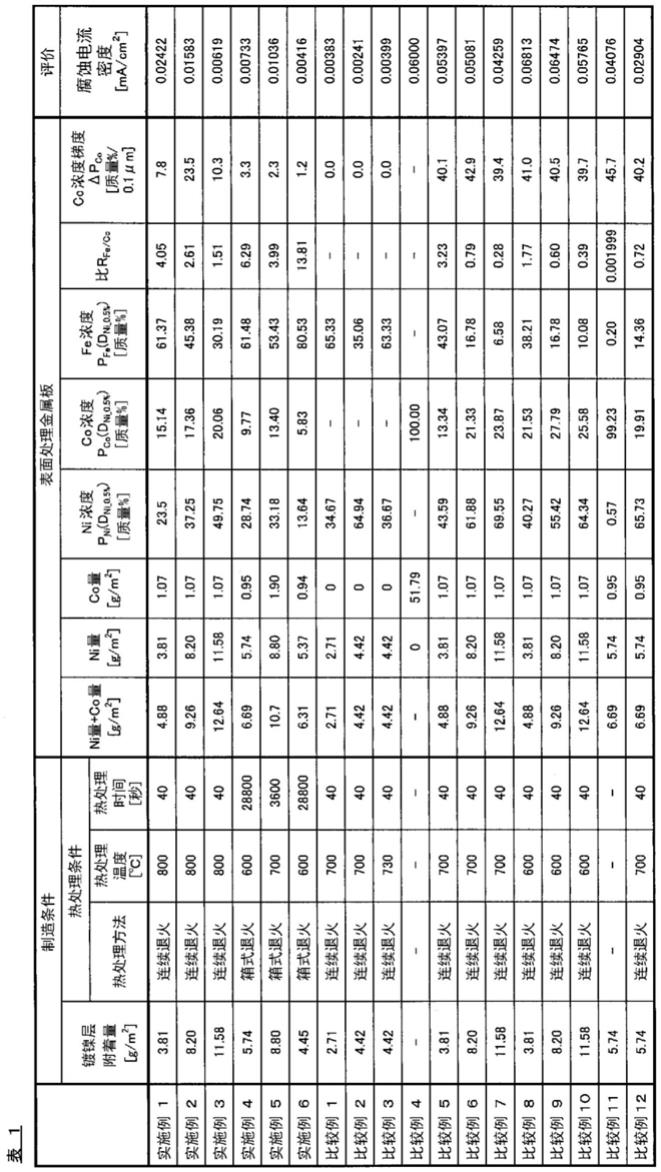
1.本发明涉及表面处理钢板和其制造方法。
背景技术:2.近年来,在音频设备、移动电话等多方面使用有便携用设备,作为其工作电源,大多使用有作为一次电池的碱性电池、作为二次电池的镍氢电池、锂离子电池等。这些电池中,要求高功率化和长寿命化等高性能化,填充由正极活性物质、负极活性物质等形成的发电元件的电池容器也要求作为电池的重要的构成元件的性能的改善。
3.例如,专利文献1中,用作电池容器的情况下,从改善电池特性的观点出发,公开了一种在成为电池容器内表面的面的最表面形成有特定的镍
‑
钴合金层的电池容器。
4.现有技术文献
5.专利文献
6.专利文献1:国际公开第2012/147843号
技术实现要素:7.发明要解决的问题
8.然而,将上述专利文献1的电池容器用作碱性电池、镍氢电池等使用强碱性的电解液的电池的电池容器的情况下,随着时间经过,与电解液接触的电池容器内表面的接触电阻值上升,存在电池特性会降低的问题。针对于此,要求抑制经时后的电池特性的降低等电池特性进一步的改善。
9.本发明的目的在于,提供:用作使用强碱性的电解液的电池的电池容器时的电池特性优异,经时后也能抑制电池特性的降低的表面处理钢板。另外,本发明的目的还在于,提供这样的表面处理钢板的制造方法。
10.用于解决问题的方案
11.本发明人等为了达成上述目的而进行了深入研究,结果发现:在钢板上形成有镍
‑
钴
‑
铁扩散层作为最表面侧的层的表面处理钢板中,关于对表面处理钢板进行基于高频辉光放电发射光谱分析法的测定从而求出的镍
‑
钴
‑
铁扩散层中的co浓度,控制作为co浓度的变化率的co浓度梯度δp
co
为特定的范围,从而可以达成上述目的,至此完成了本发明。
12.即,根据本发明,提供一种表面处理钢板,其具备:钢板;和,作为最表层形成于前述钢板上的镍
‑
钴
‑
铁扩散层,通过高频辉光放电发射光谱分析法从前述镍
‑
钴
‑
铁扩散层的表面侧向深度方向连续地测定ni强度、co强度和fe强度,基于前述ni强度、前述co强度和前述fe强度,求出前述镍
‑
钴
‑
铁扩散层的各深度位置处的、ni浓度、co浓度和fe浓度时,将前述co浓度示出最大值的深度位置设为d
co_max
,将比前述深度位置d
co_max
还靠近前述钢板侧、且前述co浓度相对于前述最大值示出15%的值的深度位置设为d
co_15%
的情况下,从前述深度位置d
co_max
至前述深度位置d
co_15%
为止之间的、co浓度梯度δp
co
为33质量%/0.1μm以下。
13.本发明的表面处理钢板中,优选通过高频辉光放电发射光谱分析法从前述镍
‑
钴
‑
铁扩散层的表面侧向深度方向连续地测定ni强度、co强度和fe强度,基于前述ni强度、前述co强度和前述fe强度,求出前述镍
‑
钴
‑
铁扩散层的各深度位置处的、ni浓度、co浓度和fe浓度时,将前述ni浓度示出最大值的深度位置设为d
ni_max
,将比前述深度位置d
ni_max
还靠近前述钢板侧、且前述ni浓度相对于前述最大值示出15%的值的深度位置设为d
ni_15%
的情况下,从前述深度位置d
ni_max
至前述深度位置d
ni_15%
为止之间的、ni浓度梯度δp
ni
为15质量%/μm以上。
14.本发明的表面处理钢板中,优选通过高频辉光放电发射光谱分析法从前述镍
‑
钴
‑
铁扩散层的表面侧向深度方向连续地测定ni强度、co强度和fe强度,基于前述ni强度、前述co强度和前述fe强度,求出前述镍
‑
钴
‑
铁扩散层的各深度位置处的、ni浓度、co浓度和fe浓度时,将前述镍
‑
钴
‑
铁扩散层中的前述ni强度相对于最大值成为0.5%的深度位置中、位于表面侧的深度位置设为d
ni_0.5%
的情况下,前述深度位置d
ni_0.5%
处的、ni浓度p
ni
(d
ni_0.5%
)为70质量%以下,co浓度p
co
(d
ni_0.5%
)为5质量%以上,fe浓度p
fe
(d
ni_0.5%
)为15质量%以上。
15.本发明的表面处理钢板中,优选前述深度位置d
ni_0.5%
处的、fe浓度p
fe
(d
ni_0.5%
)为30质量%以上。
16.本发明的表面处理钢板中,优选前述深度位置d
ni_0.5%
处的、co浓度p
co
(d
ni_0.5%
)为12质量%以上。
17.本发明的表面处理钢板中,优选前述镍
‑
钴
‑
铁扩散层中所含的co的含量为0.2g/m2以上。
18.本发明的表面处理钢板中,优选前述镍
‑
钴
‑
铁扩散层中所含的ni的含量为0.2~12.5g/m2。
19.本发明的表面处理钢板中,优选前述镍
‑
钴
‑
铁扩散层中所含的ni的含量为0.2~7.0g/m2。
20.本发明的表面处理钢板中,优选前述镍
‑
钴
‑
铁扩散层中所含的ni和co的总计含量为1.6~14.0g/m2。
21.本发明的表面处理钢板中,优选前述镍
‑
钴
‑
铁扩散层中所含的ni和co的总计含量为1.6~7.5g/m2。
22.另外,本发明的表面处理钢板优选在前述钢板与前述镍
‑
钴
‑
铁扩散层之间还具备铁
‑
镍扩散层。
23.本发明的表面处理钢板中,优选前述镍
‑
钴
‑
铁扩散层和前述铁
‑
镍扩散层中所含的ni的总计含量为1.0~12.5g/m2。
24.本发明的表面处理钢板中,优选前述镍
‑
钴
‑
铁扩散层和前述铁
‑
镍扩散层中所含的ni和co的总计含量为1.6~14.0g/m2。
25.另外,根据本发明,提供一种电池容器,其包含上述任意的表面处理钢板。
26.根据本发明,提供一种电池,其具备上述电池容器。
27.进而,根据本发明,提供一种表面处理钢板的制造方法,其为制造上述表面处理钢板的方法,所述制造方法具备如下工序:在钢板上形成镍的含量为0.2~12.5g/m2的镀镍层的工序;在前述镀镍层上形成钴的含量为0.2~5.0g/m2的镀钴层的工序;和,对形成有前述镀镍层和前述镀钴层的钢板,在450~900℃的温度下实施热处理,从而形成co浓度梯度δp
co
为33质量%/0.1μm以下的镍
‑
钴
‑
铁扩散层作为最表层的工序。
28.发明的效果
29.根据本发明,可以提供:用作使用强碱性的电解液的电池的电池容器时的电池特性优异,经时后也能抑制电池特性的降低的表面处理钢板。另外,根据本发明,还可以提供这样的表面处理钢板的制造方法。
附图说明
30.图1为示出应用了本发明的表面处理钢板的电池的一实施方式的立体图。
31.图2为沿图1的ii
‑
ii线的剖视图。
32.图3为本发明的表面处理钢板的一实施方式且图2的iii部的放大剖视图。
33.图4为用于说明制造图3所示的表面处理钢板的方法的图。
34.图5为用于对基于高频辉光放电发射光谱分析法的测定进行说明的图。
35.图6为用于说明求出co浓度梯度δp
co
、ni浓度梯度δp
ni
的方法的图。
36.图7为示出本发明的表面处理钢板的第2实施方式的剖视图。
37.图8为示出对于实施例2的表面处理钢板、利用高频辉光放电发射光谱分析装置测得的结果的图。
具体实施方式
38.以下,基于附图,对本发明的一实施方式进行说明。本发明的表面处理钢板被加工成符合期望的电池形状的外形形状。作为电池,没有特别限定,可以示例作为一次电池的碱性电池、作为二次电池的镍氢电池、锂离子电池等,作为这些电池的电池容器的构件,可以使用本发明的表面处理钢板。以下,作为使用强碱性的电解液的电池的一例,列举了碱性电池,以构成碱性电池的电池容器的正极罐中使用本发明的表面处理钢板的实施方式,对本发明进行说明。
39.图1为示出应用了本发明的表面处理钢板的碱性电池2的一实施方式的立体图,图2为沿图1的ii
‑
ii线的剖视图。对于本例的碱性电池2,在有底圆筒状的正极罐21的内部,隔着分隔件25填充有正极合剂23和负极合剂24,在正极罐21的开口部内表面侧敛缝安装有负极端子22、集电体26和由垫片27构成的封口体。需要说明的是,在正极罐21的底部中央,形成有凸状的正极端子211。而且,在正极罐21上,为了赋予绝缘性和改善设计性等,借由绝缘环28安装外壳29。
40.图1所示的碱性电池2的正极罐21可以通过利用深拉拔加工法、拉拔减薄加工法(di加工法)、拉拔拉伸加工法(dtr加工法)、或拉拔加工后组合使用拉伸加工与减薄加工的加工法等将本发明的表面处理钢板进行成型加工而得到。以下,参照图3,对于本发明的表面处理钢板(表面处理钢板1)的构成进行说明。
41.图3为放大了图2所示的正极罐21的iii部而示出的剖视图,相同图中,上侧相当于图1的碱性电池2的内表面(与碱性电池2的正极合剂23接触的面)。本实施方式的表面处理钢板1如图3所示那样,其在构成表面处理钢板1的钢板11上形成有镍
‑
钴
‑
铁扩散层12。需要说明的是,本实施方式的表面处理钢板1只要在钢板11的至少一个面、具体而言成为碱性电池2的内表面的面(成为电池容器的内表面的面)上形成镍
‑
钴
‑
铁扩散层12即可。也可以在成为外表面的面(成为电池容器的外表面的面)上形成镍
