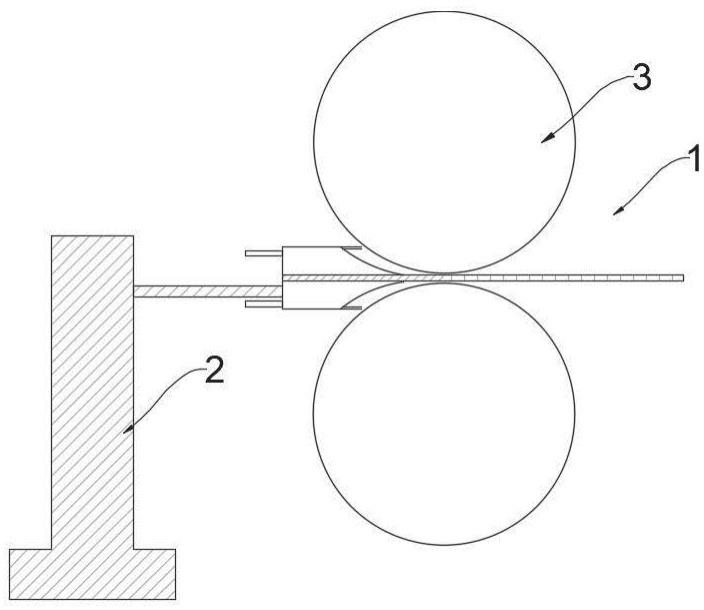
1.本实用新型涉及铝合金材料的铸轧制造技术,特别是铸轧法生产铝合金带材的铸轧设备。
背景技术:2.铸轧也称无锭轧制,是铸造方法与轧制方法的联合成形方法。铸轧是直接将金属熔体“铸造及轧制”成半成品坯或成品材的一种工艺。这种工艺的显著特点是其结晶器为两个带水冷系统的旋转铸轧辊,熔体在其铸轧辊缝间,很短的时间内完成凝固和热轧两个过程,它的优点是熔融的金属液体直接通过旋转的结晶器结晶、铸造、轧制而直接生产出金属材料产品。连续铸轧工艺生产铝合金带材投资少、成本低、流程短、生产效率高,在国内被广泛使用。
3.在连续铸轧生产中,铸轧设备、立板工序各工艺参数的控制是决定铸轧板面质量的关键,而目前工业生产中,铸轧法生产的铝合金带材非常容易出现“虎皮纹”,且这种缺陷很难消除。“虎皮纹”的具体表现是铸轧法生产的铝合金带材经酸液侵蚀后在“虎皮纹”缺陷部位存在不同程度的明暗相间的波浪状条纹,这种铝合金带材冷轧加工后,条纹间隔增大,条纹明暗处的晶粒大小不一。因“虎皮纹”产生原因复杂,当下生产中对铸轧设备、合金成分以及生产工艺方面不断优化。
4.铸轧最为核心的设备包括铸嘴小车和轧辊,轧辊主要由辊体和辊套等组成。工作过程中,轧辊不断旋转,从而辊套表面受到冷热载荷的周期性循环交替作用,使辊套形成了交替变化的温度场,产生相应的热应力,导致辊套的周边表面出现断裂裂纹。随着工作时间的增长,辊套周边表面的断裂裂纹逐渐增多和扩大。而铝为性质比较活泼的有色金属,在自然环境下极易与空气中的氧气发生化学反应生成氧化膜。特别是在高温环境下,活泼金属的氧化反应更为迅速。由于双辊铸轧工艺的固有特性,铸嘴与轧辊之间的间隙处的铝合金熔融液体由于暴露在空气中,必将发生氧化反应并生成氧化膜。氧化膜为硬脆性杂质,特别是在铸轧制过程中非自然形成的氧化膜,存在间断的、随机的、持续的特性。随表面存在裂纹的温度不均匀的轧辊的转动,氧化膜更容易被辊套带到并残留在金属带材的表面,给金属带材生产过程和产品的表面质量造成不利影响,从而在带材表面上形成孔洞或造成断带,从而降低铝合金带材表面质量。
5.现有技术zl201310060633.7,名称:一种消除铸轧板表面虎皮纹的方法。本发明通过在铸轧辊的表面上均匀形成石墨颗粒与氧化物组成的混合涂层层后,通过先生产1系、8系合金合金于铸轧辊辊面上再形成一层三氧化二铝与石墨粒混合而成稳定涂层,从而消除铝铸轧板表面的虎皮纹。但是本发明工艺复杂,且需耗费时间生产1系、8系合金合金,生产成本明显提高。
技术实现要素:6.现有技术铸轧法生产的铝合金圆片存在“虎皮纹”的技术问题,为此本实用新型目
的是提供一种消除铸轧法生产的铝合金圆片表面“虎皮纹”的铸轧设备。
7.本实用新型提出的一种铸轧法生产铝合金带材的铸轧设备包括包括两个相对设置的轧辊,铸轧设备还包括设于两轧辊一侧的铸嘴小车,所述铸嘴小车包括铸嘴小车板、铸嘴、铸嘴压板、耳子和铸嘴挡块,所述铸嘴固定在铸嘴小车板之上,所述铸嘴压板将铸嘴压在其下,铸嘴两侧向外且处于铸嘴压板与铸嘴小车之间依次设有耳子和铸嘴挡块,紧邻铸嘴压板上方设有第一风刀,紧邻铸嘴小车下方设有第二风刀,紧邻铸嘴挡块外侧分别设有第三风刀与第四风刀,风刀设扁口形出风口,出风口朝向轧辊,所述四把风刀与轧辊将铸嘴包围于相对封闭的空间内。
