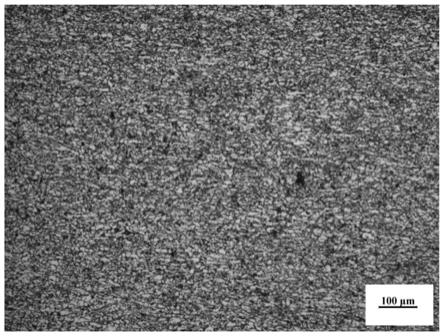
一种低碳当量含钛q420md钢板及其制备方法
技术领域
1.本发明涉及轧钢技术领域,尤其涉及一种低碳当量含钛q420md钢板及其制备方法。
背景技术:2.国内生产的q420级钢板主要应用于建筑及工程机械领域,随着2019年gb/t 1591-2018《低合金高强度结构钢》的实施,在国内设计领域采用多年的q420d牌号逐渐被新一代的热机械轧制q420md所代替,并朝着低碳、合金减量化方向发展。新一代的钢铁材料的开发,尽量或少量的添加合金元素或微合金元素,以达到生产高性能钢材的目的,这就要求在不以碳含量为主要强化方式的前提下,不以钒、ni、mo贵重金属为主要强化方式,依靠对冶炼、连铸、轧制和冷却路径的设计,实现钢的塑韧性的有机结合。
3.原有q420d的生产工艺主要采用高合金配比,以控轧交货状态为主,其典型成份是高碳高锰高合金,特征是强度有余、低温韧性不足、碳当量高,特别是在加入贵重合金v元素后,不仅生产成本居高不下,碳当量高,而且v的加入导致韧性转变温度提高,低温韧性降低。部分企业为平衡低温韧性和降低碳当量,采用低碳体系(c≤0.12%),但随之而来的是以更多的合金元素来弥补碳对强度的损失,虽然整体焊接性有所提高,但成本方面丧失了竞争力。
4.钛元素作为一种廉价的合金元素,已经越来越得到重视,但始终未能批量应用于高强度低温用钢板上,钛的广泛应用,不仅可以大幅度降低合金成本,而且其不占用任何一个碳当量,不对焊接产生有害作用。另一方面,虽然钛能够大幅度的提高强度,但一般也会损害钢的韧性,提高韧脆转变温度。
5.申请号为202010392608.9的中国专利公开了一种低成本含铬q460mc钢板及其生产方法,虽然该专利通过合金成分的设计,不添加v元素,利用廉价cr元素固溶强化和提高淬透性,优化tmcp生产工艺,最终得到具有高强度、高韧性和低成本的钢板,但是,一方面,该方法生产的是含q460mc钢板,而本发明生产的是q420md钢板;另一方面,利用该方法制备的q460mc钢板中的碳含量仍旧较高,铬的加入导致碳当量升高,其碳当量cev范围在0.33-0.43%,而本发明以钛强化为主,不占有任何碳当量,而由于钛的强化和专属工艺的匹配,碳含量可以更低,使本专利碳当量cev范围在0.28~0.32%,明显优于对比专利,对于焊接性能是极为有利的;并且,利用该方法制备的q460mc钢板适用温度为0℃以上,冲击试验温度为0℃,不适用于更低温度,而本发明q420md适用温度为-20℃,冲击温度为-20℃。
技术实现要素:6.有鉴于此,本发明提供了一种低碳当量含钛q420md钢板及其制备方法,采用低碳体系大幅度降低碳当量,利用廉价强化元素钛代替钒等贵重金属元素,优化连铸二冷区冷却工艺及tmcp生产工艺,最终得到具有高强度、低温高韧性和低碳当量的钢板。
7.本发明的第一个目的是提供一种低碳当量含钛q420md钢板,所述钢板的化学组分
及各组分重量百分含量为:c:0.04~0.06%、si:0.20~0.40%、mn:1.40~1.60%、p:≤0.020%、s:≤0.005%、als:0.015~0.035%、nb:0.025~0.035%、ti:0.035~0.055%,其余为fe及不可避免的杂质。
8.优选地,所述钢板的厚度为8mm~16mm。
9.本发明的第二个目的是提供所述低碳当量含钛q420md钢板的制备方法,包括以下步骤:
10.步骤a、转炉冶炼,高炉冶炼的铁水经转炉冶炼,转炉钢水用挡渣锥和滑板联合挡渣出钢,渣厚≤50mm,出钢过程中向钢包内加入nbfe合金,mn合金在出钢至1/4到2/3时添加完毕;
11.步骤b、精炼,转炉出钢后的钢水进精炼工位进行精炼处理,造白渣控铝脱氧,白渣保持时间15-25min,造白渣后加入tife合金,然后软吹氩,软吹氩时间8-12min,同时对钢水中的c、si、mn、nb、ti成份进行微调;
