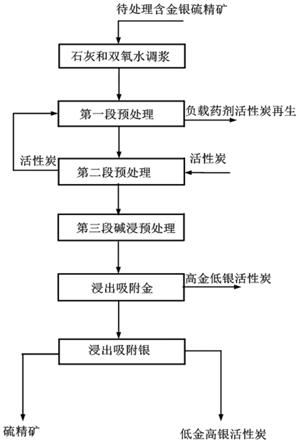
[0001]
本发明涉及一种从含金银硫精矿中高效提取金银的方法,所属选矿领域。
背景技术:[0002]
选矿是利用物理或化学方法将矿物原料中的有用矿物和无用矿物或有害矿物分开,或将多种有用矿物分离开的工艺过程,又称为“矿物加工”,产品中有用成分富集的称精矿,无用成分富集的称尾矿,选矿提供的有用成分富集的产品主要作为冶炼行业提取金属的原料。就目前来说,从含金银硫精矿提取金银的常用方法有直接氰化浸出法和氧化预处理(包括焙烧、湿法氧化、微生物氧化法)后—再氰化浸出法。对于直接氰化浸出法,矿物颗粒表面附着的捕收剂,使金银浸出速度和浸出率急剧下降;在氰化浸出补充氧气时(一般通过充空气的形式补充消耗的氧气),由于矿浆中有大量的起泡剂,矿浆表面漂浮有大量泡沫,易形成跑冒滴漏,给生产操作带来较大的困难,也易形成金银损失;在用活性炭富集金银时,由于溶液中有捕收剂和起泡剂等浮选药剂,这些有机物质被活性炭吸附,堵塞活性炭的微细孔洞,导致金银的吸附速度和吸附率急剧下降,尾液中金银含量偏高;氰化浸出时,由于硫铁矿的溶解,矿浆中存在硫离子和亚铁离子,与氰化物起化学反应,大量消耗氰化物,硫离子也与亚金银氰络离子形成沉淀,降低金银的浸出率,特别是对银的浸出率影响较大;在氰化尾液中含有大量的氰化物及少量的金银,因此必须循环利用,在此过程中,捕收剂和起泡剂不断富集,严重影响生产。对于氧化预处理(包括焙烧、湿法氧化、微生物氧化法)后—再氰化浸出法,由于工艺流程长、工艺复杂、生产控制难度大、生产成本高、选矿综合经济效益低,三废污染管控困难、生产安全可控性差;且不适用于从金、银、硫、铁含量较低的硫精矿浮选产品中提取金银。因此,从含金银硫精矿中高效提取金银,寻求科学的及效果显著的处理方法是解决现存问题的关键。
技术实现要素:[0003]
本发明提供一种从含金银硫精矿中高效提取金银的方法,能提高活性炭吸附速度、吸附率,提高金银浸出速度、浸出率,降低尾液金银含量。
[0004]
技术方案包括活性炭两次梯度逆流脱药与一次硫铁矿表面强化钝化的预处理,氰化浸出—活性炭分步提取金和银两部分,具体为:(1)、活性炭梯度逆流脱药与硫铁矿表面氧化钝化预处理。其分三段搅拌进行,其步骤如下:(a)将待处理的含金银硫精矿,添加石灰16~20kg/t和双氧水或高锰酸钾等氧化剂1~1.5kg/t,按液固比为1:1进行调浆,依次进行两段搅拌解吸脱药和一段碱浸强化表面钝化的预处理,每段预处理时间为2~4小时,第三段为充气强化碱浸槽,其充气量为0.3m
3
/(m
2
·
h)。在此过程中,石灰作用是将矿物颗粒表面的浮选药剂(捕收剂)解吸至水溶液中,同时确保适宜的矿浆终点ph值(ph=11~12);双氧水作用是在硫铁矿颗粒表面氧化生成一层钝化膜,阻止硫铁矿与氰化钠起化学反应及硫离子将已经溶解亚金银氰络离子沉淀;
(b)吸附剂颗粒活性炭从第二段脱药、钝化搅拌槽加入,搅拌吸附一段时间后,把炭和浆混合物依次向前窜送(即第二段至第一段),活性炭与矿浆相互逆流,两段脱药搅拌桶间安装有隔离炭浆的隔炭筛,矿浆返回原脱药搅拌槽,颗粒活性炭保留在前脱药搅拌槽中。当第一段吸附搅拌槽中的活性炭吸附饱和后,将炭浆混合物输送至1#振动筛进行炭浆分离,矿浆返回第一段脱药槽,负载浮选药剂的活性炭再生后,循环利用。活性炭的提炭量和再生频次,依活性炭吸附浮选药剂的饱和程度来确定。脱药搅拌槽中活性炭浓度保持在45~65g/l之间,活性炭的作用是将矿浆中的浮选药剂(捕收剂和起泡剂)吸附除去,确保氰化浸出矿浆不含浮选药剂。
