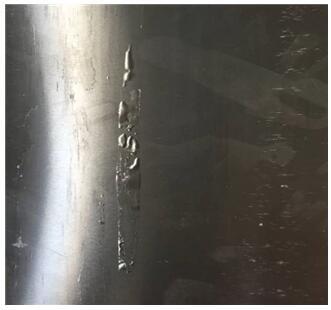
1.本发明涉及一种提高冷轧深冲钢表面质量的方法,属于冶炼及轧制工艺技术领域。
背景技术:2.冷轧深冲钢是一种超低碳钢,其特点是c、n含量低,并加入一定量的nb、ti等微合金元素形成碳氮化物,从而使钢中没有c、n间隙原子的存在,故称为无间隙原子钢。由于其优良的成型性和深冲性而广泛应用于汽车用结构件和工程机械用覆盖件等领域。由于冷轧深冲钢要求c、n含量极低,纯净度要求高,目前现有技术生产仍然存在一定的质量问题,主要表现就是钢水纯净度不佳,钢板经冷轧后会出现起皮、线状缺陷,影响钢板的表面质量。
3.冷轧深冲钢产品市场前景广阔,技术要求高、生产难度大,对生产线的工艺与装备一体化系统控制要求高。因此,为解决这一问题,提出一种高表面质量冷轧深冲钢的控制方法,可改善钢水纯净度,有效控制热轧钢带氧化皮厚度,提高冷轧钢板的表面质量。
技术实现要素:4.为了克服上述不足,本发明旨在提供一种提高冷轧深冲钢表面质量的方法,所生产钢板的纯净度高,夹杂物少,冷轧后钢板的表面质量优良。
5.本发明提供的一种提高冷轧深冲钢表面质量的方法,包括如下步骤:铁水预处理
→
转炉冶炼
→
炉外精炼(rh)
→
连铸
→
连铸坯加热
→
粗轧
→
精轧
→
层流冷却
→
卷取
→
酸洗
→
冷轧。具有步骤如下:(1)铁水预处理:高炉铁水在铁水预处理工序进行喷吹镁粉或石灰粉进行脱硫,经铁水预处理后,硫含量≤0.003%。
6.(2)转炉冶炼:转炉冶炼进行脱磷、脱碳,提高钢水纯净度,出钢温度满足炉外精炼(rh)的要求。
7.(3)炉外精炼(rh):rh进行深脱碳、脱气(n、o等),提高钢水纯净度。
8.(4)连铸:将冶炼合格的钢水浇注成合格的连铸坯。
9.(5)连铸坯加热:连铸坯加热到一定的加热温度,不仅能保证微合金元素充分固溶,还能降低轧机的负荷。
10.(6)粗轧:粗轧是经过多道次大变形轧制将连铸坯轧制成一定厚度的中间坯。
11.(7)精轧:精轧是将粗轧后的中间坯经多机架精轧机连续轧制成更小厚度的带钢。
12.(8)层流冷却:精轧后的带钢经过层流冷却,保证带钢的卷取温度和力学性能。
13.(9)卷取:带钢在一定的卷取温度下卷取成钢卷,卷取温度直接影响到钢板的的组织和性能。
14.(10)酸洗:钢板经酸洗去除表面氧化铁皮,保证钢板表面质量。
15.(11)冷轧:将酸洗后的钢板冷轧至成品厚度。
16.本发明所采用的技术方案是:
(1)转炉终点控制c*o积(碳的质量百分含量与氧的质量百分含量二者的乘积)在(0.0018-0.0020)
×
10-4
,可有效达到c、o平衡,冶炼效果好。转炉出钢前进行大流量(氩气流量为0.12-0.14nm3/(t
•
min))底吹搅拌1-3min。转炉终点[o]≤850ppm,转炉出钢通过有效控制氧含量,可降低钢水碳含量,减少rh脱碳量。
[0017]
(2)转炉出钢采用滑板挡渣,下渣量≤40mm,随后进行炉后扒渣,保证渣层厚度<15mm。通过采用低氧化渣控制技术,可降低成品p含量,提高钢水纯净度。
[0018]
(3)转炉出钢后加入改质剂(改质剂成分为cao:40-50%、al2o3:30-40%、al:10-12%、其它杂质成分≤10%进行炉渣改性,渣中feo≤5%,可有效降低炉渣中的氧化性。所述百分含量是质量比。
[0019]
(4)rh到站到抽真空时间≤6min,rh到站温度≥1650℃,能够提高脱碳效率。
[0020]
(5)rh脱碳结束加铝后循环时间控制在6-8min,保证足够的rh循环时间,使钢中的脱氧产物充分上浮、去除。
[0021]