12.步骤c、连铸,精炼炉出来的钢水上钢经中间包、结晶器浇注成180mm厚的板坯,浇注过程采用保护浇注,连铸二冷区冷却工艺采用强冷工艺;
13.步骤d、加热,连铸板坯进加热炉加热保温,加热段温度为1100~1300℃,均热段温度为1130~1250℃,加热速率为6.5min/cm~8.0min/cm,加热时间2.0-2.5h;
14.步骤e、粗轧,钢坯出加热炉除鳞去除表面氧化皮后进入粗轧阶段,粗轧开轧温度为1070~1110℃,粗轧终轧温度970℃~1030℃;
15.步骤f、精轧,粗轧开坯后随即进行精轧阶段,精轧开轧温度为920~1000℃,精轧终轧温度810~850℃;
16.步骤g、冷却,精轧钢板经冷却后得到成品钢板,精轧钢板进入层流冷却装置进行冷却,终冷温度为550~600℃,冷却时间为10s~20s。
17.优选地,步骤c中所述连铸二冷区比水量为0.9~1.0l/kg,二冷区水温在26.5~28.5℃。
18.优选地,步骤e中所述粗轧轧制道次为7道次~10道次,粗轧末道次压下率22-26%,中间坯厚度3.0-4.0倍成品厚度,最小中间坯厚度36-50mm。
19.优选地,步骤f中所述精轧道次为6道次~8道次,精轧末3道次总压下率20-28%。
20.优选地,步骤g中所述冷却的速率为10℃/s~18℃/s。
21.采用了上述技术方案,本发明取得的技术进步是:
22.合理设计q420md钢板的化学成分,并通过改变合金元素的配比,不以碳为强化元素,不添加v元素,利用廉价ti元素析出强化提高强度,以ti强化为基础,轧制过程利用控轧控冷工艺,在较高的冷却速度下,使制得的钢板各项性能满足q420md的各项性能要求,由于不添加v等提高碳当量的元素和采用更低的c含量设计,钢材具有强韧性的同时,大幅度提高焊接性能,同时大幅度降低碳当量,碳含量为0.04~0.06%,碳当量稳定控制在《0.33%,优于国标≤0.43%要求,提高焊接性的同时,大幅提高塑韧性和冷成型性并降低了生产成本。
23.合理设计钢材的化学成分及配比,首先考虑钛元素的添加和配比,钛作为强化元素,钛一方面作为细化晶粒元素,在加热过程可以抑制奥氏体的长大,防止晶粒粗化;另一方面,钛超过一定含量时(如0.030%)可以大幅度的提升钢的强度,但钛过量时,容易生成
大颗粒的氮化钛夹杂,对低温韧性不利,因此将钛含量限定在0.035~0.055%。
24.碳作为影响焊接性能的主要元素之一,直接影响工程机械结构的焊接质量和焊接效率,同时碳含量的降低将大幅度提高钢板的塑性、韧性和成型性,因此将其限定在0.04%~0.06%。
25.硅是钢液弱脱氧元素,其主要作用为预脱氧并防止气泡等缺陷的产生,但硅含量过高,不利于表面质量的控制,易生成氧化铁皮,同时也会提高焊接裂纹敏感性指数,所以,将其含量限定在0.20~0.40%之间。
26.锰是提高强度和韧性的有效元素。随锰含量提高,钢的淬透性也会提高,易于贝氏体钢转变,因此,设定其含量限定在1.40~1.60%。
27.磷是钢中有害元素之一,特别对冷塑性冷成型性能危害最大,最大设定其含量上限为0.020%;硫也是钢中有害元素之一,通常在钢中以硫化锰夹杂的形式存在,恶化钢的韧性并造成性能的各向异性,所以,钢中硫含量越低越好,将钢中硫含量控制在0.005%以下。
28.铝是强脱氧元素,可以有效的控制钢中的氧含量,铝≥0.015%是本质细晶粒钢的基本要求,但其含量过高,已生成过多的氧化铝夹杂,对韧性不利,所以将铝含量限定在0.015~0.035%之间。
29.铌作为晶粒细化元素,在较多钢种都具有普遍适用性,铌可以改善钢板的韧性,降低韧脆转变温度,且能够通过析出强化提高钢的强度,但铌也属于贵重金属,因此设定铌含量为0.025~0.035%。