[0005]
(2)、氰化浸出—活性炭分步分别吸附提取金和银,步骤如下:(a)将完成上述脱药、钝化步骤的矿浆输送至2#搅拌桶,添加氰化钠4~6kg/t进行调浆后,采用1#、2#浸出槽进行单独氰化浸出,其它浸出吸附槽进行边浸边吸附,每个浸出槽充气量为0.3m
3
/(m
2
·
h),总浸出时间为24~36小时。提金活性炭从7#浸出吸附槽添加,浸出吸附一段时间后,将炭浆混合物依次向前窜送,活性炭与矿浆相互逆流,两段浸出吸附槽间安装有隔离炭浆的隔炭筛,矿浆返回原浸出吸附槽,活性炭保留在前浸出吸附槽。当金在3#槽吸附饱和后,将炭浆混合物输送至2#振动筛进行炭浆分离,矿浆返回3#浸出吸附槽,高金低银活性炭进入解吸车间。提炭量及活性炭再生频次,依活性炭吸附金的饱和程度来确定,浸出吸附槽中活性炭浓度保持在15~30g/l之间。
[0006]
(b)提银活性炭从11#浸出吸附槽添加,浸出吸附一段时间后,将炭浆混合物依次向前窜送,活性炭与矿浆相互逆流,两段浸出吸附槽间安装有隔离炭浆的隔炭筛,矿浆返回原浸出吸附槽,活性炭保留在前浸出吸附槽。当银在8#槽吸附饱和后,将炭浆混合物输送至3#振动筛进行炭浆分离,矿浆返回8#浸出吸附槽,低金高银活性炭进入解吸车间。提炭量及活性炭再生频次,依活性炭吸附银的饱和程度来确定,浸出吸附槽中活性炭浓度保持在15~30g/l之间。
[0007]
本发明提供一种从含金银硫精矿中高效提取金银的能提高活性炭吸附速度、吸附率,提高金银浸出速度、浸出率,降低尾液金银含量,同时能避免跑冒滴漏现象、含氰尾液再处理的流程简单、容易控制、三废污染小、安全可控、适应性强的新方法。
[0008]
有益效果:(1)采用16~20kg/t石灰和1~1.5kg/t双氧水或高锰酸钾等氧化剂进行6~12小时预处理,破坏矿物颗粒表面吸附的捕收剂;(2)采用石灰和双氧水相互配合,进行6~12小时预处理,对硫铁矿矿物颗粒表面进行预先钝化,在氰化浸出时,起到阻止或降低硫铁矿与氰化钠反应及硫离子将已溶解亚金银络离子沉淀的作用,同时确保适宜的矿浆终点ph值(ph=11~12)。
[0009]
(3)采用了三段梯度逆流活性炭吸附工艺,清除溶液中的浮选药剂,脱药活性炭浓度为45~65g/l。避免了浮选药剂对氰化钠浸出、活性炭吸附金银效果和生产操控的影响;(4)单独进行充气量为0.3m
3
/(m
2
·
h)的硫铁矿表面强化钝化碱浸预处理段,浸出时间为2~4小时。
[0010]
(5)在2#搅拌桶中添加氰化钠4~6kg/t进行调浆后,采用1#、2#浸出槽先进行单独氰化浸出,然后分阶段分别对金和银进行边浸边吸附,浸出槽活性炭浓度为15~30g/l,总浸出时间为24~36小时,强化提金银效率,获得高金低银活性炭和低金高银活性炭两种产品,
该工艺特别适用于银含量高且波动大的含金银硫精矿的处理,对贵液中含银量较高的浸出液吸附较彻底。
[0011]
