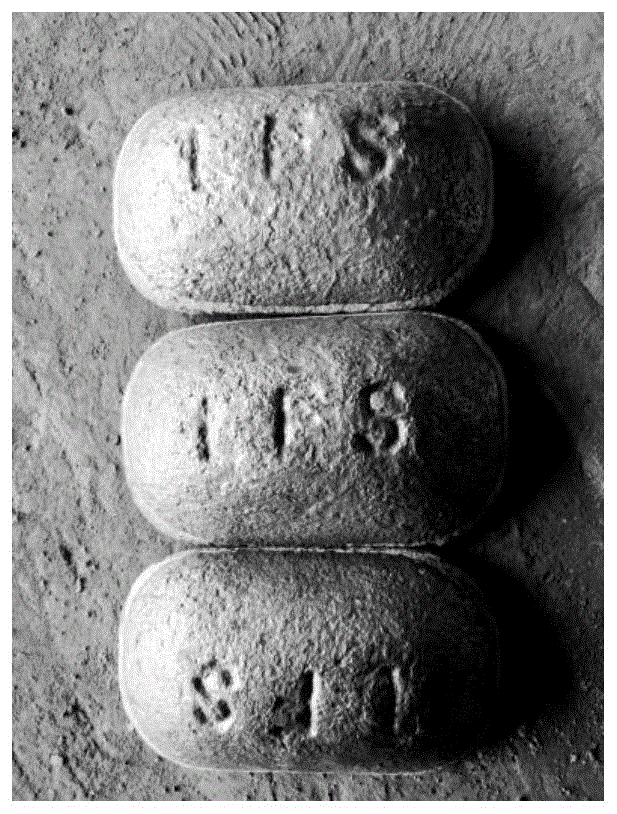
本发明属于黑色金属冶炼
技术领域:
,涉及一种提高铸造用超高纯生铁外观质量的方法。
背景技术:
:铸造业是制造业的基础产业,而铸造用超高纯生铁是高端铸铁件的关键基础材料,铸造用超高纯生铁生产工艺包括(1)精选原料:充分利用优质矿源,精选低p、低ti、低微量元素的铁精矿粉;(2)优化烧结预配:对铁精矿粉和石灰采用自动化预配工艺,实行两配两混,保证铁精矿粉的品位、碱度、tio2、p2o5及石灰的均匀与稳定;(3)铁精矿粉润磨工艺:提高铁精粉的细度与球团矿强度,减少了球团矿中tio2、p2o5的杂质含量;(4)高炉采用低硅冶炼;(5)精炼深度提纯:将高炉低温冶炼的铁液进行精炼深度提纯,“精炼深度提纯”整个装备系统包括铁液运输单元、脱硅单元、喷吹单元、脱磷单元和脱硫单元。脱硅单元、脱磷单元和脱硫单元分别用于去除铁液中的硅、磷、硫等元素,通过喷吹单元向铁液罐中加入反应物料(烧结返矿、钝化石灰粉、钝化镁粒等)并通入氧气、氮气,使反应物料与铁液均匀接触,使铁液中的有害元素及微量元素去除得更加彻底,达到铸造用超高纯生铁化学成分要求。因在精炼深度提纯过程中,硅与氧的亲合力比磷与氧的亲合力大,故在脱磷之前,先脱硅(si≤0.15%);并在脱硅、脱磷、脱硫过程中铁液中的碳也易脱除,铁液中si≤0.15%,p≤0.008%,s≤0.010%时,碳在3.50~3.90%。铁液中ce(碳当量)仅在3.55%~3.95%,ce(碳当量)远离共晶点,此时铁液的流动性极差,生铁锭外观质量严重恶化,铸造用超高纯生铁外观质量存在大量的碎块、渣铁、气孔等缺陷,对下游铸造企业生产的铸件质量受到严重影响。技术实现要素:本发明提出一种提高铸造用超高纯生铁外观质量的方法,解决了现有技术中生铁外观质量差的问题。本发明的技术方案是这样实现的:一种提高铸造用超高纯生铁外观质量的方法,生铁铁液脱硅、脱磷、脱硫后,进行炉外增硅脱氧处理,所述增硅脱氧处理包括生铁铁液中加入增硅剂和助剂使生铁铁液碳当量控制在4.20%~4.30%。进一步地,所述增硅脱氧处理前生铁铁液顶渣扒渣,至渣层厚度≤5mm。进一步地,所述增硅剂包括75#硅铁,75#硅铁的粒度3~10mm。进一步地,所述的助剂包括质量比为(0.5-1):1的纳米tin粉、氟化铝;助剂与增硅剂的质量比为(1-2.5):600。进一步地,所述增硅脱氧处理时,生铁铁液温度控制在1400℃~1450℃。进一步地,所述碳当量计算公式为ce%=c%+1/3(si+p)%。进一步地,所述生铁铁液中加入增硅剂时,将喷枪插入铁液进行喷吹搅拌后静置,搅拌时间3-5min,静置4-6min。进一步地,所述喷枪的喷孔为“喇叭口”形状,喷枪搅拌气为氮气,氮气压力控制在0.4~0.5mpa。本发明的工作原理及有益效果为:1、本发明在生铁铁液脱硅、脱磷、脱硫后,设计了炉外增硅脱氧处理,采用该方法对铁液增硅,能精准控制铁液的含硅量,降低铁液中氧含量,硅的收得率达到90~97%,实现铁液ce(碳当量)在共晶点4.26%附近,显著提高铁液的流动性和铸造性能,解决超高纯生铁碎块、渣铁、气孔等缺陷,使生铁锭形状规整、表面洁净,提高铸造用超高纯生铁外观质量。2、本发明炉外增硅脱氧处理包括在生铁铁液中加入增硅剂和助剂,通过增硅剂和助剂的协同搭配设计,促进了硅铁的熔化分散吸收以及硅在铁液中的均匀稳定,其中助剂采用纳米tin粉、氟化铝协同,并优化设计了二者的质量比为(0.2-0.5):1,纳米tin粉作为新生夹杂物和结晶的非均匀形核质点,弥散细化了夹杂物和生铁的晶粒,氟化铝的加入,与纳米tin粉协同促进了硅铁在铁液中的均匀熔化及分散,并且协同抑制了质点的长大,使质点分布均匀弥散,有效控制了铸造生铁产品夹渣严重,细化能力差的问题,从而改善了生铁碎块、渣铁、气孔的缺陷。