30.钛一方面作为细化晶粒元素,在加热过程可以抑制奥氏体的长大;另一方面,钛超过一定含量时(如0.030%)可以大幅度的提升钢的强度,但钛过量时,容易生成大颗粒的氮化钛夹杂,对低温韧性不利,因此将钛含量限定在0.035~0.055%。
31.本发明低碳当量q420md钢板的生产方法,出钢过程中加入铌铁,由于铌铁的熔化温度约为1520℃~1600℃,熔化温度较高,在出钢过程中加入,可以增加铌铁的吸收时间和均匀时间,使铌铁的吸收率提高至95%以上,而如果在精炼时加入,则有可能导致铌的吸收率低,铌含量分布不均匀。
32.转炉钢水用挡渣锥和滑板联合挡渣出钢,可以精确控制转炉下渣量,防止转炉内氧化性渣子大量进入钢包,造成后道工序脱氧时间增长,增加脱氧剂消耗,同时控制渣厚≤50mm,由于转炉内渣子含有大量磷酸钙,如下渣过多会导致钢中回磷,增加判废的质量风险。
33.白渣保持时间15-25min,白渣保持时间长,说明渣子还原性好,氧含量低,脱硫及去除夹杂物能力强且稳定;
34.软吹氩是充分保障钢水纯净度的重要工序,造白渣后软吹氩,在软吹氩阶段,细小夹杂物被氩气泡捕捉,进而充分上浮,其需保证一定时间,同时兼顾生产节奏,因此软吹氩时间8-12min。
35.连铸二冷区采用强冷,比水量0.9~1.0l/kg,二冷区水温在26.5~28.5℃,均是为了增加连铸坯冷却速度,促进细小钛的碳氮化物的析出,减少粗大氮化钛或氧化钛的生成。如果在铸坯中钛的析出物较为粗大,则在加热工序不能被固溶,也无法在接下来的控轧控冷中以tic析出,从而起不到析出强化的作用。
36.由于q420md属于低合金钢,同时也是铌微合金钢,铌含量为0.025%~0.035%,铌的碳化物理论条件下完全固溶温度为1150℃~1200℃,实际生产钢坯温度要低于炉温温度,因此炉温要高于1250℃,但是温度过高会导致钢坯微观组织晶粒粗大,直接导致成品钢板晶粒粗大,无法起到原有tmcp工艺细晶强化的作用,同时会损害塑性和低温韧性,因此加热段温度控制为1100℃~1300℃。
37.在粗轧阶段,为奥氏体再结晶区轧制,采用高温大压下工艺,使奥氏体晶粒充分再结晶,细化奥氏体晶粒,对于微合金钢一般不低于950℃,而随着粗轧轧制过程的自然降温,为保障再结晶充分,温度越低,所需压下率越大,特别是末道次保证压下率,同时作为薄规格钢板,在随后的精轧阶段降温速率较快,因此粗轧开轧温度为1070℃~1110℃,粗轧终轧温度970℃~1030℃,粗轧末道次压下率22-26%。
38.中间坯厚度3.0-4.0倍成品厚度,能够保证精轧的累积压缩比足够大,即保证未再结晶区轧制有足够大的总变形量,使得在拉长的奥氏体中获得大量均匀的变形带,进而细化和均匀的铁素体组织。
39.精轧后快速进行层流冷却,在加速冷却时,能够抑制铁素体晶粒的长大,得到细小的铁素体组织,由于本发明碳含量仅为0.04~0.06%,属于低碳,主要依靠细化晶粒和钛的析出提高钢的强韧性,因此控制终冷温度为550℃~600℃,冷却速率为10℃/s~18℃/s。
附图说明
40.图1是本发明实施例1制备产物的金相显微组织结构图;
41.图2是本发明实施例2制备产物的金相显微组织结构图;
42.图3是本发明实施例3制备产物的金相显微组织结构图。
具体实施方式
43.为使本发明的目的、技术方案和优点更加清楚,下面将对本发明的技术方案进行清楚、完整的描述。显然,所描述的实施例仅是本发明一部分实施例,而不是全部的实施例。基于本发明中的实施例,本领域普通技术人员在没有做出创造性劳动的前提下所得到的所有其它实施例,都属于本发明所保护的范围。
44.下述实施例中所述试验方法或测试方法,如无特殊说明,均为常规方法;所述原料和助剂,如无特殊说明,均从常规商业途径获得,或以常规方法制备。
45.实施例1
46.一种低碳当量q420md钢板的化学组分及各组分重量百分含量为:c:0.04~0.06%、si:0.20~0.40%、mn:1.40~1.60%、p:≤0.020%、s:≤0.005%、als:0.015~0.035%、nb:0.025~0.035%、ti:0.035~0.055%,其余为fe及不可避免的杂质;
