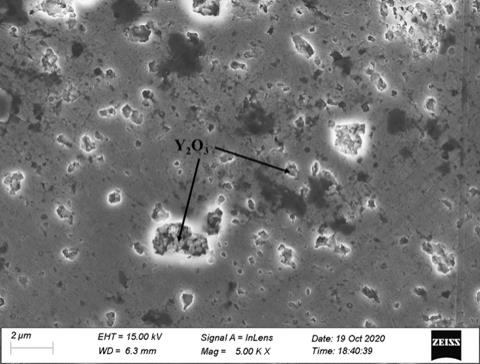
[0001]
本发明属于金属基复合材料制备技术领域,具体涉及一种氧化钇弥散强化铜的制备方法。
背景技术:[0002]
弥散强化铜基复合材料通过将热力学稳定性高、化学性质稳定和强度高的纳米级第二相颗粒均匀地分散在铜基体中,大幅度强化基体材料的强度,并尽可能保留铜优异的导电性,因此,在航天航空、电子电气行业中有着广泛的应用。在众多第二相颗粒中,氧化钇等稀土氧化物颗粒被认为是最合适的弥散强化相。氧化钇具有高温热动力学稳定性,良好的制冷效率,优异的耐蠕动和疲劳性;而且更重要的是,氧化钇具有类萤石结构,在合适的条件下,与铜基体存在位相匹配关系,从而能够引起切割粒子强化。然而,弥散强化相的添加,材料强度虽会提高,但随着增强体含量的增加,增强体颗粒容易发生团聚,进而影响材料的综合性能。目前单纯的球磨工艺不能实现增强体的均匀分散,如何有效地降低增强体的团聚情况是目前亟需解决的问题。
技术实现要素:[0003]
本发明所要解决的技术问题在于针对上述现有技术的不足,提供一种氧化钇弥散强化铜的制备方法。该方法通过对铜粉氧化有效降低了铜粉塑性,然后与氧化钇分两步进行高能球磨处理,使得氧化后的铜粉进一步得到细化,且使氧化钇更均匀地分布在混合粉末中,实现了氧化钇的均匀分散,避免了氧化钇弥散强化铜中氧化钇增强体的团聚,进而有利于提高了氧化钇弥散强化铜的力学性能。
[0004]
为解决上述技术问题,本发明采用的技术方案是:一种氧化钇弥散强化铜的制备方法,其特征在于,该方法包括以下步骤:步骤一、对铜粉进行氧化处理,在铜粉表面生成氧化膜,得到氧化后的铜粉;步骤二、将步骤一中得到的氧化后的铜粉与氧化钇进行两步高能球磨处理,然后进行真空干燥,得到混合粉末;步骤三、将步骤二中得到的混合粉末进行热还原处理,得到复合粉末;步骤四、将步骤三中得到的复合粉末进行放电等离子烧结,得到氧化钇弥散强化铜。
[0005]
本发明首先将铜粉进行氧化处理,在铜粉表面生成含有纳米氧化物颗粒的氧化膜,有效降低了铜粉塑性,然后与氧化钇分两步进行高能球磨处理,由于氧化后的铜粉塑性降低,经高能球磨处理易于变形,从而其尺寸进一步得到细化,且使氧化钇更均匀地分布在混合粉末中,同时,通过两步高能球磨处理减少了氧化钇的团聚,达到均匀分散氧化钇的目的;经后续热还原处理,混合粉末中铜粉表面生成的含有纳米氧化物颗粒的氧化膜被还原生成铜纳米颗粒,实现纳米级分散的效果,从而得到铜和氧化钇均匀分散的复合粉末,经烧结成型得到氧化钇弥散强化铜。综上,本发明的方法实现了氧化钇的均匀分散,避免了氧化钇弥散强化铜中氧化钇增强体的团聚,提高了氧化钇弥散强化铜的力学性能。
[0006]
上述的一种氧化钇弥散强化铜的制备方法,其特征在于,步骤一中所述氧化处理的温度为250℃~450℃。该优选温度有利于在铜粉表面形成含有纳米氧化物颗粒的氧化膜,且氧化后的铜粉容易分散,不易团聚。
[0007]
上述的一种氧化钇弥散强化铜的制备方法,其特征在于,步骤二中所述氧化钇与步骤一中铜粉的质量之比为1:200~5.92:200。该优选的质量之比保证了氧化钇的加入量,且有利于实现氧化钇的分散。
[0008]
上述的一种氧化钇弥散强化铜的制备方法,其特征在于,步骤二中所述两步高能球磨处理采用的转速均为450rpm。该优选的转速有利于氧化后的铜粉进一步得到细化,同时有效减少了氧化钇的团聚。
[0009]
上述的一种氧化钇弥散强化铜的制备方法,其特征在于,步骤四中所述放电等离子烧结的温度为850℃~1050℃,压力为40mpa~160mpa,保温时间为5min~30min。该优选工艺参数制备得到的复合材料没有显著空隙且致密度高。
[0010]
