始温度,进而降低奥氏体稳定性,后续的组织转变易得到细小均匀的热轧组织,该组织有利于钢材的冷锻加工。上述轧制方式中,2#、3#水箱冷却强度相对1#、4#较弱,其设计目的是确保钢材以预设的温度进入精轧机组,若2#、3#水箱的冷却水过大,一则不利于精确控制精轧机组的开始温度,二则会增大钢材表面和内部的温度差,钢材表面由于受到冷却水的喷淋,表面降温变硬增加轧机负荷,由于精轧机组的轧机负荷能力相对较低,钢材表面温度过低易导致轧机超负荷。进一步设置进精轧机组钢坯温度控制在780~870℃之间,精轧时确保单相区轧制,可有效改善轧材的带状组织及避免混晶的产生。再者,控制进精轧机的温度,对提高钢材的热轧尺寸稳定性起到十分积极的作用,有助于提高钢材的尺寸加工精度。(4)冷却:轧制结束后,坯料在冷床上鼓风冷却,控制上冷床时坯料温度750~830℃,降低奥氏体相变开始温度,进而降低开始冷却前奥氏体的稳定性,控制平均冷速控制在45~70℃/min,采用较高的风冷速度可以缩小珠光体层层间距(使控制在0.14-0.15μm,提高强度和硬度),终冷温度为300~450℃,冷却过程中奥氏体转变为铁素体和珠光体,且较高的冷速可以在转变过程中降低带状组织级别,使带状组织级别≤2级,提高延伸率、面缩率,进一步提升钢材的冷锻性能,终冷之后材料空冷至室温。本发明齿轴钢中各元素的设计依据如下:c:0.15~0.45%。本发明钢种在热轧状态下直接冷锻,锻前为铁素体加珠光体组织,c含量将直接影响材料中珠光体的比例,从而影响材料的强度。珠光体比例过低,材料将缺乏足够的强度,c含量比例过高,强度提高,但会明显降低钢材的冷锻性,为了调和强度和冷锻性。为了确保齿轴在最终热处理后芯部的韧性,c含量也不易过高,采用中低碳设计。本发明中的钢材c含量范围设定为0.15~0.45%。si:≤0.35%。si固溶在铁素体相中,有较强的固溶强化作用,能显著地提高铁素体强度,但同时降低铁素体的塑性和韧性,且si还会促进元素p、s的晶界偏聚,使得晶界发生一定程度的脆化。一般的钢种中,si在炼钢时作为脱氧元素,添加到钢材中。本发明钢种用于一种可直接冷锻加工的齿轴钢,要求材料有较好的冷锻性能,也就是要求钢中铁素体优良的塑性和韧性。且齿轴在最终热处理时若si过高,易产生晶间氧化,恶化齿轴的性能。所以si范围设定为≤0.35%,更优选为≤0.20%。mn:0.60~1.40%。mn作为脱氧剂作用的元素,适量的mn可不明显影响材料塑性的基础上提高钢材强度,添加一定量的mn对确保材料的力学性能非常重要。此外mn将钢中的s等结合形成硫化物,硫化物具有良好的塑性,在切削时发挥切口效应,提高材料切削性能。为充分发挥上述效果,本发明中的钢材mn含量范围设定为0.60~1.40%。p:≤0.030%。p在铸造凝固时会有较严重的微观偏析倾向,随后在加热时在晶界聚集,增加钢材脆性,特别是冷脆性能,且恶化材料的冷锻性。一般的钢材需尽可能地降低p含量,本发明中的钢材p含量范围设定为≤0.030%,更优选为≤0.020%。s:≤0.030%。s是易切削元素。当钢中含有一定量的mn时,易形成mns或者含mns的复合物,从而提高材料切削性能。但硫化物通常熔点较低,s含量过高,材料会发生热脆效应及增加脱碳的倾向。为充分发挥上述效果,本发明中的钢材s含量范围设定为≤0.030%更优选为0.010~0.020%。cr:0.60~1.40%。cr元素增加淬透性,并且细化珠光体的片层间距,有利于提高细片状珠光体组织的形成比例及显微组织的均匀性,从而有效提高材料的强度及疲劳等性能。本发明中的钢材cr含量范围设定为0.60~1.40%。为了满足材料的强度、塑性、淬透性等综合性能,本发明设计的齿轴钢也可添加mo、ni、b等一种或多种合金元素。同时为了防止材料在最终热处理过程中晶粒粗大化,可添加al、ti、nb、v等一种或多种合金元素。本发明为一种较典型的中低碳齿轴钢设计,齿轴通过最终热处理后表面强度、硬度高,耐磨性好,而芯部则要具有较好的韧性,有利于提高减速箱寿命。