通过上述方式实现了:(1)提高活性炭吸附金银速度、吸附率。在预处理的脱药阶段,采用活性炭预先彻底脱出浮选药剂,避免了后续金银浸出吸附阶段,浮选药剂吸附在提金银活性炭表面,堵塞其孔洞,阻碍对金银的吸附;(2)提高金银浸出速度、浸出率,降低尾液金银含量。在预处理阶段,石灰将金银颗粒表面吸附的疏水性捕收剂解吸到溶液;同时,双氧水和氧气将硫铁矿表面钝化,降低亚铁离子和硫离子的影响,促进了金银浸出吸附阶段,金银颗粒对氰和氧的吸附及相互间的化学反应;(3)能避免跑冒滴漏现象、含氰尾液再处理。在预处理的脱药阶段,采用活性炭预先彻底脱出矿浆中的起泡剂,避免了后续金银浸出吸附阶段,在充气过程中,矿浆表面大量起泡,形成跑冒滴漏,使部分金银颗粒损失;(4)工艺流程简单、容易控制、三废污染小、安全可控。工艺中采用结构简单、容易操作的搅拌槽和浸出槽;同时,产生的废水全部循环利用,安全保障容易;(5)适应性强,特别适用于银含量高且波动大的含金银硫精矿的处理,对贵液中含银量较高的浸出液吸附较彻底。在金银浸出吸附阶段,将金和银分步、分别进行提取,克服了金对活性炭吸附银的阻碍,提高金银的回收率。
[0012]
综上所述,本发明提供一种从含金银硫精矿中高效提取金银方式,通过浮选精矿里存在的浮选药剂影响金银的浸出和吸附提取;硫精矿颗粒表面的硫和亚铁离子会与氰化钠反应而消耗氰化钠,及溶解在溶液中的硫离子与金、银离子生成沉淀,因此降低金银回收率。(1)主要解决影响金银回收率的外在原因(对共同的影响),(2)主要解决金银混合在一起,相互间影响,导致各自的回收率降低,金与银分开处理,排除或者降低相互间的影响程度,而达到提高各自回收率的目的。本发明能提高活性炭吸附速度、吸附率,提高金银浸出速度、浸出率,降低尾液金银含量,同时能避免跑冒滴漏现象、含氰尾液再处理的流程简单、容易控制、三废污染小、安全可控、适应性强的新方法。
附图说明
[0013]
图1一种从含金银硫精矿中高效提取金银工艺流程;图2一种从含金银硫精矿中高效提取金银设备联系图;其中,1:1#搅拌桶,2:2#脱药窜炭装置,3:1#振动筛,4:脱药桶;5:矿浆泵,6:2#搅拌桶,7浸出槽,8:2#振动筛,9:2#浸出窜炭装置,10:3#振动筛。
具体实施方式
[0014]
如图2所示的一种从含金银硫精矿中高效提取金银的系统,包括预处理系统和浸出系统;所述预处理系统包括1#搅拌桶1、1#预处理槽、2#预处理槽和充气浸出预处理槽,所述1#搅拌桶1高位设置(位置高于预处理槽,便于搅拌桶中的矿浆进入预处理槽中),1#搅拌桶1上端加入待处理含金银硫精矿和石灰,1#搅拌桶1、1#预处理槽、2#预处理槽和充气浸出预处理槽侧壁上端分别设置有溢流口,1#搅拌桶1溢流口出口与1#预处理槽中部连接,1#预
处理槽溢流口出口与2#预处理槽中部连接,2#预处理槽中加入活性炭,2#预处理槽溢流口出口与充气浸出预处理槽中部连接,充气浸出预处理槽溢流口出口通过矿浆泵5与2#搅拌桶上端入口连接;1#预处理槽、2#预处理槽中部伸入吸附管10,吸附管10上设置有泵,由吸附泵4提供负压进行吸附,2#预处理槽中吸附管10的另一端伸入1#预处理槽中,1#预处理槽的吸附管的另一端伸入1#振动筛,1#振动筛筛网下端收集的固体颗粒为载药活性炭,返回再生装置进行再生;1#振动筛下端收集的液体与1#搅拌桶溢流口出口的矿浆一起进入1#预处理槽中;充气浸出预处理槽内通过管道设置有充气泵6;所述浸出系统包括:2#搅拌桶7、1#~11#浸出槽、2#振动筛和3#振动筛,2#搅