8.具体的,所述轧辊辊体设有冷却回路,冷却回路包括至少一个进液通道和至少一个出液通道,辊体周边表面还设有冷却环槽,辊体周边表面下还设有进液集液管,进液集液管与冷却环槽连通处开设进液集液管出口,所述进液通道和进液集液管间由至少一个进液分支通道相连通,冷却环槽和出液通道间由出液汇集通道相连通,出液汇集通道与冷却环槽连通处开设出液汇集通道入口,进液集液管出口与出液汇集通道入口成对相邻布置且沿辊体周边方向交替布置,冷却环槽内设隔液板,隔液板将相邻成对的进液集液管出口与出液汇集通道入口分隔,隔液板将冷却环槽分隔为不相连通的若干区段。
9.具体的,所述第一风刀和第二风刀为圆弧形曲面。
10.具体的,所述进液集液管与轧辊轴心线平行。
11.具体的,所述进液集液管为不连续的数段。
12.具体的,所述进液通道和出液通道呈盲孔形状,开口处于辊体一端,向与辊体轴心线方向平行延伸,所述进液通道为1个,出液通道为4个,进液通道沿辊体轴心线设置,所述出液通道布设于进液通道外围。
13.具体的,所述进液通道与出液通道数量相等,进液通道与出液通道沿轧辊轴心线间隔交替设置。
14.具体的,所述进液分支通道和出液通道数量优选各为3个。
15.具体的,所述出液汇集通道的轴心线与出液汇集通道入口处冷却环槽的切线垂直相交。
16.具体的,所述所述冷却环槽为圆环形的冷却环槽,冷却环槽圆心与轧辊横剖面的圆心重合,沿轧辊轴心线方向的各进液分支通道之间相互平行,沿轧辊轴心线方向的出液汇集通道之间相互平行。
17.本实用新型的铸轧设备保证铸轧过程中铝合金熔融液体液面相对稳定且不易发生氧化反应,铝合金熔融液体与温度均匀的辊套直接接触并轧制成铝合金带材,从而避免了铝合金带材表面虎皮纹的出现,大大提高了铝合金带材的品质。本发明的铝合金圆片有较高的抗拉强度和延伸率,并具有良好的深冲性、成型性、挺括度,且外观色泽均匀美观。
附图说明
18.图1 本实用新型铸轧设备的结构示意图。
19.图2 本实用新型的铸嘴小车结构示意图。
20.图3 本实用新型的轧辊结构示意图。
21.图4 本实用新型的轧辊横剖结构示意图。
22.图5 本实用新型的轧辊的纵剖结构示意图。
23.图6 本实用新型的另一种轧辊横剖结构示意图。
24.图7 本实用新型的另一种铸嘴小车结构示意图。
25.图号说明:1、双辊铸轧设备;2、铸嘴小车;21、铸嘴小车板;22、铸嘴;23、铸嘴压板;24、耳子;25、铸嘴挡块;26、第一风刀;27、第二风刀;28、第三风刀;29、第四风刀;3、轧辊;31、辊体;311、隔液板;32、辊套;33、冷却回;331、进液通道;332、出液通道;333、冷却环槽;334、进液分支通道;335、出液汇集通道;4、气嘴。
具体实施方式
26.下面详细描述本实用新型的实施例,所描述的实施例均为示例性的,仅用于解释本实用新型,而不能理解为对本实用新型的限制。实施例中未注明具体技术或条件的,按照本领域内的文献所描述的技术或条件或者按照产品说明书进行。所用试剂或仪器未注明生产厂商者,均为可以通过市购获得的常规产品。