(6)rh破空到连铸开浇之间的镇静时间大于30min,保证足够的镇静时间,使钢中的脱氧产物充分上浮、去除。
[0022]
(7)连铸过程采用中包内用氩气清扫、填充,进行氩气保护,防止二次氧化。
[0023]
(8)连铸坯经加热炉加热后进行粗轧和精轧,精轧时投入机架间冷却水量控制在60-80%(针对机架间冷却水喷水口的投入量),采用润滑轧制可改善钢带表面氧化皮与基体间的结合力状态,精轧终轧温度控制在850-890℃,在较低的温度下终轧,可减少钢带表面的氧化皮厚度,易于酸洗。
[0024]
(9)钢带精轧后采用层流冷却方式冷却,冷却速率控制在20-25℃/s,通过较快的冷却速率来防止或减轻feo转化成fe3o4。层流冷却每组上、下水比控制在4∶6每组上、下水比使得钢带上、下表面沿板宽方向能够保持良好的冷却均匀性,从而提高氧化皮的厚度均匀性,提高酸洗效果。
[0025]
此处层流冷却分为上、下两处进水,层流冷却包含若干组水管,每组水管分为上水管和下水管,上水管和下水管上均分布着10个喷水口,上、下水比4∶6即意味着上水管开4个喷水口喷到带钢的上表面,下水管开6个喷水口喷到带钢的下表面。
[0026]
(10)钢带冷却后卷取,卷取温度控制在550-650℃,合理的卷取温度既能保证力学性能,又可以抑制feo的转化,减少钢带表面的氧化皮厚度,易于酸洗。
[0027]
(11)钢板经酸洗去除氧化皮后冷轧,冷轧机工作辊的表面粗糙度ra控制在1.0-1.2μm,既能保证轧制稳定性,又能提高冷轧钢板的表面质量。
[0028]
上述的高表面质量冷轧深冲钢的控制方法,其特征是:步骤(1)转炉出钢时通过有效控制氧含量,可降低钢水碳含量,减少rh脱碳量;步骤(2)通过采用低氧化渣控制技术,可降低成品p含量,提高钢水纯净度;步骤(3)转炉出钢后通过加入合适的改质剂,可有效降低炉渣中的氧化性;步骤(4)通过控制rh抽真空时间和到站温度,能够有效提高脱碳效率;步骤(5)通过保证足够的rh循环时间,使钢中的脱氧产物充分上浮、去除。步骤(6)通过保证足够的连铸开浇前镇静时间,使钢中的夹杂物充分上浮。步骤(7)连铸时通过保护浇铸,能防止二次氧化。步骤(8)通过控制机架间冷却水量和精轧终轧温度,可改善钢带表面氧化皮与基体间的应力状态,并减少钢带表面的氧化皮厚度,易于酸洗。步骤(9)通过控制层流冷却的冷却速率和上、下水比,能防止或减轻feo转化成fe3o4,并提高氧化皮的厚度均匀性,提高
酸洗效果。步骤(10)通过控制合理的卷取温度,既能保证力学性能,又可以抑制feo的转化,减少钢带表面的氧化皮厚度,易于酸洗。步骤(11)通过控制冷轧机工作辊的表面粗糙度,既能保证轧制稳定性,又能提高冷轧钢板的表面质量。
[0029]
本发明的有益效果:采用该高表面质量冷轧深冲钢控制方法,可以减少转炉出钢钢水过氧化程度,降低炉渣中的氧化性,减少脱氧产物al2o3生成量,提高钢水纯净度水平,钢中o含量可控制在0.0018%(质量含量)以下,p含量可控制在0.0009%以下;热轧钢带表面的氧化皮厚度能够减薄到7μm以下,易于酸洗;冷轧后钢板表面反射率能达到85%以上,冷轧钢板的表面质量优良。
附图说明
[0030]
图1是未采用本发明方法冷轧后的钢板表面起皮缺陷情况;图2是实施例2中所得冷轧深冲钢的表面情况。
具体实施方式
[0031]
下面结合实施例详细说明本发明的具体实施方式,但本发明的具体实施方式不局限于下述的实施例。
[0032]
实施例一本高表面质量冷轧深冲钢的控制方法的实施例为下述依次的步骤:(1)铁水预处理:高炉铁水在铁水预处理工序进行喷吹镁粉或石灰粉进行脱硫,经铁水预处理后,硫含量≤0.005%。
[0033]
(2)转炉冶炼:
