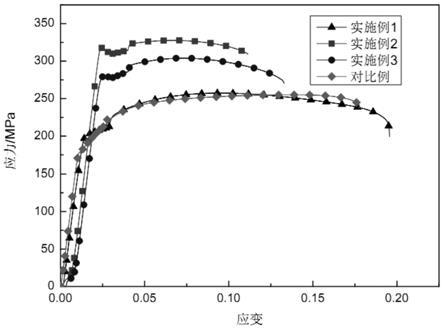
1.本发明属于镁合金技术领域,具体涉及一种能用于高速挤压的变形镁合金及该镁合金的制备方法。
背景技术:2.镁合金作为最轻的工程金属材料,具有比重轻、比强度及比刚度高、阻尼性及切削加工性好、导热性好、电磁屏蔽能力强以及减震性好和易于回收等一系列独特的优点,被誉为“21世纪的绿色工程材料”。与铸造镁合金相比,变形镁合金更具发展前途与潜力,通过变形可以生产尺寸多样的板、棒、管、型材及锻件产品,并且可以通过材料组织的控制和热处理工艺的应用,获得比铸造镁合金材料更高的强度,更好的延展性,更多样化的力学性能的材料,从而满足更多结构件的需要,因此,发展变形镁合金及其加工技术具有重要的现实意义。
3.尽管变形镁合金的研究和应用取得了很大进展,但是常规商用mg
‑
al
‑
zn系合金和mg
‑
zn
‑
zr系合金变形加工窗口较铝合金狭窄的多,因此通常只能采用较低的挤压速度,导致生产效率降低,生产成本提高,不利于镁合金的商业化运用。例如,商用az80和zk60镁合金的挤压速度只有0.5~2.5m/min,主要是由于随着镁合金中铝元素或着锌元素含量的增加,形成了大量低熔点的镁铝相或者镁锌相,在高速挤压过程中由于模具出口端由于温度急剧上升而这些低熔点第二相发生溶解,不足以钉扎晶界导致晶粒粗化,使得挤压产品的性能较低。要保证高速挤压下的变形镁合金依然具有较高的综合性能,就需要合金中存在或者挤压过程中产生高熔点的第二相,以阻碍再结晶晶粒的长大。
4.如中国发明专利申请《一种zn
‑
mg双相异构材料及其制备方法》,其专利申请号为cn202011113751.6(申请公布号为cn112501474a)公开了一种zn
‑
mg双相异构材料,其中,所述的zn
‑
mg双相异构材料中的mg相,除了含有mg,还含有合金化元素m1,m1包括zn、ca、sr、mn、sn、in、ga、ge、bi、co、ag、cu、si、zr、li、na、k、fe、ti、al、sc、y、la、ce、pr、nd、pm、sm、eu、gd、tb、dy、ho、er、tm、yb、lu、th中的至少一种,上述合金化元素m1含量均为0~10wt.%。其明确指出了在采用铸造、挤压纯镁或镁合金时,挤压速度为2~200mm/min,其挤压速度过低。
5.又如中国发明专利《用于高速挤压的变形镁合金及其制备方法》,其专利号为zl201010152389.3(授权公告号为cn101805866b)公开了一种用于高速挤压的变形镁合金,按照重量百分比计包括有以下组分:2.0
‑
9.0%al、0.1
‑
1.0%mn、0.1
‑
3.0%si、0.1
‑
2.0%ce、0.1
‑
1.0%y、0.1
‑
1.0%sr、0.1
‑
1.0%sb,其余为镁,该镁合金的元素组成比较复杂,挤压速度可达到15m/min,抗拉强度280
‑
350mpa,屈服强度160
‑
220mpa,该合金的屈服强度相比于抗拉强度偏低,屈强比仅为0.57
‑
0.62。
6.又如中国发明专利《用于高速挤压的变形镁合金》,其专利号为cn200810172222.6(授权公告号为cn101418404b)公开了一种用于高速挤压的变形镁合金,按照重量百分比计包括有以下组分:5.0~7.0%al、7.0
‑
9.0%mn、2.0~3.0%zn、3.0
‑
4.0%li、1.0
‑
3.0%zr,
其余为镁,该镁合金的挤压速度可达20m/min,抗拉强度248
‑
275mpa,屈服强度142
‑
178mpa,该合金的力学性能偏低,主要是屈服强度偏低,并且在合金中添加了较多的li,增加了合金熔炼的难度和成本。
技术实现要素:7.本发明所要解决的第一个技术问题是针对上述现有技术的现状,提供一种具有良好的抗拉强度、屈服强度及优良的延伸率的变形镁合金。
8.本发明所要解决的第二个技术问题是,提供了一种上述变形镁合金的制备方法。
9.本发明解决上述第一个技术问题所采用的技术方案为:一种变形镁合金,其特征在于,按照质量百分比计,包括有以下组分al:0.5%~2.5%,ca:0.2%~0.6%,mn:0.3%~0.8%,er:0.05%~0.5%,ag:0.01%~0.05%,余量为mg及不可避免的杂质。