47.所述低碳当量q420md钢板的制备步骤如下:
48.步骤a、转炉冶炼,高炉冶炼的铁水经转炉冶炼,转炉钢水用挡渣锥和滑板联合挡渣出钢,渣厚40mm,出钢过程中向钢包内加入nbfe合金,mn合金在出钢至1/4到2/3时添加完毕,转炉定氧702ppm,出钢时间5min;
49.步骤b、精炼,转炉出钢后的钢水进精炼工位进行精炼处理,造白渣控铝脱氧,白渣保持时间17min,造白渣后加入tife合金,然后软吹氩,软吹氩时间10min,同时对钢水中的
c、si、mn、nb、ti成份进行微调;
50.步骤c、连铸,精炼炉出来的钢水上钢经中间包、结晶器浇注成180mm厚的板坯,浇注过程采用保护浇注,连铸二冷区冷却工艺采用强冷工艺,二冷区比水量0.95l/kg,二冷区水温在26.5℃;
51.步骤d、加热,连铸板坯进加热炉加热保温,加热段温度为1280℃,均热段温度为1160℃,加热速率为7.3min/cm,加热时间为2.2h;
52.步骤e、粗轧,钢坯出加热炉除鳞去除表面氧化皮后进入粗轧阶段,粗轧开轧温度为1110℃,粗轧终轧温度1020℃,轧制道次为8道次,粗轧末道次圧下率为22%,最小中间坯厚度为36mm;
53.步骤f、精轧,粗轧开坯后随即进行精轧阶段,精轧开轧温度为1000℃,精轧终轧温度830℃,精轧道次为6道次,精轧末3道次总圧下率为26%;
54.步骤g、冷却,精轧钢板经冷却后得到成品钢板,精轧钢板进入层流冷却装置进行冷却,终冷温度为570℃,冷却时间为15s,冷却速率为15.3℃/s。
55.获得的最终成品钢板的厚度为8mm。
56.经检验最终成品钢板得知,低碳当量q420md钢板其化学组分及各组分重量百分含量为:c:0.04%、si:0.30%、mn:1.50%、p:0.014%、s:0.002%、als:0.020%、nb:0.032%、ti:0.036%,其余为fe及不可避免的杂质。
57.使用电子显微镜对实施例1制备的低碳当量q420md钢板进行金相组织观察检测,如图1所示,从图1可以看出钢板微观组织均匀细小,晶粒度达到10.5级。
58.分别使用设备微机屏显液压万能试验机、双立柱金属摆锤冲击试验机和连续弯曲试验机测量实施例1制备的低碳当量q420md钢板的各项力学性能,其中设备微机屏显液压万能试验机测量上屈服强度reh(试样发生屈服而力首次下降前的最大应力);抗拉强度rm(拉伸过程相应最大力fm对应的应力);屈强比reh/rm;延伸率a(试样拉断后标距的增量与原有标距的比值);使用双立柱金属摆锤冲击试验机测量纵向-20℃冲击akv(v型缺口试样在2mm摆锤刀刃下的冲击吸收能量);连续弯曲试验机测量180
°
d=2a冷弯试验,其中,d为(弯曲压头直径),a为钢板厚度,冷弯试样进行180
°
弯折,试样表面无裂纹等缺陷,表示冷弯合格;各项力学性能检测结果如表1所示:
59.表1实施例1制备产物各项力学性能测试结果
[0060][0061]
从表1可以看出实施例1制备的低碳当量q420md钢板具有优良的强度、塑性和韧性,其屈服强度达到480mpa,较国标高出60mpa,抗拉强度达到610mpa以上,延伸率达到27.5%,屈强比reh/rm为0.79,具有较好的冷塑性,冷弯试样表面无任何缺陷;通过低温韧性试验可以看出,在-20℃时,纵向冲击功(5*10mm试样)可达到50j以上,远高于要求值20j
(5*10mm试样)的水平,表明该钢具有良好的低温韧性。
[0062]
实施例2
[0063]
一种低碳当量q420md钢板的化学组分及各组分重量百分含量为:c:0.04~0.06%、si:0.20~0.40%、mn:1.40~1.60%、p:≤0.020%、s:≤0.005%、als:0.015~0.035%、nb:0.025~0.035%、ti:0.035~0.055%,其余为fe及不可避免的杂质;
