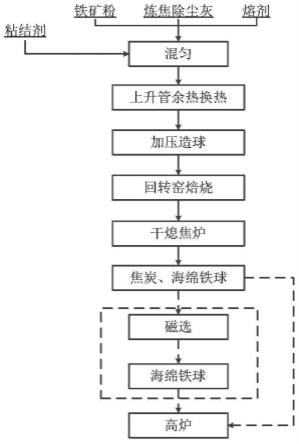
1.本发明属于炼铁原料领域,尤其涉及一种含碳废物制备直接还原铁的方法。
背景技术:2.焦炭作为高炉炼铁的主要原燃料,对高炉起着不可替代的作用。一方面,在焦炭生产过程中,会产生大量除尘灰,包括装煤除尘灰、推焦除尘灰、干熄焦除尘灰、筛转运焦除尘灰等。各工序除尘灰性质差异较大,但固定碳含量较高。以往一般作为发电或者烧结工序中的普通燃料,为了保证燃烧充分,要求除尘灰粒度不能过细,所以粒度较小的炼焦除尘会利用附加值不高。另一方面,焦炭从焦炉推出后,一般红焦温度达到800~1000℃,目前主要是将红焦运至干熄焦炉,与氮气进行换热后,再利用蒸汽锅炉进行热量回收。为了实现含碳固废高附加值利用以及充分利用红焦余热,提出利用炼焦除尘灰含碳废物制备含碳球团,并利用含碳球团与红焦换热,含碳球团发生预还原反应,进而制备金属化率较高的含铁球团。
技术实现要素:3.为克服现有技术的不足,本发明的目的是提供一种含碳废物制备直接还原铁的方法,实现炼焦除尘灰等含碳废物高附加值利用,同时利用红焦余热制备出金属化率较高的含铁球团。
4.为实现上述目的,本发明通过以下技术方案实现:
5.一种含碳废物制备直接还原铁的方法,包括以下步骤:
6.1)将铁矿粉、炼焦除尘灰、熔剂混匀,在混匀过程中喷洒粘结剂,利用焦炉上升管余热进行换热10~30min后,加压造球,然后再在1000~1300℃条件下焙烧10~40mim,得到一次还原球团;
7.2)将焦炭、步骤1)中的一次还原球团分别分批装入干熄焦炉,利用干熄焦炉中焦炭余热,对一次还原球团进行二次还原得到海绵铁球;
8.或将步骤1)中的一次还原球团均匀布料在干熄焦罐储存的红焦外表层,与干熄焦焦罐中的红焦一同进干熄焦炉,得到二次还原的海绵铁球;一次还原球团与红焦质量比控制在1:50~1:10;
9.3)海绵铁球与焦炭在干熄炉内一同冷却,并随焦炭一同由干熄焦炉排焦口排出,一同进入高炉;
10.或在干熄炉排焦口处、转运皮带处分别设有磁选装置,海绵铁球随焦炭一同由干熄焦炉排焦口排出、转运时,海绵铁球与焦炭分离。
11.步骤1)中,铁矿粉质量百分比50%~80%,炼焦除尘灰质量百分比5%~45%,粘结剂质量百分比0.5%~3.0%,熔剂质量百分比1%~20%。
12.步骤1)获得的一次还原球团的耐压力≥2000n,转鼓强度≥78%。
13.所述的炼焦除尘灰为干熄焦除尘灰、装煤除尘灰、推焦除尘灰、皮带转运站除尘灰中的一种或者多种,所述的炼焦除尘灰固定碳含量80%~90%,挥发分为1.0%~5.0%,灰
分为5.0%~13.5%。
14.步骤1)炼焦除尘灰配入量大于铁矿粉中全部可被还原的氧化物还原所需的固定碳折算出的除尘灰量。
15.步骤1)中所述的铁矿粉包括磁铁矿、赤铁矿、针铁矿以及选铁后的尾矿中的一种或多种。
16.步骤2)中,焦炭、一次还原球团分别分批装入干熄焦炉,或者一次还原球团均匀布料在干熄焦罐储存的红焦外表层,均利用螺旋布料器进行均匀布料,螺旋布料器与中心轴角度可调,螺旋布料球团均匀分布在干熄焦炉红焦或干熄焦罐红焦表面上。
17.步骤1)中所述的熔剂包括石灰、石灰石、理石粉、熟石灰中的一种或多种。
18.步骤1)中所述的粘结剂包括焦油、沥青、树脂中的一种或多种,在物料混匀过程中,焦油、沥青、树脂均以雾状形式喷入,其中,焦油的温度控制在80℃以上,沥青的温度控制在200℃以上,树脂的温度控制在100℃以上。
19.所述的全部可被还原的氧化物包括feo、fe3o4、fe2o3、feo(oh)、sio2。
20.与现有技术相比,本发明的有益效果是:
