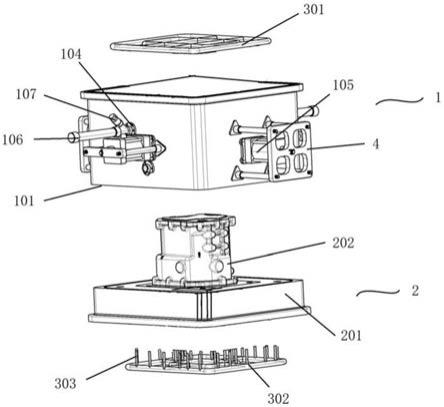
1.本实用新型属于消失模铸造模具技术领域,具体涉及一种模具。
背景技术:2.消失模铸造是将铸件尺寸形状相似的石蜡或泡沫模型组合成模型簇,刷涂耐火涂料并烘干后,干石英砂中振动造型,在负压下浇注,使模型气化,液体金属占据模型位置,凝固冷却后形成铸件的新型铸造方法,因其工艺无需取模、无分型面、无砂芯,以及其铸件没有飞边、毛刺和拔模斜度,因此和传统的砂型铸造相比得到了广泛的应用。
3.目前,现有的消失模铸造行业内最常见的方案是中心线分型,即将一个模型分成两个或者多个部分进行铸造,保证成型后每一部分模型能够顺利出模,增加了一道组模的工序,将多个模型粘接组合成目标模型。这样就增加了模具的数量和制造成本,并且对消失模铸造整个工艺过程也会有较多的影响,增加组模粘接工序,增大了组模过程造成废品的概率,延长了工艺周期,增大了人工成本和辅料消耗,现有的模具在冷却过程中,因冷却系统的布置不均匀,冷却管的长短不一,导致的压力不同,冷却管的出水量差异较大,模具冷却不均匀,对模型的脱离带来较大的影响。
技术实现要素:4.针对现有技术存在的不足,本实用新型的目的在于,本实用新型提供一种模具,解决现有技术中的模具制造采用中心线分型,这样增加了模具的数量和制造成本,并且对消失模铸造整个工艺过程也会有较多的影响,增加组模粘接工序,增大了组模过程中造成废品的概率,延长了工艺周期,增大了人工成本和辅料消耗以及现有的模具在冷却过程中,因冷却系统的布置不均匀,冷却管的长短不一,导致的压力不同,冷却管的出水量差异较大,模具冷却不均匀,对模型的脱离带来较大的影响的问题。
5.为了解决上述技术问题,本实用新型采用如下技术方案予以实现:
6.一种模具,包括移动模与固定模,所述移动模包括模框与多个侧模,所述侧模设于模框的各内侧壁上,所述侧模与模框内侧壁平行,各所述侧模能够沿着移动模轴线方向运动并能够围合成封闭的腔体,所述模框与侧模上分别设有加料孔并通过管子连接,所述固定模包括底座与模芯,所述模芯设于底座上,所述模芯的径向长度小于腔体的径向长度,所述侧模的内壁结构与对应的模芯的结构相匹配,模芯与腔体相互配合能够形成一体的模型腔。
7.进一步地,所述模具还包括冷却机构,所述冷却机构包括设于所述移动模的第一冷却管网,所述第一冷却管网围绕模框内侧壁设置并位于各侧模上方,所述第一冷却管网上设有多个喷头。
8.进一步地,所述冷却机构还包括第二冷却管网,所述底座为中空结构,上表面上开有多个通孔,所述第二冷却管网围绕底座内侧壁设置,所述第二冷却管网上设置多个喷管,所述喷管上设有多个喷头。
9.进一步地,所述模框的各外侧壁上分别设有气缸,所述气缸还穿过模框的各外侧壁与侧模连接。
10.进一步地,所述加料孔与加料管道连接,所述加料管道上开设有吹气口。
11.进一步地,如权利要求所述的模具,其特征在于,所述移动模的轴对称的两个外侧壁上的把手结构相同。
12.进一步地,所述移动模、腔体模芯与底座的中心线同轴设置。
13.进一步地,所述模框与底座为矩形,所述模框能够套设在所述底座上。
14.进一步地,所述底座与模芯之间还有起模板。
15.本实用新型与现有技术相比,具有如下技术效果:
16.(ⅰ)本实用新型的模具,通过在设置移动模与固定模,并在移动模的各内侧壁上设置多个侧模,多个侧模能够沿着移动模轴线方向运动并能够围合成封闭的腔体,在固定模上设置模芯,设置模芯的径向长度小于腔体的径向长度,侧模的内壁结构与对应的模芯的结构向匹配,移动模套设在固定模上,腔体能够包围模芯,此时,通过模芯在腔体内与各侧模形成封闭的模型腔,通过加料孔104向模型腔内加入模型原料,将原料填充到模型腔形成模型,本实用新型的模具只需要一台成型机制造出一体成型的模型,通过侧模与模芯的相互配合能够形成一体的模型腔,不需要将多个模型粘接呈目标模型,不仅节简了整个铸模的工艺过程,缩短了工艺周期,还避免了在多个模型粘接过程中因操作失误造成的废品率增加,大幅度的提升了模型的生产效率。
