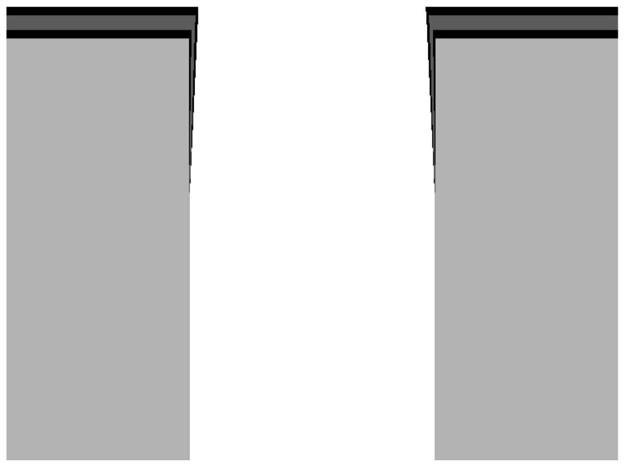
1.本发明涉及微通道板技术领域,具体而言涉及一种在微通道板通道阵列制备复合金属膜层过程中减少开口面积比损失量的工艺及微通道板。
背景技术:2.微通道板是一种大面阵的通道电子倍增器,由数百万根圆形通道规则排列而成,依靠元件中圆形孔内壁材料对电子进行倍增。微通道板在工作过程中需要通电,因此在该元件的两个表面镀制膜层以起到导电的作用。开口面积比为微通道板工作区的通道开口面积与整个工作区面积之比,开口面积比决定微通道板的探测效率,并在一定程度上影响微通道板的增益及噪声因子,是微通道板的关键性能之一。
3.为了提高微通道板的开口面积比,现有技术中采用多种措施实现,例如通过减薄皮料厚度或者通道入口的形状来实现,例如在公开号为cn207282449的中国专利中提出的措施低延迟脉冲、低串扰、高收集效率微通道板,其每个通道包括开设在输入电极层的输入口以及开设在输出电极层的输出口;输入口与通道上端连通,输出口与通道下端连通;输入口自上而下逐渐减小,从而形成的微通道板的通道开口面积大于90%。目前所列措施因制造工艺难度较大,且合格率较低,无法实现工业批量生产,仅适用于特殊领域应用。
4.减小因金属膜层蒸镀后开口面积比的损失是提高开口面积比切实可行的办法,不改变基础工艺。在保证面电阻符合技术指标的前提下,减薄金属膜层厚度,相较原正常工艺达到提高开口面积比的目的。镍铬膜层的减薄势必导致面电阻的值将增大,为了保证面电阻,减薄膜层,引入电阻率更小的金属作为导电膜层。在确定膜层材料后,需要改进镀膜工艺,优化膜层镀制效果。
5.随着纳米薄膜材料科学研究的进展,各种先进镀膜技术也随之发展起来。通过气相转移方式镀膜成为主流,主要分为两大类,包括:物理气相沉积和化学气相沉积。物理气相沉积,是指利用物理过程实现物质转移,将原子或分子由源转移到基材表面的过程,包括真空热蒸发,电子束蒸发,磁控溅射等;化学气相沉积,是反应物质在气态条件下发生化学反应生成固态物质沉积在固态基底表面。这两种镀膜方式分别具有各自的优缺点。化学气相沉积在不规则表面进行镀膜以及膜层致密性好是其优势,并且镀制的膜层以化合物为主,膜层厚度较薄。物理气相沉积更适合在平面上镀制膜层,镀制厚度较厚膜层。故选用物理气相沉积镀膜方式,真空热蒸发对镀膜料的蒸发温度选择性更小,不适合高熔点金属材料,电子束化料能量集中且更大,适合熔点较高的金属膜层镀制。
6.例如,在公开号为cn110400738a的中国专利申请中提出的提高微通道板分辨力的方法及其蒸镀方法,在微通道板的输出端面上蒸镀一层金属材料的膜层,以覆盖微通道板原有的输出镍
‑
铬电极,镀制的金属材料膜层采用铂(pt)/镍(ni)/金(au)/银(ag)金属材料蒸镀,其逸出功高于4.0ev,利用新镀制金属膜层材料的高逸出功,提高微通道板分辨力。其最终在输出端面形成的是两种金属材料形成的双层复合膜层,其中也包含金属材料银,但
是其并不能直接或间接应用解决微通道板输入面开口面积比损失量的问题。
7.现有技术文献:
8.专利文献1cn207282449u
9.专利文献2cn110400738a
技术实现要素:10.本发明目的在于提供一种在微通道板通道阵列制备复合金属膜层过程中减少开口面积比损失量的工艺及微通道板,在微通道板输入面及一定深度内壁蒸镀复合结构的金属膜层,既满足面电阻技术指标要求,又控制开口面积比损失量问题。
11.为实现上述目的,本发明的第一方面提出一种在微通道板通道阵列制备复合金属膜层过程中减少开口面积比损失量的工艺,包括:
12.提供密集排列的圆形微孔阵列的基底;