‑
钴
‑
铁扩散层,还可以在两个面上
形成,但从成为外表面的面作为电池保管或使用时的防锈性的观点出发,优选从钢板侧起依次形成镍
‑
铁扩散层和镍层。
42.本实施方式的表面处理钢板1是在钢板11上形成有镍
‑
钴
‑
铁扩散层12作为最表面侧的层的表面处理钢板,
43.对于表面处理钢板1,通过高频辉光放电发射光谱分析法从前述镍
‑
钴
‑
铁扩散层12的表面侧向深度方向连续地测定ni强度、co强度和fe强度,基于前述ni强度、前述co强度和前述fe强度,求出前述镍
‑
钴
‑
铁扩散层12的各深度位置处的、ni浓度、co浓度和fe浓度时,
44.将前述co浓度示出最大值的深度位置设为d
co_max
,将比前述深度位置d
co_max
还靠近前述钢板11侧、且前述co浓度相对于前述最大值示出15%的值的深度位置设为d
co_15%
的情况下,从前述深度位置d
co_max
至前述深度位置d
co_15%
为止之间的、co浓度梯度δp
co
为33质量%/0.1μm以下。
45.<钢板11>
46.作为本实施方式的钢板11,只要成型加工性优异就没有特别限定,例如可以使用低碳铝镇静钢(碳量0.01~0.15重量%)、碳量低于0.01重量%的极低碳钢、或极低碳钢中添加ti、nb等而成的非时效性极低碳钢。本实施方式中,也可以使用:对这些钢的热轧板进行酸洗而去除表面的氧化皮(氧化膜)后、冷轧、接着电解清洗后、退火并经表面光轧而成者;或,经前述冷轧、电解清洗后不进行退火而实施了表面光轧而成者等。另外,从生产率的观点出发,作为钢板11,优选使用连续钢带。
47.钢板11的厚度可以根据表面处理钢板的用途而适宜选择,没有特别限定,优选0.015~1.5mm。如果为碱性电池、硬币电池等的电池用钢板(碳钢或不锈钢),则优选0.15~0.6mm,特别是作为碱性电池罐用钢板,优选0.15~0.5mm。另一方面,在要求轻量化、柔性的用途中,优选0.015mm~0.1mm的箔状。
48.<镍
‑
钴
‑
铁扩散层12>
49.本实施方式的表面处理钢板1在钢板11上具备镍
‑
钴
‑
铁扩散层12。本实施方式中,作为形成镍
‑
钴
‑
铁扩散层12的方法,例如如图4所示那样,可以使用如下方法:在钢板11的表面依次形成镀镍层13和钴层14后,实施热处理,从而使钢板和各层中所含的铁、镍和钴分别热扩散,得到镍
‑
钴
‑
铁扩散层12。但是,作为形成镍
‑
钴
‑
铁扩散层12的方法,不特别限定于这样的方法。
50.对于本实施方式的表面处理钢板1的镍
‑
钴
‑
铁扩散层12,镍
‑
钴
‑
铁扩散层12中的、特定的深度区域中的、co浓度的变化率、即、co浓度梯度δp
co
被控制为特定的范围。
51.即,对于表面处理钢板1,通过高频辉光放电发射光谱分析法,在规定的测定条件下,从镍
‑
钴
‑
铁扩散层12的表面侧向钢板11沿深度方向连续地测定ni强度、co强度和fe强度,基于得到的ni强度、co强度和fe强度,求出镍
‑
钴
‑
铁扩散层12的各深度位置处的、ni浓度、co浓度和fe浓度时,将co浓度示出最大值的深度位置设为d
co_max
,将比深度位置d
co_max
还靠近钢板11侧、且co浓度相对于该最大值示出15%的值的深度位置设为d
co_15%
的情况下,从深度位置d
co_max
至深度位置d
co_15%
为止之间的、co浓度梯度δp
co
被控制为33质量%/0.1μm以下。
52.此处,对于co浓度梯度δp
co
的求解方法,参照图5的(a)、图5的(b)、图6的(a)进行
说明。
53.首先,为了设定通过高频辉光放电发射光谱分析法进行测定时的测定条件,准备测定条件调整用样品(在钢板上依次形成有镍镀层和钴镀层的样品)。然后,对于准备好的测定条件调整用样品,通过高频辉光放电发射光谱分析装置,在得到的ni强度、co强度和fe强度的最大值(即,镍镀层中的ni以单质检测的区域中的ni强度、钴镀层中的co以单质检测的区域中的co强度、和钢板中的fe以单质检测的区域中的fe强度)分别成为基本等同的值的条件下,从钴镀层的表面向钢板进行测定。将测得的结果的一例示于图5的(a)。图5的(a)中,纵轴表示强度,横轴表示边通过高频辉光放电发射光谱分析装置从表面处理钢板1的表面利用ar等离子体进行溅射边沿深度方向测定时的蚀刻深度。需要说明的是,作为以ni强度、co强度和fe强度的最大值分别成为等同的值的方式进行调整的方法,可以利用根据测定的每种元素调整高频辉光放电发射光谱分析装置的光电子增压器通路的电压(h.v.)的方法。
54.此处,镍、钴和铁由于基于ar等离子体的溅射速率基本等同,因此,通过高频辉光放电发射光谱分析装置测定镍、钴和铁的各自的单一材料的情况下,将溅射的条件(ar气体压力(单位为pa)和功率(单位为w))设为相同的情况下,各单一材料被蚀刻的量成为基本等量,因此,有利于测定的ni强度的镍的蚀刻量、有利于测定的co强度的钴的蚀刻量、和有利于测定的fe强度的铁的蚀刻量分别成为基本等量。
55.因此,如图5的(a)那样,在ni强度、co强度和fe强度的最大值分别成为基本等同的值(图5的(a)所示的例子中,强度(intensity)为约2.0v)的条件下,通过高频辉光放电发射光谱分析装置进行测定,从而由得到的ni强度、co强度和fe强度求出的强度比可以直接作为ni的质量、co的质量和fe的质量的质量比使用。例如fe强度相对于ni强度、co强度和fe强度的总计的比率可以直接作为fe的质量相对于ni的质量、co的质量和fe的质量的总计的比率(fe的含有比率(质量%)),这一点,对于ni、co也是同样的。本实施方式中,如此设定基于预先高频辉光放电发射光谱分析装置的测定条件(光电子增压器通路的电压),在设定好的条件下,对于表面处理钢板1进行测定,从而由得到的ni强度、co强度和fe强度,可以分别求出各深度位置(根据边溅射边测定时的测定时间求出的深度位置)处的、相对于镍、钴和铁的总计含量的、ni的含有比率、co的含有比率和fe的含有比率。
56.需要说明的是,对于基于高频辉光放电发射光谱分析装置的测定条件,图5的(a)所示的例子中,将ni强度、co强度和fe强度的最大值分别调整为约2.0v,但强度的最大值不限定于2.0v,可以设为任意的值,但值如果过低,则有测定的灵敏度降低的担心,另一方面,值如果过高,则得到的强度饱和而有无法得到准确的值的担心,因此,对测定条件调整用样品进行测定的情况下,在得到不成为饱和和灵敏度不足的程度的充分的强度的最大值那样的h.v.下设定。通常,成为测定装置的推荐或者目标h.v.下测得的值的
±
1.0v的范围。后述的实施例的测定中,使用的是,将ni的h.v.设定为630v进行测定时的ni强度的最大值。需要说明的是,为了得到充分的强度,测定条件调整用样品的镍镀层和钴镀层的各层的厚度优选设为0.2~1.0μm。
57.然后,通过图5的(a)所示的方法设定高频辉光放电发射光谱分析装置的测定条件后,在该测定条件下,测定本实施方式的表面处理钢板1,从而可以求出镍
‑
钴
‑
铁扩散层12中的ni含有比率、co含有比率和fe含有比率。
58.此处,图5的(b)为对于后述的实施例1的表面处理钢板1,通过高频辉光放电发射光谱分析法,在上述测定条件下,从镍
‑
钴
‑
铁扩散层12的表面侧向钢板11沿深度方向连续地测定ni强度、co强度和fe强度的图。另外,图6的(a)为示出基于图5的(b)所示的co强度数据制成的、蚀刻深度与co浓度的关系的图,图6的(b)为示出基于图5的(b)所示的ni强度数据制成的、蚀刻深度与ni浓度的关系的图。需要说明的是,上述图5的(a)、以及图5的(b)、图6的(a)、图6的(b)均是将横轴作为蚀刻深度的图,但蚀刻深度可以由高频辉光放电发射光谱分析的测定条件(包含溅射条件)和溅射时间求出。亦即,预先形成有不实施附着量明确的热处理的镀镍层的钢板中,由从蚀刻开始至相对于fe强度的最大值成为10%的强度的时间为止的溅射时间和附着量算出蚀刻速率,利用与此时相同的测定条件,从而可以基于表面处理钢板的溅射时间求出蚀刻深度。
59.而且,图5的(b)所示的图示出在上述测定条件下测得的结果,因此,由ni强度、co强度和fe强度求出的强度比可以直接作为ni的质量、co的质量和fe的质量的质量比使用,可以求出镍
‑
钴
‑
铁扩散层12中的各深度位置处的、ni的质量比率、co的质量比率和fe的质量比率、即、ni浓度、co浓度和fe浓度。具体地例如,ni强度相对于ni强度、co强度、fe强度的总计的比率(%)(ni强度/(ni强度+co强度+fe强度)
×
100)可以作为ni的质量比率、即、ni浓度使用。另外,co的质量比率、fe的质量比率也可以同样求出,同样地,可以将这些作为co浓度、fe浓度使用。而且,图6的(a)为示出如此求出的、镍
‑
钴
‑
铁扩散层12中的各深度位置处的、co浓度(即,co的质量相对于ni的质量、co的质量和fe的质量的总计的比率)的图。
