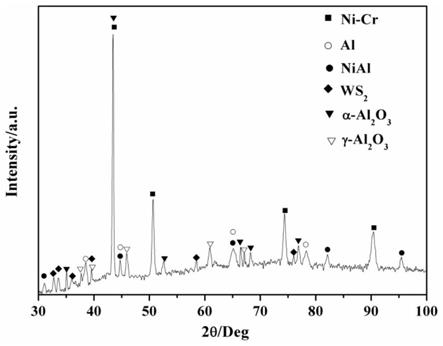
1.本发明属于镍基合金表面涂层及制备,尤其涉及一种镍基合金表面耐磨涂层及其制备方法。
背景技术:2.镍基合金因具有良好的力学性能及耐腐蚀性能等优点,广泛应用在化工能源产业、核能产业、交通运输等领域的装备制造材料,如,发动机涡轮部件、连铸机辊子、挤压模具等。在往复传动条件下,镍基合金易发生摩擦磨损现象,难以成膜而极易失效。因此,耐磨性不足致使其难以满足磨损的工作环境要求,且增加了零部件的更换频次。目前,主要通过陶瓷相增强镍基合金以及表面改性方法以提高镍基合金的耐磨性:一是以石墨及陶瓷相为代表的耐磨相加入到镍基合金基体中,通过粉末冶金工艺成形镍基复合材料,但上述增强相与镍基合金界面存在结合强度弱,同时增强相在镍基合金中的分布状态调控困难,难以有效提高镍基合金的耐磨性。另一方面,表面改性技术为提高镍基合金耐磨性提供了一种途径,如,渗氮、渗碳和渗硼等表面化学热处理可提高金属材料的表面硬度和耐磨性,但渗透层较薄,难以满足长时间的磨损要求,限制了镍基合金的广泛应用。
技术实现要素:3.发明目的:本发明的第一目的是提供一种镍基合金表面耐磨涂层;本发明的另一目的是提供该耐磨涂层的制备方法。
4.技术方案:本发明的一种镍基合金表面耐磨涂层,包括镍基合金基体,所述镍基合金基体表面原位生长有由al2o3陶瓷层和具有润滑功能的ws2颗粒组成的耐磨涂层,所述ws2颗粒分散在al2o3陶瓷层中。
5.其中, al2o3和ws2复合涂层是通过镍基合金表面浸铝层在na2wo4和na2s的混合水溶液经微弧氧化原位形成。
6.本发明还保护一种镍基合金表面耐磨涂层的制备方法,包括以下步骤:(1)对镍基合金进行预处理,然后采用氢氟酸稀溶液进行表面腐蚀,获得粗糙的表面;(2)采用惰性氩气辅助的热浸铝工艺,在具有粗糙表面的镍基合金表面制备浸铝层,在氩气保护环境下对浸铝层进行退火,使浸铝层与镍基合金间形成nial扩散层;(3)取na2wo4、na2s、na3po4和naoh混合于水中,配置成混合溶液;(4)将步骤(2)的镍基合金浸铝层置于步骤(3)的混合溶液中,用分段式正/反向电流协同控制的恒流微弧氧化工艺进行氧化处理,在浸铝层表面原位形成具有al2o3陶瓷层和ws2颗粒复合强化的耐磨涂层。
7.进一步的,所述步骤(2)中,采用惰性氩气辅助的热浸铝工艺具体包括:将纯度为99.5%的纯铝在真空炉中加热至690~720℃得纯铝液,在真空炉内冲入氩气至炉内压力为0.1~0.2mpa,将具有粗糙表面的镍基合金浸入纯铝液中10~30min。
8.进一步的,所述步骤(2)中,退火温度为250~400℃,退火时间为1~2 h。
9.进一步的,所述步骤(2)中,浸铝层厚度为500~1000μm。
10.进一步的,所述步骤(3)中,na2wo4、na2s、na3po4和naoh的质量比为6~10:10~20:7~12:1~1.5。
11.进一步的,所述步骤(4)中,分段式正/反向电流协同控制的恒流微弧氧化工艺具体为:在0~50s时间范围内正向电流密度为2~4a/cm3、反向电流密度为1.5~2a/cm3;50s后采用正向电流密度为3~5a/cm3、反向电流密度为2~2.5a/cm3。
12.进一步的,所述步骤(1)中,预处理具体是指:将镍基合金采用砂纸打磨及金刚石研磨膏抛光至镜面。
13.进一步的,所述步骤(1)中,腐蚀时间为3~10s。
14.进一步的,所述镍基合金为ni-cr合金、ni-cr-mo合金、ni-cr-fe合金中的任一种。