10.本发明解决上述第二个技术问题所采用的技术方案为:一种上述的变形镁合金的制备方法,其特征在于,依次包括有以下步骤:
11.1)镁合金铸棒制备:
12.将mg锭、al锭、ag粒、mg
‑
ca中间合金、mg
‑
mn中间合金、mg
‑
er合金放入熔炼炉中进行熔炼,铸造出镁合金铸棒;
13.2)固溶处理:将步骤1)所制备出的镁合金棒在进行固溶处理;
14.3)挤压:将步骤2)的镁合金铸棒和挤压模具在270~500℃下预热1.5~3.0h,挤压机盛锭筒预热至270~500℃,挤压比10:1~60:1,挤压速度5~20m/min,经挤压变形后制备出变形镁合金棒材;
15.4)热处理:将挤压棒材在500℃固溶处理10~30min,热水冷却,然后在200℃时效0.6~2h。
16.优选地,在步骤2)中,固溶处理的温度为450~550℃,处理时间为5~8h。
17.具体地,固溶处理的温度为500℃。
18.优选地,在步骤1)中,在熔炼前,首先将mg锭、al锭、ag粒、mg
‑
ca中间合金、mg
‑
mn中间合金、mg
‑
er合金在温度为200~300℃下烘干。
19.优选地,在烘干后,在sf6+co2气体保护下,依次进行以下步骤:
20.步骤s1:加热至温度为680~730℃下,将mg锭熔化;
21.步骤s1:加热至温度为710~750℃下,将al锭、mg
‑
mn中间合金加入镁熔体中,充分搅拌至熔化;
22.步骤s3:将ag粒、mg
‑
er中间合金加入镁熔体中,充分搅拌至熔化;
23.步骤s4:将mg
‑
ca中间合金加入镁熔体中,充分搅拌至熔化;
24.步骤s5:将熔体升温至760~780℃,通入ar气精炼,降温至740~750℃,静置30~40分钟,待温度降低至700~720℃,刮出熔体表面的浮渣;
25.步骤s6:进行铸棒。
26.具体地,在步骤s6中:采用半连续铸造,浇铸温度:700℃~720℃,铸造速度:100mm/min~200mm/min,冷却水流量:50l/min~100l/min,得到镁合金铸棒。
27.优选地,在步骤s5中,精炼时间为10~15分钟。
28.与现有技术相比,本发明的优点在于:该变形镁合金中的镁中添加al、ca、mn,可生
成弥散分布的耐热al8mn5和al2ca相,al8mn5和al2ca相在挤压过程中起到钉扎晶界而阻碍再结晶长大的作用,并可提高合金的抗拉强度和屈服强度;通过添加稀土er,生成almner相,在挤压过程中被破碎后弥散分布在基体上,可以颗粒激发形核的方式促进动态再结晶,并有利于保证良好的延伸率;而微量ag添加利用其在镁中高的固溶度可以起到固溶强化的作用;在挤压加工后通过t6热处理还可实现热处理强化,采用上述方法制备出的镁合金表面质量优良。
附图说明
29.图1为本发明实施例1、2、3和对比例1的挤压棒实物图;
30.图2是本发明实施例2挤压态组织中存在的al8mn5、al2ca相的sem和tem照片;
31.图3是本发明实施例2挤压态组织中存在的almner相的sem照片;
32.图4是本发明实施例1、2、3和对比例1的拉伸应力应变曲线。
具体实施方式
33.以下结合附图实施例对本发明作进一步详细描述。
34.实施例1:
35.本实施例的变形镁合金按照质量百分比其成分为:al:0.5%,ca:0.2%,mn:0.4%,er:0.1%,ag:0.03%,余量为mg及不可避免的杂质。
36.本实施例的变形镁合金的制备方法依次包括以下步骤:
37.1)镁合金铸棒制备:
38.首先将mg锭、al锭、mg
‑
mn中间合金、mg
‑
ca中间合金、mg
‑
er中间合金在200℃烘干;随后进行以下步骤:
39.步骤s1:在sf6+co2气体保护下,将mg锭在680℃熔化;
40.步骤s2:在730℃,将al锭、mg
‑
mn中间合金加入镁熔体中,充分搅拌至熔化;
41.步骤s3:在750℃,将ag粒、mg
‑
er中间合金加入镁熔体中,充分搅拌至熔化;
42.步骤s4:在730℃,将mg
‑
ca中间合金加入镁熔体中,充分搅拌至熔化;
43.步骤s5:将熔体升温至760℃,通入ar气精炼10~15分钟,降温至740℃,静置30~40分钟,待温度降低至710℃,刮出熔体表面的浮渣;