60.而且,本实施方式中,如图6的(a)所示,将co浓度示出最大值的点f
co_max
所对应的深度位置设为d
co_max
,将比这样的点f
co_max
还靠近钢板11侧(即,深度较深的方向)、且浓度相对于在点f
co_max
(深度位置d)所示的co浓度的最大值示出15%的值的点f
co_15%
所对应的深度位置设为d
co_15%
的情况下,求出从深度位置d
co_max
至深度位置d
co_15%
为止之间的、co浓度梯度δp
co
时,以这样的co浓度梯度δp
co
成为33质量%/0.1μm以下的方式进行控制。即,如果参照图6的(a),则深度位置d
co_max
(点f
co_max
)处的co浓度为约45质量%,因此,深度位置d
co_15%
(点f
co_15%
)处的co浓度成为约6.75质量%。而且,深度位置d
co_max
(点f
co_max
)的蚀刻深度为0.2μm附近,深度位置d
co_15%
(点f
co_15%
)的蚀刻深度为0.7μm附近,如果算出co浓度梯度δp
co
,则成为7.8质量%/0.1μm。
61.即,该图6的(a)所示的实施例1中,将深度位置d
co_max
(点f
co_max
)作为顶点,逐渐向深度较深的方向推进测定直至深度位置d
co_15%
(点f
co_15%
)时,每0.1μm,以7.8质量%的比率co浓度示出减少。需要说明的是,如图6的(a)所示,co浓度的减少比率不恒定,因此,本实施方式中,将基于深度位置d
co_max
与深度位置d
co_15%
这2点处的co浓度测定的co浓度的变化率作为co浓度梯度δp
co
。即,可以以“co浓度梯度δp
co
(质量%/0.1μm)={深度位置d
co_max
处的co浓度(质量%)
‑
深度位置d
co_15%
处的co浓度(质量%)}/0.1
×
|深度位置d
co_max
处的深度(μm)
‑
深度位置d
co_15%
处的深度(μm)|”算出。
62.需要说明的是,基于高频辉光放电发射光谱分析装置的测定中,测定对象的硬度对溅射速率(和溅射时间)有影响,进一步特别是越成为距离最表层更深的地点,测定的强度有时越受到深度(从最表层至测定点的深度)的影响。因此,对于本实施方式的表面处理钢板1,在上述图5的(a)的方法中设定的测定条件下开始测定,求出各测定点(各深度位置)处的各元素的强度比作为各元素的含有比率。另外,即使在相同的溅射条件、h.v.下进行测
定,随着阳极的状态,整体的数值也有时上下波动,例如,上述图5的(a)的例子中,以强度(intensity)的最大值成为约2.0v的方式进行调整,但测定实际制作的表面处理钢板1的镍
‑
钴
‑
铁扩散层12的情况下,强度(intensity)的最大值有时不成为2.0v,但如上述,求出各测定点处的各元素的强度比作为各元素的含有比率是没有问题的。
63.而且,本实施方式中,使如此算出的co浓度梯度δp
co
为33质量%/0.1μm以下,由此,以镍
‑
钴
‑
铁扩散层12成为内表面的方式将表面处理钢板1形成电池容器的情况下,可以使得到的电池为内阻值低、电池特性优异者,且也可以成为对电解液的耐腐蚀性优异者,也能抑制经时后电池特性的降低。
64.即,以往已知的是,对于电池容器中使用的表面处理钢板1,以在表面形成铁
‑
镍扩散层,且该铁
‑
镍扩散层成为内表面的方式形成电池容器,从而使铁在电池容器内表面露出,由此,与不使铁露出的情况相比,可以使得到的电池的电池特性优异。然而,电池容器内表面处的铁的露出量如果过多,则伴随于此,电池容器内表面处的镍的存在比率降低,作为电池历经长时间地保管乃至使用的情况下,铁会向电解液溶出,由于铁的溶出而产生的气体会导致电池内部的内压上升,有产生由于内压的上升而电解液会从密封部漏液的不良情况的担心。另外,电池容器内表面处的镍的存在比率降低,从而还有作为电池容器成型前的板、电池容器保管时的对大气的防锈性降低的担心。
65.另外,以往,对于电池容器中使用的表面处理钢板,还已知有如下方法:以在表面形成镍
‑
钴合金层,且该镍
‑
钴合金层成为内表面的方式形成电池容器。上述情况下,已知的是,通过增加镍
‑
钴合金层中的钴的含有比率,从而电池特性改善。然而,如果增加镍
‑
钴合金层中的钴的含量,则通过单纯地钴的含量的增加而导致钴变得容易从电池容器内表面溶出,且随着钴的含量的增加,镍的含有比率会减少,因此,不与镍合金化的钴的量会增加,由此,也存在钴会变得容易溶出的问题。
66.即,以往已知的是,通过在电池容器内表面形成铁
‑
镍扩散层、镍
‑
钴合金层,且增加这些层中的铁、钴的含有比率,可以改善得到的电池的电池特性,但上述情况下,随着含有铁、钴,会降低镍的含有比率,因此,由此存在防锈性、对电解液的耐腐蚀性会降低的问题。
67.与此相对,根据本实施方式,使上述镍
‑
钴
‑
铁扩散层12、即镍、钴和铁的三元素共存于表面处理钢板1,且控制co浓度示出最大值的深度位置d
co_max
与相对于这样的最大值co浓度示出15%的值的深度位置d
co_15%
之间的、co浓度梯度δp
co
为上述范围,从而即使在使有利于防锈性、对电解液的耐腐蚀性的改善的镍的含有比率较低的情况下,也可以确保使铁适度地在电池容器内表面露出来改善电池特性的效果,且可以使对电解液的耐腐蚀性也优异,经时后也能抑制电池特性的降低。
68.特别是本发明人等发现:对于电解液的耐腐蚀性不仅由镍
‑
钴
‑
铁的表面的组成比率、镍和钴的含量确定。更具体而言,发现如下情况作为新的课题:在镍
‑
钴
‑
铁扩散层中,根据制造条件而钴的分布方式变得不同,进而,根据制造条件,钴不在镍
‑
钴
‑
铁扩散层的厚度方向的整体扩展,而在厚度方向上部分地形成钴浓度高的区域等,从而有时成为钴浓度的梯度变得急剧的方式,而且这样的情况下,有即使镍
‑
钴
‑
铁扩散层表面处的钴浓度低,对于电解液的耐腐蚀性也容易变差的倾向。特别是,这样的分布方式在钴沿厚度方向无法充分扩散时容易产生,进而,热处理前的镀层表面的钴浓度高时也容易产生,特别是热处理前在
钢板上具有镀钴层时容易产生。可知,这样的现象大概是由于钴与镍相比不易扩散而产生的,因此可知,这样的情况下,需要通过使成为基材的钢板中所含的铁充分扩散,从而使钴浓度的梯度缓和。即,发现:通过形成镍
‑
钴
‑
铁扩散层,从而为了兼顾电池特性的改善和对于电解液的耐腐蚀性,需要适当组合镀层构成/镀层附着量/热处理条件,由此,使钴浓度的梯度处于特定的范围,特别是作为容易控制镍附着量和钴附着量的总附着量的制造方法,选择形成镀镍层和镀钴层后通过热处理形成镍
‑
钴
‑
铁扩散层的制造方法的情况下,必须注意使得充分降低钴浓度的梯度,根据这样的观点,着眼于co浓度梯度δp
co
,至此完成了本发明。
69.另外,根据本实施方式,通过使co浓度梯度δp
co
为33质量%/0.1μm以下,从而如上述可以成为低的内阻值、对于电解液的耐腐蚀性优异,此外,还可以较低地抑制经时的色调变化,由此,可以抑制变色所导致的制品性的降低。
70.co浓度梯度δp
co
只要为33质量%/0.1μm以下即可,优选30质量%/0.1μm以下、更优选27质量%/0.1μm以下、进一步优选24质量%/0.1μm以下。另外,co浓度梯度δp
co
的下限没有特别限定,优选0.1质量%/0.1μm以上、更优选2质量%/0.1μm以上。需要说明的是,本实施方式中,将co浓度梯度δp
co
的单位用“质量%/0.1μm”表示,即,用每0.1μm的质量%的变化率表示。
71.另外,本实施方式中,镍
‑
钴
‑
铁中的铁优选钢板的铁进行了扩散。钢板的铁扩散的情况下,fe浓度从co浓度的成为最大值的蚀刻深度向钢板单调地增加。需要说明的是,此处,单调地增加是指,在中途浓度不转变为减少,增加率可以不恒定。
72.另外,本实施方式中,优选使表面处理钢板1的co浓度梯度δp
co
为上述范围,此外,ni浓度梯度δp
ni
被控制为15质量%/μm以上。即,对于表面处理钢板1,通过高频辉光放电发射光谱分析法、与上述同样地进行测定,从而求出镍
‑
钴
‑
铁扩散层12的各深度位置处的、ni浓度、co浓度和fe浓度时,将ni浓度示出最大值的深度位置设为d
ni_max
,将比深度位置d
ni_max
还靠近钢板11侧、且ni浓度相对于该最大值示出15%的值的深度位置作为d
ni_15%
的情况下,从深度位置d
ni_max
至深度位置d
ni_15%
为止之间的、ni浓度梯度δp
ni
优选被控制为15质量%/μm以上。
73.此处,ni浓度梯度δp
ni
可以与上述co浓度梯度δp
co
同样的求出,说明其具体方法时,如以下所述。即,如图6的(b)所示,将ni浓度示出最大值的点f
ni_max
所对应的深度位置设为d
ni_max
,将比这样的点f
ni_max
还靠近钢板11侧(即,深度较深的方向)、且浓度相对于在点f
ni_max
(深度位置d
ni_max
)所示的ni浓度的最大值示出15%的值的点f
ni_15%
所对应的深度位置设为d