3、本发明中采用75#硅铁对铁液增硅,选用合适的硅铁粒度,硅的收得率高;75#硅铁熔点1300℃,si(l)=[si]自由能为△f。=-8500-6.09t,硅熔入铁液是放热的,不会对铁液造成大幅度降温,因此增硅过程铁液温度波动幅度小,不影响后续铸铁。4、本发明中生铁铁液中加入增硅剂时,喷枪插入铁液喷吹搅拌,喷枪喷孔采用“喇叭口”形状的特殊设计,在铁液增硅时搅拌力强,可实现铁液的全方位搅拌,无搅拌死区,铁液的混匀时间最短,促进铁液的化学成分和温度均匀化;喷吹气流能很好的分散,不会发生喷溅现象。附图说明下面结合附图和具体实施方式对本发明作进一步详细的说明。图1为本发明实施例1铸造得到的生铁锭外观质量示意图;图2为本发明对比例1铸造得到的生铁锭外观质量示意图;图3为本发明对比例2铸造得到的生铁锭外观质量示意图;图4为本发明对比例3铸造得到的生铁锭外观质量示意图;图5为本发明增硅脱氧处理采用的增硅装备系统示意图;图6为本发明增硅装备系统中的喷枪形状示意图。具体实施方式下面将结合本发明实施例,对本发明实施例中的技术方案进行清楚、完整地描述,显然,所描述的实施例仅仅是本发明一部分实施例,而不是全部的实施例。基于本发明中的实施例,本领域普通技术人员在没有作出创造性劳动前提下所获得的所有其他实施例,都属于本发明保护的范围。实施例1生铁铁液脱硅、脱磷、脱硫后,顶渣扒至渣层厚度≤5mm;然后对生铁铁液测温,温度在1435℃,并进行化学分析,其主要元素见表1:表1元素csimnpsti含量%3.860.080.0150.0070.0080.002计算ce(碳当量)控制在4.30%所需含硅量:根据ce%=c%+1/3(si+p)%,则si=(ce-c-1/3p)×3即:si=(4.26%-3.86%-1/3*0.007%)×3≈1.19301%所需硅含量(si)=1.19301%-0.08%=1.11301%75#硅铁含硅量73.5%,粒度5mm,吸收率为95%,铁液称重42.55吨,计算应加入75#硅铁量:73.5%×95%=69.825%1.11301%/69.825%≈0.015940.01594×42550kg≈678kg在增硅装备系统(如图5)中设定75#硅铁加入量678kg,助剂加入量为1.13kg,助剂中纳米tin粉、氟化铝的质量比为0.5:1;启动增硅装备,增硅剂硅铁和助剂混合,同时加入铁液中(即铁液包);等75#硅铁开始加入铁液时,将喷枪(如图6,喷枪为喇叭口形状)插入铁液进行喷吹搅拌,启动喷枪,喷枪搅拌气为氮气,氮气压力控制在0.4mpa,设定喷吹搅拌时间4min,喷吹搅拌后静置6min;增硅处理完毕后,运送到铸铁机开始铸生铁锭;经过增硅处理后,生铁锭化学成分见表2:表2元素csimnpsti含量%3.821.260.0180.0070.0060.003最终得到的生铁锭的外观质量如图1。实施例2生铁铁液脱硅、脱磷、脱硫后,顶渣扒至渣层厚度≤5mm;然后对生铁铁液测温,温度在1482℃,并进行化学分析,其主要元素见表3:表3元素csimnpsti含量%3.550.120.0070.0050.0070.001计算ce(碳当量)控制在4.20%所需含硅量:根据ce%=c%+1/3(si+p)%,则si=(ce-c-1/3p)×3即:si=(4.20%-3.55%-1/3*0.005)×3≈1.94499%所需硅含量(si)=1.94499%-0.12%=1.82499%75#硅铁含硅量73.5%,粒度3mm,吸收率为95%,铁液称重56.28吨,计算应加入75#硅铁量:73.5%×95%=69.825%1.82499