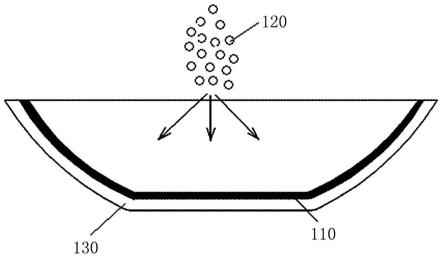
1.本技术涉及厨房用具领域,更具体地讲,涉及一种不粘涂层及其制备方法和一种包括该不粘涂层的锅具。
背景技术:2.自从不粘锅面世以来,由于其在烹饪食物时不会使食物粘在锅底上,因而能够避免传统锅具在烹饪过程中时常发生的食物粘锅现象,从而能够避免食物出现焦糊,也能够避免由于焦糊而引起的产生有害物质的问题。而且,不粘锅不仅降低了锅具的清洗难度,同时还能够轻松煎、炒食物,能够避免传统锅具需要较多的油脂来防止食物粘锅,从而最大限度地减少了用油,降低了人对脂肪的摄入量,顺应了现代人追求低脂肪、低热量的消费潮流。因此,不粘锅成为很多家庭的首选。
3.市场上的锅具主要是通过在锅具的内表面上涂覆不粘层来实现不粘,其中,氟涂料、陶瓷涂料和有机硅树脂涂料是较为常见的不粘层。虽然氟涂料、陶瓷涂料和有机硅树脂涂料均能作为锅具的不粘层使用,但是在使用过程中也存在着较为明显的问题。比如,由氟涂料形成的不粘层不耐磨损,并且在高温下容易分解出有害物质;由陶瓷涂料形成的不粘层的持久不粘性差,使用3~6个月后就容易脱落;由有机硅树脂涂料形成的不粘层在高温或明火的条件下容易发黄或发灰,并且不粘层在高温下硬度下降,容易产生“回粘”现象。
技术实现要素:4.为了解决上述问题中的一个或多个,本发明提供一种具有持久不粘性和耐磨性的不粘涂层。
5.为此,本技术的第一方面在于提供一种不粘涂层的制备方法。
6.本技术的第二方面在于提供一种不粘涂层。
7.本技术的第三方面在于提供一种包括不粘涂层的锅具。
8.为实现上述目的,本技术的第一方面的实施例提供一种不粘涂层的制备方法,包括以下步骤:通过在基体的表面上热喷涂合金粉来形成热喷涂涂层;对热喷涂涂层进行保温;采用激光重熔使保温后的热喷涂涂层的表层完全熔化,使得所述热喷涂涂层形成为包括熔化层和过渡层;对熔化层进行快速冷却,从而在所述基体的所述表面上形成具有非晶结构的不粘层。所述制备方法可以避免采用含有非晶结构的合金粉热喷涂形成含有非晶结构的不粘涂层的过程中存在非晶结构的晶化现象,并降低了热喷涂工艺的要求和对原材料合金粉选材的要求,在一定程度上降低其制备成本,并且不粘涂层的制备工艺简单,容易实现批量生产。
9.在一些实施例中,可以采用液氮执行快速冷却步骤,其中,在快速冷却步骤中,冷却速度可以不小于104k/s。该条件下能够快速将熔化层中的原子冷冻下来,避免熔化层中原子发生晶化,因此,熔化层中的非晶态被冷却形成非晶结构,最后获得含有非晶结构的不粘层。
10.在一些实施例中,在保温步骤中,保温温度可以为350℃~450℃、保温时间可以至少为20min。通过保温的方式,使热喷涂涂层中的热应力降低,避免热喷涂涂层中热应力过大导致热喷涂涂层不能自由地胀缩,从而防止熔化层冷却形成不粘层时热喷涂涂层产生裂纹,最终避免获得的不粘涂层发生开裂以及脱落等问题。
11.在一些实施例中,所述热喷涂涂层的厚度可以为100μm~800μm,其中,形成的所述熔化层的厚度可以为热喷涂涂层厚度的30%~60%。在本实施例中,激光只对热喷涂涂层的表层进行重熔,重熔后的表层形成熔化层,避免熔化层冷却形成不粘层时熔化层与基体之间的温差较大导致热喷涂涂层与基体变形的问题,因此,熔化层的厚度小于热喷涂涂层的厚度在一定程度上能够防止热喷涂涂层与基体之间的结合力降低导致形成的不粘涂层在使用过程中脱落的问题。
12.在一些实施例中,所述合金粉的粒度可以为300~800目。该粒度范围的合金粉在热喷涂时能够受热熔化形成热喷涂涂层,形成的热喷涂涂层具有良好的致密性并且形成的涂层中杂质含量较低。
13.在一些实施例中,所述合金粉可以包括不锈钢粉、zr合金粉、cu合金粉、al合金粉、mg合金粉、ti合金粉和等原子比高熵合金粉中的至少一种。
