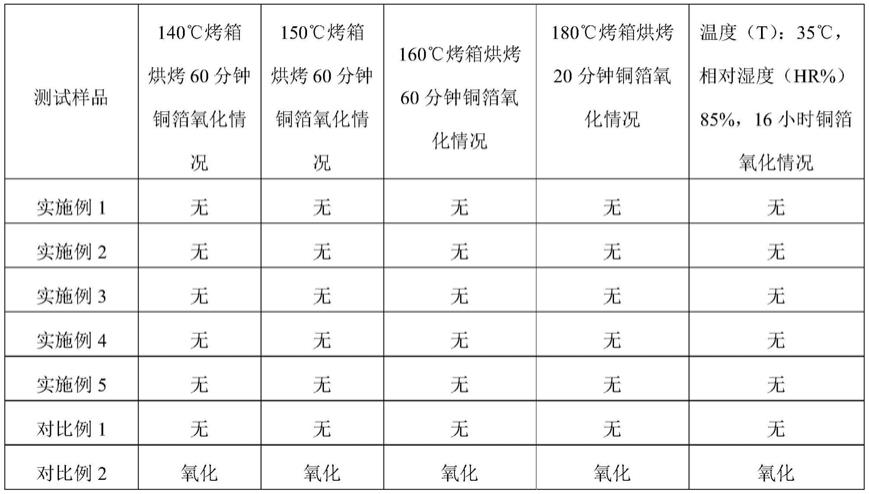
1.本发明涉及一种锂离子电池用电解铜箔防氧化液,更具体地说,尤其涉及一种锂离子电池用电解铜箔低铬无水洗防氧化液。本发明同时还涉及采用该无水洗防氧化液的无水洗防氧化工艺。
背景技术:2.常用的锂离子电池用的连体机电解铜箔生箔制造工序,防氧化液主要包括以下两种:
①
镀铬、锌的工艺:生成铜箔—酸洗—水洗—烘干—铜箔剥离—防氧化处理—水洗—挤压水—收卷前烘干—收卷。在防氧化处理过程中,现有的防氧化剂为酸性或碱性cr、zn为主的化合物组金属防氧化膜,使其与空气隔绝,达到抗氧化目的。
②
有机防氧化液:生成铜箔—酸洗—水洗—烘干—铜箔剥离—防氧化处理—挤压水—收卷前烘干—收卷。在防氧化处理过程中,可以在电解铜箔表面形成均匀的聚合络合薄膜为主的化合物组金属防氧化膜,使其与空气隔绝,达到抗氧化目的。
3.上述防氧化工艺在生产超薄电解铜箔时易产生如下问题:
①
镀铬、锌防氧化工艺:不进行水洗铜箔表面易出现黄色条纹色差、水点印、小红点、小黑点色差等外观问题;
②
有机防氧化工艺虽然可以不用水洗,其抗氧化能力只能达到150度10分钟效果。
4.另外,使用含铬、锌防氧化工艺或使用含(bta)苯骈三氮唑等一种或多种组合物有机防氧化工艺,防氧化钝化液还存在以下缺点和不足:
5.①
防氧化钝化液中含有锌,电沉积后在铜箔表面形成金属锌,锌单质在电池内电解质下能形成原电池,降低电池的容量和充放电性能,甚至引起爆炸。
②
在使用含铬、锌的防氧化钝化液进行防氧化处理后,还需经过水洗,而水洗的装置包括1个泵和2条喷管,需要耗费大量的电能和纯水,后续还会产生废水,这不仅污染环境,而且会增加水处理成本。
6.无铬免水洗防氧化液工艺,达到杜绝水洗,减少水处理成本,不含六价铬等对环境有害物质。但是,我们在实际使用后发现,防氧化液在使用一段时间后,由于铜箔带入的少量硫酸铜溶液等不断积累,使原本透明的防氧化液出现变化,使得防氧化处理后的铜箔表面出现白色条纹色差,也即说明硫酸铜的带入会使有机防氧化液出现防氧化效果变差的问题,因此有机防氧化液在使用一周左右后就需要进行更换,而更换防氧化液需要停机操作,又影响产品产量及生产的稳定性。同时,因为有机防氧化液中随着使用时间的不断加长,液体中cod、氨氮含量逐步累积,换液会产生大量废水,又会增加水处理成本。
技术实现要素:7.本发明的前一目的在于针对上述现有技术的不足,提供一种不含降低电池性能的锌单质,而且不需要水洗,在防氧化处理工序上不会产生废水污染环境,既环保又节约成本的锂离子电池用电解铜箔低铬无水洗防氧化液。
8.本发明的后一目的在于提供一种采用上述低铬无水洗防氧化液的无水洗防氧化
工艺。
9.本发明的前一技术方案是这样实现的:一种锂离子电池用电解铜箔低铬无水洗防氧化液,该防氧化液包括下述组分:三氧化铬0.3-5g/l、葡萄糖1-5g/l、柠檬酸1-10g/l、硼酸5-20g/l、重铬酸钾0.1-3g/l和重铬酸钠0.1-0.3g/l。