ni_15%
的情况下,算出从深度位置d
ni_max
至深度位置d
ni_15%
为止之间的ni浓度的变化率,从而可以求出ni浓度梯度δp
ni
。需要说明的是,如图6的(b)所示,ni浓度的减少比率不恒定,因此,本实施方式中,将基于深度位置d
ni_max
与深度位置d
ni_15%
这2点处的ni浓度而测定的ni浓度的变化率作为ni浓度梯度δp
ni
。即,可以以“ni浓度梯度δp
ni
(质量%/μm)={深度位置d
ni_max
处的ni浓度(质量%)
‑
深度位置d
ni_15%
处的ni浓度(质量%)}/|深度位置d
ni_max
处的深度(μm)
‑
深度位置d
ni_15%
处的深度(μm)|”算出。
74.ni浓度梯度δp
ni
优选15质量%/μm以上、更优选17质量%/μm以上、进一步优选18质量%/μm以上、特别优选20质量%/μm以上。另外,ni浓度梯度δp
ni
的上限没有特别限定,优选90质量%/μm以下、更优选80%以下、进一步优选50质量%/μm以下。需要说明的是,本
实施方式中,关于ni浓度梯度δp
ni
的单位,以“质量%/μm”、即、以每1μm的质量%的变化率表示,例如,ni浓度梯度δp
ni
为30质量%/μm的情况下,将深度位置d
ni_max
(点f
ni_max
)作为顶点,向深度较深的方向逐渐推进测定直至深度位置d
ni_15%
(点f
ni_15%
)时,示出每1μm,以30质量%的比率(每0.1μm,为3质量%的比率),ni浓度减少。
75.另外,本实施方式中,对于表面处理钢板1,通过高频辉光放电发射光谱分析法,与上述同样地进行测定,从而求出ni浓度、co浓度和fe浓度时,将镍
‑
钴
‑
铁扩散层12中的ni浓度相对于最大值成为0.5%的深度位置中、位于表面侧的深度位置设为d
ni_0.5%
的情况下,优选使该深度位置d
ni_0.5%
处的、ni浓度p
ni
(d
ni_0.5%
)、co浓度p
co
(d
ni_0.5%
)、fe浓度p
fe
(d
ni_0.5%
)为特定的范围,由此,将表面处理钢板1用作使用强碱性的电解液的电池的电池容器时的电池特性更优异,进而可以进一步减少经时后的电池特性的降低。
76.此处,如上述,图5的(b)所示的图示出蚀刻深度方向上的、ni强度、co强度和fe强度的变化,图5的(b)所示的图所示的ni强度、co强度和fe强度可以直接换算为ni的质量、co的质量和fe的质量。因此,本实施方式中,基于这样的ni强度、co强度和fe强度的图,可以通过以下中说明的方法求出镍
‑
钴
‑
铁扩散层12中的ni强度相对于最大值成为0.5%的深度位置d
ni_0.5%
处的、ni浓度p
ni
(d
ni_0.5%
)、co浓度p
co
(d
ni_0.5%
)、和fe浓度p
fe
(d
ni_0.5%
),本实施方式中,适合使这些为后述的范围。
77.以下,对ni浓度p
ni
(d
ni_0.5%
)、co浓度p
co
(d
ni_0.5%
)、和fe浓度p
fe
(d
ni_0.5%
)的测定方法进行详述时,首先,如图5的(b)所示,图5的(b)的实施例1的表面处理钢板1在表层部分(蚀刻深度0~2.5μm左右的区域)中存在有ni、co和fe共存的镍
‑
钴
‑
铁扩散层12。该镍
‑
钴
‑
铁扩散层12如上述,例如可以通过在钢板11的表面依次形成镀镍层和镀钴层,之后,在特定的条件下实施热处理而形成,通过热处理,钢板11中的铁变得热扩散直至最表面。然后,对于这样的镍
‑
钴
‑
铁扩散层12,提取ni强度的最大值,特定相对于提取出的最大值成为0.5%的强度的深度位置作为深度位置d
ni_0.5%
。需要说明的是,相对于最大值成为0.5%的强度的深度位置存在有多个的情况下,特定它们中的、最接近于镍
‑
钴
‑
铁扩散层12的表面的位置作为深度位置d
ni_0.5%
。具体而言,图5的(b)的图中,ni强度的最大值位于蚀刻深度位置0.47μm附近,其强度为约1.36v。因此,相对于ni强度的最大值(1.36v),0.5%的强度为0.00679v,根据作为部分放大了图5的(b)所示的图的图的、图5的(c)所示的图,ni强度成为0.00679v的深度位置d
ni_0.5%
的蚀刻深度可以特定为0.055μm附近。但是,图5的(b)、图5(c)的所示的实施例1中,实际上,每约0.00465μm地设定基于测定的数据的收集间隔,因此,将最接近于0.5%的强度的值的深度位置作为相对于ni强度的最大值成为0.5%的强度的特定深度位置d
ni_0.5%
(图5的(c)所示的实施例1中,蚀刻深度为最接近于0.0558μm),但本发明人等进行了研究,结果深度位置0.055μm处的各元素的强度比率与深度位置0.0558μm处的各元素的强度比率相同。而且,可以依据上述方法算出该深度位置d
ni_0.5%
处的、ni浓度p
ni
(d
ni_0.5%
)、co浓度p
co
(d
ni_0.5%
)、和fe浓度p
fe
(d
ni_0.5%
)。需要说明的是,本实施方式中,着眼于深度位置d
ni_0.5%
处的、ni浓度p
ni
(d
ni_0.5%
)、co浓度p
co
(d
ni_0.5%
)、和fe浓度p
fe
(d
ni_0.5%
)是由于,可以判断深度位置d
ni_0.5%
处的、这些浓度表示镍
‑
钴
‑
铁扩散层12的表层(最表层和最表层的附近)中的、浓度比率。本发明人等发现:用高频辉光放电发射光谱分析装置对本实施方式的具有镍
‑
钴
‑
铁扩散层的表面处理钢板进行分析时,在测定开始点得到的强度由于表面粗糙度的影响等而不稳定,因此,不稳定,另一方面,通过进行蚀刻直至ni强度相对于
最大值成为0.5%的强度的深度,从而可以不依赖于测定对象地稳定地得到某种程度的强度。如上述,本实施方式中,ni强度相对于最大值成为0.5%的强度的点的蚀刻深度为0.01~0.1μm,为镍
‑
钴
‑
铁扩散层的最表层和最表层的附近。即,可以说ni浓度p
ni
(d
ni_0.5%
)、co浓度p
co
(d
ni_0.5%
)和fe浓度p
fe
(d
ni_0.5%
)实质上表示镍
‑
钴
‑
铁扩散层12的最表面中的、ni浓度、co浓度和fe浓度。
78.而且,本实施方式中,出于可以进一步改善经时后的电池特性的观点,深度位置d
ni_0.5%
处的、co浓度p
co
(d
ni_0.5%
)优选5质量%以上、更优选12质量%以上、进一步优选16质量%以上、特别优选20质量%以上。出于抑制使用表面处理钢板1作为电池容器时的钴的溶出从而可以抑制耐腐蚀性的降低的观点,co浓度p
co
(d
ni_0.5%
)的上限优选65质量%以下、更优选55质量%以下、进一步优选39质量%以下、特别优选30质量%以下。
79.另外,出于可以进一步提高得到的电池中的电池特性的观点,深度位置d
ni_0.5%
处的、fe浓度p
fe
(d
ni_0.5%
)优选15质量%以上、更优选20质量%以上、进一步优选25质量%以上、特别优选30质量%以上。出于抑制使用表面处理钢板1作为电池容器时的铁的溶出从而可以抑制耐腐蚀性的降低的观点,fe浓度p
fe
(d
ni_0.5%
)的下限优选90质量%以下、更优选85质量%以下、进一步优选75质量%以下、特别优选70质量%以下。
80.进而,本实施方式中,出于使用表面处理钢板1作为电池容器的情况下可以抑制接触电阻的增大的观点、和电池特性改善的观点,深度位置d
ni_0.5%
处的、ni浓度p
ni
(d
ni_0.5%
)优选70质量%以下、更优选60质量%以下、进一步优选55质量%以下、特别优选50质量%以下。出于使用表面处理钢板1作为电池容器的情况下可以更适当地抑制钴和铁的溶出的观点,ni浓度p
ni
(d
ni_0.5%
)的下限优选5质量%以上、更优选7质量%以上、进一步优选10质量%以上、特别优选12质量%以上。
81.另外,本实施方式的表面处理钢板1中,fe浓度p
fe
(d
ni_0.5%
)相对于co浓度p
co
(d
ni_0.5%
)之比r
fe/co
(p
fe
(d
ni_0.5%
)/p
co
(d
ni_0.5%
))的下限优选0.5以上、更优选0.8以上、进一步优选1.0以上,上限优选20以下、更优选14以下、进一步优选8.0以下。通过使比r
fe/co
为上述范围,从而可以使改善得到的电池的电池特性的效果与改善对于电解液的耐腐蚀性的效果更高度地均衡。
82.另外,可以进一步改善初始的电池特性的观点上,优选使fe浓度p
fe
(d
ni_0.5%
)为55质量%以上,更优选为65质量%以上。该情况下,为了抑制向电解液的溶出,此外co浓度p
co
(d
ni_0.5%
)优选为5质量%以上,后述的镍
‑
钴
‑
铁扩散层12中的钴含量优选为0.2g/m2以上,进而,镍
‑
钴
‑
铁扩散层12中的镍和钴的总计含量优选为1.6g/m2以上。此时,出于经时后的电池特性改善的观点,镍
‑
钴
‑