[0064]
所述低碳当量q420md钢板的制备步骤如下:
[0065]
步骤a、转炉冶炼,高炉冶炼的铁水经转炉冶炼,转炉钢水用挡渣锥和滑板联合挡渣出钢,渣厚38mm,出钢过程中向钢包内加入nbfe合金,mn合金在出钢至1/4到2/3时添加完毕,转炉定氧650ppm,出钢时间4min;
[0066]
步骤b、精炼,转炉出钢后的钢水进精炼工位进行精炼处理,造白渣控铝脱氧,白渣保持时间20min,造白渣后加入tife合金,然后软吹氩,软吹氩时间12min,同时对钢水中的c、si、mn、nb、ti成份进行微调;
[0067]
步骤c、连铸,精炼炉出来的钢水上钢经中间包、结晶器浇注成180mm厚的板坯,浇注过程采用保护浇注,连铸二冷区冷却工艺采用强冷工艺,二冷区比水量1.0l/kg,,二冷区水温在28.0℃;
[0068]
步骤d、加热,连铸板坯进加热炉加热保温,加热段温度为1250℃,均热段温度为1150℃,加热速率为6.6min/cm,加热时间为2.0h;
[0069]
步骤e、粗轧,钢坯出加热炉除鳞去除表面氧化皮后进入粗轧阶段,粗轧开轧温度为1095℃,粗轧终轧温度1005℃,轧制道次为8道次,粗轧末道次圧下率为24%,最小中间坯厚度为40mm;
[0070]
步骤f、精轧,粗轧开坯后随即进行精轧阶段,精轧开轧温度为960℃,精轧终轧温度835℃,精轧道次为6道次,精轧末3道次总圧下率为24%;
[0071]
步骤g、冷却,精轧钢板经冷却后得到成品钢板,精轧钢板进入层流冷却装置进行冷却,终冷温度为600℃,冷却时间为16s,冷却速率为13.4℃/s。
[0072]
获得的最终成品钢板的厚度为12mm。
[0073]
经检验最终成品钢板得知,低碳当量q420md钢板其化学组分及各组分重量百分含量为:c:0.05%、si:0.29%、mn:1.45%、p:0.019%、s:0.003%、als:0.030%、nb:0.035%、ti:0.045%,其余为fe及不可避免的杂质。
[0074]
使用电子显微镜对实施例2制备的低碳当量q420md钢板进行金相组织观察检测,如图2所示,从图2可以看出钢板微观组织均匀细小,晶粒度达到10.0~11.0级。
[0075]
分别使用设备微机屏显液压万能试验机、双立柱金属摆锤冲击试验机和连续弯曲试验机测量实施例2制备的低碳当量q420md钢板的各项力学性能,其中设备微机屏显液压万能试验机测量上屈服强度reh(试样发生屈服而力首次下降前的最大应力);抗拉强度rm(拉伸过程相应最大力fm对应的应力);屈强比reh/rm;延伸率a(试样拉断后标距的增量与原有标距的比值);使用双立柱金属摆锤冲击试验机测量纵向-20℃冲击akv(v型缺口试样在2mm摆锤刀刃下的冲击吸收能量);连续弯曲试验机测量180
°
d=2a冷弯试验,其中,d为弯曲压头直径,a为钢板厚度,冷弯试样进行180
°
弯折,试样表面无裂纹等缺陷,表示冷弯合格;各项力学性能检测结果如表2所示:
[0076]
表2实施例2制备产物各项力学性能测试结果
[0077][0078]
从表2可以看出实施例2制备的低碳当量q420md钢板具有优良的强度、塑性和韧性,其屈服强度达到477mpa,较国标高出57mpa,抗拉强度达到586mpa以上,延伸率达到23%,屈强比reh/rm为0.81,具有较好的冷塑性,冷弯试样表面无任何缺陷;通过低温韧性试验可以看出,在-20℃时,纵向冲击功可达到120j以上,远高于要求值40j的水平,表明该钢具有良好的低温韧性。
[0079]
实施例3
[0080]
一种低碳当量q420md钢板的化学组分及各组分重量百分含量为:c:0.04~0.06%、si:0.20~0.40%、mn:1.40~1.60%、p:≤0.020%、s:≤0.005%、als:0.015~0.035%、nb:0.025~0.035%、ti:0.035~0.055%,其余为fe及不可避免的杂质;