本发明与现有技术相比具有以下优点:1、本发明通过对铜粉氧化,有效降低了铜粉塑性,然后与氧化钇分两步进行高能球磨处理,使得氧化后的铜粉进一步得到细化,且使氧化钇更均匀地分布在混合粉末中,经后续热还原处理得到铜和氧化钇均匀分散的复合粉末并烧结成型,实现了氧化钇的均匀分散,避免了氧化钇弥散强化铜中氧化钇增强体的团聚,提高了氧化钇弥散强化铜的力学性能。
[0011]
2、本发明采用两步高能球磨处理减少了氧化钇的团聚,达到均匀分散氧化钇的目的。
[0012]
3、本发明的制备工艺简单,易于实现。
[0013]
下面通过附图和实施例对本发明的技术方案作进一步的详细描述。
附图说明
[0014]
图1为本发明实施例1中铜粉的sem图。
[0015]
图2本发明实施例1制备的混合粉末的eds面扫描图。
[0016]
图3为本发明实施例1制备的氧化钇弥散强化铜的sem图。
具体实施方式
[0017]
实施例1本实施例包括以下步骤:步骤一、将200g铜粉置于大气气氛中,在温度为250℃的条件下进行氧化处理5h,在铜粉表面生成氧化膜,得到氧化后的铜粉;步骤二、将步骤一中得到的氧化后的铜粉与2.96g氧化钇、60ml乙醇在转速为450rpm的条件下进行第一步高能球磨处理6h,然后进行真空干燥,再加入2.96g氧化钇在转速为450rpm的条件下进行第二步高能球磨处理6h,经真空干燥,得到混合粉末;步骤三、将步骤二中得到的混合粉末在400℃进行热还原处理4h,得到复合粉末;所述热还原处理采用的还原气氛为氢气体积分数为8%的氢氩混合气;步骤四、将步骤三中得到的复合粉末进行放电等离子烧结,得到氧化钇弥散强化铜;所述放电等离子烧结的温度为850℃,压力为40mpa,保温时间为10min。
[0018]
图1为本实施例中铜粉的sem图,图2本实施例制备的混合粉末的eds面扫描图,将图1和图2比较可以看出,经两步高能球磨处理后,铜粉进一步细化,尺寸减小。
[0019]
图3为本实施例制备的氧化钇弥散强化铜的sem图,从图3可以看出,氧化钇弥散强化铜中氧化钇分散均匀。
[0020]
实施例2本实施例包括以下步骤:步骤一、将200g铜粉置于大气气氛中,在温度为300℃的条件下进行氧化处理5h,在铜粉表面生成氧化膜,得到氧化后的铜粉;步骤二、将步骤一中得到的氧化后的铜粉与0.5g氧化钇、60ml乙醇在转速为450rpm的条件下进行第一步高能球磨处理6h,然后进行真空干燥,再加入0.5g氧化钇在转速为450rpm的条件下进行第二步高能球磨处理6h,经真空干燥,得到混合粉末;步骤三、将步骤二中得到的混合粉末在400℃进行热还原处理4h,得到复合粉末;所述热还原处理采用的还原气氛为氢气体积分数为8%的氢氩混合气;步骤四、将步骤三中得到的复合粉末进行放电等离子烧结,得到氧化钇弥散强化铜;所述放电等离子烧结的温度为900℃,压力为100mpa,保温时间为5min。
[0021]
实施例3本实施例包括以下步骤:步骤一、将200g铜粉置于大气气氛中,在温度为450℃的条件下进行氧化处理5h,在铜粉表面生成氧化膜,得到氧化后的铜粉;步骤二、将步骤一中得到的氧化后的铜粉与1.5g氧化钇、60ml乙醇在转速为450rpm的条件下进行第一步高能球磨处理6h,然后进行真空干燥,再加入1.5g氧化钇在转速为450rpm的条件下进行第二步高能球磨处理6h,经真空干燥,得到混合粉末;步骤三、将步骤二中得到的混合粉末在400℃进行热还原处理4h,得到复合粉末;所述热还原处理采用的还原气氛为氢气体积分数为8%的氢氩混合气;步骤四、将步骤三中得到的复合粉末进行放电等离子烧结,得到氧化钇弥散强化铜;所述放电等离子烧结的温度为1050℃,压力为160mpa,保温时间为30min。
[0022]
以上所述,仅是本发明的较佳实施例,并非对本发明作任何限制。凡是根据发明技术实质对以上实施例所作的任何简单修改、变更以及等效变化,均仍属于本发明技术方案的保护范围内。