14.在一些实施例中,所述合金粉可以包括不锈钢粉和/或锆合金粉。本实施例中的合金粉的非晶化能力强,利于获得非晶结构含量高的不粘层,进一步降低不粘层的表面能,使获得的不粘涂层表现出优异的不粘性。
15.在一些实施例中,所述基体可以为锅具的基体。
16.本技术第二方面的实施例提供一种不粘涂层,所述不粘涂层包括:过渡层,位于基体的表面上,过渡层具有晶体结构;不粘层,位于过渡层的表面上,不粘层具有非晶结构,不粘层的厚度为不粘涂层的总厚度的30%~60%,其中,过渡层和不粘层具有相同的组成元素。本实施例在不粘层和基体之间设置有过渡层,过渡层在熔化层冷却形成不粘层时对熔化层与基体之间的温差形成缓冲,从而避免温差过大导致热喷涂涂层与基体之间发生形变,因此,在一定程度上保持热喷涂涂层与基体之间的结合力不发生改变,延长制备的不粘涂层的使用寿命。
17.在一些实施例中,所述热喷涂涂层的厚度可以为100~800μm。本实施例中该范围内的热喷涂涂层形成的不粘涂层不仅具有好的耐磨性,同时还能够避免熔化层冷却转化为不粘层时温差较大容易导致的基体与涂层热膨胀系数不一致产生崩裂的问题,也避免涂层厚度太厚容易热量聚集产生热应力而导致的裂纹等缺陷发生。
18.本技术第三方面的实施例提供一种包括基体和上述的不粘涂层。
附图说明
19.图1示出了根据本技术的制备不粘涂层的示意图。
20.附图标记说明:
21.110-热喷涂涂层,120-液氮,130-基体。
具体实施方式
22.现在,将在下文更充分地描述本发明的构思。
23.不粘锅实现不粘的原理主要有三方面:(1)锅具自身的表面具有低表面能;(2)锅具的表面形成有微观凹凸结构,该凹凸结构形成类似于荷叶疏水疏油的表面;(3)锅具的表面涂覆有多孔储油材料而形成稳定油膜,利用形成的油膜实现锅具不粘。
24.发明人在对不同的材料研究过程中发现非晶合金(即,具有非晶结构的液态金属)相对于普通材料具有更低的表面能,表现出良好的不粘性;发明人对产生的原因进一步分析发现,非晶合金之所以表现出低表面能是因为非晶合金具有的非晶结构,其具有长程无序、短程有序的非晶结构特性。
25.对此,发明人通过在锅具的内表面附着一层具有非晶结构的涂层来实现锅具的不粘。经过实验发现,可以通过热喷涂方式将具有非晶结构的合金粉喷涂在锅具的内表面上来形成含有非晶结构的不粘涂层,但是形成的不粘涂层的不粘性会随着热喷涂的条件发生改变,在一定程度上会导致不粘涂层的不粘性降低。经过进一步对热喷涂形成的不粘涂层的不粘性降低的原因研究发现,因为在热喷涂的过程中,合金中的非晶结构通常会随着热喷涂的温度升高和喷涂的时间的延长具有晶化的趋势,导致获得不粘涂层中的非晶结构的占比降低,使得不粘涂层的表面能升高,从而导致不粘涂层的不粘性降低;因此,通过热喷涂的方式将含有非晶结构的合金粉喷涂在锅具基体的表面形成不粘涂层时对热喷涂的工艺的要求较高。
26.本技术提供了一种不粘涂层的制备方法。下面将结合图1来详细地描述根据本技术的制备不粘涂层的方法。图1示出了制备不粘涂层的示意图。
27.根据本技术,制备不粘涂层的方法可以包括以下步骤:采用热喷涂工艺将合金粉喷涂在基体的表面上,从而在基体的表面形成热喷涂涂层;对形成的热喷涂涂层进行保温;采用激光重熔使保温后的热喷涂涂层的表层完全熔化以形成熔化层;对熔化层进行快速冷却,从而在基体的表面上形成具有非晶结构的不粘涂层。
28.在本技术的实施例中,基体可以为锅具的基体。可以在执行热喷涂之前先对基体的表面进行预处理,例如进行清洗,以使基体的表面粗化,从而增强基体与将要形成的不粘层之间的结合力。