%/69.825%≈0.026140.02614×56280kg≈1471kg在增硅装备系统中设定75#硅铁加入量1471kg,助剂加入量为3.68kg,助剂中纳米tin粉、氟化铝的质量比为1:1;启动增硅装备,增硅剂硅铁和助剂混合同时加入;等75#硅铁开始加入铁液时,将喷枪插入铁液进行喷吹搅拌,启动喷枪,喷枪搅拌气为氮气,氮气压力控制在0.5mpa,设定喷吹搅拌时间5min,喷吹搅拌后静置4min;增硅处理完毕后,运送到铸铁机开始铸生铁锭;经过增硅处理后,得到的生铁锭化学成分见表4:表4元素csimnpsti含量%3.541.970.0070.0050.0060.001实施例3生铁铁液脱硅、脱磷、脱硫后,顶渣扒至渣层厚度≤5mm;然后对生铁铁液测温,温度在1478℃,并进行化学分析,其主要元素见表5:表5元素csimnpsti含量%3.720.110.0090.0080.0100.002计算ce(碳当量)控制在4.30%所需含硅量:根据ce%=c%+1/3(si+p)%,则si=(ce-c-1/3p)×3即:si=(4.30%-3.72%-1/3*0.008)×3≈1.73199%所需硅含量(si)=1.73199%-0.11%=1.62199%75#硅铁含硅量73.5%,粒度10mm,吸收率为95%,铁液称重52.34吨,计算应加入75#硅铁量:73.5%×95%=69.825%1.62199%/69.825%≈0.023230.02323×52340kg≈1216kg在增硅装备系统中设定75#硅铁加入量1216kg,助剂加入量为5.07kg,助剂中纳米tin粉、氟化铝的质量比为0.6:1;启动增硅装备,增硅剂硅铁和助剂混合同时加入;等75#硅铁开始加入铁液时,将喷枪插入铁液进行喷吹搅拌,启动喷枪,喷枪搅拌气为氮气,氮气压力控制在0.5mpa,设定喷吹搅拌时间5min,喷吹搅拌后静置5min;增硅处理完毕后,运送到铸铁机开始铸生铁锭;经过增硅处理后,得到的生铁锭化学成分见表6:表6元素csimnpsti含量%3.701.790.0080.0080.0090.002对比例1与实施例1相比,区别仅在于未加入助剂,经过增硅处理后,得到的生铁锭外观质量如图2,存在碎块、渣铁、气孔等缺陷。对比例2与实施例1相比,区别仅在于助剂,助剂只加入了氟化铝,经过增硅处理后,得到的生铁锭外观质量如图3,存在碎块、渣铁、气孔等缺陷。对比例3与实施例1相比,区别仅在于助剂,助剂只加入了纳米tin粉,经过增硅处理后,得到的生铁锭外观质量如图4,存在碎块、渣铁、气孔等缺陷。由上述实施例1和对比例1-3可知,本发明实施例1中通过增硅脱氧处理将铁液碳当量控制在共晶点附近,大大提高了铁液的流动性和铸造性能,得到的生铁锭外观质量好,而对比例1增硅脱氧处理中未加入助剂制备得到的生铁锭外观质量差,存在碎块、渣铁、气孔等缺陷,可见通过增硅剂和助剂的协同搭配设计,促进了硅铁的熔化吸收以及硅在铁液中的均匀稳定;由对比例2、对比例3和实施例1比较可知,本发明中助剂单独使用纳米tin粉或氟化铝,制备得到的生铁锭外观质量均差,可见本发明中纳米tin粉、氟化铝协同,促进了硅铁在铁液中的均匀熔化及分散;分析原因为纳米tin粉作为新生夹杂物和结晶的非均匀形核质点,弥散细化了夹杂物和生铁的晶粒,氟化铝的加入,与纳米tin粉协同促进了硅铁在铁液中的均匀熔化及分散,并且协同抑制了质点的长大,使质点分布均匀弥散,有效控制了铸造生铁产品夹渣严重,细化能力差的问题,从而改善了生铁碎块、渣铁、气孔的缺陷。以上仅为本发明的较佳实施例而已,并不用以限制本发明,凡在本发明的精神和原则之内,所作的任何修改、等同替换、改进等,均应包含在本发明的保护范围之内。当前第1页12