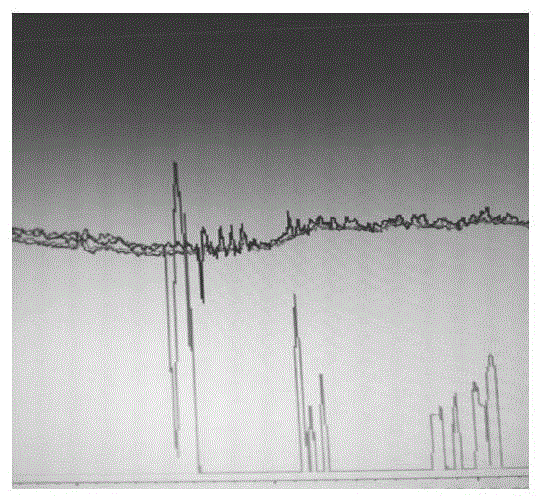
本发明属于连铸中包定径水口浇注
技术领域:
,具体是涉及一种连铸机定径水口浇注断流补救漏钢方法。
背景技术:
:目前,连铸分厂1、2号方坯连铸机,生产150x150mm断面是使用中包快速更换定径水口浇铸,生产中定径水口容易发生堵塞现象,分析原因如下:由耐火材料涂抹的中间包工作层、以及中间包内的挡渣堰,受到高温钢液侵蚀、冲刷过程中,会有颗粒较大的非金属夹杂物随着钢水卷入定径水口中,造成定径水口堵塞引起拉速下降,该情况发生于瞬间且没有预兆,特别是当该颗粒物的大小与定径水口直径相当时、会造成瞬间断流,有时断流仅持续3到4秒之后钢流又突然下来。小方坯的平均拉速是3m/min.因为定径水口断流的时候,液面自动控制系统是降低拉速的,严重的时候拉速回零。当颗粒物通过定径水口后,钢流回复正常,这时候自动拉速很小或者为0m/min,自动液面控制系统虽然反应迅速、自动快速提高拉速,但是拉矫机起步惯性太大,导致拉速提高缓慢,定径水口出钢速度正常后,结晶器浇注钢液面迅速上升把镶嵌在结晶器铜管壁上的凝固保护渣带覆盖,随着铸坯向下移动出结晶器后发生卷渣漏钢,失去控制。因此,本发明一种连铸机定径水口浇注断流补救漏钢方法的研制对于连铸中包定径水口浇注
技术领域:
来说具有重要的意义。技术实现要素:1.发明要解决的技术问题本发明的目的在于克服现有钢液液面控制技术中,浇注过程中的给定钢液液位不能变更液位,无法修改钢液液面自动控制模型,容易造成结晶器浇注钢液液面迅速上升把镶嵌在结晶器铜管壁上的凝固保护渣带覆盖,随着铸坯向下移动出结晶器后发生卷渣漏钢,失去控制等问题,提供了一种连铸机定径水口浇注断流补救漏钢方法;本发明利用引入前馈控制系统,根据实际钢液液位a与给定钢液液位a1的偏差及偏差变化率,进行模糊推理,将推理后的决策值输送给钢液拉速控制器进行运算,下调给定钢液液位以实现稳定拉速的效果,方便生产,解决瞬间无流引起的卷渣漏钢,减少了二次开浇次数,降低了职工劳动强度,降低了钢铁料消耗。2.技术方案为达到上述目的,本发明提供的技术方案为:一种连铸机定径水口浇注断流补救漏钢方法,该方法包括如下步骤:s1:使用干式料中包,中包烘烤需两个小时以上,中间包的烘烤质量直接决定着中间包的热稳定状态,从而影响到中间包开浇或快换的成功与否,对提高中间包连浇炉数,提高连铸机作业率,降低生产成本起着重要作用;同时连铸的生产节奏较快,现场的影响因素比较复杂,要求中间包具备快速烘烤的能力,烤包速度快,中间包内的气氛温度能够准确达到开浇所要求的温度。中间包在浇注过程中,特别是开浇或快换第一包中间包内温度变化稳定,具有较好的热稳定状态;s2:结晶器液位标定,预设结晶器给定钢液液位a1,固定拉速值b,固定拉速值对连铸机产量和铸坯质量都有极为重要的影响,观察结晶器内实际钢液液位a,引入前馈控制;s2:将检测到的实际钢液液位a信号与给定钢液液位a1信号进行比较;s3:计算实际钢液液位a与给定钢液液位a1的偏差及偏差变化率;s4:进行模糊推理,将推理后的决策值输送给钢液拉速控制器进行运算;s5:钢液拉速控制器计算后输出控制拉矫机的拉速值b;s6:根据拉速值b计算并快速下调给定钢液液位至a2,用拉速值b计算出匹配的钢液液位;s7:拉速值逐步恢复至b时,把给定钢液液位a2调回到a1的位置,继续进行浇铸。