该钢材设计成分时,si、p等不利于冷锻性的元素要抵控。与现有技术相比,本发明的优点在于:本发明的齿轴钢具有一定的抗拉强度、淬透性波动范围窄,且该钢种经过控轧控冷,轧材脱碳层浅、带状组织级别低,表面质量好、组织均匀、硬度适中,热轧组织为铁素体+珠光体,且珠光体片层间距小,有利于提高钢材塑形,提高冷加工塑形。该轧材可直接进行车铣、滚齿等齿轴的加工,加工前可免去软化退火、等温退火甚至球化退火等热处理。附图说明图1为本发明实施例1齿轴钢的100倍微观结构图;图2为本发明实施例1齿轴钢的500倍微观结构图;图3为本发明实施例1齿轴钢珠光体片层结构照片。具体实施方式以下结合附图实施例对本发明作进一步详细描述,以下实施例是对本申请技术方案中较优试样的举例说明,并不对本发明的技术方案构成限定。实施例1—3按下面工序制造本发明实施例1~3中的可直接冷锻加工的齿轴钢:1)冶炼:100吨炼钢炉冶炼后进行lf炉外精炼,白渣时间25-60min,精炼总时间至少要达到40min,钢液再经vd真空脱气处理,真空下保持30min,精炼和真空脱气过程中采用氩气搅拌钢液,各化学元素质量百分比严格按要求控制。2)连铸:将钢水连铸成240mm×240mm的方坯,控制中间包浇注时的过热度为10~40℃。为控制材料的偏析,连铸时则采用先进的末端电磁搅拌、连铸轻压下先进装备及工艺。所得连铸坯化学成分百分比见下表1所示:表1.(wt.%,余量为fe及其他不可避免的杂质元素)序号csimnpscral10.200.151.100.0070.0160.950.03220.190.200.960.0150.0111.120.02030.220.080.850.0100.0201.200.0153)加热:坯料在步进式加热炉中加热,包括预热段、第一加热段、第二加热段、均热段,其中预热段温度控制在750~865℃,第一加热段温度控制在950~1070℃,第二加热段温度控制在1000~1200℃,均热段温度控制在1070~1200℃,总加热时间3小时以上。4)热轧:开轧温度为970~1100℃,终轧温度为770~850℃,单相区内轧制:采用14架二辊轧机+5架三辊轧机轧制,包括4架粗轧—6架中轧—4架预精轧—5架三辊精轧,单道次最大压下量控制在20~26mm之间。轧制过程中控冷,设置四个水箱进行水雾冷却,包括位于中轧机组后的1#水箱(冷却水开启度分别为40~65%)、位于预精轧机组后的2#、3#水箱(冷却水开启度分别为10~20%)、位于精轧机组后的4#水箱。采用三辊精轧,控制轧材的尺寸精度,确保尺寸精度控制在±0.5d%,d为直径。5)冷却:精轧后钢材通过4#水箱,此时冷却水开启度为30~50%,将坯料快速冷却到上冷床温度750~830℃,上冷床后组织发生转变时继续控制冷却速度,以改善带状组织,冷床采用空步的排钢方式控制鼓风冷却速度,对应的平均冷却速度是45~70℃/min,一直冷却到300~450℃,终冷后材料可自由冷却至室温,所得热轧钢材的金相组织为铁素体+珠光体。上述各实施例中的齿轴钢的制造方法的具体工艺参数如下表2所示:表2.(加热、热轧、冷却的具体工艺参数)对实施例1~3中的可直接冷锻加工的齿轴钢进行相关测试,测得力学性能如下表3表3从表3中可见,实施例中的材料具有较高的强度,淬透性高,j9mm的硬度已经达到35hrc以上,证明均匀性好。另外实施例中齿轴钢试样的延伸率≥25%,面缩率≥50%,说明可塑性高,具备直接冷锻加工的条件。图1、图2展示了实施例1齿轴钢的微观组织。从图可知,该齿轴用钢的微观组织为铁素体+珠光体,图3展示了实施例齿轴钢微观结构中珠光体片间距为0.14μm左右,片层间距极小,强度和硬度很高。尽管以上详细地描述了本发明的优选实施例,但是应该清楚地理解,对于本领域的技术人员来说,本发明可以有各种更改和变化。凡在本发明的精神和原则之内所作的任何修改、等同替换、改进等,均应包含在本发明的保护范围之内。当前第1页12