拌桶高位设置,2#搅拌桶7以及1#~11#浸出槽侧壁上端分别设置有溢流口,2#搅拌桶7溢流口出口与1#浸出槽中部连接,1#浸出槽溢流口出口与2#浸出槽中部连接,2#浸出槽溢流口出口与3#浸出槽中部连接,2#搅拌桶加入氰化钠;3#~7#浸出槽溢流口出口顺序与下一级浸出槽中部连接,4#~7#浸出槽中部伸入吸附管10,吸附管上设置有吸附泵2,4#~7#浸出槽中吸附管10的另一端伸入上一级浸出槽中;3#浸出槽中部伸入吸附管,吸附管上设置有泵,3#浸出槽中吸附管的另一端伸入2#振动筛9中,2#振动筛9筛网下端收集的固体颗粒为高金低银活性炭,2#振动筛9下端收集的液体与2#浸出槽溢流口出口的矿浆一起进入3#浸出槽中,3#浸出槽中加入氰化钠,7#浸出槽中加入活性炭;8#~11#浸出槽溢流口出口顺序与下一级浸出槽中部连接,9#~11#浸出槽中部伸入吸附管,吸附管上设置有泵,9#~11#浸出槽中吸附管的另一端伸入上一级浸出槽中;8#浸出槽中部伸入吸附管,吸附管上设置有泵,8#浸出槽中吸附管的另一端伸入3#振动筛11中,3#振动筛11筛网下端收集的固体颗粒为低金高银活性炭,3#振动筛11下端收集的液体与7#浸出槽溢流口出口的矿浆一起进入8#浸出槽中,11#浸出槽中加入活性炭,11#浸出槽溢流口出口流出的为硫精矿;1#搅拌桶、2#搅拌桶、1#预处理槽、2#预处理槽、充气浸出预处理槽以及1#~11#浸出槽中均设置有搅拌装置;1#预处理槽、2#预处理槽、3#~11#浸出槽溢流口处设置有筛网,避免活性炭通溢流口流入下一级槽中;所述1#振动筛3、2#振动筛9和3#振动筛11均为倾斜振动筛,振动筛下端设置漏斗形收集装置,用于收集液体;振动筛筛网下端为固体颗粒出料口。
[0015]
提取方法包括活性炭两次梯度逆流脱药与一次硫铁矿表面强化钝化的预处理,氰化浸出—活性炭分步提取金和银两部分,具体为:(1)、活性炭梯度逆流脱药与硫铁矿表面氧化钝化预处理。其分三段搅拌进行,其步骤如下:(a)将待处理的含金银硫精矿,添加石灰16~20kg/t和双氧水或高锰酸钾等氧化剂1~1.5kg/t,按液固比为1:1进行调浆,依次进行两段搅拌解吸脱药和一段碱浸强化表面钝化的预处理,每段预处理时间为2~4小时,第三段为充气强化碱浸槽,其充气量为0.3m
3
/(m
2
·
h)。在此过程中,石灰作用是将矿物颗粒表面的浮选药剂(捕收剂)解吸至水溶液中,同时确保适宜的矿浆终点ph值(ph=11~12);双氧水作用是在硫铁矿颗粒表面氧化生成一层钝化膜,阻止硫铁矿与氰化钠起化学反应及硫离子将已经溶解亚金银氰络离子沉淀;(b)吸附剂颗粒活性炭从第二段脱药、钝化搅拌槽加入,搅拌吸附一段时间后,把炭和浆混合物依次向前窜送(即第二段至第一段),活性炭与矿浆相互逆流,两段脱药搅拌桶间安装有隔离炭浆的隔炭筛,矿浆返回原脱药搅拌槽,颗粒活性炭保留在前脱药搅拌槽中。当
第一段吸附搅拌槽中的活性炭吸附饱和后,将炭浆混合物输送至1#振动筛进行炭浆分离,矿浆返回第一段脱药槽,负载浮选药剂的活性炭再生后,循环利用。活性炭的提炭量和再生频次,依活性炭吸附浮选药剂的饱和程度来确定。脱药搅拌槽中活性炭浓度保持在45~65g/l之间,活性炭的作用是将矿浆中的浮选药剂(捕收剂和起泡剂)吸附除去,确保氰化浸出矿浆不含浮选药剂。
[0016]