29.根据本技术的实施例,形成热喷涂涂层的合金粉可以是晶态合金粉,也可以是非晶合金粉。根据本技术的一些实施例,合金粉可以包括不锈钢粉、zr合金粉、cu合金粉、al合金粉、mg合金粉、ti合金粉和等原子比高熵合金粉中的至少一种。根据本技术,热喷涂涂层可以通过热喷涂形成在锅具基体的内表面上。优选地,合金粉可以使用不锈钢粉和/或zr合金粉。合金粉的非晶化能力强,则非晶化冷却速度低;合金粉的非晶化能力越强,则越容易获得高非晶含量的合金。热喷涂工艺可以包括等离子喷涂,然而,本技术不限于此,本领域技术人员可以在本发明构思的教导下选用合适的热喷涂工艺来形成热喷涂涂层。
30.根据本技术的实施例,合金粉的粒度可以为300目~800目。具体地,如果合金粉末太粗,则在热喷涂时粉末在飞行过程中受热熔化不充分,到达基体的表面时变形较小,导致热喷涂形成的热喷涂涂层不致密,容易产生缺陷,比如耐磨性和持久不粘性差的问题;另一方面,如果合金粉末太细,则合金粉在热喷涂过程中容易过烧氧化,从而会在形成的热喷涂涂层中引入大量的氧化物杂质而降低热喷涂涂层的性能。
31.根据本技术的实施例,在基体(例如,锅具基体)的表面(例如,内表面)上形成的热喷涂涂层的厚度可以在100μm至800μm的范围内。由于热喷涂形成的涂层中通常会存在热应
力,如果热喷涂涂层过厚,则涂层在锅具的制备过程和使用过程中容易发生热量聚集而产生热应力,导致热喷涂涂层产生裂纹等缺陷,因此,热喷涂涂层的厚度不能超过800μm。另一方面,如果热喷涂涂层的厚度小于100μm,则由于涂层的厚度太薄且耐磨寿命较差,且在急冷进行非晶化转变时由于温差较大而容易导致基体与涂层热膨胀系数不一致产生崩裂。此外,在本实施例中,热喷涂工艺可以是等离子喷涂工艺。
32.根据本技术的实施例,在形成基体的表面上形成热喷涂涂层之后且在执行激光重熔之前,需要对涂层进行保温。具体地讲,由于热喷涂形成的涂层中通常会有热应力的存在,而热应力将会导致热喷涂涂层不能自由地胀缩从而引起热喷涂涂层开裂以及发生脱落等问题,因此,采用保温的方式来削弱热喷涂涂层中的热应力。即,在形成热喷涂涂层后进行一段时间的保温,使得热喷涂涂层中的热应力在保温的过程中得以缓慢的释放,从而最终使热喷涂涂层中的热应力完全或基本上释放出或最小化,进而防止随后通过激光重熔形成的熔化层在冷却形成不粘层时在热喷涂涂层中产生裂纹。根据本技术的实施例,可以对热喷涂涂层保温至少20min以使热喷涂涂层中的热应力尽可能地释放出。
33.在本技术的一些实施例中,保温温度可以控制在350℃~450℃。具体地讲,根据本技术,刚形成的热喷涂涂层的温度可以在550℃~650℃,若保温温度低于350℃,则因保温温度与热喷涂涂层的温度之间存在较大温差,热喷涂涂层的表面散热快,会引起热喷涂涂层的表面和热喷涂涂层的内部之间的热伸缩速率差异较大,最终无法消除热喷涂涂层中的热应力;而如果保温温度过高(高于650℃),则经济性差。因此,用于对热喷涂涂层进行保温的温度可以在350℃~450℃的范围内。
34.根据本技术的实施例,在对基体的表面形成的热喷涂涂层进行保温之后,可以执行激光重熔。具体地讲,利用激光主要是将热喷涂涂层的表层进行重熔,使涂层中重熔的表层形成熔化层,该熔化层在后续工艺中转变为非晶组织层,而涂层的底层为未熔化区域作为过渡层。在本实施例中,通过激光重熔,破坏热喷涂涂层的表层中原有的晶态结构,使其趋于非晶态,将处于非晶态的熔化层经冷却可以形成含有非晶结构的不粘层。由于激光重熔时保留了一定厚度的热喷涂涂层作为过渡层,过渡层在对熔化层进行冷却时能够在熔化层与基体之间形成缓冲,从而避免温差较大导致热喷涂涂层与基体变形的问题,因此,过渡层在一定程度上至少让热使热喷涂涂层与基体之间的结合力保持不变,从而避免形成的不粘涂层在使用过程中发生脱落。