17.(ⅱ)本实用新型的模具设置冷却机构,通过在移动模和固定模上分别设置第一冷却管网与第二冷却管网,第一冷却管网与第二冷却管网采用喷头能够在模型铸造过程中对全方位的对多个侧模进行冷却,冷却过程中冷却水达到雾化状态,使模具达到快速均匀冷却。
附图说明
18.图1是本实用新型的模具的装配结构爆炸图;
19.图2是本实用新型的移动模的侧模打开状态与模芯的配合图;
20.图3是本实用新型的移动模的侧模围合形成腔体结构示意图;
21.图4是本实用新型的移动模的侧模围合形成腔体后与模芯的结构示意图。
22.图中各个标号的含义为:
[0023]1‑
移动模,2
‑
固定模,3
‑
冷却机构,4
‑
把手;
[0024]
101
‑
模框,102
‑
侧模,103
‑
腔体,104
‑
加料孔,105
‑
气缸,106
‑
加料管道,107
‑
吹气口,108
‑
模型腔;
[0025]
201
‑
底座,202
‑
模芯,203
‑
通孔,204
‑
起模板;
[0026]
301
‑
第一冷却管网,302
‑
第二冷却管网,303
‑
喷管。
[0027]
以下结合实施例对本实用新型的具体内容作进一步详细解释说明。
具体实施方式
[0028]
以下给出本实用新型的具体实施例,需要说明的是本实用新型并不局限于以下具体实施例,凡在本申请技术方案基础上做的等同变换均落入本实用新型的保护范围。
[0029]
实施例:
[0030]
一种模具,包括移动模1与固定模2,所述移动模1包括模框101与多个侧模102,所述侧模102设于模框101的各内侧壁上,所述侧模102与模框101内侧壁平行,各所述侧模102能够沿着移动模1轴线方向运动并能够围合成封闭的腔体103,所述模框101与侧模102上分别设有加料孔104并通过管子连接,所述固定模2包括底座201与模芯202,所述模芯202设于底座201上,所述模芯202的径向长度小于腔体103的径向长度,所述侧模102的内壁结构与对应的模芯202的结构相匹配。
[0031]
本实用新型的模具,通过在设置移动模1与固定模2,并在移动模1的各内侧壁上设置多个侧模102,多个侧模102能够沿着移动模轴线方向运动并能够围合成封闭的腔体103,在固定模2上设置模芯202,设置模芯的径向长度小于腔体的径向长度,侧模102的内壁结构与对应的模芯202的结构向匹配,移动模1套设在固定模2上,腔体103能够包围模芯202,此时,通过模芯202在腔体103内与各侧模102形成封闭的模型腔108,通过加料孔104向模型腔108内加入模型原料,将原料填充到模型腔108形成模型,本实用新型的模具只需要一台成型机制造出一体成型的模型,通过侧模102与模芯202的相互配合能够形成一体的模型腔108,不需要将多个模型粘接呈目标模型,不仅节简了整个铸模的工艺过程,缩短了工艺周期,还避免了在多个模型粘接过程中因操作失误造成的废品率增加,大幅度的提升了模型的生产效率。
[0032]
其中,本实施例中的侧模102与模芯202的材料为铝合金,通过加料孔104向模型腔108中注入的原料为预发熟化后的珠粒将模型腔108充满。
[0033]
作为本实施例的一种优选方案,所述模具还包括冷却机构3,所述冷却机构3包括设于所述移动模1的第一冷却管网301,所述第一冷却管网301围绕模框101内侧壁设置并位于各侧模102上方,所述第一冷却管网301上设有多个喷头,冷却机构3用于对铸造后的侧模102进行冷却,目的是为了使侧模102冷却后进一步的使模型腔108的珠粒能够快速降温,使之尽快凝固成型,便于模型从模具中取出。