27.在本实用新型的描述中,需要理解的是,术语“第一”、“第二”仅用于描述目的,而不能理解为指示或暗示相对重要性或者隐含指明所指示的技术特征的数量。在本实用新型的描述中,“多个”的含义是两个或两个以上,除非另有明确具体的限定。
28.在本说明书的描述中,需要理解的是,术语“一个实施例”或“具体示例”等的描述意指结合该实施例或示例描述的具体特征、结构、材料或者特点包含于本实用新型的至少一个实施例或示例中。在本说明书中,对上述术语的示意性表述不必须针对的是相同的实施例或示例。而且,描述的具体特征、结构、材料或者特点可以在任一个或多个实施例或示例中以合适的方式结合。此外,在不相互矛盾的情况下,本领域的技术人员可以将本说明书中描述的不同实施例或示例以及不同实施例或示例的特征进行结合和组合。
29.本实用新型提出了一种双辊铸轧设备,其结构详细描述如下:如图1所示,所述双辊铸轧设备1包括两个相对设置的轧辊3,两个轧辊间存在一定距离的间隙,该间隙与铸轧出的铝合金带材的厚度相同。所述双辊铸轧设备还包括一个设于两个轧辊一侧的铸嘴小车2。
30.如图1
‑
2所示,本实用新型的一个方面提出的铸嘴小车包括铸嘴小车板21、铸嘴22、铸嘴压板23、耳子24和铸嘴挡块25,所述铸嘴固定在铸嘴小车板之上,所述铸嘴压板将铸嘴压在其下,铸嘴两侧边向外依次设有耳子和铸嘴挡块,所述铸嘴和耳子处于铸嘴压板与铸嘴小车之间且伸入两轧辊间隙。在紧邻铸嘴压板上方设有第一风刀26,紧邻铸嘴小车下方设有第二风刀27,紧邻铸嘴挡块外侧分别设有第三风刀28与第四风刀29,所述第一风刀、第二风刀、第三风刀和第四风刀的风刀口为扁口形,开口朝向轧辊,所述四把风刀与轧辊将铸嘴包围于相对封闭的空间内。风刀尾部设有气嘴4,所述气嘴通过管路连接外设的惰性气源,管路上设有控制气体流量的装置。
31.如图3
‑
5所示,所述轧辊包括辊体31和套于辊体外周的辊套32,所述辊体中还设有冷却回路33。所述冷却回路包括至少一个进液通道331和至少一个出液通道332,进液通道和出液通道呈盲孔形状,开口于辊体一端,向与辊体轴心线方向平行延伸。所述进液通道连接外部冷却液供应管路,出液通道连接外部冷却液排出管路。辊体周边表面还设有若干冷却环槽333,若干冷却环槽形成的轴心线与辊体轴心线重合。辊体周边表面下还设有进液集
液管336,进液集液管与冷却环槽连通处开设进液集液管出口3361,所述进液通道和进液集液管间由至少一个进液分支通道334相连通。冷却环槽和出液通道间由出液汇集通道335相连通,出液汇集通道与冷却环槽连通处开设出液汇集通道入口3351。进液集液管出口与出液汇集通道入口成对相邻布置且沿辊体周边方向交替布置,冷却环槽内设一隔液板311,隔液板将相邻成对的进液集液管出口与出液汇集通道入口分隔,隔液板将冷却环槽分隔为不相连通的若干区段。