10.上述的一种锂离子电池用电解铜箔低铬无水洗防氧化液,该防氧化液包括下述组分:三氧化铬2-3g/l、葡萄糖2.5-3.5g/l、柠檬酸4-6g/l、硼酸10-15g/l、重铬酸钾0.8-1.5g/l和重铬酸钠0.15-0.25g/l。
11.上述的一种锂离子电池用电解铜箔低铬无水洗防氧化液,该低铬无水洗防氧化液的电导率为60-150μs/cm。
12.上述的一种锂离子电池用电解铜箔低铬无水洗防氧化液,该低铬无水洗防氧化液的ph值为2-4。
13.本发明采用上述配方后,三氧化铬、重铬酸钠的添加可以修复铜箔的表面细小划痕,使其在防氧化处理过程中,形成均匀的钝化膜。
14.葡萄糖是化学中一种良好的配合剂几乎能与所有的金属离子形成稳定的螯合物。在配方中,葡萄糖的主要作用是用于控制cod的含量,cod作为有机物相对含量的综合指标之一,如果防氧化液中cod过高,当铜箔经160度烤后,会在表面出现小红点或小黑点,影响铜箔品质甚至造成铜箔不合格。
15.柠檬酸的主要作用是:
①
除垢作用,导电辊通电、挤水辊长时间通电运行后会产生结垢,添加柠檬酸有效减少结垢生产;
②
调节防氧化液中的ph值,使防氧化液在合适的ph条件下发挥防氧化钝化作用。
16.本发明通过对上述组分的选择,并优选其配比,将三氧化铬、重铬酸钠、葡萄糖和柠檬酸配制于同一溶液体系中,并协同作用,与现有技术相比,具有下述的有益效果:
17.①
本发明提供的电解铜箔的低铬防氧化液,不含有降低电池性能的锌单质,能在电解铜箔表面形成均匀的聚合络合薄膜,保证了锂离子电池用电解铜箔的常温高温抗氧化性能,满足客户要求。
18.②
使用本发明的低铬防氧化液,对电解铜箔进行防氧化钝化,提高铜箔的外观质量,避免防氧化液在使用一段时间后会出现防氧化液变色以及导电辊和挤水辊产生结垢,造成铜箔表面出现黄色条纹色差、压印、打折、小红点、小黑点、小蓝点等外观问题,由于钝化膜均匀一致,避免分切后切边端部存放后氧化,保持了电解铜箔较高的浸润性和导电性。
19.③
采用酸性的低铬防氧化液,使其避免了水洗的工序,不仅节约了生产成本,而且不产生含铬废水,环保不污染环境。
20.本发明的后一技术方案是这样实现的:一种无水洗防氧化工艺包括下述步骤:
21.(1)将生箔机制得的铜箔,依序经酸洗、纯水水洗和热风烘干后进行剥离;
22.(2)剥离后的铜箔采用权利要求1所述锂离子电池用电解铜箔低铬无水洗防氧化液进行防氧化处理;
23.(3)采用气动自压式挤液将铜箔表面的防氧化液挤压回防氧化槽;
24.(4)依序经烘干、收卷和分切后得成品电解铜箔。
25.上述的一种无水洗防氧化工艺,步骤(2)中,进行防氧化处理时,防氧化槽内防氧化液温度为25-35℃、供液量≥28立方米/小时、溶剂为电导率<4μs/cm的去离子水、防氧化
处理时间为6s。
26.上述的一种无水洗防氧化工艺,步骤(2)中,在进行防氧化处理时,对铜箔进行电镀处理,电流密度为1-6a/dm2。