作为本发明更进一步的改进,所述前馈控制为预先控制,将给定钢液液位a1设定成可调节的数值。作为本发明更进一步的改进,所述钢液拉速控制器为pid控制器,所述pid控制器控制实际的钢液液位。作为本发明更进一步的改进,所述给定钢液液位a1由给定钢液控制器l控制,所述给定钢液控制器l为可操作型控制器。作为本发明更进一步的改进,所述下调给定钢液液位至a2后,用捞渣棒及时挑出镶嵌在结晶器铜管壁的渣带。3.有益效果采用本发明提供的技术方案,与现有技术相比,具有如下有益效果:(1)本发明的一种连铸机定径水口浇注断流补救漏钢方法,本发明利用引入前馈控制系统,根据实际钢液液位a与给定钢液液位a1的偏差及偏差变化率,进行模糊推理,将推理后的决策值输送给钢液拉速控制器进行运算,下调给定钢液液位以实现稳定拉速的效果,方便生产,解决瞬间无流引起的卷渣漏钢,减少了二次开浇次数,降低了职工劳动强度,降低了钢铁料消耗。(2)本发明的一种连铸机定径水口浇注断流补救漏钢方法,通过使用后,解决瞬间无流引起的卷渣漏钢。一个方坯连铸机每月一般有20次无流发生,那么漏钢或非正常停浇废品将产生约40吨,按每吨钢合格品与废品的差价1000元/吨来计算,年节约经济效益约:40吨*1000元/吨*12月=48万元/年。(3)本发明的一种连铸机定径水口浇注断流补救漏钢方法,本发明可以减少因卷渣漏钢等事故带来的设备损坏,每年节约设备维护费用约3万元;同时,通过这种方法补救成功,没有发生漏钢和溢钢停浇事故,使连铸的全流率指标大幅提高,铸坯收得率提高,安全得到保证,给生产带来顺行。(4)本发明的一种连铸机定径水口浇注断流补救漏钢方法,本发明减少了产生废钢的损失,也节约了设备维护费,合计年降本48+3=51万元/年。(5)本发明的一种连铸机定径水口浇注断流补救漏钢方法,本发明使用干式料中包,中包的干式料是一种高科技碱性不定形耐火材料,它是中间包工作衬的更新换代产品,该料以优质镁砂为主要原料,外加结合剂和添加剂,经严格的生产工艺控制加工而成。干式料中包施工时不需加水,不需搅拌,施工简便,速度快,劳动强度低;干式料中包振动施工完以后,施工体不需养护,可直接点火烘烤,施工体不会出现裂或剥落现象;干式料中包在使用过程中,耐钢水和熔渣的侵蚀,使用寿命长,可依客户须求提供不同的材料吨钢耐材消耗低;干式料中包使用完以后,工作层与永久衬不易烧结,清渣方便,翻包容易;干式料中包主要成分是mg0,它对钢水中非金属夹杂物(如a1203、si02等),有很强的吸附作用,从而净化钢液,提高钢水的质量;干式料中包对烘烤条件要求不高,它只需烘烤到150-200c即可,烘烤温度低,烘烤时间短,节能效果十分显著;使用过程无毒性气体产生,环境干净,无粉尘污染。附图说明图1为本发明一种连铸机定径水口浇注断流补救漏钢方法的流程图;图2为本发明补救前漏钢的趋势线;图3为本发明补救成功后的趋势线。示意图1中标号说明:s1:加入发热剂烘烤中包,所述发热剂采用干式料,发热剂用量高于包底,中包烘烤需两个小时以上;s2:结晶器液位标定,预设结晶器给定钢液液位a1,固定拉速值b,观察结晶器内实际钢液液位a,引入前馈控制;s2:将检测到的实际钢液液位a信号与给定钢液液位a1信号进行比较;s3:计算实际钢液液位a与给定钢液液位a1的偏差及偏差变化率;s4:进行模糊推理,将推理后的决策值输送给钢液拉速控制器进行运算;s5:钢液拉速控制器计算后输出控制拉矫机的拉速值b;s6:根据拉速值b计算并下调给定钢液液位至a2;s7:拉速值逐步恢复至b时,把给定钢液液位a2调回到a1的位置,继续进行浇铸。