铁扩散层12中的钴含量更优选为0.5g/m2以上、进一步优选为0.7g/m2以上。通过使钴含量为上述值,从而不仅表层的co含有比率而且在扩散层中含有恒定量的钴,从而可以使经时后的电池特性优异。
83.另外,本实施方式中,如图7所示的表面处理钢板1a那样,在钢板11与镍
‑
钴
‑
铁扩散层12之间可以还具备铁
‑
镍扩散层15。由此,将表面处理钢板1a用作电池容器的情况下,可以进一步改善对电解液的耐腐蚀性。
84.需要说明的是,本实施方式的表面处理钢板1a中,通过如下的方法,可以确认铁
‑
镍扩散层15的存在。即,利用与上述的图5的(b)同样的方法,对于表面处理钢板1a,通过高频辉光放电发射光谱分析法,从镍
‑
钴
‑
铁扩散层12的表面向钢板11沿深度方向连续地测定
ni强度、co强度和fe强度时,将从镍
‑
钴
‑
铁扩散层12的表面朝深度方向测定的co强度达到其最大值后相对于该最大值成为15%的强度的深度作为起点,存在有从镍
‑
钴
‑
铁扩散层12的表面朝深度方向测定的ni强度达到其最大值后相对于该最大值成为15%的强度为止的深度的区域的情况下,可以判断这样的深度区域为不含钴的铁和镍所形成的扩散层、即、铁
‑
镍扩散层,上述情况下,可以判断存在有铁
‑
镍扩散层。需要说明的是,基于高频辉光放电发射光谱分析装置的测定中随着蚀刻推进,来自蚀刻的地点的侧壁的元素信息变得容易进入,存在于表层的元素容易以噪声被检测,因此,在除表层和表层附近以外的、比其还充分深的深度处,相对于各元素的强度的最大值成为15%以下的强度的情况下,通常可以视为该元素基本不存在。
85.本实施方式中,关于镍
‑
钴
‑
铁扩散层12中的钴的含量,对于下限,优选0.2g/m2以上,从进一步改善电池特性的观点出发,更优选0.5g/m2以上、进一步优选0.7g/m2以上。另外,从抑制来自扩散层的钴溶出的过剩的溶出的观点出发,钴的含量的上限优选5.0g/m2以下、更优选3.0g/m2以下、进一步优选2.0g/m2以下。
86.对于形成铁
‑
镍扩散层15时的、镍
‑
钴
‑
铁扩散层12和铁
‑
镍扩散层15中所含的镍的总计含量的下限,从改善耐腐蚀性的观点出发,优选1.0g/m2以上、更优选1.3g/m2以上、进一步优选1.6g/m2以上。对于镍
‑
钴
‑
铁扩散层12和铁
‑
镍扩散层15中所含的镍的总计含量的上限,从存在如果过厚则铁露出变困难的担心、无法形成稳定的比率的担心的方面出发,优选12.5g/m2以下、更优选9.5g/m2以下、进一步优选8.5g/m2以下、特别优选7.0g/m2以下。
87.另外,对于未形成铁
‑
镍扩散层15时的、镍
‑
钴
‑
铁扩散层12中的镍的含量的下限,从改善耐腐蚀性的观点出发,优选0.2g/m2以上、更优选0.5g/m2以上、进一步优选0.7g/m2以上。对于未形成铁
‑
镍扩散层15时的、镍
‑
钴
‑
铁扩散层12中的镍的含量的上限,从存在如果过厚则铁露出变困难的担心、无法形成稳定的比率的担心的方面出发,优选11.3g/m2以下、更优选9.5g/m2以下、进一步优选8.5g/m2以下、特别优选7.0g/m2以下。
88.关于镍
‑
钴
‑
铁扩散层12中的镍和钴的总计含量(形成铁
‑
镍扩散层15的情况下,为镍
‑
钴
‑
铁扩散层12和铁
‑
镍扩散层15中所含的镍和钴的总计量),对于下限,从抑制来自铁的溶出的观点出发,优选1.6g/m2以上、更优选2.5g/m2以上、进一步优选3.0g/m2以上、特别优选3.5g/m2以上。对于镍和钴的总计含量的上限,从存在如果过厚则铁露出变困难的担心、无法形成稳定的比率的担心的方面出发,优选14.0g/m2以下、更优选10.0g/m2以下、进一步优选9.0g/m2以下、特别优选7.5g/m2以下。
89.需要说明的是,上述镍的含量和钴的含量例如可以通过对于表面处理钢板1、1a进行荧光x射线分析,基于预先求出的标准曲线,测定镍和钴的各自的附着量,从而求出。
90.需要说明的是,测定上述附着量时,也可以进行基于荧光x射线分析的半定量分析(相对于任意元素为组成比率的算出),但x射线的侵入深度为10μm以上,因此,镍
‑
钴
‑
铁扩散层12的镍和钴的含量为14.0g/m2以下的情况下,即使从最表层测定,也会成为包含基材的铁在内的比率。例如,对于后述的实施例1的表面处理钢板(通过高频辉光放电发射光谱分析法求出的值为ni浓度p
ni
(d
ni_0.5%
)=23.50质量%、co浓度p
co
(d
ni_0.5%
)=15.14质量%、fe浓度p
fe
(d
ni_0.5%
)=61.37质量%的表面处理钢板)进行荧光x射线分析时,镍、钴、铁的比率分别成为13.6质量%、5.6质量%、80.8质量%,基于荧光x射线分析的测定结果变得不同于基于高频辉光放电发射光谱分析法的测定结果。因此,特别是使铁露出直至表层的情况
下,由镀覆附着量、荧光x射线分析算出比率的情况、与以高频辉光放电发射光谱分析分析表层(最表层和最表层的附近)的比率的情况变得不同。与此相对,根据高频辉光放电发射光谱分析,可以适当分析表层(最表层和最表层的附近)的比率。
91.本实施方式的表面处理钢板1、1a如以上构成。
92.对于本实施方式的表面处理钢板1、1a,通过深拉拔加工法、拉拔减薄加工法(di加工法)、拉拔拉伸加工法(dtr加工法)、或拉拔加工后组合使用拉伸加工与减薄加工的加工法等,以镍
‑
钴
‑
铁扩散层12成为容器内表面侧的方式,成型加工为图1、2所示的碱性电池2的正极罐21、其他电池的电池容器等而使用。
93.本实施方式的电池容器是使用上述本实施方式的表面处理钢板1、1a而成的,因此,形成电池的情况下,可以使内阻值低、电池特性优异,且可以使对强碱性的电解液的耐腐蚀性也优异,经时后也能抑制电池特性的降低,可以适合作为使用强碱性的电解液的电池的电池容器利用。需要说明的是,上述例子中,示出了将本实施方式的表面处理钢板1、1a作为碱性电池的构件的例子,但不限定于碱性电池,本实施方式的表面处理钢板1、1a可以适合作为使用强碱性的电解液的电池的电池容器利用。特别是,本实施方式的电池容器可以适合作为具备使在电池内部产生的气体释放的机构的电池的电池容器使用。这是由于,具备这样的气体释放机构时,从形成于本实施方式的电池容器内表面侧的镍
‑
钴
‑
铁扩散层12极微量地溶出钴、铁,由此会产生微量的气体的情况下,也可以适当地释放所产生的气体。
94.<表面处理钢板的制造方法>
95.接着,对本实施方式的表面处理钢板1的制造方法进行说明。
96.首先,准备钢板11,对钢板11实施镀镍,从而如图4所示那样,在钢板11的成为电池容器内表面的面形成镍镀层13。需要说明的是,镍镀层13不仅形成于钢板11的成为电池容器内表面的面,优选还形成于相反的面。在钢板11的两面形成镍镀层13时,在钢板11中的成为电池容器的内表面的面、与成为电池容器的外表面的面,使用各自组成的镀浴,可以分别形成组成、表面粗糙度等不同的镍镀层13,从改善制造效率的观点出发,可以在钢板11的两面用相同的镀浴以1个工序形成镍镀层13。
97.作为用于形成镍镀层13的镀镍浴,没有特别限定,可以利用电镀镍中通常使用的镀浴、即、瓦特浴、氨基磺酸浴、氟化硼浴、氯化物浴、柠檬酸浴等。例如,可以使用硫酸镍200~350g/l、氯化镍20~60g/l、硼酸10~50g/l的浴组成者作为瓦特浴,在ph3.0~4.8(优选ph3.6~4.6)、浴温50~70℃下、电流密度0.5~60a/dm2(优选1~40a/dm2)的条件下形成镍镀层13。
98.镍镀层13中所含的镍的含量只要为12.5g/m2以下即可,优选10.0g/m2以下、更优选9.0g/m2以下、进一步优选8.8g/m2以下。需要说明的是,镍的含量可以如下求出:对于形成有镍镀层13的钢板11,进行荧光x射线分析,从而测定构成镍镀层13的镍原子的附着量,由此可以求出。镍镀层13中所含的镍的含量的下限没有特别限定,优选0.2g/m2以上、更优选0.4g/m2以上、进一步优选0.8g/m2以上、进一步更优选1.2g/m2以上,从可以进一步提高耐腐蚀性的观点出发,特别优选1.6g/m2以上。通过使镍镀层13中所含的镍的含量为上述范围,从而如后述,在镍镀层13上形成镀钴层14,进一步进行热处理,从而形成镍
‑
钴
‑
铁扩散层12,此时,通过热处理构成钢板11的铁经过镍镀层13可以更良好地热扩散至镀钴层14的表
面,由此,可以更良好地进行镍
‑
钴
‑
铁扩散层12的形成。
99.接着,对于形成有镍镀层13的钢板11,实施镀钴,从而形成镀钴层14。
100.作为用于形成镀钴层14的镀钴浴,没有特别限定,使用硫酸钴:200~300g/l、氯化钴:50~150g/l、氯化钠:10~50g/l、硼酸10~60g/l的浴组成的镀钴浴,在ph:2~5、浴温:40~80℃、电流密度:1~40a/dm2的条件下可以形成。