27.上述的一种无水洗防氧化工艺,步骤(3)中,采用气动自压式结构控制挤液辊,由挤液辊和导电辊配合将铜箔表面的防氧化液挤压回防氧化槽,在电镀时,向挤液辊和导电辊喷淋防氧化液。
28.本发明采用上述工艺后,其采用上述经过优选组分的低铬防氧化液,无需水洗,减少了电解铜箔生产过程中的一道工序,不仅节约了生产成本,而且不产生含铬废水,环保不污染环境。
具体实施方式
29.下面结合具体实施例对本发明作进一步的详细说明,但并不构成对本发明的任何限制。
30.本发明的一种锂离子电池用电解铜箔低铬无水洗防氧化液,该防氧化液包括下述组分:三氧化铬0.3-5g/l、葡萄糖1-5g/l、柠檬酸1-10g/l、硼酸5-20g/l、重铬酸钾0.1-3g/l和重铬酸钠0.1-0.3g/l。优选地,该防氧化液包括下述组分:三氧化铬2-3g/l、葡萄糖2.5-3.5g/l、柠檬酸4-6g/l、硼酸10-15g/l、重铬酸钾0.8-1.5g/l和重铬酸钠0.15-0.25g/l。该防氧化液采用的溶剂为电导率<4μs/cm的去离子水。
31.同时,本发明防氧化液的ph值为2-4。根据单独使用不同种类酸或各类酸的混合调节ph值,连续试生产试验发现使用柠檬酸和硼酸相结合对调节ph值效果最好,防氧化液不会变色,且高温180度抗氧化10分保持铜箔原有色泽。使用硫酸、硝酸以及硫酸、硝酸和柠檬酸及硼酸等的组合调节ph值时,防氧化液使用48-72小时开始由深黄色转变为黄绿色,同时箔面出现整幅黄色色差,高温180度抗氧化10分钟严重变色。不同种类酸调整ph值跟进存放后15天、30天、45天、60天、90天对比,使用柠檬酸和硼酸相结合调整ph值箔存放90天无异常,铜箔表面无色差。使用硫酸和硝酸等的组合调整ph值时,存放30天开箱检查箔面出现轻微黄色色差。
32.将防氧化液配制成酸性,在保留低铬含量的前提下,实现了不水洗,且有效保证了防氧化的效果。
33.进一步优选地,该低铬无水洗防氧化液的电导率为60-150μs/cm。电导率过低或过高均会影响抗氧化性能。
34.一种采用上述低铬无水洗防氧化液的无水洗防氧化工艺,包括下述步骤:
35.(1)将生箔机制得的铜箔,依序经酸洗、纯水水洗和热风烘干后进行剥离;酸洗液的酸含量为105-115g/l、铜含量为80-85g/l;纯水水洗压力为2mpa,纯水电导率<4μs/cm;生箔机制备电解铜箔的工艺为现有技术,非本发明所要保护的技术点,在此不再赘述。
36.(2)剥离后的铜箔采用上述锂离子电池用电解铜箔低铬无水洗防氧化液进行防氧化处理;进行防氧化处理时,防氧化槽内防氧化液温度为25-35℃、供液量≥28立方米/小时、溶剂为电导率<4μs/cm的去离子水、防氧化处理时间为6s。在进行防氧化处理时,对铜箔进行电镀处理,电流密度为1-6a/dm2。
37.(3)采用气动自压式结构控制挤液辊,由挤液辊和导电辊配合将铜箔表面的防氧
化液挤压回防氧化槽,在电镀时,向挤液辊和导电辊喷淋防氧化液;
38.(4)依序经160℃热风烘干、收卷和分切后得成品电解铜箔。
39.实验例1