(2)、氰化浸出—活性炭分步分别吸附提取金和银,步骤如下:(a)将完成上述脱药、钝化步骤的矿浆输送至2#搅拌桶,添加氰化钠4~6kg/t进行调浆后,采用1#、2#浸出槽进行单独氰化浸出,其它浸出槽进行边浸边吸附,每个浸出槽充气量为0.3m
3
/(m
2
·
h),总浸出时间为24~36小时。提金活性炭从7#浸出槽添加,浸出吸附一段时间后,将炭浆混合物依次向前窜送,活性炭与矿浆相互逆流,两段浸出槽间安装有隔离炭浆的隔炭筛,矿浆返回原浸出槽,活性炭保留在前浸出槽。当金在3#槽吸附饱和后,将炭浆混合物输送至2#振动筛进行炭浆分离,矿浆返回3#浸出槽,高金低银活性炭进入解吸车间。提炭量及活性炭再生频次,依活性炭吸附金的饱和程度来确定,浸出槽中活性炭浓度保持在15~30g/l之间。
[0017]
(b)提银活性炭从11#浸出槽添加,浸出吸附一段时间后,将炭浆混合物依次向前窜送,活性炭与矿浆相互逆流,两段浸出槽间安装有隔离炭浆的隔炭筛,矿浆返回原浸出槽,活性炭保留在前浸出槽。当银在8#槽吸附饱和后,将炭浆混合物输送至3#振动筛进行炭浆分离,矿浆返回8#浸出槽,低金高银活性炭进入解吸车间。提炭量及活性炭再生频次,依活性炭吸附银的饱和程度来确定,浸出槽中活性炭浓度保持在15~30g/l之间。
[0018]
实施例一:一种含金银浮选硫精矿,其磨矿细度为-0.043mm占86%,主要元素化学分析结果为:金au5.68g/t、银 ag46.45g/t 、铜cu0.15% 、硫s47.34%、砷 as0.026%、 铁fe42.16%;物相分析结果见表1。
[0019]
由元素分析可知,硫精矿中含金5.68g/t,是一种低品位含金物料,此外,该精矿中铜、铁、硫含量较高,在氰化浸出过程中不利于金银的浸出。 由表1可知,金主要以裸露金的形态存在,其次是被硫化物( 即黄铁矿) 所包裹,少量为被其它脉石包裹裸,包裹部分不利于金的浸出。
[0020]
采用本发明对该含金银硫精矿进行实施,技术方案包括了活性炭次段梯度逆流脱药与一次硫铁矿表面强化钝化的预处理和氰化浸出—活性炭分步提取金和银两部分:(1)、活性炭梯度逆流脱药与硫铁矿表面氧化钝化预处理。其分三段搅拌进行,其步骤如下:(a)将待处理的含金银硫精矿,添加石灰16~20kg/t和双氧水或高锰酸钾等氧化剂1~1.5kg/t,按液固比为1:1进行调浆,依次进行两段搅拌解吸脱药和一段碱浸强化表面钝化的预处理,每段预处理时间为2~4小时,第三段为充气强化碱浸槽,其充气量为0.3m
3
/(m
2
·
h)。在此过程中,石灰作用是将矿物颗粒表面的浮选药剂(捕收剂)解吸至水溶液中,同时确保适宜的矿浆终点ph值(ph=11~12);双氧水作用是在硫铁矿颗粒表面氧化生成一层钝化膜,阻止硫铁矿与氰化钠起化学反应及硫离子将已经溶解亚金银氰络离子沉淀;(b)吸附剂颗粒活性炭从第二段脱药、钝化搅拌槽加入,搅拌吸附一段时间后,把炭和浆混合物依次向前窜送(即第二段至第一段),活性炭与矿浆相互逆流,两段脱药搅拌桶间安装有隔离炭浆的隔炭筛,矿浆返回原脱药搅拌槽,颗粒活性炭保留在前脱药搅拌槽中。当第一段吸附搅拌槽中的活性炭吸附饱和后,将炭浆混合物输送至1#振动筛进行炭浆分离,矿浆返回第一段脱药槽,负载浮选药剂的活性炭再生后,循环利用。活性炭的提炭量和再生频次,依活性炭吸附浮选药剂的饱和程度来确定。脱药搅拌槽中活性炭浓度保持在45~65g/l之间,活性炭的作用是将矿浆中的浮选药剂(捕收剂和起泡剂)吸附除去,确保氰化浸出矿浆不含浮选药剂。