101.镀钴层14中所含的钴的含量的下限没有特别限定,优选0.2g/m2以上、更优选0.4g/m2以上、进一步优选0.6g/m2以上、进一步更优选0.8g/m2以上,出于可以进一步提高耐腐蚀性的观点,特别优选1.0g/m2以上。上限没有特别限定,出于抑制自扩散层的钴溶出的过剩的溶出的观点,优选5.0g/m2以下、更优选3.0g/m2以下、更优选2.0g/m2以下。通过使镀钴层14中所含的钴的含量为上述范围,从而对于形成有镀镍层13和镀钴层14的钢板11,如后述进行热处理时,通过热处理构成钢板11的铁经过镀镍层13可以良好地热扩散直至镀钴层14的表面,由此,可以更良好地进行镍
‑
钴
‑
铁扩散层12的形成。
102.接着,对于形成有镀镍层13和镀钴层14的钢板11,进行热处理,从而使构成钢板11的铁与构成镀镍层13的镍与构成镀钴层14的镍和钴分别相互热扩散,形成镍
‑
钴
‑
铁扩散层12。由此,如图3所示,可以得到在钢板11上形成有镍
‑
钴
‑
铁扩散层12的表面处理钢板1。或者,根据镀镍层13中所含的镍的含量、镀钴层14中所含的镍和钴的总计含量、热处理的条件等,如图7所示,可以得到在钢板11与镍
‑
钴
‑
铁扩散层12之间形成有铁
‑
镍扩散层15的表面处理钢板1a。
103.热处理的条件可以根据镀镍层13中所含的镍的含量、镀钴层14中所含的镍和钴的总计含量而适宜选择,亦即,可以以温度和时间的组合选择提供仅钢板的铁充分扩散的热量的热处理条件。例如,连续退火中,热处理温度只要为480~900℃即可,镍和钴的总计含量为2.7g/m2以上时,优选650~850℃、更优选680~840℃。另外,热处理中的均热时间(保持上述热处理温度的时间)优选10秒~2分钟、更优选10秒~1.5分钟、进一步优选20~70秒。提供仅钢板的铁充分扩散的热量的热处理条件例如是指,4.5g/m2以上的情况下,优选以700℃以上且低于750℃保持1分钟以上,或以750℃~840℃保持20秒~1.5分钟。另外,箱式退火中,热处理温度优选450~680℃、更优选500℃~650℃。另外,箱式退火中的均热时间可以根据镍和钴的总计含量和热处理温度在1~24小时的范围内适宜选择,优选3~20小时、更优选6~18小时。作为热扩散处理的方法,可以为连续退火和箱式退火,均可,但从连续钢带中的生产率良好的观点出发,优选连续退火,从使铁进一步露出、实现电池特性的改善的观点出发,优选箱式退火。特别是,连续钢带的制造中,通常以将钢带形成卷状的状态进行箱式退火,结果基于箱式退火的热处理温度过高时,钴从形成于表面的镍
‑
钴
‑
铁扩散层12会向与其接触的背面扩散,存在品质不稳定的问题,此外,有镍
‑
钴
‑
铁扩散层12中的、ni浓度梯度δp
ni
的值会过度变低的倾向。
104.如以上,可以制造本实施方式的表面处理钢板1、1a。特别是,本实施方式中,对于依次形成有镀镍层13和镀钴层14的钢板11,进行热处理,从而使构成钢板11的铁与构成镀镍层13的镍与镀钴层14分别相互热扩散,形成镍
‑
钴
‑
铁扩散层12,例如,与形成镍
‑
钴合金镀层代替镀钴层14的情况等相比,可以容易地控制以连续钢带进行制造时的、得到的镍
‑
钴
‑
铁扩散层12中的镍量、钴量为期望的范围,由此,可以实现优异的生产率。
105.根据本实施方式的制造方法,将镀镍层13中所含的镍的含量、镀钴层14中所含的
镍和钴的总计含量、和热处理的条件分别控制为上述范围,从而可以适合地得到形成的镍
‑
钴
‑
铁扩散层12中的、co浓度梯度δp
co
被控制为33质量%/0.1μm以下者。而且,由此,根据本实施方式的制造方法,将得到的本实施方式的表面处理钢板1、1a用作电池容器的情况下,可以使得到的电池为内阻值低、电池特性优异者,且可以使对强碱性的电解液的耐腐蚀性也优异,经时后也能抑制电池特性的降低,可以适合作为使用强碱性的电解液的电池的电池容器利用。特别是,形成于容器内表面侧的镍
‑
钴
‑
铁扩散层12中,由于钴、铁的溶出而产生微量的气体的情况下,也可以适当地释放所产生的气体,因此,可以适合作为具备使在电池内部产生的气体释放的机构的电池的电池容器利用。尤其镀镍后进行镀钴的热处理的制造方法中,基材侧的co容易扩散,在接近于表面的区域中,co容易残留,因此,结果作为co分布,容易形成co向接近于表面的区域集中的区域,因此,镍
‑
钴
‑
铁扩散层12中的、co浓度的半值宽度w
co
变得较小至0.1~0.35μm,但通过使co浓度梯度为特定的范围,从而可以进一步提高内阻的减少效果、对于强碱性的电解液的耐腐蚀性的改善效果。需要说明的是,co浓度的半值宽度w
co
如变更了图6的(a)的图的横轴的比例尺的图即图6的(c)所示,算出相对于co浓度示出最大值的点f
co_max
处的co浓度,示出50%的co浓度的深度位置d
co_50%_ini
与深度位置d
co_50%_end
之差(即,|深度位置d
co_50%_ini
处的深度(μm)
‑
深度位置d
co_50%_end
处的深度(μm)|),从而可以求出。
106.需要说明的是,上述中,示例了在钢板11的表面依次形成镀镍层13和镀钴层14后,实施热处理,从而使各层中所含的铁、镍和钴分别进行热扩散,形成镍
‑
钴
‑
铁扩散层12的方法,但代替这样的方法,也可以采用:在钢板11的表面仅直接形成镍
‑
钴合金镀层14’而不形成镍镀层13后,实施热处理,从而使钢板11与镍
‑
钴合金镀层14’进行热扩散,形成镍
‑
钴
‑
铁扩散层12的方法。
107.以下,对仅形成镍
‑
钴合金镀层14’而不形成镍镀层13后,实施热处理,从而形成镍
‑
钴
‑
铁扩散层12时的、表面处理钢板1的制造方法进行说明。
108.作为用于形成镍
‑
钴合金镀层14’的镍
‑
钴合金镀浴,没有特别限定,优选使用以含有硫酸镍、氯化镍、硫酸钴和硼酸的瓦特浴为基础的镀浴。需要说明的是,镍
‑
钴合金镀浴中的、钴/镍比以钴/镍的摩尔比计、优选设为0.05~1.0的范围、更优选设为0.1~0.7的范围。例如,可以利用如下镀浴:使用以含有硫酸镍、氯化镍、硫酸钴和硼酸的瓦特浴为基础的镀浴的情况下,以硫酸镍:10~300g/l、氯化镍:20~60g/l、硫酸钴:10~250g/l、硼酸:10~40g/l的范围,以钴/镍比成为上述范围的方式,适宜调整各成分而成的镀浴。另外,镀镍
‑
钴合金优选设为浴温40~80℃、ph1.5~5.0、电流密度1~40a/dm2的条件。
109.镍
‑
钴合金镀层14’中所含的镍和钴的总计含量优选11.5g/m2以下、更优选10.0g/m2以下、进一步优选9.0g/m2以下、特别优选7.5g/m2以下。需要说明的是,镍
‑
钴合金镀层14’中所含的镍和钴的含量可以如下求出:对于形成有镍
‑
钴合金镀层14’的钢板11,进行荧光x射线分析,从而测定构成镍
‑
钴合金镀层14’的镍原子和钴原子的总计的附着量,由此可以求出。镍
‑
钴合金镀层14’中所含的镍和钴的总计含量的下限没有特别限定,优选1.6g/m2以上、更优选2.5g/m2以上、进一步优选3.0g/m2以上、特别优选3.5g/m2以上。通过使镍
‑
钴合金镀层14’中所含的镍和钴的总计含量为上述范围,从而对于形成有镍
‑
钴合金镀层14’的钢板11,如后述进行热处理时,通过热处理而构成钢板11的铁可以更良好地热扩散至镍
‑
钴合金镀层14’的表面,由此,可以更良好地进行镍
‑
钴
‑
铁扩散层12的形成。
110.接着,对于形成有镍
‑
钴合金镀层14’的钢板11,进行热处理,从而使构成钢板11的铁、与构成镍
‑
钴合金镀层14’的镍和钴相互进行热扩散,形成镍
‑
钴
‑
铁扩散层12。由此,如图3所示那样,可以得到在钢板11上形成有镍
‑
钴
‑
铁扩散层12的表面处理钢板1。需要说明的是,本制造方法中,其制造方法的性质上,不适于形成如图6所示的表面处理钢板1a那样的、在钢板11与镍
‑
钴
‑
铁扩散层12之间还具备铁
‑
镍扩散层15的构成。
111.热处理的条件可以根据镍
‑
钴合金镀层14’中所含的镍和钴的总计含量而适宜选择,热处理温度优选480~900℃、更优选500~800℃、进一步优选520~750℃。另外,热处理中的均热时间(保持上述热处理温度的时间)优选3秒~2分钟、更优选10秒~1.5分钟、进一步优选20~60秒。作为热扩散处理的方法,可以为连续退火和箱型退火中的任意者,从容易将热处理温度和热处理时间调整为上述范围的观点出发,优选连续退火。
112.根据上述的制造方法,通过将镍
‑
钴合金镀层14中所含的镍和钴的总计含量、和热处理的条件分别控制为上述范围,从而可以将形成的镍
‑
钴
‑
铁扩散层12制成co浓度梯度被控制为33%/0.1μm以下者。由此,将得到的本实施方式的表面处理钢板1用作电池容器时,可以使得到的电池形成内阻值低、电池特性优异者,且可以使对强碱性的电解液的耐腐蚀性也优异,经时后也能抑制电池特性的降低,可以适合作为使用强碱性的电解液的电池的电池容器利用。特别是,形成于容器内表面侧的镍
‑
钴
‑