13.在真空环境下,在所述圆形微孔阵列的圆形微孔输入面和一定深度的内壁采用两种材料先后蒸镀的方式进行叠加,形成顺序层叠结构aba,其中a层为镍铬合金层,b层为金属银或者铜层。
14.优选地,所述a层的厚度为b层厚度的2倍。
15.优选地,所述a层的厚度为20nm,b层的厚度为10nm。
16.优选地,所述圆形微孔阵列中的圆形微孔的直径为φ6um,相邻圆形微孔之间的孔间距为7.5um,圆形微孔的长度为0.33mm。
17.优选地,在微通道板通道阵列制备复合金属膜层过程中减少开口面积比损失量的工艺的具体制备步骤包括:
18.提供密集排列的圆形微孔阵列的基底,清洗、烘干后,放置于真空镀膜机内的工装架上;
19.抽真空,使得真空镀膜机内的真空度达到1*10
‑1pa,对基底进行200℃的真空烘烤;
20.烘烤结束后开始镍铬合金膜层蒸镀;
21.镍铬合金膜层蒸镀结束后,旋转镀膜料坩埚,开始金属银或铜膜层蒸镀;
22.金属银或铜膜层蒸镀结束后,再次旋转镀膜料坩埚,开始镍铬合金膜层蒸镀;
23.其中,蒸镀过程中,控制aba顺序层叠结构的各个膜层的厚度在预设的范围内。
24.根据本发明的第二方面提出一种根据前述工艺制备得到的微通道板。
25.应当理解,前述构思以及在下面更加详细地描述的额外构思的所有组合只要在这样的构思不相互矛盾的情况下都可以被视为本公开的发明主题的一部分。另外,所要求保护的主题的所有组合都被视为本公开的发明主题的一部分。
26.结合附图从下面的描述中可以更加全面地理解本发明教导的前述和其他方面、实施例和特征。本发明的其他附加方面例如示例性实施方式的特征和/或有益效果将在下面的描述中显见,或通过根据本发明教导的具体实施方式的实践中得知。
附图说明
27.附图不意在按比例绘制。在附图中,在各个图中示出的每个相同或近似相同的组成部分可以用相同的标号表示。为了清晰起见,在每个图中,并非每个组成部分均被标记。
现在,将通过例子并参考附图来描述本发明的各个方面的实施例,其中:
28.图1是本发明的复合膜层结构的示意图
29.图2是镀膜后开口面积比计算的示意图
30.图3是不同膜层厚度在不同镀膜深度对应的开口面积比的示意图。
31.图4是传统的膜层的输入导电层和复合导电层对比图。
32.图5是镀膜速率选择装置的结构示意图。
具体实施方式
33.为了更了解本发明的技术内容,特举具体实施例并配合所附图式说明如下。
34.在本公开中参照附图来描述本发明的各方面,附图中示出了许多说明的实施例。本公开的实施例不必定意在包括本发明的所有方面。应当理解,上面介绍的多种构思和实施例,以及下面更加详细地描述的那些构思和实施方式可以以很多方式中任意一种来实施,这是因为本发明所公开的构思和实施例并不限于任何实施方式。另外,本发明公开的一些方面可以单独使用,或者与本发明公开的其他方面的任何适当组合来使用。
35.结合图1、2所示,本发明的目的旨在提出一种减小微通道板镀制金属膜层后开口面积比损失量的工艺,在微通道板输入面及一定深度内壁蒸镀复合金属膜层,既满足面电阻技术指标要求,同时避免传统厚度太厚、开口面积比损失较大的问题。
36.结合图2所示,本发明针对镀膜影响微通道板开口面积比进行理论计算,构建理想化的模型,为了方便计算,斜切角设置为0度,模型如图2所示,未镀膜时的开口面积比如下:
[0037][0038]
考虑到通道内壁靠近输入面处镀膜的膜层厚度对于孔径的影响,开口面积比为:
[0039][0040]
其中各参数含义如下:
[0041]
d:孔间距
[0042]
r:孔径
[0043]
xr:镀膜电极深度(以孔径r为单位)
[0044]
θ:微通道板输入面与入射粒子束的夹角
[0045]
a:微通道板输入面膜层厚度
[0046]
v:θ为90时,膜层沉积速率
[0047]