35.在根据本技术的一些实施例中,可选地,可以控制熔化层的厚度为热喷涂涂层的总厚度的30%~60%。如果熔化层的厚度太大,则过渡层的厚度会太小,导致缓冲效果不明显;如果熔化层的厚度太小,则非晶化层的厚度偏小,导致不粘涂层的耐磨寿命不佳,该厚度的过渡层避免的过渡层的厚度太小导致缓冲效果不明显的问题。
36.根据本技术的优选实施例,对热喷涂涂层的表层进行激光重熔的步骤可以采用以下参数:激光功率为500w~2kw,光斑直径为3mm~10mm,搭接率为40%~50%,气体保护方法为氩气保护,扫描速率为10m/min~15m/min。
37.根据本技术的实施例,在使热喷涂涂层的表面形成熔化层之后,对熔化层进行急冷(即,快速冷却),在此过程中,熔化层中的原子会随着温度的降低而逐渐失去动能,阻碍熔化层晶化,最终使熔化层中的原子被冻结下来,形成具有非晶结构的不粘层。根据本技术的一些实施例,可以采用液氮执行对熔化层进行快速冷却的步骤。根据本发明的优选实施
例,可以控制对熔化层进行冷却的冷却速率为≥104k/s。如图1所示,可以利用液氮120对形成在基体130上的热喷涂涂层110的表面上的熔化层进行急冷。然而,本技术不限于此,本领域技术人员也可以在本技术的教导下选用其它介质对熔化层进行急冷。这里,选用液氮对熔化层进行冷却时,对熔化层的冷却条件包括:气流流速为6~12l/min、压强为0.1mpa的液氮,此处液氮的气流流速指的是从直径为10mm的喷嘴喷出的液氮的流速。
38.根据上述方法在基体的表面(例如,内表面)上形成的不粘涂层包括位于基体的表面上的未被重熔的合金涂层(即,过渡层)以及位于过渡层上由熔化层冷却形成且具有非晶结构的不粘层,从而使获得的不粘涂层产生不粘效果。
39.根据本技术的上述方法可以避免采用非晶合金粉在热喷涂形成包含非晶结构的不粘涂层过程中出现非晶转向晶化问题,因此,采用上述方法制备的不粘层中的非晶含量高,不粘层的表面能低,表现出优异的不粘性,并且同时还降低了对热喷涂工艺的要求。此外,由于非晶合金(即,具有非晶结构的液态金属)没有像晶体合金那样具有晶界、孪晶、晶格缺陷、位错、层错等结构缺陷,而且没有异相、析出物、偏析以及其他成分起伏,是一种混乱的无序结构,在化学上有高度的均匀一致性,受到外力时不存在晶界滑移等塑性变形,具有更高的强度。因此,获得不粘涂层表现出优异的耐磨性以及持久不粘性。
40.本技术提供了一种可以形成在锅具的内表面上的不粘涂层。参照图1,所述不粘涂层可以包括:过渡层(未示出),位于基体130的表面上,过渡层具有晶体结构;不粘层(未示出),位于过渡层的表面上,不粘层具有非晶结构,不粘层的厚度为不粘涂层的总厚度的30%~60%,其中,过渡层和不粘层具有相同的组成元素。根据本技术,通过在不粘层与基体之间设置过渡层,在制备不粘层时可以形成缓冲,避免形成不粘层的熔化层在快速冷却时因温差过大导致热喷涂形成的涂层与基体发生变形,在一定程度上保持热喷涂涂层与基体之间的结合力不发生改变,延长制备的不粘涂层的使用寿命。此外,不粘层与过渡层由同一热喷涂涂层形成,故不粘层和过渡层为一体化。
41.下面将结合具体的实施例来详细地描述根据本技术。
42.实施例1
43.一种不粘涂层的制备,具体包括以下步骤:
44.步骤c1、热喷涂涂层的制备
45.首先,将基体用表面活性剂阿克苏226sa进行清洗,然后烘干,再对基体的表面进行喷砂处理,喷砂处理后基体表面的粗糙度ra为3μm。
46.其次,采用加热炉对喷砂处理后的基体进行预热,将基体预热到260℃。
47.最后,采用等离子喷涂的方式将粒度为300目的不锈钢粉(为市售普通316不锈钢粉)喷涂在基体的内表面上,以形成厚度为160μm的热喷涂涂层,等离子喷涂时的参数为:送粉速度35g/min;喷涂距离148mm;电弧电流520a;氢气压力0.5mpa、流量7.5l/min;氩气压力0.8mpa、流量50l/min。