21.本发明利用炼焦除尘灰含碳废物、铁矿粉、熔剂、粘结剂等制备含碳球团,直接利用高温焙烧、含碳球团与红焦换热,含碳球团发生预还原反应,进而制备金属化率较高的含铁球团,具体有益效果:
22.(1)由于固体废物炼焦除尘灰本身不具有粘结性,因此在将铁矿粉、炼焦除尘灰、熔剂混匀,在混匀过程中添加粘结剂,进而提高成球率和生球强度,同时保证了还原的充分性。
23.(2)在混料过程中添加熔剂,提高球团矿在高温直接还原过程中的液相生成量,改善还原过程中碳与含铁矿物的充分接触,制备出金属化率较高的海绵球团。
24.(3)利用无粘结黏度、高固定碳含量的含碳固废除尘灰作为还原剂,利用少量粘结剂、熔剂实现加压造球、回转窑焙烧一次还原后制备耐压和耐磨的含碳球团,同时充分利用红焦余热,实现含碳球团在干熄炉中的二次还原,显著降低高炉co2排放量,实现炼焦除尘废物的高附加值利用。
附图说明
25.图1是本发明的流程示意图。
具体实施方式
26.下面结合说明书附图对本发明进行详细地描述,但是应该指出本发明的实施不限于以下的实施方式。
27.实施例1:
28.见图1,一种含碳废物制备直接还原铁的方法,具体步骤如下:
29.1、将赤铁矿粉、炼焦除尘灰、石灰按照质量百分比53.5%:35%:10%混合,在混匀过程中,将焦油加热至110℃,占混匀物料质量1.5%的焦油以雾状形式喷入,利用焦炉上升管余热进行换热10min后,待焦油呈膏状后加压至10mpa造球,然后待加压球干燥后置于1300℃条件下焙烧40mim,得到一次还原球团矿。焙烧后一次还原球团耐压力为2200n,转鼓
强度为85%。炼焦除尘灰为筛焦除尘灰,固定碳含量为85%,挥发分为1.0%,灰分为13.5%。
30.2、将焦炭、步骤1中一次还原球团分批分别加入干熄焦炉,利用螺旋布料器进行均匀布料,螺旋布料器与中心轴角度在30~85
°
,螺旋布料球团均匀分布在红焦表面上。充分利用干熄焦炉中焦炭余热,在干熄炉预存段将含碳球团进行二次还原得到海绵铁球。一次还原球团矿与红焦质量比控制在1:50。
31.发生的还原反应包括两部分:
32.①
一次还原球团矿中的固定碳与含铁矿物、sio2直接还原反应:
[0033][0034][0035]
②
还原产生的co或干熄焦循环气体中的co、h2与含铁矿物反应或干熄炉焦炭与含
[0036]
铁矿物界面还原反应:
[0037][0038][0039][0040][0041][0042][0043][0044]
3、还原后的海绵铁球与焦炭在干熄炉内一同冷却,并随焦炭一同由干熄焦炉出口处排出,在干熄焦炉出口处和转运皮带处利用磁选装置将海绵铁球与焦炭的分离,得到金属化率为88%的海绵铁球。
[0045]
实施例2:
[0046]
见图1,一种含碳废物制备直接还原铁的方法,具体步骤如下:
[0047]
1、将磁铁矿粉、炼焦除尘灰、石灰石、理石粉按照质量百分比57%:22%:10%:10%混合,在混匀过程中,将废沥青加热至215℃,占混匀物料质量1.0%的废沥青以雾状形式喷入,利用焦炉上升管余热进行换热30min后,待废沥青呈膏状后加压至15mpa造球,然后待加压球干燥后置于1000℃条件下焙烧40mim,得到一次还原球团。焙烧后一次还原球团矿耐压力为2100n,转鼓强度为78%。炼焦除尘灰为装煤除尘灰、推焦除尘灰混合物,固定碳含量为80%,挥发分为3.5%,灰分为11.5%,由于装煤除尘灰中含有煤粉,煤粉在高温加热过程中会析出具有粘结性的胶质体,为此可适当降低废沥青配比。
[0048]
2、将步骤1中的一次还原球团矿均匀直接布料在干熄焦罐储存的红焦外表层,与干熄焦焦罐中的红焦一同进干熄焦炉,充分利用干熄焦炉中焦炭余热,在干熄炉预存段将含碳球团进行二次还原得到海绵铁球,一次还原球团与红焦质量百分比控制在1:50。