从上述本发明构建的模型可以看出,镀膜厚度与镀膜深度对于开口面积比的损失量影响非常大。
[0048]
本发明的示例性实施例公开一种减小微通道板镀制金属膜层后开口面积比损失量的方法,在微通道板输入面先蒸镀一层镍铬合金,作用是增强复合膜层在玻璃基底上的附着力,再蒸镀一层10nm金属银或铜,以较薄的膜层厚度实现较好的导电性,最后在此基础上蒸镀镍铬合金膜层,保证复合膜层表面与原单一膜层相同,不引入其他问题。例如通过聚焦电子枪光斑和加装蒸镀速率选择装置优化镀膜工艺,达到蒸镀在微通道板输入面的镍铬
合金膜层比改进前的膜层更致密、电阻率更小的目的。然后,在镍铬合金膜层表面蒸镀一层10nm金属银或铜,增加输入面导电性能,最后镀制一层镍铬合金膜层。由于金属银或铜的电阻率远远小于镍铬合金合金,在满足输入面面电阻的要求的前提下,与现有技术相比,可减薄整体膜层厚度,达到减小微通道板镀制金属膜层后开口面积比损失量的目的。
[0049]
而金属银/铜材料如果直接镀制在输入端面,会影响输入端面对于入射光的反射率,部分穿过阴极膜层的光被输入端面电极反射造成杂散情况、信号串扰影响整体像管成像效果,因此在金属银或铜膜层表面蒸镀一层20nm镍铬合金膜层,保证输入面导电膜层未对微通道板的其他性能产生影响,故在本发明的实施过程中采取aba顺序层叠结构的复合膜层。
[0050]
在可选的例子中,安装镀膜速率选择装置,该装置放置于镀膜料之上,由于摆放镀膜料的坩埚是设备厂家设计的固定尺寸,而每次镀膜料使用电子枪进行预熔后可开启挡板进行蒸镀。因电子光斑的尺寸远远小于镀膜料的尺寸,镀膜料表面温度呈中心高边缘低的梯度分布:镀膜料中心温度高,蒸发出的原子或团簇能量高,沉积于基底上形成膜层致密度好,电阻率低;镀膜料边缘温度低,蒸发出的原子或团簇能量低,沉积于基底上形成膜层致密度差,电阻率高。对于本发明的实施来说,成膜的料能量越大对成膜的状态越好。在无法规避因镀膜机产生的镀膜料不同速率的固有存在影响情况下,本发明在常规镀膜机基础上增加设计了镀膜选择装置,作为可选的实施例,该镀膜选择装置使用铝板开孔,放置于坩埚上方,孔正对镀膜料光斑区域,使用孔对镀膜料蒸发区域进行选择,使镀膜料的边缘低温区蒸发的原子/团簇无法到达基底,提高到达基底处的镀膜料原子/团簇的能量,使得蒸镀的膜层质量更优,降低电阻率。
[0051]
现有技术中的提高微通道板分辨力的方法及其蒸镀方法中,金属银等材料直接镀制在输入端面,会影响输入端面对于入射光的反射率,部分穿过阴极膜层的光被输入端面电极反射造成杂散情况、信号串扰影响整体像管成像效果;同时,直接在输入端面增镀金属材料而不改变输入端面镍铬合金膜层镀膜工艺,无法达到减小开口面积比损失量的目的,反而会因为增加镀膜而使得开口面积比损失更多,因此其并不能直接或间接应用解决本专利申请所针对的减小微通道板输入面开口面积比损失量的问题。
[0052]
作为可选的实施例,本发明整体上提供一种在微通道板通道阵列制备复合金属膜层过程中减少开口面积比损失量的工艺,包括以下步骤:提供密集排列的圆形微孔阵列的基底;以及在真空环境下,在圆形微孔阵列的圆形微孔输入面和一定深度的内壁采用两种材料先后蒸镀的方式进行叠加,形成顺序层叠结构aba,其中a层为镍铬合金层,b层为金属银或者铜层。
[0053]
其中,a层的厚度为b层厚度的2倍。
[0054]
其中,a层的厚度为20nm,b层的厚度为10nm。
[0055]
其中,圆形微孔阵列中的圆形微孔的直径为φ6um,相邻圆形微孔之间的孔间距为7.5um,圆形微孔的长度为0.33mm。微通道板的尺寸为φ25mm。
[0056]
在可选的实施例中,前述工艺的具体制备步骤包括:
[0057]
提供密集排列的圆形微孔阵列的基底,清洗、烘干后,放置于真空镀膜机内的工装架上;