铁扩散层12中,由于钴、铁的溶出而产生微量的气体的情况下,可以适当地释放所产生的气体,因此,可以适合作为具备使在电池内部产生的气体释放的机构的电池的电池容器利用。
113.或者,也可以采用与上述同样地,形成镀镍层13后,对于形成有镀镍层13的钢板11,实施镍
‑
钴合金镀覆,形成镍
‑
钴合金镀层14”,对其进行热处理的方法。
114.作为用于形成镍
‑
钴合金镀层14”的镍
‑
钴合金镀浴,没有特别限定,优选使用将含有硫酸镍、氯化镍、硫酸钴和硼酸的瓦特浴作为基础的镀浴。需要说明的是,镍
‑
钴合金镀浴中的、钴/镍比以钴/镍的摩尔比计、优选设为0.05~1.0的范围,更优选设为0.1~0.7的范围。例如,使用将含有硫酸镍、氯化镍、硫酸钴和硼酸的瓦特浴作为基础的镀浴的情况下,在硫酸镍:10~300g/l、氯化镍:20~60g/l、硫酸钴:10~250g/l、硼酸:10~40g/l的范围内,可以使用以钴/镍比成为上述范围的方式,适宜调整各成分而成的镀浴。另外,镍
‑
钴合金镀覆优选设为浴温40~80℃、ph1.5~5.0、电流密度1~40a/dm2的条件。
115.镍
‑
钴合金镀层14”中所含的镍和钴的总计含量只要为7.5g/m2以下即可,优选4.0g/m2以下、更优选3.0g/m2以下。需要说明的是,镍
‑
钴合金镀层14”中所含的镍和钴的含量可以如下求出:对于形成有镀镍层13和镍
‑
钴合金镀层14”的钢板11,进行荧光x射线分析,从而测定构成镀镍层13和镍
‑
钴合金镀层14”的镍原子和钴原子的总计的附着量,从得到的总计的附着量中减去上述镀镍层13中所含的镍的含量(或者,减去形成镀镍层13时的镍的附着量),从而可以求出。镍
‑
钴合金镀层14”中所含的镍和钴的总计含量的下限没有特别限定,优选0.4g/m2以上、更优选0.8g/m2以上、进一步优选1.2g/m2以上、特别优选1.6g/m2以上。通过使镍
‑
钴合金镀层14”中所含的镍和钴的总计含量为上述范围,从而对于形成有镀镍层13和镍
‑
钴合金镀层14”的钢板11,如后述进行热处理时,通过热处理,构成钢板11的铁经过镀镍层13变得可以更良好地热扩散至镍
‑
钴合金镀层14”的表面,由此,可以更良好地进行镍
‑
钴
‑
铁扩散层12的形成。
116.镍
‑
钴合金镀层14”中所含的钴的含量优选0.2g/m2以上,为了进一步改善得到的
电池的电池特性,更优选0.5g/m2以上、进一步优选0.7g/m2以上。钴的含量的上限只要不妨碍使表层的含有比率为规定的范围就没有特别限定,钴的含量如果过度变多,则有铁不易露出的担心,优选5.0g/m2以下、更优选3.0g/m2以下、进一步优选2.0g/m2以下。需要说明的是,钴的含量可以如下求出:对于形成有镀镍层13和镍
‑
钴合金镀层14”的钢板11,进行荧光x射线分析,从而测定构成镍
‑
钴合金镀层14”的钴原子的附着量,由此可以求出。通过使镍
‑
钴合金镀层14”中所含的钴的含量为上述范围,从而使用表面处理钢板1作为电池容器的情况下,可以进一步改善得到的电池的电池特性。
117.接着,对于形成有镀镍层13和镍
‑
钴合金镀层14”的钢板11,进行热处理,从而使构成钢板11的铁与构成镀镍层13的镍与构成镍
‑
钴合金镀层14”的镍和钴分别相互热扩散,形成镍
‑
钴
‑
铁扩散层12。由此,如图3所示,可以得到在钢板11上形成有镍
‑
钴
‑
铁扩散层12的表面处理钢板1。或者,根据镀镍层13中所含的镍的含量、镍
‑
钴合金镀层14”中所含的镍和钴的总计含量、热处理的条件等,如图7所示,可以得到在钢板11与镍
‑
钴
‑
铁扩散层12之间形成有铁
‑
镍扩散层15的表面处理钢板1a。
118.热处理的条件可以根据镀镍层13中所含的镍的含量、镍
‑
钴合金镀层14”中所含的镍和钴的总计含量而适宜选择,热处理温度只要为480~900℃即可,优选500~800℃、更优选520~750℃。另外,热处理中的均热时间(保持上述热处理温度的时间)优选3秒~2分钟、更优选10秒~1.5分钟、进一步优选20~60秒。作为热扩散处理的方法,可以为连续退火和箱式退火,均可,但出于容易将热处理温度和热处理时间调整为上述范围的观点,优选连续退火。需要说明的是,镍和钴的含量为11.5g/m2以下时,出于可以使铁更稳定地露出的观点,更优选热处理温度600~900℃的连续退火,进一步优选热处理温度700~830℃的连续退火。镍和钴的含量为5.4g/m2以下时,可以为热处理温度480℃以上且低于600℃的连续退火。
119.实施例
120.以下,列举实施例,对本发明更具体地进行说明,但本发明不限定于这些实施例。
121.需要说明的是,各特性的定义和评价方法如以下所述。
122.<ni量和co量>
123.通过荧光x射线分析装置(rigaku corporation制、zsx100e)测定表面处理钢板的表面,从而分别测定镍
‑
钴
‑
铁扩散层中所含的镍量和钴量(在钢板与镍
‑
钴
‑
铁扩散层之间形成有铁
‑
镍扩散层的情况下,为镍
‑
钴
‑
铁扩散层和铁
‑
镍扩散层中所含的总计的镍量和钴量)。
124.<co浓度梯度δp
co
、ni浓度梯度δp
ni
、ni浓度p
ni
(d
ni_0.5%
)、co浓度p
co
(d
ni_0.5%
)、fe浓度p
fe
(d
ni_0.5%
)>
125.对于表面处理钢板,依据上述方法,通过高频辉光放电发射光谱分析法,从镍
‑
钴
‑
铁扩散层的表面侧向钢板沿深度方向连续地测定ni强度、co强度和fe强度,基于得到的ni强度、co强度和fe强度,分别求出ni浓度、co浓度和fe浓度,基于求出的结果,求出co浓度梯度δp
co
、ni浓度梯度δp
ni
、ni浓度p
ni
(d
ni_0.5%
)、co浓度p
co
(d
ni_0.5%
)、和fe浓度p
fe
(d
ni_0.5%
)。另外,基于求出的co浓度p
co
(d
ni_0.5%
)、和fe浓度p
fe
(d
ni_0.5%
),还求出fe浓度p
fe
(d
ni_0.5%
)相对于co浓度p
co
(d
ni_0.5%
)之比r
fe/co
(p
fe
(d
ni_0.5%
)/p
co
(d
ni_0.5%
))。需要说明的是,基于高频辉光放电发射光谱分析法的测定条件如以下。
126.测定装置:marcus型高频辉光放电发光表面分析装置(株式会社堀场制作所制、型号:gd
‑
profiler2)
127.光电子增压器通路的电压(h.v.):fe为785v、ni为630v、co为720v
128.阳极直径:φ4mm
129.气体种类:ar
130.收集间隔:0.05秒
131.气体压力:600pa
132.功率:35w
133.<腐蚀电流密度>
134.切断表面处理钢板,从而制作宽度20mm、长度40mm的条状的试验片。接着,在制作好的试验片上,使测定面积为φ6mm,使其浸渍于液温为25℃的浓度10m的氢氧化钾水溶液,用电化学测定系统(北斗电工株式会社制、型号:hz
‑
5000),分别地,使用银/氯化银电极作为参比电极,使用铂作为对电极,以50mv/分钟的速度从
‑
800mv扫描至800mv进行测定。然后,基于测定结果,得到电位为100mv的时刻下的电流密度作为腐蚀电流密度。需要说明的是,腐蚀电流密度的评价中,如果腐蚀电流密度为0.025ma/cm2以下、优选0.015ma/cm2以下,则判断表面处理钢板的耐溶出性优异。
135.<接触电阻值>
136.切断表面处理钢板,从而依据jis z 2241:2011“金属材料拉伸试验方法”,制作13b号试验片。接着,对于制作好的一个试验片,用电接点模拟器(山崎精密研究所株式会社制、型号:crs
‑
1),在接触载荷:100gf的条件下进行测定,从而得到试验片的第1次的接触电阻值。接着,对测定了第1次的接触电阻值的试验片,用台式精密万能试验机(株式会社岛津制作所制、型号:ags
‑
x),在拉伸率20%的条件下进行拉伸试验后,对于得到的拉伸试验后的试验片,同样地进行测定,从而得到试验片的第2次的接触电阻值。进而,在60℃、20天的条件下,使测定了第2次的接触电阻值的试验片浸渍于浓度10m的氢氧化钾水溶液中后,从氢氧化钾水溶液中提拉,同样地进行测定,从而得到试验片的第3次的接触电阻值。需要说明的是,将测定好的接触电阻值记载于后述的表1,表1中,分别地,将第1次的接触电阻值记作“拉伸前”、第2次的接触电阻值记作“经时前”、和第3次的接触电阻值记作“经时后”。另外,表1中,记载第2次的接触电阻值与第3次的接触电阻值的差值作为“经时前后变化量”。需要说明的是,接触电阻值的评价中,“经时后”的测定值如果为12mω以下,则判断表面处理钢板可以抑制经时后的电池特性的劣化,进一步如果为10mω以下、特别是8mω以下,则判断可以进一步抑制该电池特性的劣化。
137.<基于恒温恒湿试验的色调变化>
138.对于表面处理钢板,用恒温恒湿器(制品名“lhl
‑
113”、espec corporation制),在温度55℃、湿度85%、400小时的条件下,进行恒温恒湿试验。然后,在恒温恒湿试验前后,对于表面处理钢板的形成有镍