①
转炉终点控制c*o积在0.0018
×
10-4
,转炉出钢前进行大流量(0.14nm3/(t
•
min))底吹搅拌2min。转炉终点[o]为850ppm。
[0034]
②
转炉出钢采用滑板挡渣,下渣量35mm,随后进行炉后扒渣,渣层厚度14mm。
[0035]
③
转炉出钢后加入改质剂(改质剂成分为cao:45%、al2o3:35%、al:10%、其它杂质成分≤10%)进行炉渣改性,渣中feo为5%。
[0036]
(3)炉外精炼(rh):
①
rh到站到抽真空时间5min,rh到站温度1650℃。
[0037]
②
rh脱碳结束加铝后循环时间控制在7min。
[0038]
③
rh破空到连铸开浇之间的镇静时间36min。
[0039]
(4)连铸:连铸过程采用中包内用氩气清扫、填充,进行氩气保护,防止二次氧化。将冶炼合格的钢水浇注成合格的连铸坯,连铸坯厚度230mm。
[0040]
(5)连铸坯加热:将连铸坯加热到1200℃,保证微合金元素充分固溶。
[0041]
(6)粗轧:经过多道次大变形轧制将连铸坯轧制成厚度为40mm的中间坯。
[0042]
(7)精轧:将粗轧后的中间坯经多机架精轧机连续轧制成厚度为9mm的带钢,精轧时投入机架间冷却水量70%,精轧终轧温度870℃。
[0043]
(8)层流冷却:钢带精轧后采用层流冷却方式冷却,冷却速率23℃/s,层流冷却每组上、下水比4∶6。
[0044]
(9)卷取:钢带冷却后卷取,卷取温度610℃。
[0045]
(10)酸洗:钢板经酸洗后去除表面氧化铁皮,保证钢板表面质量。
[0046]
(11)冷轧:钢板经酸洗后冷轧,冷轧机工作辊的表面粗糙度ra :1.2μm。
[0047]
采用该方法生产的冷轧深冲钢的化学成分的质量百分配比如下:c:0.004%,si:0.01%,mn:0.15%,s:0.004%,ti:0.04%,al:0.05%,n:0.0020%, o:0.0018%,p:0.0009%,其余为fe与不可避免的杂质。钢水纯净度水平高,冷轧后钢板表面反射率为87%(冷轧后钢板表面反射率达到70%以上,即认为达到较好的表面质量),冷轧钢板的表面质量优良。
[0048]
实施例二本高表面质量冷轧深冲钢的控制方法的实施例为下述依次的步骤:(1)铁水预处理:高炉铁水在铁水预处理工序进行喷吹镁粉或石灰粉进行脱硫,经铁水预处理后,硫含量≤0.005%。
[0049]
(2)转炉冶炼:
①
转炉终点控制c*o积在0.0020
×
10-4
,转炉出钢前进行大流量(0.13nm3/(t
•
min))底吹搅拌1min。转炉终点[o]为800ppm。
[0050]
②
转炉出钢采用滑板挡渣,下渣量40mm,随后进行炉后扒渣,渣层厚度13mm。
[0051]
③
转炉出钢后加入改质剂(改质剂成分为cao:50%、al2o3:30%、al:11%、其它杂质成分≤10%)进行炉渣改性,渣中feo为4%。
[0052]
(3)炉外精炼(rh):
①
rh到站到抽真空时间6min,rh到站温度1670℃。
[0053]
②
rh脱碳结束加铝后循环时间控制在8min。
[0054]
③
rh破空到连铸开浇之间的镇静时间31min。
[0055]
(4)连铸:连铸过程采用中包内用氩气清扫、填充,进行氩气保护,防止二次氧化。将冶炼合格的钢水浇注成合格的连铸坯,连铸坯厚度230mm。
[0056]
(5)连铸坯加热:将连铸坯加热到1220℃,保证微合金元素充分固溶。
[0057]
(6)粗轧:经过多道次大变形轧制将连铸坯轧制成厚度为40mm的中间坯。
[0058]