48.步骤c2、不粘层的制备
49.首先,将形成的热喷涂涂层在350℃的温度环境中保温20min。
50.其次,将保温后的热喷涂涂层的表层进行激光重熔,其中,熔化层的厚度为热喷涂涂层的厚度的30%;激光重熔的条件为:激光功率:1.1kw;光斑尺寸:光斑直径7mm;搭接率:45%,气体保护方法:氩气保护;扫描速率:12m/min。
51.最后,将熔化层用液氮以2.1
×
104k/s的冷却速度进行冷却,形成具有非晶结构的不粘层,从而获得包括过渡层和不粘层的不粘涂层。
52.实施例2
53.除了以下条件不同之外,按照与实施例1相同的方法制备不粘涂层:步骤c1中使用的不锈钢粉的粒度为800目,形成的热喷涂涂层的厚度为790μm;步骤c2中的热喷涂涂层的保温温度为420℃,保温时间为75min,熔化层的厚度为热喷涂涂层的厚度的58%,用液氮以3.4
×
104k/s的冷却速度冷却熔化层。
54.实施例3
55.除了以下条件不同之外,按照与实施例1相同的方法制备不粘涂层:步骤c1中的不锈钢粉的粒度为600目,形成的热喷涂涂层的厚度为500μm;步骤c2中的热喷涂涂层的保温温度为400℃,保温时间为75min,熔化层的厚度为热喷涂涂层的厚度的45%。
56.实施例4
57.除了以下条件不同之外,按照与实施例1相同的方法制备不粘涂层:步骤c1中的不锈钢粉的粒度为600目,形成的热喷涂涂层的厚度为650μm;步骤c2中的热喷涂涂层的保温温度为370℃,保温时间为60min,熔化层的厚度为热喷涂涂层的厚度的50%,用液氮以2.4
×
104k/s的冷却速度冷却熔化层。
58.对比例1
59.除了在步骤c2中不对热喷涂涂层进行保温之外,按照与实施例4相同方法制备不粘涂层。
60.对比例2
61.除了在步骤c2中用液氮以以0.7
×
104k/s的冷却速度冷却熔化层之外,按照与实施例4中相同的方法制备不粘涂层。
62.对比例3
63.除了在步骤c2中用激光将热喷涂涂层全部进行重熔之外,按照与实施例4相同的方法制备不粘涂层。
64.对比例4
65.第一涂层的制备:
66.首先,将基体用碱性溶剂进行清洗,清洗并烘干后再在基体的表面进行喷砂处理,喷砂处理后基体表面的粗糙度ra为3μm。
67.其次,采用加热炉对喷砂处理后的锅身基体进行预热,将锅身基体预热到260℃。
68.最后,采用等离子喷涂的方式将粒度为600目的不锈钢粉喷涂在基体的表面,从而在基体的表面形成第一涂层,形成的第一涂层的厚度为325μm,等离子喷涂时的参数与实施例1相同。
69.第二涂层的制备:
70.待第一涂层的温度降低至280℃后,将粒度为600目的fe40-zr25-cr9-b6-cu15-y5非晶合金等离子喷涂在第一涂层的表面,在第一涂层的表面形成具有非晶结构的第二涂层,且第二涂层的厚度为325μm,最后获得包括第一涂层和第二涂层的不粘涂层。
71.性能指标测试
72.对实施例1-4和对比例1-4制备的不粘涂层的性能进行测试,并将测试结果记载在
下表1中。
73.(1)不粘性检测
74.采用国标gb/t32095中对不粘涂层的不粘性试验方法,按照其中的煎蛋不粘性试验来检测不粘涂层的不粘性。检查煎蛋与涂层之间的粘附情况,将涂层的不粘性分为以下三个等级:
75.优(
○
):用塑料铲可使鸡蛋无损伤取出并不留残渣。
76.良(
◎
):用塑料铲不能使鸡蛋无损伤取出,但用湿海绵轻拭可去除残渣。
77.差(
×
):用湿海绵轻拭不能去除残渣。
78.(2)持久不粘性检测
79.持久不粘性检测参照gb/t32095.2中平面耐磨测试方法进行,每磨1000次进行一次煎蛋测试,连续两次煎蛋出现“差(