‑
钴
‑
铁扩散层的面的表面,使用分光测色计(制品名“cm
‑
5”、konica minolta japan co.,ltd.制)进行测定,从而求出恒温恒湿试验前后的、表面处理钢板的形成有镍
‑
钴
‑
铁扩散层的面的表面的色调变化量(δl
*
)。需要说明的是,使用分光测色计测定的测定条件如下:主光源:d65、视野:10
°
、测定方法:反射、正反射光处理:sce、测定直径:φ8mm。恒温恒湿试验前后的色调变化量(δl
*
)的值越小,经时的色调变化越小,
可以判断变色所导致的制品性的降低越被抑制。需要说明的是,基于恒温恒湿试验的色调变化的评价对于实施例3、4、比较例4、6、12进行。
139.《实施例1》
140.作为金属板,准备如下钢板:其是将具有下述所示的化学组成的低碳铝镇静钢的tm轧制板(厚度0.25mm)退火而得到的。
141.c:0.04重量%、mn:0.21重量%、si:0.02重量%、p:0.012重量%、s:0.009重量%、al:0.061重量%、n:0.0036重量%、余量:fe和不可避免的杂质
142.然后,对于准备好的钢板,进行碱电解脱脂、硫酸浸渍的酸洗后,在下述条件下进行镀镍,从而形成镍的附着量为3.81g/m2的镍镀层。
143.<镀镍>
144.浴组成:硫酸镍250g/l、氯化镍45g/l、硼酸30g/l
145.ph:3.6~4.6
146.浴温:60℃
147.电流密度:20a/dm2148.接着,对于形成有镀镍层的钢板,在下述条件下进行镀钴,从而在镀镍层上形成镀钴层。需要说明的是,形成镀钴层时,设为镍和钴的总计量(还包含成为基底的镀镍层的镍量)成为表1、2所示的量的条件。
149.<镀钴>
150.镀浴的浴组成:硫酸钴250g/l、氯化钴90g/l、氯化钠20g/l、硼酸30g/lph:3.5~5.0
151.浴温:60℃
152.电流密度:10a/dm2153.接着,对于形成有镀镍层和镀钴层的钢板,在保持热处理温度800℃40秒的条件下,进行连续退火(热处理),从而形成镍
‑
钴
‑
铁扩散层,得到表面处理钢板。对于得到的表面处理钢板,依据上述方法,进行ni量、co量、co浓度梯度δp
co
、ni浓度p
ni
(d
ni_0.5%
)、co浓度p
co
(d
ni_0.5%
)、fe浓度p
fe
(d
ni_0.5%
)、腐蚀电流密度、以及接触电阻值的评价。将结果示于表1、2和图5的(b)、图6的(a)、图6的(b)。需要说明的是,图5的(b)、图6的(a)、图6的(b)为示出求出co浓度梯度δp
co
、ni浓度梯度δp
ni
、ni浓度p
ni
(d
ni_0.5%
)、co浓度p
co
(d
ni_0.5%
)、和fe浓度p
fe
(d
ni_0.5%
)时、通过高频辉光放电发射光谱分析法测定表面处理钢板的结果的图。
154.《实施例2~5》
155.变更形成镀镍层时的镍的附着量、形成镀钴层时的条件、以及进行热处理时的热处理温度和热处理方法使其分别成为表1、2所示,除此之外,与实施例1同样地制作表面处理钢板,同样地进行评价。需要说明的是,形成镀钴层时的条件设为镍和钴的总计量(还包含成为基底的镀镍层的镍量)成为表1、2所示的量的条件。将结果示于表1、2。需要说明的是,对于实施例2,作为图8的(a)~图8的(c),求出co浓度梯度δp
co
、ni浓度梯度δp
ni
、ni浓度p
ni
(d
ni_0.5%
)、co浓度p
co
(d
ni_0.5%
)、和fe浓度p
fe
(d
ni_0.5%
)时,表示示出通过高频辉光放电发射光谱分析法测定表面处理钢板的结果的图。
156.《实施例6》
157.在镀镍层上形成镍
‑
钴合金镀层代替镀钴层,以及变更进行热处理时的热处理温
度和热处理方法使其分别成为表1、2所示,除此之外,与实施例1同样地制作表面处理钢板,同样地进行评价。将结果示于表1、2。需要说明的是,镍
‑
钴合金镀层的形成条件如下述,进行镍
‑
钴合金镀覆使得镍和钴的总计量(还包含成为基底的镀镍层的镍量)成为表1、2所示的量。
158.<镍
‑
钴合金镀覆>
159.镀浴的浴组成:以钴/镍的摩尔比0.30含有硫酸镍、氯化镍、硫酸钴、氯化钴、和硼酸
160.ph:3.6~4.6
161.浴温:60℃
162.电流密度:20a/dm2163.《比较例1~3》
164.变更形成镀镍层时的镍的附着量使其成为表1所示的方面,不形成镀钴层的方面,和变更进行热处理时的热处理温度和热处理方法使其成为表1、2所示,除此之外,与实施例1同样地制作表面处理钢板,同样地进行评价。将结果示于表1。需要说明的是,比较例1~3中,未形成镀钴层,因此,荧光x射线分析中的测定中,也未检到测钴,另一方面,基于高频辉光放电发射光谱分析法的测定中,钴的发光波长接近于镍、铁的发光波长,因此,作为测定结果,有时会检测到钴。然而,比较例1~3的表面处理钢板中,未形成镀钴层,因此,表明不含有钴,由此,基于通过高频辉光放电发射光谱分析法得到的强度比的各元素的浓度的计算中,基于测定结果的co强度而计算的co浓度p
co
(d
ni_0.5%
)的值是非常小的值(2质量%以下左右),因此,判断为不含有钴,基于将ni强度和fe强度的总计设为100%时的、ni强度的比、fe强度的比,求出ni浓度p
ni
(d
ni_0.5%
)和fe浓度p
fe
(d
ni_0.5%
)。另外,比较例1~3中,也未进行比r
fe/co
的算出。
165.《比较例4》
166.未形成镀镍层,在钢板上直接形成镀钴层的方面,变更形成镀钴层时的条件使其成为表1所示的方面,未进行热处理的方面,除此之外,与实施例1同样地制作表面处理钢板,同样地进行评价。需要说明的是,形成镀钴层时的条件设为镍和钴的总计量(还包含成为基底的镀镍层的镍量)成为表1所示的量的条件。将结果示于表1。对于比较例4,腐蚀电流密度的值明显大,用作电池容器的情况下,确认了对于电解液的耐腐蚀性变差,因此,未进行接触电阻值的测定。
167.《比较例5~12》
168.变更形成镀镍层时的镍的附着量、形成镀钴层时的条件、以及进行热处理时的热处理温度和热处理方法使其分别成为表1所示,除此之外,与实施例1同样地制作表面处理钢板,同样地进行评价。需要说明的是,形成镀钴层时的条件设为镍和钴的总计量(还包含成为基底的镀镍层的镍量)成为表1所示的量的条件。将结果示于表1。对于比较例5~12,腐蚀电流密度的值明显大,用作电池容器的情况下,确认了对于电解液的耐腐蚀性变差,因此,未进行接触电阻值的测定。
169.[表1]
[0170][0171]
[表2]
[0172][0173]
如表1、2所示,形成有从深度位置d
co_max
至深度位置d
co_15%
为止之间的、co浓度梯度δp
co
被控制为33质量%/0.1μm以下的镍
‑
钴
‑
铁扩散层的表面处理钢板的腐蚀电流密度为0.03ma/cm2以下、优选0.002ma/cm2以下,经时后的接触电阻值为8mω以下,因此,确认了耐
溶出性优异、而且经时后的电池特性的劣化被抑制(实施例1~6)。需要说明的是,对于实施例1~6,进行从深度位置d
ni_max
至前述深度位置d
ni_15%
为止之间的、ni浓度梯度δp
ni
的测定,结果实施例1的ni浓度梯度δp
ni
为36.6质量%/μm,实施例2为39.8质量%/μm,实施例3为32.5质量%/μm,实施例4为21.4质量%/μm,实施例5为13.6质量%/μm,实施例6为29.1质量%/μm。另外,实施例1~6中的、co浓度的半值宽度w
co
如下:实施例1为0.23μm、实施例2为0.19μm、实施例3为0.20μm、实施例4为0.25μm、实施例5为0.53μm、实施例6为0.47μm。
[0174]
另一方面,如表1、2所示,在最表层未形成镍
‑
钴
‑
铁扩散层的情况下、co浓度梯度δp
co
超过33质量%/0.1μm的情况下,腐蚀电流密度变高,耐溶出性变差,或者,成为经时后的接触电阻值高、经时后的电池特性会恶化的结果(比较例1~12)。
[0175]
另外,基于恒温恒湿试验的色调变化量(δl
*
)如下:实施例3中,色调变化量(δl
*
):
‑
0.3,实施例4中,色调变化量(δl
*
):
‑
0.6,比较例4中,色调变化量(δl
*
):
‑
3.0,比较例6中,色调变化量(δl
*
):
‑
1.4,比较例12中,色调变化量(δl
*
):
‑
1.1,实施例3、实施例4的基于恒温恒湿试验的色调变化量(δl
*
)被抑制得较低。而且,对于实施例3、4以外的实施例1、2、5、6,也与实施例3、4同样地,认为基于恒温恒湿试验的色调变化量(δl*)被抑制得较低。
[0176]
附图标记说明
[0177]
1、1a
…
表面处理钢板
[0178]
11
…
钢板
[0179]
12
…
镍
‑
钴
‑
铁扩散层
[0180]
13
…
镀镍层
[0181]
14
…
镀钴层
[0182]
15
…
铁
‑
镍扩散层