(7)精轧:将粗轧后的中间坯经多机架精轧机连续轧制成厚度为9mm的带钢,精轧时投入机架间冷却水量80%,精轧终轧温度890℃。
[0059]
(8)层流冷却:钢带精轧后采用层流冷却方式冷却,冷却速率25℃/s,层流冷却每组上、下水比4∶6。
[0060]
(9)卷取:钢带冷却后卷取,卷取温度550℃。
[0061]
(10)酸洗:钢板经酸洗后去除表面氧化铁皮,保证钢板表面质量。
[0062]
(11)冷轧:钢板经酸洗后冷轧,冷轧机工作辊的表面粗糙度ra :1.0μm。
[0063]
采用该方法生产的冷轧深冲钢的化学成分的质量百分配比如下:c:0.005%,si:0.03%,mn:0.20%,s:0.003%,ti:0.03%,al:0.04%,n:0.0025%, o:0.0017%,p:0.0007%,其余为fe与不可避免的杂质。钢水纯净度水平高,冷轧后钢板表面反射率为85%,冷轧钢板的表面质量优良。
[0064]
图1示出了未采用此方法冷轧后的冷轧钢板表面起皮缺陷情况;图2是实施例2中采用此方法冷轧后的冷轧深冲钢表面情况,表面反射率为85%。
[0065]
实施例三本高表面质量冷轧深冲钢的控制方法的实施例为下述依次的步骤:(1)铁水预处理:高炉铁水在铁水预处理工序进行喷吹镁粉或石灰粉进行脱硫,经铁水预处理后,硫含量≤0.005%。
[0066]
(2)转炉冶炼:
①
转炉终点控制c*o积在0.0019
×
10-4
,转炉出钢前进行大流量(0.12nm3/(t
•
min))底吹搅拌3min。转炉终点[o]为750ppm。
[0067]
②
转炉出钢采用滑板挡渣,下渣量38mm,随后进行炉后扒渣,渣层厚度11mm。
[0068]
③
转炉出钢后加入改质剂(改质剂成分为cao:40%、al2o3:40%、al:12%、其它杂质成分≤10%)进行炉渣改性,渣中feo为3%。
[0069]
(3)炉外精炼(rh):
①
rh到站到抽真空时间3min,rh到站温度1660℃。
[0070]
②
rh脱碳结束加铝后循环时间控制在6min。
[0071]
③
rh破空到连铸开浇之间的镇静时间38min。
[0072]
(4)连铸:连铸过程采用中包内用氩气清扫、填充,进行氩气保护,防止二次氧化。将冶炼合格的钢水浇注成合格的连铸坯,连铸坯厚度230mm。
[0073]
(5)连铸坯加热:将连铸坯加热到1180℃,保证微合金元素充分固溶。
[0074]
(6)粗轧:经过多道次大变形轧制将连铸坯轧制成厚度为40mm的中间坯。
[0075]
(7)精轧:将粗轧后的中间坯经多机架精轧机连续轧制成厚度为9mm的带钢,精轧时投入机架间冷却水量60%,精轧终轧温度850℃。
[0076]
(8)层流冷却:钢带精轧后采用层流冷却方式冷却,冷却速率20℃/s,层流冷却每组上、下水比4∶6。
[0077]
(9)卷取:钢带冷却后卷取,卷取温度650℃。
[0078]
(10)酸洗:钢板经酸洗后去除表面氧化铁皮,保证钢板表面质量。
[0079]
(11)冷轧:钢板经酸洗后冷轧,冷轧机工作辊的表面粗糙度ra :1.1μm。
[0080]
采用该方法生产的冷轧深冲钢的化学成分的质量百分配比如下:c:0.002%,si:0.02%,mn:0.10%,s:0.002%,ti:0.05%,al:0.03%,n:0.0030%, o:0.0016%,p:0.0008%,其余为fe与不可避免的杂质。钢水纯净度水平高,冷轧后钢板表面反射率为90%,冷轧钢板的表面质量优良。
[0081]
本发明上述实施例,其并不是用来限定本发明,本发明还可以有其它实施方式,凡采用等同替换或等效变换形成的技术方案,均落在本发明权利要求所界定的保护范围之内。