40.低铬无水洗防氧化液配方:三氧化铬0.3g/l、葡萄糖1g/l、柠檬酸1g/l、硼酸5g/l、重铬酸钾0.1g/l和重铬酸钠0.1g/l,溶剂为电导率<4μs/cm去离子水;其中,低铬防氧化液的ph为2、电导率为60μs/cm。
41.无水洗防氧化工艺,包括以下步骤:
42.(1)将生箔机制得的铜箔,依序经酸洗、纯水水洗和热风烘干后进行剥离;酸洗液的酸含量为105-115g/l、铜含量为80-85g/l;纯水水洗压力为2mpa,纯水电导率<4μs/cm;
43.(2)剥离后的铜箔采用上述锂离子电池用电解铜箔低铬无水洗防氧化液进行防氧化处理;进行防氧化处理时,防氧化槽内防氧化液温度为25℃、供液量≥28立方米/小时、溶剂为电导率<4μs/cm的去离子水、防氧化处理时间为6s。在进行防氧化处理时,对铜箔进行电镀处理,电流密度为1a/dm2。
44.(3)采用气动自压式结构控制挤液辊,由挤液辊和导电辊配合将铜箔表面的防氧化液挤压回防氧化槽,在电镀时,向挤液辊和导电辊喷淋防氧化液;
45.(4)依序经160℃热风烘干、收卷和分切后得成品电解铜箔。
46.实验例2
47.低铬无水洗防氧化液配方:三氧化铬2g/l、葡萄糖2.5g/l、柠檬酸4g/l、硼酸10g/l、重铬酸钾0.8g/l和重铬酸钠0.15g/l,溶剂为电导率<4μs/cm去离子水;其中,低铬防氧化液的ph为2.5、电导率为80μs/cm。
48.无水洗防氧化工艺,包括以下步骤:
49.(1)将生箔机制得的铜箔,依序经酸洗、纯水水洗和热风烘干后进行剥离;酸洗液的酸含量为105-115g/l、铜含量为80-85g/l;纯水水洗压力为2mpa,纯水电导率<4μs/cm;
50.(2)剥离后的铜箔采用上述锂离子电池用电解铜箔低铬无水洗防氧化液进行防氧化处理;进行防氧化处理时,防氧化槽内防氧化液温度为28℃、供液量≥28立方米/小时、溶剂为电导率<4μs/cm的去离子水、防氧化处理时间为6s。在进行防氧化处理时,对铜箔进行电镀处理,电流密度为2a/dm2。
51.(3)采用气动自压式结构控制挤液辊,由挤液辊和导电辊配合将铜箔表面的防氧化液挤压回防氧化槽,在电镀时,向挤液辊和导电辊喷淋防氧化液;
52.(4)依序经160℃热风烘干、收卷和分切后得成品电解铜箔。
53.实验例3
54.低铬无水洗防氧化液配方:三氧化铬2.5g/l、葡萄糖3g/l、柠檬酸5g/l、硼酸12g/l、重铬酸钾1g/l和重铬酸钠0.2g/l,溶剂为电导率<4μs/cm去离子水;其中,低铬防氧化液的ph为3、电导率为100μs/cm。
55.无水洗防氧化工艺,包括以下步骤:
56.(1)将生箔机制得的铜箔,依序经酸洗、纯水水洗和热风烘干后进行剥离;酸洗液的酸含量为105-115g/l、铜含量为80-85g/l;纯水水洗压力为2mpa,纯水电导率<4μs/cm;
57.(2)剥离后的铜箔采用上述锂离子电池用电解铜箔低铬无水洗防氧化液进行防氧化处理;进行防氧化处理时,防氧化槽内防氧化液温度为30℃、供液量≥28立方米/小时、溶