[0081]
所述低碳当量q420md钢板的制备步骤如下:
[0082]
步骤a、转炉冶炼,高炉冶炼的铁水经转炉冶炼,转炉钢水用挡渣锥和滑板联合挡渣出钢,渣厚46mm,出钢过程中向钢包内加入nbfe合金,mn合金在出钢至1/4到2/3时添加完毕,转炉定氧670ppm,出钢时间5min;
[0083]
步骤b、精炼,转炉出钢后的钢水进精炼工位进行精炼处理,造白渣控铝脱氧,白渣保持时间20min,造白渣后加入tife合金,然后软吹氩,软吹氩时间9min,同时对钢水中的c、si、mn、nb、ti成份进行微调;
[0084]
步骤c、连铸,精炼炉出来的钢水上钢经中间包、结晶器浇注成180mm厚的板坯,浇注过程采用保护浇注,连铸二冷区冷却工艺采用强冷工艺,二冷区比水量0.90l/kg,,二冷区水温在26.5℃;
[0085]
步骤d、加热,连铸板坯进加热炉加热保温,加热段温度为1250℃,均热段温度为1180℃,加热速率为8.0min/cm,加热时间为2.4h;
[0086]
步骤e、粗轧,钢坯出加热炉除鳞去除表面氧化皮后进入粗轧阶段,粗轧开轧温度为1110℃,粗轧终轧温度990℃,轧制道次为9道次,粗轧末道次圧下率为22%,最小中间坯厚度为48mm;
[0087]
步骤f、精轧,粗轧开坯后随即进行精轧阶段,精轧开轧温度为940℃,精轧终轧温度825℃,精轧道次为6道次,精轧末3道次总圧下率为22%;
[0088]
步骤g、冷却,精轧钢板经冷却后得到成品钢板,精轧钢板进入层流冷却装置进行冷却,终冷温度为590℃,冷却时间为17s,冷却速率为12.6℃/s。
[0089]
获得的最终成品钢板的厚度为16mm。
[0090]
经检验最终成品钢板得知,低碳当量q420md钢板其化学组分及各组分重量百分含量为:c:0.04%、si:0.32%、mn:1.48%、p:0.017%、s:0.001%、als:0.026%、nb:0.029%、ti:0.035%,其余为fe及不可避免的杂质。
[0091]
使用电子显微镜对实施例3制备的低碳当量q420md钢板进行金相组织观察检测,如图3所示,从图3可以看出钢板微观组织均匀细小,晶粒度达到9.5~10.0级。
[0092]
分别使用设备微机屏显液压万能试验机、双立柱金属摆锤冲击试验机和连续弯曲试验机测量实施例3制备的低碳当量q420md钢板的各项力学性能,其中设备微机屏显液压万能试验机测量上屈服强度reh(试样发生屈服而力首次下降前的最大应力);抗拉强度rm(拉伸过程相应最大力fm对应的应力);屈强比reh/rm;延伸率a(试样拉断后标距的增量与原有标距的比值);使用双立柱金属摆锤冲击试验机测量纵向-20℃冲击akv(v型缺口试样在2mm摆锤刀刃下的冲击吸收能量);连续弯曲试验机测量180
°
d=2a冷弯试验,其中,d为弯曲压头直径,a为钢板厚度,冷弯试样进行180
°
弯折,试样表面无裂纹等缺陷,表示冷弯合格;各项力学性能检测结果如表3所示:
[0093]
表3实施例3制备产物各项力学性能测试结果
[0094][0095]
从表3可以看出实施例3制备的低碳当量q420md钢板具有优良的强度、塑性和韧性,其屈服强度达到468mpa,较国标高出48mpa,有充足富余量,抗拉强度达到579mpa,延伸率达到21.5%,屈强比reh/rm为0.81,具有较好的冷塑性,冷弯试样表面无任何缺陷;通过低温韧性试验可以看出,在-20℃时,纵向冲击功可达到140j以上,远高于要求值40j的水平,表明该钢具有良好的低温韧性。
[0096]
以上所述仅是本发明的优选实施方式,应当指出,对于本技术领域的普通技术人员来说,在不脱离本发明原理的前提下,还可以做出若干改进和润饰,这些改进和润饰也应视为本发明的保护范围。