44.步骤s6:采用半连续铸造,浇铸温度:710℃;铸造速度:100mm/min;冷却水流量:75l/min,得到镁合金铸棒。
45.2)固溶处理:将制得的镁合金棒在500℃条件下固溶处理8h,热水冷却;
46.3)挤压:将镁合金铸棒和挤压模具在380℃下预热1.5h,挤压机盛锭筒预热至350℃,挤压比24:1,挤压速度20m/min,经挤压变形后制备出变形镁合金棒材。
47.4)热处理:将挤压棒材在500℃固溶处理10min,热水冷却,然后在200℃时效0.8h。
48.实施例2
49.本实施例与实施例1的区别仅在于:镁合金的质量百分比组成为al:1.5%,ca:0.4%,mn:0.4%,er:0.3%,ag:0.03%,余量为mg及不可避免的杂质。将挤压棒材在500℃固溶处理30min,热水冷却,然后在200℃时效1.0h。
50.实施例3
51.本实施例与实施例1区别仅在于:镁合金的质量百分比组成为al:2.5%,ca:0.4%,mn:0.4%,er:0.3%,ag:0.03%,余量为mg及不可避免的杂质。将挤压棒材在500℃固溶处理30min,热水冷却,然后在200℃时效1.0h。
52.实施例4
53.本实施例与实施例1区别仅在于:
54.镁合金的质量百分比组成为al:2.5%,ca:0.6%,mn:0.3%,er:0.05%,ag:0.01%,余量为mg及不可避免的杂质。
55.制备方法中的工艺参数存在不同,具体地,步骤s1中,mg锭在700℃熔化;步骤s2中的温度为710℃;步骤s3中的温度为710℃;步骤s4中的温度为710℃;步骤s5中的温度为780℃,精炼10min,降温至745℃,静置时间为30min,待温度降低至700℃;步骤s6中,浇铸温度:720℃;铸造速度:200mm/min;冷却水流量:70l/min,得到镁合金铸棒。
56.实施例5:
57.本实施例与实施例1区别仅在于:
58.镁合金的质量百分比组成为al:2.5%,ca:0.6%,mn:0.8%,er:0.5%,ag:0.05%,余量为mg及不可避免的杂质。
59.制备方法中的工艺参数存在不同,具体地,步骤s1中,mg锭在730℃熔化;步骤s2中的温度为750℃;步骤s3中的温度为720℃;步骤s4中的温度为750℃;步骤s5中的温度为770℃,精炼15min,降温至750℃,静置时间为40min,待温度降低至720℃;步骤s6中,浇铸温度:700℃;铸造速度:150mm/min;冷却水流量:50l/min,得到镁合金铸棒。
60.对比例:选取目前商用可高速挤压镁合金az31,将镁合金az31合金的铸锭经400℃固溶处理12h,采用与实施例1相同的挤压参数进行挤压加工。
61.对于上述实施例1~实施例3以及对比例所得到的变形镁合金进行室温拉伸性能测试,测试结果如表1所示。
62.表1本发明实施例和对比例的微观组织、力学性能
63.编号屈服强度(mpa)抗拉强度(mpa)延伸率(%)实施例119225619实施例231732710实施例330627611对比例16125316
64.下面结合实验结果数据,对实施例1、2、3和对比例1,从经过挤压加工后所获得的材料外观质量、微观组织和力学性能三个方面进行对比分析,具体如下:
65.图1为实施例1、2、3和对比例1的挤压棒的宏观实物图,由图1可以看出,实施例1、2、3的表面质量较好,且与对比例1的表面质量相当,可见本发明制备的镁合金具有较好的高速挤压性能。
66.图2为实施例2在挤压态的sem和tem照片,从图2中可以看出,经固溶处理后合金基体内存在大量弥散分布的第二相,这些第二相可以在挤压过程中钉扎晶界阻碍再结晶晶粒长大,并提高合金的力学性能。
67.图3为实施例2在挤压态的sem照片,从图3中可以看出,未在固溶处理溶解的almner相在挤压过程中破碎,在挤压过程中可以促进动态再结晶,提高镁合金的强度。
68.将本发明实施例1、2、3和对比例1的挤压样品的室温拉伸应力
‑
应变曲线如图4所示,从中得到镁合金的屈服强度、抗拉强度和断后延伸率列于上述表1中。各个实施例合金的屈服强度和抗拉强度均有大幅度的提高,屈服强度达到190mpa以上,甚至高于300mpa,这与合金中大量存在的弥散析出相密切相关。