剂为电导率<4μs/cm的去离子水、防氧化处理时间为6s。在进行防氧化处理时,对铜箔进行电镀处理,电流密度为3a/dm2。
58.(3)采用气动自压式结构控制挤液辊,由挤液辊和导电辊配合将铜箔表面的防氧化液挤压回防氧化槽,在电镀时,向挤液辊和导电辊喷淋防氧化液;
59.(4)依序经160℃热风烘干、收卷和分切后得成品电解铜箔。
60.实验例4
61.低铬无水洗防氧化液配方:三氧化铬3g/l、葡萄糖3.5g/l、柠檬酸6g/l、硼酸15g/l、重铬酸钾1.5g/l和重铬酸钠0.25g/l,溶剂为电导率<4μs/cm去离子水;其中,低铬防氧化液的ph为3.5、电导率为120μs/cm。
62.无水洗防氧化工艺,包括以下步骤:
63.(1)将生箔机制得的铜箔,依序经酸洗、纯水水洗和热风烘干后进行剥离;酸洗液的酸含量为105-115g/l、铜含量为80-85g/l;纯水水洗压力为2mpa,纯水电导率<4μs/cm;
64.(2)剥离后的铜箔采用上述锂离子电池用电解铜箔低铬无水洗防氧化液进行防氧化处理;进行防氧化处理时,防氧化槽内防氧化液温度为32℃、供液量≥28立方米/小时、溶剂为电导率<4μs/cm的去离子水、防氧化处理时间为6s。在进行防氧化处理时,对铜箔进行电镀处理,电流密度为4a/dm2。
65.(3)采用气动自压式结构控制挤液辊,由挤液辊和导电辊配合将铜箔表面的防氧化液挤压回防氧化槽,在电镀时,向挤液辊和导电辊喷淋防氧化液;
66.(4)依序经160℃热风烘干、收卷和分切后得成品电解铜箔。
67.实验例5
68.低铬无水洗防氧化液配方:三氧化铬5g/l、葡萄糖5g/l、柠檬酸10g/l、硼酸20g/l、重铬酸钾3g/l和重铬酸钠0.3g/l,溶剂为电导率<4μs/cm去离子水;其中,低铬防氧化液的ph为4、电导率为150μs/cm。
69.无水洗防氧化工艺,包括以下步骤:
70.(1)将生箔机制得的铜箔,依序经酸洗、纯水水洗和热风烘干后进行剥离;酸洗液的酸含量为105-115g/l、铜含量为80-85g/l;纯水水洗压力为2mpa,纯水电导率<4μs/cm;
71.(2)剥离后的铜箔采用上述锂离子电池用电解铜箔低铬无水洗防氧化液进行防氧化处理;进行防氧化处理时,防氧化槽内防氧化液温度为35℃、供液量≥28立方米/小时、溶剂为电导率<4μs/cm的去离子水、防氧化处理时间为6s。在进行防氧化处理时,对铜箔进行电镀处理,电流密度为6a/dm2。
72.(3)采用气动自压式结构控制挤液辊,由挤液辊和导电辊配合将铜箔表面的防氧化液挤压回防氧化槽,在电镀时,向挤液辊和导电辊喷淋防氧化液;
73.(4)依序经160℃热风烘干、收卷和分切后得成品电解铜箔。
74.对比例1含铬、锌防氧化液水洗工艺
75.含铬、锌防氧化液配方:1.4g/l的重铬酸钠、5.875g/l葡萄糖、七水硫酸锌4.3g/l、硼酸5.785g/l,溶剂:去离子水电导率<4μs/cm;其中,含铬、锌防氧化液的ph为4。