15.本发明的制备原理为:本发明依据镍基合金在服役过程中摩擦学性能需求,依据材料表面改性原理,将抛光后的镍基合金进行腐蚀形成粗糙表面,在惰性氩气的压力辅助下,将粗糙表面的镍基合金表面浸入纯铝液中进行表面热浸铝,既能避免纯铝与镍基合金界面间的氧化,也能在压力辅助下增强其界面间的润湿作用,增加浸铝层与镍基合金基体间的机械结合强度,同时通过氩气环境退火处理,促使镍、铝等原子的扩散,在浸铝层与镍基合金基体界面形成nial扩散层,显著增强界面结合强度;其次,基于al2o3陶瓷的高耐磨性、ws2的润滑功能,在含na2wo4和na2s的磷酸盐水溶液中进行微弧氧化处理,促使浸铝层原位形成含具有耐磨陶瓷al2o3和润滑功能ws2复合强化的耐磨涂层,增强了陶瓷相与涂层的结合强度,且在al2o3与w2s减磨与自润滑的协同作用下,以进一步提高镍基合金的耐磨性。
16.本发明基于分段式正/反向电流协同控制的恒流微弧氧化工艺,在镍基合金浸铝层表面原位制备含具有耐磨陶瓷al2o3和润滑功能ws2复合强化的耐磨涂层,一方面因先低后高的分段式正/反向电流的施加能促进微弧氧化膜层中孔隙尺寸趋于均匀;另一方面因陶瓷al2o3的耐磨强化作用、ws2的自润滑作用,促使镍基合金在摩擦过程中形成层状摩擦层,有效降低镍基合金的摩擦系数,且陶瓷相的强化作用,提高了耐磨性能。
17.有益效果:与现有技术相比,本发明的显著优点为:本发明采用惰性氩气辅助的热浸铝工艺在腐蚀的镍基合金表面制备浸铝层,惰性氩气的辅助作用既能避免纯铝与镍基合金界面间的氧化,也能在压力辅助下增强其界面间的润湿作用,增强浸铝层与镍基合金基体的机械结合强度,通过氩气气氛下的退火处理形成nial扩散层,进一步增强浸铝层与镍基合金基体的冶金结合强度;另一方面,采用微弧氧化工艺在浸铝层表面原位形成的al2o3和润滑功能ws2复合强化的耐磨涂层,其中ws2相与al2o3涂层形成较强的冶金结合界面,上述界面强度的增强能显著降低涂层在摩擦过程中的粘附,避免涂层因界面强度弱而产生的剥落与失效,从而提高材料的耐磨性。
附图说明
18.图1是实施例1制得镍基合金表面耐磨涂层的物相谱图;图2是实施例2制得镍基合金表面耐磨涂层表面形貌;图3是实施例1-4制得的自润滑镍基合金的磨损率。
具体实施方式
19.下面结合附图和实施例对本发明的技术方案作进一步详细说明。
20.实施例1(1)将ni-cr镍基合金采用砂纸打磨及金刚石研磨膏抛光至镜面,然后采用氢氟酸稀溶液中腐蚀3s,获得粗糙的表面;(2)纯度为99.5%的纯铝在真空炉中加热至690℃,采用惰性氩气辅助的热浸铝工艺,在真空炉内冲入氩气至炉内压力至0.1mpa,将上述步骤中所述粗糙表面的ni-cr镍基合金表面浸入纯铝液中10min,制备厚度为500 μm的浸铝层,在氩气保护环境下浸铝层进行250℃退火2h,在浸铝层与镍基合金间形成nial扩散层;(3)配置6g/l na2wo4、10g/l na2s、7g/l na3po4、1g/l naoh的混合水溶液;(4)利用0~50s时间范围内采用正向电流密度为2a/cm3、反向电流密度为1.5a/cm3;50s后采用采用正向电流密度为3a/cm3、反向电流密度为2a/cm3的微弧氧化工艺对上述步骤中(2)所述ni-cr镍基合金表面浸铝层在步骤中(3)的水溶液中进行氧化处理,在浸铝层表面原位形成具有陶瓷al2o3和润滑功能w2s复合强化的耐磨涂层。
21.从图1可发现,镍基合金表面耐磨涂层的物相谱图中除镍基合金基体衍射峰外,还发现了热浸铝层的衍射峰,以及nial相的衍射峰,说明在热浸铝层与镍基合金基体中ni在界面间扩散层的形成,同时物相图谱上还存在微弧氧化形成的原位陶瓷al2o3和润滑功能ws2相的衍射峰,说明本发明提供镍基合金表面耐磨涂层及制备方法能增强涂层与镍基合金的界面的润湿性能,且形成氧化物陶瓷相及自润滑相。