[0021]
(2)、氰化浸出—活性炭分步分别吸附提取金和银,步骤如下:(a)将完成上述脱药、钝化步骤的矿浆输送至2#搅拌桶,添加氰化钠4~6kg/t进行调浆后,采用1#、2#浸出槽进行单独氰化浸出,其它浸出吸附槽进行边浸边吸附,每个浸出槽充气量为0.3m
3
/(m
2
·
h),总浸出时间为24~36小时。提金活性炭从7#浸出吸附槽添加,浸出吸附一段时间后,将炭浆混合物依次向前窜送,活性炭与矿浆相互逆流,两段浸出吸附槽间安装有隔离炭浆的隔炭筛,矿浆返回原浸出吸附槽,活性炭保留在前浸出吸附槽。当金在3#槽吸附饱和后,将炭浆混合物输送至2#振动筛进行炭浆分离,矿浆返回3#浸出吸附槽,高金低银活性炭进入解吸车间。提炭量及活性炭再生频次,依活性炭吸附金的饱和程度来确定,浸出吸附槽中活性炭浓度保持在15~30g/l之间。
[0022]
(b)提银活性炭从11#浸出吸附槽添加,浸出吸附一段时间后,将炭浆混合物依次向前窜送,活性炭与矿浆相互逆流,两段浸出吸附槽间安装有隔离炭浆的隔炭筛,矿浆返回原浸出吸附槽,活性炭保留在前浸出吸附槽。当银在8#槽吸附饱和后,将炭浆混合物输送至3#振动筛进行炭浆分离,矿浆返回8#浸出吸附槽,低金高银活性炭进入解吸车间。提炭量及活性炭再生频次,依活性炭吸附银的饱和程度来确定,浸出吸附槽中活性炭浓度保持在15~30g/l之间。最终获得高金低银活性炭含金为1265.52g/t、含银为1854.78g/t,低金高银活性炭含金为217.66g/t、含银为5375.66g/t,金总回收率为86.83%,银总回收率为64.87%。
[0023]
(5)提高活性炭吸附速度、吸附率。在预处理的脱药阶段,采用活性炭预先彻底脱出浮选药剂,避免了后续金银浸出吸附阶段,浮选药剂吸附在提金银活性炭表面,堵塞其孔洞,阻碍对金银的吸附;(6)提高金银浸出速度、浸出率,降低尾液金银含量。在预处理阶段,石灰将金银颗粒表面吸附的疏水性捕收剂解吸到溶液;同时,双氧水和氧气将硫铁矿表面钝化,降低亚铁离子和硫离子的影响,促进了金银浸出吸附阶段,金银颗粒对氰和氧的吸附及相互间的化学反应;(7)能避免跑冒滴漏现象、含氰尾液再处理。在预处理的脱药阶段,采用活性炭预先彻底脱出矿浆中的起泡剂,避免了后续金银浸出吸附阶段,在充气过程中,矿浆表面大量起泡,形成跑冒滴漏,使部分金银颗粒损失;(8)工艺流程简单、容易控制、三废污染小、安全可控。工艺中采用结构简单、容易操作的搅拌槽和浸出槽;同时,产生的废水全部循环利用,安全保障容易。
[0024]
实施例二:一种含金银浮选硫精矿,其磨矿细度为-0.043mm占85%,主要元素化学分析结果为:金au6.31g/t、银 ag78.18g/t 、铜cu0.10% 、硫s46.85%、砷 as0.11%、 铁fe42.49%;物相分析结果见表2。
[0025]
由元素分析可知,硫精矿中含金6.31g/t,是一种低品位含金物料,此外,该精矿中铜、铁、硫含量较高,在氰化浸出过程中不利于金的浸出。 由表1可知,金主要以裸露金的形态存在,其次是被硫化物( 即黄铁矿) 所包裹,少量为被其它脉石包裹裸,包裹部分不利于金的浸出。
[0026]