[0034]
其中,通过在移动模上设置第一冷却管网301,第一冷却管网301设置用喷头,能够在模型铸造过程中从上方开始对多个侧模102进行冷却,冷却水在重力的作用下从上至下流动,对模具进行全面冷却,冷却过程中喷头能够使冷却水达到雾化状态,从而达到均匀冷却的目的。
[0035]
作为本实施例的一种优选方案,所述冷却机构3还包括第二冷却管网302,所述底座201为中空结构,上表面上开有多个通孔203,所述第二冷却管网302围绕底座201内侧壁设置,所述第二冷却管网302上设置多个喷管303,所述喷管303上设有多个喷头。
[0036]
其中,通过在固定模上设置第二冷却管网,在第二冷却管网302上设置多个喷管303,在喷管303的作用下冷却水能够克服重力向上喷洒通过通孔203冷却侧模,通过第二冷却管网302与第一冷却管网301的相互的配合实现了侧模的上下两个方位的冷却,提高了冷却效率,通孔203还用于整个模具在蒸汽加热过程中使蒸汽通过,目的是为了在模具加热珠粒时,使珠粒在蒸汽的作用下充分加热泡发后,珠粒之间的缝隙变小,使模型表面的珠粒良好的融合,制得的模型表面更光滑。
[0037]
作为本实施例的一种优选方案,所述模框101的各外侧壁上分别设有气缸105,所述气缸105还穿过模框101的各外侧壁与侧模102连接。
[0038]
其中,气缸105用于带动侧模102在模框101上移动,进行围合形成腔体103或打开,操作方便,提高工作效率。
[0039]
作为本实施例的一种优选方案,所述加料孔104与加料管道106连接,所述加料管道106上开设有吹气口107。
[0040]
其中,加料管道106用于向模型腔108中添加预发熟化后的珠粒,吹气口107与外部动力设备连接,外部动力设备向吹起口107提供气动力,在吹气口107作用下使预发熟化后的珠粒进入模型腔108后分布更均匀,使得最终制得的模具密度均匀,质量高。
[0041]
作为本实施例的一种优选方案,所述移动模1的各外侧壁上分别还设有把手4,便于工作人员对模具的操作与移动。
[0042]
作为本实施例的一种优选方案,所述移动模1的轴对称的两个外侧壁上的把手结构相同,用于适应不同工作模式下对模具的移动,本实施例中的把手结构设置有2组。
[0043]
作为本实施例的一种优选方案,所述移动模1、腔体103模芯202与底座201的中心线同轴设置。
[0044]
作为本实施例的一种优选方案,所述模框101与底座201为矩形,对应的侧模102设置数量为4个,所述模框101能够套设在所述底座201上,通过模框101与底座201的相互配合实现模型的铸造与分离等工艺的实现。
[0045]
作为本实施例的一种优选方案,所述底座201与模芯202之间还有起模板204,起模板204在动力气缸的作用下能够向侧型施加向上的冲力,使模型与腔体103脱离,便于工作人员将铸造好的模型取出。
[0046]
本实施例的使用过程:
[0047]
将移动模1套设在固定模2上方,在气缸105的带动下侧模102向模芯202方向移动,侧模102与模芯202形成封闭的模型腔108,接着通过加料孔向模型腔108中加入预发熟化后的珠粒,通过吹气口107使得预发熟化后的珠粒更均匀的进入模型腔108中,加料完成后对整个模具采用蒸汽加热,对模具进行保压,此时模型的形状已经形成,停止加热,启动冷却机构3,通过第一冷却管网301与第二冷却管网302从上下两方位向侧模102喷水,实现快速的将侧模102冷却实现模型的快速成型,最后,启动气缸105,在气缸105的带动下侧模102向远离模芯202方向移动,侧模102与模具分离,启动动力气缸,在启动动力气缸的作用下将起模板204向上推起,在推力的借助下实现模型与模具与模芯202的分离,将模型取出。