[0049]
发生的还原反应包括两部分:
[0050]
①
一次还原球团矿中的固定碳与含铁矿物、sio2直接还原反应:
[0051][0052][0053]
②
还原产生的co或干熄焦循环气体中的co、h2与含铁矿物反应或干熄炉焦炭与含
[0054]
铁矿物界面还原反应:
[0055][0056][0057][0058][0059][0060]
3、还原后的海绵铁球与焦炭在干熄炉内一同冷却,并随焦炭一同由干熄焦炉出口处排出,在干熄焦炉出口处和转运皮带处利用磁选装置将海绵铁球与焦炭的分离,得到金属化率为85%的海绵铁球。
[0061]
实施例3:
[0062]
见图1,一种含碳废物制备直接还原铁的方法,具体步骤如下:
[0063]
1、将针铁矿粉、炼焦除尘灰、石灰按照质量百分比52%:35%:10%混合,在混匀过程中,将废树脂加热至200℃,占混匀物料质量3.0%的废树脂以雾状形式喷入,利用焦炉上升管余热进行换热20min后,待废树脂呈膏状后加压至12mpa造球,然后待加压球干燥后置于1200℃条件下焙烧20mim,得到一次还原球团矿。焙烧后一次球团耐压力为2400n,转鼓强度为88%。炼焦除尘灰主要为装煤除尘灰,固定碳含量为88%,挥发分为5.0%,灰分为9.5%。
[0064]
2、将步骤1中的一次还原球团均匀直接布料在干熄焦罐储存的红焦外表层,与干熄焦焦罐中的红焦一同进干熄焦炉,充分利用干熄焦炉中焦炭余热,在干熄炉预存段将一次还原球团进行二次还原得到海绵铁球,一次还原球团矿与红焦质量百分比控制在1:20。
[0065]
发生的还原反应包括两部分:
[0066]
①
一次还原球团矿中的固定碳与含铁矿物、sio2直接还原反应:
[0067][0068][0069]
②
还原产生的co或干熄焦循环气体中的co、h2与含铁矿物反应或干熄炉焦炭与含
[0070]
铁矿物界面还原反应:
[0071][0072][0073][0074]
[0075][0076]
3、还原后的海绵铁球与焦炭在干熄炉内一同冷却,并随焦炭一同由干熄焦炉出口处排出,在干熄焦炉出口处和转运皮带处利用磁选装置将海绵铁球与焦炭的分离,得到金属化率为95%的海绵铁球。
[0077]
实施例4:
[0078]
见图1,一种含碳废物制备直接还原铁的方法,具体步骤如下:
[0079]
1、将选铁尾矿粉、炼焦除尘灰、熟石灰按照质量百分比53%:25%:20%混合,在混匀过程中,将焦油与沥青混合物加热至205℃,占混匀物料质量2.0%的焦油与沥青混合物以雾状形式喷入,利用焦炉上升管余热进行换热40min后,待焦油与沥青混合物呈膏状后加压造球,然后待加压球干燥后置于1300℃条件下焙烧40mim,得到一次还原球团矿。焙烧后一次还原球团耐压力为2600n,转鼓强度为87%。炼焦除尘灰为干熄焦除尘灰、装煤除尘灰、推焦除尘灰、皮带转运站除尘灰混合物,固定碳含量为80%,挥发分为2.0%,灰分为13.0%。
[0080]
2、将步骤1中的一次还原球团利用螺旋布料器进行均匀布料红焦表面上,螺旋布料器与中心轴角度在30~85
°
。一次还原球团与干熄焦焦罐中的红焦一同进干熄焦炉,充分利用干熄焦炉中焦炭余热,在干熄炉预存段将含碳球团进行二次还原得到海绵铁球,一次还原球团与红焦质量百分比控制在1:30。
[0081]
发生的还原反应与实施例1相同。
[0082]
3、还原后金属化率为90%的海绵铁球与焦炭在干熄炉内一同冷却,并随焦炭一同由干熄焦炉出口处排出进入高炉。
[0083]
上述实施例中,铁矿粉可为磁铁矿、赤铁矿、针铁矿以及选铁后的尾矿中的一种或多种,还可以是难选或者常规方法不适用的含铁矿物。