采用本发明对该含金银硫精矿进行实施,技术方案包括了活性炭两次梯度逆流脱药与一次硫铁矿表面强化钝化的预处理和氰化浸出—活性炭分步提取金和银两部分:(1)、活性炭梯度逆流脱药与硫铁矿表面氧化钝化预处理。其分三段搅拌进行,其步骤如下:(a)将待处理的含金银硫精矿,添加石灰16~20kg/t和双氧水或高锰酸钾等氧化剂1~1.5kg/t,按液固比为1:1进行调浆,依次进行两段搅拌解吸脱药和一段碱浸强化表面钝化的预处理,每段预处理时间为2~4小时,第三段为充气强化碱浸槽,其充气量为0.3m
3
/(m
2
·
h)。在此过程中,石灰作用是将矿物颗粒表面的浮选药剂(捕收剂)解吸至水溶液中,同时确保适宜的矿浆终点ph值(ph=11~12);双氧水作用是在硫铁矿颗粒表面氧化生成一层钝化膜,阻止硫铁矿与氰化钠起化学反应及硫离子将已经溶解亚金银氰络离子沉淀;(b)吸附剂颗粒活性炭从第二段脱药、钝化搅拌槽加入,搅拌吸附一段时间后,把炭和浆混合物依次向前窜送(即第二段至第一段),活性炭与矿浆相互逆流,两段脱药搅拌桶间安装有隔离炭浆的隔炭筛,矿浆返回原脱药搅拌槽,颗粒活性炭保留在前脱药搅拌槽中。当第一段吸附搅拌槽中的活性炭吸附饱和后,将炭浆混合物输送至1#振动筛进行炭浆分离,矿浆返回第一段脱药槽,负载浮选药剂的活性炭再生后,循环利用。活性炭的提炭量和再生频次,依活性炭吸附浮选药剂的饱和程度来确定。脱药搅拌槽中活性炭浓度保持在45~65g/l之间,活性炭的作用是将矿浆中的浮选药剂(捕收剂和起泡剂)吸附除去,确保氰化浸出矿浆不含浮选药剂。
[0027]
(2)、氰化浸出—活性炭分步分别吸附提取金和银,步骤如下:(a)将完成上述脱药、钝化步骤的矿浆输送至2#搅拌桶,添加氰化钠4~6kg/t进行调浆后,采用1#、2#浸出槽进行单独氰化浸出,其它浸出吸附槽进行边浸边吸附,每个浸出槽充气量为0.3m
3
/(m
2
·
h),总浸出时间为24~36小时。提金活性炭从7#浸出吸附槽添加,浸出吸附一段时间后,将炭浆混合物依次向前窜送,活性炭与矿浆相互逆流,两段浸出吸附槽间安装有隔离炭浆的隔炭筛,矿浆返回原浸出吸附槽,活性炭保留在前浸出吸附槽。当金在3#槽吸附饱和后,将炭浆混合物输送至2#振动筛进行炭浆分离,矿浆返回3#浸出吸附槽,高金低银活性炭进入解吸车间。提炭量及活性炭再生频次,依活性炭吸附金的饱和程度来确定,浸
出吸附槽中活性炭浓度保持在15~30g/l之间。
[0028]
(b)提银活性炭从11#浸出吸附槽添加,浸出吸附一段时间后,将炭浆混合物依次向前窜送,活性炭与矿浆相互逆流,两段浸出吸附槽间安装有隔离炭浆的隔炭筛,矿浆返回原浸出吸附槽,活性炭保留在前浸出吸附槽。当银在8#槽吸附饱和后,将炭浆混合物输送至3#振动筛进行炭浆分离,矿浆返回8#浸出吸附槽,低金高银活性炭进入解吸车间。提炭量及活性炭再生频次,依活性炭吸附银的饱和程度来确定,浸出吸附槽中活性炭浓度保持在15~30g/l之间。最终获得高金低银活性炭含金为1357.38g/t、含银为1728.85g/t,低金高银活性炭含金为215.66g/t、含银为6165g/t,金总回收率为88.15%,银总回收率为67.41%。
[0029]
通过上述案例说明了,采用该发明,获得金银指标稳定、可靠,对不同浮选含金银硫精矿具有较好的适应性,特别适用于金银含量比例较高的含金银硫精矿的处理。