76.上述含铬、锌防氧化液的有水洗防氧化工艺,包括以下步骤:
77.(1)将生箔机制得的铜箔,依序经酸洗、纯水水洗和热风烘干后进行剥离;酸洗液的酸含量为105-115g/l、铜含量为80-85g/l;纯水水洗压力为2mpa,纯水电导率<4μs/cm;
78.(2)剥离后的铜箔采用上述锂离子电池用电解铜箔含铬、锌防氧化液进行防氧化处理;进行防氧化处理时,防氧化槽内防氧化液温度为25-35℃、供液量≥28立方米/小时、溶剂为电导率<4μs/cm的去离子水、防氧化处理时间为6s。在进行防氧化处理时,对铜箔进行电镀处理,电流密度为1-6a/dm2。
79.(3)采用2mpa压力、电导率<4μs/cm的纯水水洗铜箔光面和毛面。
80.(4)采用气动自压式结构控制挤液辊,由挤液辊和导电辊配合将铜箔表面的防氧化液挤压回防氧化槽,在电镀时,向挤液辊和导电辊喷淋防氧化液。
81.(5)依序经160℃热风烘干、收卷和分切后得成品电解铜箔。
82.对比例2含铬、锌防氧化液无水洗工艺
83.含铬、锌防氧化液配方:与对比例1相同。
84.防氧化工艺与对比例1相比,省去了步骤(3)的水洗工序。其余相同。
85.防氧化测试实验
86.将实施例1-实施例5和对比例1、对比例2制得的铜箔产品进行防氧化测试,测试结果如下:
87.表1实施例1-实施例5和对比例1、对比例2的铜箔产品进行防氧化测试结果
[0088][0089]
由表1的测试结果可以看出,只是使用含铬、锌的防氧化钝化液,不进行水洗几乎对铜箔无保护效果,而采用上述低铬防氧化液的铜箔,防氧化效果非常好,可以在电解铜箔表面形成均匀的聚合络合薄膜,保证了锂离子电池用电解铜箔的常温高温抗氧化性能,具有良好的抗腐蚀保护作用,满足客户要求。
[0090]
另外,在进行防氧化测试时发现,将实施例1-5及对比例1和2制备的电解铜箔在分切结束后,不进行端部防氧化处理,即时用无油保鲜膜将整卷铜箔密封包好,纸管两端用电工胶带缠绕。(实施例1-5、对比例1-2样品各准备6箱,平均分配存放在车间和仓库两个地方,按以前分切后端部不做防氧化处理出现氧化经验,前一个月间隔7天开箱检查箔面、切边端部情况。之后每半个月开箱检查一次,实施例1-5制备的铜箔存放3个月,端部、箔面均未出现氧化问题。而对比例1存放42天开箱检查出现端部氧化变色问题,比例2存放7天开箱
检查出现端部、及铜箔毛面氧化变色问题。)
[0091]
针对上述现象,技术人员进行了实验分析,截止申请时,仍未发现避免端部氧化的原因。
[0092]
上述意外发现,可以使任意宽幅的切面起到良好的防氧化作用,符合量产要求,不必每种宽幅分切后进行防氧化端部喷淋防氧化雾化液工序。
[0093]
以上所举实施例为本发明的较佳实施方式,仅用来方便说明本发明,并非对本发明作任何形式上的限制,任何所属技术领域中具有通常知识者,若在不脱离本发明所提技术特征的范围内,利用本发明所揭示技术内容所作出局部更动或修饰的等效实施例,并且未脱离本发明的技术特征内容,均仍属于本发明技术特征的范围内。