[0058]
抽真空,使得真空镀膜机内的真空度达到1*10
‑1pa,对基底进行200℃的真空烘烤;
[0059]
烘烤结束后开始镍铬合金膜层蒸镀;
[0060]
镍铬合金膜层蒸镀结束后,旋转镀膜料坩埚,开始金属银或铜膜层蒸镀;
[0061]
金属银或铜膜层蒸镀结束后,再次旋转镀膜料坩埚,开始镍铬合金膜层蒸镀;
[0062]
其中,蒸镀过程中,控制aba顺序层叠结构的各个膜层的厚度在预设的范围内。
[0063]
下面结合具体的示例进行说明。
[0064]
[1].制作材料层a
[0065]
[1.1].将清洗后的基底放置于真空镀膜机行星工装架上,开始抽真空,真空度达到1*10
‑1pa,对基底进行200℃的真空烘烤;
[0066]
[1.2].烘烤结束后开始镍铬合金膜层蒸镀,厚度由膜厚仪精确控制;
[0067]
[2].制作材料层b
[0068]
镍铬合金膜层蒸镀结束后,旋转镀膜料坩埚,开始金属银或铜膜层蒸镀,厚度由膜厚仪精确控制;
[0069]
[3].制作材料层a
[0070]
金属银或铜膜层蒸镀结束后,旋转镀膜料坩埚,开始镍铬合金膜层蒸镀,厚度由膜厚仪精确控制。
[0071]
在可选的实施例中,镀膜设备选用电子束蒸发型真空镀膜机,调整工装,使其膜层蒸镀的角度符合该元件通道内壁膜层覆盖深度的要求。
[0072]
[1].将清洗干净的基底通过检验表面是否合格,合格后装入镀膜夹具中,而后将装有基底的镀膜夹具装入调整好的镀膜工装上,检查无误后,关闭腔体门抽真空;
[0073]
[2].安装镀膜速率选择装置,该装置放置于镀膜料之上,由于摆放镀膜料的坩埚是设备厂家设计的固定尺寸,而每次镀膜料使用电子枪进行预熔后开启挡板进行蒸镀。因电子光斑的尺寸远远小于镀膜料的尺寸,这就导致镀膜料表面进行蒸镀的速率是不一致的,越往边缘蒸镀的速率越小,因而到达基板进行成膜的料能量就较小,通过前期试验证明,成膜的料能量越大对产品成膜的状态越好。在无法规避因镀膜机产生的这种镀膜料不同速率这种固有存在的影响,设计了镀膜速率选择装置,该装置是使用铝板开孔,孔正对镀膜料,大小取决于想要选择从镀膜料往出蒸镀料速率的大小,最终确定大小为176mm2(镀膜料的表面积是1256mm2),从而达到对不同镀膜速率进行选择的目的,使得蒸镀的膜层质量更优。
[0074]
[3].真空度达到1.0*10
‑1pa时对基底进行200℃烘烤,烘烤过程中真空系统正常工作;
[0075]
[4].制作材料层a
[0076]
[1.1].烘烤结束后,调整电子枪光斑大小达到12mm2,使其在束流达到500ma时可以蒸镀镍铬合金合金膜料,蒸镀过程中的速率控制在3nm/s
‑
5nm/s;
[0077]
[1.2].镍铬合金膜层蒸镀,厚度20nm由膜厚仪精确控制;
[0078]
[2].制作材料层b
[0079]
镍铬合金膜层蒸镀结束后,旋转镀膜料坩埚,开始金属银或铜膜层蒸镀,厚度10nm由膜厚仪精确控制;
[0080]
[3].制作材料层a
[0081]
金属银或铜膜层蒸镀结束后,旋转镀膜料坩埚,开始镍铬合金膜层蒸镀,厚度20nm
由膜厚仪精确控制。等待10分钟后对腔体放气;放气完成后取出基底,完成制备过程。
[0082]
通过本发明的方法制备膜层,面电阻满足技术指标要求,同时膜层厚度比原正常工艺(200nm)减薄150nm,结合图3所示,微通道板的输入面开口面积比损失量由原来的4.8%减小到2%,有效降低。
[0083]
虽然本发明已以较佳实施例揭露如上,然其并非用以限定本发明。本发明所属技术领域中具有通常知识者,在不脱离本发明的精神和范围内,当可作各种的更动与润饰。因此,本发明的保护范围当视权利要求书所界定者为准。