示意图2和图3的说明:红色是给定钢液液位的趋势线;黑色是实际钢液液位的趋势线;蓝色是自动控制状态下实际拉速趋势线。具体实施方式为进一步了解本发明的内容,结合附图和实施例对本发明作详细描述。实施例1如图1所示,本实施例的一种连铸机定径水口浇注断流补救漏钢方法,该方法包括如下步骤:s1:使用干式料中包,发热剂用量高于包底,中包烘烤需两个小时以上;中间包的烘烤质量直接决定着中间包的热稳定状态,从而影响到中间包开浇或快换的成功与否,对提高中间包连浇炉数,提高连铸机作业率,降低生产成本起着重要作用;同时连铸的生产节奏较快,现场的影响因素比较复杂,要求中间包具备快速烘烤的能力,烤包速度快,中间包内的气氛温度能够准确达到开浇所要求的温度。中间包在浇注过程中,特别是开浇或快换第一包中间包内温度变化稳定,具有较好的热稳定状态;s2:结晶器液位标定,预设结晶器给定钢液液位a1,固定拉速值b,固定拉速值对连铸机产量和铸坯质量都有极为重要的影响,观察结晶器内实际钢液液位a,引入前馈控制;s2:将检测到的实际钢液液位a信号与给定钢液液位a1信号进行比较;s3:计算实际钢液液位a与给定钢液液位a1的偏差及偏差变化率;s4:进行模糊推理,将推理后的决策值输送给钢液拉速控制器进行运算;s5:钢液拉速控制器计算后输出控制拉矫机的拉速值b;s6:根据拉速值b计算并快速下调给定钢液液位至a2,用拉速值b计算出匹配的钢液液位;s7:拉速值逐步恢复至b时,把给定钢液液位a2调回到a1的位置,继续进行浇铸。所述前馈控制为预先控制,将给定钢液液位a1设定成可调节的数值。所述钢液拉速控制器为pid控制器,所述pid控制器控制实际的钢液液位。所述给定钢液液位a1由给定钢液控制器l控制,所述给定钢液控制器l为可操作型控制器。所述下调给定钢液液位至a2后,用捞渣棒及时挑出镶嵌在结晶器铜管壁的渣带。本实施例利用引入前馈控制系统,根据实际钢液液位a与给定钢液液位a1的偏差及偏差变化率,进行模糊推理,将推理后的决策值输送给钢液拉速控制器进行运算,下调给定钢液液位以实现稳定拉速的效果,方便生产,解决瞬间无流引起的卷渣漏钢,减少了二次开浇次数,降低了职工劳动强度,降低了钢铁料消耗。本实施例使用干式料中包,中包的干式料是一种高科技碱性不定形耐火材料,它是中间包工作衬的更新换代产品,该料以优质镁砂为主要原料,外加结合剂和添加剂,经严格的生产工艺控制加工而成。干式料中包施工时不需加水,不需搅拌,施工简便,速度快,劳动强度低;干式料中包振动施工完以后,施工体不需养护,可直接点火烘烤,施工体不会出现裂或剥落现象;干式料中包在使用过程中,耐钢水和熔渣的侵蚀,使用寿命长,可依客户须求提供不同的材料吨钢耐材消耗低;干式料中包使用完以后,工作层与永久衬不易烧结,清渣方便,翻包容易;干式料中包主要成分是mg0,它对钢水中非金属夹杂物(如a1203、si02等),有很强的吸附作用,从而净化钢液,提高钢水的质量;干式料中包对烘烤条件要求不高,它只需烘烤到150-200c即可,烘烤温度低,烘烤时间短,节能效果十分显著;使用过程无毒性气体产生,环境干净,无粉尘污染。