22.实施例2本实施例与实施例1的区别是:步骤(2)中纯度为99.5%的纯铝在真空炉中加热至720℃,将在真空炉内冲入氩气至炉内压力至0.15mpa,制备热浸铝层厚度为800 μm,退火温度为设置为350℃,其余与实施例1相同。
23.从图2中可发现al2o3陶瓷涂层中分散着ws2相颗粒,且al2o3陶瓷涂层分布着微小的孔隙。
24.实施例3本实施例与实施例2的区别是:步骤(1)中镍基合金为ni-cr-mo;步骤(3)中na2wo4的浓度为8g/l、na2s浓度为16g/l;步骤4中0~50s时间范围内采用正向电流密度为3a/cm3、反向电流密度为2a/cm3;50s后采用采用正向电流密度为4a/cm3;其余与实施例2相同。
25.实施例3制备的镍基合金表面耐磨涂层室温下摩擦系数的平稳值约为0.21,低于粉末烧结制备的mos2增强nicr合金的最优摩擦系数(约0.36),同时也低于微弧氧化获得的单一al2o3涂层的摩擦系数(0.3~0.4)。
26.实施例4本实施例与实施例3的区别是:步骤3中na2wo4的浓度为10g/l、na2s浓度为20g/l、na3po4浓度为12 g/l、naoh浓度为1.5 g/l;步骤(4)中0~50s时间范围内采用正向电流密度为4a/cm3、反向电流密度为2a/cm3;50s后采用采用正向电流密度为5a/cm3、反向电流密度为2.5a/cm3;其余与实施例3相同。
27.从图3中可发现实施例1-4的镍基合金表面耐磨涂层的磨损率在1.6~2.3
×
10-5 mm3/n
•
m范围,低于粉末烧结制备的mos2增强nicr合金磨损率(4.6~8.1)
×
10-5 mm3/n
•
m,这
是因为镍基合金表面浸铝层经微弧氧化形成的原位陶瓷al2o3相的硬度与强度高,在摩擦过程中塑性变形困难,难以产生摩擦粘附,从而降低磨损率;另一方面,在腐蚀的镍基合金表面制备浸铝层有利于增强浸铝层与镍基合金基体的机械结合强度,同时热浸铝层的退火处理促使其与镍基合金基体形成具有冶金结合的nial扩散层,且微弧氧化工艺在浸铝层表面原位形成的al2o3层,上述界面强度的增强显著降低了涂层在摩擦过程中的粘附,提高镍基合金的耐磨性,进一步说明本发明提供的镍基合金表面耐磨涂层的成形方法能有效提高镍基合金的摩擦性能。
28.对比例1具体制备工艺同实施例1,不同之处在于,包括步骤(2)中不采用在氩气保护环境下浸铝层进行250℃退火2h,直接在ni-cr镍基合金表面制备浸铝层,以及微弧氧化工艺制备陶瓷涂层。
29.对比例2具体制备工艺同实施例1,不同之处在于,步骤(3)中不采用分段式正/反向电流,直接采用恒定电流密度为2a/cm3,进行氧化处理,得到微弧氧化的陶瓷涂层。
30.将对比例1-2得到的微弧氧化耐磨涂层,并进行耐磨性能对比。对比例1中不采用氩气保护环境下浸铝层进行250℃退火处理,其浸铝层与ni-cr镍基合金基体界面间无扩散层,界面结合能力降低,在摩擦过程中,在平行于摩擦方向的摩擦剪应力循环作用下,因浸铝层中铝的剪切强度较低,且微弧氧化多孔涂层加剧了涂层受力的不均匀性,导致涂层产生区域性粘附磨损,增大了磨损率(3.8
×
10-5 mm3/n
•
m)。对于对比例2中不采用分段式正/反向电流模式进行微弧氧化处理,其膜层中孔隙尺寸变化范围较大,在摩擦过程中摩擦剪应力循环作用下产生受力不均匀,应力较大区域极易产生粘度磨损,加剧涂层的磨损(4.3
×
10-5 mm3/n
•
m),因此可以说明本发明中浸铝层/镍基合金界面出形成的nial扩散层以及分段式正/反向电流协同控制的恒流微弧氧化工艺的双重作用下,提高了涂层的耐磨性。