×
)”等级则测试结束,记录耐磨次数。
80.(3)耐磨性检测
81.参照gb/t32095.2中平面耐磨测试方法进行,记录不粘涂层磨穿露底的耐磨次数。
82.(4)结合强度检测
83.采用冷热冲击的方法对上述实施例和对比例制备的不粘涂层与基体之间的结合强度进行分析,其具体测试方式为:首先将有不粘涂层的基体加热到260℃,保温30min,然后立刻放入20℃冷水中,其中,将加热、保温和冷却作为一个循环。企业锅具标准为冷热冲击50次循环涂层与基体之间仍无损坏为合格。
84.表1性能指标测试结果
[0085][0086]
从表1中的实施例4和对比例1可以看出,热喷涂涂层保温后形成的不粘涂层与锅具基体之间的结合力更好。从表1中的实施例4和对比例2可以看出,冷却速度过低时,形成的不难涂层的耐磨性以及持久不粘性均明显降低,其原因是,冷却速度过低时,熔化层中被打乱的原子发生了晶化,形成的不粘层中晶体结构含量较高,导致制备的不粘涂层的耐磨性和持久不粘性降低。从表1中的实施例4和对比例3可以看出,热喷涂涂层全部被激光重熔后形成的不粘涂层与基体之间的结合强度小,这是因为在对激光重熔的涂层进行冷却时,没有过渡层作为缓冲,涂层与基体之间由于较大的温差发生了形变,导致获得的不粘涂层与基体之间的结合力变弱。
[0087]
从表1中的实施例4和对比例4可以看出,采用本技术制备的不粘涂层在持久不粘
性、耐磨性以及与基体之间的结合强均比对比例4制备的不粘涂层好,其原因主要有两方面,一方面,本实施例中制备的不粘涂层中的过渡层和不粘层是由同一热喷涂涂层形成,而对比例中的不粘涂层中的第一涂层和第二涂层采用等离子喷涂分开形成,导致对比例4中的不粘涂层与基体之间的结合力较差;另一方面,本技术中的不粘涂层中的不粘层通过熔化层冷却形成,具有较高的非晶含量,而对比例4中的第二涂层采用等离子喷涂形成过程中合金粉中的部分非晶结构发生晶化,导致形成的不粘涂层的耐磨性和持久不粘性所有降低。
[0088]
综上,从上述表1中可以看出,采用本技术所述方法制备的不粘涂层表现出较为优异的不粘性、耐磨性、持久不粘性以及与基体之间较好的结合强度。其原因是设有过渡层的不粘涂层与基体之间的结合力更好,这是因为过渡层降低了不粘层制备时涂层与基体之间的温差较大导致涂层与基体的变形,因此,过渡层在一定程度上至少让热喷涂涂层与基体之间的结合力保持不变,形成的不粘涂层与基体之间表现出较为优异的结合强度。此外,保温降低了热喷涂涂层中的热应力,并且对服役中的不粘涂层进行观察,保温后制备的不粘涂层也不容易产生裂纹。
[0089]
根据以上描述,本技术的不粘涂层及其制备方法具有以下优点:
[0090]
(1)将形成的热喷涂涂层的表层进行重熔,并将熔化层冷却形成具有非晶结构的不粘层,且形成的不粘层中的非晶含量较高,具有较低的表面能,产生好的不粘效果,同时还降低对等离子喷涂工艺的要求。此外,本技术中不粘涂层的制备还具有工艺简单以及容易实现批量生产的特点。
[0091]
(2)不粘涂层还包括过渡层,通过在不粘层与基体之间设置过渡层,降低了不粘涂层制备时热喷涂涂层与基体之间的温差较大导致热喷涂涂层与基体的变形,使得形成的不粘涂层牢固地附着在基体上。此外,不粘涂层的制备过程中还采取保温的方式来降低热喷涂涂层中热应力,防止熔化层冷却形成不粘层时热喷涂涂层产生裂纹,延长了不粘涂层的服役时间。
[0092]
上面对本技术的具体实施方式进行了详细描述,虽然已表示和描述了一些实施例,但本领域技术人员应该理解,在不脱离由权利要求及其等同物限定其范围的本技术的原理和精神的情况下,可以对这些实施例进行修改和完善(例如,可以对不同实施例中描述的不同特征进行组合),这些修改和完善也应在本技术的保护范围内。