实施例2如图1至图3所示,本实施例与实施例1基本相同,进一步地,本实施例中连铸厂方坯连铸机生产150x150mm断面的方坯,生产过程中使用中包快速更换定径水口浇铸,生产中定径水口容易发生堵塞现象,分析原因如下:由耐火材料涂抹的中间包工作层、以及中间包内的挡渣堰,受到高温钢液侵蚀、冲刷过程中,会有颗粒较大的非金属夹杂物随着钢水卷入定径水口中,造成定径水口堵塞引起拉速下降,该情况发生于瞬间且没有预兆,特别是当该颗粒物的大小与定径水口直径相当时、会造成瞬间断流,有时断流仅持续3到4秒之后钢流又突然下来。本实施例中小方坯的平均拉速是3m/min,因为定径水口断流的时候,液面自动控制系统是降低拉速的,严重的时候拉速回零。当颗粒物通过定径水口后,钢流恢复正常,这时候自动拉速很小或者为0m/min,自动液面控制系统虽然反应迅速、自动快速提高拉速,但是拉矫机起步惯性太大,导致拉速提高缓慢,定径水口出钢速度正常后,结晶器浇注钢液面迅速上升把镶嵌在结晶器铜管壁上的凝固保护渣带覆盖,随着铸坯向下移动出结晶器后发生卷渣漏钢,失去控制。采取措施如下:设定给定钢液液位a1距结晶器上口100mm左右,控制精度±3mm,采用修改液面自动控制模型方式,根据生产工艺特点,引入前馈控制,将检测的实际钢液液位a信号与给定钢液液位a1信号比较,计算出实际钢液液位a与给定钢液液位a1的偏差及偏差变化率,并进行模糊化、模糊推理和决策后,送给实际的拉速液位pid控制器进行运算,其输出控制拉矫机的拉速值b,根据拉速值b计算并下调给定钢液液位至a2。拉速值逐步恢复至b时,把给定钢液液位a2调回到a1的位置,继续进行浇铸。本实施例克服了传统液面控制方案应对大扰动响应慢的缺点,当发生断流的时候,此时结晶器里面钢水液面下降,操作盘上的实际液位线也同时下降,操作工将操作盘上控制液面按钮,按下3秒,使给定液位由正常液位80%下调到20%(体积百分比)的低液位。然后用捞渣棒及时挑出镶嵌在结晶器铜管壁的渣带,等到钢流浇铸正常时再把自动液位线调回到正常浇铸。本实施例中实际钢液液位a与给定钢液液位a1的变化如下表:结晶器给定钢液液位a1高度(体积百分比)0%20%80%100%实际钢液液位a距离铜管定径水口距离(mm)26022010060本实施例中pid控制器为用比例-积分-微分控制的仪器,用来进行结晶器液位的稳定控制。例如,提供一预设的液位高度设值至pid控制器,使pid控制器根据此液位高度设值和结晶器的液位实际高度来控制结晶器液位,使结晶器液位的液位稳定而不会产生剧烈的变化本实施例解决瞬间无流引起的卷渣漏钢,一个方坯连铸机每月一般有20次无流发生,那么漏钢或非正常停浇废品将产生约40吨,按每吨钢合格品与废品的差价1000元/吨来计算,年节约经济效益约:40吨*1000元/吨*12月=48万元/年。本实施例可以减少因卷渣漏钢等事故带来的设备损坏,每年节约设备维护费用约3万元;同时,通过这种方法补救成功,没有发生漏钢和溢钢停浇事故,使连铸的全流率指标大幅提高,铸坯收得率提高,安全得到保证,给生产带来顺行。本实施例减少了产生废钢的损失,也节约了设备维护费,合计年降本48+3=51万元/年。以上示意性的对本发明及其实施方式进行了描述,该描述没有限制性,附图中所示的也只是本发明的实施方式之一,实际的结构并不局限于此。所以,如果本领域的普通技术人员受其启示,在不脱离本发明创造宗旨的情况下,不经创造性的设计出与该技术方案相似的结构方式及实施例,均应属于本发明的保护范围。当前第1页12