32.本实用新型所述的铸嘴小车和轧辊的详细工作过程描述如下:生产前15分钟,打开惰性气源,控制惰性气体以一定流量向风刀供气,风刀向铸轧辊方向喷射惰性气体,形成惰性气体保护圈。后开启两个轧辊,旋转方向彼此相反,冷却液通过进液通道注入辊体,后被分流至进液分支通道,再通过进液分支通道至进液集液管,后经进液集液管出口至冷却环槽,由于隔液板的分隔,冷却液仅可沿顺时针或逆时针的单方向有序流动,冷却液流经冷却环槽,带走辊套的热量,冷却液经由最近的出液汇集通道入口汇集流至出液汇集通道,后依次通过出液通道、冷却液排出管路排出轧辊。因扁口形的四把风刀直吹轧辊体进而形成惰性气体保护圈,保证铝合金熔融液体液面相对稳定。进一步进液集液管布设于辊体周边表面内,其中的冷却液可以初步吸收辊体周边表面的热量,又因隔液板的设置,进液集液管流至冷却环槽的冷却液,仅能沿冷却环槽单方向有序流动,能够更加高效的带走辊套的热量,从而更好的保持辊套处于一个恒定且较低的温度。当铝合金熔融液体通过铸嘴注入两个辊体之间间隙的一侧,惰性气体圈保证铝合金熔融液体液面相对稳定且不易发生氧化反应,温度均匀的辊套与铝合金熔融液体直接接触并将其轧制成铝合金带材,从而避免了铝合金带材表面水泼纹的出现,大大提高了铝合金带材的品质。
33.根据本实用新型的一个具体实施例,如图7所示,本实用新型的铸嘴小车的第一风刀26和第二风刀27呈圆弧形曲面。
34.根据本实用新型的一个具体实施例,如图4所示,所述冷却回路包括1个进液通道和4个出液通道332,辊体周边表面内还设有4根进液集液管,进液集液管与冷却环槽连通处开设进液集液管出口,所述进液通道和进液集液管间由进液分支通道相连通。冷却环槽和出液通道间由出液汇集通道相连通,出液汇集通道与冷却环槽连通处开设出液汇集通道入口。进液集液管出口与出液汇集通道入口成对相邻布置且沿辊体周边方向交替布置,冷却环槽内设隔液板,隔液板将相邻成对的进液集液管出口与出液汇集通道入口分隔,隔液板将冷却环槽分隔为不相连通的若干区段。
35.根据本实用新型的一个具体实施例,如图5所示,所述述进液集液管与轧辊轴心线平行设置,所述进液集液管为不连续的数段。
36.根据本实用新型的一个具体实施例,如图6所示,所述进液通道与出液通道数量相等,进液通道与出液通道围绕轧辊轴心线成对间隔布设。
37.根据本实用新型的一个具体实施例,如图6所示,所述冷却回路优选为3个进液通道和3个出液通道,进液通道和出液通道呈盲孔形状,开口于辊体一端。所述3个进液通道和3个出液通道围绕轧辊轴心线成对间隔布设。
38.根据本实用新型的一个具体实施例,如图6所示,出液汇集通道的长轴心线与出液汇集通道入口处冷却环槽的切线相垂直。
39.根据本实用新型的一个具体实施例,如图3所示,冷却环槽为圆环形冷却环槽,各
冷却环槽间相互独立,冷却环槽圆心与轧辊横剖面的圆心重合。
40.根据本实用新型的一个具体实施例,沿轧辊轴心线方向的各进液分支通道之间相互平行,沿轧辊轴心线方向的出液汇集通道之间相互平行。
41.尽管上面已经示出和描述了本发明的实施例,可以理解的是,上述实施例是示例性的,不能理解为对本发明的限制。在不脱离本发明精神和范围的前提下,本发明还会有各种变化和改进,这些变化和改进都落入要求保护的本发明范围内。